第6章 数控铣削加工技术
数控铣削加工

数控铣削加工数控铣削加工是现代工业中非常重要的制造工艺之一。
它采用计算机控制的工具和机器,在三维坐标系下进行精密的硬质材料加工,确保部件尺寸精确、表面质量好并且生产效率高。
下面是一些关于数控铣削加工的详细介绍。
一、数控铣削加工的原理数控铣削加工设备通过计算机程序来控制工件在坐标系内的位置、方向和加工轨迹,从而完成各种形状的加工。
数控铣削加工的工作原理与手动操作的铣床是基本相同,但是数控铣削加工具有更高的精度和自动化程度。
二、数控铣削加工的设备数控铣削加工设备通常由数控系统、伺服电机、工作台、加工刀具等组成。
数控系统是整个设备的核心部分,它由电气元件、主控板、输入/输出接口、操作面板以及计算机软件等构成,它控制整个设备的运行和加工过程。
伺服电机是数控系统把指令转化为机械运动的执行部件,它们通过控制机械运动来实现加工与移动。
工作台是加工零件的位置,它通常具有载重能力和平移性能。
在加工过程中,工作台可以按照预先编好的程序移动,以便于定位及相对刀具进行加工。
加工刀具是数控铣削设备中最重要的部分,因为它们直接参与加工过程。
根据加工需要,可以使用直径、锥度和球形切削刀具来实现加工,它们可以依次更换或采用不同的切削方式来完成不同的加工任务。
三、数控铣削加工的优点数控铣削加工的优点主要体现在以下几个方面:1. 精度高。
数控铣削加工的精度达到了高水平,可以保证极高的形状和位置精度。
2. 自动化程度高。
数控铣削设备搭载了计算机控制系统,可以通过程序自动完成加工,而不需要人工干预。
3. 生产效率高。
相对于传统的手动铣床,数控铣削设备可以在更短的时间内完成同样的工作量,并且可以实现加工自动化,提高生产效率。
4. 应用范围广。
数控铣削加工适用于高精度、复杂形状零件的制造,如模具、零件、工具等。
四、数控铣削加工的应用数控铣削加工是一种重要的制造工艺,因此广泛应用于各种行业,如汽车、飞机、机械、模具制造、医疗仪器制造等。
下面是一些具体的应用场景:1. 汽车制造。
维修电工第六章数控铣削及加工中心加工工艺课件

加工工艺分析
一、数控铣削及加工中心的加工范围
1.数控铣削及加工中心加工的工艺范围
数控铣床和加工中心除了能铣削普通铣床能铣削的各种零件
表面外,还能铣削普通铣床不能铣削的复杂轮廓及三维曲面轮廓。
其不需要分度盘即可实现钻、镗、攻螺纹等孔系加工,添加附加
轴后可方便地实现多坐标联动的各种复杂槽形及立体轮廓的加工,
二、数控铣削加工零件的工艺性
图6-
11 统一定位基准的工艺要求a)以精铣规则外表面定位 b)增设工艺销孔定位 c)增设
工艺凸台
7)零件毛坯应具有一定的铣削加工余量和合理的余量分配。
二、数控铣削加工零件的工艺性
2.数控铣削加工的尺寸精度
普通数控铣床和加工中心的加工精度可达±(0.005~0.01)m
采用回转工作台和立卧转换的主轴头还可实现除安装基面外的五
面加工,加工工艺范围相当宽。数控铣削及加工中心的主要加工
对象有以下三类。
(1)平面类零件 加工面平行或垂直于水平面、加工面与水平面的
夹角为定角的零件,如箱体、盘、套、板类等平面零件,加工内
容包括内外形轮廓、筋台、各类槽形及台肩、孔系、花纹图案等
3.铣削加工
1)铣削前把机床调整好后,应将不用的运动方向锁紧。
2)机动快速进给时,靠近工件前应改为正常进给速度,以防刀具与
工件撞击。
三、切削加工通用工艺守则 铣削(JB/T 9168.3—1998)
3)铣螺旋槽时,应按计算选用的交换齿轮先进行试切,检查导程与
螺旋方向是否正确,合格后才能进行加工。
4)用成形铣刀铣削时,为提高刀具寿命,铣削用量一般应比圆柱形
和加工精度,因此需增加换刀与对刀次数。这会导致零件加工表面
第6章 数控铣削技术.ppt
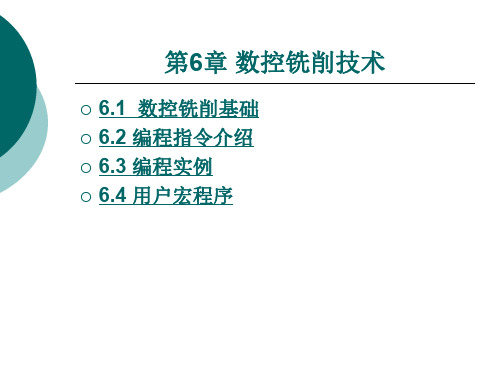
6.1 数控铣削基础
对刀步骤 数控铣床的对刀内容包括基准刀具的对刀和各个刀具相对偏
差的测定两部分。 从某零件加工所用到的众多刀具中选取一把作为基准刀具,
进行对刀操作 分别测出其他各个刀具与基准刀具刀位点的位置偏差值存人
刀具数据库
书中以基准刀具的对刀操作进行说明。
日标点,一般在G28或G30指令后使用,这样,经过的中间 点坐标就是由G28或G30指令所指定的中间点。 指令格式:G29 X_Y_Z_ X, Y, Z值指从参考点返回后日标点的坐标
上一页 下一页 返回
6.2 编程指令介绍
返回第2, 3, 4参考点G30
在程序中使用该指令,可使刀具经由一个中间点返回到第2、 3、4参考点,与G28的差别在于,G28只是返回第1参考点。
下一页 返回
6.1 数控铣削基础 来自.1.2 数控铣削编程特点 数控铣削编程方法及内容 数控铣削编程,在建立编程坐标系后,即按工件静止不动,刀
具绕工件运动的思路,确定走刀轨迹和编写程序,其编程的步 骤与数控车削编程类似。 主要内容包括:分析零件图样,确定加工工艺过程,图形的数学 处理,编写数控加工程序,最后进行程序的校验。 数控铣削编程点的确定及进退刀方式 加工时的进刀点应选在工件实体之外,以免在下刀过程中损坏 刀具;退刀点也选在工件实体之外,使零件表面能全部加工完毕。 一般的加工过程如图6-7所示。
上一页 下一页 返回
6.2 编程指令介绍
锁孔循环G85 指令格式:G98 (G99) G85 X_Y_Z_R_F_K_; 锁孔循环G86 指令格式:G98 (G99) G86 X_Y_Z_R_F_K_; 背锁循环G87 指令格式:G98 G87 X_Y_Z_R_Q_P_F_K_; 锁孔循环G88 指令格式:G98 G88 X_Y_Z_R_P_F_K_; 镗孔循环G89 指令格式:G98 G89 X_Y_Z_R_P_F_K_;
数控铣削加工技术实训报告

一、实训目的本次实训旨在使学生了解数控铣削加工的基本原理、加工工艺、编程方法和操作技能,提高学生的动手能力和实际操作水平。
通过本次实训,使学生掌握以下技能:1. 熟悉数控铣床的结构、性能及操作方法;2. 掌握数控铣削加工工艺参数的设置;3. 熟练运用CAD/CAM软件进行零件编程;4. 熟悉数控铣削加工过程中的常见问题及解决方法。
二、实训内容1. 数控铣床的结构及性能(1)数控铣床的分类:根据加工对象的不同,数控铣床可分为立式数控铣床、卧式数控铣床和立卧两用数控铣床。
(2)数控铣床的结构:数控铣床主要由床身、主轴箱、进给箱、工作台、刀架、数控系统等部分组成。
(3)数控铣床的性能:数控铣床具有较高的加工精度、自动化程度和加工效率。
2. 数控铣削加工工艺(1)加工前的准备工作:熟悉图纸、分析加工工艺、选择刀具、确定加工参数等。
(2)加工过程:装夹工件、设置加工参数、启动数控系统、进行加工、检查加工质量。
(3)加工后的工作:卸下工件、清理加工表面、检查加工质量、整理加工资料。
3. 数控铣削加工编程(1)编程软件:常用的编程软件有UG、Cimatron、Pro/E等。
(2)编程方法:根据零件的形状和尺寸,选择合适的编程方法,如轮廓编程、参数编程、直接编程等。
(3)编程步骤:分析零件形状、确定编程方法、编写程序、编译程序、调试程序。
4. 数控铣削加工操作(1)装夹工件:根据加工要求,选择合适的装夹方式,确保工件在机床上的稳定。
(2)设置加工参数:根据加工工艺和刀具参数,设置切削深度、进给量、转速等参数。
(3)启动数控系统:打开数控系统,输入程序,启动机床。
(4)进行加工:观察机床运行状态,确保加工过程中刀具与工件的位置关系正确。
(5)检查加工质量:加工完成后,检查加工表面质量、尺寸精度等。
三、实训过程1. 学习数控铣床的结构、性能及操作方法,了解数控铣削加工的基本原理。
2. 分析零件图纸,确定加工工艺,选择合适的刀具和加工参数。
数控铣削加工工艺PPT课件

定中心装夹 a) 用三爪自定心卡盘装夹 b) 用两顶尖装夹 c) 用自定心虎钳装夹
ห้องสมุดไป่ตู้、组合夹具
组合夹具的基本特点是满足标准化、 系列化、 通 用化的要求,具有组合性、 可调性、 柔性、 应急性和 经济性,使用寿命长,能适应产品加工中的周期短、 成本低等要求,比较适合在加工中心上应用。
数控夹具的调整 a) 平移式 b) 回转式 c) 复合式
1—定位支撑 2—钩形压板 3, 7—滚珠丝杠副 4—步进电动机 5, 6—齿轮 8—滑座 9—活动定位销
平移式自调数控夹具
数控夹具还有哪几种? 数控车床上有吗?
5. 专用夹具
l一夹具体 2一压板 3、7一螺母 4、5一垫圈 6一螺栓 8一弹簧 9一定位键 10一菱形销 11一圆柱销
双刃镗刀分类
结构特点不同
整体式(Ⅰ和Ⅱ) 模块式 (Ⅲ和Ⅳ)
工作特点不同 尺寸是否可调
浮动式(Ⅰ) 固定式(Ⅱ,Ⅲ,Ⅳ) 可调式(Ⅰ, Ⅲ,Ⅳ)
不可调式(Ⅱ)
可转位双刃镗刀的特点及适用场合见表4—3。
(2) 镗刀刀头 分为粗镗刀刀头和精镗刀刀头。
粗镗刀刀头
精镗刀刀头
将精镗刀刀头旋转一周,刀头在半径方向 上移动多少?镗孔直径变化多少?
第一节 工件在数控铣床/ 加工中心上的装夹
一、 工件的夹紧
1. 夹紧装置应具备的基本要求
(1) 夹紧过程可靠,不改变工件定位后所占据的正确位置。 (2) 夹紧力的大小适当,既要保证工件在加工过程中其位置 稳定不变, 振动小,又要使工件不会产生过大的夹紧变形。 (3) 操作简单、 方便、 省力、 安全。 (4) 结构性好, 夹紧装置的结构力求简单、 紧凑,以便于制 造和维修。
数控机床加工工艺第6章数控铣床加工工艺PPT课件
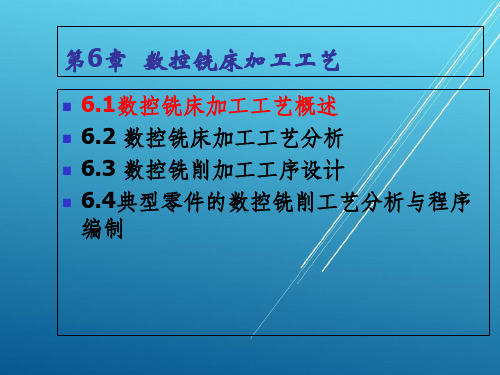
(2)零件尺寸所要求的加工精度、尺寸公差是否都可 以得到保证?
(3)内槽及缘板之间的内转接圆弧是否过小?
(4)零件铣削面的槽底圆角或腹板与缘板相交处的圆 角半径r是否太大?
(5)零件图中各加工面的凹圆弧(R与r)是否过于零乱, 是否可以统一?
(6)零件上有无统一基准以保证两次装夹加工后其相 对位置的正确性?
(3)零件铣槽底平面时,槽底圆角半径r不要
过大。 (4)应采用统一的基准定位。在有关的铣削件
的结构工艺性实例见表6-1。
(a) R较小
(b) R较大
图6-11 内槽结构工艺性对比
(a) r较小
(b) r较大
图6-12 零件槽底平面圆弧对铣削工艺的影响
3.零件毛坯的工艺性分析
(1)毛坯应有充分、稳定的加工余量。 经验表明,数控铣削中最难保证的是加工 面与非加工面之间的尺寸,在零件图样注 明的非加工面处也增加适当的余量。
(2)平面加工方法的选择 在数控铣床上加工平面主要采用端铣 刀和立铣刀加工。粗铣的尺寸精度和表面粗糙度一般可达
IT11~IT13,Ra6.3~25;精铣的尺寸精度和表面精糙度一 般可达IT8~IT10,Ra1.6~6.3。
(3)平面轮廓加工方法的选择通常采用3坐标数控铣床进行两轴 半坐标加工。
(4)固定斜角平面加工方法的选择 固定斜角平面是与水平成成 一固定夹角的斜面,常用的加工方法如下:
1.加工方法的选择
对于数控铣床,应重点考虑几个方面:能保证零件的加工精 度和表面粗糙度的要求;使走刀路线最短,既可简化程序段, 又可减少刀具空行程时间,提高加工效率;应使数值计算简 单,程序段数量少,以减少编程工作量。
(1)内孔表面加工方法的选择
在数控铣床上加工内孔表面加工方法主要有钻孔、扩孔、铰 孔、镗孔和攻丝等,应根据被加工孔的加工要求、尺寸、具 体生产条件、批量的大小及毛坯上有无预制孔等情况合理选 用。
6.数控铣削加工工艺

通常数控镗铣床和加工中心(MC,Machine Center)在结构、工艺和编程等方面有许多相似之处。
特别是全功能型数控镗铣床与加工中心相比,区别主要在于数控镗铣床没有自动刀具交换装置( ATC , Automatic Toos Changer )及刀具库,只能用手动方式换刀,而加工中心因具备ATC及刀具库,故可将使用的刀具预先安排存放于刀具库内,需要时再通过换刀指令,由ATC自动换刀。
数控镗铣床和加工中心都能够进行铣削、钻削、镗削及攻螺纹等加工。
数控镗铣、加工中心机床的类型立式龙门式卧式主要技术参数主要技术参数主要技术参数主要技术参数高速加工中心立式加工中心主要技术参数项目\型号VMC-850工作台面积1000x500 mm左右行程(X 轴) 800 mm前后行程(Y 轴) 500 mm上下行程(Z 轴) 610 mm主轴锥度BT-40CAT-40, HSK A63(选配)主轴转速60~8000 rpm7.5/5 kWX-Y-Z 快速进给30 / 30 / 20 m/min切削进给率1~12000 mm/min刀具选择模式双向任意式,最短距离选刀储刀数圆盘式24机械手式24/32 (选配)相邻刀最大刀具直径75 mm最大刀具直径100 mm最大刀具长度300 mm最大刀具重量10 kg工作台荷重600 kg机床净重5500 kg机床尺寸(LxWxH) 2350x3200x2698 mm数控镗铣、加工中心机床的类型卧式加工中心主要技术参数项目\型号VHMC-630工作台面积630 x 630 mm工作台最大负载1200 kgX 轴行程1000 mmY 轴行程800 mmZ 轴行程950 mm主轴锥度BT-50 / CAT-50主轴转速20~6000 rpmX-Y-Z 切削进给率1~12000 mm/minX-Y-Z 快速进给18 / 10 / 18 m/min储刀数60 (80, 120 选配)最大刀具直径x 长度Ø75 x 320最大刀具重量10 kg刀具选择模式双向任意式, 最短距离选刀换刀时间9 sec主轴电动机15 kW工作台旋转分度1°(0.001°选配)工作台数目 2 (6, 12 选配)交换时间(自动交换工作台) 15 sec机床尺寸(LxWxH) 5305x3200x3550 mm机床重量21000 kg数控镗铣、加工中心机床的类型龙门式加工中心主要技术参数项目/型号定柱式DMC-3000工作台尺寸3200x2200 mmX 轴行程3000 mmY 轴行程2650 mmZ 轴行程800 mm , 1066 mm 选配主轴锥度BT-50 / CAT-50主轴直径Ø90 mm主轴转速6000 rpm 自动高低档主轴马达26 / 22 kWX-Y-Z 快速进给12x 12x 10 m / minX-Y-Z 切削进给1-10000 mm / min自动换刀系统相邻刀最大刀具直径Ø135 mm储刀数40 刀(60,80,120 选配)最大直径Ø200 mm最大刀长350 mm最大刀重20 kg刀具选择模式双向任意,最短距离选刀工作台荷重6000 kg to 20000 kg机床尺寸(LxWxH)8870 x 5935 x4900机床重量58500 kg数控镗铣、加工中心机床的类型高速加工中心主要技术参数工作范围纵向长度:X400 mm横向长度:Y450 mm垂直高度:Z350 mm 工作主轴30'000 min-1S612.5 kWS110.0 kW 工作主轴42'000 min-1S613.0 kWS110.0 kW 工作主轴60'000 min-1S68.5 kWS1 6.5 kW 进给驱动进给速度X, Y, Z 40m/分加速度X, Y, Z17 m/秒²工作台工作台面积320 x 320工作台承重200 kg自动控制系统刀库位置18 -76机上激光对刀仪标准工件托盘转换装置位置7, 20, 48红外工件测头可选重量包括工件托盘交换装置6500 kg数控镗铣、加工中心机床的类型数控镗铣、加工中心的工艺特点三坐标数控镗铣床与加工中心的共同特点是除具有普通铣床的工艺性能外,还具有加工形状复杂的二维以至三维复杂轮廓的能力。
第6章数控铣削加工工艺

肋板高度与内孔转接圆 弧对零件铣削工艺性的影响
零件底面与肋板的转接圆弧对零 件铣削工艺性的影响
5.保证基准统一
最好采用统一基准定位,因此零件上应有合适的孔作 为定位基准孔,也可以专门设置工艺孔作为定位基准(如 在毛坯上增加工艺凸台或在后继工序要铣去的余量上设基 准孔)。若无法制出工艺孔,最起码也要用精加工表面作 为统一基准,以减少二次装夹产生的误差。
6.3.3 夹具的选择
1、夹具的要求
(1)为保持工件在本工序中所有需要完成的待加工面充分暴露在外,夹具要 做得尽可能开敞,因此夹紧机构元件与加工面之间应保持一定的安全距离,同时要 求夹紧机构元件能低则低,以防止夹具与铣床主轴套筒或刀套、刃具在加工过程中 发生碰撞。
(2)为保持零件安装方位与机床坐标系及编程坐标系方向的一致性,夹具应能 保证在机床上实现定向安装,还要求能协调零件定位面与机床之间保持一定的坐标 联系。
2.铣削外轮廓的进给路线
(1)铣削平面零件外轮廓时,一般采用立铣刀侧刃切削。刀具切入工件时,应 避免沿零件外轮廓的法向切入,而应沿切削起始点的延伸线逐渐切入工件,保证零 件曲线的平滑过渡。在切离工件时,也应避免在切削终点处直接抬刀,要沿着切削 终点延伸线逐渐切离工件。
(2)当用圆弧插补方式铣削外整圆时 要安排刀具从切向进入圆周铣削加工, 当整圆加工完毕后,不要在切点处直接退刀,而应让刀具沿切线方向多运动一段距 离,以免取消刀补时,刀具与工件表面相碰,造成工件报废。
6.2.2 数控机床铣削加工内容的选择
1.采用数控铣削加工内容 (1)工件上的曲线轮廓内、外形,特别是由数学表达式给出
的非圆曲线与列表曲线等曲线轮廓。 (2)已给出数学模型的空间曲线。 (3)形状复杂,尺寸繁多,划线与检测困难的部位。 (4)用通用铣床加工时难以观察、测量和控制进给的内、外
- 1、下载文档前请自行甄别文档内容的完整性,平台不提供额外的编辑、内容补充、找答案等附加服务。
- 2、"仅部分预览"的文档,不可在线预览部分如存在完整性等问题,可反馈申请退款(可完整预览的文档不适用该条件!)。
- 3、如文档侵犯您的权益,请联系客服反馈,我们会尽快为您处理(人工客服工作时间:9:00-18:30)。
夹具的刚性与稳定性要好。尽量不采用在加工过程中 更换夹紧点的设计,当的确需要在加工过程中更换夹紧
点时,要特别注意不能因更换夹紧点而破坏夹具或工件
定位精度。 2. 常用夹具种类 万能组合夹具——适用于小批量生产或研制时的中、 小型工件在数控铣床上进行铣加工。
专用铣切夹具——是特别为某一项或类似的几项工件
6.4 数控铣削加工程序编制
同数控车床一样,数控铣床的编程指令也随控制系统 辅助功能,还是符合ISO标准的。
的不同而不同,但一些常用的指令,如某些准备功能、 与数控车床编程功能相似,数控铣床的编程功能指令
也分为准备功能和辅助功能两大类。准备功能主要包 缩放和旋转加工、零点偏置等等;辅助功能主要指主 轴启停、换刀、冷却液开关等。
3.立卧两用数控铣床
由于这类铣床的主轴方向可以更换,能达 到在一台机床上既可以进行立式加工,又可以 进行卧式加工,同时具备上述两类机床的功能,
故其使用范围更广,功能更全,选择加工对象
的余地更大,且给用户带来不少方便。
二、数控铣床的特点
高柔性 多坐标联动
高适应性
高精度
大大减轻操作者的劳动强度
设计制造的夹具,一般在批量生产或研制时非要不可时 采用。
多工位夹具——可以同时装夹多个工件,可减少换刀 次数,也便于一面加工,一面装卸工件,较适宜于中批 量生产。
气动或液压夹具——适用于生产批量较大,采用其他
夹具又特别费工、费力的工件。但此类夹具结构较复杂,
造价往往较高,而且制造周期较长。
除上述几种夹具外,数控铣削加工中也经常采用虎钳、
刀具长度补偿指令 G43 、G44、 G49
用于补偿编程时假定的刀具与实际使用刀具之间的长度差。
1) G43——刀具长度正补偿指令;
2) G44——刀具长度负补偿指令; 3) G49——刀具长度补偿注销指令。 刀具长度补偿是在与插补平面相垂直的轴上进行的。 编程格式: G17 G43(G44) G01 Z__ H__; G18 G43(G44) G01 Y__ H__; G19 G43(G44) G01 X__ H__; G43、G44、G49为同组的模态代码。
2. 常用的铣刀种类 盘铣刀——一般采用在盘状刀体上机夹刀片或刀 头组成,常用于端铣较大的平面。 端铣刀——是数控铣加工中最常用的一种铣刀, 广泛用于加工平面类零件。
成型铣刀——一般都是为特定的工件或加工内容专门 设计制造的,适用于加工平面类零件的特定形状(如 角度面、凹槽面等),也适用于特形孔或台。下图所
第6章 数控铣床编程与加工
数控铣床概述 数控铣削加工工艺处理 数控铣削加工的刀具补偿
数控铣床的基本操作
数控铣床加工时的对刀
零件加工实例
6.1 数控铣床概述
一、数控铣床的类型
1. 立式数控铣床 立式数控铣床的主轴垂直于工作台所在的水平面, 最适合高度相对较小的零件。 2. 卧式数控铣床 与普通卧式铣床相同,卧式数控铣床主轴轴线平行 于水平面,可以实现在一次安装中,通过转盘改变工 位,进行“四面加工”。
应用广泛
高效率
半封闭或全封闭防护 主轴无级变速器且变速范围宽 采用手动换刀,刀具装夹方便
6.2 数控铣削加工工艺处理
一、数控铣床的加工对象
对工件进行钻、扩、铰、锪和镗孔加工与攻丝等, 但它主要还是被用来对工件进行铣削加工的。
所能加工的零件形式主要有:
• 平面类零件 • 曲面类(立体类)零件 • 孔类零件
二、零件图的工艺性分析 零件图中各加工面的凹圆弧半径(R与r)是否过于 零乱,是否可以统一。
零件所要求的加工精度、尺寸公差是否都可以得
到保证。
三、零件毛坯的工艺性分析
在对零件图进行工艺性分析后,还应结合数控铣削的
特点,对所用毛坯(常为板料、铸件自由锻及模锻件)进
行工艺性分析,否则,如果毛坯不适合数控铣削,加工 将很难进行下去;甚至会造成前功尽弃的后果。这方面 的教训在实际工作中也是不少见的,应引起充分重视。 根据经验,下列几方面应作为毛坯工艺性分析的要点:
示的是几种常用的成型铣刀。 球头铣刀——适用于加工空间曲面零件,有时也用于 平面类零件较大的转接凹圆弧的补加工。下图所示是一
种常见的球头铣刀。
三、数控铣床的夹具
1. 对夹具的基本要求
为保持零件安装方位与机床坐标系及编程坐标系方向一致, 夹具应能保证在机床上实现定向安装,还要求能协调零件定位 面与机床之间保持一定的坐标尺寸联系。 为保持工件在本工序中所有需要完成的待加工面充分暴露在 外,夹具要做得尽可能开敞,以防止夹具与铣床主轴套筒或刀 套、刃具在加工过程中发生碰撞。
毛坯的加工余量是否充分,批量生产时的毛坏余量是
否稳定。
分析毛坯在安装定位方面的适应性。
主要是考虑毛坯在加工时的安装定位方面的可靠 性与方便性,以便充分发挥数控铣削在一次安装中加 工出许多待加工面。
分析毛坯的余量大小及均匀性。
四、在确定走刀路线时,主要遵循以下原则: 应能保证零件的加工精度和表面粗糙度要求; 应使走刀路线最短,减少刀具空行程时间,提 高加工效率;
括快速定位、直线插补、圆弧插补、暂停、刀具补偿、
一、换刀与刀具管理
1. 选刀指令 T×× 或 T ×× ×× 2. 换刀动作指令M06 数控装置读入M06指令后,会自动送出并执行M05、 M09指令,即自动使主轴停转并关闭冷却液,然后 完成换刀动作。 例如: 标系设定指令
1.设置加工坐标系指令 G92 编程格式: G92 X__ Y__ Z__
G92指令是用刀具刀位点的初始位置与工件原点的 相对距离来间接地定义工件原点的。
如右图所示,工件坐标系设定指令为,
2、刀具半径补偿 G40 ,G41, G42
G41——刀具半径左补偿指令,简称左偏,按程序路径前进 方向刀具偏在零件左侧进给; G42——刀具半径右补偿指令,简称右偏,按程序路径前进 方向刀具偏在零件右侧进给; G40——取消刀具半径补偿指令,按程序路径进给。
分度头和三爪夹盘等通用夹具。
3. 数控铣床夹具的注意事项
选用时可参照下列原则:
安装零件时,应保证零件在本次定位装夹中所有
需要完成的待加工面充分暴露在外,以方便加工,
同时考虑机床主轴与工作台面之间的最小距离和
刀具的装夹长度,确保在主轴的行程范围内能使 零件的加工内容全部完成; 夹具在机床工作台上的安装位置必须给刀具运动 轨迹留有空间,不能和各工步刀具轨迹发生干涉。
应使数值计算简单,程序段数量少,以减少编
程工作量。
6.3 数控铣床的工艺装备
刀 柄 刀 具
夹 具
附 件
一、数控铣床的刀具
1. 对刀具的要求 刚性好 1) 为提高生产效率而采用大切削用量的需要; 2)为适应数控铣床加工过程中难以调整切削用量的特点。 耐用度高 尤其是当一把铣刀加工的内容很多时,如刀具不耐用 而磨损较快,就会影响工件的表面质量与加工精度,而 且会增加换刀引起的调刀与对刀次数,也会使工作表面 留下因对刀误差而形成的接刀台阶,降低了工件的表面 质量。