焦化分馏塔上部取热流程比较
焦化反应分馏部分工艺流程说明
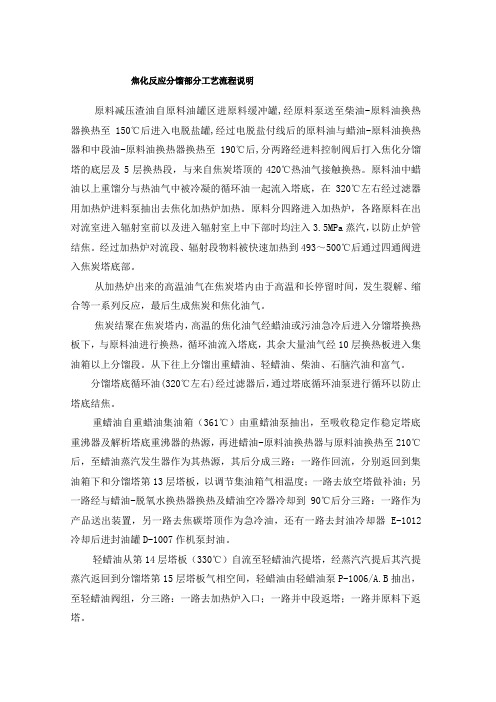
焦化反应分馏部分工艺流程说明原料减压渣油自原料油罐区进原料缓冲罐,经原料泵送至柴油-原料油换热器换热至150℃后进入电脱盐罐,经过电脱盐付线后的原料油与蜡油-原料油换热器和中段油-原料油换热器换热至190℃后,分两路经进料控制阀后打入焦化分馏塔的底层及5层换热段,与来自焦炭塔顶的420℃热油气接触换热。
原料油中蜡油以上重馏分与热油气中被冷凝的循环油一起流入塔底,在320℃左右经过滤器用加热炉进料泵抽出去焦化加热炉加热。
原料分四路进入加热炉,各路原料在出对流室进入辐射室前以及进入辐射室上中下部时均注入3.5MPa蒸汽,以防止炉管结焦。
经过加热炉对流段、辐射段物料被快速加热到493~500℃后通过四通阀进入焦炭塔底部。
从加热炉出来的高温油气在焦炭塔内由于高温和长停留时间,发生裂解、缩合等一系列反应,最后生成焦炭和焦化油气。
焦炭结聚在焦炭塔内,高温的焦化油气经蜡油或污油急冷后进入分馏塔换热板下,与原料油进行换热,循环油流入塔底,其余大量油气经10层换热板进入集油箱以上分馏段。
从下往上分馏出重蜡油、轻蜡油、柴油、石脑汽油和富气。
分馏塔底循环油(320℃左右)经过滤器后,通过塔底循环油泵进行循环以防止塔底结焦。
重蜡油自重蜡油集油箱(361℃)由重蜡油泵抽出,至吸收稳定作稳定塔底重沸器及解析塔底重沸器的热源,再进蜡油-原料油换热器与原料油换热至210℃后,至蜡油蒸汽发生器作为其热源,其后分成三路:一路作回流,分别返回到集油箱下和分馏塔第13层塔板,以调节集油箱气相温度;一路去放空塔做补油;另一路经与蜡油-脱氧水换热器换热及蜡油空冷器冷却到90℃后分三路:一路作为产品送出装置,另一路去焦碳塔顶作为急冷油,还有一路去封油冷却器E-1012冷却后进封油罐D-1007作机泵封油。
轻蜡油从第14层塔板(330℃)自流至轻蜡油汽提塔,经蒸汽汽提后其汽提蒸汽返回到分馏塔第15层塔板气相空间,轻蜡油由轻蜡油泵P-1006/A.B抽出,至轻蜡油阀组,分三路:一路去加热炉入口;一路并中段返塔;一路并原料下返塔。
分馏操作规程及流程
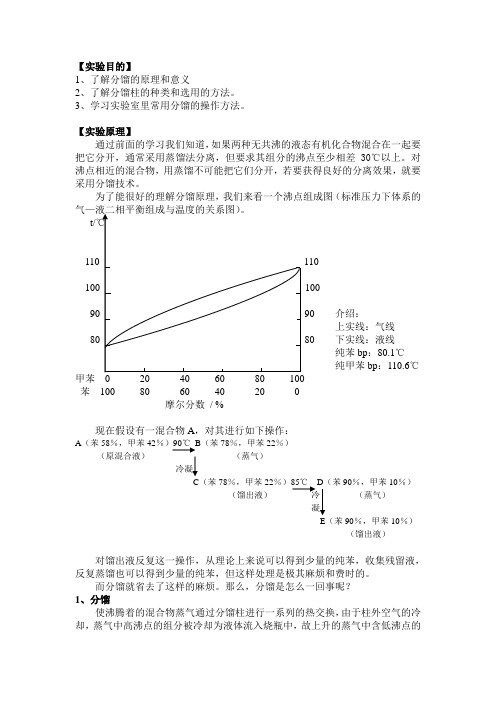
【实验目的】1、了解分馏的原理和意义2、了解分馏柱的种类和选用的方法。
3、学习实验室里常用分馏的操作方法。
【实验原理】通过前面的学习我们知道,如果两种无共沸的液态有机化合物混合在一起要把它分开,通常采用蒸馏法分离,但要求其组分的沸点至少相差30℃以上。
对沸点相近的混合物,用蒸馏不可能把它们分开,若要获得良好的分离效果,就要采用分馏技术。
为了能很好的理解分馏原理,我们来看一个沸点组成图(标准压力下体系的t/100介绍:上实线:气线下实线:液线纯苯bp:80.1℃纯甲苯bp:110.6℃甲苯苯100 80 60 40 20 0摩尔分数/ %现在假设有一混合物A,对其进行如下操作:A(苯58%,甲苯42%)90℃B(苯78%,甲苯22%)(原混合液)(蒸气)冷凝C(苯78%,甲苯22%)85℃D(苯90%,甲苯10%)(馏出液)冷(蒸气)凝E(苯90%,甲苯10%)(馏出液)对馏出液反复这一操作,从理论上来说可以得到少量的纯苯,收集残留液,反复蒸馏也可以得到少量的纯苯,但这样处理是极其麻烦和费时的。
而分馏就省去了这样的麻烦。
那么,分馏是怎么一回事呢?1、分馏使沸腾着的混合物蒸气通过分馏柱进行一系列的热交换,由于柱外空气的冷却,蒸气中高沸点的组分被冷却为液体流入烧瓶中,故上升的蒸气中含低沸点的组分就相对地增加;当冷凝回流途中遇到上升地蒸气,两者之间又进行热交换,上升的蒸气中高沸点的组分又被冷凝,低沸点的组分仍然继续上升,易挥发的组分又增加了。
如此在分馏柱内反复进行着气化——冷凝——回流等程序,最终低沸点的组分从分馏柱的顶部蒸馏出来,高沸点组分留在容器中,从而将不同沸点的物质分离开来。
需要指出的是,分馏也不能分离共沸混合物。
2、影响分馏效率的因素(1)理论塔板:分馏柱中的混合物,经过一次汽化和冷凝的热力学平衡过程,相当于一次普通蒸馏所达到的理论浓缩效率,当分馏柱达到这一浓缩效率时,那么分馏柱就具有一块理论塔板。
延迟焦化工艺参数优化及操作控制

化气,并使汽油的蒸汽压合格;柴油需要加氢精
制;蜡油可作为催化裂化原料或燃料油。
二、主要工艺参数
焦化装置的工艺参数包括加热炉、焦炭塔温度、压力、循 环比以及分馏、吸收、放空系统操作温度、压力等。 主要控制指标是加热炉、焦炭塔温度与压力及循环比。
1.操作温度
焦化装置操作温度一般指加热炉出口温度或焦炭塔温度,一般控 制在493-502℃。
0.105-0.141MPa或更低,循环比降到0.05,焦化液体收率
可提高3%,焦炭产率降低2%。 福斯特-惠勒公司典型焦化装置的设计压力为0.103MPa, Lummus公司典型低压焦化装置焦炭塔压力亦为0.103MPa,
Kellog公司典型设计压力为0.1-0.141MPa.
④加工高沥青质渣油时,为了减少弹丸焦(shot-coke)的 生成;
⑤加热炉燃烧工况不佳,需增加循环比,减缓炉管结焦。
降低循环比的影响:
①单程(零循环比)或低循环比焦化,液体收率高,焦炭收率低; ②单程或低循环比使焦化蜡油变重、质量变差,残炭与重金属含
量增加,其残炭可高达1.9%,会影响下游催化裂化及加氢裂化 装置。
(3) 可高循环比方案
通过循环油泵抽出分馏塔底含焦粉的循环油,以一定比例混入 加热炉进料缓冲罐。
特点:
①采用分馏塔底循环油代替新鲜原料渣油成分馏塔底与焦炭塔高温油气 换热,由于循环油中胶质、沥青质含量低,其结焦倾向降低,用于提 高蒸发段温度的低循环比操作。 ②该方案中的循环油既可使用分馏塔换热、洗涤段冷凝下来的循环油, 也可用蜡油或柴油馏分,实现选择性馏分油循环。 ③塔底循环油经塔外换热器循环回流,可控制塔底温度,减缓塔底结焦
(2) 大陆-菲利浦斯公司低循环比+馏分油循环方案
焦化装置分馏塔上部结盐分析及其应对措施

焦化装置分馏塔上部结盐分析及其应对措施
夏文伟; 朱天福; 付强; 郭守学
【期刊名称】《《当代化工研究》》
【年(卷),期】2018(000)009
【摘要】中国石化青岛炼化公司延迟焦化装置于2008年5月建成投产,由中国石化工程公司设计,装置原设计规模为250万吨/年,采用"两炉四塔"工艺技术。
装置于2011年7月进行扩能改造,改造后规模扩大为290万吨/年。
在装置实际运行中分馏塔上部系统曾多次发生结盐问题,导致顶循回流流量大幅波动、顶循泵密封泄露、管线腐蚀穿孔、塔盘分离效果变差,严重影响产品质量和装置长周期运行。
本文就分馏塔上部结盐的现象进行介绍、原因进行分析,提出了减缓分馏塔上部结盐的措施。
【总页数】2页(P20-21)
【作者】夏文伟; 朱天福; 付强; 郭守学
【作者单位】中国石化青岛炼油化工有限责任公司山东266500
【正文语种】中文
【中图分类】T
【相关文献】
1.延迟焦化装置分馏塔结盐原因分析及预防措施 [J], 杨万强;周建刚;万生瑶
2.延迟焦化装置分馏塔结盐原因分析及解决措施 [J], 李林;吴云鹏;孙丽琳
3.延迟焦化装置分馏塔顶结盐原因分析与对策 [J], 巫文娟;段波;徐佳;鲍阳
4.焦化装置分馏塔上部结盐分析及其应对措施 [J], 夏文伟;朱天福;付强;郭守学
5.延迟焦化装置分馏塔顶结盐问题分析与技术改造 [J], 陈楠;陶新建;张磊
因版权原因,仅展示原文概要,查看原文内容请购买。
延迟焦化装置换热分馏流程方案分析

摘要 : 以国内两套典型的分别为可调循环 比和传统工 艺流程 的延 迟焦化装 置作为研 究背景 , 借助三 环节能量
系统综合优化方法 , 根据延迟焦化两种工艺流程各 自的特点 , 分别对 加热炉对 流段和辐射 段热负荷分 配、 分馏塔操
见 ) 分馏塔 实际塔板数 迟焦化装置 作为研究背景 , 助过程系统能量综 采用一炉两塔流程( 图 2 , 借 合优化“ 三环节” 策略方法 , 】对装置 的加热炉能 为 3 块 , 8 循环 比为 0 2 。对两种流程所进行 的对 .5
量利用、 分馏塔操作、 换热流程 、 装置 白产蒸 汽量 比分析计算均采用装置设计数据。 等方面进行对 比分析。
作、 换热流程 、 装置 自 产蒸汽量等进行分析 比较 , 探讨不 同工艺流程 对装置 整体用能 的影 响 。分 析结果表 明 。 工艺
流程 的不 同及原料渣油换热流程 的差别对于装置稳定操 作 、 加热 炉用能 、 分馏 塔取热 、 热流程 安排 、 换 自产 燕汽 的 温度和压力等有着不同程度的影响。相关焦化流程的对 比分析对焦 化装置 的流程选择及设 计优 化有着 十分重 要
2 用能 比较
2 1 加热 炉 .
传统流程和可调循环 比流程 由于原料油进加 热炉的方式不同 , 而使 加热炉的对流段和辐射段 的负荷分配以及加热炉单位能耗出现差异。两流 程 的加热炉能量对 比见表 1 。传统 流程 中, 流 对 段 的热负荷主要用来预热原料油 、 过热蒸汽等 。 20 的原 料油在加 热炉对 流段 中加 热到 30 3 4 ℃ , 加热炉总热负荷 的 3 . 1 。而对流段是 占 58% 加热炉的低温区, 能量利用集 中在低温位 , 使加热 炉能量利用效率降低 , 单位能耗 比可调循环 比流
提高焦化全馏分加氢精制装置柴油收率的探讨

以延迟 焦 化 装 置 产 出 的焦 压 加 氢 反 应 进 行 脱 氮 、 硫 经 高 脱
和烯 烃饱 和 ; 在 分馏 塔 中切割 成 3种产 品 , 再 即石 脑 油 ( AT) 轻 柴 油 ( G 及 蜡 油 ( O) 1 9 N 、 L O) HG 。 9 9年 ,
型及 计 算精 度 是 可靠 的。
投稿 日期 :0 1 2—1 。 2 0 —1 0
作 者 简 介 : 莉 莉 ,7岁 , 理 工 程 师 。 19 王 2 助 9 6年 毕 业 于 南 京 理
由表 1可 见 , 际 生产 中 轻 柴 油 与蜡 油 重叠 度 实
工 大 学 精 细 化 工 专 业 , 年 分 配 至 扬 子 石 化 公 司 炼 油 厂 , 在 炼 油 同 现 厂 技 改 办 从 事 炼 油 厂 第 3套 柴 油 加 氢 精 制 装 置 的 筹 备 工作 。
维普资讯
20 0 2年第 1 7卷第 2期
王莉莉 . 提高焦化 全馏 分加氢精 制装置柴 油收率 的探讨
・1 ・ 5
表 3 计算机模 拟 的各 物流产量 与实际 比较 ℃
汽、 液相 负 荷 过大 , 塔 内雾 沫 夹 带 严 重 , 离 效 率 则 分
5 影 响 因素分 析 及 优化
5. 提 高 进 料温 度 1 4 分 馏 塔 工 况分 析
分 馏 炉 实 际 出 口温 度 为 3 22, 算 热 负 荷 为 3* 计 (
3 4 4 J 1, 设 计 分 馏 炉 出 口温度 为 3 0 , 91 18 8 k / 而 1 5℃ 设 计 热 负荷 为 4 8 0 J 1。分馏 炉实 际 热 负荷 02 40 0k /1 已接 近 设计 热 负 荷 , 出 口温 度 比设 计 低 1 ℃ , 但 8 出
华东院延迟焦化装置三种换热分馏流程方案分析

延迟焦化装置三种换热分馏流程的比较谢崇亮李小娜毕治国中国石油工程建设公司华东设计分公司,青岛,266071摘要:以一套加工大庆减压渣油的240万吨/年延迟焦化装置为例,经过模拟计算及用能分析,对原料油与反应油气塔外换热流程(以下简称“流程一”)、原料油与反应油气塔内换热流程(流程二)、蜡油与反应油气塔内换热流程(流程三)进行了能耗、能质利用及设备投资等方面的分析。
分析结果表明:在三种流程均达到同样的分离效果前提下,流程一设备投资最高,流程二能质利用最优,流程三能耗最低。
关键词:延迟焦化分馏塔换热能耗分析1.前言随着常规原油的日益减少,重质油、油砂、沥青砂等非常规原油的开发和利用越来越多,加上全球高油价的推动及石油焦的气化技术和焦化-气化-汽电联产组合工艺的开发和大规模应用,使得延迟焦化装置因其自身的优点成为劣质重油加工的重要手段,这也使得对延迟焦化工艺流程进行优化分析,节能降耗具有更普遍的现实意义。
本文以国内某240万吨/年延迟焦化装置为例,以ASPEN 2006的模拟计算及用能分析为媒介,对三种流程进行分析比较。
比较的基础是保证分馏塔各侧线产品质量合格,同时尽量保持分馏塔上部取热比例相同。
2.工艺流程简介流程一如图1所示,减压渣油经过一系列原料油换热器换热后,进入加热炉进料缓冲罐,与来自分馏塔底的焦化循环油一起在加热炉进料缓冲罐内混合后进入焦化加热炉。
其特点在于减压渣油不再进入焦化分馏塔进行换热和洗涤,增设分馏塔底循环油外取热器、循环油回流泵,通过调节分馏塔底循环油的取热量来灵活调节循环比。
流程二如图2所示,减压渣油经过一系列原料油换热器换热后,分上、下两股物料进入分馏塔下段,与焦炭塔顶来的反应油气直接接触,进行传质和传热。
换热后的渣油与循环油一起经加热炉进料泵进入焦化加热炉。
通过调节焦化分馏塔换热挡板上方的减压渣油量来调节循环比。
流程三如图3所示,减压渣油经过一系列原料油换热器换热后直接进入分馏塔底部,不再作为洗涤油与焦炭塔顶反应油气直接接触。
焦化分馏塔顶部结盐的预防及处理措施

焦化分馏塔顶部结盐的原因及防治措施林健谢崇亮范海玲颜峰中国石油工程建设公司华东设计分公司,青岛,266071摘要:分析了延迟焦化分馏塔顶部结盐的机理、原因和危害,详细介绍了目前国内外就分馏塔顶部结盐问题所采取的各种预防和处理措施。
对今后延迟焦化工艺流程的设计,以及焦化装置日常生产操作起到了一定的指导作用。
关键词:延迟焦化分馏塔结盐焦化装置加工原料大多是来自常减压蒸馏装置的渣油,还有其他劣质重油、污油、油浆等,这些原料一般含有较多N、S及无机盐及其他机械杂质。
由于常减压装置的原油电脱盐不彻底或油田在原油开采过程中使用助剂,会使焦化原料含有较多的氮化物等成分,由此造成延迟焦化装置生产过程中在分馏塔顶部及塔顶冷却器等部位结盐(结垢)。
由于原料性质的不断变化,分馏塔顶系统结盐现象逐渐成为一个普遍存在的问题。
针对分馏塔顶系统结盐问题分析其形成原因和对装置操作的影响,并提出相应的预防和处理的措施。
1.结盐产生的原因及危害分馏塔顶结盐主要是由于焦化原料携带的氮化合物在焦炭塔内反应时生成无机物NH3,NH3与Cl-反应生成极易溶于水的NH4Cl。
在分馏塔的下部因为温度高,NH4Cl分解为NH3和HCl,以气相形式存在。
但在随油气上升至塔顶的过程中,随着温度逐渐降低会重新生成NH4Cl晶体颗粒。
若分馏塔顶部操作温度较低,会产生部分凝结水,细小的NH4CL颗粒就会溶解在低温水相中,内回流至下面的塔盘,随着温度升高液态水又会慢慢汽化,如此在塔顶几层塔盘之间作冷凝和汽化循环。
在向下内回流过程中,NH4CL逐步失水并浓缩,最终成为一种粘度很大的半流体。
这种半流体与铁锈、焦炭粉末等混合在一起沉积于塔盘、塔顶回流线、降液管、受液盘处,积累到一定程度就会阻碍液体的流动,堵塞塔盘上的开孔,从而导致分馏塔压降逐渐增大,气液接触减少,塔板效率下降,塔顶气相负荷较大,破坏了分馏塔的正常操作。
严重时还会发生冲塔等事故,对富气压缩机安全运行造成危害。
- 1、下载文档前请自行甄别文档内容的完整性,平台不提供额外的编辑、内容补充、找答案等附加服务。
- 2、"仅部分预览"的文档,不可在线预览部分如存在完整性等问题,可反馈申请退款(可完整预览的文档不适用该条件!)。
- 3、如文档侵犯您的权益,请联系客服反馈,我们会尽快为您处理(人工客服工作时间:9:00-18:30)。
焦化分 馏 塔是 延 迟 焦 化 装 置 的 主要 过 热 源 , 合 理 安排分 馏 塔取 热 流 程 对 产 品结 构 、 温 热 利 低 用 及设 备投 资 的优 化 具 有 重 要 意 义 ¨ 。 目前 国 J 内外 关 于延迟 焦化装 置 分馏塔 是否 设置 顶循 取热 流程 的分歧 一 直存 在 , 内设 计 普 遍 倾 向于设 置 国 顶循 流程 , 国外 倾 向于采 用 分 馏 塔 顶 冷 回流 取 而
分 馏 塔
至 吸收稳 定
密 度 (0 ℃ ) g・ m一 2 / c ( ) % 硫 , w( ) l g 氮 / g・  ̄
AS ( 6 / TM D1 0) 1
1 % 5 % O 9 %Байду номын сангаас 5
1 0 .5
3 5 .5
96 5 0
图 1 焦化分馏塔上部的两种取热流程
了 比较。结果表 明 : 两种流程均可 以达到相 同的分离要 求 , 对原 油换后 温度没 有影 响; 流程 2分馏 塔顶蒸 汽分压
低、 温度 高, 有利 于减少 N 1 H C 溶液产生 , 防结盐弹性大 , 但在线洗盐操作不 易控制且污油量大 ; 于低 温热无法再 对 利用的装 置 , 流程 2比流程 1投资多 16×1 R 3 0 MB¥, 电负荷减少 2 W; 9k 对于低温热可回收的装 置 , 推荐流程 1 。 关键词 : 延迟焦化 分馏塔 顶循环取热 塔顶冷回流取热
示 , 分馏 塔顶循 部 位设 置全抽 出集 油箱 , 在 通过 顶 循 环油 泵抽 出液 相 , 分 经 顶 循 空 冷器 冷 却 后 作 部
第 8期
谢崇亮 等. 焦化分馏塔上部取 热流程 比较
分 馏 塔 顶 冷 回 流 取 热 流 程 ( 程 2) 图 流 如
后 的粗汽 油作冷 回流 返 回分馏塔 顶 , 塔顶 油气 总量 大, 油气分压 增加 , 故塔顶 温度 明显 高于流程 1 。
2 1 年 8月 01
炼 油 技 术 与 工 程 P T O E M R FN R N I E R N E R L U E IE YE GN E IG
第 4 卷第 8期 1
焦 化 分 馏 塔 上 部 取 热流 程 比较
谢崇亮 , 李小娜 , 毕治 国 , 李爱凌
( 中国石油工程建设公司华东设计分公司 , 山东省青 岛市 2 67 ) 6 0 1
例 , 过 A P NPU 通 S E L S和 H R 软 件 对 两 种 流 程 TI
至 吸 收稳 定
的产 品质 量指 标 、 馏塔 顶结 盐 、 资及 能耗 等方 分 投 面进 行分 析 比较 , 焦 化装 置 分 馏 部 分 的 流程 设 为
计 提 供参考 。 1 比较基 础
热量。
2 1 分 馏塔 产 品 .
采 用 A P NP U 06进行 模 拟 计 算 , 收 SE L S20 其 率 如表 2所 示 , 顶 温度 及产 品指 标如 表 3所示 。 塔
表 2 分 馏 塔 产 品 流 率
Ta e 2 Flw ae o r d t bl o rt fp o ucs k /h g
44 5
69 8 82 7
F g 1 T w f w da r ms o mo i g h a i . o l ig a fr o e vn et
fo c kng fa to ao rm o i r ci n tr
1 2 流程 简述 .
收稿 E期 :0 1一 2—2 ; l 21 O 4 修改稿收到 日期 :0 1— 5— 3 21 0 2。 作者简介 : 谢崇亮 , 高级工程师 ,9 6年 7月 毕业于大庆石 油 18
分馏塔 顶循 取 热 流 程 ( 程 1 如 图 1 a 所 流 ) ()
学院石油加工专业 , 现从事炼油设计工作 , 任该公司总工程师 ,
副总经理。联 系电话 :52—890 , - a :i hnln @ 03 05  ̄ E m i x cogag l e i
c p cic 。 n c e.n
摘要 : 以一套 5 6 / 延 迟焦化装置为例 , A P N P US和 HT 1 .0Mta 用 SE L R 软件对分馏塔顶循取 热流程 ( 流程 1 、 ) 分 馏塔顶冷回流取热 流程 ( 流程 2) 进行 了模拟计算及流程分析 , 对产品指标 、 分馏塔 顶结盐 、 投资及 能耗等方面进行
1 1 原料 性质 .
() 循取 热流 程 a顶 分 馏塔 顶 分 馏塔 顶
体 压缩
该装 置为 减压渣 油进 料 , 其原 料性 质见表 1 。
表 1 减 压 渣 油 主 要 性 质
T b e 1 Man p o e t so a u m e i u a l i r p ri fv c u r s e e d
1 b 所示 , () 自分 馏塔 顶 三 相 分离 罐 抽 出 的油相 返 回分 馏塔 顶建 立 分 馏塔 内循 环 , 现 分馏 塔 的传 实
质 传 热过 程 。
2 对 比分析
比较 原 则为保 证 分馏 塔侧 线产 品收率及 控制 指标 相 同 , 量 高 温 位 取 热 , 分 利 用 高 品 质 尽 充
热流 程 。
为 塔顶 过冷 液相 回流 , 分 直 接返 回集 油 箱 下 部 部 作 内回流 。分馏塔 顶气 相通 过分 馏塔 顶空 冷器 冷 却 后在 三相 分离 罐 中进行分 离 。
分馏塔 顶 分 馏塔顶 空冷器 三 相分 离罐
至气 体压 缩
本 研究 以某 拟建 56 / .0Mta延迟 焦 化装 置 为
2 2 分馏 塔取 热 . 两种 流程 分馏 塔取 热情 况如 表 4所示 。
表 4 分馏塔取热- 隋况对 比
T be 4 C mp r o f e tr mo i g f m r ci n tr a l o a i n o a e v n o f t ao s h r a o