延迟焦化装置分馏塔腐蚀原因分析及改进措施_杨涛
延迟焦化装置的腐蚀原因分析与防护对策

延迟焦化装置的腐蚀原因分析与防护对策作者:李华来源:《中国科技博览》2014年第23期[摘要]大庆石化延迟焦化装置原料为常减压装置的减压渣油,大庆原油含硫量低,对装置的腐蚀很小,但运行四年后全面检测发现顶循泵出去口管线腐蚀严重。
现对其腐蚀原因进行分析,并提出防腐蚀危害的方案。
[关键词]延迟焦化;顶循线;水箱;腐蚀机理;对策中图分类号:TE986 文献标识码:A 文章编号:1009-914X(2014)23-0276-01一、装置简介120万吨/年延迟焦化装置于2008年8月建成投产。
本装置总体设计由洛阳石化工程公司承担,系统配套由大庆设计院设计,中油第一建设公司承担施工任务。
该装置主要由焦化、吹汽放空部分、水力除焦部分,切焦水闭路循环部分、冷焦水密闭处理部分、分馏部分、富气吸收稳定部分及干气液态烃脱硫部分组成,设计年开工时间为8000小时(连续运转),年加工量为120万吨,生焦周期为24小时。
该装置采用一炉两塔的工艺路线及可灵活调节循环比的工艺流程,装置设计循环比为0.5,以减压渣油、催化油浆、乙烯焦油为原料,主要产品为干气、液化石油气、汽油、柴油、轻蜡油、重蜡油和石油焦。
二、焦化系统的装置腐蚀情况分析1)腐蚀机理描述减压渣油及油浆混合后进入原料缓冲罐,经一系列换热后与焦化分馏塔底循环油混合,升温到335℃进入加热炉进料缓冲罐,然后进入加热炉F1101,加热到500℃左右进入焦炭塔(T1101A,B)底部。
原料进入加热炉前的设备主要采用16MnR材质,主要考虑高温硫腐蚀机理。
最后一组换热器采用了0Cr13复合板,较好地控制了高温硫腐蚀。
加热炉进/出口温度为335/500℃,炉管采用Cr9Mo材质,故炉管的腐蚀机理主要考虑炉管外的高温氧化和烟灰腐蚀,管内有高温硫腐蚀。
炉管在高温下材质劣化主要是内部结焦引起传热效率下降,使壁温升高导致材料蠕变和氧化破坏。
焦炭塔采用15CrMo材质,存在高温硫腐蚀机理。
延迟焦化装置腐蚀原因分析与对策
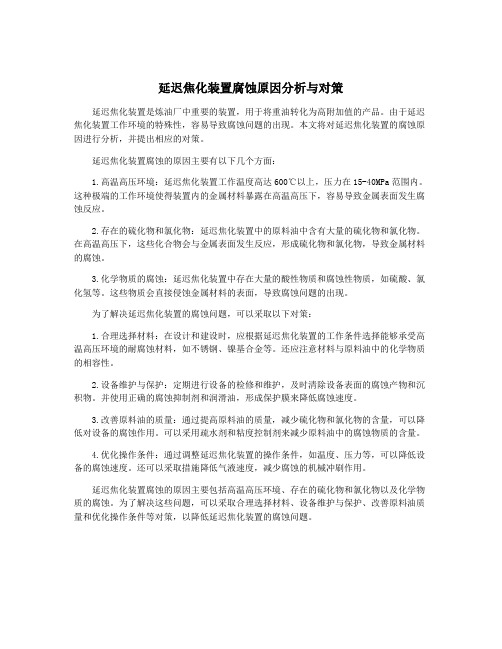
延迟焦化装置腐蚀原因分析与对策延迟焦化装置是炼油厂中重要的装置,用于将重油转化为高附加值的产品。
由于延迟焦化装置工作环境的特殊性,容易导致腐蚀问题的出现。
本文将对延迟焦化装置的腐蚀原因进行分析,并提出相应的对策。
延迟焦化装置腐蚀的原因主要有以下几个方面:1.高温高压环境:延迟焦化装置工作温度高达600℃以上,压力在15-40MPa范围内。
这种极端的工作环境使得装置内的金属材料暴露在高温高压下,容易导致金属表面发生腐蚀反应。
2.存在的硫化物和氯化物:延迟焦化装置中的原料油中含有大量的硫化物和氯化物。
在高温高压下,这些化合物会与金属表面发生反应,形成硫化物和氯化物,导致金属材料的腐蚀。
3.化学物质的腐蚀:延迟焦化装置中存在大量的酸性物质和腐蚀性物质,如硫酸、氯化氢等。
这些物质会直接侵蚀金属材料的表面,导致腐蚀问题的出现。
为了解决延迟焦化装置的腐蚀问题,可以采取以下对策:1.合理选择材料:在设计和建设时,应根据延迟焦化装置的工作条件选择能够承受高温高压环境的耐腐蚀材料,如不锈钢、镍基合金等。
还应注意材料与原料油中的化学物质的相容性。
2.设备维护与保护:定期进行设备的检修和维护,及时清除设备表面的腐蚀产物和沉积物。
并使用正确的腐蚀抑制剂和润滑油,形成保护膜来降低腐蚀速度。
3.改善原料油的质量:通过提高原料油的质量,减少硫化物和氯化物的含量,可以降低对设备的腐蚀作用。
可以采用疏水剂和粘度控制剂来减少原料油中的腐蚀物质的含量。
4.优化操作条件:通过调整延迟焦化装置的操作条件,如温度、压力等,可以降低设备的腐蚀速度。
还可以采取措施降低气液速度,减少腐蚀的机械冲刷作用。
延迟焦化装置腐蚀的原因主要包括高温高压环境、存在的硫化物和氯化物以及化学物质的腐蚀。
为了解决这些问题,可以采取合理选择材料、设备维护与保护、改善原料油质量和优化操作条件等对策,以降低延迟焦化装置的腐蚀问题。
延迟焦化装置腐蚀原因分析与对策
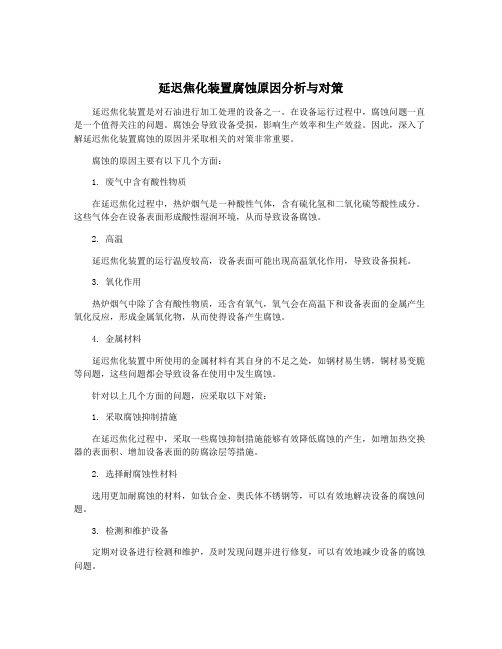
延迟焦化装置腐蚀原因分析与对策延迟焦化装置是对石油进行加工处理的设备之一。
在设备运行过程中,腐蚀问题一直是一个值得关注的问题。
腐蚀会导致设备受损,影响生产效率和生产效益。
因此,深入了解延迟焦化装置腐蚀的原因并采取相关的对策非常重要。
腐蚀的原因主要有以下几个方面:1. 废气中含有酸性物质在延迟焦化过程中,热炉烟气是一种酸性气体,含有硫化氢和二氧化硫等酸性成分。
这些气体会在设备表面形成酸性湿润环境,从而导致设备腐蚀。
2. 高温延迟焦化装置的运行温度较高,设备表面可能出现高温氧化作用,导致设备损耗。
3. 氧化作用热炉烟气中除了含有酸性物质,还含有氧气,氧气会在高温下和设备表面的金属产生氧化反应,形成金属氧化物,从而使得设备产生腐蚀。
4. 金属材料延迟焦化装置中所使用的金属材料有其自身的不足之处,如钢材易生锈,铜材易变脆等问题,这些问题都会导致设备在使用中发生腐蚀。
针对以上几个方面的问题,应采取以下对策:1. 采取腐蚀抑制措施在延迟焦化过程中,采取一些腐蚀抑制措施能够有效降低腐蚀的产生,如增加热交换器的表面积、增加设备表面的防腐涂层等措施。
2. 选择耐腐蚀性材料选用更加耐腐蚀的材料,如钛合金、奥氏体不锈钢等,可以有效地解决设备的腐蚀问题。
3. 检测和维护设备定期对设备进行检测和维护,及时发现问题并进行修复,可以有效地减少设备的腐蚀问题。
4. 设备运行条件控制控制设备运行环境,注意环境湿度、温度等因素,可以有效地减小设备的腐蚀情况。
综上所述,延迟焦化装置腐蚀问题是一个需要注意的问题,应该采取相应措施来预防和消除腐蚀现象。
通过不断地加强设备的维护和保护,可以提高设备的使用寿命,保证生产效率和经济效益。
延迟焦化装置腐蚀原因分析与对策
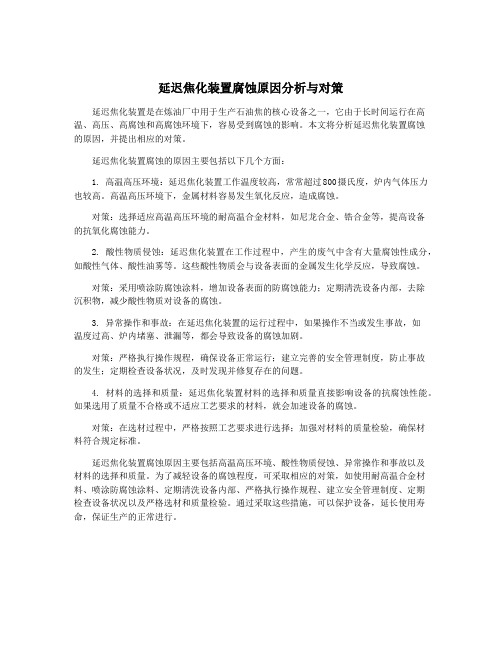
延迟焦化装置腐蚀原因分析与对策延迟焦化装置是在炼油厂中用于生产石油焦的核心设备之一,它由于长时间运行在高温、高压、高腐蚀和高腐蚀环境下,容易受到腐蚀的影响。
本文将分析延迟焦化装置腐蚀的原因,并提出相应的对策。
延迟焦化装置腐蚀的原因主要包括以下几个方面:1. 高温高压环境:延迟焦化装置工作温度较高,常常超过800摄氏度,炉内气体压力也较高。
高温高压环境下,金属材料容易发生氧化反应,造成腐蚀。
对策:选择适应高温高压环境的耐高温合金材料,如尼龙合金、锆合金等,提高设备的抗氧化腐蚀能力。
2. 酸性物质侵蚀:延迟焦化装置在工作过程中,产生的废气中含有大量腐蚀性成分,如酸性气体、酸性油雾等。
这些酸性物质会与设备表面的金属发生化学反应,导致腐蚀。
对策:采用喷涂防腐蚀涂料,增加设备表面的防腐蚀能力;定期清洗设备内部,去除沉积物,减少酸性物质对设备的腐蚀。
3. 异常操作和事故:在延迟焦化装置的运行过程中,如果操作不当或发生事故,如温度过高、炉内堵塞、泄漏等,都会导致设备的腐蚀加剧。
对策:严格执行操作规程,确保设备正常运行;建立完善的安全管理制度,防止事故的发生;定期检查设备状况,及时发现并修复存在的问题。
4. 材料的选择和质量:延迟焦化装置材料的选择和质量直接影响设备的抗腐蚀性能。
如果选用了质量不合格或不适应工艺要求的材料,就会加速设备的腐蚀。
对策:在选材过程中,严格按照工艺要求进行选择;加强对材料的质量检验,确保材料符合规定标准。
延迟焦化装置腐蚀原因主要包括高温高压环境、酸性物质侵蚀、异常操作和事故以及材料的选择和质量。
为了减轻设备的腐蚀程度,可采取相应的对策,如使用耐高温合金材料、喷涂防腐蚀涂料、定期清洗设备内部、严格执行操作规程、建立安全管理制度、定期检查设备状况以及严格选材和质量检验。
通过采取这些措施,可以保护设备,延长使用寿命,保证生产的正常进行。
延迟焦化装置分馏塔底结焦原因分析及优化
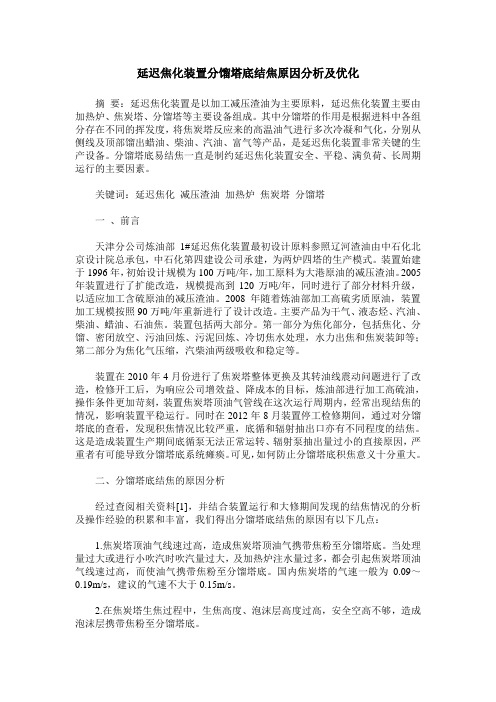
延迟焦化装置分馏塔底结焦原因分析及优化摘要:延迟焦化装置是以加工减压渣油为主要原料,延迟焦化装置主要由加热炉、焦炭塔、分馏塔等主要设备组成。
其中分馏塔的作用是根据进料中各组分存在不同的挥发度,将焦炭塔反应来的高温油气进行多次冷凝和气化,分别从侧线及顶部馏出蜡油、柴油、汽油、富气等产品,是延迟焦化装置非常关键的生产设备。
分馏塔底易结焦一直是制约延迟焦化装置安全、平稳、满负荷、长周期运行的主要因素。
关键词:延迟焦化减压渣油加热炉焦炭塔分馏塔一、前言天津分公司炼油部1#延迟焦化装置最初设计原料参照辽河渣油由中石化北京设计院总承包,中石化第四建设公司承建,为两炉四塔的生产模式。
装置始建于1996年,初始设计规模为100万吨/年,加工原料为大港原油的减压渣油。
2005年装置进行了扩能改造,规模提高到120万吨/年,同时进行了部分材料升级,以适应加工含硫原油的减压渣油。
2008年随着炼油部加工高硫劣质原油,装置加工规模按照90万吨/年重新进行了设计改造。
主要产品为干气、液态烃、汽油、柴油、蜡油、石油焦。
装置包括两大部分。
第一部分为焦化部分,包括焦化、分馏、密闭放空、污油回炼、污泥回炼、冷切焦水处理,水力出焦和焦炭装卸等;第二部分为焦化气压缩,汽柴油两级吸收和稳定等。
装置在2010年4月份进行了焦炭塔整体更换及其转油线震动问题进行了改造,检修开工后,为响应公司增效益、降成本的目标,炼油部进行加工高硫油,操作条件更加苛刻,装置焦炭塔顶油气管线在这次运行周期内,经常出现结焦的情况,影响装置平稳运行。
同时在2012年8月装置停工检修期间,通过对分馏塔底的查看,发现积焦情况比较严重,底循和辐射抽出口亦有不同程度的结焦。
这是造成装置生产期间底循泵无法正常运转、辐射泵抽出量过小的直接原因,严重者有可能导致分馏塔底系统瘫痪。
可见,如何防止分馏塔底积焦意义十分重大。
二、分馏塔底结焦的原因分析经过查阅相关资料[1],并结合装置运行和大修期间发现的结焦情况的分析及操作经验的积累和丰富,我们得出分馏塔底结焦的原因有以下几点:1.焦炭塔顶油气线速过高,造成焦炭塔顶油气携带焦粉至分馏塔底。
延迟焦化装置腐蚀原因分析与对策

延迟焦化装置腐蚀原因分析与对策延迟焦化装置是炼油工业中常用的设备之一,用于将重质石油切割成较轻的石油产品。
在延迟焦化装置运行的过程中,腐蚀问题是一个常见的技术难题。
本文将对延迟焦化装置腐蚀原因进行分析,并提出相应的对策。
1. 高温环境:延迟焦化装置中气体和液体都处于高温环境下,高温容易促进腐蚀反应的进行。
高温环境还会使金属材料的蠕变和应力腐蚀开裂等问题加剧。
对策:选择耐高温的材料和涂层,如镍基合金、不锈钢等,可以有效降低高温环境下的腐蚀问题。
通过冷却系统和隔热措施,降低设备温度,也可以减缓腐蚀速度。
2. 高温下的硫化物腐蚀:在延迟焦化装置中,存在一些含硫化物的物质,如硫化氢、硫酸和含硫油品等,它们会与金属表面反应,生成黄铜、黄铜绿等腐蚀产物。
对策:加强硫化物的监测和控制,确保含硫物质的浓度在安全范围内。
加装除硫装置、增加碱洗灰灰塔等处理设备,可以有效减少硫化物对设备的腐蚀。
3. 延迟焦化装置中的酸性物质:延迟焦化装置中经常使用一些酸性物质,如稀盐酸、硝酸等,这些物质会对设备表面产生腐蚀作用。
对策:采用酸性物质的替代品,选择性能更好的缓蚀剂,加强设备的保护涂层等,可以减轻酸性物质对设备的腐蚀。
4. 介质中的悬浮颗粒物:延迟焦化装置中运行的介质中往往含有固体颗粒,这些颗粒物会磨损金属表面,加速腐蚀作用的进行。
对策:在介质中加入过滤装置,减少悬浮颗粒物的含量;采用耐磨材料和涂层,增加金属表面的耐磨性。
延迟焦化装置腐蚀的原因主要包括高温环境、高温下的硫化物腐蚀、酸性物质的腐蚀和介质中的悬浮颗粒物等。
针对这些原因,可采取的对策包括选择耐高温材料和涂层、控制硫化物浓度、加装除硫装置、减少酸性物质的使用、加强设备保护涂层、过滤介质中的悬浮颗粒物等。
通过合理的措施和对策,能够降低延迟焦化装置的腐蚀问题,延长设备寿命,提高生产效益。
焦炭塔切换后分馏系统操作优化(杨涛)
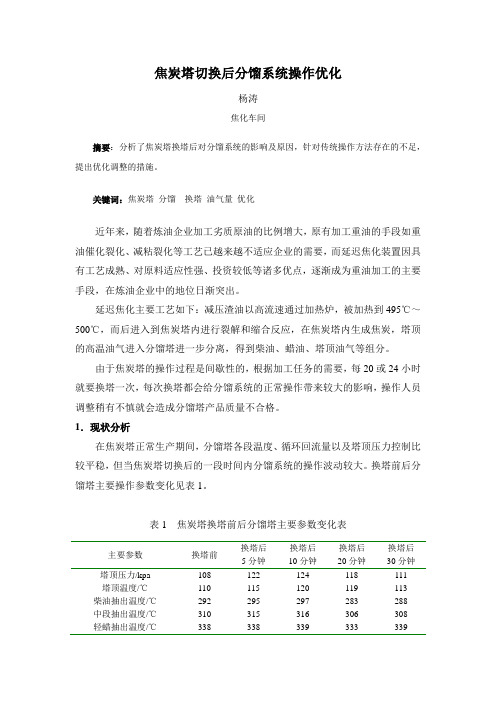
焦炭塔切换后分馏系统操作优化杨涛焦化车间摘要:分析了焦炭塔换塔后对分馏系统的影响及原因,针对传统操作方法存在的不足,提出优化调整的措施。
关键词:焦炭塔分馏换塔油气量优化近年来,随着炼油企业加工劣质原油的比例增大,原有加工重油的手段如重油催化裂化、减粘裂化等工艺已越来越不适应企业的需要,而延迟焦化装置因具有工艺成熟、对原料适应性强、投资较低等诸多优点,逐渐成为重油加工的主要手段,在炼油企业中的地位日渐突出。
延迟焦化主要工艺如下:减压渣油以高流速通过加热炉,被加热到495℃~500℃,而后进入到焦炭塔内进行裂解和缩合反应,在焦炭塔内生成焦炭,塔顶的高温油气进入分馏塔进一步分离,得到柴油、蜡油、塔顶油气等组分。
由于焦炭塔的操作过程是间歇性的,根据加工任务的需要,每20或24小时就要换塔一次,每次换塔都会给分馏系统的正常操作带来较大的影响,操作人员调整稍有不慎就会造成分馏塔产品质量不合格。
1.现状分析在焦炭塔正常生产期间,分馏塔各段温度、循环回流量以及塔顶压力控制比较平稳,但当焦炭塔切换后的一段时间内分馏系统的操作波动较大。
换塔前后分馏塔主要操作参数变化见表1。
表1 焦炭塔换塔前后分馏塔主要参数变化表主要参数换塔前换塔后5分钟换塔后10分钟换塔后20分钟换塔后30分钟塔顶压力/kpa 108 122 124 118 111 塔顶温度/℃110 115 120 119 113 柴油抽出温度/℃292 295 297 283 288 中段抽出温度/℃310 315 316 306 308 轻蜡抽出温度/℃338 338 339 333 339重蜡抽出温度/℃363 361 363 360 363蒸发段温度/℃384 378 370 375 384 反应油气入塔温度/℃408 379 370 381 386顶循上返塔流量(阀位)/% 47 47 48 50 47顶循下返塔流量/t·h-123 23 23 23 23柴油上返塔流量/t·h-162 62 62 62 62柴油下返流量塔/t·h-10 0 0 0 0中段上返塔流量/t·h-1111 111 111 111 111重蜡上返流量塔/t·h-112 12 12 12 12重蜡下返塔流量/t·h-19 9 9 9 9循环油上返塔(阀位)/% 48 46 40 32 30塔顶富气量/Nm3·h-111000 12000 9950 10600 109002焦炭塔切换对分馏系统的影响及原因2.1焦炭塔切换对分馏系统的影响从表1可以看出,焦炭塔切换后,进入分馏塔底油气温度由408℃降至378℃,油气量也有所降低。
延迟焦化装置腐蚀原因分析与对策
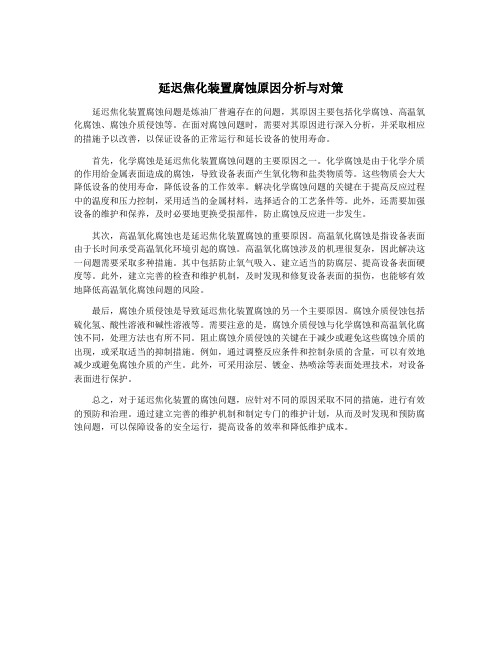
延迟焦化装置腐蚀原因分析与对策延迟焦化装置腐蚀问题是炼油厂普遍存在的问题,其原因主要包括化学腐蚀、高温氧化腐蚀、腐蚀介质侵蚀等。
在面对腐蚀问题时,需要对其原因进行深入分析,并采取相应的措施予以改善,以保证设备的正常运行和延长设备的使用寿命。
首先,化学腐蚀是延迟焦化装置腐蚀问题的主要原因之一。
化学腐蚀是由于化学介质的作用给金属表面造成的腐蚀,导致设备表面产生氧化物和盐类物质等。
这些物质会大大降低设备的使用寿命,降低设备的工作效率。
解决化学腐蚀问题的关键在于提高反应过程中的温度和压力控制,采用适当的金属材料,选择适合的工艺条件等。
此外,还需要加强设备的维护和保养,及时必要地更换受损部件,防止腐蚀反应进一步发生。
其次,高温氧化腐蚀也是延迟焦化装置腐蚀的重要原因。
高温氧化腐蚀是指设备表面由于长时间承受高温氧化环境引起的腐蚀。
高温氧化腐蚀涉及的机理很复杂,因此解决这一问题需要采取多种措施。
其中包括防止氧气吸入、建立适当的防腐层、提高设备表面硬度等。
此外,建立完善的检查和维护机制,及时发现和修复设备表面的损伤,也能够有效地降低高温氧化腐蚀问题的风险。
最后,腐蚀介质侵蚀是导致延迟焦化装置腐蚀的另一个主要原因。
腐蚀介质侵蚀包括硫化氢、酸性溶液和碱性溶液等。
需要注意的是,腐蚀介质侵蚀与化学腐蚀和高温氧化腐蚀不同,处理方法也有所不同。
阻止腐蚀介质侵蚀的关键在于减少或避免这些腐蚀介质的出现,或采取适当的抑制措施。
例如,通过调整反应条件和控制杂质的含量,可以有效地减少或避免腐蚀介质的产生。
此外,可采用涂层、镀金、热喷涂等表面处理技术,对设备表面进行保护。
总之,对于延迟焦化装置的腐蚀问题,应针对不同的原因采取不同的措施,进行有效的预防和治理。
通过建立完善的维护机制和制定专门的维护计划,从而及时发现和预防腐蚀问题,可以保障设备的安全运行,提高设备的效率和降低维护成本。
- 1、下载文档前请自行甄别文档内容的完整性,平台不提供额外的编辑、内容补充、找答案等附加服务。
- 2、"仅部分预览"的文档,不可在线预览部分如存在完整性等问题,可反馈申请退款(可完整预览的文档不适用该条件!)。
- 3、如文档侵犯您的权益,请联系客服反馈,我们会尽快为您处理(人工客服工作时间:9:00-18:30)。
石 油 炼 制 与 化 工2013年3月 收稿日期:2012-06-19;修改稿收到日期:2012-10-21。
作者简介:杨涛,技师,从事生产管理工作。
通讯联系人:孙艳朋,E-mail:sypai62@126.com。
延迟焦化装置分馏塔腐蚀原因分析及改进措施杨 涛,孙艳朋,翟志清,程前进(中国石化洛阳分公司,河南洛阳471012)摘 要:对中国石化洛阳分公司延迟焦化装置在检修期间发现的分馏塔顶部塔盘存在不同程度的腐蚀问题进行分析,认为造成分馏塔顶部塔盘腐蚀的主要原因为焦化原料和回炼重污油的盐含量高、分馏塔水洗操作不当。
结合装置的原料性质、操作参数及设备条件,采取加强原料盐含量监控、改善分馏塔上部热量分布、增设分馏塔顶部水洗专用线、优化分馏塔侧向回流等一系列改进措施,改善了分馏塔的结盐现象,为保证装置的长周期运行奠定了基础。
关键词:延迟焦化分馏塔 腐蚀 水洗中国石化洛阳分公司(以下简称洛阳分公司)1.40Mt?a延迟焦化装置在平稳运行38个月后于2011年9月1日进行首次停工检修。
检修期间发现分馏塔第3~11层塔盘出现明显的腐蚀减薄现象,而第4~7层塔盘的腐蚀减薄现象尤为严重。
为确保下一周期的安全平稳运行,在决定更换第3~11层塔盘的同时,认真分析腐蚀减薄现象产生的原因,提出一系列改进措施和建议,最大程度地减缓了生产期间塔盘的腐蚀速率,保证装置长周期运行。
本文主要介绍延迟焦化装置分馏塔腐蚀原因及改进措施。
1 装置腐蚀状况及原因分析1.1 塔盘腐蚀状况分馏塔第1、2层塔盘基体平整,有少量浮阀脱落;第3层塔盘约有1?3的浮阀脱落;第4层塔盘基体蚀坑连片,坑深约1~3mm;第5~7层塔盘和浮阀腐蚀减薄严重,局部腐蚀穿孔,且有大量浮阀脱落;第8~9层塔盘腐蚀减轻,但有大量黑色垢物堆积,浮阀基本已失去弹性。
利用扫描电子显微镜能谱仪(EDX)对第8层塔盘堆积的垢蚀物进行元素分析,结果见表1。
从表1可以看出,垢蚀物中以Fe,S,Cr,O等元素为主(约占94.7%),其中Fe和Cr为塔盘材质元素,S和O为腐蚀产物元素。
为进一步确定腐蚀产物的物相组成,利用X射线衍射仪对腐蚀产物进行表征,确定腐蚀产物以铁的硫化物为主,其物相组成为:Fe7S8,53.8%;Fe3S4,26.6%;Fe0.95S1.05,12.8%;FeS2,6.8%。
表分馏塔第层塔盘垢蚀物元素分析结果1.2 腐蚀原因分析1.2.1 结盐水洗低温H2S-HCl-NH3-H2O腐蚀 装置开工运行至2011年,各设备工况进入平稳运行期,为减轻油品罐区罐容压力,焦化装置开始回炼重污油,在1月、3月、5月、6月4个月共回炼重污油3 335t,其中1月份最多,达到1 158t;5月份最少,为528t。
重污油回炼期间,罐区送污油进入焦化装置重污油罐,再由污油泵送入焦炭塔顶作为急冷油回炼。
由于这部分污油的来源、成分复杂,且含水、含盐较多,含水多时易导致焦炭塔压力大幅波动,故必须停止回炼进行反复脱水;盐含量较高对装置造成的影响是非常显著的,高盐含量减压渣油和重污油以急冷油方式进入焦炭塔,氯离子与焦炭塔塔顶油气一起被携带进入焦化分馏塔,在分馏塔顶部与高温油气中的氮化物反应生成NH4C1,最终在分馏塔塔顶低温区结晶析出,造成石 油 炼 制 与 化 工 2013年第44卷降液槽、抽出管线、机泵入口滤网、机械密封波纹管等堵塞。
重污油盐、水含量和常压二脱原油的盐含量分析数据分别见表2和表3。
从表2和表3可以看出,重污油、常压二脱原油的盐含量严重超标,导致进焦化装置原料(减压渣油)的盐含量也严重超标。
表2 重污油的盐、水含量项 目数 据标 准密度(20℃)?(kg·m-3)897.6GB?T 1884—1885w(水),%>10.0GB?T 8929ρ(盐)?(mg·L-1)368.4ZBE 21001表3 常压二脱原油盐含量采样日期ρ(盐)?(mg·L-1)2011-03-13 4.382011-03-12 4.892011-03-11 8.542011-03-10 3.762011-03-09 8.542011-03-08 6.102011-03-07 3.722011-03-06 4.112011-03-05 3.482011-03-04 3.932011-03-03 4.45 注:标准规定原油中盐的质量浓度不大于3.0mg?L。
NH4Cl会对塔盘造成严重的垢下腐蚀及磨损腐蚀[1]。
从操作表象看:首先是顶循环泵机械密封泄漏频次逐渐加快,维修频次愈来愈高,严重时每周更换1套机械密封(每套密封造价在5 000元左右),设备检修费用大幅上升;其次是顶循环流量逐渐减小,为了降低顶循环泵机械密封更换频率,对分馏塔塔顶循环泵入口管线进行在线优化改进,利用顶循环泵入口排凝线(DN20管线)与除盐水线连接改成水洗线(如图1所示)。
当发现顶循环泵机械密封泄漏时,及时打开入口DN20水洗阀,以3t?h的水量进行水洗,除盐水从入口通过机泵泵体时能溶解去除机械密封波纹管内附着的铵盐,一般清洗40min左右就能恢复密封性能,使波纹管恢复弹性后压紧密封面,消除泄漏,从而大大降低了机械密封的维护费用。
然而,由于频繁地进行水洗操作,导致分馏塔顶部塔盘温度经常低于露点温度而出现液态水,这为低温H2S-HCl-NH3-H2O型腐蚀的发生创造了条件,也因此加剧了顶部塔盘的腐蚀程度[2-3]。
图1 分馏塔塔顶循环泵入口除盐水水洗线1.2.2 结盐磨损腐蚀 由于进料盐含量以及污油回炼量愈大,分馏塔塔顶系统积聚的盐类愈多,相应水洗的次数也增多。
当除盐水进入系统之后,水将顶循环系统析出的铵盐溶解成细小的盐粒留在系统内循环,盐粒随塔顶循环汽油被不断地抽出,经过顶循环泵升压后返回塔内。
由于塔顶循环回流自上而下的洗涤、分馏作用,盐颗粒对塔盘上面的磨损始终存在,当与自下而上的塔内油气逆向接触时,又对塔盘造成自下而上的磨损[4]。
2011年3—8月,顶循环泵机械密封频繁泄漏,最严重时造成机泵入口过滤网筒体(DN200、材质为0Cr13)腐蚀并消失,只剩下滤网两头的加强圈,叶轮腐蚀减薄严重。
并且在检修机泵的过程中,检修人员曾经有2次在泵体内发现脱落的塔盘构件,从外形推测认为是分馏塔塔盘脱落的浮阀。
由于顶循环的下回流返回至分馏塔塔顶循环集油箱下第4层塔盘,当装置顶循环量达到设计加工进料166t?h时,顶循环上、下回流分配量一般在4∶1左右,也就是顶循环回流量在120t?h左右,下回流一般维持在30t?h左右,第4~10层塔盘只有30t?h的液相回流,这7层塔盘间的液相流量远远小于气相流量,气相线速在这几层塔盘之间会明显增大,当顶循环汽油中夹带的盐颗粒与油气逆向接触时对塔盘下面的冲刷磨损成倍增加。
第11层塔盘有流量30t?h、温度40℃的再吸收塔富吸收油返塔,再向下到第13层塔盘有100t?h左右、温度120℃的柴油上回流返塔,第10~14层塔盘的液相洗涤分馏作用逐渐增强,顶循环油越向下气相温度越高,盐颗粒逐渐被高温溶解成极小的分子状态,越向下磨损现象越弱,直至消失,这是第11层以下塔盘腐蚀较轻的原因之一。
1.2.3 高线速冲刷磨损 在分馏塔各个塔盘之间气液相达到平衡时,上升的油气线速是一定的。
67第3期杨 涛,等.延迟焦化装置分馏塔腐蚀原因分析及改进措施但是如果某一段塔盘注入的液相回流过小,那么在短时间内该段塔盘液相的气化量会迅速增加,所以相比于其它段塔盘,这一段塔盘的气相线速一定是过高的,过高的线速冲刷很容易破坏金属表面形成的保护膜。
由于顶循环的下回流注入流量只有20~30t?h,分馏塔第4~10层塔盘区间的油气线速过高,会将活性硫对塔盘腐蚀形成的硫化铁膜吹掉,不断更新腐蚀界面,腐蚀也就不断进行,造成第4~7层塔盘的浮阀减薄并脱落,塔盘也减薄、穿孔,严重时造成塔盘塌落。
2 分馏塔塔盘防腐蚀改进措施通过对焦化装置分馏塔第4~7层塔盘严重腐蚀现象及腐蚀物的成分进行分析,认为水洗操作是造成分馏塔顶部塔盘腐蚀的主要原因。
为了在以后的生产中能够有效地避免塔盘腐蚀现象的发生,针对分馏塔曾出现的以H2S-HCl-NH3-H2O型和盐粒磨损为主的两种类型腐蚀,采取了一系列的改进措施。
2.1 加强原料盐含量监控为了降低焦化原料中的杂质含量,应加强常减压电脱盐装置对原油二级脱盐的效果,以保证减压渣油中的盐含量在指标要求之内。
油品罐区重污油回炼时,要求罐区必须出具水含量不大于10%的化验分析单,同时要求罐区加强脱水工作。
每次送油之前,要到罐区现场确认脱水效果,直至脱水合格方可进行重污油回炼。
通过加强电脱盐和污油脱水,降低焦化装置原料中的盐含量和水含量,改善了焦化原料性质,有效地减少了分馏塔顶部出现H2S-HCl-NH3-H2O腐蚀的几率。
2.2 改善分馏塔上部热量分布2011年10月装置大检修之后进入正常生产阶段,控制分馏塔塔顶温度在125~130℃范围内,将分馏塔塔顶温度控制的下限指标提高15℃,尽量避免分馏塔内的铵盐在塔顶塔盘结晶析出,将铵盐结晶区域向塔顶后部转移,最大限度地避免分馏塔顶部在线水洗次数,避免分馏塔顶部出现液态水造成的塔盘露点H2S-HCl-NH3-H2O腐蚀和盐颗粒的磨损腐蚀。
2.3 增设分馏塔顶部水洗专用线在分馏塔塔顶空气冷却器入口阀后的吹扫蒸汽管线上增加DN50除盐水线,用于在线水洗空气冷却器管束内析出的铵盐盐垢。
分馏塔水洗流程示意见图2。
如果空气冷却器管束出现铵盐结晶,塔顶油气经过空气冷却器的流通面积会减小,塔顶压力逐渐升高而气压机入口压力会逐渐降低,塔顶油气通过空气冷却器时就会受阻,应根据压力变化及时对空气冷却器进行分批水洗。
根据生产需要将1~3台空气冷却器同时进行水洗。
2012年4月16日,装置运行6个月之后进行了一次分馏塔空气冷却器的成功水洗,该过程未对装置生产造成任何不良影响。
图2 分馏塔水洗流程示意当分馏塔上部塔盘结盐之后,可以通过塔顶循环的上回流返塔调节阀阀后的第二条水洗线进行水洗,塔盘洗掉的铵盐落入顶循环集油箱,通过塔顶循环泵入口DN80排凝阀前的排污油线送入含硫污水罐进行油水分离,再送出装置,不再将铵盐压到柴油系统,有效地降低了分馏塔塔盘的腐蚀速率,并且避免柴油系统出现铵盐结垢问题。
通过上述水洗流程的优化改造,最大程度地减少了焦化分馏塔在水洗过程中出现的液态水量,降低了H2S-HCl-NH3-H2O类型腐蚀的程度,延长了分馏塔上部塔盘的运行周期。
2.4 优化分馏塔侧向回流针对焦化分馏塔第4~10层塔盘气液两相始终存在不平衡性的特点,规定塔顶循环的下回流流量下限不小于35t?h,上返塔流量保持在100t?h左右,装置低负荷生产时,逐步提高塔顶循环返塔温度至100℃左右,确保塔顶循环的上返塔流量。