裂解气的分馏与净化
石油裂解

石油裂化和裂解在石油化工生产过程里,常用石油分馏产品(包括石油气)作原料,采用比裂化更高的温度(700〜800C,有时甚至高达1000C以上),使具有长链分子的烃断裂成各种短链的气态烃和少量液态烃,以提供有机化工原料。
工业上把这种方法叫做石油的裂解。
所以说裂解就是深度裂化,以获得短链不饱和烃为主要成分的石油加工过程。
石油裂解的化学过程是比较复杂的,生成的裂解气是一种复杂的混合气体,它除了主要含有乙烯、丙烯、丁二烯等不饱和烃外,还含有甲烷、乙烷、氢气、硫化氢等。
裂解气里烯烃含量比较高。
因此,常把乙烯的产量作为衡量石油化工发展水平的标志。
把裂解产物进行分离,就可以得到所需的多种原料。
这些原料在合成纤维工业、塑料工业、橡胶工业等方面得到广泛应用。
定义:裂化(cracking )就是在一定的条件下,将相对分子质量较大、沸点较高的烃断裂为相对分子质量较小、沸点较低的烃的过程。
单靠热的作用发生的裂化反应称为热裂化,在催化作用下进行的裂化,叫做催化裂化。
裂解是石油化工生产过程中,以比裂化更高的温度(700r〜800r,有时甚至高达i000r以上),使石油分馏产物(包括石油气)中的长链烃断裂成乙烯、丙烯等短链烃的加工过程。
裂解(pyrolysis )是一种更深度的裂化。
石油裂解的化学过程比较复杂,生成的裂解气是成分复杂的混合气体,除主要产品乙烯外,还有丙烯、异丁烯及甲烷、乙烷、丁烷、炔烃、硫化氢和碳的氧化物等。
裂解气经净化和分离,就可以得到所需纯度的乙烯、丙烯等基本有机化工原料。
目前,石油裂解已成为生产乙烯的主要方法。
裂化分类:(1)热裂化:热裂化是在热的作用下(不用催化剂)使重质油发生裂化反应,转变为裂化气(炼厂气的一种)、汽油、柴油的过程。
热裂化原料通常为原油蒸馏过程得到的重质馏分油或渣油,或其他石油炼制过程副产的重质油[1]。
在400〜600C,大分子烷烃分裂为小分子的烷烃和烯烃;环烷烃分裂为小分子或脱氢转化成芳烃,其侧链较易断裂;芳烃的环很难分裂,主要发生侧链断裂。
裂解(裂化)工艺简介

19
20
(二)停留时间
1. 停留时间 指裂解原料由进
入裂解辐射管到离 开裂解辐射管所经 过的时间。
6
2.环烷烃裂解的一次反应 原料中的环烷烃可以发生断链和脱氢反应,生成
乙烯、丁烯、丁二烯、芳烃等。 例如环己烷裂解:
C6H12 C6H12
C2H4 + C4H8 C2H4 + C4H6+H2 C4H6 + C2H6 3/2C4H6 + 3/2H2
C6H6+3H2
7
(二)烃类裂解的二次反应
所谓二次反应是在裂解反应条件下,一次反应生成的烯 烃都可以继续反应,转化成新的产物。
裂解(乙烯)工艺简介
第一节 概述 第二节 烃类热裂解 第三节 烃类裂解工艺过程 第四节 裂解气的净化与分离
1
第一节 概述
石油化学工业的发展,促进了国民经济的巨大进步。乙烯、 丙烯、丁二烯(三烯)、苯、甲苯、二甲苯(三苯)等是石油 化工最基本的原料,是生产各种重要的有机化工产品的基础。 所以生产“三烯”、“三苯”的乙烯装置是石油化学工业的龙 头,它的生产规模、产量、和技术标志着一个国家石油化学工 业的发展水平。
24
3. 水蒸汽作为稀释剂的优点 (1)易于从裂解气中分离; (2)水蒸气热容大,使系统有较大“热惯性”,可
以稳定裂解温度,保护炉管; (3)可脱除炉管的部分结焦,延长运转周期; (4)减轻了炉管中铁和镍对烃类气体分解生碳的催
化作用; (5)可以抑制原料中的硫对合金钢管的腐蚀。
裂解气分离与精制工艺流程及其关键设备

1)裂解气顺序分离过程简述
① 压缩净化的裂解气,经过冷箱(9)降至约-37~ -100℃后,分别送到脱甲烷塔(3)相应位置;
② 在脱甲烷塔塔顶分离出H2和CH4(C1馏分)返回冷 箱,塔釜液(C2以上馏分)送至脱乙烷塔(4);(C1 分割)
③ 在脱乙烷塔塔顶分离出C2馏分(乙烷和乙烯混合 物)经加氢脱炔并脱除绿油后,送至乙烯精馏塔 (5),塔釜液送至脱丙烷塔(6);(C2分割)
④ 在脱丙烷塔塔顶分离出C3馏分(丙烷和丙烯混合 物)经加氢脱炔并脱除绿油后,送至丙烯精馏塔 (8),塔釜液则送至脱丁烷塔(7);(C3分割)
⑤ 在脱丁烷塔的塔顶分离出C4混合物送至下一工 段进行加工利用,塔釜液是裂解汽油等产品; (C4分割)
⑥ 最后,在乙烯精馏塔分别得到产品乙烯和乙烷, 乙烷作为原料返回裂解炉循环利用;同样,在丙 烯精馏塔分别得到丙烯产品和丙烷。
分离方法
可采用的 液相分离方法
• 深冷分离法
• 油吸收精馏分离法
• 吸附分离法 • 络合分离法
技术不成熟
• 膨胀机法等等
4.10 裂解气分离与精制工艺流程及其关键设备
裂解气的预分馏及净化
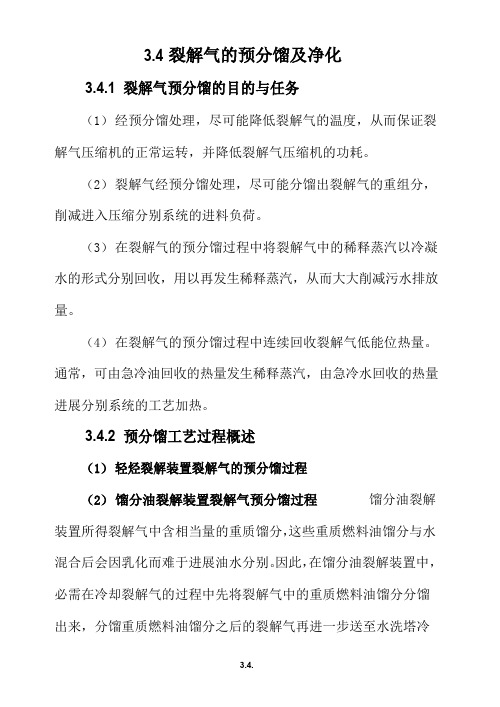
3.4 裂解气的预分馏及净化3.4.1裂解气预分馏的目的与任务(1)经预分馏处理,尽可能降低裂解气的温度,从而保证裂解气压缩机的正常运转,并降低裂解气压缩机的功耗。
(2)裂解气经预分馏处理,尽可能分馏出裂解气的重组分,削减进入压缩分别系统的进料负荷。
(3)在裂解气的预分馏过程中将裂解气中的稀释蒸汽以冷凝水的形式分别回收,用以再发生稀释蒸汽,从而大大削减污水排放量。
(4)在裂解气的预分馏过程中连续回收裂解气低能位热量。
通常,可由急冷油回收的热量发生稀释蒸汽,由急冷水回收的热量进展分别系统的工艺加热。
3.4.2预分馏工艺过程概述(1)轻烃裂解装置裂解气的预分馏过程(2)馏分油裂解装置裂解气预分馏过程馏分油裂解装置所得裂解气中含相当量的重质馏分,这些重质燃料油馏分与水混合后会因乳化而难于进展油水分别。
因此,在馏分油裂解装置中,必需在冷却裂解气的过程中先将裂解气中的重质燃料油馏分分馏出来,分馏重质燃料油馏分之后的裂解气再进一步送至水洗塔冷却,并分馏其中的水和裂解汽油。
3.4.3 裂解汽油与裂解燃料油(1) 裂解汽油烃类裂解副产的裂解汽油 C 至沸点 204O C 5以下的全部裂解副产物,也作为乙烯装置的副产品。
裂解汽油经一段加氢可作为高辛烷值汽油组分。
如需经芳烃抽提分别芳烃产品, 则应进展两段加氢,脱出其中的硫,氮,并使烯烃全部饱和。
(2) 裂解燃料油 烃类裂解副产的裂解燃料油是指沸点在200O C 以上的重组分。
其中沸程在 200-360O C 的馏分称为裂解轻质燃料油,相当于柴油馏分,但大局部为杂环芳烃,其中,烷基萘含量较高,可作为脱烷基制萘的原料,沸程在 360O C 以上的馏分称为裂解重质燃料油,相当于常压重油馏分。
除作燃料外,由于裂解重质燃料油的灰分低,是生产碳黑的良好原料。
3.4.4 裂解气的净化裂解气中含H 2 S 、CO 、H 2 2 O 、C 2 H 、CO 等气体杂质,来源主 2要有三方面:一是原料中带来;二是裂解反响过程生成;三是裂解气处理过程引入。
裂解过程的工艺参数和操作指标
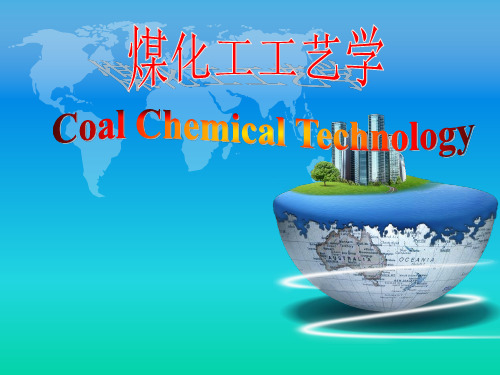
热强度:单位时间内单位炉管表面积传递的热量。 炉管表面热强度越大,则完成相同热任务所需的传热 面积越小。
Chemistry and chemical engineering institute
三、烃分压与稀释剂 1、压力对裂解反应的影响 化学平衡分析
P 总P iP 稀 P 烃
Chemistry and chemical engineering institute
2、稀释剂 目的:降低烃分压。 稀释剂种类:水蒸气、氢气、惰性气体。 优点:设备在常压或正压下操作,安全性高,不
会对以后压缩操作增加能耗。
Chemistry and chemical engineering institute
因此,应选择一个最适宜的裂解温度,发挥一次 反应在动力学上的优势,而克服二次反应在热力 学上的优势,即可得到较高的乙烯收率也可减少 焦炭的生成。
理论上适宜的裂解温度范围750~900℃。
实际T与裂解原料、产品分布、裂解技术和停留 时间等有关。如某厂乙烷裂解炉的裂解温度是 850~870℃,石脑油的是840~865℃,轻柴油的 是830~860℃。
于甲烷较稳定,基本不发生二次反应,可以用来衡 量反应的深度。
Chemistry and chemical engineering institute
(3)乙烯对丙烯的收率y(C2=)/y(C3=) 在一定裂解深度范围内,裂解深度增大,乙烯
收率增高,而丙烯收率增加缓慢,至一定裂解深度 后,丙烯收率由最高值开始下降。 (4)甲烷对乙烯或丙烯的收率比y(C10)/y(C2=)
(6)裂解炉出口温度
生产操作常用Tout 表示裂解深度。
裂解气分离设计(已处理)

裂解气分离设计1 引言1.1裂解气制取乙烯的意义乙烯是基本有机化学工业最重要的产品,它的发展带动着其他基本有机化工产品生产的发展,因此乙烯的产量往往标志着一个国家基本有机化学工业发展的水平。
乙烯生产的发展,使其他基本有机化工产品的生产也有了很大的增长。
并在开发新工艺,新技术,简化生产方法,降低原料单耗,开辟新的原料路线,提供新产品,防治环境污染等方面取得了较大的进展。
轻油裂解制乙烯技术研究始于20世纪30年代,经过60多年的发展,裂解技术日臻成熟,目前世界乙烯产量的98%以上。
与之相应的深分离方法也最为成熟,目前占据世界乙烯市场分离技术主要分为三大类,分别为顺序分离技术、前脱丙烷前加氢技术和前脱乙烷前加氢技术。
烃类经过裂解制得了裂解气,裂解气的组成是很复杂的,其中既有有用的组分,也含有一些有害的杂质。
裂解气的分离的任务就是除去裂解气中有害杂质,分离出单一烯烃产品或烃的馏分,为基本有机化学工业和高分子化学工业等提供原料。
为了得到高纯度的产品,必须对裂解气进行分离裂解技术在继续开发中,主要以下列问题为目标:1扩大重质原料的应用和裂解炉对原料改变的适应能力;2减小能耗,降低成本;3新的裂解技术研究。
降低产品成本是任何一个厂家的总目标,它与管理、产销、工艺技术水平密切相关,新的裂解技术研究有开发耐高温的裂解管材、催化裂解。
1.2流程方案的依据确定设计方案总的原则是在可能的条件下,尽量采用科学技术上的最新成就,使生产达到技术上最先进、经济上最合理的要求,符合优质、高产、安全、低消耗的原则。
为此,必须具体考虑如下几点: ①满足工艺和操作的要求所设计出来的流程和设备,首先必须保证产品达到任务规定的要求,而且质量要稳定,这就要求各流体流量和压头稳定,入塔料液的温度和状态稳定,从而需要采取相应的措施。
其次所定的设计方案需要有一定的操作弹性,各处流量应能在一定范围内进行调节,必要时传热量也可进行调整。
因此,在必要的位置上要装置调节阀门,在管路中安装备用支线。
石油化工工艺学思考题新

化学工艺学复习资料(答案仅供参考)增加部分英语题型专业(词汇)催化裂化,catalytic cracking加氢裂化,hydrocracking延迟焦化,delayed coking凝析油(Natural gasoline)、石脑油(Naphtha)、轻柴油(Atmospheric gas oil)、粗柴油(Vacuum gas oil)、加氢裂化尾油(Hydrogenated tail oil) 苯(Benzene, ),甲苯(Toluene, ),二甲苯(Xylene, );乙烯,ethylene丙烯,propylene丁二烯,butadiene邻二甲苯(Ortho-xylene,)、对二甲苯(Para-xylene,)、间二甲苯(Met-xylene,)聚乙烯,polyethylene;聚氯乙烯,polyvinylchlorid 聚苯乙烯,polystyrene思考题(第一章)1. 茂名石化乙烯出厂化工商品有塑料类、合成橡胶类、液体化工类三大类。
2. 茂名石化工业区内代表性企业有那些?主营业务?a)广东新华粤石化股份有限公司碳九资源综合利用生产基地;b)茂名鲁华化工有限公司建设国内规模最大、技术领先的碳五资源综合利用生产基地;c)广东奥克化学有限公司环氧乙烷精深加工基地;d)茂名石化实华股份有限公司碳四、芳烃精深加工基地;e)广东众和化塑有限公司、茂名市科达化工有限公司等为基础,建设广东最大的化工助剂基地。
3. 我国乙烯工业概况?答:乙烯装置在生产乙烯的同时,副产大量的丙烯、丁烯、丁二烯、苯、甲苯和二甲苯,成为石油化工基础原料的主要来源。
世界上约70%的丙烯、90%的丁二烯、30%的芳烃均来自乙烯副产。
以三烯(乙烯、丙烯、丁二烯)和三苯(苯、甲苯和二甲苯)总量计算,约65%来自乙烯生产装置。
因此,乙烯生产在石油化工基础原料生产中占据主导地位,乙烯工业的发展水平是衡量一个国家和地区石油化学工业发展水平的重要标志。
裂解气的压缩与净化工艺流程
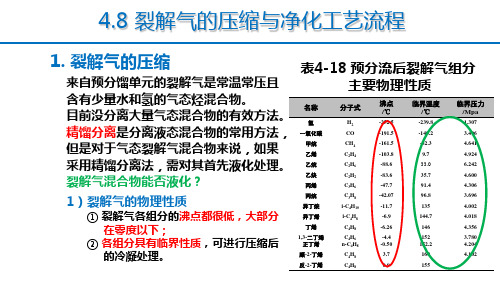
③ 炔烃的危害 如,乙炔可造成聚合催化剂中毒;降低乙烯分压;高压聚乙烯生产中,乙炔积 累过多会引起爆炸。
因此,对裂解气的压缩处理,易采用多段压缩段间换热的工艺,使压 缩机各段裂解气出口温度小于100℃,抑制二烯烃的聚合。
4.8 裂解气的压缩与净化工艺流程
3)裂解气的多段压缩工艺参数
① 典型的裂解气压缩机的操作参数
裂解气压缩及操作参数
段次
I II III IV V
温度/℃
吸入 排出
35
93
20
90
20
① ቤተ መጻሕፍቲ ባይዱ解气各组分的沸点都很低,大部分 在零度以下;
② 各组分具有临界性质,可进行压缩后 的冷凝处理。
表4-18 预分流后裂解气组分 主要物理性质
名称
氢 一氧化碳
甲烷 乙烯 乙烷 乙炔 丙烯 丙烷 异丁烷 异丁烯 丁烯 1,3-二丁烯 正丁烯 顺-2-丁烯 反-2-丁烯
分子式
H2 CO CH4 C2H4 C2H6 C2H2 C3H6 C3H8 i-C4H10 i-C4H8 C4H8 C4H6 n-C4H8 C4H8 C4H8
4.8 裂解气的压缩与净化工艺流程
问题:如果将裂解气的压力提高到3.6MPa时,裂解气的温度是多少?
例5 已知裂解气压缩前温度和压力分别为T1=20℃和P1=0.105MPa,按 一段绝热压缩计算(绝热指数k=1.228),当压缩后裂解气压力达到 P2=3.6MPa时,裂解气出口温度T2是多少?
解:根据绝热压缩时温度与压力关系式,T2=T1×(P2/P1)(K-1)/K,代入已知数据后, 得 T2=(273+20)×(3.6/0.105)(1.228-1)/1.228 =565K (292℃) 即,一段绝热压缩后,裂解气的温度从20℃上升292℃ ! 结果:这样的温度,将导致裂解气中所含的二烯烃发生聚合生成树脂(一种粘 性物质),且二烯烃的聚合速率随温度的升高而加快。
- 1、下载文档前请自行甄别文档内容的完整性,平台不提供额外的编辑、内容补充、找答案等附加服务。
- 2、"仅部分预览"的文档,不可在线预览部分如存在完整性等问题,可反馈申请退款(可完整预览的文档不适用该条件!)。
- 3、如文档侵犯您的权益,请联系客服反馈,我们会尽快为您处理(人工客服工作时间:9:00-18:30)。
两种除酸法的比较 缺优点点
碱洗法 碱碱不洗可再法生
消耗大 适除于酸酸彻含底量低
黄油问题 废水处理量大
乙醇胺法 乙醇胺法
吸收剂可再生 适用设酸备含要量求高高 吸收双烯烃再生易聚合
两段碱洗工艺流程
乙醇胺脱出酸性气工艺流程
脱水
水分的危害 在压缩系统,在段间冷凝过程分离出部分水分在低温分离系统结冰、水烃合物结晶,堵塞设备及管道 脱水要求
酸性气体的危害
裂解气分离装置
干冰堵塞管道 催化剂中毒
下游加工装置
产品达不到规定 聚合等过程催化剂中毒
脱除酸性气体的方法
碱洗法 NaOH为吸收剂 化学吸收
CO2+2NaOH H2S+2NaOH
Na2CO3+H2O Na2S+2H2O
乙醇胺法 一乙醇胺(MEA)和二乙醇胺(DEA)吸收剂
化学、物理吸收结合
一般工业上采用间接急冷
急冷方式比较
直接急冷
设备费少 操作简单 传热效果好 产生大量含油污水, 难分离 不能回收高品位的热能
间接急冷
回收高品位的热能 能量利用合理 无污水 不如直接方式中冷热物流接触空间大 结焦比较严重
不同裂解原料的急冷方式
裂解原料
稀释蒸汽含 急冷负荷 重组分液体产 结焦
量
物含量
间接急 油直冷 冷
水直冷
乙、丙 丁烷
石脑油
较少 中等
较小
较少
中等
中等
较不易 较易
轻柴油
较多
较大
很多
较易
重柴油
很多
很大
很多
很易
急冷换热器工艺要求
传热强度大 能够承受大压差和热量传递所引起的温差 便于清焦
使裂解气在0.01~0.1s内骤冷至露点左右 (但不能低于露点。为什么?)
油蒸汽在露点及低于露点时,容易冷凝聚集在急冷换热器的管壁上,在高温裂解气长期作用下,容 易结焦。
– 裂解重质燃料油 360℃以上馏分 相当于常压重油馏分 闪点应控制在100℃以上
裂解燃料油
裂解燃料油是指沸点在200℃以上的重组分。 其中:200-360℃裂解轻质燃料油,但大部分为杂环芳烃,其中,烷基萘含量较高,可作为脱烷基制
萘的原料。 沸程在360℃以上称为裂解重质燃料油,除作燃料外,由于裂解重质燃料油的灰分低,是生产碳黑的
经一段加氢可作为高辛烷值汽油组分
进行两段加氢经芳烃抽提分离芳烃产品
全部加氢 C5 C6~C8 C9-204℃ 思考:为啥裂解汽油中的芳烃含量较高?
裂解燃料油 烃类裂解副产的沸点在200℃以上的重组分 分类及控制指标 – 裂解轻质燃料油 200~360℃馏分 相当柴油馏分 闪点应控制在70~75℃以上
压差 原料进出口的温差不变,若燃料消耗量增加,则说明传热性差,应是结焦严重,热能利用率低 裂解产物中乙烯的含量下降
结焦的后果
传热系数下降(热量利用率低) 压差升高(设备阻力增大) 乙烯收率下降 能耗增大
工业上清焦的方法
停炉清焦:切断进料及出口,用惰性气体或水蒸气清扫管线,再用空气和水蒸气烧焦 在线清焦:交替裂解法和水蒸气、氢气清焦法。切换物料 其它方法:加入助剂,起到抑制作用
良好原料。 思考:为什么裂解重质燃料油的灰分低?
3.4.4 裂解气的净化 酸性气体的脱除
酸性气体的来源
CO2,H2S和其他气态硫化物
①
气体裂解原料带入的气体硫化物和CO2
②
液体裂解原料中所含的硫化物高温氢解生成的CO2和H2S
③
结炭与水蒸气反应生成CO和CO2
④
当裂解炉中有氧进入时,氧与烃类反应生成CO2
溶剂吸收法
吸收裂解气中的乙炔 同时回收一定量的乙炔 常用的溶剂
二甲基甲酰胺(DMF) N-甲基吡咯烷酮(NMP) 丙酮 沸点和熔点也是选择溶剂的重要指标
④
急冷油用于发生稀释蒸汽
⑤
急冷水用于分离系统的工艺加热
3.4.2 预分馏主要过程--急冷
急冷的目的
终止裂解反应
回收废热
急冷的意义
决定清焦周期,甚至决定裂解炉的周期
影响全装置的能耗和原料的单耗
急冷方式
直接急冷 冷却介质(水、油)与裂解气直接接触,适用于极易结焦的重质烃
间接急冷 急冷锅炉 废热锅炉 用换热器回收大量的热量,冷却介质用高压水,以提高蓄热能力
600~700×10-6 →1×10-6以下 方法
吸附干燥 吸附剂:3A分子筛
脱炔
乙炔 甲基乙炔 丙二烯 危害
炔烃影响乙烯和丙烯衍生物生产过程 影响催化剂寿命 恶化产品质量 形成不安全因素 产生不希望的副产品
脱炔要求 乙炔<5×10-5,丙二烯< 5×10-5
脱炔方法 溶剂吸收法和催化加氢法
减少急冷换热器结焦的措施
控制停留时间 一般控制在0.04s以下
控制裂解气冷却温度不低于其露点 急冷换热器出口温度 T出 = 0.56TB + α
α=340~420(随裂解深度加深而增大)
结焦与清焦
结焦的判断 在进料量不变的情况下,检查进料压力的变化,因为进料压差与设备压差有关,而结焦则影响
①
尽可能降低裂解气的温度
②
尽可能分馏出裂解气的重组分
③
在裂解气的预分馏过程中将裂解气中的稀释蒸汽以冷凝水的形式分离回收,用以
再发生稀释蒸汽
④
继续回收裂解气低能位热量
预分馏过程的作用
①
保证裂解气压缩机的正常运转,并降低裂解气压缩机的功耗,减少进入压缩分离系统的进料负
荷
②
大大减少污水排放量
③
合理的热量回收
裂解气的分馏与净化
1
Hale Waihona Puke 3.4 裂解气的分馏与净化
预分馏的目的与任务 急冷与急冷换热器 结焦与清焦 预分馏工艺过程 裂解汽油与裂解燃料油
将裂解炉出口的高温裂解气中的重组分,如燃料油、裂解汽油、水分等通过冷却手段进行分馏, 再送至下一步压缩、净化、深冷分离工段
3.4.1 预分馏的目的和任务
稀释蒸汽发生器
80℃
油水分离器
裂解汽油
950~1050℃
馏分油裂解装置裂解气预分馏过程
220~300℃
100~110℃
180~200℃
3.4.3 裂解汽油与裂解燃料油
裂解汽油 C5至沸点204℃以下的所有裂解副产物 其组成与原料油性质和裂解条件有关
表3-26 裂解汽油组成举例 特点:芳烃含量高,但也含有不饱和烃。 用途
清焦的化学反应和控制指标
C + O2 2C + O2 C + H2O
CO2 + Q 2CO + Q CO + H2+ Q
出口干气中CO+CO2含量低于 0.2%~0.5% 清焦结束
预分馏工艺过程
轻烃裂解装置的预分馏流程
原料
800~900℃ 裂解炉
200~300℃ 废热锅炉
急冷水 水洗塔
冷 却
裂解气 40℃