工厂配料称量误差标准
混凝土配料秤(称重系统)检定规程
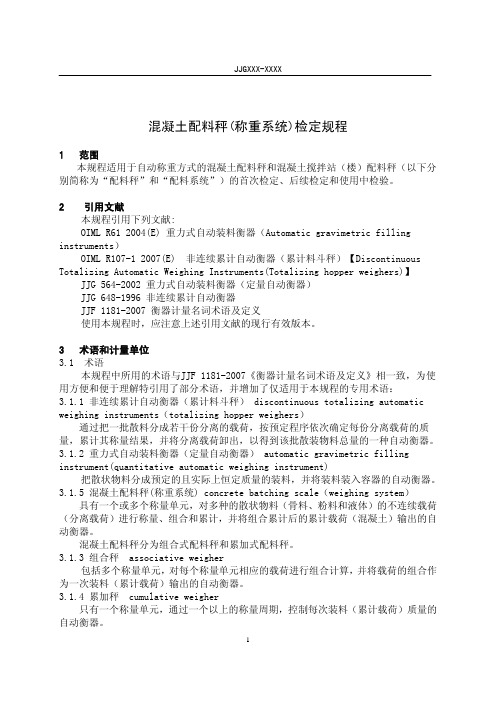
置零准确度
静态称量
偏载
鉴别力
7.3.3 物料检定
+
+
+
注:“+”表示应检项目,“-”表示可不检项目。
7.3 检定方法 7.3.1 外观检查
5 计量性能要求 5.1 准确度等级
配料秤的准确度等级划分为4个等级,用符号表示为:0.5,1,2, 5。 5.2 最大允许误差 5.2.1 自动称量
最大允许误差应是表1中累计载荷(装料)质量的百分数,可将其化整到最接近于 累计分度值(dt)的相应值。最大允许误差不适用于小于最小累计载荷(Σmin) 的装料。
3
JJGXXX-XXXX
给料装置的设计应能保证物料流量充足且稳定。
6.5 安装
配料秤应装配完整,并在使用位置固定。应保证无论是检定,还是实际使用,其
自动称量是相同的。
6.6 说明性标志
在配料秤的某一个醒目位置,有下列说明性标志。
·计量器具制造许可证的标志、编号
·配料秤的名称
·制造厂名称或商标
·配料秤的型号和序列号
表 1 自动称量的最大允许误差 MPE
准确度等级
累计载荷(装料)质量的百分数(%)
检定
使用中
0.2
0.4%
0.5%
0.5
0.8%
1.0%
1
1.6%
2.0%
2
4.0%
5.0%
注:若需要,可表中的数值化整到最接近的分度值倍数
5.2.2 静态称量 静态称量的最大允许误差应符合表2的规定。
2
JJGXXX-XXXX
公式,可得:
P=(100+0.5-0.3)kg=100.2kg
配料秤校正标定方法(试行)

配料秤校正标定方法(试行)配料是水泥生产最重要的环节,其优劣决定了产品质量的好坏和生产效益的高低,而配料皮带秤作为主要设备,在物料的输送过程中要完成对物料的称重,其准确度、可靠性和稳定性是控制的关键,为此须定期对配料秤进行校正和标定。
一、空称去皮配料秤在首次安装时、调节皮带张紧度或更换皮带后、更换传感器后、标定系数与正常比偏差±10%时,均应执行空称去皮程序。
其步骤如下:1、打死下料插板,空称运行5分钟,检查称体灵活性,皮带运行情况,计量托辊、十字簧片和传感器的接触面;2、现场仪表做好各参数记录,进入去皮程序后去皮;3、记录好去皮后参数,查找变化原因。
4、停下称体,挂码标定,校重量传感器线性。
根据传感器的量程选择挂码重量,最多挂码重量不得少于传感器量程的70%,根据线性比,至少取五个不同重量点标定,挂码重量与仪表显示重量相比,测试重量传感器的线性。
其误差范围不得大于1%。
二、实物标定工具:磅秤、秒表、计算器、接料盒(斗车)、铁锹、扫把等配料秤实物标定是利用在生产时实测流量,周期为每周一次,由分厂和电仪工段、质控处共同完成,标定步骤如下:1、检查称体运行情况:包括称体计量称架的灵活性;传感器、托辊、皮带运行状态是否良好;物料下料稳定性,仪表数据稳定性,在各项指标运行正常后方能开始标称;2、准备好计量相关器具,校好计量小磅秤;检查下料翻板的灵活,有无漏料等;3、现场仪表做好各参数记录,通知中控,进入实物标定程序;4、在正常运行时,标定人在打开翻板的同时按下秒表(尽量做到同步,减少人为误差),控制好接料时间和接料量,流量小于20T/H的称接料时间为皮带运行一圈,流量在20~40T/H之间的称接料时间为皮带运行3/4圈,流量大于40T/H的称接料时间为皮带1/2圈,收集完取的料称量,计算的流量值和仪表流量值比较,至少两次标定后按计算误差修改参数,在复测一次。
注:根据公司粉磨工艺会要求规定,此类大流量标定为每月一次,其它时候标定取料时间不得低于30S.5、标定完成记录各参数,如显示流量、实际瞬时流量、接料时长、实际物料重量、变频器频率、标定系数等,建立台账,掌握配料秤运行状态供以后对比和更好的查找问题。
工程混凝土配料秤的校准方法
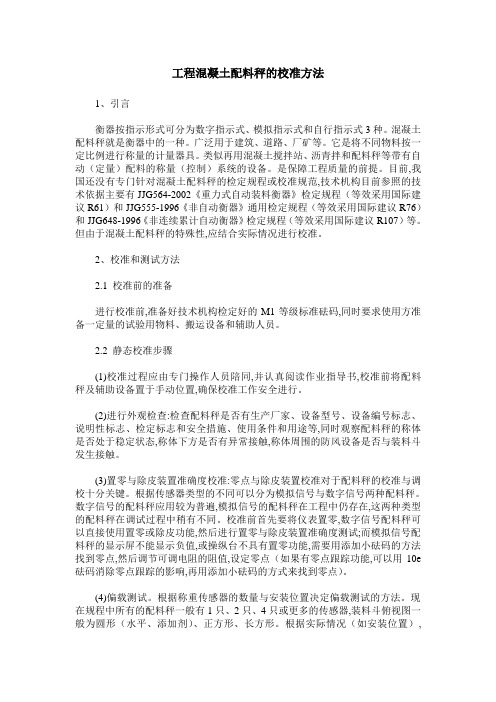
工程混凝土配料秤的校准方法1、引言衡器按指示形式可分为数字指示式、模拟指示式和自行指示式3种。
混凝土配料秤就是衡器中的一种。
广泛用于建筑、道路、厂矿等。
它是将不同物料按一定比例进行称量的计量器具。
类似再用混凝土搅拌站、沥青拌和配料秤等带有自动(定量)配料的称量(控制)系统的设备。
是保障工程质量的前提。
目前,我国还没有专门针对混凝土配料秤的检定规程或校准规范,技术机构目前参照的技术依据主要有JJG564-2002《重力式自动装料衡器》检定规程(等效采用国际建议R61)和JJG555-1996《非自动衡器》通用检定规程(等效采用国际建议R76)和JJG648-1996《非连续累计自动衡器》检定规程(等效采用国际建议R107)等。
但由于混凝土配料秤的特殊性,应结合实际情况进行校准。
2、校准和测试方法2.1 校准前的准备进行校准前,准备好技术机构检定好的M1等级标准砝码,同时要求使用方准备一定量的试验用物料、搬运设备和辅助人员。
2.2 静态校准步骤(1)校准过程应由专门操作人员陪同,并认真阅读作业指导书,校准前将配料秤及辅助设备置于手动位置,确保校准工作安全进行。
(2)进行外观检查:检查配料秤是否有生产厂家、设备型号、设备编号标志、说明性标志、检定标志和安全措施、使用条件和用途等,同时观察配料秤的称体是否处于稳定状态,称体下方是否有异常接触,称体周围的防风设备是否与装料斗发生接触。
(3)置零与除皮装置准确度校准:零点与除皮装置校准对于配料秤的校准与调校十分关键。
根据传感器类型的不同可以分为模拟信号与数字信号两种配料秤。
数字信号的配料秤应用较为普遍,模拟信号的配料秤在工程中仍存在,这两种类型的配料秤在调试过程中稍有不同。
校准前首先要将仪表置零,数字信号配料秤可以直接使用置零或除皮功能,然后进行置零与除皮装置准确度测试;而模拟信号配料秤的显示屏不能显示负值,或操纵台不具有置零功能,需要用添加小砝码的方法找到零点,然后调节可调电阻的阻值,设定零点(如果有零点跟踪功能,可以用10e 砝码消除零点跟踪的影响,再用添加小砝码的方式来找到零点)。
031原料药车间称量、配料岗位标准操作规程

1 目的制定中药车间、综合制剂车间、原料药车间称量、配料岗位的标准操作规程,规范称量、配料岗位人员的具体操作。
2 范围适用于中药车间、综合制剂车间、原料药车间称量、配料岗位的操作过程。
3 职责3.1中药车间、综合制剂车间、原料药车间称量、配料岗位负责实施。
3.2生产技术部、质量部负责监督。
4 内容4.1生产前准备4.1.1 岗位操作人员按照《人员进出生产区更衣标准操作规程》更衣后进入一般生产区或洁净区。
4.1.2 检查:操作间、设备及房间的清洁和状态标识牌;有无前次生产清场合格证正/副本,并在有效期内;设备有无“完好”标志和“已清洁”标志;计量器具有无“计量合格证”,并在有效期内;使用工具是否完好;容器具是否有“已清洁”标志。
检查岗位相关文件及生产记录是否齐全。
环境是否符合要求。
4.1.3 根据批生产指令到物料暂存间领取物料,领取时,认真核对品名、批号、数量、检验报告单等信息。
按物料品名、批号码放整齐。
4.1.4 在器具暂存间领取在清洁效期内的不锈钢桶,内衬洁净塑料袋。
山 东 百 维 药 业 有 限 公 司文件名称 称量、配料岗位标准操作规程文件编号:PM-SOP-031-00起 草 人: 起草日期: 部门:生产技术部审 核 人: 审核日期: 生产副总 页码 1/4 审 核 人: 审核日期: 质量部 版 本 号 00 批 准 人: 批准日期:质量副总生效日期颁发部门 质量部分发部门质量副总、生产副总、质量部、生产技术部、生产车间。
4.1.5 在门前生产标识牌上填写生产品种的相关信息; 4.2 操作过程: 4.2.1 配料4.2.1.1 称量前磅秤调零(一般区配料称量用磅秤或电子称),电子秤、电子天平开机预热15min-20min 后用标准砝码校验,并填写校验记录。
4.2.1.2 将计量器具空载,调至水平并调零。
根据批生产指令、批生产记录进行配料。
4.2.1.3 根据配料量选取合适的计量器具,称量时一人称量,另一人复核。
电子配料秤的单次称量相对误差
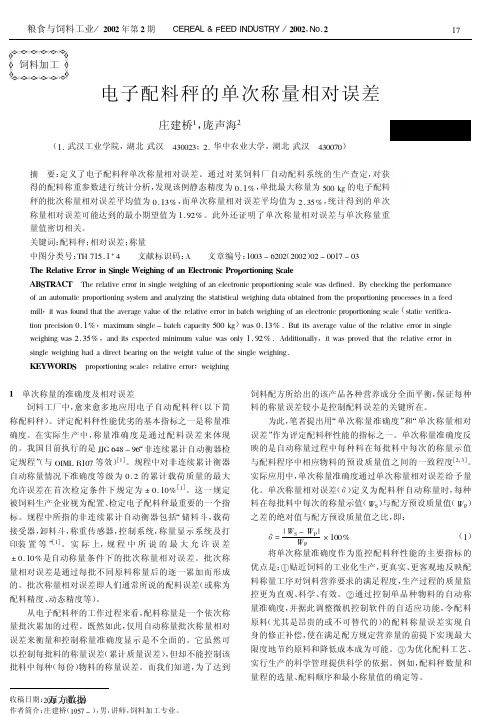
"
"
. 3 0
偏差 $ 为 ( !) $ ’ # ’-& 3 8 8 ’ # ’’& & ! " "13& 这里, ! 反映的是 13& 次单次称量条件下单次称量相对 $ ( !)8 误差的估计值; $ 反映的是 13& 个单次称量相对误差的分散 程度; 是平均值! 的 9 类标准不确定度 (用统计方法得 $ ( !) 出的不确定度) , 反映的是平均值! 分布的分散程度。 如果取置信概率 % 8 ’ # 7!, 查 ’ 分布 ’ : & 8 ! 6 % 8 13%,
整个配料工序采用计算机控制。在生产的同时, 计算机 对称量时间、 称量品种、 称量重量、 称量误差等相关参数同步 记录。在查定的 3’ 批配料称量生产记录中, 单次称量累计 (%) 对原始记录数据逐一计算单次称量相 13& 次。根据公式 对误差。将 13& 个单次称量的原始记录数据按相对误差 ( !) 值由小到大重新排列并进行统计。可以得到: 在 13& 次单次 称量的相对误差中, 相对误差不同值的有 %%! 个, 相对误差 的平均值为 & + 1!, 。其中相对误差为 ’ 的有 &1 个, 相对误 差的最大值为 &-, 。13& 个单次称量相对误差的数量分布 见表 -。 本例 13& 个单次称量相对误差的样本平均值! 为 % ! % 13& ! 8 ! "! ! !" 8 ’ # ’&1 ! " 8 13& ! 8% "8% 13& 个单次称量相对误差的样本标准偏差 $ 为 % ! % 13& & & ( ( !" 6!) 8 13% ! !" 6!) 8 ’ + ’-& 3 ! 6 %"! 8% "8% 13& 个单次称量相对误差的样本平均值 ! 分布的标准 $8
重量偏差允许范围
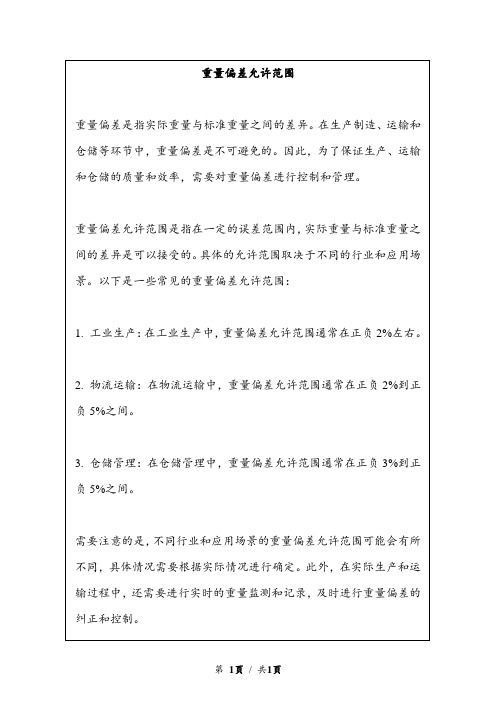
重量偏差允许范围
重量偏差是指实际重量与标准重量之间的差异。
在生产制造、运输和仓储等环节中,重量偏差是不可避免的。
因此,为了保证生产、运输和仓储的质量和效率,需要对重量偏差进行控制和管理。
重量偏差允许范围是指在一定的误差范围内,实际重量与标准重量之间的差异是可以接受的。
具体的允许范围取决于不同的行业和应用场景。
以下是一些常见的重量偏差允许范围:
1. 工业生产:在工业生产中,重量偏差允许范围通常在正负2%左右。
2. 物流运输:在物流运输中,重量偏差允许范围通常在正负2%到正负5%之间。
3. 仓储管理:在仓储管理中,重量偏差允许范围通常在正负3%到正负5%之间。
需要注意的是,不同行业和应用场景的重量偏差允许范围可能会有所不同,具体情况需要根据实际情况进行确定。
此外,在实际生产和运输过程中,还需要进行实时的重量监测和记录,及时进行重量偏差的纠正和控制。
第1页/ 共1页。
lcs配料称标准
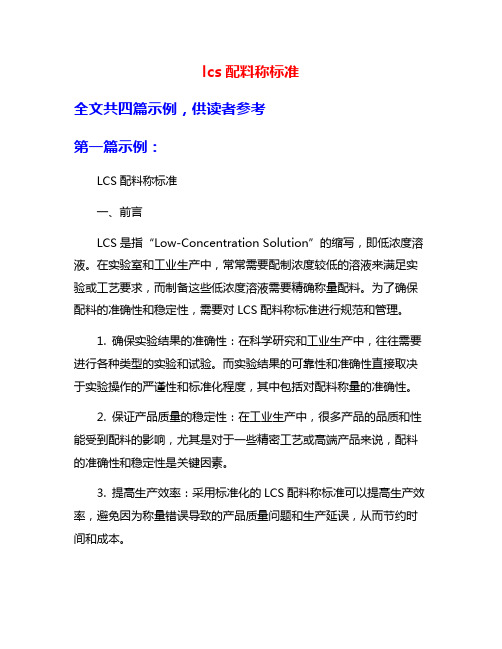
lcs配料称标准全文共四篇示例,供读者参考第一篇示例:LCS配料称标准一、前言LCS是指“Low-Concentration Solution”的缩写,即低浓度溶液。
在实验室和工业生产中,常常需要配制浓度较低的溶液来满足实验或工艺要求,而制备这些低浓度溶液需要精确称量配料。
为了确保配料的准确性和稳定性,需要对LCS配料称标准进行规范和管理。
1. 确保实验结果的准确性:在科学研究和工业生产中,往往需要进行各种类型的实验和试验。
而实验结果的可靠性和准确性直接取决于实验操作的严谨性和标准化程度,其中包括对配料称量的准确性。
2. 保证产品质量的稳定性:在工业生产中,很多产品的品质和性能受到配料的影响,尤其是对于一些精密工艺或高端产品来说,配料的准确性和稳定性是关键因素。
3. 提高生产效率:采用标准化的LCS配料称标准可以提高生产效率,避免因为称量错误导致的产品质量问题和生产延误,从而节约时间和成本。
1. 确定配料称量的精度要求:根据实验或生产的需要确定配料称量的精度要求,一般来说,LCS溶液的精确度要求比较高,通常要求误差在0.1%以内。
2. 确定配料称标的单位:根据实验或生产的需要确定配料称标的单位,一般来说,常用的称量单位有克、毫克、微克等。
3. 确定称量方法和工具:根据配料称量的性质和要求确定称量方法和工具,一般来说,常用的称量方法有天平称量、分注管称量等,工具有电子天平、瓶口分注器等。
4. 制定称量规程和操作规范:根据实验室或生产车间的具体情况,制定配料称标的规程和操作规范,明确称量的步骤和操作要求,加强对操作人员的培训和管理。
1. 配料称标的标准化:建立健全的LCS配料称标准规范体系,明确配料称标的要求、方法、程序和责任,确保每一次称量都能够符合标准要求。
2. 设备的维护和校准:定期对配料称标使用的设备进行维护和校准,保持设备的良好状态和准确度,确保称量的准确性和可靠性。
3. 资料的记录和管理:建立配料称标的档案记录系统,记录每一次称量的配料信息、操作人员、日期、时间等关键信息,便于查证和追溯。
1公斤以下重量的误差标准

1公斤以下重量的误差标准根据不同的物品和应用场景而有所不同。
根据国家重量标准,对于粮食、蔬菜、水果等每公斤价值在6元内的物品,称重1公斤以下的允许20克的误差。
对于肉、蛋、禽、海产品、糕点、糖果、调味品类等,每公斤价值在6元至30元以内的物品,称重为0.5公斤的允许1克的误差,称重为0.5公斤以上至2公斤的允许2克的误差,称重在2公斤以上至5公斤的允许3克的误差。
需要注意的是,具体情况可能会受到不同因素的影响,如物品的性质、计量设备的精度等。
因此,在实际操作中,应根据具体的要求和条件来确定相应的误差标准。
以上信息仅供参考,如需了解更多信息,建议查阅国家相关标准文件或咨询行业专业人士。
- 1、下载文档前请自行甄别文档内容的完整性,平台不提供额外的编辑、内容补充、找答案等附加服务。
- 2、"仅部分预览"的文档,不可在线预览部分如存在完整性等问题,可反馈申请退款(可完整预览的文档不适用该条件!)。
- 3、如文档侵犯您的权益,请联系客服反馈,我们会尽快为您处理(人工客服工作时间:9:00-18:30)。
10kg-50kg(含)
±50g
4
>50kg
±100g
油脂类 注
1
0-100kg(含)
±1kg
使用抽油系统抽料
2
>100kg
±2kg
使用抽油系统抽料
鲜货、泡菜类原料
序号
重量范围
误差值
备 注
1
0-10kg(含)
±50g
2
>10kg
±100g
2
非限量粉类添加剂
±1g
除限量添加剂外
3
0--3kg(含)
±5g
4
3kg-10kg(含)
±10g
5
10kg-30kg(含)
±30g
6
30kg-50kg(含)
±50g
7
>50kg
±100g
半固体、液体原料
序号
重量范围
误差值
备 注
1
液体类添加剂
±5g
包含花椒油树脂、辣椒红、香精等
2
0-10kg(含)
±30g
原料称量误差标准
一、目的
为统一原料在配制过程的误差标准,规范人员操作,特制定本标准。
2、适用范围
适用于配料过程中原料称量的误差要求。
3、职责
1、各工厂配料车间按照标准要求执行、管理;
2、工厂QC负责日常监督查核。
4、称量标准要求
固体、粉类原料
序号
重量范围
误差值
备 注
1
限量粉类添加剂
±0.2g
山梨酸钾、干贝素(琥珀酸二钠)、茶多酚、二氧化硅、乳酸链球菌素等