事故分析表
工程事故分析表

危害名称
发生原因
发生部位
影响程度
1
触电
绝缘、接地不好,用电设备不完好,不遵守规程,不了解维护区域线路情况。
作业过程
人员伤亡
2
着火
作业附近有易燃物或可燃气体,未按规定用火,电气火灾。
施工现场
人员伤亡
财产损失
3
爆炸
作业空间有可燃气体或油气未清理净,未按规定用火,电气火空坠落
脚手架不牢、未系安全带未按操作规程进行作业。
施工现场
人员伤亡
5
机械伤害
机械故障、机械防护装置失效、未按规定着装,未按设备操作规程作业。
作业过程
人员伤亡
6
环境影响
垃圾乱倒、废油未经处理乱倒、现场作业垃圾及粉尘造成,草木被破坏。
作业过程
人身伤害
事故原因综合分析表(CLC)应用方法2019年

1、未遵 循现有的 程序
2、工具 、装置/ 设备或车 辆的使用
3、防护 设备或方 法的使用
事故因素
分析细则-免责减责条件
1.1违章(个人)
该项操作具有规章制度、操作要求、安全注意事项、要求图片示范 、培训要求等员工知晓的条款;
1.2违章(集体)
作业现场长期存在、作业时多人违反、班组多人违反上述的规章制 度、公司管理制度中的条款;
作业动作超出作业要求范围,未意识到操作存在的危险性; 日常行为不属于工作操作内事项,走路、跌倒、摔倒等; 精神状态、个人行为、情绪存在问题;
监控、录音; 作业沟通录音、互保记录、
师徒记录; 作业过程记录、操作范围规
定; 视频、录音; 班前记录、状态检查、视频
、录音
可能的直接原因—状态
分析细则-免责减责条件
1.3违章指挥(管理人员)
班组长及以上管理人员违反安全操作要求、公司管理制度、员工提 出安全质疑、安全标准法规安排作业人员作业;
1.4无程序可用
该项操作无作业规程、管理制度、作业培训内容的约束;
1.5不理解程序
员工对规章制度及岗前操作技能、安全方面的培训理解不清楚,仍 然进行作业;
1.6其他
相关作业票据、作业证件、防范措施有明确未落实等;
6.工具、 6.3工具故障 装置/设 6.4工具的准备 备和车辆
6.5车辆故障
6.6车辆准备
6.7其他
7.1火灾和爆炸
7.2噪音
7.3带电电气系统
7.4非电气类的能量来源
7.工作暴 7.5极端温度
露
7.6危险化学品
7.7机械危险
7.8暴风雨或自然现象 7.9其他
事故质量趋势分析报表

事故质量趋势分析报表概述本报表旨在分析事故质量的趋势,并提供相关数据和图表,以帮助企业了解和改善事故质量管理。
数据收集为了准确分析事故质量的趋势,我们收集了以下数据:- 事故发生日期和时间- 事故类型和级别- 受影响的部门或区域- 造成的损失和影响- 在事故发生后采取的纠正措施趋势分析事故数量趋势通过对事故发生日期和时间的分析,我们可以观察到事故数量的趋势。
以下是一份事故数量趋势图表:根据图表,我们可以看到事故数量在过去一年中保持了相对稳定的趋势。
然而,在某些月份,事故数量明显增加,这提示了我们在这些特定时间段需要额外的注意和预防措施。
事故类型分布通过对事故类型和级别的分析,我们可以了解不同类型事故的分布情况。
以下是一份事故类型分布图表:根据图表,最常见的事故类型是人为操作失误和设备故障。
这为我们提供了改进培训和设备维护的机会,以减少这些类型的事故发生。
纠正措施效果评估通过对事故发生后采取的纠正措施的分析,我们可以评估这些措施的实际效果。
以下是一份纠正措施效果评估表:根据评估表,采取的纠正措施被认为是有效的,因为它们已经成功地减少了类似事故的再次发生。
结论与建议基于以上分析,我们得出以下结论和建议:- 在事故数量较多的月份,加强预防措施和员工培训,以降低事故风险。
- 针对人为操作失误和设备故障类型的事故,加强员工培训和设备维护。
- 继续监测纠正措施的效果,并根据评估结果调整和改进措施。
请注意,本报表所提供的结论和建议仅供参考,具体实施还需要基于企业的实际情况进行个性化调整和决策。
感谢阅读本报表,如有任何疑问或进一步讨论,请及时与我们联系。
事故原因综合分析表

5-1 不恰当的行为得到奖励
6-1 对需要的技能未作充分的评估
节省时间或努力
6-2 未充分使用掌握的机能
图方便
6-3 技能未经常操练
博取他人注意
6-4 缺乏对技能的指导
5-2 不当的管理示范
6-5 没有充分的温习以巩固技能
55--34 对对关关键键的的安安全全行行为为没没有有足足够够的的认强识化执 6-6 其他
可能的系统原因
人的因素
4.精神紧张 4-1 全神灌注于别的问题 4-2 困扰 4-3 混淆的工作指示或要求 4-4 相冲突的工作指示或要求 4-5 无意义或降低等级的活动 4-6 情绪超负荷 4-7 超量的对判断和决定的需求 4-8 过度需要集中精力感知 4-9 极度乏味 4-10 其他
5.行为
6.技能水平
行 正确的行为被责备
不当的同事压力
表现反馈不足
纪律处分的不充分
5-5 过分的急工好利
5-6 采用不当的生产奖励方法
5-7 主管暗中催促
5-8 员工性急
5-9 其他
工作因素
10、工程/设计
11、工作计划
10-1 技术设计欠妥
11-1 工作计划欠妥
设计依据陈旧
11-2 预防性保养欠妥
设计依据不正确
对需求的评估
2.身体条件 2-1 原先受过伤或得过病 2-2 疲劳
由于工作量 由于缺乏休息 由于感官超载 2-3 能力下降 由于温度过高或过低 由于缺氧 由于气压变化 22--45 血由糖于不使足用药物或酒精而使能力削 弱 2-6 其他
3.精神状态 3-1 判断能力差 3-2 记忆力丧失 3-3 不良的协调和反映时间 3-4 情绪干扰 3-5 害怕或恐惧 3-6 机械能力差 3-7 学习能力差 3-8 受药物影响 3-9 其他
生产线火灾事故分析表格

生产线火灾事故分析表格1. 事故基本信息事故名称:生产线火灾事故发生时间:2021年5月15日事故地点:某工厂生产车间事故等级:重大事故事故类型:火灾事故2. 事故背景简述在某工厂生产车间,一台生产线突然发生火灾事故,造成了严重的损失及生产中断。
事故发生后,工厂立即组织应急救援,并报告相关部门进行事故调查处理。
3. 事故原因分析3.1 设备故障在初步调查中发现,火灾事故是由生产线上的设备故障引起的。
设备在运行过程中出现异常,导致设备起火,随后火灾迅速蔓延。
3.2 维护保养不当相关负责人在事后承认,该设备存在维护保养不当的情况,缺乏定期检查与维护,导致设备发生故障的风险增加。
3.3 解决方案不及时工厂员工发现设备出现异常后,并未立即采取有效措施进行处理,导致事故发展失控。
4. 事故损失评估4.1 人员伤亡事故中未造成人员伤亡,但部分员工因情绪激动而受到影响。
4.2 财产损失设备受损严重,需要大量资金进行修复和更换;同时生产线上的产品原料等也受到了损坏;由于事故导致生产中断,工厂面临了巨大的经济损失。
4.3 环境影响火灾导致车间内的环境污染,需要进行清理和修复。
5. 事故应对及后续处理5.1 应急救援事故发生后,工厂立即启动应急救援程序,安全疏散员工,防止事故危害扩大。
5.2 事故调查工厂成立专门的事故调查组,对事故进行深入调查,查明事故原因,并提出防范措施。
5.3 安全预防工厂立即对所有生产设备进行全面检查,并对设备维护保养进行加强,降低设备故障发生的概率。
5.4 维护人员培训加强对维护人员的培训,提高其对设备运行情况的敏感度,增强设备维护保养的专业性和及时性。
5.5 组织整改工厂针对事故原因,对相关管理责任人进行约谈并进行整改,加强事故防范措施。
6. 事故启示及教训6.1 安全防范意识生产线上设备的安全防范意识需要进一步增强,员工需要时刻关注设备运行情况,发现异常及时处理。
6.2 安全培训对相关管理人员和员工进行安全培训,提高其应对突发事件的能力和应变能力。
火灾事故报告表

火灾事故报告表
引言:
本次报告是对最近发生的一起火灾事故进行调查分析,并总结出造成火灾的原因,以及提出预防措施和建议,旨在增强公众对火灾危害的认识和应对能力。
第一部分:事故背景
1. 事故概述
2. 事故地点和时间
3. 人员伤亡情况
第二部分:事故原因分析
1. 火源起因
a) 引燃原因
b) 烟火自燃、电器故障等可能性
2. 燃烧传播途径
a) 建筑结构、装修材料的易燃性
b) 通风条件的影响
3. 消防设施评估
a) 系统完整性与有效性
b) 自动喷水系统、消防栓等是否正常运行
第三部分:现行管理制度存在问题及改进方案建议
1. 建筑设计与建设规范方面有待加强
a) 加强建筑材料的选取和使用限制
2. 监督检查体系需完善,执法力度加大
a) 提高相关技术人员的培训和资质要求
3. 提升公众火灾安全意识与应急能力
a) 宣传普及消防知识,加强火灾预防教育
b) 加强社区消防设备建设和演练
第四部分:事故对策与预防措施
1. 建议完善消防技术标准和规范
a) 更新现有建筑材料可燃性评估方法
2. 消防安全责任划分明确,各方共同参与
a) 增加自动化火灾报警系统覆盖范围
3. 新建建筑物必须符合严格的消防标准
a) 强制使用耐火门、消防玻璃等装置
结语:
通过对本次火灾事故进行调查和分析,我们深入了解了造成事故发生的原因,
并提出了一系列改进与预防措施。
只有不断加强公众对火灾风险的认识以及相关管理制度的实施,才能有效预防和减少类似事件的发生。
这是一个长期而复杂的过程,需要各界共同努力,守望相助,以实现火灾安全的目标。
生产安全事故案例分析表

事故案例剖析人
时间:
部门:
事故案例名称
机械伤害事破碎岗位员工,未停机状态下,佩戴手套用手清理破碎机中杂物,造成该员工右手卷入设备中,事故发生后榨油车间员工赶来,将设备停机,拿取工具拆卸设备,因对设备的不熟悉更换几次工具后,最后拿来撬杠将破碎辊撬开缝隙,将该名员工的手拿出,送往医院救治,最终该员工右手腕部以下部位截肢。据事后调查,该员工在以往作业过程中多次存在不停机清理设备的情况。
事故直接原因
事故间接原因
防范措施及依据的法律法规、标准规范
事故原因分析
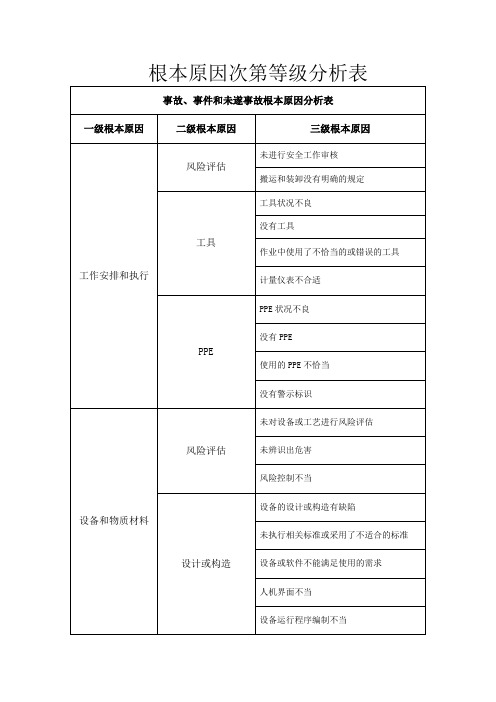
事故、事件和未遂事故根本原因分析表
一级根本原因
二级根本原因
三级根本原因
工作安排和执行
风险评估
未进行安全工作审核
搬运和装卸没有明确的规定
工具
工具状况不良
没有工具
作业中使用了不恰当的或错误的工具
计量仪表不合适
PPE
PPE状况不良
没有PPE
使用的PPE不恰当
没有警示标识
设备和物质材料
没有进行PPE穿戴的培训
没有进行使用工具的培训
岗位职责
工作任务不清
职责不清
绩效指标的设定
未制定团队或个人的绩效目标
管理层的义务
政策不健全
缺乏领导可视化
缺乏对整改措施的跟踪检查
监督
没有清晰地向员工说明重大安全风险
资源的支持
人手不足
5项
24项
93项
设备上无合适的防护装置
超能力和超极限使用设备
包括紧急停止开关在内的各种控制按钮未明确标识或区分
维修
没有维修
设备故障
维修不当(缺乏备件、缺乏定期维修或预防性维修等等)
使用报废或超期服役的设备
安全设施失效
软件或硬件未更新
材料
没有物质安全数据表
未辨识出有害物质
存在有毒气体或异味
标签不当
对材料的质量要求不当
材料被污染
材料的处理不当(存储、运输、使用或处置)
采样不当
一级根本原因
二级根本原因
三级根本原因
设备和物质材料
人机工程
使用不便
人机界面有缺陷
环境
当地的环境
生产工艺经常变换带来影响
生产工艺受到湿度、震动、噪音和光线等的影响。