焦炉煤气净化工艺的有关思考
焦炉煤气净化过程中的问题与治理

焦炉煤气净化过程中的问题与治理摘要:从系统、工艺以及设备等角度论述了焦炉煤气净化过程中容易出现的问题,并针对性的提出了解决措施。
关键词:焦炉煤气净化煤气作为燃料在使用前必须进行净化,其净化系统一般由冷凝鼓风、除油脱萘、脱硫、脱氰、脱氨和脱苯等工序组成,不同的净化工艺主要区别于脱硫和脱氨工艺上,无论选用何种工艺都必须保证所确定的煤气净化指标的要求,并尽可能保证最终产品质量好、价值高且投资省以及运行和管理费用低等,但目前大多工艺在运行中经常会出现系列问题导致其预期目标受到影响,对运行中经常出现的问题进行研究并针对性的解决具有非常现实的意义。
1 系统存在问题1.1 系统阻力增加在系统运行过程中若煤气流量超出设计能力则将会造成系统阻力骤然增加,压力达到一定值后则会引起鼓风机吸力不足,继而导致煤气输送困难,最终影响到焦炉煤气管内压力的稳定性和向外输送的效果等现象。
1.2 硫铵工段饱和器运行不正常目前焦炉煤气净化工艺中硫铵工段一般采用喷淋式饱和器回收氨工艺,但在运行过程中会出现煤气流量超出设计能力的现象,该现象将会导致饱和器内各项生产运行技术指标出现恶化,致使最终硫酸铵产品的外观颜色频繁变深的结果。
1.3 硫铵饱和器等设备发生腐蚀、泄漏随着系统运行时间的增长,硫铵饱和器等设备会发生腐蚀泄漏的现象,系统内容易发生腐蚀泄漏的部位主要有小母液泵和结晶泵进出口管道焊缝部位出现刀线腐蚀,管壁变薄;喷淋式饱和器本体出现内壁多出呈凹坑状腐蚀,焊口周围呈密集的海绵状孔隙;满流槽焊缝部位出现刀线腐蚀,木材出现蜂窝状腐蚀;母液储槽的木材和焊缝宜出现点蚀和泄漏;饱和器连接管道焊缝及焊趾周围木材宜腐蚀,焊口周围呈密集的海绵状孔隙等。
1.4 冷凝单元效果差大部分来自焦炉的荒煤气与焦油和氨水沿吸煤气管道进入气液分离器进行气液分离,分离以后荒煤气从上部排放后进入初冷器进行冷却,初冷器分为上下两段,冷却后的荒煤气由横管初冷器下部排放的煤气进入并联操作的电捕焦油器来将煤气中夹带的焦油除掉,除油后的煤气经鼓风机加压送入硫铵工段。
焦炉煤气制甲醇工艺中的净化脱硫探讨
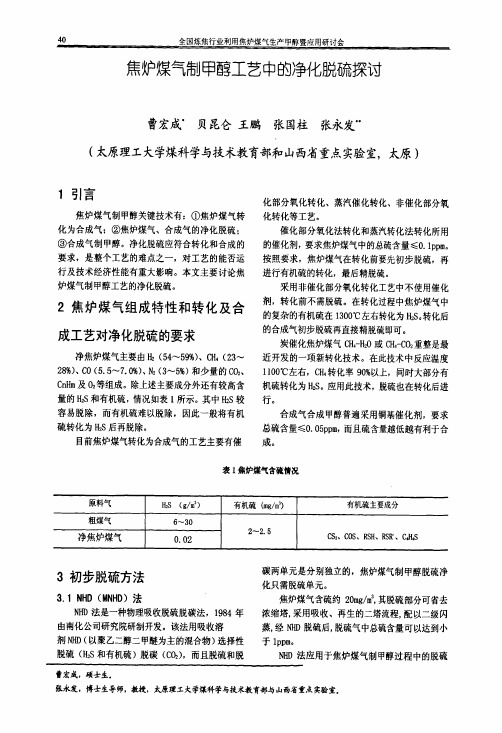
净焦炉煤气
0.02
CS2、COS、RSH、RSR’、c4H‘S
3初步脱硫方法
3.1
碳两单元是分别独立的,焦炉煤气制甲醇脱硫净 化只需脱硫单元。 焦炉煤气含硫约20mg/m3,其脱硫部分可省去 浓缩塔,采用吸收、再生的二塔流程,配以二级闪 蒸,经NttD脱硫后,脱硫气中总硫含量可以达到小 于lppm。
全国炼焦行业利用焦炉煤气生产甲醇暨应用研讨会
焦炉煤气制甲醇工艺中的净化脱硫探讨
曹宏成’
贝昆仑王鹏
张国柱
张永发“
(太原理工大学煤科学与技术教育部和山西省重点实验室,太原) 1引言
焦炉煤气制甲醇关键技术有;①焦炉煤气转
化为合成气;②焦炉煤气、合成气的净化脱硫:
化部分氧化转化、蒸汽催化转化、非催化部分氧 化转化等工艺。 催化部分氧化法转化和蒸汽转化法转化所用 的催化剂,要求焦炉煤气中的总硫含量40.1ppm。 按照要求,焦炉煤气在转化前要先初步脱硫,再 进行有机硫的转化,最后精脱硫。 采用非催化部分氧化转化工艺中不使用催化 剂,转化前不需脱硫。在转化过程中焦炉煤气中 的复杂的有机硫在1300℃左右转化为H。S。转化后 的合成气初步脱硫再直接精脱硫即可。 炭催化焦炉煤气cH。一Hzo或eH。一C02重整是最 近开发的一项新转化技术。在此技术中反应温度
100℃左右,CH4转化率90%以上,同时大部分有
机硫转化为H2S。应用此技术,脱硫也在转化后进 行。
合成气合成甲醇普遍采用铜基催化剂,要求
总硫含量40.05ppm,而且硫含量越低越有利于合 成。
表1焦炉煤气含硫情况
原料气 粗煤气
H2S(g/m3) 6~30
有机硫(mg/m3)
有机硫主要成分
2~2.5
新型焦炉煤气净化工艺的开发及进展

新型焦炉煤气净化工艺的开发及进展随着环保意识的不断提高,对于大气污染物的排放要求也越来越严格。
作为高污染源之一的焦化行业,其排放的煤气含有大量的污染物,对环境污染严重。
煤气净化成为了焦化行业面临的重要任务之一。
在此情况下,新型焦炉煤气净化工艺的开发及进展成为了研究的热点之一。
一、传统焦炉煤气净化存在的问题传统的焦炉煤气净化工艺存在着诸多问题,主要包括以下几个方面:1.低净化效率:传统焦炉煤气净化工艺通常采用湿法净化,采用水洗等方式去除污染物。
但是由于浓度低、温度低等原因,致使净化效率不高,无法完全去除煤气中的污染物。
2.高能耗:传统的煤气净化工艺需要大量的水资源和能源,造成了较大的能源浪费,且处理过程中产生的废水也需要进一步处理,增加了处理成本。
3.废水处理难题:传统湿法净化工艺会产生大量含有有机物和化学物质的废水,对废水的处理和排放造成了一定的困难。
4.设备占地大:传统净化工艺需要大量的净化设备,占地面积大,增加了投资成本。
传统焦炉煤气净化工艺在净化效率、能耗和废水处理等方面存在着较大的问题,迫切需要新的工艺来解决这些问题。
二、新型焦炉煤气净化工艺的开发及进展随着焦化行业的发展和技术进步,一些新型的焦炉煤气净化工艺逐渐得到了关注和应用,取得了一定的进展。
主要包括以下几种工艺:2.活性炭吸附技术活性炭吸附技术是利用活性炭对煤气中的有机物质和颗粒物进行吸附,从而达到净化的目的。
该技术具有净化效率高、操作稳定等优点,且产生的废水较少,对环境影响小,逐渐成为焦炉煤气净化的重要技术之一。
3.等离子体净化技术等离子体净化技术是利用等离子体在高温和高频电场的作用下,对煤气中的有机物质和颗粒物进行分解和氧化的一种新型净化技术。
该技术对高浓度、高温、高湿度的煤气也具有良好的净化效果,且处理过程中不会产生废水,是一种环保型的净化工艺。
4.膜分离技术膜分离技术是利用高分子材料膜对煤气中的二氧化碳、氧气和氮气等进行分离,从而实现煤气的净化。
浅谈焦炉煤气制氢工艺

浅谈焦炉煤气制氢工艺焦炉煤气是焦炭生产过程中煤炭在高温、缓慢干馏过程中产生的一种可燃性气体。
我国是焦炭产量最大的国家,2023年我国焦炭产量43142.6万t,依此计算,我国焦炉煤气产量是非常高的。
全国焦炭产能约有1/3在钢铁联合企业,2/3在独立焦化企业。
独立焦化企业富余的焦炉气曾因无法直接用于生产而被大量放散,放散量最高峰时曾达30km³/a。
焦炉煤气自2023年1月1日起实施的《焦化行业准入条件》修订版规定,焦化生产企业生产的焦炉煤气应全部回收利用,不得放散。
这给焦炉煤气的综合利用提供了有利的政策支持,也进一步推动了焦炉煤气制氢、甲醇等工业技术的发展。
炼焦过程中释放的焦炉煤气中富含氢气(55%左右),焦炉煤气制氢是目前可实现的大规模低成本高效率获得工业氢气的重要途径。
而我国晋、冀、豫几省是资源大省和焦化大省,氢源非常丰富,如何高效、合理地利用是关系环保、资源综合利用和节能减排的重大课题。
1、焦炉煤气制氢原理焦炉煤气制氢工序主要有:脱硫脱萘、压缩预处理、变压吸附制氢、脱氧干燥等。
其中焦炉煤气预处理系统为变温吸附(TSA),制氢系统为变压吸附(PSA),而氢气精制系统也为变温吸附(TSA),可用焦炉煤气制取99.999%的氢气。
吸附剂在常温高压下大量吸附原料气中除氢以外的杂质组分,然后降解杂质的分压使各种杂质得以解吸。
在实际应用中一般依据气源的组成、压力及产品要求的不同来选择组合工艺。
变温吸附的循环周期长、投资较大,但再生彻底,通常用于微量杂质或难解吸杂质的净化;变压吸附的循环周期短,吸附剂利用率高,用量相对较少,不需要外加换热设备,广泛用于大气量、多组分气体的分离和提纯。
由于焦炉煤气提纯氢气的特点是:原料压力低,原料组分复杂并含有焦油、萘、硫、重烃等难以解吸的重组分,产品纯度要求高。
因而装置需采用“加压+TSA预处理+PSA氢提纯+脱氧+TSA干燥”流程。
2、主要生产过程焦炉煤气是炼焦的副产品,产率和组成因炼焦煤质量和焦化过程不同而有所差别,一般每吨干煤可生产焦炉煤气300~350m³(标准状态)。
焦炉煤气净化装置的应用浅析

焦炉煤气净化装置的应用浅析前言:自70年代末开始,我国一些大型的焦化厂为了配合大容积焦炉的投入使用,从国外引入了大量的先进技术和工艺,其中比较典型的有脱酸蒸氨工艺、全负压净化工艺、氨分解工艺等等。
下面简要介绍一下我国煤气净化技术的应用情况。
1.分析焦炉煤气净化技术的应用现状焦炉煤气净化属于炼焦过程中的重要环节之一。
多年以来,我国各大焦化厂均沿袭着传统的煤气回收工艺流程,即初冷、洗氨、终冷、洗苯。
直至上世纪50年代末,经过焦化工作者的不懈努力终于设计出了与我国自行研发的58型焦炉相适应的煤气净化工艺,如ADA脱硫、硫胺与氨水流程、氨法脱硫、氨焚烧工艺、污水处理以及单塔脱苯工艺等等。
但是,虽然这些工艺流程也均能起到煤气净化的作用,但经各厂实际应用后却发现,这些煤气净化工艺普遍存在净化效果较差、环境污染严重、对设备腐蚀性强、产品质量差、氨苯回收率无法达到指定要求等缺点。
这不仅与国际先进技术水平相差甚远,而且也无法满足炼焦生产及绿色环保的要求。
1.1初步冷却煤气简单的讲,煤气初冷就是对焦炉煤气进行初步冷却降温,使其从800℃左右的高温降至25℃左右的温度。
在这一过程中主要依靠的装置是初冷器,相应的冷却方法主要有直接式、间接式以及直接与间接相结合三种方式。
冷却装置又分为立管式、横管式和直冷式喷淋塔三种。
在间接冷却的过程中,一般冷却水不会与煤气发生直接接触,主要是利用换热器来完成冷却。
由于在该过程中冷却水并未受到污染,故此可循环重复使用,这种方法比较适合在水资源紧缺的焦化厂中使用。
而直冷式主要是通过塔來完成冷却,在此过程中不仅能够对煤气进行冷却,同时还可以起到净化的效果。
基于这两种冷却方式的优点,大部分焦化厂均选择两种方式结合使用来进行煤气初冷。
实践证明,冷却后煤气中含萘量能够降低到每立方米1克以下。
1.2焦油的脱除与回收在煤气冷却的过程中,大部分焦油会随氨水一并冷却,其余的一小部分则会被焦油捕集装置混合到氨水当中。
焦炉煤气净化技术研究
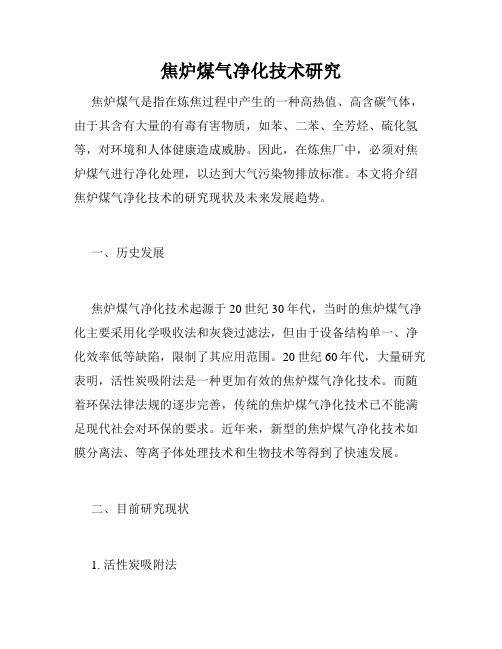
焦炉煤气净化技术研究焦炉煤气是指在炼焦过程中产生的一种高热值、高含碳气体,由于其含有大量的有毒有害物质,如苯、二苯、全芳烃、硫化氢等,对环境和人体健康造成威胁。
因此,在炼焦厂中,必须对焦炉煤气进行净化处理,以达到大气污染物排放标准。
本文将介绍焦炉煤气净化技术的研究现状及未来发展趋势。
一、历史发展焦炉煤气净化技术起源于20世纪30年代,当时的焦炉煤气净化主要采用化学吸收法和灰袋过滤法,但由于设备结构单一、净化效率低等缺陷,限制了其应用范围。
20世纪60年代,大量研究表明,活性炭吸附法是一种更加有效的焦炉煤气净化技术。
而随着环保法律法规的逐步完善,传统的焦炉煤气净化技术已不能满足现代社会对环保的要求。
近年来,新型的焦炉煤气净化技术如膜分离法、等离子体处理技术和生物技术等得到了快速发展。
二、目前研究现状1. 活性炭吸附法活性炭吸附法在焦化炉气体净化中得到广泛应用,其吸附剂具有强的吸附、选择性和再生性能,能够高效地去除苯、二苯、全芳烃等有害成分。
目前活性炭吸附法中存在着吸附剂失活、吸附速率慢等问题,研究人员正在通过改变吸附剂结构、增加吸附剂表面积等措施来提高活性炭吸附效率。
2. 膜分离法膜分离技术在气体分离领域具有广泛应用,可高效地分离和去除焦炉煤气中的有害成分。
与传统的吸附法相比,膜分离法具有操作简单、净化效率高等优点。
目前,膜分离技术研究仍处于实验室规模,尚未得到工业化应用。
3. 等离子体处理技术等离子体处理技术是一种新型的焦炉煤气净化技术,其原理是利用高能等离子体对有害物质进行氧化降解,将其转化为无害成分。
该技术具有能耗低、处理效率高等优点,在焦化炉气体净化方面存在广阔的应用前景。
4. 生物技术生物技术在焦化炉气体净化中应用也逐渐得到重视,其原理是利用微生物对有害成分进行降解,将其转化为无害物质。
与传统的焦炉煤气净化技术相比,生物技术有着对环境影响小、操作简单等优点,但目前该技术还存在处理效率低、微生物保存等问题,需要进一步完善。
焦炉煤气净化技术的应用现状与改进

直冷方式可冷却煤气,也可净化焦炉煤气。
而间接冷却方式在冷却焦炉煤气过程中,煤气不会直接与冷却水接触,而是借助于换热器来完成冷却过程。
间接冷却方式过程中由于冷却水不直接接触煤气,可不受煤气污染,因此,间接冷却方式所用冷却水可重复利用,适用于水资源紧缺的焦化企业。
基于直接冷却和间接冷却的优缺点,多数焦化企业选择使用直接、间接冷却结合式来完成煤气初冷过程。
焦炉企业煤气净化实践结果证明,煤气初冷后,其中所含萘气体量大大降低。
1.2 焦油脱除与焦油回收煤气初冷过程中,多数焦油也会随着煤气的冷却而冷却,小部分焦油则会进入焦油捕集装置,和氨水混合。
目前多数焦化企业均以氨水焦油分离设备来脱除焦油,此过程还可以有效去除渣尘。
一般而言,焦油脱除效果随着分离时间的延长而逐渐显著,但随着分离时间的延长,分离温度也会下降,使得焦油粘度大大增加,降低分离效果。
因此,焦油脱除过程还需要满足温度和时间两个因素。
1.3 萘脱除工艺粗煤气中含有约10g/m 3萘气体,经煤气初冷后,萘气体含量可降至2g/m 3左右,但冷却后的萘气体则处于过饱和状态。
焦炉煤气经管路输送至下道工序时,可能会在温度过低或流速过慢的制约下出现萘沉积现象,进而堵塞管路。
因此,将焦炉气体中的萘气体除去对焦化企业来说至关重要。
目前,萘脱除工艺主要有水洗工艺和油洗工艺两类。
其中,以油洗工艺来清洗焦炉煤气管路,可将其中萘气体含量降至1g/m 3以下,进而降低管路堵塞概率。
1.4 煤气输送及煤气调节常用的焦炉煤气输送设备主要是鼓风机,根据鼓风机结构的差异可将其分为两种:容积式鼓风机和离心式鼓风机。
其中,离心式鼓风机可进行调节,根据要求可进行循环调节、自动调节以及转速调节。
因此,国内多数焦化企业的煤气输送设备均选用离心式鼓风机。
2 焦炉煤气净化过程中存在的主要问题焦炉煤气在净化过程中存在诸多问题,主要分为以下几个方面。
第一,煤气初冷问题。
横管初冷器在设备运行期间容易出现故障,导致煤气在管路中堵塞。
煤气净化工艺分析论文

毕业设计(论文)设计课题:煤气净化工艺分析专业:煤炭深加工与利用班级:10级(2)班姓名:张震指导老师:朱海龙平顶山工业职业技术学院2013年3月6日目录绪论正文一、焦炉煤气净化工艺经历的三个阶段二、我国焦炉煤气净化工艺的发展方向三、焦炉煤气净化工艺1、传统的煤气净化工艺2、煤气净化的内容及技术现状3、现有焦炉煤气净化技术存在的问题焦炉4、煤气净化新技术探讨四、焦炉煤气净化工艺研究进展1、国内外焦炉煤气净化工艺的发展2、焦炉煤气典型净化工艺及比较3、国内外对焦炉煤气净化工艺的最新研究4、对焦炉煤气净化工艺的建议五、焦炉煤气净化工艺流程的选择1、采用以氨为碱源的HPF湿式氧化法脱硫为中心的煤气净化工艺流程2、采用以真空碳酸盐脱硫为中心的煤气净化流程3、以碳酸钠为碱源的改良ADA法4、以氨为碱源的HPF法5、氨硫循环洗涤法6、发展煤气净化技术的设想六、总结绪论焦炭作为冶金工业的主要原料被炼铁厂大量使用。
炼焦用煤在复杂的地质状况下含有上百中成分,这样煤在焦炉中成焦的同时,其中多种成分将随煤气一起进入下面的工序。
随着用户对煤气需求质量的不断提高,对煤气净化并除去其中多种成分的净化工艺便产生了,这样经过处理后的煤气称之为净煤气。
1792年苏格兰人发明用铁甑干馏烟煤以来,煤气制造技术得到了发展。
法国、德国、英国、荷兰先后建立起能够回收化学产品的焦炉,并以奥托一霍夫曼型焦炉最为著名,从此炼焦工业不仅生产焦炭,同时也产生净煤气。
焦炉煤气净化工艺流程的选择,主要取决于脱氨和脱硫的方法。
众所周知,在炼焦过程中,煤中约有30%的硫进入焦炉煤气,95%的硫以硫化氢的形式存在。
焦炉煤气中一般含有硫化氢6~8g /m3 , 氰化氢 1. 5~2g/m'。
若不事先脱除,就有50%的氰化氢和10%~40%的硫化氢进入氨、苯回收系统,加剧了设备的腐蚀,还会增加外排污水中的酚、氰含量。
含有硫化氢和氰化氢的煤气作为燃料燃烧时,会生成大量SO2和NO2而污染大气。
- 1、下载文档前请自行甄别文档内容的完整性,平台不提供额外的编辑、内容补充、找答案等附加服务。
- 2、"仅部分预览"的文档,不可在线预览部分如存在完整性等问题,可反馈申请退款(可完整预览的文档不适用该条件!)。
- 3、如文档侵犯您的权益,请联系客服反馈,我们会尽快为您处理(人工客服工作时间:9:00-18:30)。
焦炉煤气净化工艺的有关思考
作者:郭晓林
来源:《中国化工贸易·中旬刊》2018年第07期
摘要:焦炉煤气装置主要包括煤气脱苯、煤气脱硫、煤气脱氮等几个环节,不同工序具有不同的施工工艺。
在全球环保法规日益严格的背景下,以往煤气净化技术弊端逐渐凸显。
而焦炉煤气中含有的HCN、H2S及其他燃烧后废料对大气也造成了严重的影响。
因此本文根据现阶段焦炉煤气净化主要工序特点,对焦炉煤气净化工艺进行了优化分析,以便为焦化工业的可持续发展提供有效地借鉴。
关键词:煤炉;煤气;净化
某焦化厂主要包括4座4.2m焦炉、1座6.2m焦炉,其设计煤气处理能力为
125000Nm3/h。
随着该焦化企业生产规模拓展,在2017年建成投产后,年度设计生产能力由以往的210万t焦炭上升到300万t焦炭,同时焦炉煤气总发生量也由以往的120000Nm3/h上升到150000Nm3/h。
这种情况下,实际生产系统指标就出现不匹配风险。
本文对该焦化企业焦炉煤气净化工艺进行了优化分析。
1 焦炉煤气净化工艺主要工序
①焦炉煤气脱氮:在焦炉干馏环节,大多数氮可转化为以氨根离子为基础的含氮化合物,在煤气粗提取环节也存在6-8g/m3的氮。
由于氨具有腐蚀性质,因此在实际处理过程中,需要采用氨水焦油分离装置将其分层分离。
②焦炉煤气脱苯:焦炉中煤气脱苯主要依据理论脱苯标准,依次通过冷冻、吸附、洗涤等工序进行处理。
在焦化工业生产过程中,依据焦油来源共分为石油洗油洗苯、焦油洗油洗苯两种类型。
在粗焦油加工系统的大规模焦化企业,大多选择自产焦油洗油洗涤模式。
③焦炉煤气脱硫:在焦炉煤气中存在着少量的硫化氢及氰化氢气体。
现阶段我国煤气脱硫方式主要包括干式氧化、湿式吸收、湿式氧化等几种类型。
其中干式氧化主要采用氧化铁箱法,整体使用较普遍。
2 焦炉煤气净化工艺的改进
2.1 环保技术
焦炉煤气净化工艺根据净煤气质量指标及焦化产业市场标准,具有不同的工艺流程。
而系统工艺改进则是通过物料流、能源流、信息流、资金流等各个环节设计控制及优化组织,结合环保技术的合理应用,实现过程分析优化。
以1t干煤为基础,该企业生产煤气在焦炉煤气装置中释放热量76%左右被循环氨气吸收。
在具体传质环节,循环氨气液面水汽分压、煤气水汽分压差值为主要驱动力。
这种情况下,煤气热交换时,煤气到金属壁之间热量传递效率就为水蒸气体积占湿煤气总体积比例与固定系数的乘积。
因此控制循环氨水蒸发率,可提高煤气初次冷却过程中煤气与冷却装置总体传热系数。
最后在煤气净化工艺实施过程中,煤气温度与前期要求相符是整体净化工艺顺利开展的前提,所以在煤气净化工艺改进环节,相关设计人员应加大对煤气露点情况的重视,控制煤气管中蒸汽通入量。
在必要情况下,可控制初冷温度合格率,并将最低控制温度与煤气中萘含量进行关联分析,如在煤气中萘含量为564.8时,可控制煤气净化温度为25℃[1]。
2.2 新型干法净化技术
为了进一步降低后续工序设备负载压力,可采用新型干法净化工艺,从根本上避免循环液体蒸发导致循环效益下降。
一方面在保证煤气质量与环保要求相符的基础上,可将焦化生产系统转化为不同的操作模块,如煤气净化、煤气利用、煤气原料准备、焦炉热工、污水处理等。
其中煤气净化主要包括煤气冷却、煤气焦油脱离、脱硫、脱氨、脱苯等几个环节。
在工艺优化改造过程中,应及时进行物料能量平衡计算,结合上下工艺产生的匹配设置,确定最佳性价比能源指标。
如在焦炉脱苯环节,可将最低成本回收煤气中最多苯作为主要工作目标,依此为依据对蒸汽、电力、洗油、再生渣及废水量进行优化操作参数核算,确定最佳操作数值。
另一方面可采用连铸加压站净化模式,将煤气脱萘与煤气脱硫工艺顺序进行适当调整。
然后考虑到脱萘装置内填料再生效益,可采取空气通入再生的方式,将填料压力增加到12.0kPa,并利用换热装置将温度控制在125℃左右[2]。
最后在焦炉煤气净化冷却杂质分离后,可将其输送到再生焦炉煤气主管网络通道中。
将冷却塔冷凝后产物排入酚水池,综合采用冷却喷淋、蒸汽清洗两种措施,提高焦炉煤气冷却实际效益。
此外,在焦炉煤气干式煤气净化系统工艺运行过程中,若煤气净化温度一定,吸附质在吸附剂中的吸附量与吸附质分压浓度成正比;若煤气净化压力一定,则吸附质在吸附剂中吸附量与吸附温度成反比,因此在焦炉煤气干式净化系统运行过程中,可采取适当升温、降压或降温、加压措施,便于吸附质吸附或再生。
3 总结
综上所述,经过近6个月的试验,该再生煤气系统设备运行效益良好。
较再生前期脱除效益提升了700mg/m3左右。
因此在焦炉煤气净化过程中,相关焦化企业可依据自身发展需要,不断学习先进技术,并进行相关工艺的优化改进。
促使整体生产系统在有条不紊的环境中良性循环,保证焦炉煤气净化后指标达到国家级标准。
参考文献:
[1]徐杰.焦炉煤气净化工艺改进探讨[J].工业c,2016(6):47.。