NiPdSi界面常温扩散及硅化物形成的XPS证据
镁合金表面Ni(P)-Sn界面扩散层研究

镁合 金表 面 N i ( P )一S n 界 面扩 散 层 研 究
戈晓岚 , 马 洪涛 ,陈志超 ,王彩俊 ,曾 兵
( 江苏大学 机械工程学院 ,江苏 镇江 2 1 2 0 1 3 )
摘要 : 对A Z 9 1 D镁合金表 面进行化 学镀 N i ( P ) 以及热浸镀纯锡 , 从 而获得 了 N i ( P ) 一S n双层 镀
n e s i u m a l l o y t o p r e p a r e N i ( P)一S n d o u b l e — l a y e r c o a t i n g i f l m.A t f e r 2 h o u r s o f t h e r m a l d i f f u s i o n t r e a t —
引文格式 : 戈晓岚 , 马洪涛 , 陈志超 , 等. 镁 合金表 面 N i ( P ) 一S n 界面 扩散层研 究 【 J ] . 江苏 大学学 报 : 自然 科学 版 , 2 0 1 4 , 3 5 ( 1 )
N i ( P)一S n i n t e r f a c e d i f u s i o n o n s u r f a c e o f ma g n e s i u m a l l o y
膜. 2 2 0 c l C 进行 2 h热 扩散 处理后 , 研 究镀 层 界 面的 结构和 腐蚀 性 能. 通过 S E M、 能谱 仪 分 别进 行界
面结构检测和元素分析 , 采用 X R D对 N i ( P ) 一 S n 镀层表层相结构进行 分析 , 利用动电位极化 曲线 检测 了镀层热处理前后的的耐腐蚀性能. 研 究结果表明: 沿界 面连续分布的 N i — P化合物层能有效 地 阻止 S n向 N i 层 的扩散 , 化合 相 N i s n 呈“ 块 状” 漂 浮在 s n层 中, 该 相 的产 生和 生 长破 坏 了镀 层
扩散阻挡层对NiCrAlYSi涂层不同条件下热腐蚀行为的影响
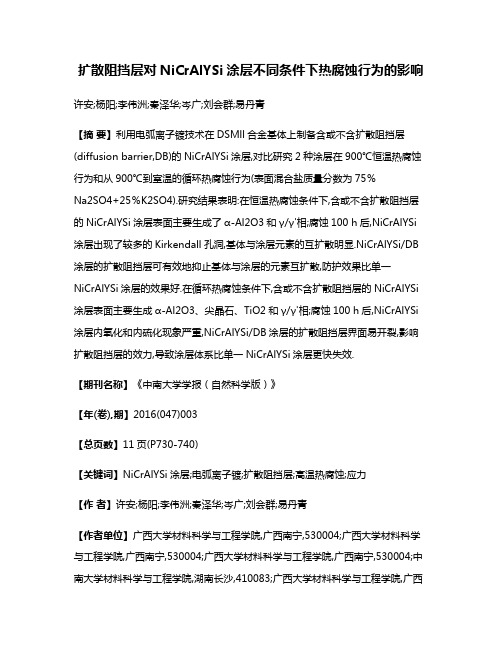
扩散阻挡层对NiCrAlYSi涂层不同条件下热腐蚀行为的影响许安;杨阳;李伟洲;秦泽华;岑广;刘会群;易丹青【摘要】利用电弧离子镀技术在DSMll合金基体上制备含或不含扩散阻挡层(diffusion barrier,DB)的NiCrAlYSi涂层,对比研究2种涂层在900℃恒温热腐蚀行为和从900℃到室温的循环热腐蚀行为(表面混合盐质量分数为75%Na2SO4+25%K2SO4).研究结果表明:在恒温热腐蚀条件下,含或不含扩散阻挡层的NiCrAlYSi涂层表面主要生成了α-Al2O3和γ/γ'相;腐蚀100 h后,NiCrAlYSi 涂层出现了较多的Kirkendall孔洞,基体与涂层元素的互扩散明显.NiCrAlYSi/DB 涂层的扩散阻挡层可有效地抑止基体与涂层的元素互扩散,防护效果比单一NiCrAlYSi涂层的效果好.在循环热腐蚀条件下,含或不含扩散阻挡层的NiCrAlYSi 涂层表面主要生成α-Al2O3、尖晶石、TiO2和γ/γ'相;腐蚀100 h后,NiCrAlYSi 涂层内氧化和内硫化现象严重,NiCrAlYSi/DB涂层的扩散阻挡层界面易开裂,影响扩散阻挡层的效力,导致涂层体系比单一NiCrAlYSi涂层更快失效.【期刊名称】《中南大学学报(自然科学版)》【年(卷),期】2016(047)003【总页数】11页(P730-740)【关键词】NiCrAlYSi涂层;电弧离子镀;扩散阻挡层;高温热腐蚀;应力【作者】许安;杨阳;李伟洲;秦泽华;岑广;刘会群;易丹青【作者单位】广西大学材料科学与工程学院,广西南宁,530004;广西大学材料科学与工程学院,广西南宁,530004;广西大学材料科学与工程学院,广西南宁,530004;中南大学材料科学与工程学院,湖南长沙,410083;广西大学材料科学与工程学院,广西南宁,530004;广西大学材料科学与工程学院,广西南宁,530004;中南大学材料科学与工程学院,湖南长沙,410083;中南大学材料科学与工程学院,湖南长沙,410083【正文语种】中文【中图分类】TB43;TG174.44燃气轮机是十分重要的动力机械设备,广泛应用于航空航天、船舶和能源等领域。
Ni-SiC
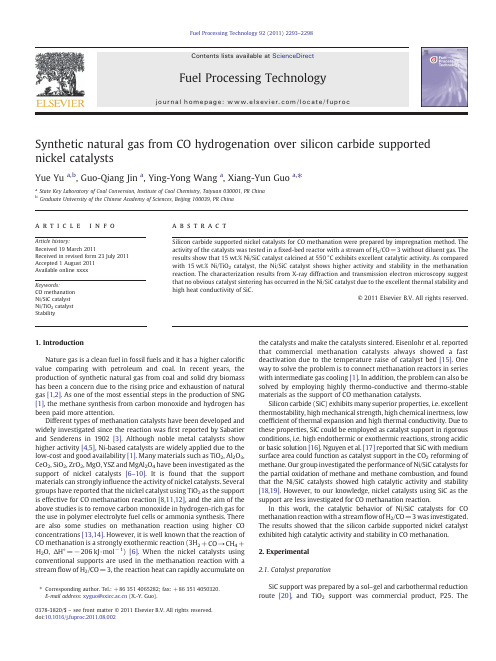
Synthetic natural gas from CO hydrogenation over silicon carbide supported nickel catalystsYue Yu a ,b ,Guo-Qiang Jin a ,Ying-Yong Wang a ,Xiang-Yun Guo a ,⁎a State Key Laboratory of Coal Conversion,Institute of Coal Chemistry,Taiyuan 030001,PR China bGraduate University of the Chinese Academy of Sciences,Beijing 100039,PR Chinaa b s t r a c ta r t i c l e i n f o Article history:Received 19March 2011Received in revised form 23July 2011Accepted 1August 2011Available online xxxx Keywords:CO methanation Ni/SiC catalyst Ni/TiO 2catalyst StabilitySilicon carbide supported nickel catalysts for CO methanation were prepared by impregnation method.The activity of the catalysts was tested in a fixed-bed reactor with a stream of H 2/CO =3without diluent gas.The results show that 15wt.%Ni/SiC catalyst calcined at 550°C exhibits excellent catalytic activity.As compared with 15wt.%Ni/TiO 2catalyst,the Ni/SiC catalyst shows higher activity and stability in the methanation reaction.The characterization results from X-ray diffraction and transmission electron microscopy suggest that no obvious catalyst sintering has occurred in the Ni/SiC catalyst due to the excellent thermal stability and high heat conductivity of SiC.©2011Elsevier B.V.All rights reserved.1.IntroductionNature gas is a clean fuel in fossil fuels and it has a higher calori fic value comparing with petroleum and coal.In recent years,the production of synthetic natural gas from coal and solid dry biomass has been a concern due to the rising price and exhaustion of natural gas [1,2].As one of the most essential steps in the production of SNG [1],the methane synthesis from carbon monoxide and hydrogen has been paid more attention.Different types of methanation catalysts have been developed and widely investigated since the reaction was first reported by Sabatier and Senderens in 1902[3].Although noble metal catalysts show higher activity [4,5],Ni-based catalysts are widely applied due to the low-cost and good availability [1].Many materials such as TiO 2,Al 2O 3,CeO 2,SiO 2,ZrO 2,MgO,YSZ and MgAl 2O 4have been investigated as the support of nickel catalysts [6–10].It is found that the support materials can strongly in fluence the activity of nickel catalysts.Several groups have reported that the nickel catalyst using TiO 2as the support is effective for CO methanation reaction [8,11,12],and the aim of the above studies is to remove carbon monoxide in hydrogen-rich gas for the use in polymer electrolyte fuel cells or ammonia synthesis.There are also some studies on methanation reaction using higher CO concentrations [13,14].However,it is well known that the reaction of CO methanation is a strongly exothermic reaction (3H 2+CO →CH 4+H 2O,ΔH°=−206kJ·mol −1)[6].When the nickel catalysts using conventional supports are used in the methanation reaction with a stream flow of H 2/CO=3,the reaction heat can rapidly accumulate onthe catalysts and make the catalysts sintered.Eisenlohr et al.reported that commercial methanation catalysts always showed a fast deactivation due to the temperature raise of catalyst bed [15].One way to solve the problem is to connect methanation reactors in series with intermediate gas cooling [1].In addition,the problem can also be solved by employing highly thermo-conductive and thermo-stable materials as the support of CO methanation catalysts.Silicon carbide (SiC)exhibits many superior properties,i.e.excellent thermostability,high mechanical strength,high chemical inertness,low coef ficient of thermal expansion and high thermal conductivity.Due to these properties,SiC could be employed as catalyst support in rigorous conditions,i.e.high endothermic or exothermic reactions,strong acidic or basic solution [16].Nguyen et al.[17]reported that SiC with medium surface area could function as catalyst support in the CO 2reforming of methane.Our group investigated the performance of Ni/SiC catalysts for the partial oxidation of methane and methane combustion,and found that the Ni/SiC catalysts showed high catalytic activity and stability [18,19].However,to our knowledge,nickel catalysts using SiC as the support are less investigated for CO methanation reaction.In this work,the catalytic behavior of Ni/SiC catalysts for CO methanation reaction with a stream flow of H 2/CO=3was investigated.The results showed that the silicon carbide supported nickel catalyst exhibited high catalytic activity and stability in CO methanation.2.Experimental 2.1.Catalyst preparationSiC support was prepared by a sol –gel and carbothermal reduction route [20],and TiO 2support was commercial product,P25.TheFuel Processing Technology 92(2011)2293–2298⁎Corresponding author.Tel.:+863514065282;fax:+863514050320.E-mail address:xyguo@ (X.-Y.Guo).0378-3820/$–see front matter ©2011Elsevier B.V.All rights reserved.doi:10.1016/j.fuproc.2011.08.002Contents lists available at ScienceDirectFuel Processing Technologyj o u r n a l h o me p a g e :w w w.e l s ev i e r.c om /l o c a t e /f u p ro ccatalysts were prepared by conventional impregnation method[18]. To prepare15wt.%Ni/SiC catalyst,1g of above SiC was added into 25.5mL Ni(NO3)2aqueous solution(0.1mol/L)with stirring for12h. Then the slurry was heated at80°C until nearly all the water evaporated and the mixture was dried at100°C for6h.Afterward the dried sample was calcined in air at different temperatures for4h. The similar processes can be used to prepare Ni/SiC catalysts with different nickel loadings.15wt.%Ni/TiO2catalyst was prepared by the similar route to15wt.%Ni/SiC catalyst.1g of TiO2was added into 25.5mL Ni(NO3)2aqueous solution and stirred for12h.After being heated and dried,the catalyst was calcined at550°C for4h in air.2.2.Catalyst testThe performance of the catalysts was tested in afixed-bed reactor (a40cm long stainless steel tube with an inner diameter of6mm). The reactor was heated up by a PID regulated oven and the reaction temperature was measured in the middle of the catalyst bed using a K-type thermocouple.Reaction gases,which consisted of H2and CO (molar ratio of H2/CO=3,without diluent gas),were supplied from high-pressure gas cylinders and theflow rate was controlled by mass-flow controller(MFC)to ensure a space velocity(GSV)of4500h−1.0.8mL of catalyst(sieve fraction40–60mesh)was placed in thecenter of the tubular reactor.All experiments were performed at a pressure of2.0MPa.Before each catalyst test,the catalyst was reduced at500°C in the CO/H2mixture gases for2h,then decreased to reaction temperature and kept for1h.The outlet gases were analyzed by GC-14B gas chromatograph with TDX-01column and a GDX-104 column using thermal conductivity detector andflame ionization detector.The selectivity of a certain product is calculated by the formula,S i=n i C i/∑n i C i,where n i and C i are the number of carbon atoms and the concentration of product“i”,respectively.2.3.Catalyst characterizationThe crystalline phases of the catalysts were analyzed by a Rigaku D-Max/RB X-ray diffractometer(XRD)with Cu Kαradiation with a scanning rate of6°/min.The catalyst morphology and structure were analyzed by a JEOL-2010transmission electron microscopy(TEM).The surface areas of catalysts were calculated from the BET method,which was performed at nitrogen temperature at77K on a Micromeritics Tristar3000analyzer.The nickel amount of catalysts was measured by ICP spectrometer.TG–DSC studies of the catalysts after reaction were performed on NETZSCHSTA409PC thermoanalyzer within a temper-ature range from room temperature to850°C at a heating rate of 10°C/min in airflow.3.Results and discussion3.1.CO methanation over Ni/SiC catalyst3.1.1.Influence of nickel loadingThe effect of metal loading on the activity of Ni/SiC catalysts was investigated,and the results are shown in Fig.1and Table1.It can be seen from Fig.1that the methanation activity of SiC supported catalysts increases with the nickel loading from5wt.%to15wt.%. Reaction rate of CO conversion which is defined as moles of CO converted per gram of Ni per second at250°C is shown in Table1.It can be seen that increasing the nickel loading from10wt.%to15wt.% results in an increase of the rate of CO conversion from1.28to 5.10μmol s−1g−1.However,when the nickel loading further in-creases to20wt.%,the rate of CO conversion at250°C decreases to 1.34μmol s−1g−1.As compared with15wt.%Ni/SiC catalyst,there is no significant increase in methanation activity for20wt.%Ni/SiC catalyst(Fig.1).The metal crystallite sizes calculated by Scherrer's equation[21]are shown in Table2.From the table,the metal crystallite size increases with increasing the nickel loading.The influences of the metal particle size on methanation activity have been studied by several authors.Panagiotopoulou et al.[8]reported that the rate of CO conversion increased by a factor of166with increasing the loading of Ru on TiO2from0.5wt.%to5wt.%.Takenaka et al.[11]reported that the Ni crystallites with relatively large sizes were more effective for CO methanation.Zhou et al.[22]demon-strated that the activity of CO hydrogenation increased with increasing the rhodium particle size in the range of 3.0–5.0nm. Therefore,CO methanation is a structure sensitive reaction and the larger particle size facilitates CO hydrogenation.20wt.%Ni/SiC catalyst has larger metallic particles but lower methanation activity than15wt.%Ni/SiC catalyst.The reason may be that both particle size and amount of active sites affect the methanation activity.It is well known that the larger crystallite size results in the decrease of metal dispersion on the surface of catalyst[8]and the latter one can affect the amount of active sites.Therefore,the lower rate of CO conversion may be due to the less active sites over20wt.%Ni/SiC compared with 15wt.%Ni/SiC catalyst.This is in accordance with the results reported by Aksoylu et al.[23],who found that the methane production per square meter of nickel surface area was enhanced with lower Ni loading over Ni/Al2O3catalysts.On the other hand,the large particle size on20wt.%Ni/SiC catalyst may block the external surface of support and this can also decrease the activity of CO methanation. Therefore,15wt.%is an optimal loading of Ni/SiC catalyst for methanation reaction.It should be noted that the products of CO hydrogenation under present reaction condition include methane,higher hydrocarbons (C2H6,C2H4,C3H8and C3H6),carbon dioxide and water.The forma-tion of CO2may be due to the water-gas-shift reaction,CO+Temperature (o C)EquilibriumCOConversion(%)T emperature (o C)COconversion(%)Fig.1.Influence of nickel loading on the activity of Ni/SiC catalysts and the calculated equilibrium CO conversions under P=2.0MPa,H2/CO=3and GSV=4500h−1.Table1Catalytic performance of Ni/SiC and Ni/TiO2catalysts.Catalyst Ni loading(wt.%)Rate of CO conversionat250°C(μmol s−1g−1)aCH4selectivityat320°C(%)Ni/SiC5–70.8910 1.2890.3115 5.1092.0420 1.3493.60Ni/TiO215 3.5282.21Reaction condition:H2/CO=3,GSV=4500h−1,and P=2.0MPa.a Converted CO per second per gram catalyst.2294Y.Yu et al./Fuel Processing Technology92(2011)2293–2298H2O=CO2+H2.The methane selectivity over the Ni/SiC catalysts at 320°C is shown in Table1.It can be seen that the methane selectivity increases with increasing the Ni loading.For CO methanation reaction, CO is adsorbed and dissociated on the surface of metal particles[24]and the dissociation of C\O bond in adsorbed CO species is the rate-determining step[25].It has been reported that there are three forms of adsorbed CO:linear CO,bridged CO and twin CO[26].The activity of adsorbed CO breaking into surface carbon and surface oxygen on the catalyst surface follows the sequence,bridged CO N linear CO N twin CO[10].According to the methanation mechanism,adsorbed CO is dissociated and converted into CH x as intermediate species by assistance of H on the surface of catalysts,and the concentration of the intermediate species determines the distribution of reaction products [25].For the methanation reaction,there are more active bridged CO on larger metallic particles[27],and then the rate of the dissociation and hydrogenation of intermediate species becomes faster[22,28]. Therefore,the methane selectivity is higher on high loading Ni/SiC catalysts.3.1.2.Thermodynamics and equilibrium conversionFrom Fig.1,the conversion of CO over Ni/SiC catalysts can increase up to100%with increasing the reaction temperature.When the reaction temperature is higher than440°C,however the CO con-version begins to decrease.It is most likely due to thermodynamic limitation.According to the thermodynamic equilibrium,theΔG can become positive when the temperature is higher than530°C[29]. Therefore,high temperature is favorable to the stream reforming of methane—the reverse of methanation.Supposing that the only product of CO hydrocarbon is methane, thermodynamic equilibrium data at the temperature range from100 to500°C are calculated.The calculation is performed under the same operating conditions as our experiments,i.e.H2/CO=3,P=2MPa. From Fig.1,the complete conversion of CO can be obtained below 250°C,and then the conversion slightly decreases with increasing the reaction temperature.The CO conversion decreases to87%when the reaction temperature rises to500°C.These are in agreement with the experimental results.3.1.3.Effect of calcination temperatureThe sizes of metallic particles in15wt.%Ni/SiC catalysts under different calcination temperatures are shown in Table2.It can be seen that the particle size increases with increasing the calcination temperature.It has been established that the methanation reaction is structure sensitive and larger particle size facilitates the cleavage of C\O bond[8,22,27,30].Therefore,the catalysts calcined at higher temperatures have higher catalytic activity for CO methanation.Fig.2 shows the influences of the calcination temperature on the activity of 15wt.%Ni/SiC catalyst for CO methanation.It can be seen that the CO conversion increases with increasing the calcination temperature from450°C to550°C.However,there is a little decrease in the CO methanation activity over the Ni/SiC catalyst calcined at600°C.This is likely due to that oversize particles formed at the high temperature could result in a decrease of active sites.Therefore,550°C is an optimal calcination temperature for15wt.%Ni/SiC catalyst.3.2.Performance of Ni/SiC and Ni/TiO2catalystsAccording to literature,TiO2supported nickel catalysts are effective for the CO methanation[8,11,12].Therefore,15wt.%Ni/SiC and15wt.%Ni/TiO2catalysts were tested under the same conditions for comparison.It can be seen from Table1that15wt.%Ni/SiC catalyst is more active than15wt.%Ni/TiO2catalyst.Fig.3shows the evolution of CO conversion over Ni/SiC and Ni/TiO2catalysts at340°C.For the Ni/SiC catalyst,there is an activity rise in the initial stage of the methanation reaction and CO is nearly converted completely.When the reaction time is longer than40h the activity of Ni/SiC catalyst exhibits a slow drop and the CO conversion decreases from initial97% to91%after100h.The decrease of activity is due to the losing of nickel by the formation of nickel carbonyl.According to ICP analysis,the nickel amount of the Ni/SiC catalyst has decreased by16%after reaction for100h.For Ni/TiO2catalyst,the activity decreases rapidly and the CO conversion decreases from initial98%to below50%afterTable2Particle sizes of different Ni/SiC and Ni/TiO2catalysts.Catalyst Ni loading(wt.%)Calculationtemperature(°C)Metal crystallitesize(nm)aNi/SiC55508.61055015.31545017.450018.155019.060020.92055023.5 Ni/TiO215550–Used Ni/SiC1555021.6b Used Ni/TiO21555023.5ba Calculated from NiO(021)plane by Scherrer's equation.b Calculated from Ni(111)plane by Scherrer's equation.COconversion(%)Temperature(o C)Fig.2.Influence of calcination temperature on the activity of Ni/SiC catalysts under P=2.0MPa,H2/CO=3and GSV=4500h−1.COconversion(%)Time (h)parison of the catalytic performance between15wt.%Ni/SiC and15wt.% Ni/TiO2catalysts under T=340°C,P=2.0MPa,H2/CO=3and GSV=4500h−1.2295Y.Yu et al./Fuel Processing Technology92(2011)2293–2298100h reaction.These results indicate that the Ni/SiC catalyst exhibits an obviously better stability than the Ni/TiO 2catalyst.3.3.TG –DSC analysis of used Ni/SiC and Ni/TiO 2catalystsTG –DSC analysis was performed for the used Ni/SiC and Ni/TiO 2catalysts and the results are shown in Fig.4.From the TG pro file shown in Fig.4A,no weight loss but a viewable increase of weight can be observed,indicating that there are no carbon depositions over both catalysts.The weight increase over both catalysts is likely due to the oxidation of metallic Ni to NiO.As seen in Fig.4B,no remarkable exothermic peaks can be observed for the used Ni/SiC and Ni/TiO 2catalysts,indicating that the oxidation of deposited carbon on the used catalysts does not occur.This is in agreement with the results reported by Zhu et al.[31].Therefore,the decrease in the activity of the Ni/SiC catalyst for methanation reaction is not due to the carbon deposition.3.4.XRD resultsFig.5shows the XRD results of 15wt.%Ni/SiC and 15wt.%Ni/TiO 2catalysts before and after reaction at 340°C for 100h.In the XRD patterns of fresh Ni/SiC catalyst shown in Fig.5A,the diffraction peak at 2θ=43.3°is attributed to NiO (012)plane [18].According to Scherrer's equation [21],the average NiO crystallite size calculated from the peak is about 19.0nm.In the XRD patterns of fresh Ni/TiO 2catalyst,diffraction peaks attributed to NiTiO 3phase can be detected (Fig.5A).Rao et al.[32]reported that NiTiO 3was formed whenNi/TiO 2catalyst was calcined above 500°C.Therefore the NiTiO 3phase in the present XRD patterns may be formed during the calcination.In our experiments,the color of Ni/TiO 2catalyst can become light yellow,which is the color of NiTiO 3[33].From both XRD patterns shown in Fig.5B,no diffraction peak of carbon can be found,indicating that the carbon deposition on the two methanation catalysts can be ignored.This is in accordance with the results of TG –DSC analysis.The diffraction peak at 2θ=44.56°is attributed to metallic Ni (111)[18].Metallic nickel exists in both catalysts,indicating that the active phase for CO methanation is metallic nickel.For the used Ni/SiC catalyst,the mean nickel particle size calculated from Ni (111)plane by Scherrer's equation [21]is about 21.6nm.The nickel particle size only has a slight increment during the reaction,suggesting that no serious sintering has occurred on the Ni/SiC pared with the fresh Ni/TiO 2catalyst,the crystallite size of used Ni/TiO 2increased signi ficantly (particle size from 24.2to 30.3nm and from 26.6to 35.9nm for rutile and anatase,respectively).The increase of particle size may be due to the production of hot spots during the CO methanation,which possibly make TiO 2crystallites sintered.In addition,the speci fic surface areas of Ni/TiO 2catalyst decreased from 32.1to 16.7m 2/g after reaction at 340°C for 100h.Ruckenstein et al.[34]reported that TiO x could1002003004005006007008009092949698100102104Ab aS a m p l e w e i g h t (%)temperature(o C)temperature(o C)a---15 wt.% Ni/SiC b---15 wt.% Ni/TiO 2BD S C /(m W /m g )Fig.4.TG –DSC pro files of used 15wt%Ni/SiC and 15wt.%Ni/TiO 2catalysts.AI n t e n s i t y (c p s )2 Theta (o )2 Theta (o )BI n t e n s i t y (c p s )Fig.5.XRD patterns of 15wt.%Ni/SiC and 15wt.%Ni/TiO 2catalysts before (A)and after (B)methanation reaction at 340°C for 100h.(●)NiTiO 3;(■)anatase;(▲)rutile;(★)SiC;(♦)NiO;(○)Ni.2296Y.Yu et al./Fuel Processing Technology 92(2011)2293–2298migrate onto the surface of metal nickel particles due to the strong interaction of support –metal.During the methanation reaction,the TiO 2may amalgamate with the reduced Ni due to the strong metal –support interaction.This is not favorable for CO absorption and decomposition on metal Ni.Therefore,the Ni/TiO 2catalyst shows a declining activity and stability in the methanation reaction.3.5.TEM characterization of Ni/SiC catalystsTEM images of fresh and used 15wt.%Ni/SiC catalyst are shown in Fig.6.From the two TEM images,it can be seen that the metal particles are well distributed on the support surface.From the image of fresh Ni/SiC catalyst (Fig.6A),the size of NiO particles ranges from 10to 25nm.In Fig.6B,the size of nickel particles in the used catalyst is about 10–30nm.These results are in accordance with those derived from XRD analysis.From both XRD and TEM results,15wt.%Ni/SiC catalyst shows better stability in the methanation reaction due to the excellent thermal conductivity and thermostability of the SiC support.4.ConclusionThe synthesis of methane from syngas was investigated over Ni/SiC catalysts which were prepared by impregnation method.From the present work,15wt.%Ni/SiC catalyst calcined at 550°C exhibits excel-lent catalytic activity for CO pared with Ni/TiO 2catalyst,the Ni/SiC catalyst exhibits higher activity and better stability in the CO methanation due to the excellent thermostability and high heat conductivity of the SiC support,which can ef ficiently avoid the sintering of nickel particles.AcknowledgmentsThe work was financially supported by NSFC (Ref.20973190),the in-house research project of SKLCC (Ref.SKLCC-2008BWZ010),and the National Basic Research Program (Ref.2011CB201405).References[1]J.Kopyscinski,T.J.Schildhauer,S.M.A.Biollaz,Production of synthetic natural gas(SNG)from coal and dry biomass —a technology review from 1950to 2009,Fuel 89(2010)1763–1783.[2]N.R.Udengaard,A.Olsen,C.Wix-Nielsen,Pittsburgh Coal Conf.,2006.[3]P.Sabatier,J.B.Senderens,New synthesis of methane,Académie des Sciences 134(1902)514–516.[4]M.A.Vannlce,R.L.Garten,Supported palladium catalysts for methanation,Industrial and Engineering Chemistry Product Research and Development 18(1979)186–191.[5]O.G őrke,P.Pfeifer,K.Schubert,Highly selective methanation by the use of amicrochannel reactor,Catalysis Today 110(2005)132–139.[6]P.Panagiotopoulou,D.I.Kondarides,X.E.Verykios,Selective methanation of COover supported noble metal catalysts:effects of the nature of the metallic phase on catalytic performance,Applied Catalysis A 344(2008)45–54.[7] A.L.Kustov,A.M.Frey,rsen,T.Johannessen,J.K.Nørskov,C.H.Christensen,CO methanation over supported bimetallic Ni –Fe catalysts:from computational studies towards catalyst optimization,Applied Catalysis A 320(2007)98–104.[8]P.Panagiotopoulou,D.I.Kondarides,X.E.Verykios,Selective methanation of COover supported Ru catalysts,Applied Catalysis B 88(2009)470–478.[9]R.A.Dagle,Y.Wang,G.G.Xia,J.J.Strohma,J.Holladay,D.R.Palo,Selective COmethanation catalysts for fuel processing applications,Applied Catalysis A 326(2007)213–218.[10]R.F.Wu,Y.Zhang,Y.Z.Wang,C.G.Gao,Y.X.Zhao,Effect of ZrO 2promoter on thecatalytic activity for CO methanation and adsorption performance of the Ni/SiO 2catalyst,Journal of Fuel Chemistry and Technology 37(2009)578–582.[11]S.Takenaka,T.Shimizu,K.Otsuka,Complete removal of carbon monoxide inhydrogen-rich gas stream through methanation over supported metal catalysts,International Journal of Hydrogen Energy 29(2004)1065–1073.[12]W.J.Shen,M.Okumura,Y.Matsumura1,M.Haruta,The in fluence of the supporton the activity and selectivity of Pd in CO hydrogenation,Applied Catalysis A 213(2001)225–232.[13]M.A.Vannice, C.C.Twu,S.H.Moon,SMSI effects on CO adsorption andhydrogenation on Pt catalysts,Journal of Catalysis 79(1983)70–80.[14]R.L.Chin,A.Elattar,W.E.Wallance,D.M.Hercules,ESCA studies of methanationcatalysts derived from intermetallic compounds,Journal of Physical Chemistry 84(1980)2895–2898.[15]K.H.Eisenlohr,F.W.Moeller,M.Dry,In fluence of certain reaction parameters onmethanation of coal gas to SNG,ACS Division of Fuel Chemistry 19(1974)1–9.[16]M.J.Ledoux,S.Hantzer,C.P.Huu,J.Guille,M.P.Desaneaux,New synthesis and usesof high-speci fic-surface SiC as a catalytic support that is chemically inert and has high thermal-resistance,Journal of Catalysis 114(1988)176–185.[17] D.L.Nguyen,P.Leroi,M.J.Ledoux,P.C.Huu,In fluence of the oxygen pretreatmenton the CO 2reforming of methane on Ni/β-SiC catalyst,Catalysis Today 141(2009)393–396.[18]W.Z.Sun,G.Q.Jin,X.Y.Guo,Partial oxidation of methane to syngas over Ni/SiCcatalysts,Catalysis Communications 6(2005)135–139.[19]Q.Wang,W.Z.Sun,G.Q.Jin,Y.Y.Wang,X.Y.Guo,Biomorphic SiC pellets as catalystsupport for partial oxidation of methane to syngas,Applied Catalysis B 79(2008)307–312.[20]G.Q.Jin,X.Y.Guo,Synthesis and characterization of mesoporous silicon carbide,Microporous and Mesoporous Materials 60(2003)207–212.[21]Y.H.Ni,F.Wang,H.J.Liu,Y.Y.Liang,G.Yin,J.M.Hong,X.Ma,Z.Xu,Fabrication andcharacterization of hollow cuprous sul fide (Cu 2−x S)microspheres by a simple template-free route,Inorganic Chemistry Communications 6(2003)1406–1408.[22]S.T.Zhou,X.L.Pan,X.H.Bao,Effect of rhodium particle size in Rh/SiO 2catalystprepared by microemulsion method on reaction performance of CO hydrogena-tion,Chinese Journal of Catalysis 27(2006)474–478.[23] A.E.Aksovlu,A.N.Akin,Z.I.Őnsan,D.L.Trimm,Structure/activity relationships incoprecipitated nickel –alumina catalysts using CO 2adsorption and methanation,Applied Catalysis A 145(1996)185–193.[24]R.E.Hayes,W.J.Thomas,K.E.Hayes,A study of the nickel-catalyzed methanationreaction,Journal of Catalysis 92(1985)312–326.[25]T.Morl,H.Masuda,H.Imal,Kinetics,isotope effects,and mechanism for thehydrogenation of carbon monoxide on supported nickel catalysts,Journal of Physical Chemistry 86(1982)2753–2760.[26] C.W.Hu,Y.Q.Chen,P.Li,H.Min,Y.Chen,A.M.Tian,On the interaction of CO andH 2with Ni-based catalyst,Journal of Molecular Catalysis (China)9(1995)435–444.[27]H.Arakawa,T.Fukushima,M.Ichikawa,K.Takeuchi,T.Matsuzaki,Y.Sugi,Highpressure in situ FT-IR study of CO hydrogenation over Rh/SiO 2catalyst,Chemistry Letters 1(1985)23–26.[28]R.P.Underwood, A.T.Bell,In fluence of particle size on carbon monoxidehydrogenation over silica-and lanthana-supported rhodium,Applied Catalysis 34(1987)289–310.100nm A 100nmBFig.6.TEM images of 15wt.%Ni/SiC catalysts before (A)and after (B)reaction at 340°C for 100h.2297Y.Yu et al./Fuel Processing Technology 92(2011)2293–2298[29] F.Haga,T.Nakajima,H.Miya,S.Mishima,Catalytic properties of supported cobaltcatalysts for steam reforming of ethanol,Catalysis Letters48(1997)223–227. [30]M.P.Andersson,F.Abild-Pedersen,I.N.Remediakis,T.Bligaard,G.Jones,J.Engbæk,O.Lytken,S.Horch,J.H.Nielsen,J.Sehested,J.R.R.Nielsen,J.K.Nørskov,I.Chorkendorff,Structure sensitivity of the methanation reaction:H2-induced CO dissociation on nickel surfaces,Journal of Catalysis255(2008)6–19.[31]J.Q.Zhu,X.X.Peng,L.Yao,J.Shen,D.M.Tong,C.W.Hu,The promoting effect of La,Mg,Co and Zn on the activity and stability of Ni/SiO2catalyst for CO2reforming of methane,International Journal of Hydrogen Energy36(2011)7094–7104.[32]G.Sankar, C.N.R.Rao,T.Rayment,Promotion of the metal–oxide supportinteraction in the Ni/TiO2catalyst—crucial role of the method of preparation, the structure of TiO2and the NiTiO3intermediate,Journal of Materials Chemistry 1(1991)299–300.[33]T.H.Wu,Q.G.Yan,H.L.Wan,Partial oxidation of methane to hydrogen and carbonmonoxide over a Ni/TiO2catalyst,Journal of Molecular Catalysis A:Chemical226 (2005)41–48.[34] E.Ruckenstein,Y.H.Hu,Role of support in CO2reforming of CH4to syngas over Nicatalysts,Journal of Catalysis162(1996)230–238.2298Y.Yu et al./Fuel Processing Technology92(2011)2293–2298。
基于铯铟硒薄膜特性的研究
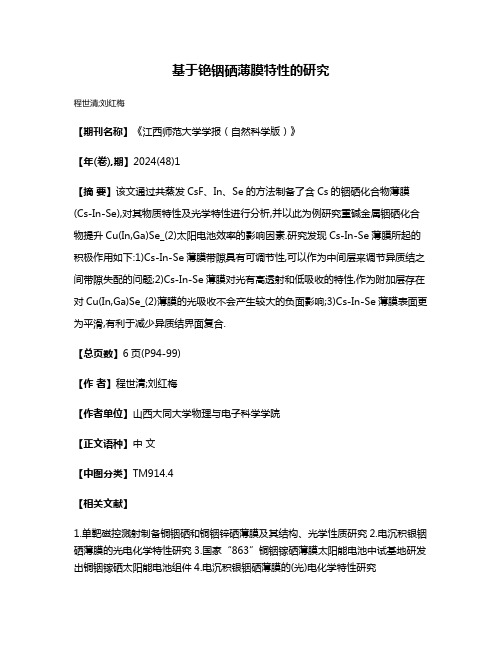
基于铯铟硒薄膜特性的研究
程世清;刘红梅
【期刊名称】《江西师范大学学报(自然科学版)》
【年(卷),期】2024(48)1
【摘要】该文通过共蒸发CsF、In、Se的方法制备了含Cs的铟硒化合物薄膜(Cs-In-Se),对其物质特性及光学特性进行分析,并以此为例研究重碱金属铟硒化合物提升Cu(In,Ga)Se_(2)太阳电池效率的影响因素.研究发现Cs-In-Se薄膜所起的积极作用如下:1)Cs-In-Se薄膜带隙具有可调节性,可以作为中间层来调节异质结之间带隙失配的问题;2)Cs-In-Se薄膜对光有高透射和低吸收的特性,作为附加层存在对Cu(In,Ga)Se_(2)薄膜的光吸收不会产生较大的负面影响;3)Cs-In-Se薄膜表面更为平滑,有利于减少异质结界面复合.
【总页数】6页(P94-99)
【作者】程世清;刘红梅
【作者单位】山西大同大学物理与电子科学学院
【正文语种】中文
【中图分类】TM914.4
【相关文献】
1.单靶磁控溅射制备铜铟硒和铜铟锌硒薄膜及其结构、光学性质研究
2.电沉积银铟硒薄膜的光电化学特性研究
3.国家“863”铜铟镓硒薄膜太阳能电池中试基地研发出铜铟镓硒太阳能电池组件
4.电沉积银铟硒薄膜的(光)电化学特性研究
因版权原因,仅展示原文概要,查看原文内容请购买。
Ni(Pt)Si硅化物温度稳定性的研究

Ni(Pt)Si硅化物温度稳定性的研究黄伟;张利春;高玉芝;金海岩;卢建政;张慧【期刊名称】《固体电子学研究与进展》【年(卷),期】2005(25)3【摘要】对比研究了夹层结构Ni/Pt/Ni分别与掺杂p型多晶硅和n型单晶硅进行快速热退火形成的硅化物薄膜的电学特性.实验结果表明,在600~800°C范围内,掺Pt的NiSi薄膜电阻率低且均匀,比具有低电阻率的镍硅化物的温度范围扩大了100~150°C.依据吉布斯自由能理论,对在Ni(Pt)Si薄膜中掺有2%和4%的Pt样品进行了分析.结果表明,掺少量的Pt可以推迟NiSi向NiSi2的转化温度,提高了镍硅化物的热稳定性.最后,制作了I-V特性良好的Ni(Pt)Si/Si肖特基势垒二极管,更进一步证明了掺少量的Pt改善了NiSi肖特基二极管的稳定性.【总页数】5页(P422-426)【关键词】镍硅化物;快速热退火;X射线衍射分析;卢瑟福背面散射分析【作者】黄伟;张利春;高玉芝;金海岩;卢建政;张慧【作者单位】北京大学微电子研究院【正文语种】中文【中图分类】TN311.7【相关文献】1.Cr13Ni5Si2/γ-Ni三元金属硅化物高温耐磨复合材料 [J], 方艳丽;李安;张凌云;王华明2.激光熔敷Cr_2Ni_3Si/Cr_3Si金属硅化物复合材料涂层组织与高温耐磨性 [J], 段刚;王华明3.激光熔覆Ni_2Si/Ni_3Si_2金属硅化物合金涂层显微组织与耐蚀性 [J], 王春敏;蔡良续;王华明4.Pt层对Ni/Si(100)固相反应NiSi薄膜高温稳定性的增强效应 [J], 韩永召;李炳宗;屈新萍;茹国平5.激光熔敷Cr_3Si/Cr_2Ni_3Si金属硅化物涂层耐磨性与耐蚀性研究 [J], 段刚;王华明因版权原因,仅展示原文概要,查看原文内容请购买。
一种利用夹层Ta难熔金属提高NiSi薄膜热稳定性的新方法
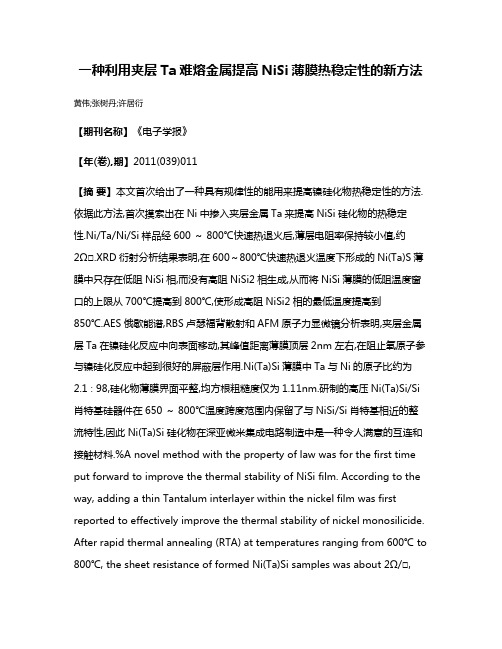
一种利用夹层Ta难熔金属提高NiSi薄膜热稳定性的新方法黄伟;张树丹;许居衍【期刊名称】《电子学报》【年(卷),期】2011(039)011【摘要】本文首次给出了一种具有规律性的能用来提高镍硅化物热稳定性的方法.依据此方法,首次摸索出在Ni中掺入夹层金属Ta来提高NiSi硅化物的热稳定性.Ni/Ta/Ni/Si样品经600 ~800℃快速热退火后,薄层电阻率保持较小值,约2Ω□.XRD衍射分析结果表明,在600~800℃快速热退火温度下形成的Ni(Ta)S薄膜中只存在低阻NiSi相,而没有高阻NiSi2相生成,从而将NiSi薄膜的低阻温度窗口的上限从700℃提高到800℃,使形成高阻NiSi2相的最低温度提高到850℃.AES俄歇能谱,RBS卢瑟福背散射和AFM原子力显微镜分析表明,夹层金属层Ta在镍硅化反应中向表面移动,其峰值距离薄膜顶层2nm左右,在阻止氧原子参与镍硅化反应中起到很好的屏蔽层作用.Ni(Ta)Si薄膜中Ta与Ni的原子比约为2.1∶98,硅化物薄膜界面平整,均方根粗糙度仅为1.11nm.研制的高压Ni(Ta)Si/Si 肖特基硅器件在650 ~800℃温度跨度范围内保留了与NiSi/Si肖特基相近的整流特性,因此Ni(Ta)Si硅化物在深亚微米集成电路制造中是一种令人满意的互连和接触材料.%A novel method with the property of law was for the first time put forward to improve the thermal stability of NiSi film. According to the way, adding a thin Tantalum interlayer within the nickel film was first reported to effectively improve the thermal stability of nickel monosilicide. After rapid thermal annealing (RTA) at temperatures ranging from 600℃ to 800℃, the sheet resistance of formed Ni(Ta)Si samples was about 2Ω/□,and its value is also lower than that of nickel monosilicide without the interlayer.X-ray diffraction (XRD) , AES,RBS and AFM results both reveal that NiSi phase exists in these samples,but the high resistance NiSi2 phase does not exist because tantalum interlayer as the diffusion barrier for oxygen element moved to the top of the thin film after rapid thermal annealing. Fabricated Ni(Ta)Si/Si Schottky barrier diodes with the guard ring structure displayed good quality,with the barrier height being located generally about 0.64 Ev and the ideality factor approachingunity.Therefore,It shows that Ni(Ta)Si is a satisfactory local connection and contact material.【总页数】5页(P2502-2506)【作者】黄伟;张树丹;许居衍【作者单位】中国电子科技集团公司第五十八研究所,江苏无锡214035;中国电子科技集团公司第五十八研究所,江苏无锡214035;中国电子科技集团公司第五十八研究所,江苏无锡214035【正文语种】中文【中图分类】TN311+.7【相关文献】1.反应射频磁控溅射法制备HfTaO薄膜的热稳定性和光学性能 [J], 马春雨;苗春雨;李树林;王文娟;张庆瑜2.一种提高金刚石薄膜形核密度的新方法 [J], 张贵锋;付庆辉3.纳米晶NbMoTaW难熔高熵合金薄膜力学性能及其热稳定性 [J], 冯骁斌;张金钰;刘刚;孙军4.一种修饰钙掺杂钛酸铅湿敏纳米薄膜的新方法--钾修饰薄膜的制备、湿敏特性和结构表征 [J], 王智民;左霞;韩基新;刘静波;张艳熹5.难熔夹层金属提高NiSi薄膜热稳定性的新思路 [J], 黄伟;孙华;张利春;张树丹;许居衍因版权原因,仅展示原文概要,查看原文内容请购买。
磷腈碱催化开环聚合制备含氟聚乙基硅氧烷

Vol. 35 No. 5功 能 高 分 子 学 报2022 年 10 月Journal of Functional Polymers417文章编号: 1008-9357(2022)05-0417-08DOI: 10.14133/ki.1008-9357.20220105001磷腈碱催化开环聚合制备含氟聚乙基硅氧烷刘正阳1, 时金凤1, 赵 娜1, 李志波1,2(青岛科技大学 1. 高分子科学与工程学院; 2. 化工学院, 山东 青岛 266042)摘 要: 以有机环三磷腈碱(CTPB)作为催化剂,在温和条件下催化六乙基环三硅氧烷(E3)开环聚合(ROP),以及E3与1,3,5-三甲基-1,3,5-三(3,3,3-三氟丙基)环三硅氧烷(F3)开环共聚合,制备了聚二乙基硅氧烷(PDES)和含有不同三氟丙基甲基硅氧(F)单元摩尔分数(0~46%)的聚(二乙基-ran-三氟丙基甲基)硅氧烷(PDES-ran-PTFPMS)。
采用凝胶渗透色谱仪(GPC)、核磁共振波谱仪(NMR)表征了聚合物的组成和结构,利用差示扫描量热仪(DSC)和微观接触角测量仪对聚合物的性质进行研究。
结果表明:成功制得PDES-ran-PTFPMS。
当F单元摩尔分数高于6%时,可以有效抑制PDES的低温结晶,且PDES-ran-PTFPMS具有极低的玻璃化转变温度(T g =−134 ℃)。
含氟聚乙基硅氧烷薄膜的接触角测试结果表明,F单元的引入有效提高了聚乙基硅氧烷的疏水性及降低了油的浸润性。
关键词: 有机磷腈碱;开环聚合;聚(二乙基- ran-三氟丙基甲基)硅氧烷;低玻璃化转变温度中图分类号: O633.4 文献标志码: APreparation of Fluorine-Containing Polyethylsiloxane by Ring-Opening Polymerization of Cyclic Siloxanes Catalyzed by Phosphazene BaseLIU Zhengyang1, SHI Jinfeng1, ZHAO Na1, LI Zhibo1,2(1. College of Polymer Science and Engineering; 2. College of Chemical Engineering,Qingdao University of Science and Technology, Qingdao 266042, China)Abstract: The ring-opening copolymerization (ROP) of hexaethylcyclotrisiloxane (E3) and 1,3,5-trimethyl-1,3,5-tri(3,3,3-trifluoropropyl) cyclotrisiloxane (F3) was catalyzed by organic cyclotrisiloxane base (CTPB) under mild conditions. CTPB showed high catalytic activity for the polymerization of E3 and F3. Linear polydiethylsiloxanes (PDES) and poly(diethyl-ran-trifluoropropylmethyl) siloxanes (PDES-ran-PTFPMS) with different mole fractions of trifluoropropylmethyl siloxane group (F unit) (mole fraction (f F): 0−46%) were successfully synthesized. The composition and structure of the PDES-ran-PTFPMS copolysiloxanes were characterized in detail by gel permeation chromatography (GPC) and nuclear magnetic resonance (NMR), and the glass transition temperature (T g) and crystallization behavior of the polymers were comprehensively analyzed by differential scanning calorimetry, and the water-oil contact angle of fluorine-containing polyethylsiloxane film was investigated by microscopic contact angle test. The chemical positions of the resonance peaks in the nuclear magnetic收稿日期: 2022-01-05基金项目: 山东省自然科学基金联合基金(No. ZR2020LFG014)作者简介: 刘正阳(1994—),男,山东潍坊人,硕士生,主要研究方向为聚硅氧烷的合成及改性工作。
用XPS法研究硅基硫化锌薄膜

用XPS法研究硅基硫化锌薄膜
曾明刚;陈松岩;林爱清;邓彩玲;蔡贝妮
【期刊名称】《半导体技术》
【年(卷),期】2005(30)2
【摘要】应用X射线光电子能谱(XPS)研究Si基ZnS:Cu,Er薄膜的化学元素组成、分布和价态, 认为Cu元素只有少数部分进入晶格中替代Zn2+起激活剂的作用,Er
元素在ZnS基质中分布不均匀,且会与氧结合。
PL测试发现样品发绿光,主要发光
峰出现劈裂,对研究薄膜中的杂质中心、实现Si基发光有参考意义。
【总页数】4页(P17-20)
【关键词】X射线光电子能谱;杂质中心;Si基材料
【作者】曾明刚;陈松岩;林爱清;邓彩玲;蔡贝妮
【作者单位】厦门大学物理系
【正文语种】中文
【中图分类】O484.1
【相关文献】
1.SO1-Gel法硅基PZT铁电薄膜研究 [J], 张林涛;任天令;张武全;刘理天;李志坚
2.鼓泡法在金刚石薄膜/硅基界面结合强度定量测量中的应用分析与试验研究 [J], 胡斌;孙方宏;简晓刚;晋占峰;陈明
3.PECVD法硅基氮化硅薄膜的制备及其耐磨性研究 [J], 王大刚;张德坤
4.用XPS法研究硫化锌薄膜 [J], 陈振湘;柳兆洪;刘瑞堂;王余姜;邱伟彬
5.Sol-Gel法硅基铁电薄膜研究 [J], 张林涛;任天令;张武全;刘理天;李志坚
因版权原因,仅展示原文概要,查看原文内容请购买。