阴极剥离
ASTM G8-96(R2010)管道涂层阴极剥离的标准试验方法(中文翻译版)

ASTM G8-96(R2010)管道涂层阴极剥离的标准试验方法(中文翻译版)1这些试验方法由ASTM涂料及相关涂层、材料和应用委员会D01管辖,并由管道涂层和衬里耐久性小组委员会D01.48直接负责。
现行版本于2010年12月1日批准。
2010年12月出版。
最初批准于1969年。
上一版于2003年批准为G8–96(2003)ε1。
DOI: 10.1520/g008-96R10。
本标准以固定名称G8发布;紧跟在名称后面的数字表示最初采用的年份,如果是修订,则表示最后修订的年份。
括号中的数字表示上次重新批准的年份。
上标(')表示自上次修订或重新批准以来的编辑性更改。
1、范围1.1这些试验方法包括同时确定应用于钢管外部的绝缘涂层系统的比较特性的加速程序,目的是防止或减轻地下设施中可能发生的腐蚀,在地下设施中,管道将接触土壤,并且可能不会受到阴极保护。
该方法适用于从商业生产中获得的涂层管样品,当涂层具有电屏障功能时,也适用于此类样品。
1.2本试验方法适用于在室温下对浸没或浸没在试验溶液中的涂层进行试验。
当无法浸没试样时,可考虑使用试验方法G95,即将试验单元粘结到涂层管试样的表面。
如果需要更高的温度,见试验方法G42。
如果需要特定的试验方法而没有选择,请参见试验方法G80。
1.3以国际单位制表示的3位有效小数为标准。
括号中给出的值仅供参考。
1.4本标准无意解决与其使用相关的所有安全问题(如有)。
本标准的使用者有责任在使用前建立适当的安全和健康实践,并确定法规限制的适用性。
2、参考文件2.1 ASTM标准22有关参考的ASTM标准,请访问ASTM网站,或通过Service@联系ASTM客户服务。
有关ASTM标准年鉴卷信息,请参阅ASTM网站上的标准文件摘要页。
G12钢制管道涂层膜厚无损检测方法(2013年废止)3G42高温下管道涂层阴极剥离试验方法G80管道涂层特定阴极剥离试验方法(2013年撤销)33本历史标准的最新批准版本见。
阴极剥离

阴极剥离阴极剥离或叫阴极去黏合是涂装金属遭到破坏的一种常见形式。
涂装的钢铁设备如船舶、海上平台和地下管道,以及盛水溶液的大型槽罐的内壁常采用阴极保护手段防止腐蚀。
阴极保护不理想的后果之一是有缺陷处的涂层,由于阴极反应而失去附着力,涂层会从金属上分离,这种现象称为阴极剥离。
覆盖了高聚物的金属表面可以变为阴极区,并可催化涂层下的阴极反应。
这种阴极本性可以由有目的地诱发,如阴极保护中的阴极极化,也可由腐蚀来诱发,因为发生腐蚀时阴极区和阳极区是分开的。
阴极反应,或更确切地说阴极反应产物会对涂层和基体之间的键有不利的影响,并使涂层从基体上分离,即我们所称的阴极剥离。
受阴极保护的船体、管线和地下结构与阴极剥离有关,车辆上或暴露在大气环境下的金属构件上油漆的起泡,往往是由于基体被暴露而引起了涂层的受损,暴露面为阳极,而其邻近区为阴极。
腐蚀的扩展和油漆的起泡是由于发生了阴极剥离以及随后在使用期中干湿交替作用,使水和盐侵入的结构。
阴极剥离是引起涂装金属腐蚀的一种特别形态,它破坏了涂层对金属的附着力。
阴极剥离的机理非常复杂,并随涂装体系不同而变化,尚无一般性结论,现在提出来的有三种主要的阴极剥离机理。
这三种机理是:由于阴极吸氧反应所产生的高pH值是一前提:①涂层在界面上分离,即涂层发生了附着力的破坏,或界面被水置换,从而使涂层从金属表面上分离。
②金属上氧化物的溶解,金属上氧化膜被阴极反应所产生的碱溶解后,破坏了涂层与基体的结合而产生了剥离。
③内聚力破坏和涂层的解聚,涂层本身的物理和化学结构受到了破坏,对涂层/金属界面之间结合力起了破坏作用。
为了保证埋地金属管道在恶劣环境下的长期可靠运行,除采用防腐效果好的厚涂层环氧粉末涂料、并外加机械强度高的聚乙烯保护层进行保护,尽量减少运输施工过程可能出现的机械损伤外,还采用阴极保护的办法,管道开始腐蚀时,先腐蚀外挂的牺牲金属阳极而使管道免受腐蚀。
因此,有机涂层与阴极保护措施相结合是目前埋地管道重防腐所采用的主要方法。
阴极剥离试验原理

阴极剥离试验原理引言阴极剥离试验是一种常用的表面分析技术,用于研究材料的阴极性能。
本文将详细介绍阴极剥离试验的原理、方法和应用。
二级标题1:阴极剥离试验的概述三级标题1.1:试验目的在材料科学领域,阴极剥离试验被广泛应用于研究材料的电化学性能,包括电阻、阴极电位和电化学活性等。
通过剥离试验,可以评估阴极保护性能并研究材料的耐腐蚀性能。
三级标题1.2:试验原理阴极剥离试验主要基于以下原理: 1. 阴极剥离试验是一种电化学方法,通过在试样表面施加特定电位,将试样上的保护层(如氧化膜等)剥离下来,从而获得试样的裸露表面。
2. 剥离试验条件包括温度、电位施加速率、剥离试验时间等,这些条件会影响剥离效果。
3. 通过评估剥离试验后的试样表面形貌和化学成分,可以了解材料的防护性能和腐蚀机理。
二级标题2:阴极剥离试验方法三级标题2.1:实验器材进行阴极剥离试验所需的主要器材包括: - 剥离试验电池:用于施加电位和记录电流的电池。
- 试样:需要进行剥离试验的材料样品。
- 电位控制仪:用于控制试验电池中的电位。
- 电流计:用于测量试验电池中的电流。
- 其他辅助设备:包括样品夹持装置、电解液等。
三级标题2.2:实验步骤阴极剥离试验通常包括以下步骤: 1. 准备试样:根据试验要求,制备适当尺寸和形状的试样,并保证试样表面的洁净。
2. 装配试验电池:按照要求,将试样固定在试验电池中,并加入合适的电解液。
3. 施加电位:通过电位控制仪施加设定的电位值,并记录试验电池中的电流。
4. 剥离试验:在设定的时间内施加电位,使试样表面的保护层剥离下来。
5. 观察和分析:使用显微镜或其他表面分析技术观察试样表面的形貌和化学成分变化。
三级标题2.3:数据处理剥离试验得到的数据通常包括电流随时间的变化曲线和试样表面形貌的显微照片。
通过对数据进行分析和处理,可以获得以下信息: - 试样表面剥离的速率和程度。
- 试样表面的形貌特征,如微观孔洞、腐蚀斑点等。
耐阴极剥离定义

耐阴极剥离定义
耐阴极剥离是一种特殊的材料处理技术,用于从基底材
料上剥离薄膜或涂层。
它是一种非常有效的方法,可以在
不破坏基底材料的情况下,将薄膜或涂层从其上分离出来。
耐阴极剥离的原理是利用电化学反应来实现。
在这个过程中,基底材料被作为阴极,而阳极则是一个电解质溶液中
的金属。
当施加电流时,阳极上的金属会发生氧化反应,
形成氧化物或氢氧化物。
这些产物会与薄膜或涂层之间形
成一个界面,并且具有较强的粘附力。
随着电流的施加,
界面处的粘附力会逐渐增强。
当达到一定程度时,粘附力
将超过薄膜或涂层与基底材料之间的粘附力。
这时,薄膜
或涂层就会开始从基底材料上剥离下来。
耐阴极剥离具有
许多优点。
首先,它可以在较低的温度下进行,从而避免
了基底材料的热损伤。
其次,它可以在大面积上进行,适
用于各种尺寸和形状的基底材料。
此外,耐阴极剥离还可
以实现高效、快速和可控的剥离过程。
耐阴极剥离在许多
领域都有广泛的应用。
例如,在电子器件制造中,它可以
用于剥离薄膜电阻、金属层或其他功能性涂层。
在太阳能
电池制造中,它可以用于剥离光伏薄膜以进行再利用或回收。
此外,在纳米技术和生物医学领域,耐阴极剥离也被
广泛应用于纳米结构和生物传感器的制备。
总之,耐阴极
剥离是一种重要的材料处理技术,具有许多优点和广泛的
应用前景。
它为材料科学和工程领域提供了一种高效、可
控和环保的方法来分离薄膜或涂层,并为各种应用提供了
更多可能性。
耐阴极剥离定义

耐阴极剥离定义引言耐阴极剥离是一种用于材料加工和制造过程中的技术,主要用于去除材料表面的阴极层。
阴极层是指材料表面的一层具有负电荷的物质,常见于金属、合金和陶瓷等材料上。
耐阴极剥离技术通过一系列工艺步骤,将阴极层从材料表面剥离,并实现材料的清洁和改性。
耐阴极剥离的原理耐阴极剥离技术的实现依赖于材料表面的阴极层与剥离剂之间的相互作用。
剥离剂是一种化学物质,具有与阴极层相互作用的特性。
在耐阴极剥离过程中,剥离剂与阴极层发生反应,改变阴极层的物理和化学性质,从而使其与材料表面分离。
耐阴极剥离的应用领域耐阴极剥离技术被广泛应用于材料加工和制造领域。
以下是一些常见的应用领域:1. 金属加工耐阴极剥离技术在金属加工中起到了重要的作用。
例如,在铝合金的表面处理过程中,耐阴极剥离可以去除铝合金表面的氧化层,从而提高铝合金的表面质量和耐腐蚀性能。
2. 电子工业在电子工业中,耐阴极剥离技术被广泛用于半导体器件的制造过程中。
通过耐阴极剥离,可以去除半导体器件表面的阴极层,从而提高器件的电性能和稳定性。
3. 光学材料在光学材料的制备过程中,耐阴极剥离技术可以去除材料表面的污染物和不纯物质,从而提高光学材料的透明度和光学性能。
4. 医疗器械耐阴极剥离技术在医疗器械的制造过程中也有应用。
例如,在人工关节的制备过程中,耐阴极剥离可以去除金属表面的氧化层和污染物,从而提高人工关节的生物相容性和耐腐蚀性能。
5. 纳米材料耐阴极剥离技术在纳米材料的制备和表面改性过程中也有广泛应用。
通过耐阴极剥离,可以去除纳米材料表面的有机残留物和杂质,从而提高纳米材料的纯度和稳定性。
耐阴极剥离的工艺步骤耐阴极剥离技术通常包含以下几个工艺步骤:1. 表面处理在开始耐阴极剥离之前,需要对材料表面进行处理。
这包括清洁表面、去除污染物和油脂等。
2. 剥离剂选择根据材料的特性和剥离的要求,选择合适的剥离剂。
剥离剂的选择应考虑剥离效果、安全性和环境友好性等因素。
阴极保护的基本参数

阴极保护的基本参数一、最小保护电流密度阴极保护时,使金属腐蚀停止,或达到允许程度时所需的电流密度值称为最小保护电流度。
最小保护电流度是阴极保护设计的重要参数。
如选用不当,或者达不到完全保护,或者造成过保护,会使阴极保护的效果降低或不经济,浪费多余的电能。
直接从北保护的金属体表面测到其所分布的最小保护电流密度是比较困难的。
一般通过被保护体的总保护电流与被保护体的总面积相除来获得。
最小保护电流密度的大小取决于被保护金属的种类、表面状况、腐蚀介质的性质、组成、浓度、温度和金属表面绝缘层质量等上述条件不同、最小保护电流密度的值也不同。
碳钢在不同截止中的最小保护电流密度可参见表1到表3。
钢在不同介质中的最小保护电流密度表1介质电流密度介质电流密度含氧的35潮湿的0.055~流动的65~172含硫酸450流动的50静止的0.05~0.1涂层种类不同所需的保护电流密度值不同,这是由于保护电流经阳极因如土壤,再流经绝缘层的过渡电阻不同。
钢管外覆盖参个的绝缘电阻值越高,所需的保护电流密度值越小。
防腐层种类及所需保护电流密度表2防腐层种类保护电流密度mA/m2聚乙烯层3mm厚0.001~0.007石油沥青玻璃布7mm厚0.01~0.05石油沥青玻璃布4mm厚0.05~0.25旧沥青层0.5~3.5石蜡布0.5~1.5旧漆层1~30防腐层电阻和所需保护电流密度表3防腐层面电阻Ω·m2保护电流密度mA/m2防腐层面电阻Ω·m2保护电流密度mA/m210000000.00033000000.00011000000.003300000.001100000.0330000.110000.3300110033010对于无防腐层的裸钢管,从实际工程中的经验值大约为5~50毫安/米2。
十分大于有防腐层钢管的值。
因此,裸钢管采用阴极保护技术上是可行的,但经济上是不合理的。
埋于土壤中的钢筋或处在混凝土结构中的钢管其最小保护电流密度经验值大约为2mA/m2。
阴极剥离相关标准指标汇总
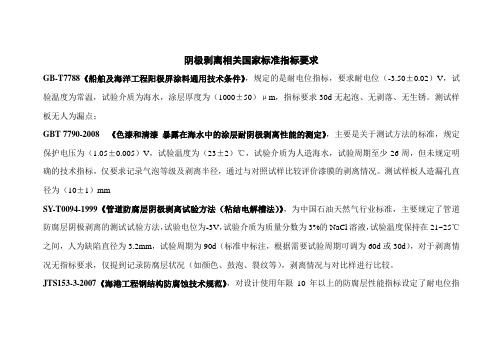
阴极剥离相关国家标准指标要求GB-T7788《船舶及海洋工程阳极屏涂料通用技术条件》,规定的是耐电位指标,要求耐电位(-3.50±0.02)V,试验温度为常温,试验介质为海水,涂层厚度为(1000±50)μm,指标要求30d无起泡、无剥落、无生锈。
测试样板无人为漏点;GBT 7790-2008 《色漆和清漆暴露在海水中的涂层耐阴极剥离性能的测定》,主要是关于测试方法的标准,规定保护电压为(1.05±0.005)V,试验温度为(23±2)℃,试验介质为人造海水,试验周期至少26周,但未规定明确的技术指标,仅要求记录气泡等级及剥离半径,通过与对照试样比较评价漆膜的剥离情况。
测试样板人造漏孔直径为(10±1)mmSY-T0094-1999《管道防腐层阴极剥离试验方法(粘结电解槽法)》,为中国石油天然气行业标准,主要规定了管道防腐层阴极剥离的测试试验方法,试验电位为-3V,试验介质为质量分数为3%的NaCl溶液,试验温度保持在21~25℃之间,人为缺陷直径为3.2mm,试验周期为90d(标准中标注,根据需要试验周期可调为60d或30d),对于剥离情况无指标要求,仅提到记录防腐层状况(如颜色、鼓泡、裂纹等),剥离情况与对比样进行比较。
JTS153-3-2007《海港工程钢结构防腐蚀技术规范》,对设计使用年限10年以上的防腐层性能指标设定了耐电位指标,测试方法执行GB/T 7788,但强调了当采用外加电流阴极保护时配套涂层耐阴极电位为-1.50V,常规情况下耐电位为-1.20V。
GBT 23257-2009《埋地钢质管道聚乙烯防腐层》,规定了环氧粉末涂料的抗阴极剥离指标,试验电位为-1.50V,试验介质为质量分数为3%的NaCl溶液,人为缺陷直径为3.2mm,涂层厚度为(300~400)μm,试验条件为(65℃,48h)时,剥离指标为≤8mm; 试验条件为(65℃,30d)时,剥离指标为≤15mm。
阴保专业知识基础篇(四)
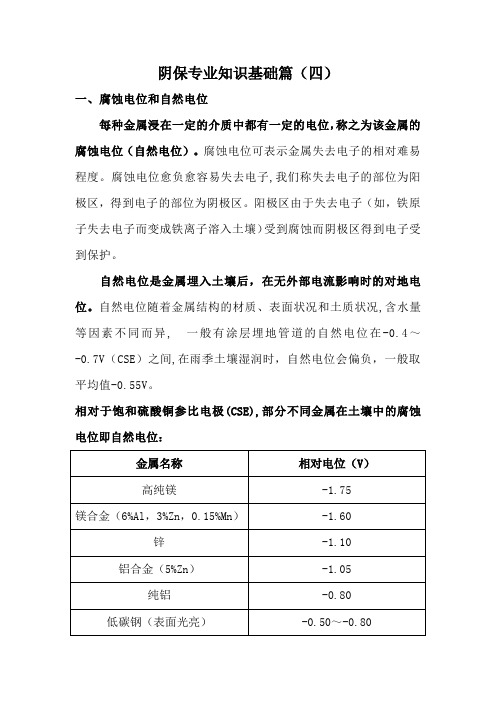
阴保专业知识基础篇(四)一、腐蚀电位和自然电位每种金属浸在一定的介质中都有一定的电位,称之为该金属的腐蚀电位(自然电位)。
腐蚀电位可表示金属失去电子的相对难易程度。
腐蚀电位愈负愈容易失去电子,我们称失去电子的部位为阳极区,得到电子的部位为阴极区。
阳极区由于失去电子(如,铁原子失去电子而变成铁离子溶入土壤)受到腐蚀而阴极区得到电子受到保护。
自然电位是金属埋入土壤后,在无外部电流影响时的对地电位。
自然电位随着金属结构的材质、表面状况和土质状况,含水量等因素不同而异, 一般有涂层埋地管道的自然电位在-0.4~-0.7V(CSE)之间,在雨季土壤湿润时,自然电位会偏负,一般取平均值-0.55V。
相对于饱和硫酸铜参比电极(CSE),部分不同金属在土壤中的腐蚀电位即自然电位:金属名称相对电位(V)高纯镁-1.75镁合金(6%Al,3%Zn,0.15%Mn)-1.60锌-1.10铝合金(5%Zn)-1.05纯铝-0.80低碳钢(表面光亮)-0.50~-0.80低碳钢(表面锈蚀)-0.20~-0.50铸铁-0.50混凝土中的低碳钢-0.20铜-0.20在同一电解质中,不同的金属具有不同的腐蚀电位,如轮船船体是钢,推进器是青铜制成的,铜的电位比钢高,所以电子从船体流向青铜推进器,船体受到腐蚀,青铜推进器得到保护。
钢管的本体金属和焊缝金属由于成分不一样,两者的腐蚀电位差有时可达0.275V,埋入地下后,电位低的部位遭受腐蚀。
新旧管道连接后,由于新管道腐蚀电位低,旧管道电位高,电子从新管道流向旧管道,新管道首先腐蚀。
同一种金属接触不同的电解质溶液(如土壤),或电解质的浓度、温度、气体压力、流速等条件不同,也会造成金属表面各点电位的不同。
二、参比电极为了对各种金属的电极电位进行比较,必须有一个公共的参比电极。
饱和硫酸铜参比电极电极,其电极电位具有良好的重复性和稳定性,构造简单,在阴极保护领域中得到广泛采用。
不同参比电极之间的电位比较:土壤中或浸水钢铁结构最小阴极保护电位(V)被保护结构相对于不同参比电极的电位饱和硫酸铜参比电极氯化银参比电极锌参比电极饱和甘汞参比电极钢铁(土壤-0.85 -0.75 0.25 -0.778 或水中)钢铁(硫酸-0.95 -0.85 0.15 -0.878 盐还原菌)三、保护电位1、最小保护电位最小保护电位是金属达到完全保护所需要的最低电位值。
- 1、下载文档前请自行甄别文档内容的完整性,平台不提供额外的编辑、内容补充、找答案等附加服务。
- 2、"仅部分预览"的文档,不可在线预览部分如存在完整性等问题,可反馈申请退款(可完整预览的文档不适用该条件!)。
- 3、如文档侵犯您的权益,请联系客服反馈,我们会尽快为您处理(人工客服工作时间:9:00-18:30)。
Compatibility of the disbondment was enhanced by selecting a temperature of 65°C and a duration of 28 days whenever Standard procedures included the parameters. Correct temperatures and durations in use are listed in Table 2.
An urgent question is how to interpret and correlate varying results obtained by different Standard Methods. Since the Standards contain different combinations of qualitatively identical group of Parameters and Procedures, it is possible to consider eight Standards in Table 1 as a complete representation of all the Standards detailed in Appendix # 1.
Toronto, Ontario, Canada M9W 1M7
ABSTRACT A critical analysis of 22 Cathodic Disbondment Test methods used in the US, European Union, France, Germany, Saudi Arabia, China, Canada, Australia, New Zeeland and Other countries is presented in this paper. Parameters and Procedures used in these Standards are qualified and problems of their application discussed. ASTM G8, ASTM G42, ASTM G80 and four of their generic modifications, as well as CSAZ245.20, EN 10289, DIN 30 671 (1987), API RP 5L7 and AWWA C-210 (old) will generate comparable results, when run under same temperature and duration conditions. Also, CD results obtained with French Standard NF A 49-711 and its generic modifications will be comparable with CD values produced by these tests. Australian AS3862 and related AS/NZS 4352 will give approximately 15 – 20 % smaller cathodic disbondments. ASTM G95 and ISO 15711 (E) test will give larger disbondments owing to the tests’ durations.
The testing is performed in accordance to local Standards and Specifications, the list of which is shown in Appendix # 1. It has to be noted that many other national Standards, not included in the selection, as well as their modifications are being practiced.
1
INTRODUCTION
Cathodic protection (CP) complimented by a barrier-coating is an uncontested method of combating corrosion of buried/immersed structures under natural conditions. It is a daunting task and a noticeable expenditure for users of these structures.
TABLE 1 REPRESENTATIVE CDT STANDARD METHODS
Standard
CSA Z-245 ASTM G8 ASTM G42 ASTM G80 ASTM G95 ISO 15711 AS 3862 NF A 49-711
Voltage [V]
1.5 or 3.5 V 1.5 1.5 1.5 3.0 1.05 3 mA 1.5
2
Comparison of the Standards was based on CD results obtained with two lines of samples coated by 2-component liquid epoxy paints. Some qualitative and limited quantitative correlations between the Standards were formulated.
EXPERIMENTAL
CDT Standard Methods Testing
Basic CD testing was run with separate sets of samples coated by two different 2-component liquid epoxy materials (coating α and coating β) having different resistance against cathodic disbondment - highly resistant coating α and less resistant coating β. In such an arrangement the extent of CD results better characterized both more and less aggressive Standards Methods. Coating thickness was kept between 800 and 900 μm.
Duration [days]
Selection Selection 30 60 90 182 Selection Selection
Notes:
1. Selection means multiple choices. 2. Triple solution is 1/1/1 % solution of NaCl, Na2S04 and Na2C03. 3. Artificial sea water is used.
Copyright
©2007 by NACE International. Requests for permission to publish this manuscript in any form, in part or in whole must be in writing to NACE International, Copyright Division, 1440 South creek Drive, Houston, Texas 777084. The material presented and the views expressed in this paper are solely those of the author(s) and are not necessarily endorsed by the Association. Printed in the U.S.A.
However, the relation between Cathodic Protection and the coating is complicated by undesired CP-side-effects, such as generation of high pH and incidental development of elemental Hydrogen, whenever the media find access to the substrate. These electrochemical processes are a major cause of a gradual increase in the substrate area exposed to the contact with the surrounding environment.
Temperature [°C]
Selection RT Selection RT RT RT Selection Selection
Solution [aqueous]
3 % NaCl Triple solution Triple solution Triple solution 3 % NaCl Sea water 3 % NaCl 3 % NaCl
Keywords : Interface oxide , Delamination and Chemical Attack, CDT Standard Methods, Cathodic disbondment, Electrical stress, Delamination, Thinning, Chemical stress, Chlorate, Oxide dissolution, rtion of CP-related expenditures is the consumption of electrical current, which directly depends on the size of conductive contact between the substrate and the surrounding corrosive media. Due to that barrier-coatings are used to separate the protected structures from the surrounding corrosive media. A well selected coating will substantially reduce the loss of protective current.