第2章 裂解气分离
化学工艺学课后习题及答案
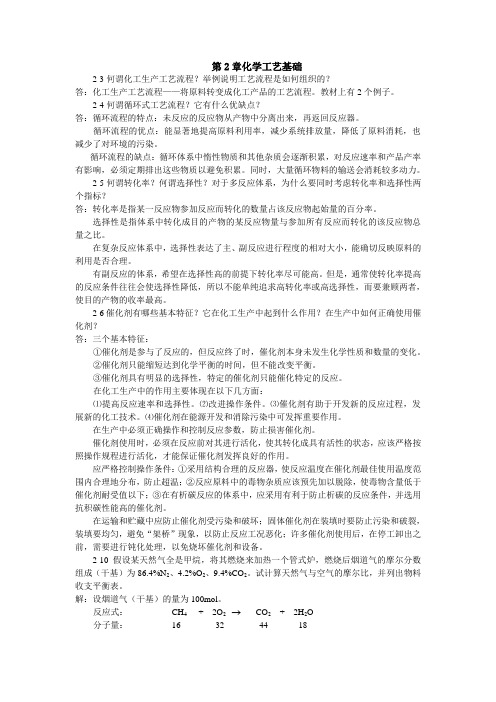
第2章化学工艺基础2-3何谓化工生产工艺流程?举例说明工艺流程是如何组织的?答:化工生产工艺流程——将原料转变成化工产品的工艺流程。
教材上有2个例子。
2-4何谓循环式工艺流程?它有什么优缺点?答:循环流程的特点:未反应的反应物从产物中分离出来,再返回反应器。
循环流程的优点:能显著地提高原料利用率,减少系统排放量,降低了原料消耗,也减少了对环境的污染。
循环流程的缺点:循环体系中惰性物质和其他杂质会逐渐积累,对反应速率和产品产率有影响,必须定期排出这些物质以避免积累。
同时,大量循环物料的输送会消耗较多动力。
2-5何谓转化率?何谓选择性?对于多反应体系,为什么要同时考虑转化率和选择性两个指标?答:转化率是指某一反应物参加反应而转化的数量占该反应物起始量的百分率。
选择性是指体系中转化成目的产物的某反应物量与参加所有反应而转化的该反应物总量之比。
在复杂反应体系中,选择性表达了主、副反应进行程度的相对大小,能确切反映原料的利用是否合理。
有副反应的体系,希望在选择性高的前提下转化率尽可能高。
但是,通常使转化率提高的反应条件往往会使选择性降低,所以不能单纯追求高转化率或高选择性,而要兼顾两者,使目的产物的收率最高。
2-6催化剂有哪些基本特征?它在化工生产中起到什么作用?在生产中如何正确使用催化剂?答:三个基本特征:①催化剂是参与了反应的,但反应终了时,催化剂本身未发生化学性质和数量的变化。
②催化剂只能缩短达到化学平衡的时间,但不能改变平衡。
③催化剂具有明显的选择性,特定的催化剂只能催化特定的反应。
在化工生产中的作用主要体现在以下几方面:⑴提高反应速率和选择性。
⑵改进操作条件。
⑶催化剂有助于开发新的反应过程,发展新的化工技术。
⑷催化剂在能源开发和消除污染中可发挥重要作用。
在生产中必须正确操作和控制反应参数,防止损害催化剂。
催化剂使用时,必须在反应前对其进行活化,使其转化成具有活性的状态,应该严格按照操作规程进行活化,才能保证催化剂发挥良好的作用。
裂解气分离设计范文

裂解气分离设计范文裂解气分离设计是一种常见的化工过程,用于将原料气体进行分离和提纯。
该过程主要用于石油化工工业中,在裂解炉中对重质石油化工原料进行热裂解,生成炼油气等多种气体组分,然后通过分离和提纯过程,将所需的各种气体分离出来。
裂解气分离设计的关键步骤包括原料气体的预处理、主分离过程和后处理过程。
其中,原料气体的预处理是为了去除杂质和调整气体组分的组成,以满足下一步的分离要求。
该步骤通常包括氢气、烯烃、硫化氢和一氧化碳等气体的除去,并根据具体工艺要求,调整气体组分的比例。
主分离过程是指将原料气体中的不同组分进行有效分离的过程。
常用的主分离技术包括吸收、膜分离、吸附和蒸馏等。
吸收是指通过溶剂将原料气体中的特定组分吸收到液相中,从而达到分离的目的。
常用的溶剂包括乙二醇、N-甲基吡咯烷酮和脱氟溶剂等。
膜分离是通过选择适当的膜材料,根据不同气体分子的大小和极性差异,使其通过膜的速率不同,从而实现分离。
吸附是指利用吸附剂的亲和性差异,将原料气体中的特定组分吸附到固体表面上,然后通过调整吸附条件,使吸附剂释放出被吸附的组分。
蒸馏是利用原料气体中各组分的沸点差异,通过加热和冷凝的方式,将各组分逐一分离出来。
后处理过程是指对分离出来的气体进行进一步净化和提纯的过程。
常见的后处理技术包括冷却凝结、压缩和吸附等。
冷却凝结是将气体通过冷却和压缩,使其凝结成液体,然后通过重力分离或离心分离的方式,将液体与气体分离。
压缩是将气体通过增加压力,使其体积减小,从而使其中的杂质浓度增加,然后通过吸附或冷却凝结的方式将杂质去除。
吸附是通过在固体表面上吸附分子的方式,将气体中的杂质吸附到固体表面上,从而净化气体。
裂解气分离设计的关键是选择合适的分离技术和优化操作条件。
在选择分离技术时,需要考虑气体组分的差异和目标分离效果,并综合考虑经济性、操作简便性和安全性等因素。
优化操作条件可以通过调整温度、压力、流量和各组分的比例等参数,以达到最佳的分离效果和经济效益。
第2章生产单体的原料路线2

加拿大 1752 11.91 348 221
伊朗 1370 9.31 425 185
伊拉克 1150 7.82 264 69.4
•石油用途很广,其需要经过加工制成各种产品 才能满足各种需求。
第2章生产单体的原料路线2
• (2)石油炼制工业
•指原油经石油炼制加工得到单体及其他石油产品的工业。
•石油炼厂主要生产装置:
第2章生产单体的原料路线2
•第二节 从石油和天然气获得的石油化工原料路线
•1. 石油的组成及炼制 •(1)石油(原油)的组成
• 石油主要存在于地球表面以下的一种有气味的从黄色到黑
色的粘稠液体, 比水轻(密度大约在0.75~1.0),不溶于水。 • 主要为:碳、氢两种元素所组成的各种烃类混合物(C: 83%~87%。H:11%~14%),并含有少量的含氮、含硫、 含氧化合物。 •石油中的化合物分:烃类、非烃类以及胶质和沥青三大类。
• 5. 有机硅聚合物 • 所需单体:甲基硅氧烷。
• 6. 酚醛树脂 • 所需单体:甲醛、苯酚。
• 7. 脲醛树脂 • 所需单体:甲醛、尿素。
• 8. 环氧树脂 • 所需单体:双酚A、环氧氯丙烷。
• 三. 溶剂 • 1. 烃类溶剂 • 如:加氢汽油、己烷、抽余油。
第2章生产单体的原料路线2
• 2. 芳香族溶剂 • 如:甲苯、二甲苯。
•一些石油裂解装置的主要作用:
•裂解炉:裂解反应在管式裂解炉中进行。为减少副反 应,提高烯烃收率,液态烃在高温裂解区的停留时间 仅0.2~0.5秒。
•急冷锅炉:将800℃的裂解气用水冷却,同时水被加 热成高温高压的水蒸气,作为驱动汽轮和压缩机透平 (涡轮:透平是英文turbine的音译)的动力使用(即 回收能量),同时停止裂解反应。
吴元欣版反应工程答案解析

第一章 例题与习题解答例1每100 kg 乙烷(纯度100%)在裂解器中裂解,产生45.8 kg 乙烯,乙烷的单程转化率为59%,裂解气经分离后,所得到的产物气体中含有4.1kg 乙烷,其余未反应的乙烷返回裂解器。
求乙烯的选择性、收率、总收率和乙烷的总转化率。
解:以B 点的混合气体为计算基准进行计算即得到单程转化率和单程收率,而以对A 点的新鲜气体为计算基准进行计算得到全程转化率和全程收率。
新鲜原料通过反应器一次所达到的转化率,单程转化率(反应器进口为基准);新鲜原料进入反应系统起到离开系统止所达到的转化率,全程转化率(新鲜原料为基准)。
现对B 点进行计算,设B 点进入裂解器的乙烷为100 kg 。
新鲜乙烷产品由于乙烷的单程转化率为59%,则在裂解器中反应掉的原料乙烷量为1000.5959H kg =⨯=E 点乙烷的循环量100 4.110059 4.136.9Q H kg =--=--=A 点补充的新鲜乙烷量为10010036.963.1F Q kg =-=-=乙烯的选择性为45.8/2845.8/28100%100%83.172%/3059/30S H =⨯=⨯=乙烯的单程收率45.8/28100%49.07%100/30y =⨯=乙烯的总收率(摩尔收率)45.8/2845.8/28100%100%77.77%/3063.1/30Y F =⨯=⨯= 乙烯的总质量收率'45.845.8100%100%72.58%63.1Y F =⨯=⨯= 乙烷的总转化率 %.%.%59310016359100===⨯⨯F H X 例2工业上采用铜锌铝催化剂由一氧化碳和氢合成甲醇,其主副反应如下:OH CH H CO 322⇔+ ))(O H O CH H CO 223242+⇔+ O H CH H CO 2423+⇔+ O H OH H C H CO 2942384+⇔+222H CO O H CO +⇔+由于化学平衡的限制,反应过程中一氧化碳不可能全部转化成甲醇。
第二章乙烯生产工艺简介

项目 石脑油 乙烷 丙烷 1995 52.4 27.6 9.4 2000 52.2 28.0 10.0 柴油 丁烷 其它 1995 6.3 3.3 1.0 2000 6.3 2.8 0.7
目前世界乙烯原料结构中,石脑油仍占主要地位,2003年 全球乙烯原料结构:石脑油 47.5%、轻烃 36.3%、柴油 4.6%、 其他 11.6%。
17
2. 加氢和脱氢
烯烃可以加氢成饱和的烷烃,例如:
C2H4+H2 C2H6 反应温度低时,有利于加氢平衡。 烯烃也可以进一步脱氢生成二烯烃和炔烃,例如: C2H4 C2H2+H2 CH3CH=CH2 CH3C≡CH+H2 CH3CH2CH=CH2 CH2=CH—CH=CH2+H2 从热力学分析,烯烃的脱氢反应比烷烃的脱氢反应推动 力更小,故需要更高的温度。
裂解炉及急冷换热气的操作指标见表1及表原料项目煤柴油乙烷反应管出口温度765820反应管入口温度600600反应管出口压力atm078107078107反应管内压力降atm1717停留时间秒04510蒸汽稀释比w075030急冷换热气工艺指标裂解原料出口温度535380停留时间秒005发生的蒸汽压力atm8686从裂解气中分离出燃料油及裂解气油部分裂解气经急冷油喷雾急冷至190后进入初分馏塔塔底分出燃料油裂解重油送至稀释蒸汽发生器利用其热量发生7kgcm表压的稀释蒸汽本身被冷却后一部分作为急冷油循环进入油急冷器使用另一部分作为急冷油被掺入塔底急冷油中以降低油的粘度抽出量由塔中段的液面控制其余部分作为燃料油送出系统外
聚合物合成工艺学第2章生产单体的原料路线

CH2
CH2
+CH2
CH
CH2
+Cl2+O2
CH2Cl
CH2Cl
CH2
CHCl
+CH3COOH+O2
CH2
CH
OOCCH3
聚乙烯 乙丙橡胶
聚氯乙烯 聚乙酸乙烯酯
聚乙烯醇
+C6H6 AlCl3
C2H5
C6H5 -H2
CH2
维纶树脂
CH
C6H5
聚苯乙烯 ABS树脂 丁苯橡胶
O2
CH2
CH2
O
CH2
OH
CH2
➢ 矿产资源是不可再生的。
2-2 石油化工路线
石油化工路线
原油
石油炼制得
炼厂气和 汽油、石脑油、
煤油、柴油 高温裂解 等馏分
裂解气
分离
乙烯、 丙烯、丁烯、
丁二烯等
液体
加氢后
芳烃
催化重 整
萃取 分离
苯、 甲苯、二甲苯等
芳烃化合物
原油
石油
从油田开采出来未经 加工的石油称为原油
性质: 褐红色 至黑色 的粘稠 液体。 比水轻 不溶于水
不饱和聚酯树脂 聚芳酰胺
于DMF中进入第一汽提塔与溶剂DMF分离。
粗丁二烯气体经压缩液化送入第二萃取蒸
馏塔(塔3),一部分则回第一萃取蒸馏塔。 在塔 (3)中丁二烯被馏出进入塔 (5)进行第一
次精馏。脱除了甲基乙炔的丁二烯,再进
入塔 (6)进行第二次精馏,塔顶得精丁二烯, 塔底高沸点物为顺丁烯-2,丁二烯-1,2, 乙 剂基DM乙F炔中、含C有5馏一分部等分。丁塔二(烯3)和底乙部烯流基出乙的炔溶, 送入塔 (4)以回收丁二烯。含有乙烯基乙炔 的DMF经精制后回收DMF。
第二章烃类热裂解反应
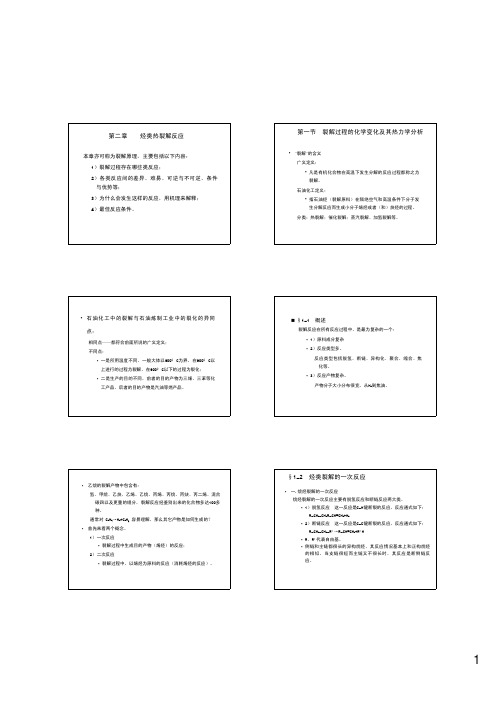
:,Dβ=289.8k J/m o l,而烷的容易程度按下列顺序递增:烷烃的C-C键<双键β位置的C-和反应过程的标准吉布斯函准吉布斯函数变,简称标衡常数。
——化合物i 在化学反应中的化学计量系数;化合物i 的标准生成吉布斯函数,k J /m o l ;度的函数:=A +B T +C T 2+D T 3、C 、D 为计算系数。
几种烃的计算系数见教材52页表2-1。
得,示反应达到平衡时成物愈占率越高,反应可能向向进行而若是正值,并负值的情若时就可以第二节裂解反应机理和动力学规律•§2-1自由基链反应机理一.乙烷的自由基链反应机理•首先从裂解过程最简单的乙烷脱氢生成乙烯的反应谈起。
C2H6→C2H4+H2•该反应式只是说明了从什么反应物分子,按什么计量关系,最后生成什么产物分子。
但这个反应式仅给出了总的反应结果,并不说明反应进行的途径。
说道这里我们不禁要问:是不是乙烷分子中两个C-H键断裂而脱下就生成乙烯分子哪?还是通过生成其他的中间物质,经过几步才生成乙烯哪?乙烷的裂解反应的三个阶段:如表中数据所示,乙烷中C-C键的解离能是88.0k c a l/l,而C-H键的解离能是98.0k c a l/m o l,所以乙烷的引发是C-C键的断裂引起的。
第二阶段是链增长反应,又称链传递反应或链转移反应就是自由基与分子反应,生成目的产物及新的自由基的程。
第三阶段是链终止反应。
如果链增长阶段不受阻碍的继链反应长度L c h在乙烷裂解中:随着温度的上升链长度是减小的,但乙烯的生成对于乙烷的分解的相对速度仍是一个很大的数值。
而且从各个基元反应的速度常数看乙烷引发反应的k11远小于其主基元反应的k33、k44、k55。
乙烷的引发反应是整个反应的控制步骤,而随着温度的上升,k比k33、k44、k55增大的倍数要大的多,所以提高温度对提高整个反应速度是有利的,此时链长度仍是很大的数值。
1.烃类在裂解时的几条规律1.烃烃分子中不同位置氢原子与自由基的反应速度不同,其反应途径也不同。
第2章 烃类热裂解
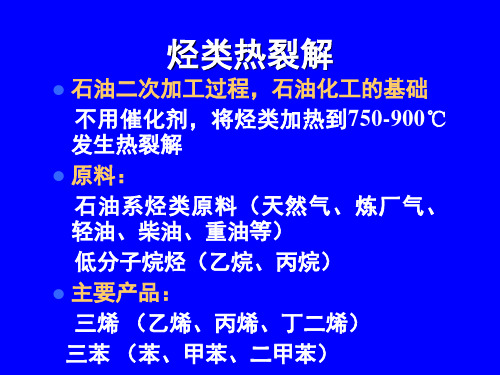
烯烃在裂解条件下继续反应,最终生成焦或炭
烯烃裂解成较小分子烯烃 烯烃加氢生成饱和烷烃 烃裂解生成炭 烯烃聚合、环化、缩合和生焦反应
2.3 裂解反应的热力学 和动力学
2.3.1 裂解反应的热力学分析
裂解反应的热效应
强吸热过程
基尔霍夫公式:
根据裂解反应器的实际进出口
温度计算反应器的热负荷
异构烷烃裂解规律
比正构烷烃容易裂解或脱氢 脱氢能力与分子结构有关,难
易顺序为叔氢>仲氢>伯氢
随着碳原子数的增加,异构烷
烃与正构烷烃裂解所得乙烯和 丙烯收率的差异减小
异构烷烃
主要产物:氢、甲烷、乙烯、丙烯、C4烯烃 特点:
异构烷烃裂解所得乙烯、丙烯收率远较正
构烷裂解所得收率低,而氢、甲烷、C4及
2.1 热裂解过程的化学反应
2.1.1 烷烃
脱氢反应 :
CnH2n+2
断链反应 :
CnH2n+H2
(C—H键断裂 )
CnH2n+2
CmH2m+ CkH2k+2
m+k=n
正构烷烃裂解规律
相同烷烃断链比脱氢容易 碳链越长越易裂解 断链是不可逆过程,脱氢是可逆过程 在分子两端断链的优势大 乙烷不发生断链反应,只发生脱氢反应生成 乙烯,甲烷在一般裂解温度下不发生变化 主要产物: 氢、甲烷、乙烯、丙烯 特点: 生产乙烯、丙烯的理想原料
ArH+CnH2n Ar-CkH2k+1+CmH2m
Ar-CnH2n+1
Ar-CnH2n-1+H2
芳烃缩合反应
R1
R2
R3
+
- 1、下载文档前请自行甄别文档内容的完整性,平台不提供额外的编辑、内容补充、找答案等附加服务。
- 2、"仅部分预览"的文档,不可在线预览部分如存在完整性等问题,可反馈申请退款(可完整预览的文档不适用该条件!)。
- 3、如文档侵犯您的权益,请联系客服反馈,我们会尽快为您处理(人工客服工作时间:9:00-18:30)。
❖节约压缩功耗
段间冷却,节省压缩功 段数多,接近等温压缩
二烯烃易聚合,危及正常操作 温度愈高,聚合速度愈快 控制压、酸性气体、C3及C3以上重组分 减少负荷,节省冷量
原料:轻烃和石脑油 生产能力:68万t/a
段数
Ⅰ ⅡⅢ Ⅳ Ⅴ
进口温度/ ℃ 38 34 36 37·2 38 进口压力/ MPa 0·13 0·245 0·492 0·998 2·028
解决办法
加压 提高组分的沸点 提高操作温度
裂解气压缩
单位 MPa
单位 k
T2
T1 (
p2 p1
) (k 1) /
k
=cp/ cv
绝热过程,压力升高,温度也上升
举例: T2=T1(P2/P1)(-1)/ 绝热指数: =1·228
P1 =0·105MPa 排气温度293℃
P2=3·6MPa
多级压缩
出口温度/ ℃ 87·2 85·6 90·6 92·2 92·2
出口压力/ MPa 0·286 0·509 1·019 2·108 4·125
压缩比
2·0 2·08 1·99 2·11 2·04
裂解气五段压缩工艺参数实例
深冷分离操作中,裂解气压缩常采用往复式 和离心式压缩机,由于裂解炉废热锅炉副产 高压水蒸汽,多用蒸气透平驱动离心式压缩 机,达到能量合理利用。大规模生产厂广泛
制冷剂
蒸发 压缩 冷凝 节流
反复进行,形成一个闭合循环操作过程
单级制冷循环组成
蒸发器 制冷剂吸热蒸发,变成低温低压气体 节流阀 压力、温度降低 冷凝器 制冷剂在冷凝器中冷却冷凝成液体 压缩机 制冷剂由低温低压气体变为高温高压气体
制冷循环
❖实质:通过制冷不断将处于低温的被冷物料的热量传给温度较高的冷水
消耗,又堵塞设备及管道,并影响产物 分离。
脱水方法
常用方法:吸附干燥 常用吸附剂:
分子筛 活性氧化铝 硅胶 工业上常用3A分子筛
低温有利
常用吸附剂比较
分子筛
低相对湿度下,吸附能 力仍较大。
吸附容量受温度影响 小,低温也较大
活性氧化铝
相对湿度>60% 吸附容量>分子筛 相对湿度↓, 吸附容量<分子筛 吸附量受温度影响较大
-140
深冷分离采用经济上合理技术上可行的 压力,一般为3.54~3.95MPa。
压缩净化原则流程图 请自己画出用方框表示的原则流程图。
分离要求
低于环境温 度的深冷温 度条件下进 行
制冷系统
制冷
制冷剂
创造环境空 气、水等
所不能实现 的低温条件
制冷循环中 完成热量转 移的工作介 质
单级制冷循环四个基本过程
烃类与稀释 水蒸汽反应
CO的危害
部分富集于甲烷馏分 部分富集于富氢馏分
❖ 少量的CO带入富氢馏分中,会使加氢催化剂中毒 ❖ 随着烯烃聚合高效催化剂的发展,对乙烯和丙烯
中CO含量的要求也越来越高。
甲烷化法:催化剂存 在的条件下,使裂解 气中的一氧化碳催化 加氢生成甲烷和水, 达到脱除CO的目的
CO脱除的方法
碱 洗 工 艺 流 程 图
碱洗塔
塔的除沫装置
乙醇胺法脱除酸性气原理
MEA DEA为吸收剂 化学、物理吸收结合
乙醇胺法脱除酸性气
特点:吸收剂可以循环使用 工艺组成:吸收、解吸
尝试设计吸收解吸流程
吸收和解吸过程
吸收塔
解吸塔
乙醇胺法工艺
碱洗法与醇胺法比较
碱洗法 适于酸含量低 碱不可再生 碱消耗大 黄油问题 废水处理量大
开来,达到分离的目的
深冷分离
深冷分离过程组成
压缩和 制冷系统
净化系统
精精馏馏分分离离系系统统
压缩和制冷系统
❖ 目的和任务 ❖ 压力、压缩功与冷量的关系 ❖ 多级压缩的优点 ❖ 多级压缩段数的确定 ❖ 制冷剂的选择
❖需要大量冷量和耐低温设备 ❖常压,冷凝、精馏分离温度低 ❖裂解气常压沸点很低
压缩的原因
后加氢
❖ 工艺流程或控制复杂。 需设第二脱甲烷塔或侧 线采出塔
❖ 氢气定量供给,加氢选 择性好,温度较易控制, 不易发生飞温问题
❖ 加氢原料气中杂质少, 催化剂使用周期长,产 品纯度也高。
C2馏分后加氢工艺
脱乙烷塔顶 回流罐C2气
预热、注氢 一段加氢
反应气
冷却 二段加氢
反应气
冷却 C2吸收绿油
C2馏分 干燥
裂解气分离方法
油吸收 精馏分离
❖用 吸 收 剂 吸 收 除 甲 烷 和 氢 气 以 外 的 其 它组分,然后精馏,把各组分从吸收剂 中逐一分离。
❖流 程 简 单 , 动 力 设 备 少 , 投 资 少 , 但 技术经济指标和产品纯度差。
在-100℃左右的低温下,将裂解气中除了氢和 甲烷以外的其它烃类全部冷凝下来。然后利用 裂解气中各种烃类的相对挥发度不同,在合适 的温度和压力下,以精馏的方法将各组分分离
CO
H 2
CH4
H2O
裂解气的深冷分离系统
脱甲烷塔
丙烯精馏
分离流程
乙烯精馏
❖ 深冷分离流程的组织 ❖ 深冷分离流程的评价指标 ❖ 关键设备 ❖ 脱甲烷塔、乙烯精馏塔 ❖ 能量利用 ❖ 中间再沸器、中间冷凝器
经预分馏后裂解气组成
裂解原料 转化率
CO+CO2+H2S H2O C2H2 C3H4 C2H4 C3H6 H2 CH4 C2H6 C3H8
3A
2
3~3.8 2/3K2O·1/3Na2O·Al2O3·2SiO2·4.5H2O
4A
2
4.2~4.7 Na2O·Al2O3·2SiO2·4.5H2O
5A
2
4.3~5.6 0.7CaO·0.3Na2O·Al2O3·2SiO2·4.5H2O
10x 2.3~3.3 8~9 0.8CaO·0.2Na2O·Al2O3·2.5SiO2·6H2O
第二部分 裂解气分离
主要内容
❖ 裂解气的组成与分离方法 ❖ 压缩与制冷 ❖ 气体净化 ❖ 裂解气深冷分离 ❖ 裂解气分离操作中的异常现象
裂解气的组成与分离方法
组成 ❖ 烃类:
CH4、C2H2、C2H4、C2H6、 C3H4、C3H6、C3H8、 C4、C5、C6~204℃馏分 ❖ 非烃类:
H2 、H2O、CO、CO2、H2S
复叠制冷循环
节流膨胀制冷
❖气体由较高的压力通过一个节流阀膨胀到 较低的压力,过程非常快,来不及与外界 发生热交换,膨胀所需的热量必须由自身 供给,从而引起温度降低。
❖生产中,高压脱甲烷分离,可用节流膨胀 获得-110℃
精馏过程
热泵
塔顶需用外来冷剂引入冷量,从塔顶移出热量; 塔釜又要用外来热剂供给热量。
酸性气体的危害
CO2:低温下结成干冰,堵 塞设备管道;
H2S:腐蚀设备管道;使分 子筛寿命降低;造成加氢 脱炔和甲烷化催化剂中毒
使下游聚合或催化反应 的催化剂中毒;在生产 聚乙烯等时造成聚合速 度降低、聚乙烯的分子 量降低;影响产品质量
裂解气分离装置
下游加工装置
酸性气体脱除方法
方法 ❖碱洗法 ❖乙醇胺法
溶剂吸收法
优
脱出裂解气中的乙炔
❖ 乙烯装置的大型化, 裂解温度高, 停留
点
回收到一定量的乙炔
时间短,乙炔增加 ❖ 石脑油为原料的
300 kt/a乙烯装置,
常规裂解回收乙炔
常
丙酮
用
量约6700t/a,毫秒 炉裂解回收乙炔量 可达11500t/a
的
N-甲基吡咯烷酮(NMP)
溶
剂
二甲基甲酰胺(DMF)
催化加氢脱炔
典型的两个吸附器 轮流操作的流程图
炔烃脱除
来源
裂解过程中生成 乙炔集于C2馏分 甲基乙炔和丙二 烯富集于C3馏分
危害
对产品再加工不利, 影响催化剂寿命, 恶化产品质量,形 成不安全因素,产 生副产品
炔烃脱除方法
方法:
❖溶剂吸收法 ❖催化加氢法 要求 ❖乙炔<5×10-5(mol) ❖丙炔< 5×10-5 丙二烯<1×10-5
乙醇胺法 适用酸含量高 吸收剂可再生,消耗少 吸收不如碱洗彻底 设备要求高 吸收双烯烃,再生易聚合
脱水 (干燥)
含饱和水量(600~700)×10-6 要求:水含量(W)降至1×10-6以下
❖ 脱水原因
❖水分在低温下结冰 ❖加压和低温条件下,可与烃生成白色结
晶水合物如:CH4·6H2O,C2H6·7H2O ❖水合物和冰附着在管壁上,既增加动能
乙炔加氢转化为乙烷 的化学平衡常数大于 乙炔加氢转化为乙烯 的反应。
前加氢
在脱甲烷塔前进 行,利用裂解气 中 H2 进 行 选 择 性 加氢,自给氢催 化加氢
加氢工艺
后加氢
裂解气分离出C2、 C3馏分后,对C2和 C3馏分进行催化加 氢,脱除乙炔、甲 基乙炔和丙二烯
前加氢与后加氢比较
前加氢
❖流程简化,节省投资 ❖操作稳定性差。 ❖氢气自给,过量,副 反应剧烈,选择性差, 造成乙烯和丙烯损失, 严重时还会导致反应温 度失控,床层飞温,威 胁生产安全。
裂解气的净化系统
脱酸性气体
脱CO 净化过程
脱炔
脱水
酸性气体的脱除
酸性气体
硫化氢、 二氧化碳 有机硫化物
来源
原料带入 反应过程生成 氧与烃类反应生 成CO2 烃和炉管中的结 炭与水蒸气反应 可生成CO2
来源
硫醇、硫醚、噻吩 等在高温下与氢和 水蒸气反应生成的 CO2和H2S
例如: RSH+H2→RH+H2S
制冷剂的选择
制冷
制冷剂丙烯数据分析
沸点-47.7 ℃ ,临界温度 91.89℃ ; 丙烯单独使用,可以实现被水冷凝, 但不能将被冷物料降温到-100 ℃