工艺笔筒塑料注塑成型可能性分析
注塑缺陷原因分析与解决方案
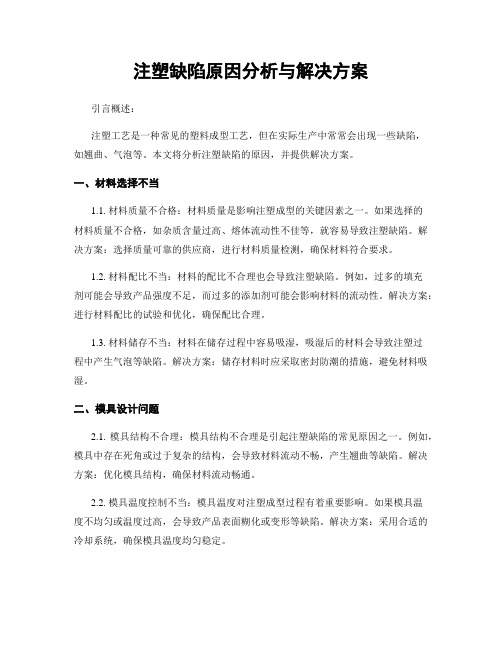
注塑缺陷原因分析与解决方案引言概述:注塑工艺是一种常见的塑料成型工艺,但在实际生产中常常会出现一些缺陷,如翘曲、气泡等。
本文将分析注塑缺陷的原因,并提供解决方案。
一、材料选择不当1.1. 材料质量不合格:材料质量是影响注塑成型的关键因素之一。
如果选择的材料质量不合格,如杂质含量过高、熔体流动性不佳等,就容易导致注塑缺陷。
解决方案:选择质量可靠的供应商,进行材料质量检测,确保材料符合要求。
1.2. 材料配比不当:材料的配比不合理也会导致注塑缺陷。
例如,过多的填充剂可能会导致产品强度不足,而过多的添加剂可能会影响材料的流动性。
解决方案:进行材料配比的试验和优化,确保配比合理。
1.3. 材料储存不当:材料在储存过程中容易吸湿,吸湿后的材料会导致注塑过程中产生气泡等缺陷。
解决方案:储存材料时应采取密封防潮的措施,避免材料吸湿。
二、模具设计问题2.1. 模具结构不合理:模具结构不合理是引起注塑缺陷的常见原因之一。
例如,模具中存在死角或过于复杂的结构,会导致材料流动不畅,产生翘曲等缺陷。
解决方案:优化模具结构,确保材料流动畅通。
2.2. 模具温度控制不当:模具温度对注塑成型过程有着重要影响。
如果模具温度不均匀或温度过高,会导致产品表面糊化或变形等缺陷。
解决方案:采用合适的冷却系统,确保模具温度均匀稳定。
2.3. 模具磨损严重:模具长时间使用后会出现磨损,磨损严重的模具会导致产品尺寸不准确或表面粗糙等缺陷。
解决方案:定期检查和维护模具,及时更换磨损严重的模具部件。
三、注塑工艺参数设置不当3.1. 注射压力过高或过低:注射压力是影响注塑成型的关键参数之一。
如果注射压力过高,会导致产品变形或开裂,而注射压力过低则会导致产品表面光洁度不高。
解决方案:根据产品要求和材料特性,合理设置注射压力。
3.2. 注射速度不合理:注射速度对产品的充填和冷却过程有着重要影响。
如果注射速度过快,会导致产品内部产生气泡或短射,而注射速度过慢则会导致产品表面瑕疵。
笔筒注塑模设计-图文

笔筒注塑模设计-图文材成06彭滔雷陆锋李福军一、塑件的工艺性分析1、塑件的原材料分析塑料品种结构特点使用温度化学稳定性高密度聚乙烯(HDPE)属于热塑性塑料结晶度高、非极性的热塑性树脂使用温度在110℃以下,脆化温度在-70℃以下具有良好的耐热性和耐寒性,化学稳定性好无毒、无味、无臭的白色颗粒该聚合物不吸湿并具有好的防水蒸汽性,可用于包装用途。
HDPE具有很好的电性能,特别是绝缘介电强度高,使其很适用于电线电缆。
中到高分子量等级具有极好的抗冲击性,在常温甚至在-40F低温度下均如此。
还具有较高的刚性和韧性,机械强度好。
介电性能,耐环境应力开裂性亦较好性能特点成型特点熔化温度220~260C。
对于分子较大的材料,建议熔化温度范围在200~250C之间。
加热时间过长易烧伤,并发生费;成型时料温应均匀,宜用高压注射,冲模速度要快,保压应充分成型制品收缩率波动范围大,制品易发生翘曲变形2、塑件尺寸精度分析根据书:p54页表3.4选取塑件尺寸精度为5级塑件外型尺寸:H1080.68mm;L上750.52mm;L下720.52mm;R外20.16mm。
塑件内型尺寸:h1060.68mm;l上730.52mm;l下700.52mm;r内10.16mm。
3、塑件表面质量分析该塑件要求色泽鲜艳,内表面没有斑点及熔接痕,粗糙度可以取Ra=0.4μm。
而塑件外部成型后要进行外包装,所以没有较高的表面粗糙度要求。
4、塑件工艺性分析二、确定成型设备选择与模塑工艺规程编制1、计算塑件的体积和重量计算塑件的重量是为了选择注塑机及确定模具型腔数计算塑件的体积:V=41120ml计算塑件的重量:查书得密度为:ρ=0.94g/cm3所以塑件的重量为M=ρv=38.6528g根据塑件形状及尺寸,采用一模一腔的模具结构,考虑外形所需的压力情况,参考书初选螺杆式注射机:某S-ZY-1252、塑件模塑成型工艺参数的确定查附录D得出工艺参数如下:注射机类型:螺杆式计算收缩率:1.5%~3%预热:(无)后段:180-1890c0料筒温度中段:180-220c0前段:140-160c喷嘴温度:150-1800c模具温度:30-600c注射压力:70-100MPA保压压力:40-50MPA注射时间:2-5保压时间:15-60成型时间()冷却时间:15-60总周期:40-140干燥设备:卧式沸腾温度:90-1000c时间:<0.5h螺杆转速:30r/min3、填写模塑成型工艺卡笔筒模塑工艺卡如下:1、分型面的选择在选择分型面时,考虑不影响塑件的外观质量以及成型后能顺利取出塑件,选择大端面为分型面。
注塑缺陷原因分析与解决方案学习报告

注塑缺陷原因分析與解決方案學習報告一.注塑常見不良現像:缩水、缩孔、不饱模、毛边、烧焦、熔接线、喷痕、银丝、破裂、龟裂、翘曲变形、尺寸偏差.二.縮水、縮孔的主要原因與對策(1)注射压力、保压压力不足、塑胶熔体补缩不足。
(2)保压压力保持时间不足,塑胶熔体补缩不足,同时也容易造成回流(backflow)。
(3)注射速度过慢,塑胶熔体补缩不足。
(4)注射量不足。
(5)料温、模温偏高,冷却慢,塑胶收缩完全而产生收缩下陷。
(6)流道、浇口尺寸偏小,压力损失增大,同时浇口凝固太早,补缩不良。
(7)局部肉太厚。
(8)注塑机的CUSHIONVOLUME不足或止逆阀动作不畅时,产品壁厚均匀也会产生缩水,产品表面有波浪现象。
三.不飽模(1)增加浇口和流道尺寸,使压力有效作用于成型品的肉厚部。
必要时也可调整胶口位置。
(2)提高保压压力、延长保压时间。
(3)提高填充速度,在塑胶冷却固化以前可以达到充分压缩。
(4)射胶转保压太快。
(5)使肉厚变化圆滑些,并提高此部分的冷却效率。
对策---气泡(1)胶粒预先充分干燥除去水份。
(2)料筒温度设定不宜偏高,可有效防止塑料分解气体之产生。
(3)换用小螺杆或机台,防止螺杆产生过剪切。
(4)升高背压,使气体能由料筒排出。
(5)适当降低填充速度,气体有充足时间排出。
原因及对策---不饱模(1) 塑胶材料流动性不好。
流动比L/t。
(2) 制品与注塑机匹配不当, 注塑机塑化能力或注射量不足。
(3) 料温、模温太低,塑胶在当前压力下流动困难。
(4) 塑料熔化不充分,流动性不好,导致注射压力降过大。
(5) 射胶速度太慢。
(6) 射胶时太快转换为保压或保压压力过低。
(7)流道中冷料井预留不足或不当,冷料头进入型腔而阻碍塑胶之正常流动。
(8)流道和浇口太小,流程太长,塑胶填充阻力大。
(9)不平衡排布多腔不平衡充填。
(10)模具排气不良时,空气无法排除。
原因及对策---毛边(1)锁模力不足,射入型腔的高压塑胶使分模面或镶件配合面产生间隙,塑料熔体溢进此间隙。
塑件成型工艺性分析3

一、塑件成型工艺性分析1、塑件的分析(1)外形尺寸该塑件壁厚为3mm,塑件外形尺寸不大.塑件熔体流程不太长.适合于注射成型。
(2)精度等级每个尺寸的公差都不一样.有的属于一般精度.有的属于高精度.就按实际公差进行计算。
(3)脱模斜度 ABS属无定形塑料.成型收缩率较小.选择该塑件上型芯和凹模的统一脱模斜度为1度。
2、ABS的性能分析(1)使用性能综合性能好.冲击强度、力学强度较高.尺寸稳定.耐化学性.电气性能好;易于成型和机械加工.其表面可镀铬.适合制作一般机械零件、减摩零件、传动零件和结构零件。
(2)成型性能1)无定型塑料。
其品种很多.各品种的机电性能及成型特性也各有差异.应按品种来确定成型方法及成型条件。
2)吸湿性强。
含水量应小于0.3%(质量)。
必须充分干燥.要求表面光泽的塑件应要求长时间预热干燥。
3)流动性中等。
溢边料0.04mm左右。
4)模具设计时要注意浇注系统.选择好进料口位置、形式。
推出力过大或机械加工时塑件表面呈白色痕迹。
(3)ABS的主要性能指标其性能指标见下表ABS 性能指标密度/g ·3cm 1.02~1.08 屈服强度/MPa 50 比体积/13-∙g cm 0.86~0.96 拉伸强度/MPa 38 吸水率(%) 0.2~0.4 拉伸弹性模量/MPa 1.4×310熔点/C ο 130~160 抗弯强度/MPa 80 计算收缩率(%) 0.4~0.7 抗压强度/MPa 53 比热熔/1)(-∙∙C kg J ο1470弯曲弹性模量/MPa1.4310⨯3、ABS 的注射成型过程及工艺参数 (1)注射成型过程1)成型前的准备。
对ABS 的色泽、粒度和均匀度等进行检验.由于ABS 吸水性较大.成型前应进行充分的干燥。
2)注射过程。
塑件在注射机料和筒内经过加热、塑化达到流动状态后.由模具的浇注系统进入模具型腔成型.其过程可分为充模、压实、保压、倒流和冷却五个阶段。
注塑件常见品质问题及原因分析报告、解决方法

注塑件常见品质问题及原因分析、解决方法一、注塑件常见品质问题塑胶件成型后,与预定的质量标准(检验标准)有一定的差异,而不能满足下工序要求,这就是塑胶件缺陷,即常说的品质问题,要研究这些缺陷产生原因,并将其降至最低程度,总体来说,这些缺陷不外乎是由如下几方面造成:模具、原材料、工艺参数、设备、环境、人员。
现将缺陷问题总结如下:1、色差:注塑件颜色与该单标准色样用肉眼观看有差异,判为色差,在标准的光源下(D65)。
2、填充不足(缺胶):注塑件不饱满,出现气泡、空隙、缩孔等,与标准样板不符称为缺胶。
3、翘曲变形:塑胶件形状在塑件脱模后或稍后一段时间内产生旋转和扭曲现象,如有直边朝里,或朝外变曲或平坦部分有起伏,如产品脚不平等与原模具设计有差异称为变形,有局部和整体变形之分。
4、熔接痕(纹):在塑胶件表面的线状痕迹,由塑胶在模具内汇合在一起所形成,而熔体在其交汇处未完全熔合在一起,彼此不能熔为一体即产生熔接纹,多表现为一直线,由深向浅发展,此现象对外观和力学性能有一定影响。
5、波纹:注塑件表面有螺旋状或云雾状的波形凹凸不平的表征现象,或透明产品的里面有波状纹,称为波纹。
6、溢边(飞边、披锋):在注塑件四周沿分型线的地方或模具密封面出现薄薄的(飞边)胶料,称为溢边。
7、银丝纹:注塑件表面的很长的、针状银白色如霜一般的细纹,开口方向沿着料流方向,在塑件未完全充满的地方,流体前端较粗糙,称为银丝纹(银纹)。
8、色泽不均(混色):注塑件表面的色泽不是均一的,有深浅和不同色相,称为混色。
9、光泽不良(暗色):注塑件表面为灰暗无光或光泽不均匀称为暗色或光泽不良。
10、脱模不良(脱模变形):与翘曲变形相似,注塑件成型后不能顺利的从模具中脱出,有变形、拉裂、拉伤等、称为脱模不良。
11、裂纹及破裂:塑胶件表面出现空隙的裂纹和由此形成的破损现象。
12、糊斑(烧焦):在塑件的表面或内部出现许多暗黑色的条纹或黑点,称为糊斑或烧焦。
塑料产品注射成型常见问题分析

塑料产品注射成型常见问题分析作者:黄春来源:《科学与财富》2017年第24期摘要:随着经济的不断发展和科学技术的不断进步,塑料已经应用到人们生产和生活的各个方面。
当今社会,人们对塑料制品的需求量越来越大,要求也越来越高,加强注射成型塑料件结构设计的研究,能够提高塑料产品的质量,更好的满足人们对塑料制品的需求。
塑料成型质量的好坏,关键在于模具的设计与制造水平,同时也与原料、成型工艺、设备和塑件结构工艺性等因素密切相关。
本文介绍了在注射成型塑料产品时存在的常见问题以及解决措施。
关键词:塑料产品;注射成型;问题分析0.引言塑料是一种以合成树脂为主要成分,加入适量的添加剂,在一定的温度和压力下制成的混合物,可以用模具成型出具有一定形状和尺寸的塑件,当外力解除后,在常温下仍能保持加工时的形状和尺寸。
在塑料制品生产中,注射成型是最常用的方法之一. 虽然注射成型得到了较为广泛的应用,但是在实际生产中经常出现由于设计经验不足、塑料件结构复杂、注射成型工艺影响因素多等原因造成塑料件不合格. 成型时的各种缺陷造成塑料件的不合格. 常见的塑料件缺陷有:充填不足、飞边、缩孔、气泡、熔接痕等. 造成注塑件这些缺陷的原因非常复杂,有时很多原因相互影响,要准确确定缺陷产生的原因有一定的困难.1 常见问题及措施1.1填充不足熔料进入型腔后在未充满型腔之前即已经固化,导致模腔没有充填完全,尤其在流程末端和薄壁区域容易产生。
这种现象称为填充不足。
其产生原因及解决措施如下:a. 模具原因:模具温度太低或不均;模具排气不良。
解决措施:开机前将模具预热至工艺要求的温度;在模具上加设排气槽,改变浇口的位置。
b. 成型工艺原因:注射压力或保压不足;浇注系统设计不合理;折射周期反常。
解决措施:适当延长注射时间;扩展流道或浇口;调整操作条件。
c. 塑料原因:原料流动性能太差;塑件体积过大。
解决措施:增加适量助剂,改善流动性,改善模具浇注系统;使用成型能力大的注塑机。
工艺笔筒塑料注塑成型可能性分析

题:分析自己工艺笔筒塑料注塑成型的可能性
解:
(1)分析分型面的位置
将分型面选择在笔筒中间剖切面上。
这样,不致影响塑件外观,既有利于脱模(注:
分型面应使塑料件在开模时留在有脱模机构的一边,通常是在动模一侧。
),又使
模具的加工制造更容易。
分型面设计
(2)是否需要侧抽芯
我的这个工艺笔筒注射成型侧壁带有孔、凸台等的塑料制件时,模具上成型该处
的零件就必须制成可侧向移动的零件,以便衣脱模之前先抽掉侧向成型零件,否
则就无法脱模。
带动侧向成型零件作侧向移动的整个机构称为侧向分型与抽芯机
构。
对于成型侧向凸台的情况,常常称为侧向分型,对于成型侧孔或侧凹的情况,
往往称为侧向抽芯。
因此需要侧抽芯。
(3)浇口位置的确定
浇口位置一般应选在制品最厚而又不影响外观的地方。
箭头所指的位置为笔筒中最厚的位置,可以选择此处为笔筒的注塑的浇注口
附图
101403126 赵丽娜。
塑件成型工艺性分析
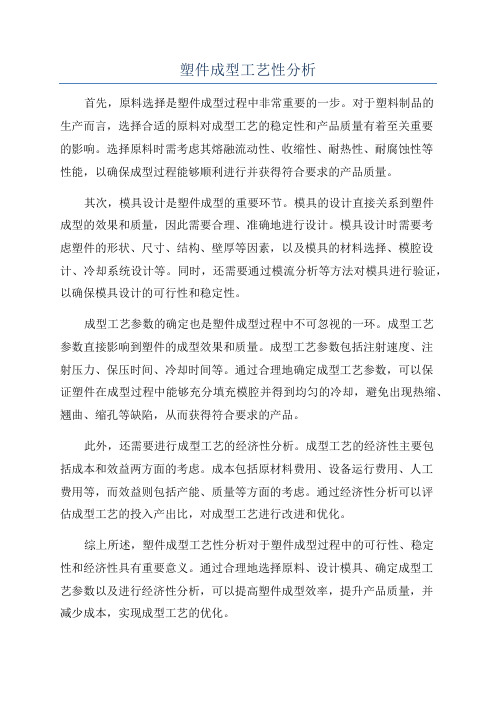
塑件成型工艺性分析首先,原料选择是塑件成型过程中非常重要的一步。
对于塑料制品的生产而言,选择合适的原料对成型工艺的稳定性和产品质量有着至关重要的影响。
选择原料时需考虑其熔融流动性、收缩性、耐热性、耐腐蚀性等性能,以确保成型过程能够顺利进行并获得符合要求的产品质量。
其次,模具设计是塑件成型的重要环节。
模具的设计直接关系到塑件成型的效果和质量,因此需要合理、准确地进行设计。
模具设计时需要考虑塑件的形状、尺寸、结构、壁厚等因素,以及模具的材料选择、模腔设计、冷却系统设计等。
同时,还需要通过模流分析等方法对模具进行验证,以确保模具设计的可行性和稳定性。
成型工艺参数的确定也是塑件成型过程中不可忽视的一环。
成型工艺参数直接影响到塑件的成型效果和质量。
成型工艺参数包括注射速度、注射压力、保压时间、冷却时间等。
通过合理地确定成型工艺参数,可以保证塑件在成型过程中能够充分填充模腔并得到均匀的冷却,避免出现热缩、翘曲、缩孔等缺陷,从而获得符合要求的产品。
此外,还需要进行成型工艺的经济性分析。
成型工艺的经济性主要包括成本和效益两方面的考虑。
成本包括原材料费用、设备运行费用、人工费用等,而效益则包括产能、质量等方面的考虑。
通过经济性分析可以评估成型工艺的投入产出比,对成型工艺进行改进和优化。
综上所述,塑件成型工艺性分析对于塑件成型过程中的可行性、稳定性和经济性具有重要意义。
通过合理地选择原料、设计模具、确定成型工艺参数以及进行经济性分析,可以提高塑件成型效率,提升产品质量,并减少成本,实现成型工艺的优化。
- 1、下载文档前请自行甄别文档内容的完整性,平台不提供额外的编辑、内容补充、找答案等附加服务。
- 2、"仅部分预览"的文档,不可在线预览部分如存在完整性等问题,可反馈申请退款(可完整预览的文档不适用该条件!)。
- 3、如文档侵犯您的权益,请联系客服反馈,我们会尽快为您处理(人工客服工作时间:9:00-18:30)。
题:分析自己工艺笔筒塑料注塑成型的可能性
解:
(1)分析分型面的位置
将分型面选择在笔筒中间剖切面上。
这样,不致影响塑件外观,既有利于脱模(注:
分型面应使塑料件在开模时留在有脱模机构的一边,通常是在动模一侧。
),又使
模具的加工制造更容易。
分型面设计
(2)是否需要侧抽芯
我的这个工艺笔筒注射成型侧壁带有孔、凸台等的塑料制件时,模具上成型该处
的零件就必须制成可侧向移动的零件,以便衣脱模之前先抽掉侧向成型零件,否
则就无法脱模。
带动侧向成型零件作侧向移动的整个机构称为侧向分型与抽芯机
构。
对于成型侧向凸台的情况,常常称为侧向分型,对于成型侧孔或侧凹的情况,
往往称为侧向抽芯。
因此需要侧抽芯。
(3)浇口位置的确定
浇口位置一般应选在制品最厚而又不影响外观的地方。
箭头所指的位置为笔筒中最厚的位置,可以选择此处为笔筒的注塑的浇注口
附图
101403126 赵丽娜。