生产过程质量问题分析及预防措施讲述
产品质量问题的原因分析及预防措施

产品质量问题的原因分析及预防措施咱今儿就来好好唠唠产品质量这档子事儿。
前几天我去超市买个电水壶,想着回家能方便烧个水喝。
结果没用两天,这水壶就开始漏水,差点没把我家插座给弄短路喽!这可把我给气坏了,我就寻思,这好好的水壶咋质量这么差呢?其实啊,产品质量出问题的原因那是五花八门。
就拿生产过程来说吧,有些厂家为了省俩钱儿,采购的原材料那质量就不过关。
比如说做家具,用的木头水分太大,没经过充分干燥处理,做出来的桌椅板凳用不了多久就变形开裂。
这能怪谁?还不是厂家自己偷工减料闹的。
还有啊,生产设备要是老化破旧,也容易出质量问题。
我认识一个开小服装厂的老板,他那缝纫机都用了十几年了,也不舍得换,结果做出来的衣服针脚歪歪扭扭,线头到处都是,这能卖得出去才怪!工人的技术水平和责任心也是关键。
有的工人干活儿毛手毛脚,不按照规范操作,能不出岔子吗?我听说有个工厂生产手机壳,有个工人给手机壳喷漆的时候心不在焉,喷得厚薄不均,颜色也不正,这一批货全砸手里了。
除了生产环节,管理不善也是个大问题。
没有严格的质量检验制度,不合格的产品就容易流向市场。
就像我买的那个电水壶,说不定就是在检验的时候蒙混过关的。
那咋预防这些质量问题呢?首先,厂家得把好原材料这一关,不能只看价格,得注重质量。
该花的钱就得花,别总想着省那仨瓜俩枣的。
设备也得定期维护更新,别让那些老掉牙的机器还在那儿硬撑着。
对工人得加强培训,让他们知道规范操作的重要性,干好了有奖励,干不好得惩罚,这样他们才能上心。
管理方面,一定要建立完善的质量检验制度,不能走过场。
每一个环节都要认真检查,不放过任何一个小毛病。
另外,厂家还得关注市场反馈。
如果消费者对产品有意见,得赶紧改进,不能装聋作哑。
总之啊,产品质量可不是小事儿,关乎着厂家的声誉和消费者的利益。
只有把质量问题重视起来,采取有效的预防措施,才能在市场上站稳脚跟,赢得消费者的信任。
可别像我买的那个破水壶似的,让人闹心!希望以后咱买东西都能买到质量杠杠的,用着舒心的好产品!。
生产中的质量问题预防措施
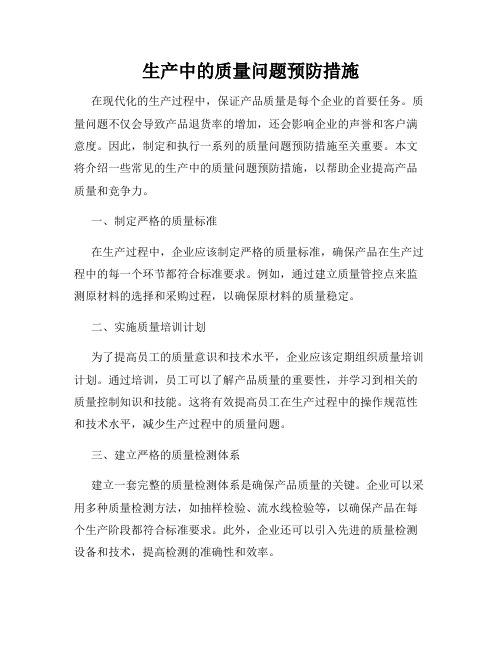
生产中的质量问题预防措施在现代化的生产过程中,保证产品质量是每个企业的首要任务。
质量问题不仅会导致产品退货率的增加,还会影响企业的声誉和客户满意度。
因此,制定和执行一系列的质量问题预防措施至关重要。
本文将介绍一些常见的生产中的质量问题预防措施,以帮助企业提高产品质量和竞争力。
一、制定严格的质量标准在生产过程中,企业应该制定严格的质量标准,确保产品在生产过程中的每一个环节都符合标准要求。
例如,通过建立质量管控点来监测原材料的选择和采购过程,以确保原材料的质量稳定。
二、实施质量培训计划为了提高员工的质量意识和技术水平,企业应该定期组织质量培训计划。
通过培训,员工可以了解产品质量的重要性,并学习到相关的质量控制知识和技能。
这将有效提高员工在生产过程中的操作规范性和技术水平,减少生产过程中的质量问题。
三、建立严格的质量检测体系建立一套完整的质量检测体系是确保产品质量的关键。
企业可以采用多种质量检测方法,如抽样检验、流水线检验等,以确保产品在每个生产阶段都符合标准要求。
此外,企业还可以引入先进的质量检测设备和技术,提高检测的准确性和效率。
四、加强供应商管理供应商的质量问题往往会直接影响到产品的质量。
为了预防质量问题,企业应建立完善的供应商管理体系。
对供应商的选择和评估要进行严格把关,确保所采购的原材料符合质量要求。
此外,企业还应与供应商保持紧密的合作和沟通,及时解决采购过程中的问题。
五、持续改进质量管理质量问题预防是一个不断改进的过程。
企业应该建立完善的质量管理体系,并进行持续改进。
通过定期的内部审查和外部评估,识别和解决潜在的质量问题,提高产品的质量水平。
同时,企业还可以借鉴其他行业的先进经验和技术,不断提升质量管理的水平。
六、建立质量问题反馈机制及时了解和处理质量问题是预防质量问题的重要环节。
企业应建立起一套完善的质量问题反馈机制,包括客户投诉管理、内部质量问题汇报等。
通过及时处理和分析质量问题,找出问题产生的原因,并采取相应措施进行改进,避免类似问题再次发生。
质量问题预警和预防措施

质量问题预警和预防措施一、引言质量问题是制造业中不可避免的风险之一。
一旦产品质量存在问题,将会对企业的声誉和利润造成巨大影响。
因此,质量问题的预警和预防措施是每个企业都需要重视和采取的措施。
本文将介绍质量问题的预警机制以及一些常见的预防措施,旨在帮助企业提高质量管理水平,降低质量风险。
二、质量问题的预警机制1. 内部预警机制企业内部的质量问题预警机制是指企业通过建立一套完善的内部监控体系,及时发现和处理潜在的质量问题。
这个机制包括以下几个方面:•质量指标监控:企业可以通过建立具体的质量指标,监控产品的关键质量参数,及时发现异常情况。
例如,可以对产品的尺寸、外观等进行监测,一旦超出预定的范围,即可引发预警。
•过程控制:企业可以通过建立严格的生产过程控制流程,确保每个环节的质量问题得到有效控制。
例如,可以设置多个检验点,对生产过程中的关键环节进行检查,发现问题及时处理。
•数据分析:企业可以通过对大量数据进行分析,寻找潜在的质量问题。
例如,可以通过统计分析生产过程中的测量数据、设备运行数据等,发现数据异常,并推断出潜在的质量问题。
2. 外部预警机制除了内部的预警机制,企业还应关注外部的预警信息,及时了解市场和行业的质量问题,以此预防自身的质量问题。
•行业监测:企业可以加入相关的行业组织,及时了解行业的质量标准和最新的质量问题。
定期参加行业会议,与同行交流,了解行业中的典型问题和解决方法。
•市场反馈:企业可以建立完善的客户投诉反馈机制,及时了解市场上的质量问题,并进行分析和处理。
例如,可以设置客户服务热线,接收客户的投诉,并对投诉进行分类和分析,找出质量问题的根本原因,并采取相应的预防措施。
三、质量问题的预防措施质量问题的预防是制造业中质量管理的核心任务之一。
通过采取一系列预防措施,企业可以减少质量问题的发生,提高产品的质量水平。
下面是一些常见的质量问题预防措施:1. 设立质量管理体系企业应建立健全的质量管理体系,明确质量目标和要求。
质量控制中经常出现的问题及解决方案

质量控制中经常出现的问题及解决方案质量控制是生产过程中至关重要的一环,直接关系到产品的质量和客户满意度。
然而,在实际操作中,经常会出现各种各样的问题,影响到质量控制的效果。
下面将就质量控制中经常出现的问题及解决方案展开讨论。
1. 材料质量不稳定在生产过程中,材料质量的稳定性直接影响到产品的质量稳定性。
解决这个问题的关键在于选择和合作优质的供应商,建立长期稳定的供应关系,并进行充分的沟通与协调,确保材料质量得到保障。
2. 加工设备故障加工设备出现故障会导致产品质量不稳定,影响生产进度。
为了避免这种情况,企业应定期对设备进行维护保养,及时发现并解决潜在问题,确保生产过程的顺利进行。
3. 人员技术不足生产线上的操作人员技术不足会导致产品质量出现问题。
企业应该加强对员工的培训和技术指导,提高员工的技术水平和操作能力,确保生产过程中的质量控制。
4. 设计缺陷产品设计缺陷是导致质量问题的重要原因之一。
企业应该加强与设计部门的沟通与协作,及时发现和解决设计缺陷,保证产品的质量稳定性。
5. 检测手段不到位检测手段不到位会导致质量问题无法及时发现和解决。
企业应该不断引进先进的检测设备和技术,提高产品的质量检测水平,确保产品质量符合要求。
6. 生产过程控制不严生产过程控制不严会导致产品质量波动较大。
企业应建立完善的生产过程控制体系,制定严格的生产工艺流程和操作规范,确保每一道生产环节都得到严格控制。
7. 供应商管理不到位供应商管理不到位会导致原材料质量无法得到保证。
企业应建立完善的供应商管理制度,对供应商进行全面评估和监督,确保供应商提供的材料符合质量标准。
8. 缺乏反馈机制鲜有反馈机制会导致质量问题无法及时发现和解决。
企业应建立健全的质量反馈机制,定期开展产品质量评估和反馈,及时发现问题并采取相关措施加以解决。
9. 零部件质量问题零部件质量问题会直接影响到产品的整体质量。
企业应加强对零部件供应商的管理和把控,确保零部件质量符合标准,从根本上解决质量问题。
生产过程中常见的质量控制失误及预防措施
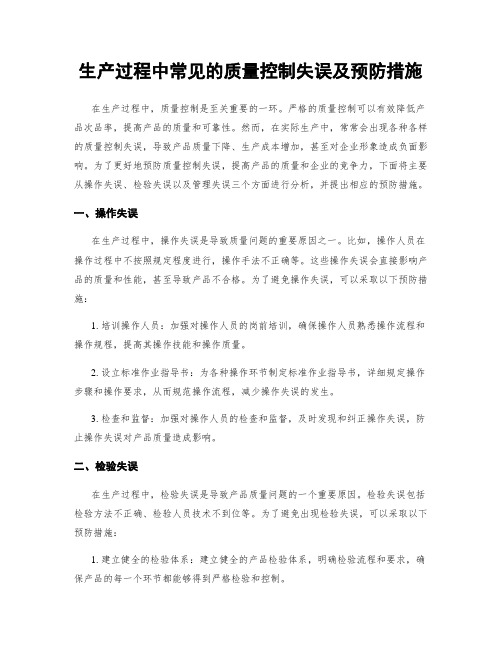
生产过程中常见的质量控制失误及预防措施在生产过程中,质量控制是至关重要的一环。
严格的质量控制可以有效降低产品次品率,提高产品的质量和可靠性。
然而,在实际生产中,常常会出现各种各样的质量控制失误,导致产品质量下降、生产成本增加,甚至对企业形象造成负面影响。
为了更好地预防质量控制失误,提高产品的质量和企业的竞争力,下面将主要从操作失误、检验失误以及管理失误三个方面进行分析,并提出相应的预防措施。
一、操作失误在生产过程中,操作失误是导致质量问题的重要原因之一。
比如,操作人员在操作过程中不按照规定程度进行,操作手法不正确等。
这些操作失误会直接影响产品的质量和性能,甚至导致产品不合格。
为了避免操作失误,可以采取以下预防措施:1. 培训操作人员:加强对操作人员的岗前培训,确保操作人员熟悉操作流程和操作规程,提高其操作技能和操作质量。
2. 设立标准作业指导书:为各种操作环节制定标准作业指导书,详细规定操作步骤和操作要求,从而规范操作流程,减少操作失误的发生。
3. 检查和监督:加强对操作人员的检查和监督,及时发现和纠正操作失误,防止操作失误对产品质量造成影响。
二、检验失误在生产过程中,检验失误是导致产品质量问题的一个重要原因。
检验失误包括检验方法不正确、检验人员技术不到位等。
为了避免出现检验失误,可以采取以下预防措施:1. 建立健全的检验体系:建立健全的产品检验体系,明确检验流程和要求,确保产品的每一个环节都能够得到严格检验和控制。
2. 提高检验人员技术水平:加强对检验人员的培训和学习,提高其专业技术水平和检验水平,减少检验失误的发生。
3. 重视检验过程:重视产品检验过程,确保检验环节符合操作规程和质量标准,避免由于检验失误导致产品质量问题。
三、管理失误在生产过程中,管理失误是导致质量问题的又一重要原因。
管理失误包括管理层对质量问题的重视程度不够、内部管理不规范等。
为了避免管理失误,可以采取以下预防措施:1. 强化管理责任:建立健全的质量管理体系,明确各级管理人员的管理责任和质量目标,引导其重视产品质量,推动整个生产过程持续改进。
工厂生产过程中的常见问题及解决方法
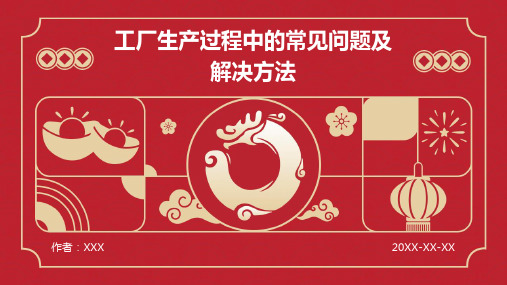
建立完善的质量检测体系,及时处理质量问题
总结词
确保产品质量
详细描述
建立完善的质量检测体系,对原材料、半成品和成品进 行严格的质量检测。采用统计过程控制(SPC)等工具 ,及时发现并处理质量问题。对质量数据进行追溯和分 析,找出潜在问题并采取改进措施。
采用新技术新工艺,降低原材料及能源消耗成本
总结词:降低成本
详细描述
通过对生产流程进行详细分析,可以发现哪些环节存在瓶颈,如物料供应、设备运转、人员操作等,针对这些瓶 颈制定相应的优化措施,可以提高生产效率。
设备运转效率低下
总结词
设备运转效率低下会直接影响生产效率和产品质量。
详细描述
设备老化、维护不当、故障频繁等问题都会导致设备运转效率低下,为了解决 这一问题,需要定期对设备进行维护和保养,及时更换老化部件,提高设备运 转效率。
噪音是工厂车间中常见的污染问题,长期暴露在噪音污染环境下会给员
工的身心健康带来严重影响。
02 03
详细描述
工厂车间的机械设备运行时会产生噪音,长期暴露在这种环境下会对员 工的听力造成损害,同时还会引起心脑血管疾病、神经系统疾病等健康 问题。
解决方法
采用低噪音设备、对设备进行定期维护和润滑、提高工厂布局合理性等 措施来降低车间噪音污染。此外,还可以为员工配备耳塞、耳机等个人 防护用品。
人员操作不熟练
总结词
人员操作不熟练会导致生产效率低下和产品质量不稳定。
详细描述
员工技能培训不足、操作不规范等问题都会导致人员操作不 熟练,为了解决这一问题,需要加强员工技能培训,制定操 作规范,提高员工操作熟练度和产品质量稳定性。
02 产品质量问题
CHAPTER
产品不良率较高
产品质量问题的根源分析及预防机制
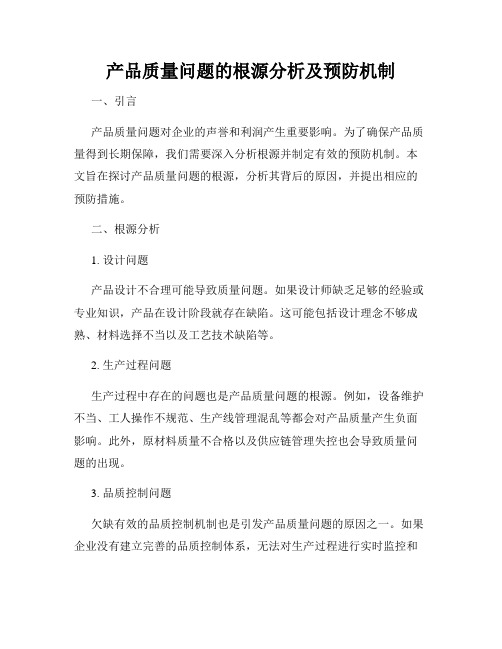
产品质量问题的根源分析及预防机制一、引言产品质量问题对企业的声誉和利润产生重要影响。
为了确保产品质量得到长期保障,我们需要深入分析根源并制定有效的预防机制。
本文旨在探讨产品质量问题的根源,分析其背后的原因,并提出相应的预防措施。
二、根源分析1. 设计问题产品设计不合理可能导致质量问题。
如果设计师缺乏足够的经验或专业知识,产品在设计阶段就存在缺陷。
这可能包括设计理念不够成熟、材料选择不当以及工艺技术缺陷等。
2. 生产过程问题生产过程中存在的问题也是产品质量问题的根源。
例如,设备维护不当、工人操作不规范、生产线管理混乱等都会对产品质量产生负面影响。
此外,原材料质量不合格以及供应链管理失控也会导致质量问题的出现。
3. 品质控制问题欠缺有效的品质控制机制也是引发产品质量问题的原因之一。
如果企业没有建立完善的品质控制体系,无法对生产过程进行实时监控和调整,那么产品质量就无法得到有效控制。
此外,缺乏内部品质文化和员工质量意识也会影响产品质量。
4. 反馈机制问题缺乏有效的反馈机制会导致产品质量问题无法及时解决。
如果企业无法及时了解到客户的反馈和投诉,就无法迅速采取措施进行整改和修复,进而导致质量问题的扩大化。
三、预防机制1. 优化设计流程加强设计团队的专业能力培养和技术培训,提高设计师的设计水平和经验积累。
同时,建立完善的设计评审机制,确保产品设计具备合理性和可行性。
2. 强化生产过程管理注重设备的日常维护保养,确保工作环境干净整洁,并制定相关操作规范以规范员工的操作行为。
建立科学合理的生产计划和制度,确保生产过程的透明度和可控性。
另外,还需要加强供应链管理,确保原材料的质量和可靠性。
3. 建立完善的品质控制体系制定严格的品质控制标准和操作规程,引入先进的质量管理工具和方法,如六西格玛、SPC等,以提高品质控制的精度和有效性。
同时,加强内部品质文化建设,通过培训和激励机制,提高员工的质量意识和责任感。
4. 健全反馈机制建立健全的客户反馈机制,及时收集客户的需求和意见,并建立快速响应机制,确保客户问题得到及时解决。
制造业生产过程中的质量问题分析与解决
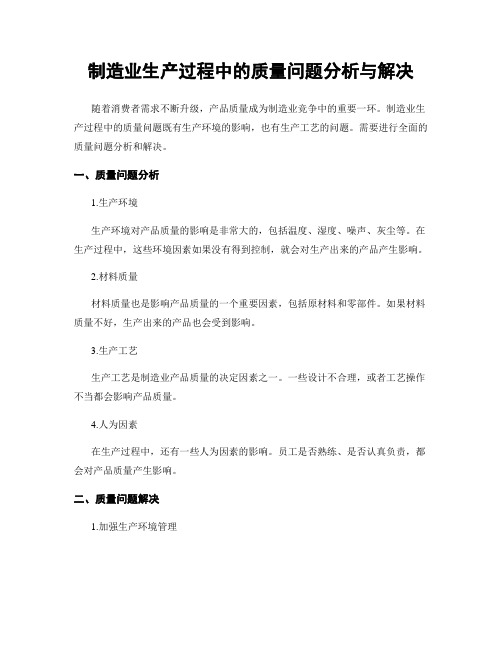
制造业生产过程中的质量问题分析与解决随着消费者需求不断升级,产品质量成为制造业竞争中的重要一环。
制造业生产过程中的质量问题既有生产环境的影响,也有生产工艺的问题。
需要进行全面的质量问题分析和解决。
一、质量问题分析1.生产环境生产环境对产品质量的影响是非常大的,包括温度、湿度、噪声、灰尘等。
在生产过程中,这些环境因素如果没有得到控制,就会对生产出来的产品产生影响。
2.材料质量材料质量也是影响产品质量的一个重要因素,包括原材料和零部件。
如果材料质量不好,生产出来的产品也会受到影响。
3.生产工艺生产工艺是制造业产品质量的决定因素之一。
一些设计不合理,或者工艺操作不当都会影响产品质量。
4.人为因素在生产过程中,还有一些人为因素的影响。
员工是否熟练、是否认真负责,都会对产品质量产生影响。
二、质量问题解决1.加强生产环境管理对于生产环境我们需要加强管理,维持生产现场的清洁卫生,保持恰当的温度、湿度、噪声和灰尘控制。
每天保持清洁,确保生产环境和生产机器始终保持干净和整洁。
2.材料质量控制在采购零部件之前,需要对各个品牌进行严格的产品质量检测,确定采购之后要经过更严格的检测,以防止采购到劣质的产品。
3.加强生产工艺控制在生产工艺控制方面,我们需要建立科学的、标准化的操作程序,同时加强工艺技能培训和监督。
有问题要及时解决,在工艺流程中遇到重要的节点,必须严格执行。
4.人为因素控制各工人要对工艺熟悉,加强对质量问题的培训,提高员工素质和责任心,让员工知道质量对企业至关重要,让其积极参与产品质量控制。
总结在生产过程中可以通过强化质量控制手段来控制生产环境和材料质量,并加强对生产工艺和人为因素的控制。
这样,就可以显著提高产品质量,让消费者对产品更满意,同时也让企业得到更好的社会效益。
- 1、下载文档前请自行甄别文档内容的完整性,平台不提供额外的编辑、内容补充、找答案等附加服务。
- 2、"仅部分预览"的文档,不可在线预览部分如存在完整性等问题,可反馈申请退款(可完整预览的文档不适用该条件!)。
- 3、如文档侵犯您的权益,请联系客服反馈,我们会尽快为您处理(人工客服工作时间:9:00-18:30)。
➢ 不良剥线的影响:
➢ a、导电性能
➢ b、机械强度
品质 服务 成本 创新
受伤或切断的线芯会降 低导电性能和机械强度
出现斜面将会 减弱导电性能
品质 服务 成本 创新
➢ 防水堵头的穿入:
➢ 方向 ➢ 位置
0.5~1.0mm
0~0.5mm预防解决措施
1.批量端子用错,偶发用错。 2.批量拉力值不够。偶发拉力值不够。
品质 服务 成本 创新
➢ 压接外观质量的基本判定(带防水堵头)
此区域必须可见线芯、绝缘皮和 防水堵头,且堵头无破损。
品质 服务 成本 创新
➢ 压接外观质量的基本尺寸判定方法(1/4)
品质 服务 成本 创新
➢ 压接外观质量的不良图例(1/5)
1.铜丝炸开、端子选型不对、操作工对要求不 理解。
4.端子铜丝外漏、铜丝不外漏、铜丝外漏过长。2.送线过短、送线过长。
3.下线时剥头长度长、工艺设计缺陷、线皮回 缩。
1.尾部压力过大防水栓破裂。
5.批量防水栓压接破裂、压到裙边等不良事项。23..钳 防口水与栓防穿水装栓不不到匹位配或过位。
4.操作工未自检。
生产过程质量问题分析与预防控制
下线工序
问题描述
原因分析
预防解决措施
1.批量下线尺寸与工艺要求不符。 2.批量性喷码错误、喷码不清
1.设备问题 2.未看清楚工艺 3.没有自检及填写自检记录与工艺文件核对。
1.未按工艺号码调整设备 2.没有自检及填写自检记录与工艺文件核对 3.设备有问题及墨材不匹配。
1.下线机压轮过紧或过松。 2.原材料线皮回缩导致剥头尺寸不符合工艺要 求。
5.批量1)线芯损伤2)线芯切断3)铜丝氧化
1.操作人员不清楚要求。2.操作工未自检 3.原材 料偏芯。4.原材料不合格操作未自检。
➢ 如何识别下线:
➢ b、不好的剥线:
线芯受伤
品质 服务 成本 创新
电线切斜
切断线芯
拉断绝缘皮
3.批量导线规格用错、导线种类用错。偶发用 错。
1.材料混放 2.未按工艺要求操作 3.未填写自检记录与工艺文件核对。 4.产品修复时未按照工艺要求规格选材。
4.批量防水栓用错、偶发防水栓用错。 5.下线时出现长短不一及剥头尺寸短、长
1.未看清工艺要求 2.产品标识未与工艺核对。 3.相似防水栓混装。
1.操作前未工艺与端子标识核对。 2.修复产品时用错端子。 3.端子外观很接近或
1.测试拉脱力选用导线线径不对。 2.未测试拉力值凭经验看压痕。 3.设备调拉力螺钉未锁紧,螺钉老化锁不紧。
3.批量端子外观压接变形。偶发端子变形。
1.操作工对压接端子外观合格与不合格不清楚。 2.端子压接完毕后没有自检。