SPS生产管理
SPS系统总装车间运行方式分析
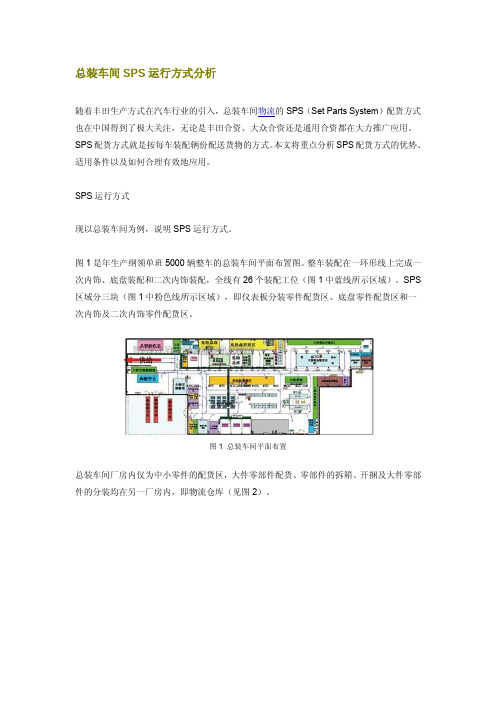
总装车间SPS运行方式分析随着丰田生产方式在汽车行业的引入,总装车间物流的SPS(Set Parts System)配货方式也在中国得到了极大关注,无论是丰田合资、大众合资还是通用合资都在大力推广应用。
SPS配货方式就是按每车装配辆份配送货物的方式。
本文将重点分析SPS配货方式的优势、适用条件以及如何合理有效地应用。
SPS运行方式现以总装车间为例,说明SPS运行方式。
图1是年生产纲领单班5000辆整车的总装车间平面布置图。
整车装配在一环形线上完成一次内饰、底盘装配和二次内饰装配,全线有26个装配工位(图1中蓝线所示区域)。
SPS 区域分三块(图1中粉色线所示区域),即仪表板分装零件配货区、底盘零件配货区和一次内饰及二次内饰零件配货区。
图1 总装车间平面布置总装车间厂房内仅为中小零件的配货区,大件零部件配货、零部件的拆箱、开捆及大件零部件的分装均在另一厂房内,即物流仓库(见图2)。
图2 物流仓库平面布置1.配货顺序总装车间的物流系统在信息控制系统指导下,有条不紊地从仓库货架取出所需零件,按SPS 配货方式送到指定工位,配货顺序如下:(1)中央控制室(CCR)根据市场分析及订单情况安排生产计划,并将生产计划的车辆顺序信息向总装车间情报中心传递。
(2)车辆顺序信息传到总装车间情报中心,由情报信息员根据实际工位查找相应信息指示卡。
(3)情报信息员将信息指示卡投递到SPS供应管理板处。
(4)物流配货人员从SPS供给管理板处获取信息选取配货指示票,配货指示票上标有某个车型在某个工程装配零件的种类和数量。
(5)物流人员按照配货指示票到SPS区配货,放在相应的台车上,物流人员将部品放到运输台车上。
(6)配完后放在供给待发区,物流人员将零件供给到生产线的起始位置。
(7)物流人员将空台车返回到零件供给待发区,通过SPS方式配货完成。
2. 物料配送的四个步骤在图3的SPS物料及信息流程图中我们可以看到,所有的物料都是经过四个步骤完成运送的:接收物料需求信息(图3中①);按需求信息进行配货(图3中②);将配货送到装配线的接收端(图3中③);随装配线完成装配工序(图3中④)。
SPS之质量管理最新

最新课件
31
3)如何正确取得和分析数据
样品
能够起参考作用,有代表性
数据
弄清楚“什么时候、什么地方、 做什么、为什么、怎么做”
最新课件
32
• 图表的运用——常用的几种图表:
图表
90 80 70 60 50 40 30 20 10
0 第一季度
第二季度
第三季度
第四季度
东部 西部 北部
帕累托图
90% 80%
最新课件
13
② 作业指导书(QSOS、装配工艺卡、作业要领书等) 说明
· 作业人员所使用的工具 · 找出工作中问题点的重要基准 · 实现目视管理
最新课件
14
③作业人员的工具: 作业人员的基本依据是作业要领书 “基本”是什么意思
忠实地遵守,不会出现不良、劳动伤害 (实现安全生产、高效、高质量)
生产出同样质量的产品
最新课件
7
(5)基础设施管理程序: 通过维护确保生产设备、工装模具、处于完好 状态,同时创造合理的工作环境、确保过程能 力、从而达到产品质量能持续的满足规定要求。
(6)过程检验控制程序: 通过对生产过程中影响产品质量各因素的控
制, 确保产品满足规定要求、防止不合格品的流出。
(7)检测试验设备管理程序: 计量器具、试验设备的管理,保证其准确度, 使之处于受控状态。
设备故障
最新课件
24
确认、指导 记录、联络 检查
对策
最新课件
25
五、班长是工序控制的主力
• 班组长是基层的管理者、直接面对员工,日常工 作中,要有耐心、细心、善于观察、(作业方法、 作业状态、设备工艺参数、)并能够从观察中发 现问题解决问题。
SPS单台物料动态拣配管理模式在工程机械行业的研究及应用

SPS单台物料动态拣配管理模式在工程机械行业的研究及应用广西柳工机械股份有限公司摘要:针对工程机械行业企业装配制造业务找取料效率低、BOM与工位数据差异、错漏装、装配线边物料多等现况,结合工程机械行业装配物料批量小品种多的特点,研究出适合工程机械装配制造的SPS单台物料动态拣配管理模式。
在装载机装配过程中采用SPS单台物料动态拣配管理模式后,不但对装配过程起到防错作用,达到在线控制质量的目标;还能满足多品种单线生产的柔性化要求,节约线边物料占地面积;降低装配物料定位的难度,使缺件得到及时发现;提高装配效率,将装错风险显著降低,避免重大装配质量事故的发生。
SPS单台物料动态拣配管理模式为今后在工程机械行业企业逐步构建精益物流体系提供重要参考。
关键词:SPS;SPS单台物料动态拣配;电子拣选系统1 概述1.1 装载机装配制造业务厂内传统物流模式装载机装配制造业务的厂内传统物流模式主要是以批量上线为主,以器具按工位拣配一天的物料量存放于装配线旁。
因一种物料量会占用一个器具或一定量组合量存于器具上,造成装配线边配送物料器具用量多、占的面积大,形成装配线边库,员工往返于装配线边各种物料器具拿取物料,效率非要低,同时物料带包装上线,拣料及流转过程中极易磕碰、出错。
而随着市场对工程机械产品品种多样性、个性化的需求增多,工程机械产品的品种和产量也越来越大,物料的规格也越来越多,产品间的物料差异越来越大,装载机装配制造业务的装配线边库管理越来越复杂。
1.2 装载机装配制造业务厂内单台物料SPS配送模式的探索和运用物料批量配送方式已经无法适应多品种小批量的装配业务需要,需要建立满足柔性化装配需求的物料配送方式来快速应对不同需求的变化,即最佳的柔性化物料配送方式——单台物料SPS配送模式,物料选择和空箱返回在SPS拣配区进行操作,装配员工只负责在随行的SPS物料小车拿取物料装配。
单台物料SPS 配送的含义:按SPS(Set Parts Supply)物料单台套供应,物料有序地从SPS 分拣区超市料架上取下,按照SPS配货方式送到指定工位[1],即集中必要数量的物品,在必要的时间将必要的物料配送到必要的地点。
汽车行业厂内精益物流、精益生产(三) SPS规划要点

汽车行业厂内精益物流、精益生产(三) SPS规划要点精益管理顾问 宋文强 (原创)SPS单辆份成套供应是一种非常符合精益理念的物料上线方式,与批量补货、线边暂存相比,更有小批量(单辆份)、准时化(同步上线、物料随行)等特点。
但是,SPS在企业中的应用不是一蹴而就的,需要进行详细规划、精心准备才行。
第一,确定需要实施SPS的零部件不是所有零件都适用SPS,一般讲,体积较小或中等,有装配关系,且质量稳定的专用零部件比较合适。
通用零部件和标准件不容易拿错,所以可以不采用SPS。
因为SPS是一种管理成本比较高的补货方式,所以SPS同步台车容量有限的情况下,可以不优先考虑。
体积太大,像座椅等,不适合物料随行,可以采用JIS同步顺序上线方式。
质量稳定很重要,由于一次只供应单辆份零部件,发现质量问题后没有可供更换的同种零部件。
考虑到零部件的这些特点,一般来讲,企业先推进SPS的生产线是内饰线和车门线中的一部分工位。
第二,设计物料台车和料箱确定了要推进SPS的工位和物料,就要考虑设计物料台车和料箱。
由于是单辆份供应,所以数量不需要太多计算,但放置方法是个大问题。
总体来讲,料箱的外部大小要基本一致或只有几种规格,这样便于料箱与台车的配载。
需要精心设计的是料箱内部的隔断方法或衬垫形式。
首先,质量总是最重要的,汽车行业尤其如此,所以物料在拣配过程、搬运过程、拿取装配过程,要不容易磕碰。
其次,零部件放置既要放置整齐、节省体积,又要便于配载、拿取。
再次,类似零部件不能容易拿错,所以,车身左侧零部件和车身右侧零部件有时需要用可视化的方法进行区分。
比如:在丰田,绿色料箱放置车身左侧的零部件,蓝色料箱放置车身右侧的零部件。
物料台车的设计也很重要,一般为多层设计,既要容纳较多料箱,又要保证在搬运、随行的过程中保持稳定性和通过性。
第三,确定拣配区域位置SPS拣配区域的确定是个较大的决策,需要高层领导拍板。
SPS拣配区域的位置决策有两种:一种是相对集中式,另一种是分散式。
物流--“SPS推进”步骤
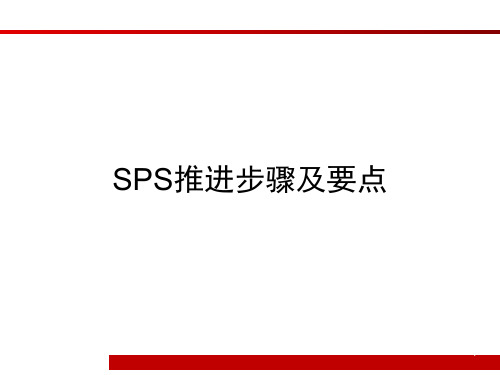
5
三、SPS推进步骤二:前期调研
1.设备情况 ① 随行台车与生产线联动 板链:台车置于两台车身之间 非板链:台车置于线侧,与生产线联动 ② PVC板、线棒的提供商,用于器具制作
2.T-A储存线在制情况 用于计算SPS配台提前期,判断SPS实施的生产线范围
3.物流仓库 确定SPS配台区域
4.IT系统 现有生产系统、物流系统的功能
2S0PS台2划.车 要开 连 员计接 包划时 :装间袋口(一袋)
0
秒/回
3秒
2空 2 箱返开还关时器 间 具门(包含0四8/1个 月 开1周关2)周 25月3周
秒/箱 3月10 秒
4周 1周 2周 3周 4周 1周
4月
2周 3周
4周
1周
5月
2周 3周
4周
1周
6月
2周 3周
4周
1周
7月
2周 3周
4周
7
四、SPS推进步骤三:基础数据的建立(SPS前提)
3.实施SPS部品明细筛选 ① 生产线选择:底盘线不可;生产提前期<物流周期不可 ② 部品选择:大物、标准件不可
4.部品明细的维护管理 ① 专门部门、专门担当负责部品明细的管理 ② 前期建立流程贯彻实施
此步骤是实施SPS的前提,也是保证配送准确率的前提
确定质量检查 时间
确定标准 在制品
编制标准作业 组合表
确定节拍内工 作顺序
确定安全注意 事项
编制标准 作业卡
细化操作 要点
编制标准 要领书
14
类别 1.行走
序号
操作描述பைடு நூலகம்
14 行走(每米)
15 行走(每步)
原单位 0.9 秒 0.6 秒
汽车行业SPS简述
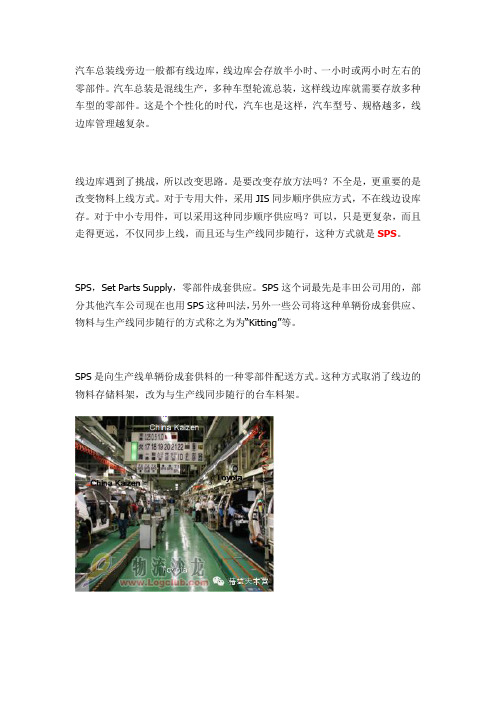
汽车总装线旁边一般都有线边库,线边库会存放半小时、一小时或两小时左右的零部件。
汽车总装是混线生产,多种车型轮流总装,这样线边库就需要存放多种车型的零部件。
这是个个性化的时代,汽车也是这样,汽车型号、规格越多,线边库管理越复杂。
线边库遇到了挑战,所以改变思路。
是要改变存放方法吗?不全是,更重要的是改变物料上线方式。
对于专用大件,采用JIS同步顺序供应方式,不在线边设库存。
对于中小专用件,可以采用这种同步顺序供应吗?可以,只是更复杂,而且走得更远,不仅同步上线,而且还与生产线同步随行,这种方式就是SPS。
SPS,Set Parts Supply,零部件成套供应。
SPS这个词最先是丰田公司用的,部分其他汽车公司现在也用SPS这种叫法,另外一些公司将这种单辆份成套供应、物料与生产线同步随行的方式称之为为“Kitting”等。
SPS是向生产线单辆份成套供料的一种零部件配送方式。
这种方式取消了线边的物料存储料架,改为与生产线同步随行的台车料架。
刚开始,SPS成套供应主要应用在在内饰线和车门线等,因为这两条线的零部件具有体积大、重量轻、配置多、颜色件多等特点,线边存放占用面积较大,操作人员拣选麻烦。
随着对SPS的应用越来越熟悉,慢慢就扩展到底盘线、发动机装配线等。
为什么SPS这种方式越来越多地被汽车企业采用呢?首先,由于SPS是单辆份成套供应,所以,降低了取料错误的可能性,提高了装配质量和装配效率。
中国汽车行业增长较快,车间新手较多,这种降低拣料、装配复杂度的方法能有效减少新手的学习时间。
其次,SPS单辆份成套供应还降低了生产线操作人员拣选物料的时间。
同时,由于零部件是与生产线同步随行,物料箱可以放在操作人员身边,不需要走出装配区域去取物料,这同样提升了装配效率。
装配效率的提升会导致装配节拍的降低,这对生产线资源紧缺的汽车总装来讲非常重要,因为同样的生产线在不扩产的情况下可以生产出更多的车辆了。
再次,由于SPS采用同步顺序上线和物料随行方式,所以节省了线边库的占用。
物流--“SPS推进”步骤
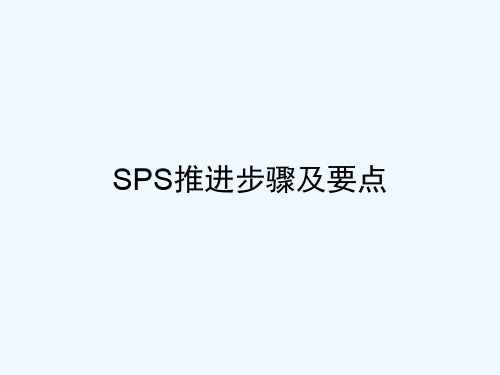
② 大日程点检是项目推进的手段
纲领 计划 目标 里程碑
大日程点检是确保项目按计划顺利推进的手段,以大日程点检为 载体,使信息在各领域充分共享,达到沟通、协调的目的
③ 以周为单位的推进日程
④ “五步工作法”
提出
物流项目第 一次大会
明确提 出∶“五步工 作法是物流项 目推进的工作 方法”
五步工作法
SPS推进步骤及要点
一、SPS推进条件
1.体制保障:公司全体部门统一认识·参与 ① SPS对公司的优势 ② SPS带来的人员、设备设施的投入
2.对部分业务流程的现状进行变革 SPS是内物流方式的一种,最为精确,要求基础管理的水平 ① 部品明细管理 ② 生产管理 ③ 设变管理 ④ 装配工艺管理 ⑤ 部品质量管理
二、SPS推进步骤一:推进方法建立
1.推进体制搭建 ① 直管生产副总作为项目组领导 ② 制造技术部作为推进部门 ③ 体制含:总装、技术、质量、IT、人力、采购部门,确定负责人
2.推进方法的建立 ① 会议:月度例会+周例会 月度例会:副总及高级经理参加 周例会:项目担当参加 ② 大日程+课题管理表
3.大日程编制 ① 大日程管理是项目推进的工具
李项
杨熙宏 殷学龙
日期 2008.4.6 2008.4.6 2008.4.6 2008.4.6 2008.4.6 2008.4.6 2008.4.6 2008.4.6 2008.04.06 物流项项目 目主主查查HQ3生管物流科人H事 Q3总部装车间 工工 业工业程工 科 程整科车物流组供应计物划信流息组组 供应构物内 流组物流内组物流组 主担 主担当当
1.信息指示类别: 是指示物流作业的一种信息表达方式,包括:零件配货指示、配货作业节拍
物流--“SPS推进”步骤

HLEAN SYSTEM 幸福·精益 高效企业管理系统!
以提案的形式与所有干系人进行确认, 直至全面达成共识
把合意结果完善到最初提案中,形成 决裁;决裁经各部门领导会签生效
将会签后的决裁在所有干系人之间展 开,以此来推进相应工作
将目标达成情况反馈给大家,总结经 验教训
我们关注企业的愿景,是帮助企业提升竞争力的发动机!
5
HLEAN SYSTEM 幸福·精益 高效企业管理系统!
我们关注企业的愿景,是帮助企业提升竞争力的发动机!
6
HLEAN SYSTEM 幸福·精益 高效企业管理系统!
四、SPS推进步骤三:基础数据的建立(SPS前提)
1.部品明细 ① 技术数据:部品编号、名称、单台用量 ② 采购数据:供应商名称、代码、供货比例 ③ 路径数据:仓库地址、存放地址、工位 ④ 包装数据:包装类别、尺寸、收容数、重量
二、SPS推进步骤一:推进方法建立
1.推进体制搭建 ① 直管生产副总作为项目组领导 ② 制造技术部作为推进部门 ③ 体制含:总装、技术、质量、IT、人力、采购部门,确定负责人
2.推进方法的建立 ① 会议:月度例会+周例会 月度例会:副总及高级经理参加 周例会:项目担当参加 ② 大日程+课题管理表
我们关注企业的愿景,是帮助企业提升竞争力的发动机!
3
HLEAN SYSTEM 幸福·精益 高效企业管理系统!
3.大日程编制 ① 大日程管理是项目推进的工具
纲领
项目
计划
目标
② 大日程点检是项目推进的手段
里程碑
大日程点检是确保项目按计划顺利推进的手段,以大日程点检为 载体,使信息在各领域充分共享,达到沟通、协调的目的
- 1、下载文档前请自行甄别文档内容的完整性,平台不提供额外的编辑、内容补充、找答案等附加服务。
- 2、"仅部分预览"的文档,不可在线预览部分如存在完整性等问题,可反馈申请退款(可完整预览的文档不适用该条件!)。
- 3、如文档侵犯您的权益,请联系客服反馈,我们会尽快为您处理(人工客服工作时间:9:00-18:30)。
庫存是企業的墓場
8.月底趕貨的庫存:為達本月份生產目標 拼命工作加班,在各製程間積壓很 多在製品庫存,庫存越多,資訊錯誤 機會越多,庫存又增加,造成惡性循 環。 9.生產參數錯誤:採購前置日,基本訂購量 提前製造日…等錯誤造成的庫存
庫存是企業的墓場
10.顧及安全的庫存:因怕發生欠品,額外準 備的庫存,以備不時之需,又稱 “安心庫存”。 11.季節變動的庫存:在淡季時,預先生產儲 存以應付旺季需求,所造成的庫存。
效率的認識
假效率:固定的人員做出更多產品的方式 多生產出的產品,還沒賣出,不但毫 無利潤,必頇增加管理成本,甚至造 成呆滯。 真效率:以最少人員,僅做出市場需要的產 品數量。
效率的認識
二、每個人做的越多越好嗎? —個別效率與全體效率 個別效率:以個別作業者評估效率 全體效率:以配置人員的多寡評估效率 例: 某製程標準為100個/hr第一工程 100 個/hr,第二工程125個/hr,第三工程90個/hr 試問全體效率為何?個別效率為何?
流線化生產的八個條件
條件二:按製程順序佈置設備
為減少運搬的浪費,將機器設備 拉攏,依照產品別加工製造所需 的機器設備,按加工順序排列佈 置。
流線化生產的八個條件
條件三:生產速度的同步化
若各製程的生產速度不一致,會在 各個製程中形成在製品的堆積,破 壞了單件流動的順暢性 ,故必頇將 各製程的生產速度都保持在相同 速度,稱“同步化”
流線化的生產
意義:依產品別將機器設備,依製程加工順 序,前製程做完,即刻流到下製程繼續 加工,迄完成一個產品為止。 例:A/C生產線,O/F生產線 優點:1.製程間無運搬距離 2.在製品數量可以大幅減少 3.生產空間減少 4.製程時間大幅縮短 5.不良品一旦發生,可立即被發覺出來
效率的認識
三、要動則動,該停則停 —稼動率與可動率 稼動率:設備實際產量/設備最大產量 稼動率不是越高越好, 是以需要量 決定(不追求100%) 可動率:設備要被使用時, 都能被用的機率 故要建立良好維修保養制度 及全員生產保全活動 (要追求100%)
庫存是企業的墓場
SPS生產管理Senate Production System
林克超 2011/12/09
SPS生產管理
流線化生產-ONE PICES FLOW(一個流) 安定化生產-人、機、質、量、管的安定 平穩化生產-生產平準化、序列生產 計畫 超市化生產-後拉式生產、看板傳票生產 及時化生產-JIT(Just In Time)、臨界生產 消除浪費 創造利益
不良品的浪費
意義:無法將購入價值,轉成商品出售 內容:1.製程不良 2.客戶退回不良 3.倉庫報廢不良 4.盤損 5.超領 6.客戶索賠
動作的浪費
意義:製程上無附加價值的動作 內容:1.拿上、拿下 2.沒必要的反轉 3.沒必要的步行 4.彎腰、對準 5.過長距離的拿取部品
流線化生產與批量生產的差別
3.在製品的流向 批量化生產:以一個批量為單位,由前一 個製程流向下一個製程,每一批在 製品都有可能在每一台機器間流動 又稱“亂流方式” 流線化生產:以產品別建立的生產線,製 品的流向很清楚,又稱“整流方式”
ቤተ መጻሕፍቲ ባይዱ
流線化生產與批量生產的差別
4.機器設備選用 批量化生產:考慮泛用機器,強調高速度, 高產能,強調高稼動率,無形中產生 製造過多的浪費
流線化生產:注重速度適當穩定,品質好 的專用機械,強調可動率
流線化生產的八個條件
基本想法:在避免製造不良品的同時,將生 產流程一個一個的製造出來。 條件一:單件流動 1. 僅做一個,傳送一個,檢查一個, 將製品一個個加工而做成成品 2.一種將“浪費顯在化”的思想與 技術
製造過多(早)的浪費
意義:非顧客要買的數量與時間前的製造 內容:1.提早用掉材料費,人工費 2. 隱藏“等待的浪費”,漠視等待存 在 3.製程的時間變長 4.現場工作的空間變大 5.機器間的佈置距離變長 6.產生搬運的浪費
效率的認識
一、效率提高了怎麼沒賺錢? —假效率與真效率 假設:某產品需要量100個/每日,投入10 人,才能產出100個 假效率:改善同樣10人,一天可生產125個, 效率可提升25%,反而成本增加,何故? 真效率:改善減少為8人,一天生產100個
造成庫存原因 1.時代錯誤的庫存:已是多樣少量時代 2.積習難改的庫存:延續大批量生產方式 3.產能不均的庫存:生產速度不一,產生堆 積庫存 4.製程集結的庫存:等集結到批量才生產 5.消化不良的庫存:後工程比前工程慢
庫存是企業的墓場
6.候鳥作業的庫存:人手缺乏,或機器設備 產能很大,作業員在這做一會,再到 那作一會…,所過之處都留下一堆 庫存。 7.討厭換模的庫存:為減少換模時間以經 濟批量的觀念生產,不考慮是否有 訂單,或增加倉庫管理成本,或呆滯
等待的浪費
意義:閒著沒事,等著下一動作的來臨 內容:1.作業不平衡 2.待工作指示 3.待料 4.品質不良,待判定 5.機台故障,待修復 6.監視機器
搬運的浪費
意義:物品在製程工程間的動態改變 內容:工廠佈置(Layout)採用批量生產 1.移動 2.堆積、放置 3.整理 4.清點、防護 5.找尋
加工的浪費
意義:製程上不合理的加工 內容:1.取消 2.合併 3.簡化 4.重整 5.替代
庫存的浪費
意義:庫存是萬惡的根源(會隱藏問題) 內容:1.不必要的搬運浪費 2.使先進先出的作業困難 3.佔用廠房空間、倉庫投資的浪費 4.變成呆滯品 5.超過儲存期間,不能使用 6.利息損失及管理費用
浪費的認識
動與人動的區別 動 :不能產生附加價值的動作-浪費 人動:會產生附加價值的動作 -賺錢 附加價值:將購入的原、材料經過人工、 設備的投入,使得物品的價值能更為提高 SPS中要做的是有附加價值的動作,故要 消除沒有附加價值的浪費
七種浪費(Loss)
1.等待的浪費 2.搬運的浪費 3.不良品的浪費 4.動作的浪費 5.加工的浪費 6.在庫的浪費 7.製造過多(早)的浪費
流線化生產與批量生產的差別
1.合理化方向 流線化生產:一個人操作數個不同製程 的機器,又稱“多製程作業”
批量化生產:一個人操作多台同一功能 的機器,又稱“多機台作業”
流線化生產與批量生產的差別
2.作業者的技能 批量化生產:作業者多操作同一製程的 設備,僅擁有一項技能,稱“單能工” 流線化生產:以多製程作業為合理化方 向,作業者能操作多種製程的 設備, 擁有多項技能,稱“多能工”
流線化生產的建立步驟
step5:設定Line Tact(L/T) L/T=每日工作時數/每日市場需要 數(做一個所需要時間) step6:決定設備,人員的數量 step7:佈置生產線(小型化,滑輪化,專用化) step8:配置作業人員 step9:單件流動 step10:維持管理 step11:水平展開
流線化生產的八個條件
條件四:多製程操作的作業
條件五:作業員的多能工化 將機械標準化,使任何作業員,都 有能力簡單操作 條件六: 邊走邊做的走動作業 一人多製程的方式,一面在走動,一面在 進行加工動作的作業
流線化生產的八個條件
條件七:機器設備的小型化 不迷戀速度愈快愈好,但求品質很穩定, 故障率也低
條件八:生產佈線的U型化 生產的投入點(Input),與完成品的取出點 (Output)盡可能的接近,可節省人力,使物 流動線順暢,消除浪費。
流線化生產的建立步驟
step1:全員的意識改革 step2:成立示範改善小組 step3:選定示範生產線 step4:現況調查分析 調查改善前,生產數量,人員數, 生產力,不良率,可動率,在製庫存數 ,佔用空間……