管理体系手册-英文版.doc
医疗器械质量管理体系核查资料 英文版

医疗器械质量管理体系核查资料英文版Title: Documents for Inspection of Medical Device Quality Management SystemIntroduction:A robust and effective quality management system is crucial for the manufacturing and distribution of medical devices. To ensure compliance with regulatory standards and maintain the highest quality standards, regular inspections and audits of the quality management system are essential. This article presents an overview of the documents required for the inspection of a medical device quality management system.1. Quality Manual:The quality manual serves as the foundation of the quality management system. It outlines the organization's quality policy, objectives, and responsibilities. During the inspection, the conformity of the quality manual with relevant regulations and standards will be evaluated.2. Standard Operating Procedures (SOPs):SOPs provide detailed instructions on processes and activities within the quality management system. These procedures cover various aspects, including design control, purchasing, manufacturing, packaging, labeling, storage, anddistribution. Inspectors will review the SOPs to ensure their compliance with applicable regulations and their effectiveness in achieving quality objectives.3. Risk Management Documents:Medical device manufacturers must have a robust risk management process in place. Documentation related to risk management, such as risk management plans, risk assessments, and risk control measures, should be available for inspection. The inspector will evaluate the adequacy of the risk management process and its integration throughout the quality management system.4. Corrective and Preventive Actions (CAPA):CAPA procedures are essential for identifying, investigating, and resolving problems that may arise during the manufacturing or distribution of medical devices. The inspection will involve reviewing the CAPA documentation, including records of non-conformities, root cause analyses, corrective actions, and preventive measures. The effectiveness of the CAPA system will be assessed to ensure continuous improvement.5. Training Records:Proper training ensures that personnel involved in thequality management system are competent and capable of performing their assigned tasks. Inspection of training records will determine if employees have received sufficient training on quality procedures, regulations, and any specific device-related requirements.6. Internal and External Audit Reports:Internal and external audits play a critical role in identifying potential issues and areas for improvement within the quality management system. The inspection will involve reviewing audit reports to assess the thoroughness of the audits, the identification of non-conformities, and the implementation and effectiveness of corrective actions.Conclusion:The inspection of a medical device quality management system requires a comprehensive review of various documents. These documents provide evidence of compliance with regulatory standards and the effectiveness of the system in ensuring the production and distribution of safe and effective medical devices. By meticulously assessing these documents, regulatory bodies can ensure that manufacturers maintain the highest quality standards and protect the well-being of patients.。
SA8000-2023修订版(中文版和英文版)

SA8000-2023修订版(中文版和英文版)
概述
SA8000是一种社会责任标准,旨在确保企业在管理、劳动条
件和对员工的权益方面达到一定的最低标准。
本文档介绍了
SA8000-2023修订版的内容和变化。
主要变化
1. 管理体系要求
- 强调企业管理层的责任,包括领导力和承诺。
- 要求企业建立有效的沟通渠道,使员工能够表达意见和关切。
- 强调在供应链管理中的交流和合作。
2. 劳动条件要求
- 强化对雇佣合同的监督和执行,确保员工享有合理的工作条
件和权益。
- 要求提供合理的工作时间和休息时间。
- 鼓励培训和职业发展机会,提高员工的技能和素质。
3. 工资和福利要求
- 规定必须支付合理的工资,以满足员工的基本需求。
- 要求提供福利措施,如医疗保险和退休金计划。
4. 儿童劳动和强制劳动禁止
- 禁止雇用未满足法定工作年龄要求的儿童。
- 禁止强制劳动和任何形式的人身剥削。
5. 员工权益和福利
- 强调员工享有自由结社和集体谈判的权利。
- 要求提供安全和健康的工作环境,预防事故和职业病发生。
- 保护员工的隐私和个人信息。
结论
SA8000-2023修订版的目标是促进企业社会责任的履行,保护员工权益,改善劳动条件。
通过遵守这一标准,企业可以建立良好的声誉,提高业务的可持续性和竞争力。
世界500强企业的KPI绩效管理操作手册(doc 68页)

世界500强名企的KPI绩效管理操作手册——精华版KPI(Key Performance Indication)即关键业绩指标,是通过对组织内部某一流程的输入端、输出端的关键参数进行设置、取样、计算、分析,衡量流程绩效的一种目标式量化管理指标,是把企业的战略目标分解为可运作的远景目标的工具,是企业绩效管理系统的基础。
KPI是现代企业中受到普遍重视的业绩考评方法。
KPI可以使部门主管明确部门的主要责任,并以此为基础,明确部门人员的业绩衡量指标,使业绩考评建立在量化的基础之上。
建立明确的切实可行的KPI 指标体系是做好绩效管理的关键。
KPI法符合一个重要的管理原理--“二八原理”。
在一个企业的价值创造过程中,在在着“20/80”的规律,即20%的骨干人员创造企业80%的价值;而且在每一位员工身上“二八原理”同样适用,即80%的工作任务是由20%的关键行为完成的。
因此,必须抓住20%的关键行为,对之进行分析和衡量,这样就能抓住业绩评价的重心。
一、建立关键业绩指标体系遵循的原则1、目标导向。
即KPI必须依据企业目标、部门目标、职务目标等来进行确定。
2、注重工作质量。
因工作质量是企业竞争力的核心,但又难以衡量,因此,对工作质量建立指标进行控制特别重要。
3、可操作性。
关键业绩指标必须从技术上保证指标的可操作性,对每一指标都必须给予明确的定义,建立完善的信息收集渠道。
4、强调输入和输出过程的控制。
设立KPI指标,要优先考虑流程的输入和输出状况,将两者之间的过程视为一个整体,进行端点控制。
二、确立KPI指标应把握的要点1、把个人和部门的目标与公司的整体战略目标联系起来。
以全局的观念来思考问题。
2、指标一般应当比较稳定,即如果业务流程基本未变,则关键指标的项目也不应有较大的变动。
3、指标应该可控制,可以达到。
4、关键指标应当简单明了,容易被执行这所接受和理解。
5、对关键业绩指标要进行规范定义,可以对每一KPI指标建立“KPI定义指标表”。
ISO9001程序文件-中英文+流程+对照表
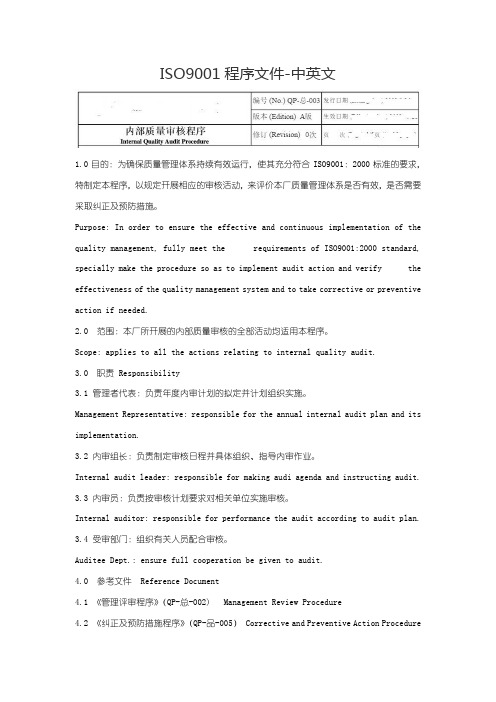
ISO9001程序文件-中英文1.0目的:为确保质量管理体系持续有效运行,使其充分符合ISO9001:2000标准的要求,特制定本程序,以规定开展相应的审核活动,来评价本厂质量管理体系是否有效,是否需要采取纠正及预防措施。
Purpose: In order to ensure the effective and continuous implementation of the quality management, fully meet the requirements of ISO9001:2000 standard, specially make the procedure so as to implement audit action and verify the effectiveness of the quality management system and to take corrective or preventive action if needed.2.0 范围:本厂所开展的内部质量审核的全部活动均适用本程序。
Scope: applies to all the actions relating to internal quality audit.3.0 职责 Responsibility3.1 管理者代表:负责年度内审计划的拟定并计划组织实施。
Management Representative: responsible for the annual internal audit plan and its implementation.3.2 内审组长:负责制定审核日程并具体组织、指导内审作业。
Internal audit leader: responsible for making audi agenda and instructing audit.3.3 内审员:负责按审核计划要求对相关单位实施审核。
ISO9001-2015全套质量管理体系文件

**********有限公司企业标准QM/YS-2016质量手册按ISO9001:2015要求编制版本号: A/0受控号:2016-5-1发布 2016-5-1实施**********有限公司发布修订记录目录批准令本《质量手册》是依据ISO9001:2015质量管理体系标准要求,结合本公司产品生产特点、生产规模和体制实际情况,为确保和提高产品质量,健全质量管理体系而编制。
本手册规定了本公司的质量方针和目标,对产品实现过程的持续改进、质量管理体系的有效运行规定了准则和方法。
本手册是本公司质量管理体系运行开展各项质量活动的指导性文件、法规性文件,现予以发布。
本公司全体员工务必认真学习,严格遵照执行,确保本手册得以认真有效的实施。
本手册于二○一六年五月一日起正式实施。
凡于本手册不一致的质量文件一律以本手册为准。
总经理: ***二○一六年五月一日管理者代表任命书为了便于公司ISO9001质量管理体系的有效推行,由总经理任命***先生为本公司管理者代表,其职责和权限为:1、负责按ISO9001标准建立保持并经济有效地实施文件化质量体系,领导各职能部门开展质量活动;2、负责方针目标管理,及时向总经理汇报质量管理体系运行情况,负责质量管理体系内部审核的组织领导工作,并提供质量体系改进的依据和建议;3、负责组织贯彻实施企业经营管理决策、目标方针,完善各项管理制度,不断提高公司管理水平;4、领导内部质量审核活动,协调解决质量管理体系运行中的不一致等问题;5、负责做好对过程的监视和测量及数据分析的领导控制工作;6、负责质量管理体系有关事宜的外部联络工作;7、负责提高公司员工文化、生活水平,营造良好的作业环境和安全舒适的生活环境;8、负责公司重大纠正/预防措施的审批和组织实施。
总经理:***本公司宗旨:品质稳定----我们成功的基石公司的质量方针:开拓进取,群策群力;持续精进,客户满意。
释义:1、在当前的市场竞争中,保持质量管理体系运行的持续有效性是企业承诺的主题,其根本目的在于为社会和顾客提供满足要求的产品。
tl测试管理体系.doc

“TL系列管理系统”项目计划简书TL系列管理系统中国推广小分队1.什么是TL系列管理系统TL系列管理系统是以Testlink测试管理系统为基本的引擎,经过汉化扩充后结合我们自己的实际操作经验进行推广的组系列产品,其中包括测试管理系统、任务管理系统、目标管理管理系统和培训训练管理系统.就象一个好的傻瓜相机,能够把业余爱好者迅速提升到接近专业水平一样,我们希望通过对它的培训使用,使得任何规模的公司组建新的团队,能够迅速达到等同于在大公司具有丰富经验的团队的管理水平.2.什么是TestiinkTestlink原是一个成熟的英文工具系统.2008年被OPENSOURCETESTING. ORG评为最受欢迎的20种主要的质量管理开放软件工具的首位.Tool popularity among survey respondants参加评选的工•具受欢迎程度列表如卜.:工具名称得票率Test Link13.2%Selenium11.7%Watir11.3%Bugzilla 4.3%Mantis 4.3%JUnit 3.5% FIT/FitNesse 3.1% JMeter 2.7% OpenSTA 1.9% Test NG 1.9% RSpec 1.6% Ruby 1.6% WatiN 1.6% Fire Fox 1.2% Testopia 1.2% Wireshark 1.2% Autolt 0.8% Canoo Web Test 0.8% easyb 0.8% Emma 0.8% Findbug 0.8% jsUnit 0.8% Marathon 0.8% PHPUnit 0.8% RTH 0.8% Web Inject 0.8% Web LOAD 0.8% WET 0.8% All other xUnits - too many to list 0.4% allpairs 0.4% Android 0.4% bugzillametrics 0.4% buildbot 0.4% checkstyle 0.4% Cobertura 0.4% Concordion 0.4% cppunit 0.4% cruise control 0.4% CubicTest 0.4% cunit 0.4% Dogtail 0.4% dotproject 0.4% Easy Mock 0.4% Eclipse 0.4% Eventum 0.4% executequery 0.4% figleaf 0.4% FireBug 0.4% FireWatir 0.4% Grinder 0.4% HL7Test Harness 0.4% htmlunit 0.4% Hudson 0.4% hyperic 0.4%jenny 0.4%JRuby 0.4%jwebunit 0.4%Lou Wilson's VBA/Excel Web Test Automation Tool 0.4% nHapi 0.4%nose 0.4%NotePad+ + 0.4%NUnit 0.4%Paros 0.4%Perl 0.4%Perl WWW, Mechanize 0.4%perlclip 0.4%perl-Win32GuiTest 0.4%PHP 0.4%pmd 0.4%Pylot 0.4%Python 0.4%QaTraq 0.4%Ruby WebBench 0.4%Sahi 0.4%SalomeTMF 0.4%SAMIE 0.4%SandCastle 0.4%Seagul 0.4%simpletest 0.4%SoapUl 0.4%STAF 0.4%STAF & STAX 0.4%SymbianOS Unit test 0.4%TestComplete 0.4%The Grinder 0.4%twill 0.4%Unitils 0.4%utPLSQL 0.4%Watij 0.4%xUnit 0.4%Testlink已经作为开发和测试技术团队的管理工具在国外数I•家大公司使用,其中世界知名品牌的公司有:INTELYAHOOCOMCASTQUANTUM McAfeeExpediaTestlink是一种专门用来为产品测试管理的团队协作工具.团队成员对一个产品或者系统进行质量测试管理的时候,对于所有做出来的产品需求功能检验、测试案例设计、测试任务分配和管理质量跟踪等全部能够用这个系统来记录管理.由于Testlink具有基于网络的优势,成员能够在不同地点实现共同协作.它的使用,强制性地把产品质量测试这样一个经验性很强的活动,变成了一项有明确要求指导的,有清晰任务分工的,有便捷报表管理的,可以组织管理很多团队成员参加的,能够追踪历史性和机械性的操作.把Testlink和一个具有丰富经验的测试设计师的具体产品知识相结合,能够把一个经验不是很丰富的新团队,迅速提高到等同于大公司里具有丰富经验团队的水平.对于需要团队协作开发和测试的产品制造公司,培训队伍熟练使用这个工具,是一种最具高回报的管理投资。
最新版本可持续发展- HSF-环境管理体系手册
最新版本可持续发展- HSF-环境管理体系手册简介本手册汇集了最新版本的可持续发展的环境管理体系,通常简称为HSF(HuiShengFeng)-环境管理体系手册。
该手册旨在帮助组织实施和维护可持续发展的环境管理体系,以促进环境保护和资源可持续利用。
目标本手册的目标是实现以下几点:- 确保组织遵守相关环境法规和标准;- 审视组织的环境问题,并采取必要的措施予以改进;- 减少环境污染和资源浪费;- 提高员工和利益相关方对可持续发展的认识和参与度;- 促进组织在市场中的可持续发展竞争力。
内容概要本手册的内容包括以下几个方面:1. 环境管理体系要求介绍了建立和维护HSF环境管理体系的要求,包括确定环境政策、制定目标和计划、执行措施和监控等。
2. 环境法规和标准列举了与环境保护相关的法律法规和标准,包括国家和地方政府制定的环境保护相关法律法规和国际标准。
3. 环境评估和管理介绍了环境评估和管理的基本原理和方法,包括环境影响评估、环境风险评估和环境管理计划的制定等。
4. 环境监测与报告说明了环境监测的目的和方法,包括环境指标的监测和数据采集、环境报告的编制和提交等。
5. 环境培训和宣传介绍了组织内部环境培训的重要性和方法,包括员工培训计划的制定和宣传策略的设计等。
6. 持续改进强调了持续改进的重要性,并提供了改进措施的选定和实施方法。
7. 文档控制和审核说明了文档控制和审核的要求,包括文档的编制、审核和审查流程等。
结论HSF-环境管理体系手册是一个有效的工具,可以帮助组织建立和维护可持续发展的环境管理体系。
通过遵守相关法规和标准,实施环境管理措施,持续改进和加强环境培训,组织可以实现环境保护和资源可持续利用的目标,提高自身在市场中的竞争力。
ISO14001文件管理与控制程序(中英文版)
文件管理与控制程序Documents management and control procedure1.目的Purpose确保环境管理体系文件、适用的外来文件(有关的法律、法规、标准、相关方提供的文件或规范)使用的有效性。
To assure the2.适用范围 scope适用于对环境管理体系相关文件及适用的外来文件的控制。
It is apply to theenvironment management system relation documents and usable external documents’ control.3.职责Responsibility3.1 环工组:负责环境管理体系文件及适用的外来文件的归口管理;负责监控文件的执行。
The environment team: to manage and be in charge of environment management documents and external documents.3.2 各部门individual department:确保各相关场所均使用现行文件的有效版本。
To ensureThe relative workplace is using the current effective documents.4.工作程序Work procedure4.1文件控制范围包括:documents control’s scopea)环境管理手册;environment management manual;b)环境管理体系程序文件;environment management system procedure documents;c)环境管理体系作业指导文件;the work instruction documents for environment management system;d)环境记录表格;environment record form;e)外来文件。
ISO9001:2000中文和英文版
ISO9001:2000中英文对照Quality management systems — Requirements质量管理体系——要求1 Scope1 范围1.1 General1.1 总则This International Standard specifies requirements for a quality management system where an organization本标准为有下列需求的组织规定了质量管理体系要求:a) needs to demonstrate its ability to consistently provide product that meets customer and applicable regulatory requirements, and需要证实其有能力稳定地提供满足顾客和适用的法律法规要求的产品;b) aims to enhance customer satisfaction through the effective application of the system, including processes for continual improvement of the system and the assurance of conformity to customer and applicable regulatory requirements.通过体系的有效应用,包括体系持续改进的过程以及保证符合顾客与适用的法律法规要求,旨在增进顾客满意。
NOTE In this International Standard, the term “product”applies only to the product intended for, or required by, a customer.注:在本标准中,术语“产品”仅适用于预期提供给顾客或顾客所要求的产品。
国际民航组织ICAO Doc9859《安全管理手册》(SMM)2013年第三版 英文
Published in separate English, Arabic, Chinese, French, Russian and Spanish editions by the INTERNATIONAL CIVIL AVIATION ORGANIZATION 999 University Street, Montréal, Quebec, Canada H3C 5H7
1-1
1.1 General...........................................................................................................................................
Doc 9859, Safety Management Manual (SMM) Order Number: 9859 ISBN 978-92-9249-214-4
© ICAO 2013 All rights reserved. No part of this publication may be reproduced, stored in a retrieval system or transmitted in any form or by any means, without prior permission in writing from the International Civil Aviation Organization.
For ordering information and for a complete listing of sales agents and booksellers, please go to the ICAO website at www.icao.int.
- 1、下载文档前请自行甄别文档内容的完整性,平台不提供额外的编辑、内容补充、找答案等附加服务。
- 2、"仅部分预览"的文档,不可在线预览部分如存在完整性等问题,可反馈申请退款(可完整预览的文档不适用该条件!)。
- 3、如文档侵犯您的权益,请联系客服反馈,我们会尽快为您处理(人工客服工作时间:9:00-18:30)。
XXXXXX有限公司XXXXXX科技有限公司XXXXXX技术有限公司QEO Management Manual (Basis of ISO9001:2008/ISO14001:2004/OHSAS18001:2007)Document No.: HM-QEOM-2015Version: D/0Compile : Distribute No :Review : Control state :Approve : Effect date : 2015 .01. 10Each department: After receiving the modification and revision of the document, the holdingThis <QEO Manual> is worked out based on ISO9001:2008, ISO14001:2004, OHSAS18001:2007, also is the programmatic document of QEO system, and is the public commitment for Customer & Social & Staff, and is the basic standard of all the employees’ behavior.This manual is a controlled document and approved & issued & implemented by General Manager. And Administrative is responsible for all the management about this manual. Nobody can show this manual to any other person without Management representative’s authorization. This manual should be returned to Administrative if the manual holder leaves company.The holder should keep the manual carefully, and shall not be damaged, lost, scribbled.The Dept. manager should summarize all advice and feedback to Administrative timely if any changes; Administrative should review the applicability and validity periodically, if necessary, should revise the manual based on relevant prevision of <Document control procedure>.Through audit, <QEO Manual > is up to the standard of ISO9001:2008(Quality management system), ISO14001:2004(Environment management system), OHSAS18001:2007(Occupational Health and Safety management system), and meets the actual situation of our company, also meets the requirement of our QEO system.This manual is issued now, hope all employees comply with it.General Manager:2015.1.10To implement the standard of ISO9001:2008, ISO14001:2004, OHSAS18001:2007, and enhance the leadership of the operation of QEO system, so company decides to appoint XXX to be the Management representative.Responsibility of Management representative:1. ensure that processes needed for the quality management system are established, implemented.2. organize & coordinate & judge all the important items on behalf of top management.3. report to top management on the performance of the quality management system and any need for improvement and solve any other problem.4. publicize and carry out relevant laws,rules,regulations,standards.Ensure the promotion of awareness of meeting customer requirements and social commitment5.liaise with external parties on matters relating to the quality management systemAppoint XXX to be employee representative.Responsibility of employee representative1.be responsible to all employees, and reflect the views and status of OHSAS’s operation to management representative or general manager.2. acquire the OHSAS’s satisfaction of employee and relevant party, communicate and advise timely.General Manager:2015.1.101.1 Policy:Quality first and treat the customer as supremacy; Full participation and continuous improvement.Safety first and precaution crucial; Law-abiding and anti-consumption.What’s said above is that providing the best quality to customers efficiently/fast/timely, though continuous improvement&anti-consumption&law-abiding.1.2 Objective:A:Customer satisfaction ≥85%B:Scarp rate ≤1%C:Reduce the consumption of resourceD:The noise and waste water will meet the standardE:Prevent and reduce the impact of environment by civilized services and beautify environment, so that meet the requirement of standardF:Safety first and precaution crucial, improve OHS’s conditions and eliminate or reduce the OHS’s risk of staff & relevant party. Completely eradicate any fire-accident or major accident, the rate should be ≤0.2% G:Observe the laws/regulations/other requirements of nation or localAlso, we are looking forward to strengthening cooperation about environment&safety with our suppliers and customers.This policy is applicable to entire company and other designated agents.Promise:We should satisfy customers’requirement by high-quality goods and best service. All employees should understand the policy and objective and requirement, and strengthen the consciousness of quality and environment safety, should strictly implement relevant regulations so that ensure the quality of goods and service.General Manager2015.1.10XXXXXX有限公司、XXXXXX科技有限公司、XXXXXX技术有限公司are located in the center of JIANGSU,ZHEJIANG,SHANGHAI, the north shore of Hangzhou Bay sea-crossing Bridge, relying on the 1-hour economic circle, and nearby SHANGHAI,HANGZHOU,SUZHOU,NINGBO and other cities. The transportation is very convenient.Haiyan Hama Hardware is created in 2002, it covers 5000 M2 and adds 33333 M2 in 2009.The company engages in the production/sale/trade of stamp parts,C type steel,spring nut, C type fastening parts,molds.The address is below:XXXXXXXXXXXXXXXXXXXXXXXXXXXXXXXXXXXXXXXXX mainly engages in engineer consulting, developing and other services, and the production/sale/trade of industrial bracket, solar energy bracket, steel structure etc.We have advanced stamp forging equipments, best management system and exquisite process to ensure the stability of product quality. We have professional design team to design new products to meet customers’needs. We are at the leading position in the peer and our products are praised by all customers which exported to Europe, Mid East, Southeast Asia and other countries.Quality, integrity, pioneering and innovative are the purposes of our company, and we adhere the policy of Quality first and treat the customer as supremacy; Full participation and continuous improvement to provide customers with the newer, more accurate and better quality products.We would like to make friends with people all over the world, let’s create a better future together.Spring NutMterial( Wire PackageChannelSaw WeldMaterial Shaping Burring Punch Galvanize Package Ship FittingMaterial Cut Saw Stamp Galvanize Package ShipWeld BurringShip1.Scope1.1Generala) This manual demonstrates the ability to consistently provide product that meets customer and applicable statutory and regulatory requirementsb)Enhance customer satisfaction and achieve environment and occupational health&safety through the effective application of the system, including processes for continual improvement of the system and the assurance of conformity to customerc)Accord with the policy which is declared through the effective implementation and improve the system, and show the conformity to outside.1.2 QEO Manual is the programmatic document of the management system, it clarifies as follows:a) the scope of system, including any excisions and the rationalityb)including all the processes and cites that work out the documents required by management systemc)the interaction description among the processes of the QEO management system1.3Applicable scopea)Quality system: All the management behavior and process in productionb)Environment system: All the management behavior and process in production located No.388 North Zhenzhong Road,Shendang Haiyanc) All the management behavior and process in production located No.388 North Zhenzhong Road,Shendang Haiyan1.4ExcisionThe products are based on the enterprise standard: Q/YHM01-2013(Q330424J13.1188-2013)and Q/YHM02-2013(Q330424J13.1406-2013), and it doesn’t involve the design and development of new products. But it doesn’t affect the company to provide products to customer, so slash the article of 7.3ISO9000:2005 《Quality management systems Fundamentals and vocabulary》ISO9001:2008 《Quality management systems Requirement》ISO14001:2004 《Environmental management systems Requirements with guidance for use》ISO14004:2004 《Environmental management systems General guidelines on principles, systems and supporting techniques》OHSAS18001:2007 《Occupational health and safety management systems Requirements》ISO19011:2011 《And (or) guidelines for quality and environmental management system auditing》All the terms and definitions are based on the standard of ISO9001:2008, ISO14001:2004, OHSAS18001:2007.3.1 QEO management system: Short for Quality, Environment, Occupational health and safety.3.2 Continual improvement: The organization shall continually improve the suitability, and effectiveness of the environmental management system based on the policy to enhance environmental performance3.3 Environment: Surroundings in which an organization operates including air, water, land, natural resources, flora, fauna, humans and their interrelations3.4 Environment aspect:Element of an organization's activities or products or services that interacts or can interact with the environment3.5 Environment impact: Change to the environment, whether adverse or beneficial, wholly or partially resulting from an organization's environmental aspects3.6 Significant environment aspect: The aspect can or maybe result from an important environmental impact3.7 Objective: Objective set by the organization consistent with the environmental policy/in terms of OH&S performance, that an organization sets itself to achieve, Objective should be quantified wherever practicable.3.8 Environment performance: performance related to the management of environmental aspects3.9 Environment policy: intentions and direction of an organization related to environmental performance, it provides the scheme for the establishment of behavior and objective and target.3.10 Environment target: Come from environment objective, or the detail requirement to achieve the environment obj ective, it’s applicable to whole organization or partly,target should be quantified wherever practicable.3.11 Interested party: person or organization that can affect, be affected by, or perceive itself to be affected by a decision or activity3.12 Prevention of pollution:reduce or control any type of pollutant, use of processes , practices, materials, products,can include process changes, efficient use of resources, material and energy substitution, recycling.3.13 Incident: events in which in injury or ill health or fatality occurred, or could have occurred.3.14 Hazard: source, situation, or act with potential for harm in terms of human injury or ill health, or a combination of these3.15 Major hazard: the hazard cant be accept or is prohibited after identification3.16 Nonconformity: can be any deviation from relevant work standards, practices, procedures, legal requirements etc. Directly or indirectly result from in injury, property loss etc.3.17 Risk: combination of the likelihood of an occurrence of a hazardous event3.18 Risk assessment: process of evaluating the risk and deciding whether or not the risk is acceptable. 3.19 Safety: eliminate the situation of unacceptable risk3.20 Ill health: Diseases caused by exposure to occupational hazards by a work activity or work-related situation3.21 Environment measure: process of measuring the characteristic related to its operation that can havea significant environment impact.3.22 Environment monitor: process that qualitative check the objective, target and legal requirements when cant be measured the characteristic related to its operation that can have a significant environment impact.3.23 OHS measurement: process of measuring the characteristic related to the OHS performance that’s quanitative3.24 OHS monitoring: process of monitoring the characteristic related to the OHS performance that’s qualitative3.25 Hazardous waste: substances of highly toxic, explosive, radioactive, radiation and infectious may be harmful to the surrounding or human health.3.26 Recyclable waste: non-hazardous waste from normal producing activity and life activity, and part can be recycle, such as the packaging material, fitting, maintain material which can be fixed.The organization shall establish, document, implement and maintain this management system and continually improve its effectiveness in accordance with the requirements of the ISO9001, ISO14001 and OHSAS18001.As follows:a)determine the processes needed for the system and their application throughout the organizationb) compile procedure, WI in accordance with the processes, to determine the sequence and interaction of these processes and the method of process controlling, ensure the operation effectivec) ensure resources and information necessary to support the operation and monitoring of these processesd) measure, monitor, analysis these processes in accordance with the responsibility and proceduree) achieve planned results through control the process implementationf) implement actions necessary to continual improvement of these processesThese processes shall be managed by the organization in accordance with the requirements of this Standard. Any outsource processes for HEAT and GALV ANIZE are controlled according to requirements of Purchasing control, and implement appropriate document of level-ⅡorⅢ4.1.1 QEO are kept separate from four processes: management activities, provision of resources, product realization, measurement, analysis and improvement, and this four processes further identify subprocess, all above processes are applicable to PDCA4.1.2Description the sequence and interaction of management activities, provision of resources, product realization, measurement, analysis and improvement4.2 Documentation requirements4.2.1 General4.2.1.1 The system documentation shall includea)documented statements of a management policy and management objectivesb) management manualc) documented procedures and records required by this systemd)documents and records that determined by the organization to ensure the effective planning, operation and control of its processes4.2.1.2 Company plans all the documents according to the QEO management system to make up a complete system, and describe the system from different side and level to the effective operation and continual improvement4.2.1.3 Administration compile <QEO management manual> and procedure document, should concern any aspects of company scale, process complication and employee competence to ensure all the documents are consistent and practicability and operational. A document can include the requirements of one or more procedure. A documented requirement of procedure also could be included several documents.4.2.1.4 QEO is dynamic and should change according to the change from outside or inside, keep suitabilityand effectiveness and adequacy.4.2.2 QEO management manual4.2.2.1 <QEO management manual> is the programmatic document that planned by management representative, compiled by administration, approved and issued by general manager.4.2.2.2 QEO management manual includes:a) the scope of QEO management system, including details of any deletion of the ISO9001:2008 and justification for any exclusionsb) the documented procedures established for the management system, or reference to themc)a description of the interaction between the processes of the management system4.2.2.3Implementation of the manual should maintain continuity and stability, when the manual content is not appropriate, it should be amended timely by administration.4.2.3 Control of documentsAdministration is the department of document controlled, and control all the document required by the QEO system, set document compilation, review, approval, issuance, use, change; recognition of current revision status, re-approval, number, recycle and cancel, recognition and distribution of external document.4.2.3.1 document compilation, review, approvala) <QEO management manual> compiled by administration and issued after approval from general managerb) procedures compiled by administration and issued after approval from general managerc)support management documents, WI(including technical documents, operation, inspection standards) and other documents are compiled by the functional departments and issued after approval from general manager4.2.3.2 Review and update of documentsThe applicability of documents(<QEO management manual>&procedure&WI&other documents) are reviewed and updated when the organization, working process, applicable laws and regulations are changed, and implement after approval from general manager4.2.3.3 document changesa) identify the changes and the current revision status by using the document control list and change recordsb) to ensure the availability of current version of the document by changing, replacing, recycling, etc.4.2.3.4 document number and releaseThe document should be numbered in order to ensure that the relevant versions of the applicable documents can be obtained in use, Issued by administration, Number and register when distributing, fill in <Document Distribute&Recycle records>.The documents distributed into company or QEO management documents are controlled, the distribution number is the control number and stamped with "controlled" chapter. The copy of the document is also stamped with "controlled" by administration.4.2.3.5 document use and managementThe department or person of using the documents are responsible for the management of documents, prevent the loss or damage of the document, to ensure documents remain legible and readily identifiable.4.2.3.6 administration is responsible for identification of external documents, and according to the need to determine the release scope of management system and operation documents, and the documents are issued and distributed according to <document control procedures> approved by the general manager4.2.3.7 document recycle and obsoleteObsolete or expired documents are recycled by administration, and destruct after the approval of the management representative. As the accumulation of knowledge as data storage failure file, the retain department apply and stamp "scrap" chapter after approval of administration manager.4.2.4 record controlAdministration is responsible for the record control,to define the controls for the identification, storage, protection, retrieval, retention and disposition of records.4.2.4.1 record numberRecords are numbered by administration. Table formats are numbered according to<record control procedures>. The picture from activities of QEO management should be numbered on the package as below name, content, production time, the producer and other related information.4.2.4.2 record form releaseThe administration is responsible for the release of the record form to each departments, and fill in the < summary of records >.4.2.4.3 record filledAll departments establish and maintain records of ISO9001:2008, ISO14001:2004 and OHSAS18001:2007 standard requirements and system documentation requirements, to provide evidence of the effective operation and compliance with the requirements. All records should be clear, complete. And the data, information should be adequacy, all records should be timely and no forgery.4.2.4.4 records collection and storageEvery department is responsible for the collection and summary of records, keep the records according to the limit time, and keep away from moisture and moth, anti-deterioration, loss prevention.4.2.4.5 record lendLend records must be approved by administration, and handle relevant procedures in the <document copy& loan record>. The borrower shall take good care of the record, keep it complete and clean,and return it timely 4.2.4.6 record disposeRecords are kept three years generally, except for special records. The expired records should be destroyed by administration, in the meantime should fill in the <document destruction record>, The records which have the value of long term preservation should be sealed after the approval of administration4.3 related documents<Document control procedure><Record control procedure>5.1Management commitmentGeneral manager shall provide evidence of its commitment to the development and implementation of the quality management system and continually improving its effectiveness as follows:a) communicating to the company the importance of meeting customer as well as statutory and regulatory requirementsb) establishing the QEO policyc) establishing quality objectives, environmental objectives and targets, and occupational health and safety objectives and indicatorsd) take charge of the audit at the planned time, and evaluate the suitability, adequacy and effectiveness of the QEO management systeme) provide adequate resources, including human resources, financial resources, infrastructure and work environment to ensure the effective operation of QEO management system5.2 interested party requirements5.2.1 customer focusa) general manager must follow the principle of customer focus, then organize relevant departments to recognize and identify customer needs and expectations through market research or communicate directly to customer, and then convert them to specific requirements (including the requirements of product, process, service), and communication in the whole company.b) general manager is responsible for the approval of the major contract, and take initiative to understand any information about customer requirements through analyzing market research, understand current and future needs from customers, and meet their requirements, and strive to exceed customer expectations.c) notification of risk sources and control measures to the customers who enter company's production area, and exert the influence to reduce the safety risk.5.2.2 other interested party requirementsIdentify requirements of other interested parties, including environmental and occupational health and safety requirements of government, employees and their families, contract, visitor, surrounding to reduce environmental hazards and occupational safety and health damage. At the same time, have the interested parties understand will result in the environmental impact and occupational health and safety impact so that regulate their behavior.5.3 QEO policyThe general manager is responsible for establishing and approving QEO policy, and to ensure that it meets the following requirements:a) appropriate to the purpose of the organization, and suitable for the company's activities, product characteristic, scale and environmental and occupational health and safety;b) commitments of meeting requirements, pollution prevention, prevention of hazard, compliance with laws and regulations and continually improving tis effectivenessc) provide a framework for planning and evaluating the QEO objective;d) document it, implement it, maintain it and communicated it to all employeese) review for continuing suitability when internal and external environment changes5.4 planning5.4.1 Quality ObjectivesGeneral manager shall ensure that quality objectives, including those needed to meet requirements for product, are established at relevant functions and levels within the organization. The quality objectives shall be measurable and consistent with the quality policyThe quality objective is in Chapter 0.3Administration is responsible for the measurement of the objective implement, and other departments are responsible for the measurement of department objectives implement at the planned time.5.4.2 objective and target5.4.2.1 general manager shall establish the objective and targets of environment and occupational health&safety at relevant functions and levels within company .5.4.2.2 environmental objectives and targets, occupational health and safety objectives and indicators are measurable and consistent with the QEO policy. The establishment of objectives and targets should consider the followings:a) applicable laws, regulations and other requirementsb) significant environmental aspects, the risk of hazard and the statusc) optional technical pland) financial, operational requirementse) opinions from interested party5.4.2.3 objectives and targets should be in compliance with QEO policy and include the commitment of pollution prevention and continuous improvement.5.4.2.4 quality objectives, environmental objectives and targets, occupational health and safety objectives and targets shall be reviewed in accordance with planned arrangements, and if necessary to be updated.5.4.3 environmental / occupational health and safety management program5.4.3.1 Administration is responsible for organizing and maintaining the environment / occupational health and safety management program to achieve the company's policy.a) responsibility and authority gave to relevant departments in order to achieve the objectives and targetsb) the schedule and method to achieve the objectives and targets5.4.3.2 The environmental / occupational health and safety management program should be reviewed at least one time a year. If necessary, should revise the environmental / occupational health and safety management program for new projects or company's activities, products, services and operating conditions, to ensure its adaptability.5.4.4 Management system planningGeneral manager ensure to plan the QEO management system, ensure below:a) QEO management system meets the requirements of quality objectives, environmental objectives and targets, occupational health and safety objectives, and identify all processes and follow the process model of PDCAb) should plan firstly, then implement when changes to the QEO management system are planned and implemented to ensure the integrity of the quality management system is maintained.5.4.4.1 Plan timeIn the following situations, general manager shall plan the management system:a) when establish and improve the management systemb)when changes to company policy, objectives, organizational structurec)when company's resource allocation, the market are changed significantlyd) when product type, enterprise scale are changede) when relevant laws and regulations are changedf) when received major complaints from interested partyg) when internal audit or management review require;h) when some special items are not included into the existing system5.4.4.2 Plan contentThe general manager shall ensure that the resources and processes needed to achieve the objectives are identified and planned:a) develop corresponding target according to QEO policyb) recognize the process and relationship of achieving quality objectives, environmental objectives and targets and occupational health and safety objectives, and make clear provisions of these processes and control them, including permitted exclusions and rationalityc) required resources;d) responsibilitye) continuous improvement of QEO management system5.4.4.3 plan outputThe output of plan is in accordance with the management system contents, to direct the establishment and change of entire management system. And lead to changes of other levels including the management manual.5.4.5 Identification, evaluation and updating of environmental aspects5.4.5.1 Administration organizes every departments to collect information of production process, infrastructure, monitoring and measurement, raw materials, equipment update and the whole process of maintenance, packaging, product and service in accordance with the <environmental aspects identification, evaluation and update procedure> , determined the aspects that can interact and exert the effect.5.4.5.2 identification of environmental aspects should mainly consider three Tenses (past, present and future), and three states (normal, abnormal and emergency), seven types (the atmospheric emissions, wastewater emissions, soil waste, soil pollution, resources and energy utilization, noise, other problems to local area and social), two sides (environmental pollution, ecological destruction and reasonable use of resources).。