焦炉煤气净化工艺流程的评述
焦炉煤气工艺流程
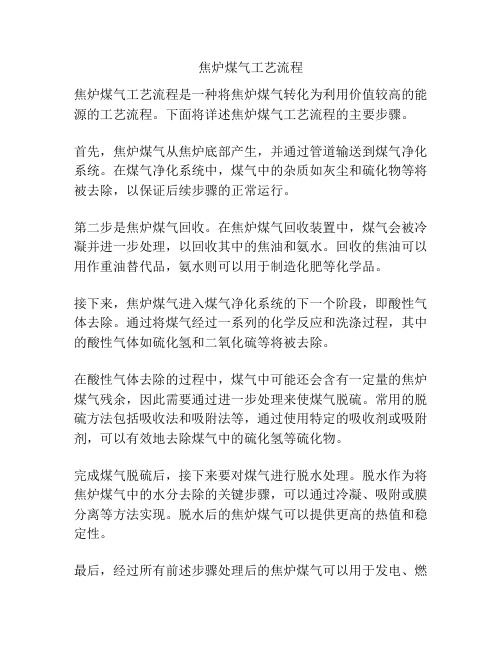
焦炉煤气工艺流程焦炉煤气工艺流程是一种将焦炉煤气转化为利用价值较高的能源的工艺流程。
下面将详述焦炉煤气工艺流程的主要步骤。
首先,焦炉煤气从焦炉底部产生,并通过管道输送到煤气净化系统。
在煤气净化系统中,煤气中的杂质如灰尘和硫化物等将被去除,以保证后续步骤的正常运行。
第二步是焦炉煤气回收。
在焦炉煤气回收装置中,煤气会被冷凝并进一步处理,以回收其中的焦油和氨水。
回收的焦油可以用作重油替代品,氨水则可以用于制造化肥等化学品。
接下来,焦炉煤气进入煤气净化系统的下一个阶段,即酸性气体去除。
通过将煤气经过一系列的化学反应和洗涤过程,其中的酸性气体如硫化氢和二氧化硫等将被去除。
在酸性气体去除的过程中,煤气中可能还会含有一定量的焦炉煤气残余,因此需要通过进一步处理来使煤气脱硫。
常用的脱硫方法包括吸收法和吸附法等,通过使用特定的吸收剂或吸附剂,可以有效地去除煤气中的硫化氢等硫化物。
完成煤气脱硫后,接下来要对煤气进行脱水处理。
脱水作为将焦炉煤气中的水分去除的关键步骤,可以通过冷凝、吸附或膜分离等方法实现。
脱水后的焦炉煤气可以提供更高的热值和稳定性。
最后,经过所有前述步骤处理后的焦炉煤气可以用于发电、燃烧或者制氢等应用领域。
利用焦炉煤气发电可以有效提高能源利用效率,降低环境污染;利用焦炉煤气燃烧可以代替部分石油和天然气的使用,降低能源依赖性;而将焦炉煤气转化为氢气可以作为清洁燃料应用于氢能源产业。
总之,焦炉煤气工艺流程通过多步骤的处理,将焦炉煤气转化为可再利用的能源,实现了能源的高效利用和减少环境污染的目标。
随着能源问题的日益突出,焦炉煤气工艺流程的发展和应用将发挥越来越重要的作用。
焦炉煤气的净化工艺流程
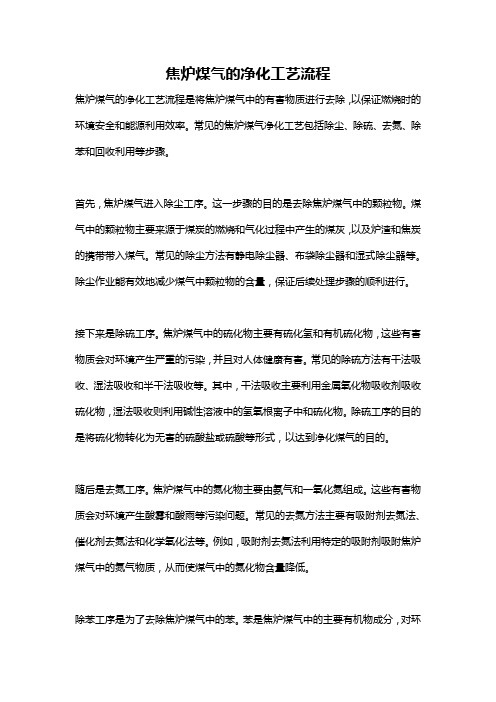
焦炉煤气的净化工艺流程焦炉煤气的净化工艺流程是将焦炉煤气中的有害物质进行去除,以保证燃烧时的环境安全和能源利用效率。
常见的焦炉煤气净化工艺包括除尘、除硫、去氮、除苯和回收利用等步骤。
首先,焦炉煤气进入除尘工序。
这一步骤的目的是去除焦炉煤气中的颗粒物。
煤气中的颗粒物主要来源于煤炭的燃烧和气化过程中产生的煤灰,以及炉渣和焦炭的携带带入煤气。
常见的除尘方法有静电除尘器、布袋除尘器和湿式除尘器等。
除尘作业能有效地减少煤气中颗粒物的含量,保证后续处理步骤的顺利进行。
接下来是除硫工序。
焦炉煤气中的硫化物主要有硫化氢和有机硫化物,这些有害物质会对环境产生严重的污染,并且对人体健康有害。
常见的除硫方法有干法吸收、湿法吸收和半干法吸收等。
其中,干法吸收主要利用金属氧化物吸收剂吸收硫化物,湿法吸收则利用碱性溶液中的氢氧根离子中和硫化物。
除硫工序的目的是将硫化物转化为无害的硫酸盐或硫酸等形式,以达到净化煤气的目的。
随后是去氮工序。
焦炉煤气中的氮化物主要由氨气和一氧化氮组成。
这些有害物质会对环境产生酸雾和酸雨等污染问题。
常见的去氮方法主要有吸附剂去氮法、催化剂去氮法和化学氧化法等。
例如,吸附剂去氮法利用特定的吸附剂吸附焦炉煤气中的氮气物质,从而使煤气中的氮化物含量降低。
除苯工序是为了去除焦炉煤气中的苯。
苯是焦炉煤气中的主要有机物成分,对环境和人体都有一定的危害。
去苯的方法多种多样,包括吸附过程、吸附剂再生过程和热解技术等。
其中,吸附过程主要是利用各种吸附剂吸附苯,吸附剂再生过程则是通过各种手段将吸附的苯从吸附剂中脱附出来。
最后是回收利用工序。
焦炉煤气中除去有害物质后,还含有一些有价值的组分,如甲烷、氢气和一些烃类等。
对于这些有价值的组分,可以通过适当的工艺进行回收利用。
一般来说,回收利用工艺分为低温分馏和高温分馏两种方式。
低温分馏主要是通过降温将焦炉煤气中的一些高沸点成分凝结出来,从而得到所需的有价值气体。
而高温分馏则是通过高温条件下焦炉煤气中的组分按沸点顺序蒸馏分离。
焦炉煤气 工艺流程

焦炉煤气工艺流程焦炉煤气是焦炉煤炭在高温下产生的一种气体,在很长一段时间里,焦炉煤气被广泛应用于燃料和化工领域。
下面将为大家介绍焦炉煤气的工艺流程。
焦炉煤气的产生主要是通过焦炉炼焦过程中的不完全燃烧和挥发分解产生的。
在焦炉内炼焦时,煤炭由上部装料口进入焦炉,经过一系列的物理化学变化,最终冷却出来的煤气即为焦炉煤气。
焦炉煤气的工艺流程主要分为三个阶段:炼焦阶段、冷却阶段和净化阶段。
在炼焦阶段,煤炭在高温环境下进行挥发分解,产生焦炭和焦炉煤气。
挥发分解的主要反应包括干馏、结焦与气化等。
煤的挥发分解温度通常在400℃-900℃之间。
焦炉内部的高温炉壁使得煤气中的有机物无法完全燃烧,形成不完全燃烧的焦炉煤气。
在冷却阶段,焦炉煤气经过煤气出口管道进入冷却塔。
冷却塔内部设置了多个冷却层和冷凝层。
焦炉煤气在通过冷却层时,通过与从上方喷洒下来的冷凝剂的交换,将煤气中的水蒸气和部分液化烃冷凝回收。
通过这种方式,焦炉煤气的温度被迅速降低,并且冷凝出来的液体可以进一步提炼。
冷却后,焦炉煤气进入冷凝层,通过与一种冷凝剂接触,使得其中的其他液态有机物冷凝,得到另一批可提炼的液体产品。
在净化阶段,焦炉煤气经过冷却后进入净化系统进行进一步处理。
净化系统主要是通过吸附、干燥和脱硫等工艺,将煤气中的杂质进行去除。
其中,吸附工艺主要是通过将焦炉煤气经过各类吸附剂的床层,实现对焦炉煤气中有机硫化物的吸附。
干燥工艺主要是通过风冷和除湿剂吸附,将煤气中的水分去除。
脱硫工艺主要是通过往煤气中添加一种化学药剂,使其与焦炉煤气中的硫化氢反应生成含硫化合物,然后通过其他工艺将其去除。
最终,经过炼焦、冷却和净化三个阶段的焦炉煤气将得到高纯度、高热值的产品。
这种产品广泛应用于燃料领域,如发电厂、炼铁厂等,也可以在化工领域中用作原料,制造各种化工产品。
总之,焦炉煤气的工艺流程经历了炼焦、冷却和净化三个阶段,通过各种反应和处理,最终得到高纯度、高热值的产品。
焦炉煤气净化工艺流程的评述
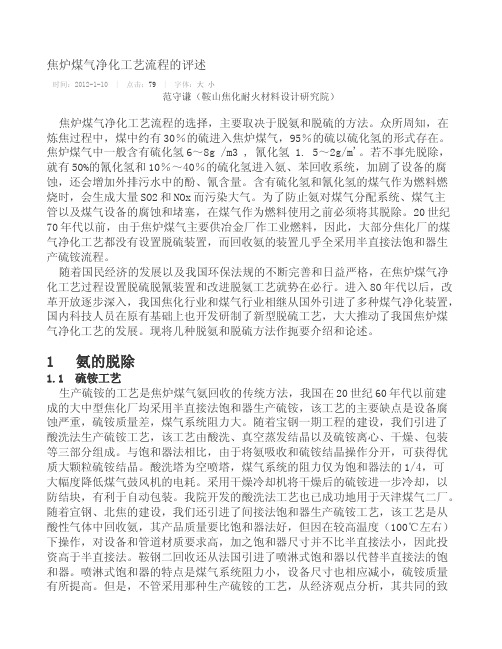
焦炉煤气净化工艺流程的评述时间:2012-1-10 | 点击:79 | 字体:大小范守谦(鞍山焦化耐火材料设计研究院)焦炉煤气净化工艺流程的选择,主要取决于脱氨和脱硫的方法。
众所周知,在炼焦过程中,煤中约有30%的硫进入焦炉煤气,95%的硫以硫化氢的形式存在。
焦炉煤气中一般含有硫化氢6~8g /m3 , 氰化氢 1. 5~2g/m'。
若不事先脱除,就有50%的氰化氢和10%~40%的硫化氢进入氨、苯回收系统,加剧了设备的腐蚀,还会增加外排污水中的酚、氰含量。
含有硫化氢和氰化氢的煤气作为燃料燃烧时,会生成大量SO2和NOx而污染大气。
为了防止氨对煤气分配系统、煤气主管以及煤气设备的腐蚀和堵塞,在煤气作为燃料使用之前必须将其脱除。
20世纪70年代以前,由于焦炉煤气主要供冶金厂作工业燃料,因此,大部分焦化厂的煤气净化工艺都没有设置脱硫装置,而回收氨的装置几乎全采用半直接法饱和器生产硫铵流程。
随着国民经济的发展以及我国环保法规的不断完善和日益严格,在焦炉煤气净化工艺过程设置脱硫脱氰装置和改进脱氨工艺就势在必行。
进入80年代以后,改革开放逐步深入,我国焦化行业和煤气行业相继从国外引进了多种煤气净化装置,国内科技人员在原有基础上也开发研制了新型脱硫工艺,大大推动了我国焦炉煤气净化工艺的发展。
现将几种脱氨和脱硫方法作扼要介绍和论述。
1 氨的脱除1.1 硫铵工艺生产硫铵的工艺是焦炉煤气氨回收的传统方法,我国在20世纪60年代以前建成的大中型焦化厂均采用半直接法饱和器生产硫铵,该工艺的主要缺点是设备腐蚀严重,硫铵质量差,煤气系统阻力大。
随着宝钢一期工程的建设,我们引进了酸洗法生产硫铵工艺,该工艺由酸洗、真空蒸发结晶以及硫铵离心、干燥、包装等三部分组成。
与饱和器法相比,由于将氨吸收和硫铵结晶操作分开,可获得优质大颗粒硫铵结晶。
酸洗塔为空喷塔,煤气系统的阻力仅为饱和器法的1/4,可大幅度降低煤气鼓风机的电耗。
焦炉煤气工艺流程

焦炉煤气工艺流程
《焦炉煤气工艺流程》
焦炉煤气工艺流程是利用焦炭生产过程中产生的煤气进行加工和利用的过程。
焦炉煤气主要由一氧化碳、氢气、甲烷和一些杂质组成,是一种重要的工业燃料和原料。
焦炉煤气的工艺流程通常分为四个主要步骤:煤气的生产、净化、加工和利用。
首先是煤气的生产。
焦炉中的焦炭生产过程会产生大量的煤气,这些煤气经过收集后被送入净化系统进行处理。
在净化系统中,煤气会经过除尘、除硫、除氮等工艺处理,去除其中的杂质。
净化后的煤气会被送入加工系统进行储存和调节。
加工系统会对煤气进行加压、干燥和调节,以适应不同的工业用途。
通过加工后的煤气可以用于工业燃料、化工原料等领域。
关键是,这些煤气可以被再次利用,从而实现资源的高效利用。
焦炉煤气的工艺流程不仅能够提供工业燃料,还可以减少环境污染,实现资源节约和循环利用。
因此,焦炉煤气工艺流程在工业生产中具有重要的意义。
总而言之,焦炉煤气工艺流程是一项重要的工业技术,通过对焦炉产生的煤气进行处理和利用,实现了资源的高效利用和环境的保护。
需要进一步研究和发展,以满足工业生产对能源和环境的需求。
焦炉煤气制液化天然气项目工艺流程
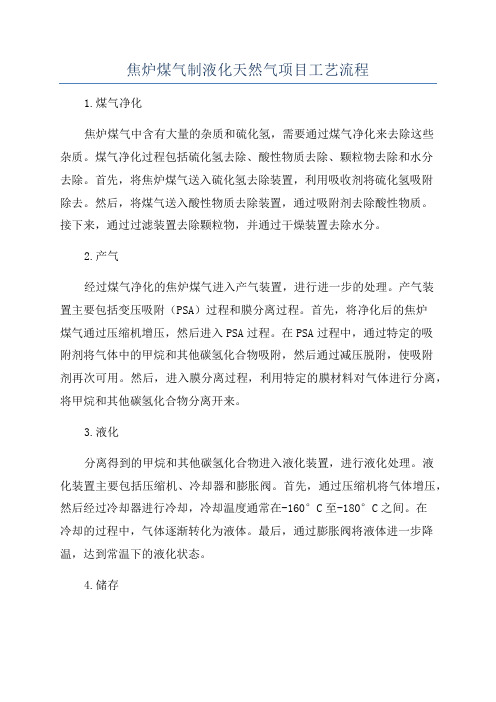
焦炉煤气制液化天然气项目工艺流程1.煤气净化焦炉煤气中含有大量的杂质和硫化氢,需要通过煤气净化来去除这些杂质。
煤气净化过程包括硫化氢去除、酸性物质去除、颗粒物去除和水分去除。
首先,将焦炉煤气送入硫化氢去除装置,利用吸收剂将硫化氢吸附除去。
然后,将煤气送入酸性物质去除装置,通过吸附剂去除酸性物质。
接下来,通过过滤装置去除颗粒物,并通过干燥装置去除水分。
2.产气经过煤气净化的焦炉煤气进入产气装置,进行进一步的处理。
产气装置主要包括变压吸附(PSA)过程和膜分离过程。
首先,将净化后的焦炉煤气通过压缩机增压,然后进入PSA过程。
在PSA过程中,通过特定的吸附剂将气体中的甲烷和其他碳氢化合物吸附,然后通过减压脱附,使吸附剂再次可用。
然后,进入膜分离过程,利用特定的膜材料对气体进行分离,将甲烷和其他碳氢化合物分离开来。
3.液化分离得到的甲烷和其他碳氢化合物进入液化装置,进行液化处理。
液化装置主要包括压缩机、冷却器和膨胀阀。
首先,通过压缩机将气体增压,然后经过冷却器进行冷却,冷却温度通常在-160°C至-180°C之间。
在冷却的过程中,气体逐渐转化为液体。
最后,通过膨胀阀将液体进一步降温,达到常温下的液化状态。
4.储存液化的天然气(LNG)通过输送管道进入储罐进行存储。
储罐通常采用双层结构,内层用于储存液化天然气,外层用于保温。
储罐还配备了安全阀和压力传感器,以确保储存的LNG的安全性。
以上是焦炉煤气制液化天然气(LNG)项目的工艺流程的详细描述。
通过煤气净化去除杂质和硫化氢,通过产气过程去除甲烷和其他碳氢化合物,然后通过液化和储存,将焦炉煤气转化为液态天然气,方便储存和运输。
这项工艺过程能够更高效地利用焦炉煤气,并提供更为清洁的能源。
煤气净化工艺工艺流程

煤气净化工艺工艺流程煤气是燃烧煤炭时产生的一种气体,其中含有大量的二氧化碳、一氧化碳、二氧化硫等有害物质。
为了减少对环境的污染和保护人们的健康,煤气净化工艺应运而生。
以下是一个常见的煤气净化工艺流程,详细介绍了各个工艺环节的作用和操作流程。
1.煤气进料系统煤气从燃烧煤炭的炉燃室进入煤气净化工艺系统的第一步是进料系统。
在进料系统中,煤气首先经过一个过滤器,用于去除颗粒物和大颗粒灰尘,以防止后面的设备受到堵塞和磨损。
然后,煤气进入预处理系统。
2.预处理系统预处理系统主要用于处理煤气中的高温粒子,包括灰尘和烟尘。
首先,煤气由预处理设备加热,然后通过旋风分离器,将大颗粒的灰尘和烟尘从煤气中分离出来。
分离出的灰尘和烟尘可用于回收处理。
3.硫化氢脱除系统硫化氢是煤气中的一种有害气体,会对环境和人体健康造成危害。
硫化氢脱除系统用于去除煤气中的硫化氢。
煤气首先通过一个吸收装置,其中含有一种吸附剂,可以吸附硫化氢。
吸附剂可以是碱性物质,如氢氧化钠或氢氧化钾。
一旦硫化氢被吸附,清洁的煤气通过分离装置被分离出来,而被吸附的硫化氢则被进一步处理。
4.硫化氢处理被吸附的硫化氢通常被处理成为硫化物或废硫。
这个过程通常包括两个步骤:再生和转化。
再生是将吸附剂中的硫化物与氧气反应,生成可再生吸附剂和硫气的反应。
转化是将硫气转化为硫化物或废硫。
常用的转化方法是将硫气转化为硫酸,再将硫酸处理成为硫化物或废硫。
5.二氧化硫脱除系统除了硫化氢,煤气中通常还含有二氧化硫等硫化合物。
二氧化硫脱除系统用于去除煤气中的二氧化硫。
煤气首先通过一个吸收装置,其中含有一种吸附剂,可以吸附二氧化硫。
吸附剂可以是氨水或乙二醇。
一旦二氧化硫被吸附,清洁的煤气通过分离装置被分离出来,而被吸附的二氧化硫则被进一步处理。
6.二氧化硫处理被吸附的二氧化硫通常被处理成为硫酸。
这个过程包括将二氧化硫转化为硫酸的反应。
常用的转化方法是将二氧化硫与氧气反应,生成硫三氧和水。
焦炉煤气净化处理技术的相关分析

焦炉煤气净化处理技术的相关分析摘要:焦炉煤气是炼焦过程中产生的副产品,其成分复杂,含有多种杂质,必须进行净化处理,才能加以回收利用,以实现节能减排,提高资源利用效率。
焦炉煤气的净化处理,包含焦化厂的初步净化处理以及下游企业的精净化处理,本文重点对焦化厂对焦炉煤气初步净化处理的技术细节进行了分析,明确了其中的一些关键技术节点。
关键词:焦炉煤气;净化处理;技术细节在炼焦过程当中会产生一种副产品,即焦炉煤气,焦炉煤气是多种气体的混合产物,其主要成分为H2、CO、CO2、CH4、C2H6、N2等,其中H2、CO、CH4、C2H6为可燃气体。
同时含有多种杂质,主要有:焦油、笨、萘、无机硫、有机硫、氨、氰化氢等。
焦炉煤气的性质是一种高热值煤气,可作为燃料,也可作为化工产品的原料,但在使用前必须要净化,除去其中的杂质,满足生产要求和环保要求。
我们公司作为焦化厂的下游企业,是利用焦化厂多余的焦炉煤气制合成天然气。
焦化厂有自己的化产车间,对焦炉煤气进行了初步净化处理,脱除了焦炉煤气中大量的焦油、笨、无机硫、氨等。
焦炉煤气进入我们公司的装置后,再进行变温吸附脱焦油和萘、水洗脱氨、常温粗脱硫、加氢脱硫等精净化处理。
焦化厂对焦炉煤气初步净化处理技术的好坏,直接决定了出焦化厂的焦炉煤气杂质含量的高低,这是我们公司装置是否能够长周期稳定运行的重要因素,是我们公司是否能够产生较好经济效益的关键。
一、关于焦炉煤气净化处理焦炉煤气中含有大量对大气不友好的杂质,据不完全统计,焦炉煤气年均产量高达110万立方,在炼焦过程中正常消耗一部分,还有一部分大约60万立方的量,若不进行净化处理将直接排放至大气中,不仅浪费资源,更是对大气造成严重污染。
焦炉煤气中的H2、CO、CH4、C2H6,是可燃气体,使焦炉煤气可以作为炼焦过程的燃料气体,但还有一些杂质,比如焦油、笨、萘、无机硫、有机硫、氨、氰化氢等,会造成环境污染。
二、焦炉煤气初步净化处理工艺(一)焦炉煤气初步净化处理工艺的关键点焦炉煤气初步净化处理的工艺相对复杂,其中比较关键的几道工序包括,脱氨、脱苯和脱硫。
- 1、下载文档前请自行甄别文档内容的完整性,平台不提供额外的编辑、内容补充、找答案等附加服务。
- 2、"仅部分预览"的文档,不可在线预览部分如存在完整性等问题,可反馈申请退款(可完整预览的文档不适用该条件!)。
- 3、如文档侵犯您的权益,请联系客服反馈,我们会尽快为您处理(人工客服工作时间:9:00-18:30)。
作者:范守谦时间:2008-7-8 10:25:53焦炉煤气净化工艺流程的评述范守谦(鞍山焦化耐火材料设计研究院)焦炉煤气净化工艺流程的选择,主要取决于脱氨和脱硫的方法。
众所周知,在炼焦过程中,煤中约有30%的硫进入焦炉煤气,95%的硫以硫化氢的形式存在。
焦炉煤气中一般含有硫化氢6~8g /m3 , 氰化氢 1. 5~2g/m'。
若不事先脱除,就有50%的氰化氢和10%~40%的硫化氢进入氨、苯回收系统,加剧了设备的腐蚀,还会增加外排污水中的酚、氰含量。
含有硫化氢和氰化氢的煤气作为燃料燃烧时,会生成大量SO2和NOx而污染大气。
为了防止氨对煤气分配系统、煤气主管以及煤气设备的腐蚀和堵塞,在煤气作为燃料使用之前必须将其脱除。
20世纪70年代以前,由于焦炉煤气主要供冶金厂作工业燃料,因此,大部分焦化厂的煤气净化工艺都没有设置脱硫装置,而回收氨的装置几乎全采用半直接法饱和器生产硫铵流程。
随着国民经济的发展以及我国环保法规的不断完善和日益严格,在焦炉煤气净化工艺过程设置脱硫脱氰装置和改进脱氨工艺就势在必行。
进入80年代以后,改革开放逐步深入,我国焦化行业和煤气行业相继从国外引进了多种煤气净化装置,国内科技人员在原有基础上也开发研制了新型脱硫工艺,大大推动了我国焦炉煤气净化工艺的发展。
现将几种脱氨和脱硫方法作扼要介绍和论述。
1 氨的脱除1.1 硫铵工艺生产硫铵的工艺是焦炉煤气氨回收的传统方法,我国在20世纪60年代以前建成的大中型焦化厂均采用半直接法饱和器生产硫铵,该工艺的主要缺点是设备腐蚀严重,硫铵质量差,煤气系统阻力大。
随着宝钢一期工程的建设,我们引进了酸洗法生产硫铵工艺,该工艺由酸洗、真空蒸发结晶以及硫铵离心、干燥、包装等三部分组成。
与饱和器法相比,由于将氨吸收和硫铵结晶操作分开,可获得优质大颗粒硫铵结晶。
酸洗塔为空喷塔,煤气系统的阻力仅为饱和器法的1/4,可大幅度降低煤气鼓风机的电耗。
采用干燥冷却机将干燥后的硫铵进一步冷却,以防结块,有利于自动包装。
我院开发的酸洗法工艺也已成功地用于天津煤气二厂。
随着宣钢、北焦的建设,我们还引进了间接法饱和器生产硫铵工艺,该工艺是从酸性气体中回收氨,其产品质量要比饱和器法好,但因在较高温度(100℃左右)下操作,对设备和管道材质要求高,加之饱和器尺寸并不比半直接法小,因此投资高于半直接法。
鞍钢二回收还从法国引进了喷淋式饱和器以代替半直接法的饱和器。
喷淋式饱和器的特点是煤气系统阻力小,设备尺寸也相应减小,硫铵质量有所提高。
但是,不管采用那种生产硫铵的工艺,从经济观点分析,其共同的致命缺点是回收硫铵的收入远远不够支付其生产费用。
1.2 无水氨工艺另一种可供选择的脱氨方法是用弗萨姆法生产无水氨。
弗萨姆工艺是由美钢联开发的,它可以从焦炉煤气中吸收氨(半直接法),也可以从酸性气体中吸收氨(间接法)。
宝钢二期工程是从美国USS公司引进的从焦炉煤气中吸收氨的弗萨姆装置,焦炉煤气导入吸收塔,,体气体xn磷酸铵溶液与煤气直接接触,吸收煤气中的氨,然后经解析、精馏制取产品无水氨。
该工艺主要是利用磷酸二氢铵具有选择性吸收的特点,从煤气中回收氨,并精馏制得纯度高达99. 98 %的无水氨。
但由于介质具有一定的腐蚀性,且解吸、精馏操作要求在较高的压力下进行,故对设备材质要求较高。
但该工艺的经济性受生产规模影响较大,规模过小时,既不经济也不易操作。
攀钢焦化厂在引进AS法脱硫的同时引进了间接法弗萨姆法无水氨装置,将脱酸塔顶的酸性气体引入间接法弗萨姆装置的吸收塔,用磷酸溶液吸收酸性气体中的氨。
由于不与煤气直接接触,几乎不产生酸焦油,与半直接法相比,可大大简化分离酸焦油的处理设施。
弗萨姆装置生产的无水氨纯度高,产值也较高,经济效益较好,但储运不方便。
1.3 氨分解工艺催化分解氨的新工艺是由德国斯蒂尔公司开发的。
由于氨和氰化氢的分解。
石家是在还原气氛下进行热裂解,除可防止硫化氢参加反应,还可避免形成NOx庄焦化厂和唐山焦化厂从德国K.K公司引进了该项技术,此工艺是通过AS循环洗涤系统将含有少量硫化氢的氨蒸汽送入氨分解炉中,在镍基催化剂的作用下将NH3和HCN分解,所得分解气体送入余热锅炉中产生蒸汽,冷却后的分解气体再经过第二个直接冷却系统冷却后(热值约2900kJ/m3)掺混到焦炉煤气中。
我院为邯钢焦化厂设计中采用了单独脱氨工艺,将水洗氨、蒸氨后的塔顶氨汽经分缩器后进入氨分解装置进行分解。
催化分解氨的工艺具有经济实用、费用低、尾气可掺入焦炉煤气和无二次污染等优点。
由于从焦炉煤气中制取氨的产品变得越来越无利可图,因此,上述工艺值得重视。
1. 4 三种氨回收工艺的比较根据有关资料报导,在下列基本参数相同的条件下,对上述三种类型的氨回收工艺进行对比分析。
焦炉煤气处理量 10.05万m3/h煤气温度25 ℃煤气压力~14 kPa煤气杂质含量HS 8 g/m32NH6 g/m33HCN 0. 6~0. 7 g/m3(体积) 2%CO2剩余氨水量 55m3/h氨水分析,游离氨 3.5 g/L固定铵 3 g/LS 0.3 g/LH2CO2.5 g/L2HCN 0.2 g/L净化后煤气0.05 g/m3NH3S 0.5 g/m3H2废水含氨 150 mg/ /L三种工艺均包括剩余氨水蒸馏。
在硫铵和无水氨工艺中,煤气进粗苯吸收塔前的终冷也作了考虑。
由于饱和器内压力损失较大,所以鼓风机所增加的能耗也包括在内。
三种脱氨工艺勺原材料、能源消耗和产品的计算结果见表1。
表1 三种脱氨工艺的原材料、能源消耗和产品* 包括约5000Pa压力损失而增加的电能; **包括煤气终冷的耗水量。
表2 三种脱氨工艺的操作费用比较(万元/年)根据表1数据,三种脱氨工艺的投资、维修费用和操作费用的比较结果见表2。
从表2可见,配有氨分解的水洗氨系统,其基建投资和消耗费用较低,但由于氨分解装置没有正式产品,其生产费用较高。
2 硫化氢的脱除和回收目前我国已经建成投产的湿法脱硫工艺有下列几种。
湿式氧化法有以氨为碱源的TH法、FRC法、HPF法和以碳酸钠为碱源的改良ADA法。
湿式吸收法有以单乙醇胺为吸收剂的索尔菲班法和以氨水为吸收剂的AS循环洗涤法。
2. 1 湿式氧化法湿式氧化法可分为以碳酸钠为碱源和以焦炉煤气中的氨为碱源两种,用不同的添加剂作催化剂从煤气中吸收硫化氢。
在氧化过程中,脱硫富液与空气接触,在再生系统中氧化再生。
这种工艺的共同优点是脱硫效率高,但不足之处是硫的产品质量低以及含有副反应生成的硫氰酸盐、硫代硫酸盐和硫酸盐等盐类的废液不允许直接外排,易造成废液处理的困难。
2.1.1以氨为碱源的TH法该技术是宝钢一期工程从日本新日铁公司成套引进的,它由TAKAHAX法脱硫脱氰和HIROHAX法废液处理两部分组成,简称TH法。
脱硫部分采用以氨为碱源、以1, 4-萘醌-2-磺酸钠为催化剂的氧化法脱硫脱氰。
废液处理部分采用高温(273℃ )、高压((7. 5MPa)下的湿式氧化法,将废液中的(NH4)2S2O3及NH4CNS转化为硫铵和硫酸,作为母液送往硫铵装置。
TH法的主要特点是:① 脱硫脱氰效率较高,塔后煤气中H2S和HCN的含量可分别降至200mg/m3和150mg/m3以下。
② 煤气中的HCN在脱硫时生成NH4SCN,在湿式氧化时转化为(NH4)2SO4后随母液送往硫铵装置,因而硫铵产量比其它流程高,但该法必须与生产硫铵装置配套建设。
③ 在脱硫过程中,元素硫的生产量仅能满足生成NH4SCN反应的需要,不析出多余的元素硫,因此不易堵塞设备及管道,操作条件好。
④ 废液处理装置虽然流程简单,占地小,但因其在高温、高压、强腐蚀性条件下操作,所以主要设备的材质要求较高,制造难度大。
⑤ 因吸收所需液气比大,再生所需空气量较大,废液处理的操作压力高,故整个装置电耗大。
⑥ 所需催化剂目前尚依赖进口。
由于以上种种原因,除宝钢使用这套装置外,在其他焦化厂就难以采用。
2.1.2 以氨为碱源的FRC法FRC法脱硫技术是天津第二煤气厂和宝钢焦化三期工程从日本大阪煤气公司引进的。
由FUMAKS-RHODACS法脱硫脱氰和COMPACS法废液焚烧和接触法制浓硫酸等工序组成。
由我院自行设计的FRC装置已成功地用于贵阳城市煤气工程。
该法的主要特点是:① 脱硫脱氰效率高,塔后煤气中的H2S和HCN含量可分别降至20mg/m3及l00mg/m3以下,达到城市煤气要求标准。
② 再生塔采用高效预混合喷咀,再生空气用量可大大降低,因此含NH3尾气可直接兑入吸收塔后的煤气中,省去了再生尾气的处理设备,防止了对大气的二次污染。
③ 所需苦味酸催化剂价廉易得,且消耗少,但因苦味酸属易爆危险品,为其存放带来了极大的困难。
④ 在废液焚烧的同时,煤气中的NH3将有25%~30%遭破坏。
且工艺流程长,占地多,制酸尾气处理不经济。
当制酸装置的规模太小时既不经济,也不好操作。
2.1.3 改良ADA法改良ADA法与原来ADA不同之处是在脱硫液中添加了酒石酸钾钠及偏钒酸钠。
该工艺由脱硫、再生和废液处理组成。
脱硫部分是以碳酸钠为碱源、ADA 为催化剂的湿式氧化法。
梅山焦化厂等大多数焦化厂、城市煤气厂的改良ADA法脱硫装置均配置在粗苯回收装置后,上海浦东煤气厂的改良ADA脱硫装置则配置在粗苯回收装置的前面;废液处理采用了蒸发、结晶法制取粗制Na2S2O3及NaCNS。
改良ADA法脱硫工艺的主要特点是:① 脱硫脱氰效率高,塔后煤气中的H2S和HCN含量分别可达到20mg/m3和50mg/m3以下,可达城市煤气标准。
② 由于是以碳酸钠为碱源,故碱耗大(见表3);此外硫磺质量差,收率低。
因此,综合经济效益差。
③ 因改良ADA法的脱硫装置位于粗苯回收装置后,即在煤气净化流程的末端,这就使解决煤气净化系统设备和管道的腐蚀问题增加了难度。
④ 废液处理流程过长,操作复杂,产品品位低,介质腐蚀性强,故对设备和管道材质的要求高,致使投资高。
表3 改良ADA法煤气脱硫的碱耗(kg碱/t硫磺)2.1.4 以氨为碱源的HPF法HPF法是采用HPF高效催化剂和以氨为碱源的新型脱硫工艺。
该工艺由我院与无锡市焦化厂共同合作开发,并已于1996年10月通过了技术鉴定。
该工艺采用的HPF (Hgdroquinone、PDS、Ferrous Sulfate)催化剂为复合催化剂,与其它催化剂相比,它对脱硫和再生过程均有催化作用(脱硫过程为全过程控制步骤)。
并具有较高的活性和较好的流动性。
废液处理采用回兑到炼焦煤中的办法。
从国内外含硫的铵盐废液回兑配煤的研究表明,废液回兑配煤后对焦炭质量影响不大,只是使配煤的水分增加了0.4%~0. 6%,其盐类在焦炉内热裂解产生硫化氢,绝大部分又转入煤气中,因此焦炭含硫量增加极少(一般仅为0.03%~0.05%),焦炭强度和耐磨性无明显变化。