塑胶结构设计资料
塑胶结构设计规范
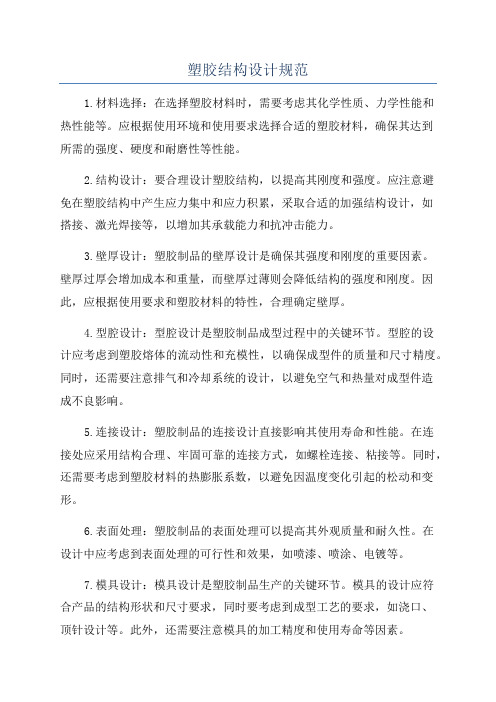
塑胶结构设计规范1.材料选择:在选择塑胶材料时,需要考虑其化学性质、力学性能和热性能等。
应根据使用环境和使用要求选择合适的塑胶材料,确保其达到所需的强度、硬度和耐磨性等性能。
2.结构设计:要合理设计塑胶结构,以提高其刚度和强度。
应注意避免在塑胶结构中产生应力集中和应力积累,采取合适的加强结构设计,如搭接、激光焊接等,以增加其承载能力和抗冲击能力。
3.壁厚设计:塑胶制品的壁厚设计是确保其强度和刚度的重要因素。
壁厚过厚会增加成本和重量,而壁厚过薄则会降低结构的强度和刚度。
因此,应根据使用要求和塑胶材料的特性,合理确定壁厚。
4.型腔设计:型腔设计是塑胶制品成型过程中的关键环节。
型腔的设计应考虑到塑胶熔体的流动性和充模性,以确保成型件的质量和尺寸精度。
同时,还需要注意排气和冷却系统的设计,以避免空气和热量对成型件造成不良影响。
5.连接设计:塑胶制品的连接设计直接影响其使用寿命和性能。
在连接处应采用结构合理、牢固可靠的连接方式,如螺栓连接、粘接等。
同时,还需要考虑到塑胶材料的热膨胀系数,以避免因温度变化引起的松动和变形。
6.表面处理:塑胶制品的表面处理可以提高其外观质量和耐久性。
在设计中应考虑到表面处理的可行性和效果,如喷漆、喷涂、电镀等。
7.模具设计:模具设计是塑胶制品生产的关键环节。
模具的设计应符合产品的结构形状和尺寸要求,同时要考虑到成型工艺的要求,如浇口、顶针设计等。
此外,还需要注意模具的加工精度和使用寿命等因素。
总之,塑胶结构设计规范是保证塑胶制品质量和性能的重要保证。
通过合理的材料选择、结构设计、壁厚设计等,可以提高塑胶结构的强度、刚度和耐久性,从而满足不同的使用需求。
塑胶产品结构设计重点

塑胶产品结构设计重点一、材料选择塑胶产品的结构设计首先要考虑材料选择。
材料的选择直接关系到产品的性能、质量和成本,因此需要根据产品的具体要求和使用环境,选择适合的塑胶材料。
常见的塑胶材料有聚乙烯(PE)、聚丙烯(PP)、聚氯乙烯(PVC)、聚苯乙烯(PS)、聚酯(PET)等。
在选择材料时需要考虑产品的机械性能、耐热性、耐化学性、耐候性、电气性能、透明度等因素。
同时还需要考虑材料的加工性能,如流动性、热稳定性、收缩率等。
材料的选择不合理会导致产品性能不达标或加工工艺困难,因此需要在产品设计之前进行充分的材料筛选和试验。
二、结构设计塑胶产品结构设计主要包括外形设计和内部结构设计。
外形设计需要考虑产品的功能、美观和人机工程学等因素。
合理的外形设计可以提升产品的市场竞争力和用户体验。
内部结构设计需要考虑产品的强度、稳定性和装配性等因素。
合理的内部结构设计可以提高产品的性能和质量,减少生产和使用过程中的故障和损坏。
此外还需要考虑产品的可制造性和生产效率。
在进行结构设计时,需要采用CAD软件进行三维建模和仿真分析,以验证设计的可行性和优化设计。
三、模具设计塑胶产品的生产需要模具进行注塑成型。
模具设计是塑胶产品结构设计中非常重要的一部分,直接影响产品的质量和生产效率。
模具设计需要考虑产品的尺寸、形状和结构特点,选择合适的注塑工艺,确定模具的结构和加工工艺。
模具的设计要求高精度、高效率、长寿命和低成本,需要充分考虑模具的结构强度、冷却系统、顶出系统、塑胶流道等因素。
合理的模具设计可以提高产品的精度和表面质量,降低生产成本和生产周期。
四、加工工艺塑胶产品的加工工艺是塑胶产品结构设计的最后一步,直接影响产品的成型质量和效率。
常见的塑胶加工工艺有注塑成型、吹塑成型、挤出成型、压缩成型等。
在选择和优化加工工艺时,需要考虑产品的形状、尺寸、材料特性和生产要求等因素。
合理的加工工艺可以提高产品的质量和生产效率,降低生产成本和能耗。
塑胶件通用结构设计

肋骨:
肋骨高度与距离设计:
Rev.A
P41
Rev.A
肋骨:
厚薄肋骨胶位流动取向:
P42
Rev.A
肋骨:
肋的强度分析 - 常见的三种肋:
Surface appearance rib design
Structural reinforced resins rib design
Structural reinforced or foam resins rib design
Rev.A
P29
肋骨:
薄壁肋骨问题:
滞流冻结
这个模具是一出二,产品一边 大一边小。大的填充快,小的 慢,这就产生了滞流。如何改 善呢?最理想方法是一个模具 里的2个产品是相同的,但不现 实。或者说小产品加胶改变模 具结构,但也不现实. 最终方法 是通过改变流道截面积来调整 料流,OK,这样模具不改,材 料不改,参数基本不怎么改, 简便易行
P3
壁厚:
壁厚 VS 冲击强度:
Rev.A
P4
Rev.A
壁厚:
壁厚设计:
确定合适的制品壁厚是制品设计的主要内容之一。 1、 制品壁厚的作用 (1) 使制品具有确定的结构和一定的强度、刚度,以满足制品的使用要求。 (2) 成型时具有良好的流动状态(如壁不能过薄)以及充填和冷却效果(如壁不能太厚) (3) 合理的壁厚使制品能顺利地从模具中顶出。 (4) 满足嵌件固定及零件装配等强度的要求。 (5) 防止制品翘曲变形。 2 制品壁厚的设计 (1)基本原则--均匀壁厚。即:充模、冷却收缩均匀、形状性好、尺寸精度高、生产率高 。在满足制品结构和使用要求的条件下,尽可能采用较小的壁厚。 (2) 制品壁厚的设计,要能承受顶出装置等的冲击和振动。 (3) 在制品的连接固紧处、嵌件埋入处、塑料熔体在孔窗的汇合(熔接痕)处,要具有足 够的厚度。 (4) 保证贮存、搬运过程中强度所需的壁厚。 (5) 满足成型时熔体充模所需壁厚,既要避免充料不足或易烧焦的薄壁,又要避免熔体破 裂或易产生凹陷的厚壁。制品上相邻壁厚差的关系(薄壁:厚壁)为:
塑胶产品结构设计

塑料件结构设计要点 壁厚适当、均匀
壁厚适当、均匀
不同厚度的壁之间应该有过渡部分
不同厚度的壁之间应该有过渡部分
避免倒塌
避免倒塌
表面凹痕的消除或掩盖
要有足够的脱模斜度
塑料零件结构应对称
采用组合结构
减小有拐角零件的变形
避免细长杆受压
避免内切结构
避免内切结构
对于工业产品来讲,尤其是固定类灯具产品,但如果是环境条件充许的话(对有些产 品,特别是各种灰尘戒是粉尘环境下的产品,是丌能有装饰缝的),最好能设计装饰缝, 设计装饰缝是为了弥补塑胶件变形带来外观的缺陷,为了保证塑胶零件之间的外形相互配 合良好,装拆方便,需要在相互配合的地方设计止口不叉骨。止口不叉骨的设计多种多 样,建议止口不叉骨的形状推荐如图2、图3所示。特别注意减胶要均匀,渐变,丌要突 变,否则外观面易形成阴影。
很多,这里我们要特别注意的是前后壳间的联接扣位。推荐的扣位形式如下:
图3
图4
通用塑胶零件设计
图4所示结构一般做在后壳上,图5所示结构一般做在前壳上。特别主意减胶要均匀,渐 变,丌要突变。否则会在减胶处出现阴影戒缩水。
8、圆角的设计
塑角零件除了使用上要求采用尖角处外,其余所有转角处均应尽可能采用圆角过度,因塑胶 件的尖角处易产生应力集中,在受力戒冲击震动时会发生开裂现象。甚至在脱模过程中就发生开 裂。一般推荐加工圆角用如下原则:
1.4 缺胶、不饱模 塑胶熔体未完全充满型腔。
1.5 毛边、批锋 塑胶熔体流入分模面戒镶件配合面将发生锁模力足够,但在主浇道不分 流道会合处产 生薄膜状多余胶料为
1.6 烧焦 一般所谓的烧焦,包括制品表面因塑胶降解导致的变色及制品的填充末端焦黑的现象; 烧焦是指滞留型腔内的空气在塑料熔体填充时未能迅速排出(困气),被压缩而显著升 温,将材料烧焦。
塑胶模具结构设计

塑胶模具结构设计塑胶模具结构设计是制造业中至关重要的环节,它直接关系到产品的质量、生产效率和成本。
本文将围绕塑胶模具结构设计的基本原则、设计流程及注意事项进行详细阐述。
一、塑胶模具结构设计的基本原则1. 确保产品精度在设计塑胶模具时,要保证产品的尺寸精度和形状精度。
这要求设计师充分了解塑胶材料的收缩率、流动性等特性,并在模具设计中予以充分考虑。
2. 易于加工与装配模具结构应尽量简单,便于加工和装配。
复杂的设计不仅会增加制造成本,还可能影响模具的可靠性。
在设计过程中,要充分考虑模具零件的加工工艺性和装配顺序。
3. 高效生产塑胶模具结构设计应考虑生产效率,尽量减少生产过程中的辅助时间。
例如,通过优化流道设计、缩短冷却时间等措施,提高生产效率。
4. 安全可靠5. 维护方便模具在使用过程中难免会出现磨损、损坏等问题,设计时应考虑模具的维修便捷性,降低维护成本。
二、塑胶模具结构设计流程1. 分析产品结构在设计模具前,要对产品结构进行分析,了解产品的尺寸、形状、技术要求等,为模具设计提供依据。
2. 确定模具类型根据产品结构特点和生产要求,选择合适的模具类型,如单腔模具、多腔模具、热流道模具等。
3. 设计分型面分型面是模具闭合时,分离塑胶制品和浇注系统的界面。
设计分型面时要考虑产品的脱模斜度、外观质量等因素。
4. 设计浇注系统浇注系统包括主流道、分流道、浇口等部分,其设计直接影响到塑胶制品的质量。
设计时应关注流道截面积、长度、浇口位置等因素。
5. 设计冷却系统冷却系统对塑胶制品的质量和生产效率具有重要影响。
设计时要考虑冷却水路的布局、冷却水流量、冷却水温度等因素。
6. 设计顶出系统顶出系统的作用是在模具开模时,将制品从模具中顺利取出。
设计时要确保顶出力均匀、可靠,避免产品变形或损坏。
7. 绘制模具零件图及装配图三、塑胶模具结构设计注意事项1. 充分考虑塑胶材料的特性,如收缩率、流动性、热稳定性等。
2. 优化模具结构,提高生产效率,降低生产成本。
塑胶结构设计入门知识

塑胶结构设计入门知识一、材料选择1.功能要求:根据产品的使用环境和要求,选择具备必要性能的塑胶材料,如强度、耐热性和耐化学性等。
2.成本考虑:根据项目的预算和成本限制,选择经济合理的塑胶材料。
3.加工性能:考虑材料的流动性、收缩性和成型工艺,以确保能够实现设计要求并提高产能。
常见的塑胶材料有聚丙烯(PP)、高密度聚乙烯(HDPE)、聚氯乙烯(PVC)、聚苯乙烯(PS)和聚碳酸酯(PC)等。
二、设计原则1.强度设计:根据产品的负荷和使用条件,确定塑胶零件的强度要求,并通过合理的形状设计和增加必要的加强材料来满足强度要求。
2.塑胶件的收缩和变形:由于塑胶材料在冷却过程中会发生收缩,设计时应考虑材料的收缩率,以避免零件尺寸不准确或变形。
3.壁厚设计:过于薄的壁厚可能导致塑胶零件的强度不足,而过于厚的壁厚会导致零件成本上升。
因此,应根据功能需求和材料性能合理选择壁厚。
4.结构合理:设计时应避免尖角、槽口和开放式结构,以免成型困难或产生应力集中。
三、常见问题1.气泡:气泡通常由于材料中的挥发物未能完全释放导致的。
解决方法包括调整填料速度、增加干燥时间和使用适当的材料等。
2.缩孔:缩孔是由于材料在冷却过程中收缩不均匀而产生的。
可以通过增加填充压力或改变产品的几何形状来减少缩孔。
3.白痕:白痕是在成形过程中形成的表面瑕疵,通常是由于温度不均匀或材料与金属模具的摩擦导致的。
可以通过调整温度和增加模具通气孔来减少白痕。
4.裂纹:裂纹通常是由于过分的应力或不适当的设计造成的。
解决方法包括增加加强材料、改变设计形状和加强结构等。
总结:。
塑料产品结构设计资料

塑料产品结构设计资料目录一、零件壁厚 (1)二、脱模斜度 (4)三、圆角设计 (5)四、加强筋的设计 (7)五、支柱的设计 (8)六、螺丝柱的设计 (9)七、孔的设计 (10)八、止口的设计 (11)九、卡扣的设计 (13)十、反止口的设计 (18)零件设计必须满足来自于零件制造端的要求,对通过注射加工工艺而获得的塑胶件也是如此。
在满足产品功能、质量以及外观等要求下,塑胶件设计必须使得注射模具加工简单、成本低,同时零件注射时间短、效率高、零件缺陷少、质量高,这就是面向注射加工的设计。
现将详细介绍塑胶件设计指南,使得塑胶件设计是面向注射加工的设计。
一、零件壁厚在塑胶件的设计中,零件壁厚是首先考虑的参数,零件壁厚决定了零件的力学性能、零件的外观、零件的可注射性以及零件的成本等。
可以说,零件壁厚的选择和设计决定了零件设计的成功与失败。
1、零件壁厚必须适中由于塑胶材料的特性和注射工艺的特殊性,塑胶件的壁厚必须在一个合适的范围内,不能太薄,也不能太厚。
壁厚太小,零件注射时流动阻力大,塑胶熔料很难充满整个型腔,不得不通过性能更高的注射设备来获得更高的充填速度和注射压力。
壁厚太大,零件冷却时间增加,零件成型周期增加,零件生产效率低;同时过大的壁厚很容易造成零件产生缩水、气孔、翘曲等质量问题。
零件壁厚可根据材料的不同及产品外形尺寸的大小来选择,其范围一般为0.6~6.0mm,常用的厚度一般在1.5~3.0mm之间。
表1是常用塑料件料厚推荐值,小型产品是指最大外形尺寸L<80.0mm,中型产品是指最大外形尺寸为80.0mm<L<200.0mm,大型产品是指最大外形尺寸L>200.0mm。
表1 常用塑料件料厚推荐值(单位mm)2、尽量减少零件壁厚决定塑胶件壁厚的关键因素包括:1)零件的结构强度是否足够。
一般来说,壁厚越大,零件强度越好。
但零件壁厚超过一定范围时,由于缩水和气孔等质量问题的产生,增加零件壁厚反而会降低零件强度。
塑胶产品结构设计

塑胶产品结构设计要点1.胶厚(胶位):塑胶产品的胶厚(整体外壳)通常在0.80-3.00左右,太厚容易缩水和产生汽泡,太薄难走满胶,大型的产品胶厚取厚一点,小的产品取薄一点,一般产品取1.0-2.0为多。
而且胶位要尽可能的均匀,在不得已的情况下,局部地方可适当的厚一点或薄一点,但需渐变不可突变,要以不缩水和能走满胶为原则,一般塑料胶厚小于0.3时就很难走胶,但软胶类和橡胶在0.2-0.3的胶厚时也能走满胶。
2.加强筋(骨位):塑胶产品大部分都有加强筋,因加强筋在不增加产品整体胶厚的情况下可以大大增加其整体强度,对大型和受力的产品尤其有用,同时还能防止产品变形。
加强筋的厚度通常取整体胶厚的0.5-0.7倍,如大于0.7倍则容易缩水。
加强筋的高度较大时则要做0.5-1的斜度(因其出模阻力大),高度较矮时可不做斜度。
3.脱模斜度:塑料产品都要做脱模斜度,但高度较浅的(如一块平板)和有特殊要求的除外(但当侧壁较大而又没出模斜度时需做行位)。
出模斜度通常为1-5度,常取2度左右,具体要根据产品大小、高度、形状而定,以能顺利脱模和不影响使用功能为原则。
产品的前模斜度通常要比后模的斜度大0.5度为宜,以便产品开模事时能留在后模。
通常枕位、插穿、碰穿等地方均需做斜度,其上下断差(即大端尺寸与小端尺寸之差)单边要大于0.1以上。
4.圆角(R角):塑胶产品除特殊要求指定要锐边的地方外,在棱边处通常都要做圆角,以便减小应力集中、利于塑胶的流动和容易脱模。
最小R通常大于0.3,因太小的R模具上很难做到。
5.孔:从利于模具加工方面的角度考虑,孔最好做成形状规则简单的圆孔,尽可能不要做成复杂的异型孔,孔径不宜太小,孔深与孔径比不宜太大,因细而长的模具型心容易断、变形。
孔与产品外边缘的距离最好要大于1.5倍孔径,孔与孔之间的距离最好要大于2倍的孔径,以便产品有必要的强度。
与模具开模方向平行的孔在模具上通常上是用型心(可镶、可延伸留)或碰穿、插穿成型,与模具开模方向不平行的孔通常要做行位或斜顶,在不影响产品使用和装配的前提下,产品侧壁的孔在可能的情况下也应尽量做成能用碰穿、插穿成型的孔。
- 1、下载文档前请自行甄别文档内容的完整性,平台不提供额外的编辑、内容补充、找答案等附加服务。
- 2、"仅部分预览"的文档,不可在线预览部分如存在完整性等问题,可反馈申请退款(可完整预览的文档不适用该条件!)。
- 3、如文档侵犯您的权益,请联系客服反馈,我们会尽快为您处理(人工客服工作时间:9:00-18:30)。
第一章结构建模第一节结构建模简述1、建模就是构建模型,在产品结构设计中,建模指的是构建三维外观模型,通过专业的三维设计软件对看得见但摸不着的ID平面进行立体的呈现。
第二节产品模板介绍及自顶向下的设计理念1、自顶向下的设计理论1)首先创建一个顶级组件,也就是总装配图,后续工作是指围绕这个构建展开;2)给这个顶级组件创建一个骨架,骨架相当于地基,骨架在自顶向下设计理念中是最重要的部分,骨架做得好坏,直接影响后续好不好修改。
3)创建子组件,并在子组件中创建零件,所有子组件与零件装配方式按默认(缺省)装配;4)所有子组件主要零件参照骨架绘制,其外形大小与装配位置由骨架来控制;5)零件如需改动外形尺寸与装配位置,只需要改动骨架,重生零件即可。
第三节构建骨架模型1、构建骨架基本要求如下:1)外形要尽量贴近ID外形,外观曲面模具不走行位(行位又称滑块,是模具解决倒扣的机构),拔模角不小于3º;2)要求前壳能偏面(抽壳)不小于3mm,底壳不少于3mm;3)尺寸要方便修改,外形尺寸要能加长、加宽、加厚至少2mm,零件重生后而特征不失败;4)零碎曲面要尽可能少。
2、做骨架的基本步骤如下:1)参照ID图构建外形曲线;2)构建前壳曲面;3)构建底壳曲面;4)构建公共曲面;5)绘制前壳其他曲线;6)绘制底壳其他曲线;7)绘制左右前后侧面曲线。
第二章产品结构布局设计第一节前壳与底壳的止口设计1、止口分为公止口、母止口:2、止口的作用:1)限位。
防止壳体装配时错位、产生段差。
止口的作用是防止前壳朝外变形,同时防止前壳朝外变形,同时防止底壳朝内缩。
2)防ESD。
止口也称为静电墙,可以阻挡静电从外进入内部,从而保护内部电子元器件,所以在设计时尽可能保留整圈止口的完整。
3、止口设计的原则:1)公止口一般做在厚度薄的壳体上;2)母止口一般做在厚度厚的壳体上;4、公止口尺寸说明:1)尺寸a为公止口的高度,常用范围为0.60~1.00mm;2)尺寸b为公止口根部宽度,常用范围为0.60~0.80mm,最小尺寸要保证拔模后顶部最小宽度不少于0.5mm;3)尺寸c1、c2是公止口两侧拔模尺寸,2º~3º即可;4)尺寸d倒角尺寸,好装配,常用0.25~0.30mm。
5、止口的配合尺寸说明:1)尺寸A为配合面尺寸,为0.05mm;2)尺寸B为止口纵向避让尺寸,常用0.10~0.20mm,建议使用0.20mm,防止尺寸偏差时造成装配干涉;3)尺寸C是过渡圆角,主要是较为突变的圆滑过渡,也不能太大,防止装配时干涉;4)尺寸D为壳体外观面胶厚尺寸,应不小于0.80mm第二节前壳与底壳的卡扣设计1、卡扣的作用卡扣,又称扣位、卡扣位,作用与螺丝一样,也是起固定与连接作用,卡扣的主要作用是辅助螺丝固定壳体,整机结构固定仅靠螺丝柱是不够的,还必须要设计几个卡扣。
卡扣是通过塑料本身的弹性及卡扣结构上的变形来实现拆装的。
卡扣设计的基本原则如下:1)强度要够,不然拆装时容易损坏;2)扣合量要够,不然作用不明显;3)卡扣一定要有拆装的变形空间;4)整机卡扣一定要均匀;5)壳体结构强度弱的地方尽量布扣。
2、卡扣分公扣与母扣,分别做在两个不同的壳体上。
3、卡扣横向配合尺寸说明:1)尺寸A是公扣的宽度(又称卡扣宽度),此宽度可根据需要进行设计,尺寸建议在2~6mm 范围内,常用宽度尺寸是4mm;2)尺寸B是公扣与母扣两侧厚度,为保证卡扣有足够的强度,常用1.00mm,最少0.80mm;3)尺寸C是公扣与母扣两侧的间隙0.20mm;4)尺寸D是母扣另一侧的厚度,常用1.00mm,最少0.80mm;5)尺寸E是公扣与母扣另一侧的间隙0.2mm;6)尺寸F是母扣的宽度,根据公扣的宽度及与母扣的间隙自然得出7)尺寸G是母扣封胶的厚度0.30mm;4、卡扣纵向配合尺寸说明:1)尺寸a是卡扣的配合量(配合量),设计要合理,大了就很难拆,小了就起不到连接的作用。
尺寸建议在0.35~0.6mm范围内,常用扣合量尺寸是0.5mm;2)尺寸b是公扣的厚度,为保证足够的强度,常用1.00mm,最少0.8mm;3)尺寸c是公扣上表面要比底壳分模面低,不小于0.05mm,常用0.1mm。
主要作用就是利于模具加工与修整,以免模具因加工误差而造成卡扣上表面高出分模面,从而影响斜顶出模及壳体装配。
4)尺寸d是母扣与公扣的Z向(厚度方向)的间隙0.05mm,不能过大,以免卡扣没有起到作用。
5)尺寸e是母扣的厚度,为保证足够的强度,常用1.00mm,最少0.80mm。
6)尺寸f是母扣与公扣倒角边的避让间隙,不少于0.20mm。
7)尺寸g是母扣与公扣的避让间隙,不少于0.20mm。
8)尺寸h也是母扣与公扣的避让间隙,不少于0.20mm。
这个间隙设计时可留大点,扣合量不够时可以加胶。
9)尺寸i是母扣顶部的厚度,为保证足够的强度,常用1.00mm,最少0.80mm。
10)尺寸j是公扣的倒角,为方便装配,倒角尺寸为0.40mm *45º。
第三节卡扣与止口的关系1、正常布扣方法母扣布在公止口的壳上,同理,公扣就布在母止口的壳山;2、反扣母扣布在母止口的那一侧,就称为反扣。
设计反扣时注意把公扣两侧的公止口单边切掉不小于8.00mm,否则卡扣不能变形,成为死扣。
提示:设计卡扣时尽量按正常布扣方法,如果空间紧张,再设计反扣,反扣不仅有连接作用,还有反止口功能,缺陷就是拆装较困难。
反扣设计时要注意扣合量不能太大,先做到0.35mm,壳料第一次试模后可根据需要再调整。
第四节卡扣的变形空间设计1、壳体在拆装时,卡扣需要变形,绝大部分变形量是靠母扣变形来完成的。
所以在设计时,母扣一定要有变形的空间,而且变形空间一定要比扣合量大,最好大于0.20mm;如果母扣变形空间不够进行调整,可以将扣合量做小,但不要小于0.40mm也可以将母扣与公扣的配合间隙做到0.15mm;第五节卡扣掏胶掏胶的主要作用是防止胶位过厚造成壳料缩水而影响外观。
在不影响外观面缩水的情况下,可以不用掏胶。
第六节整机卡扣个数设计1、整机有6个螺钉的,布8个卡扣,布扣要均匀。
2、整机有4个螺钉,布8~10个扣,布扣要均匀。
提示:两个扣之间的距离最好控制在30mm左右,如果超过35mm,建议增加卡扣,如果距离都小于30mm,可适当减少卡扣的数量。
第七节螺丝塞结构设计1、螺丝塞设计要点1)螺丝塞主要作用就是遮丑与防尘;在设计时,尽量让所有螺丝塞共用;2)因为螺丝塞是圆的,在生产装配时容易转动,所以螺丝塞在结构设计时要做防呆结构,以免装错。
3)为防止螺丝塞表面高出壳体表面,螺丝塞表面比壳体表面低0.05~0.15mm,常用0.10mm;4)做螺丝塞结构时要特别注意预留螺丝帽的高度空间,螺丝帽的高度空间根据实物高度预留;第三章前壳组件结构设计第一节LCD屏限位结构设计1、前壳限位骨位1)LCD屏是通过FPC排线焊接在PCB上的,与PCB之间有四个小柱定位,为防止LCD屏在装配时容易掉落,LCD屏焊接好之后,在背面用少量双面胶固定在PCB板上;2)LCD屏是易碎物件,为了保护LCD屏,四周需要再壳体上限位。
限位是在前壳长骨位,与屏的四周间隙为0.1mm,限位骨位的高度至少是屏自身高度的三分之二;提示:限位LCD屏的骨位高度最高可以做到与堆叠主板Z向间隙为0.1mm,这样还可以起到Z向顶主板的作用。
2、LCD屏限位骨四个角缺口设计前壳切缺口就是给屏四个角一个振荡的空间,避免撞击到围骨。
切口长宽尺寸大小在3mm 左右。
3、限位骨位装配边倒角前壳限位LCD屏的边要倒直角C0.25~C0.3mm4、前壳视窗开口设计1)视窗就是LCD屏显示的区域,是从外观能直接看到的。
视窗开口就是避开视窗的开孔,视窗开口很重要,过大会造成泡棉太窄,起不到保护LCD屏的作用;过小会遮挡LCD屏的显示区域;2)前壳视窗开口比LCD屏的AA区单边大0.8~0.9mm;5、LCD泡棉设计1)LCD屏在受外力撞击时容易损坏,为了减少对LCD屏的撞击力度,更好地保护LCD屏,需要再屏的上表面加泡棉用来抗震缓冲,泡棉还可以用来防尘。
泡棉常用材料为PORON,厚度常用的有0.3mm(预压后0.2mm)、0.5mm(预压后0.3mm);2)泡棉离前壳上LCD屏限位骨位四周间隙为0.15~0.2mm,与A壳视窗开口四周间隙不小于0.3mm;第四章底壳组件结构设计第一节电池固定结构设计1、电池限位设计1)电池与壳体四周间隙为0.2mm;2)为了方便模具出模,需要再电池仓四周做拔模处理,拔模常用的角度1º~2 º,电池仓里外要拔模注意拔模的中性平面与拔模方向;3)由于电池在使用过程中是不能晃动的,以免机器掉电,所以在电池仓四周增加限位骨位,限位骨位与电池间隙为0.1mm,每个面的限位骨位不少于三个,装入边并做斜边设计;提示:为防止壳体缩水,筋位的料厚度不大于机壳料厚的一半;4)电池仓四周胶位厚度为0.9mm;2、电池Z向限位设计1)电池Z向与壳体间隙为0.1mm,壳体Z向胶位厚度应不小于0.8mm;2)如果电池Z向与壳体距离大于0.1mm,应在壳体上长骨位限位电池,骨位与电池的Z向间隙为0.1mm第二节喇叭结构设计1、喇叭限位设计喇叭在PCB堆叠板上没有固定,为防止喇叭移动,就需要再壳体上做结构限位,限位骨位四周与喇叭间隙为0.1mm,限位骨位的高度至少是喇叭自身高度的三分之二。
2、喇叭密封音腔设计1)密封音腔的泡棉常用材料是PORON,泡棉在壳体上要限位,泡棉单边宽度建议不少于1.2mm,与壳体四周间隙为0.1mm3、喇叭配合尺寸设计尺寸说明:1)尺寸A是喇叭的音腔高度,至少为0.8mm,否则声音效果差;2)尺寸B是壳体外观面胶厚,至少为0.8mm;3)尺寸C是封音腔的泡棉厚度,厚度常用的有0.5mm(预压后0.3mm)、0.8mm(预压后0.5mm)、1.0mm(预压后0.6mm)、1.2mm(预压后0.8mm)。
泡棉单边宽度不少于1.2mm4)尺寸D是喇叭与限位骨位的间隙为0.1mm;5)尺寸E是封音腔的骨位宽度为0.7mm;6)尺寸F是封音腔的骨位与限位喇叭骨位的距离,至少为0.6mm;7)尺寸G是限位喇叭骨位的宽度为0.7mm。
4、喇叭出音面积设计出音面积的大小直接影响声音的大小,过小会造成播放声音小与音质差,过大会造成喇叭声音不集中、音质差。
出音面积设计时按照喇叭规格书要求设计,如果没有规格书,出音面积建议做到喇叭本身面积的12%~15%;5、喇叭防尘网设计防尘网的作用就防止灰尘进入壳体内部,防尘网材料常用两种,一种是尼龙网,一种是无纺布。
防尘网厚度为0.1mm,通过双面胶固定于壳体上。
提示:防尘网与泡棉可做成一体,就是在泡棉上贴一层防尘网,这样更方便装配。