热轧工艺与设备
热轧工艺流程及其设备
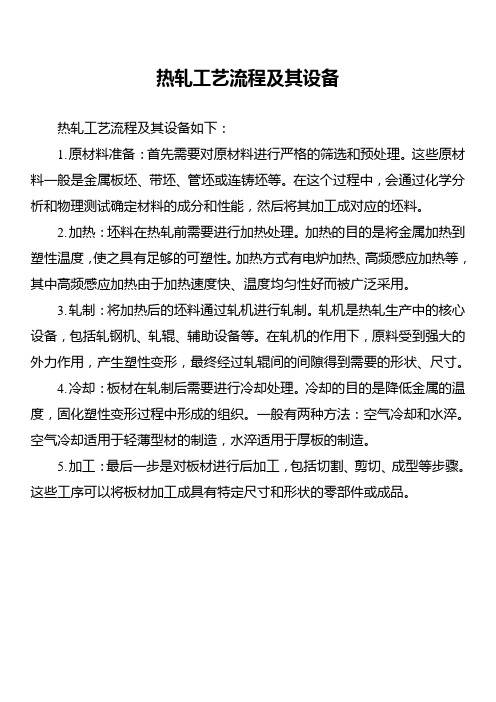
热轧工艺流程及其设备
热轧工艺流程及其设备如下:
1.原材料准备:首先需要对原材料进行严格的筛选和预处理。
这些原材料一般是金属板坯、带坯、管坯或连铸坯等。
在这个过程中,会通过化学分析和物理测试确定材料的成分和性能,然后将其加工成对应的坯料。
2.加热:坯料在热轧前需要进行加热处理。
加热的目的是将金属加热到塑性温度,使之具有足够的可塑性。
加热方式有电炉加热、高频感应加热等,其中高频感应加热由于加热速度快、温度均匀性好而被广泛采用。
3.轧制:将加热后的坯料通过轧机进行轧制。
轧机是热轧生产中的核心设备,包括轧钢机、轧辊、辅助设备等。
在轧机的作用下,原料受到强大的外力作用,产生塑性变形,最终经过轧辊间的间隙得到需要的形状、尺寸。
4.冷却:板材在轧制后需要进行冷却处理。
冷却的目的是降低金属的温度,固化塑性变形过程中形成的组织。
一般有两种方法:空气冷却和水淬。
空气冷却适用于轻薄型材的制造,水淬适用于厚板的制造。
5.加工:最后一步是对板材进行后加工,包括切割、剪切、成型等步骤。
这些工序可以将板材加工成具有特定尺寸和形状的零部件或成品。
轧制生产工艺

轧制生产工艺轧制生产工艺是一种重要的金属加工方式,常用于生产钢材、铝材等材料。
本文就轧制生产工艺的原理、设备和应用进行详细介绍。
轧制生产工艺是通过将金属材料放置在轧机上,通过轧辊的压力和摩擦力对金属材料进行压制和塑性变形,使原始坯料变成所需的产品形状。
轧制生产工艺主要分为冷轧和热轧两种方式。
冷轧是在室温下进行的轧制生产工艺,适用于生产精密的薄板、带材和线材等产品。
冷轧的优点是能够获得高度的表面光洁度和尺寸精度,同时还可以提高金属材料的强度和硬度。
冷轧的设备主要包括冷轧轧机和冷轧机组,其中轧机是通过多个轧辊的转动来对金属材料进行冷轧加工。
热轧是在较高温度下进行的轧制生产工艺,适用于生产较厚的钢板、型材和大型金属材料等产品。
热轧的优点是能够减小金属材料的变形阻力,提高轧制效率和降低能耗。
热轧的设备主要包括热轧轧机和热轧机组,其中轧机通过多个辊子的旋转和轧制来对金属材料进行热轧加工。
轧制生产工艺的应用非常广泛,主要用于制造建筑材料、汽车零部件、机械设备等领域。
例如,轧制生产工艺可以将钢坯轧制成钢筋,用于建筑中的混凝土加固。
同时,轧制生产工艺还可以将铝坯轧制成铝合金板材,用于汽车制造中的车厢板和车身结构。
在轧制生产工艺中,工艺参数的控制非常重要。
例如,轧辊的加热温度、轧制速度、轧制力度等参数都会直接影响到产品的质量和性能。
因此,在实际生产中,需要严格控制这些参数,以确保产品的稳定性和一致性。
总之,轧制生产工艺是一种常用的金属加工方式,通过轧辊的压力和摩擦力对金属材料进行塑性变形,从而获得所需的产品形状。
冷轧和热轧是常用的轧制方式,应用领域广泛。
在实际生产中,需要严格控制工艺参数,以确保产品的质量和性能。
热轧板生产工艺

热轧板生产工艺
热轧板是一种通过将钢材加热至适当温度后,在辊道上进行塑性变形而获得的板材。
热轧板的生产工艺主要包括预处理、加热、轧制和冷却四个步骤。
首先是预处理,即对原材料进行表面处理和切割。
原材料一般为热轧钢坯,首先需要对其进行表面处理,去除表面的氧化物和污物,以保证板材的质量。
然后,对钢坯进行切割,将其切割成适当长度的坯料,以便后续加工。
接下来是加热过程。
将切割好的钢坯送入加热炉中进行加热,使其达到适当的温度。
加热的目的是提高钢的塑性,使其在轧制时更容易变形。
加热炉常用的加热方法包括火焰加热、电阻加热和感应加热等。
然后是轧制过程。
将加热后的钢坯送入轧机中进行轧制。
轧机是通过多组辊道的运动和相互作用,将钢坯逐步压制成所需的板材。
轧机通常有两种类型:热轧机和冷轧机。
热轧机主要用于加工高温的钢坯,能够产生较大的变形量和变形应力,适用于大规模生产。
冷轧机则主要用于加工室温或稍低温度的钢坯,产生较小的变形量和变形应力,适用于加工高精度和高质量的板材。
最后是冷却过程。
轧制后的板材会通过冷却设备进行冷却。
冷却的目的是使板材迅速冷却固化,使其具有所需的机械性能和表面质量。
常用的冷却设备包括水箱冷却、空气冷却和喷淋冷却等,根据不同的板材要求进行选择。
总的来说,热轧板的生产工艺包括预处理、加热、轧制和冷却四个步骤。
通过这些步骤,原材料经过加热和轧制的变形,最终得到具有一定机械性能和表面质量的板材。
热轧板广泛应用于建筑、制造业等领域,对于推动经济发展和满足人们的生活需求起到了重要作用。
热轧带钢生产工艺及工艺要求

钢往板往表 破面坏不钢• 得板有的成气物品泡理、性:结能厚疤或、成度拉为1裂产.、生2~刮破2伤裂5、和.4折锈m叠蚀、的m裂缺缝陷宽、源度夹,杂成6和为50压应~入力2氧集1化中3铁的0m皮薄等弱m缺环陷节,。因为这些缺陷不仅影响轧件的外观形象,而且
板坯:厚度135~180mm 宽度650~2080mm 长度6~17m
薄板坯连铸连轧热轧带钢工艺 Nhomakorabea对定于的重 化要学1用成.2途分.2的,结保设构证备钢良板好布,的置要焊求接2具性有能较、好常的温综或合低性温能冲,击即韧除性了或有一良定好的的冲工压艺性性能能,,保甚证至一除定了的有金一相定 组的织强及度各和向塑组性织以均外匀,性还等要。求保证一
薄板坯连铸连轧热轧带钢工艺 热轧带钢生产工艺及工艺要求
2、薄板坯连铸连轧工艺
薄板坯 连铸连轧 流程1
连铸
定尺坯剪切
定尺坯加热
精轧 轧后冷却
卷取
开卷检查 钢卷运输
钢卷打包 钢卷称重 钢卷打号 钢卷入库
薄板坯 连铸连轧 设备布置1 CSP
CSP连铸机
辊底式均热炉
除鳞机 事故剪
生产能力: - 单线: 150万吨/年 - 双线: 250万吨/年
铸坯厚度: 55~70 mm 成品宽度: 900.....1 680 mm
生产线:唐钢 UTSP 本钢连铸连轧线
3、中厚板坯连铸连轧热轧带钢工艺
工艺流程
连铸
定尺坯切割 定尺坯加热
热坯下线
冷坯装炉 板坯库
可逆 粗轧
热卷
精轧
轧后 冷却
卷取
开卷检查 钢卷运输
钢卷打包
钢卷称重 钢卷打号 钢卷入库
中厚板坯 连铸连轧 设备布置
除鳞 1 定宽压力机
热轧带钢生产线及设备的设计论文
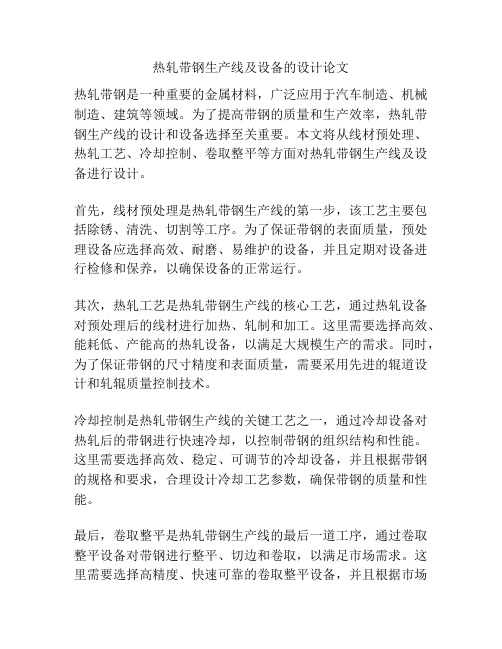
热轧带钢生产线及设备的设计论文热轧带钢是一种重要的金属材料,广泛应用于汽车制造、机械制造、建筑等领域。
为了提高带钢的质量和生产效率,热轧带钢生产线的设计和设备选择至关重要。
本文将从线材预处理、热轧工艺、冷却控制、卷取整平等方面对热轧带钢生产线及设备进行设计。
首先,线材预处理是热轧带钢生产线的第一步,该工艺主要包括除锈、清洗、切割等工序。
为了保证带钢的表面质量,预处理设备应选择高效、耐磨、易维护的设备,并且定期对设备进行检修和保养,以确保设备的正常运行。
其次,热轧工艺是热轧带钢生产线的核心工艺,通过热轧设备对预处理后的线材进行加热、轧制和加工。
这里需要选择高效、能耗低、产能高的热轧设备,以满足大规模生产的需求。
同时,为了保证带钢的尺寸精度和表面质量,需要采用先进的辊道设计和轧辊质量控制技术。
冷却控制是热轧带钢生产线的关键工艺之一,通过冷却设备对热轧后的带钢进行快速冷却,以控制带钢的组织结构和性能。
这里需要选择高效、稳定、可调节的冷却设备,并且根据带钢的规格和要求,合理设计冷却工艺参数,确保带钢的质量和性能。
最后,卷取整平是热轧带钢生产线的最后一道工序,通过卷取整平设备对带钢进行整平、切边和卷取,以满足市场需求。
这里需要选择高精度、快速可靠的卷取整平设备,并且根据市场需求和产品规格,合理设计设备工艺参数,确保产品的尺寸精度和表面质量。
综上所述,热轧带钢生产线及设备的设计需要充分考虑线材预处理、热轧工艺、冷却控制、卷取整平等因素,选择合适的设备和工艺参数,以保障带钢的质量和生产效率。
希望本文的研究能够对热轧带钢生产线的设计和设备选择提供一定的指导和参考。
热轧带钢生产线及设备的设计需要综合考虑多个因素,包括原材料质量、生产工艺、设备性能和工艺参数等。
在原材料的选择上,需要考虑钢种的适用性、含碳量和成分均匀性,以确保带钢的机械性能和化学成分符合要求。
在生产工艺方面,需要根据原材料的性能和要求,合理设计热轧工艺、冷却控制和整平工艺,以保证带钢的尺寸精度和表面质量。
1780热轧生产工艺与设备

1780热轧生产工艺与设备6.1 1780热轧的产品、规格及生产能力宝钢股份不锈钢分公司1780mm热轧以热轧不锈钢钢卷为主导产品,同时发挥轧机能力大、控制水平高的特点,兼顾生产薄规格、高强度、高附加值的优质碳素结构钢、低合金钢等。
不锈钢包括200、300、400系列,其中奥氏体不锈钢约占总量的70%,铁素体不锈钢占25〜27%,马氏体不锈钢占3〜5%;碳素钢中包括双相、多相微合金钢,高强度钢及特殊用途钢等品种,且碳钢产品中以薄规格为主,厚度 1.2〜3.5mm约占80%,以生产热轧酸洗、热轧镀锌及以热代冷用钢卷。
一期的设计产量为年产热轧钢卷282.2万吨,其中不锈钢69.8万吨,碳钢212.4万吨。
由于二期项目中炼钢扩建了炼钢和连铸生产线,热轧增加了3号加热炉,从而增加了近70万吨的不锈钢生产能力。
成品规格如下表所示:代表钢种成品厚度(mm) 成品宽度(mm)碳钢SPHC,SPHD,SPHE,10PCuRE,低合金钢SPA-H,SM400A—CSM490A-C,15MnV,09MnNb1.2〜12.75 750~1630不锈钢304,304L,316,316L,410,420,409,4302.0〜10.0 750~1600 6.2 1780热轧的生产设备及工艺流程6.2.1热轧生产线的主要工艺设备:⑥ G© O@ ©⑯膻1 \ \!'二⑪」 -1 。
j TK.——..... i_661-三座加热炉;2-高压水除鳞箱(HSB); 3-粗轧除鳞;4-粗轧前大立辊(VE); 5-粗轧机(RM); 6-热卷箱(CB); 7-飞剪(CS); 8-精轧前除鳞装置;9-精轧前立辊(F1E);10-7 机架的精轧机;11-层流冷却;12-两台地下卷取机(DC)。
6.2.2生产工艺流程热轧和碳钢连铸及不锈钢连铸毗邻布置,碳钢1号连铸出坯辊道与热轧加热炉上料辊道直接连接,碳钢2号连铸出坯辊道与热轧轧制线直接连接,不锈钢连铸与热轧板坯库用3 号板坯运输辊道连接。
热轧生产工艺
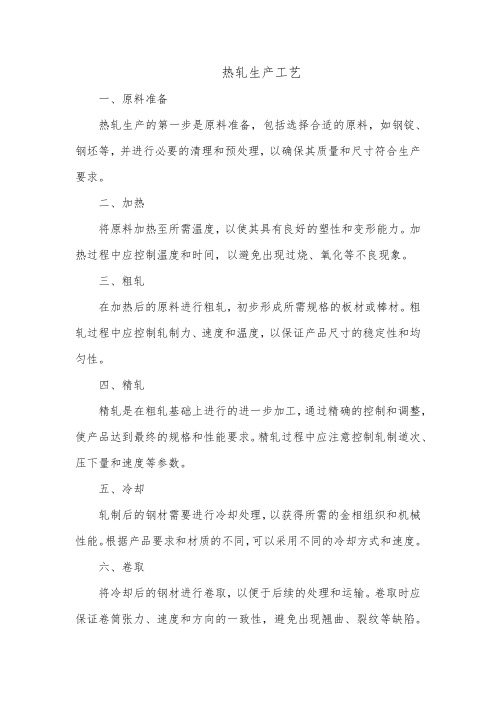
热轧生产工艺
一、原料准备
热轧生产的第一步是原料准备,包括选择合适的原料,如钢锭、钢坯等,并进行必要的清理和预处理,以确保其质量和尺寸符合生产要求。
二、加热
将原料加热至所需温度,以使其具有良好的塑性和变形能力。
加热过程中应控制温度和时间,以避免出现过烧、氧化等不良现象。
三、粗轧
在加热后的原料进行粗轧,初步形成所需规格的板材或棒材。
粗轧过程中应控制轧制力、速度和温度,以保证产品尺寸的稳定性和均匀性。
四、精轧
精轧是在粗轧基础上进行的进一步加工,通过精确的控制和调整,使产品达到最终的规格和性能要求。
精轧过程中应注意控制轧制道次、压下量和速度等参数。
五、冷却
轧制后的钢材需要进行冷却处理,以获得所需的金相组织和机械性能。
根据产品要求和材质的不同,可以采用不同的冷却方式和速度。
六、卷取
将冷却后的钢材进行卷取,以便于后续的处理和运输。
卷取时应保证卷筒张力、速度和方向的一致性,避免出现翘曲、裂纹等缺陷。
七、精整
对卷取后的钢材进行精整处理,包括矫直、剪切、表面处理等,以提高产品的表面质量和整体性能。
精整过程中应采用适当的工艺参数和技术措施。
八、质量检测
在生产过程中和成品阶段进行质量检测,以确保产品的质量和性能符合要求。
质量检测包括外观检查、尺寸测量、金相分析、力学性能测试等。
热连轧带钢生产工艺

1)立辊轧机
• 立辊轧机位于粗轧机水平轧机的前面,大多数立辊轧机的 牌坊与水平轧机的牌坊连接在一起。立辊轧机主要分为两 大类,即一般立辊轧机和有AWC功能的重型立辊轧机。 • 一般立辊轧机结构简单,主传动电机功率小、侧压能力普 遍较小,而且控制水平低,辊缝设定为摆死辊缝,不能在 轧制过程中进行调节,带坯宽度控制精度不高。 • 有AWC功能立辊轧机结构先进,主传动电机功率大,侧压 能力大,具有AWC功能,在轧制过程中对带坯进行调宽、 控宽及头尾形状控制,不仅可以减少连铸板坯的宽度规格, 而且有利于实现热轧带钢板坯的热装,提高带坯宽度精度 和减少切损。
5、精轧机组
• 精轧机组是成品轧机,布置在粗轧机组中间辊道或热卷箱 的后面,是带钢热连轧线的核心设备。精轧是决定产品质 量的主要工序,带钢的力学性能主要取决于精轧机终轧温 度和卷取温度。
1)精轧机组布置
• 精轧机组的布置有多种形式,在我国的热轧带钢轧机中, 精轧机组的布置主要有5种,如图2-13-18所示。 • 鞍钢1700和攀钢1450的精轧机组布置同属a类 • 武钢1700和本钢1700的精轧机组布置属b类 • 太钢1549和梅钢1422的精轧机组布置属c类 • 宝钢2050和鞍钢1780的精轧机组均布置属 d 或e类
3、粗轧机
粗轧机的水平轧机是把热板坯减薄成适合于精轧机轧制 的中间带坯。粗轧机的布置有四种方案。
1)全连续式
粗轧区设置5~6 台粗轧机进行连续(不可逆)轧制, 这种布置由于粗轧道次限制为5~6 道次,加上设备重量 过大,生产线过长,目前基本不再采用。
2)3/4连续式
3/4连续式粗轧机由可逆式轧机和不可逆式轧机 组成 。这一布置增加了灵活性,缩短了轧线长度, 但设备重量仍较大。
2)定宽压力机
- 1、下载文档前请自行甄别文档内容的完整性,平台不提供额外的编辑、内容补充、找答案等附加服务。
- 2、"仅部分预览"的文档,不可在线预览部分如存在完整性等问题,可反馈申请退款(可完整预览的文档不适用该条件!)。
- 3、如文档侵犯您的权益,请联系客服反馈,我们会尽快为您处理(人工客服工作时间:9:00-18:30)。
热轧工艺与设备热轧工艺与设备是金属加工领域中重要的一环。
热轧是指将金属材料加热至某一温度并通过辊道加以压制和形变,从而得到所需的形状和尺寸。
本文将深入探讨热轧工艺与设备的相关内容,包括工艺的基本原理、设备的组成和功能以及热轧工艺与设备在钢铁工业中的应用。
一、热轧工艺的基本原理:1. 加热:通过加热炉或其他方式将金属材料加热至一定温度,以使其具有较好的塑性。
2. 轧制:将加热后的金属材料送入轧机中,通过辊道的压制和形变,在一定压力作用下将其轧制成所需的形状和厚度。
3. 冷却:轧制后的金属材料将通过冷却系统进行快速冷却,以消除残余应力和提高材料的机械性能。
二、热轧设备的组成和功能:1. 加热设备:包括加热炉、燃烧器等,用于将金属材料加热至适宜温度。
2. 轧机设备:包括轧机辊道、传动系统等,用于轧制金属材料,实现形状和尺寸的变换。
3. 控制系统:包括温度控制系统、压力控制系统等,用于对热轧过程中的各项参数进行监控与调节,确保产品质量稳定。
4. 冷却设备:包括水冷系统、油冷系统等,用于对轧制后的金属材料进行冷却处理,以满足材料性能的要求。
5. 辅助设备:包括输送系统、辊道清洁系统等,用于协助轧机设备的运行和维护,提高生产效率和设备可靠性。
三、热轧工艺与设备在钢铁工业中的应用:1. 钢板生产:热轧工艺是钢铁工业中生产各种厚度的钢板的常用工艺之一。
通过热轧设备,可以将钢坯轧制成不同厚度和宽度的钢板,用于建筑、汽车制造、船舶建造等领域。
2. 型材生产:热轧工艺也广泛应用于型材生产,如角钢、槽钢、H型钢等。
通过热轧设备,可以将钢坯轧制成各种不同截面形状的型材,满足不同行业对结构材料的需求。
3. 焊管生产:热轧工艺与设备还常用于焊管生产。
通过特定的工艺和设备,可以将热轧钢板经过成型、焊接和后处理等步骤,生产出不同规格和材质的焊管,用于石油、天然气、水暖等领域。
热轧工艺与设备在金属加工领域中具有重要的地位和广泛的应用。
热轧工艺的基本原理包括加热、轧制和冷却,通过热轧设备的组成和功能,可以实现对金属材料的加工和形变。
在钢铁工业中,热轧工艺与设备被广泛应用于钢板生产、型材生产和焊管生产等领域,为各行各业提供了优质的金属材料。
(字数:1225字)氰乙酸钠合成工艺氰乙酸钠是一种广泛用途的有机合成原料,被广泛应用于染料、农药、医药等领域。
本文将详细介绍氰乙酸钠的合成工艺和步骤,以及相关的注意事项。
一、原料准备1. 氰乙酸:购买高纯度的氰乙酸,确保杂质含量低。
2. 氢氧化钠:选择优质的氢氧化钠粉末,纯度要达到工业标准。
二、设备准备1. 反应釜:选择适用的反应釜,确保材质抗腐蚀性能强,容积能够满足产量要求。
2. 冷却器:选择适当的冷却器,确保反应过程中能够有效控制温度。
3. 过滤器:选择细孔过滤器,以去除反应物中的杂质。
三、合成步骤1. 将适量的氰乙酸加入反应釜中,并加入足够的水溶解。
2. 在反应过程中,缓慢添加氢氧化钠溶液,控制反应速率和温度。
3. 继续搅拌反应物,直至完全发生反应。
4. 当反应完成后,将反应物倒入过滤器中,过滤掉未反应的固体或溶液中的杂质。
5. 收集过滤后的溶液,进行浓缩处理,得到氰乙酸钠的固体产物。
6. 将产物干燥,并进行粉碎处理,使其得到所需的粒度。
四、注意事项1. 在反应过程中,应采取严密的安全措施,戴好防护手套、口罩和护目镜,避免接触到有害物质。
2. 控制反应温度,避免反应过热或过低,以免影响反应的效果。
3. 在搅拌过程中,应控制搅拌速度,使反应更加均匀。
4. 对废液的处理要有合理规划,确保环境安全。
氰乙酸钠合成工艺涉及多个步骤,包括原料准备、设备准备和合成步骤。
在合成过程中需要注意安全措施,并严格控制反应温度和搅拌速度。
最终获得的氰乙酸钠固体产物需经过干燥和粉碎处理,以满足使用要求。
合理处理废液是保证环境安全的重要一环。
通过本文提供的合成工艺,可以有效地合成氰乙酸钠。
中国名瓷工艺基础在中国悠久的历史长河中,瓷器被誉为杰出的艺术品和文化象征,具有重要的历史和艺术价值。
中国名瓷工艺凭借其独特的制作技术和精湛的装饰艺术而闻名于世。
本文将深入探讨中国名瓷工艺的基础,从选料、造型、制作工艺以及装饰技法等方面进行详细介绍,以帮助读者更好地了解中国名瓷的制作过程和美学特点。
一、精选材料中国名瓷工艺的基础离不开精选的原材料。
在制作瓷器过程中,最常使用的原料是瓷土和瓷石。
选料的质量和种类会直接影响到瓷器的质地和品质。
瓷土通常分为高岭土和陶瓷土,前者白色,后者黄色或灰白色。
瓷石则用于瓷器的釉料,有助于增加釉面的透明度和光泽。
二、造型设计在中国名瓷工艺中,造型设计是至关重要的一环。
不同的瓷器往往采用不同的造型方式,以展示独特的韵味和美感。
常见的造型包括方盘、圆盘、高脚碗等。
此外,设计师还需要根据实际需求,考虑瓷器的功能性和耐用性,保证瓷器在使用过程中不易碎裂。
以汝窑为例,汝窑是中国宋代最具代表性的主要瓷器窑口之一。
其瓷器常采用优雅而简洁的造型设计,如瓷壶、瓷罐等,体现出中国古代文人雅士的审美趣味。
瓷器的造型多以柔和的曲线为主,富有韵律感,展现了中国传统审美理念中的“中庸之美”。
三、制作工艺中国名瓷工艺的制作过程需要经历多个复杂的工艺环节,包括制泥、拉胎、修刀、修磨、装饰等。
这些工艺环节需要熟练的工匠经过多年的经验积累和技能培养方能熟练应用。
其中,瓷器制泥是制作过程中的关键环节,通过“开坯”来制作瓷坯,然后再进行后续的造型和装饰。
青花瓷就是中国著名的彩绘瓷器之一。
青花瓷的制作工艺通常需要先将绘制好的图案在素坯上进行刻画,再涂上混有钴元素的釉料进行烧制。
青花瓷的制作精细程度要求十分高,需要熟练的工匠手工绘制,艺术效果迥异,独具风格。
四、装饰技法中国名瓷工艺的另一大特点是装饰技法的独特运用,其丰富多样的装饰形式使瓷器更具观赏价值。
常见的装饰技法包括彩绘、刻花、贴花等。
这些技法既能突出瓷器的造型特点,也能表达艺术家独有的创作理念。
景德镇瓷器作为中国最为著名的瓷器之一,其装饰技法尤为丰富。
景德镇瓷器常采用精细的彩绘装饰,如釉下彩、釉上彩等,通过不同的技法表现出丰富的绘画效果和图案构思。
中国名瓷工艺基础包括精选材料、造型设计、制作工艺和装饰技法。
这些方面的综合运用使中国名瓷得以创造出独特的艺术魅力。
通过了解中国名瓷工艺的基础知识,我们能更好地欣赏和理解中国瓷器的美学特点,从而更好地传承和发扬中国传统文化。
台湾的自动化设备走线工艺标准自动化设备走线工艺标准在台湾的制造业中起着至关重要的作用。
走线工艺标准是指在自动化设备的制造过程中,对设备内部各种线缆和连接器的布线、连接和绝缘等进行规范化管理的一套标准。
本文将详细介绍台湾在自动化设备走线工艺标准方面的实践和经验,以及该标准对设备品质和生产效率的重要性。
一、了解自动化设备走线工艺标准的重要性自动化设备走线工艺标准的制定和遵守对台湾制造业有着重要的意义。
首先,好的走线工艺标准能够提高设备的可靠性和稳定性。
合理的布线可以减少线缆的张力和扭曲,避免线缆之间的干扰和穿线错误。
其次,标准化的走线工艺能够提高设备的维修效率和可维护性。
统一的走线方式使得维修人员能够更快地找到故障线缆或连接器,并进行修复或更换。
最后,符合标准的走线工艺还可以降低设备的能耗和故障率,提高设备的使用寿命和生产效率。
二、台湾自动化设备走线工艺标准的实践和经验台湾的制造业在自动化设备走线工艺标准方面积累了丰富的实践经验。
以下将从三个方面介绍这些实践和经验。
1. 走线路径规划在自动化设备的设计和制造中,首先需要对走线路径进行规划。
这涉及到设备内部各种线缆和连接器的布置和连接方式。
在规划走线路径时,需要考虑以下因素:线缆的长度、种类和数量,设备内部的结构和空间限制,线缆与其他部件或设备的交叉与干扰等。
为了规范走线路径的设计,台湾制造业普遍采用CAD软件进行走线路径规划和模拟。
2. 走线方式和连接器选择选择合适的走线方式和连接器对设备的性能和可靠性有着重要的影响。
在台湾制造业中,常见的走线方式包括梯形走线、匀速走线和卷绕走线等。
梯形走线适用于直线型设备,匀速走线适用于圆形设备,而卷绕走线适用于曲线型设备。
此外,台湾制造业还非常注重连接器的选择。
连接器应具有良好的接触性能和防护性能,能够防止湿气、灰尘和振动的干扰。
3. 电缆绝缘和封装处理电缆的绝缘和封装处理直接关系到设备的安全和稳定性。
在台湾制造业中,常见的绝缘和封装处理方式包括绝缘套管、尼龙束带和防水胶等。
绝缘套管是一种用于绝缘和包裹电缆的保护材料,具有阻燃、耐高温和耐腐蚀的特性。
尼龙束带是一种可调节长度的束缚工具,可用于固定和捆绑电缆。
防水胶是一种耐高温和耐腐蚀的粘合材料,常用于连接器的密封处理,以防止水分和湿气的侵入。
自动化设备走线工艺标准在台湾的制造业中具有重要的地位和作用。
良好的走线工艺标准可以提高设备的可靠性和稳定性,提高设备的维修效率和可维护性,降低能耗和故障率,提高设备的使用寿命和生产效率。
台湾制造业在自动化设备走线工艺标准方面有着丰富的实践经验,包括走线路径规划、走线方式和连接器选择以及电缆绝缘和封装处理等方面。
这些实践和经验对于其他行业和地区在自动化设备走线工艺标准方面的制定和实施都具有借鉴和参考价值。
下限釉工艺优点下限釉工艺是陶瓷制作中常用的一种工艺,具有许多优点。
通过本文,我们将详细介绍下限釉工艺的特点、优点,并通过举例说明其在实际应用中的价值。
一、下限釉工艺的特点下限釉工艺是一种在陶瓷表面施以釉料的过程,其特点主要包括以下几个方面:1. 均匀性:下限釉工艺能够使釉料均匀分布在陶瓷表面,确保整体的质感和外观统一。
2. 耐磨性:通过下限釉工艺,陶瓷表面形成一层坚硬的釉层,提高陶瓷的耐磨性和抗刮擦能力。
3. 抗污性:由于下限釉工艺形成的釉层具有较高的密封性,使陶瓷表面不易吸附污垢,易于清洁和保养。
4. 色彩稳定:下限釉工艺能够保证陶瓷表面的颜色长期稳定,不易褪色。
5. 防水性:应用下限釉工艺后的陶瓷制品具有较好的防水性能,可以更好地保护陶瓷内部结构,提高陶瓷的使用寿命。
二、下限釉工艺的优点下限釉工艺在陶瓷制作中有许多显著的优点,如下所述:1. 提高产品质量:下限釉工艺能够确保陶瓷制品表面的光滑度和均匀性,提高产品的整体质量,增强其使用寿命。
2. 增强产品的美观性:下限釉工艺使陶瓷制品表面形成一层光滑的釉层,使其外观更加美观大方,提升产品的附加值。
3. 便于清洁和保养:下限釉工艺形成的釉层具有较好的防污性和耐磨性,用户可以轻松清洁和保养陶瓷制品,延长其使用寿命。
4. 提高产品的功能性:下限釉工艺能够增强陶瓷制品的防水性和耐化学性,使其更适合于一些特殊的使用环境,如厨房和浴室等。
5. 节约生产成本:下限釉工艺可以使陶瓷制品的生产过程更加简单高效,减少原材料和能源的浪费,降低生产成本。