邯钢高炉典型料制的实物模型模拟及径向参数解析
邯钢1号高炉稳定生产实践

甘 肃 冶 金GANSU METALLURGY第 43 卷第 6 期2021 年 12 月Vol.43 No.6Dec. ,20211引言近年来全国环保形势日益严峻,作为传统排放大户,钢铁企业面临的环保压力也越来越大。
钢铁 的生产流程长,污染因素多,其中尤以铁前系统为 甚。
如何适应当前新的环保形势,克服恶劣的外围 条件,保持高炉稳产,成为炼铁工作者面临的重要问题。
作为邯钢投产最早的3 200 m 3大高炉,1号高炉对自身和外围存在的问题逐一解决,减少了环保 的影响,基本保持了高炉稳定生产。
2环保改造为了实现超低排放,适应当前严峻的环保形势,1号高炉自2016年开始陆续对生产设备和工艺进行了改造和优化。
首先,对除尘系统进行升级,一方面对现有除尘能力进行优化,包括加强除尘设备点检,清理管道积灰和补焊管道漏点。
另一方面新建了集中仓除尘文章编号:1672-4461( 2021) 06-0020-04邯钢1号高炉稳定生产实践李子亮,李铭,程海龙(河钢集团邯钢公司,河北邯郸056003)摘 要:介绍了当前环保形势下高炉生产面临的问题,邯钢1号高炉通过解决外围影响因素并结合高炉内部调剂,减少了环保给高炉带来的影响。
具体包括环保设备改造、克服恶劣的原料条件、减少休风复风颗粒物排放并快速恢复达产,这些措施不但减少污染满足环保要求,同时保证了高炉的稳定生产。
关键词:高炉;改造;原料;限产;环保中图分类号:TF54 文献标识码:AStable Production Practice of Hansteel No.1 Blast FurnaceLI Zi-liang , LI Ming , CHENG Hai-long(HBIS Group Hansteel Company , Handan 056003 , China )Abstract : The problems faced by blast furnace production is introduced under the current environmental protection situa tion. Hansteel No.1 blast furnace reduces the impact of environmental protection by solving the external influence factorsand combining the internal adjustment of the blast furnace. These measures include environmental protection renovation of the equipment , overcoming the poor raw material conditions , reducing the emission of particulate matters in blowing-downand blowing-in , and quickly returning to production. These measures not only reduce pollution , meet the environmental pro tection requirements , and guarantee the stable production of blast furnace.Key Words : blast furnace ; renovation ; raw material ; production limitation ; environmental protection器,增加除尘能力。
高炉布料模型的开发与应用
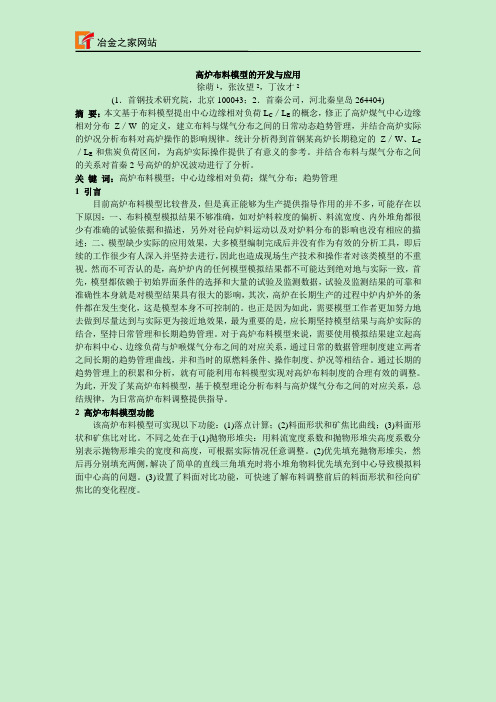
高炉布料模型的开发与应用徐萌1,张汝望2,丁汝才2(1.首钢技术研究院,北京100043;2.首秦公司,河北秦皇岛264404)摘要:本文基于布料模型提出中心边缘相对负荷L C/L E的概念,修正了高炉煤气中心边缘相对分布Z/W的定义,建立布料与煤气分布之间的日常动态趋势管理,并结合高炉实际的炉况分析布料对高炉操作的影响规律。
统计分析得到首钢某高炉长期稳定的Z/W、L C /L E和焦炭负荷区间,为高炉实际操作提供了有意义的参考。
并结合布料与煤气分布之间的关系对首秦2号高炉的炉况波动进行了分析。
关键词:高炉布料模型;中心边缘相对负荷;煤气分布;趋势管理1 引言目前高炉布料模型比较普及,但是真正能够为生产提供指导作用的并不多,可能存在以下原因:一、布料模型模拟结果不够准确,如对炉料粒度的偏析、料流宽度、内外堆角都很少有准确的试验依据和描述,另外对径向炉料运动以及对炉料分布的影响也没有相应的描述;二、模型缺少实际的应用效果,大多模型编制完成后并没有作为有效的分析工具,即后续的工作很少有人深入并坚持去进行,因此也造成现场生产技术和操作者对该类模型的不重视。
然而不可否认的是,高炉炉内的任何模型模拟结果都不可能达到绝对地与实际一致,首先,模型都依赖于初始界面条件的选择和大量的试验及监测数据,试验及监测结果的可靠和准确性本身就是对模型结果具有很大的影响,其次,高炉在长期生产的过程中炉内炉外的条件都在发生变化,这是模型本身不可控制的。
也正是因为如此,需要模型工作者更加努力地去做到尽量达到与实际更为接近地效果,最为重要的是,应长期坚持模型结果与高炉实际的结合,坚持日常管理和长期趋势管理。
对于高炉布料模型来说,需要使用模拟结果建立起高炉布料中心、边缘负荷与炉喉煤气分布之间的对应关系,通过日常的数据管理制度建立两者之间长期的趋势管理曲线,并和当时的原燃料条件、操作制度、炉况等相结合。
通过长期的趋势管理上的积累和分析,就有可能利用布料模型实现对高炉布料制度的合理有效的调整。
高炉操作参数优化数学模型

高炉操作参数优化数学模型
郝晓静;杜钢
【期刊名称】《材料与冶金学报》
【年(卷),期】2002(001)002
【摘要】采用数学规划论和最优化方法,建立高炉操作参数优化数学模型.通过对某钢厂实际生产数据的统计分析,得到了焦比、焦炭负荷、高炉利用系数等参数的多元线性回归方程,并通过计算标准回归系数确定各因素对目标函数值的影响程度和自变量与因变量的正、负相关性,调整主要参数,使目标函数接近或达到最优值.【总页数】4页(P120-123)
【作者】郝晓静;杜钢
【作者单位】东北大学,材料与冶金学院,辽宁,沈阳,110004;东北大学,材料与冶金学院,辽宁,沈阳,110004
【正文语种】中文
【中图分类】TF538.1
【相关文献】
1.新钢8号高炉提高炉顶压力的操作实践 [J], 朱先强;宫祥哲
2.基于多传感器的高炉炼铁操作参数优化 [J], 崔桂梅;侯佳;高翠玲;陈智辉
3.基于神经网络和遗传算法的高炉喷煤操作参数优化 [J], 查烽炜;刘琪
4.基于数据挖掘与清洗的高炉操作参数优化 [J], 刘馨;张卫军;石泉;周乐
5.计算机辅助高炉优化操作中的数学模型及软件 [J], 李吉鸾;刘祥官;徐伟宣
因版权原因,仅展示原文概要,查看原文内容请购买。
高炉炉缸铁水流场数值模拟

高炉炉缸铁水流场数值模拟
王平;别威
【期刊名称】《浙江冶金》
【年(卷),期】2011(000)004
【摘要】铁水环流是造成炉缸“蒜头状”侵蚀的主要原因,而导致铁水环流行程主要是由于炉缸内的死料柱引起的.本文以流体力学有关理论为基础,建立炉缸炉底三维流体数学模型,应用FLUENT软件,针对高炉炉缸中不同死料柱位置、状态及出铁口尺寸对炉缸内铁水流动的影响进行研究.结果表明:死料柱有较小的浮起时造成炉底铁水流量较大对炉底产生较强的侵蚀.当中心死料柱尺寸大时自由铁水区的铁水流速较快,反之较慢.当出铁口直径增大时,铁水的质量流量增大,炉缸底部的铁水环流明显增大.
【总页数】7页(P22-28)
【作者】王平;别威
【作者单位】安徽工业大学冶金与资源学院马鞍山243002;安徽工业大学冶金与资源学院马鞍山243002
【正文语种】中文
【相关文献】
1.高炉炉缸内不同死料柱状况对铁水流场的影响
2.高炉炉缸内铁水流动特性的物理模拟
3.基于Fluent的高炉炉缸铁水流动模拟软件
4.高炉炉缸铁水环流速度影响因素的水模试验
5.高炉炉缸内铁水流动物理模拟研究
因版权原因,仅展示原文概要,查看原文内容请购买。
轧制参数计算模型及其应用(一)

轧制参数计算模型及其应用(一)轧制参数计算模型及其应用概述轧制参数计算模型是一种用于计算轧机工艺参数的数学模型,通过模拟折弯、伸拉和扭转等过程,计算出轧制板材的几何形状和力学性能。
该模型在轧机设计、质量控制和工艺优化等方面具有广泛应用。
模型构建材料模型轧制板材的力学性能由材料性能决定,因此必须首先确定材料模型。
常用的材料模型有等效应力模型和本构模型。
轧制力学模型轧制力学模型可分为几何模型和力学模型。
几何模型是指轧制板材的形状和尺寸模型,力学模型是指轧制板材的应力、应变和塑性变形模型。
数值模拟方法常用的数值模拟方法有有限元法、边界元法和有限差分法。
其中,有限元法是最常用的方法,具有高精度、高效率和高稳定性等优点。
应用轧机设计轧机设计中需要确定轧制力学参数,以控制轧制板材的形状和力学性能。
轧制参数计算模型可以提供合理的轧制参数,以满足不同尺寸、材质和工艺需求。
质量控制轧制板材的质量受多种因素影响,如轧制力、轧制速度和冷却方式等。
轧制参数计算模型可以提供轧制板材的几何形状和力学性能参数,以确定轧制质量是否符合要求。
工艺优化轧制工艺中的轧制参数可以影响轧制板材的形状、尺寸和力学性能。
轧制参数计算模型可以提供不同轧制参数对轧制板材性能的影响程度,以优化轧制工艺,提高生产效率和产品质量。
结论轧制参数计算模型是一种重要的数学模型,可以为轧机设计、质量控制和工艺优化等方面提供重要参考,促进轧制生产技术的发展和进步。
发展方向随着轧制技术的不断发展和进步,轧制参数计算模型也在不断完善和提高。
未来,轧制参数计算模型的发展方向主要包括以下几个方面:•更精确的材料模型,使得轧制参数计算模型能够更好地预测轧制板材的性能特征;•更高效的数值计算方法,以提高计算效率并降低计算成本;•精细化的轧制力学模型,以更真实地模拟轧制板材的变形和应力分布;•基于机器学习和人工智能的轧制参数计算模型,使得模型能够“自学习”,更好地适应复杂的轧制工艺。
高炉回旋区的机理分析及三维数值模拟

收稿日期:2004208230基金项目:2001年山东省科学技术发展计划项目(012050107);2002年山东省自然科学基金项目(Y2002F19);2003山东省经贸委重大技术创新项目(鲁经贸授字2003[182])作者简介:陈举华(1948-),女,山东荣成人,教授.主要研究方向为多目标模糊优化/系统模糊可靠性/虚拟样机及环境.E 2mail :xtgc —sd @ 文章编号:167223961(2005)0120027205高炉回旋区的机理分析及三维数值模拟陈举华,沈学会,郭术义,张丽丽(山东大学 机械工程学院, 山东 济南 250061)摘要:阐述了高炉回旋区运动及反应机理,建立了模拟回旋区的三维综合模型,模拟了回旋区内物理过程和化学过程,得到了焦炭颗粒的速度分布、回旋区内的温度分布和高炉风口燃烧带的温度及煤气成分变化.冷态模拟结果与实验结果基本一致,预报的温度分布符合实际工况.关键词:高炉回旋区;气粒两相流;数值模拟中图分类号:TH122 文献标识码:AThe analysis of mechanism and research on32D numerical simulation of race w ayCHEN J u 2hua , SHEN Xue 2hui , GUO Shu 2yi , ZHAN G Li 2li(School of Mechanical Engineering , Shandong University , Jinan 250061, China )Abstract :The mechanisms of movement and reaction in raceway of blast furnace was investigated ,an integrated 32D model for raceway of blast furnace was built.The model was used to simulate both the physical and chemical process in the raceway.The simulation gave the velocity distribution of gas and particle ,the temperature distribution in raceway and the changes in temperature and gas composition in blast ignition belt.The prediction results are in agreement with the experimental results ,the pre 2dicted distribution of temperature is in accord with practice.K ey w ords :raceway of blast furnace ;gas 2particle flow ;numerical simulation0 引言高炉生产所需热量和还原剂来自回旋区,回旋区机理的研究及模拟与炉料和煤气流的合理分布、高炉生产最佳化密切相关.过去由于焦炭运动或燃烧机理不明晰而操作不当所致的“结瘤”、“管道”等冶炼事故,经济损失巨大.钢铁是国民经济的基础,炼铁又是源头,为提高高炉生产水平,国内外学者作了不懈的努力,如羽田野道春等人建立了回旋区气体力学模型【1】;B.K.杜尔诺夫等建立了回旋区动力学模型【2】;福武刚等提出了气、固、液态的平衡关系【3】.但由于问题本身的复杂和各种条件的限制,至今还未建立起模拟高炉回旋区运动和燃烧全过程的综合数学模型.模拟回旋区的关键问题在于其数模要全面反映焦炭运动过程和燃烧过程的相互影响,彼此协调.目前常用的模型普遍偏重一方面,忽略另一方面,这一顾此失彼的建模方法模拟效果较差.所 第35卷 第1期 Vol.35 No.1 山 东 大 学 学 报 (工 学 版)J OURNAL OF SHANDON G UN IV ERSITY (EN GIN EERIN G SCIENCE )2005年2月 Feb.2005 以建立模拟回旋区的综合数学模型尤为迫切.近年来,两相湍流及其相互作用成为国际上的研究前沿和热点,湍流气粒两相流理论的发展也为进一步改进回旋区研究方法提供了新的思路,基于两相流和燃烧学理论建立了综合考虑两个过程的高炉回旋区三维综合数学模型,并利用冷态实验对模拟结果进行了验证,以便应用于工程实践.1 回旋区的数值模拟回旋区内的物理、化学变化十分复杂,完整而准确的了解其机理是建立数学模型的前提,以下对回旋区机理作了系统的分析.1.1 回旋区的机理研究随着冶炼技术的不断进步,高炉逐渐趋于大型化,鼓风速度已提高到100~200m/s,这时风口前的焦炭受到强烈的流体动力作用,在风口前缘形成了焦炭作回旋运动的空腔,我们把这个空腔称为高炉回旋区【4】.回旋区内的焦炭运动是在气、固、液三相流中进行的,在高温鼓风的作用下,它在运动中不断进行着燃烧和气化反应,从而确保高炉上部炉料不断下降和高温还原煤气的不断产生.整个回旋区内由于焦炭和煤气的运动和焦炭的燃烧反应,物理过程和化学过程并存并且相互耦合.焦炭颗粒、煤气流之间的动量传递和二者之间的运动过程及相互作用构成了回旋区内的物理过程;同时焦炭在运动中还进行着燃烧反应,并与鼓风带进来的气流进行着质量、热量的传递.整个燃烧以及传质传热过程就构成了回旋区内的化学过程.两个过程相互影响,互相关联,气流运动通过强化混合而影响着平均化学反应速率,同时化学反应放热过程又影响着气流,回旋区正是物理过程和化学过程相互耦合作用而产生.1.2 回旋区三维数学模型目前常用的回旋区数学模型都是建立普通的物理/化学守恒方程,实际生产中,炼钢和炼铁炉中的反应、炉子和燃烧室内燃烧都是十分复杂的湍流条件下完成的.所以,基于气粒两相流和燃烧学理论,考虑气相和颗粒相的速度差别和相互作用,建立了反应回旋区多过程机理的三维综合数学模型,增强模拟效果,以利于指导工程实践.由于文中引用符号较多,特将所用符号列表如下,以助读者阅读.dΦ———风口直径,m;B———综合热鼓风的动能与在风口燃烧的焦炭流势能有关的一个参数;KΦ———回旋区长度与高度的形成参数;m0,n———从实验数据统计获得的参数;V g———每分钟鼓风量,m3/min;ρg———热风密度,kg/m3;T g———热风温度(开氏温度),K;P0,P g———标准大气压和热风压力,Pa;W,φ———鼓风中的含氧和水汽量,g/m3;C K———焦炭中的含炭量,%;D———天然气用量,m3;h———回旋区的高度,m;g———重力加速度,N/kg;<———求解变量,Γ<———传输系数;S<,S k<———气相和两相相互作用的源项; T———温度;T0=273K;u,v,w———速度分量,m/s;k,ε———湍流动能,J;湍流动能耗散率,%;ρ———密度,kg/m3;μ———动力粘性系数;τ———剪应力,N;n———颗粒数密度,n/m3;Y———质量分数,%;ω———反应率,kg/(v3・s);E———活化能,J;N———颗粒数总通量,kg/(m2・s);Q———热量,J.1.2.1 气粒两相流和焦炭燃烧的双流体-轨道模型 在有反应的两相流动和燃烧的双流体-轨道模型中,颗粒数密度及速度由欧拉坐标系下的连续及动量方程组来求解.颗粒由于水分蒸发和焦炭燃烧等引起的质量和温度变化由拉氏坐标系下的常微分方程组得到.气相时平均连续、动量、能量方程组以及k,ε方程可写成如下通用形式,详细表达式见文献[5].5t(ρ<)+5x j(ρv i<)=5x j(Γ<5<x j)+S<+S k<(1)颗粒相的时平均连续及动量方程组为 28 山 东 大 学 学 报 (工 学 版)第35卷 5n k 5t+55x j(n k v kj)=-55x j(n′k v′k)(2)55t(n k v ki)+55x j(n k v kj v ki)=n k g i+1τrk[n k(v i-v ki)-n′k v′kj]+Sm k(v i-v ki)- 5x j(n k v′kj v′kj)(3)1.2.2 焦炭颗粒燃烧模型在模型中,由于水分蒸发和焦炭的燃烧引起的颗粒质量和温度变化以及颗粒的热传递由一组普通的微分方程和一系列的算术表达式来定义.颗粒的质量变化率可由以下代数式来确定【6】.m k= m w+ m h,(4) m w=πd k N uDρln1+Y ws-Y w g1-Y ws,(5)Y ws=B w exp-E wR T k,(6)m k=πd p N uDρln m s/ m k-Y sm s/ m k-Y ss,(7)m s=πd2pρY ss B s exp-ER T k,(8)m h=∑ m s,(9)对颗粒温度变化用下列拉格朗日坐标系内能量方程,计算颗粒质量和温度变化沿着颗粒的流线来进行.m k C pk d T kd t=πd2kεσ(T4-T4k)+m k C pk(T-T k)×[exp(m p C pk/(πd p N uλ))-1]-1-m w L w+m h Q c.(10) 1.2.3 焦炭颗粒质量湍流、气相燃烧和辐射传热模型由于炉内流动为弱旋流动,应用k-ε-kp2相湍流模型.颗粒雷诺应力、颗粒质量流表达式为-n′k v′k=D k 5n k5x j,(11)-v′kj v′ki=v k 5v kj5x i+5v ki5x j,(12)kp方程为5t(n k k k)+5x k(n k v k k k)=5 5x k(μpσp 5k k5x k)+G kk-n kεk(13)其中,G kk=μk5v ki5x k5v k5x i5v ki5x kμk=cμkρk k2p/|εp|εp=-1τr+m km k[(v′i v′ki-2k k)-v i-v kin kυkσk5n k5x i](14)对于挥发分及CO气相燃烧子模型应用PDF输运方程模拟模型【7】.辐射传热子模型应用离散坐标辐射传热模型(discrete2ordinate DO模型)【8】.1.3 数值解法及边界条件对气相和颗粒相方程组采用混合格式进行差分,采用p-v修正的SIMPL E算法,TDMA迭代逐行求解.将计算区域分为24×25×40个网格进行计算.为了解决计算中大数据量和计算时间的矛盾,采用不同的空间步长区分“宏观”、“微观”网格;采用不同的时间步长区分“宏观”、“微观”计算.采用冷态实验中的初始数据作为数值计算的初始条件.对气相取均匀进口条件,进口网格给定均匀速度u,v,w,T,Y S并给定K in,εin;出口取压力出流条件;壁面处气相为无滑移条件,颗粒相法向速度分量为0;其它速度分量梯度和质量浓度梯度为0.2 试验装置和测量方法为了验证回旋区三维模型,依据相似与模化理论,在一个缩小的冷态模型中采用三维激光相位多普勒分析仪(32Dimensional Laser Phase Dopper Ana2lyzer,PDA)试验测量系统对气粒两相流动作了测量.实验系统如图1所示.本试验按照相似与模化原理,把实际高炉回旋区的焦炭颗粒大小范围换算成玻璃微珠的粒径范围,用玻璃微珠来模拟焦炭颗粒的行为.本试验采用了35目(平均粒径为400~600μm)的玻璃微珠,球形度为95%,折射率为1.5,密度为2400kg/m3.每个测点采样个数为1500,采样时间限时20s. 常温、常压下的空气在大功率风机的驱动下带动颗粒发生运动.气体与颗粒的流动为强迫流动,故忽略Fr(傅鲁德)准则,采用Re(雷诺)准则、Eu(欧拉)准则来设计试验测试台,图2所示为试验中测量截面部分示意图,并利用彼此相似现象具有相同准则关系的π定理,把试验数据推广到实际中,这样既 第1期陈举华,等:高炉回旋区的机理分析及三维数值模拟29保证了试验与实际高炉回旋区的相似性又保障了试验结果的可靠性.1:出风口;2:调节阀;3:试验测试台;4:石英玻璃窗;5:接受单元;6:数据处理机;7:信号处理器;8:光电转换单元;9:激光器;10:激光分光器;11:发射单元;12:进风、进料口.图1 PDF 实验系统简图Fig.1 Sketch of PDAsystem图2 测量截面简图Fig.2 Sketch of metrical section3 冷态两相流动模拟与实验结果对照及热态模拟结果预报 冷态数值模拟得到了气粒两相的速度分布.热态数值模拟得到了回旋区内温度分布、风口轴线方向上燃烧带内的温度及煤气成分分布.冷态实验得到了气粒两相的速度分布.3.1 焦炭颗粒的速度结果对照及讨论图3,图4和图5分别给出了平行和垂直风口方向以及主流方向上粒子的三维速度模拟与实验结果的对照(图中的负值与PDA 的光学性质有关).模拟和实验结果吻合良好.由图3可以看出,平行风口方向上,气体的主流速度从边缘到风口方向逐渐减小.也就是实际高炉内气流主要从回旋区的后方沿远离风口的方向向上流动,这与实际工况相符合.由图4可见垂直风口方向上,主流速度变化较大,在中心和边缘速度都较大,从中心到边缘,轴向速度逐渐减小,垂直轴向速度数值一直变化不大,但方向不断变化,这主要由于气流中的微小涡流的影响.图5是颗粒在气体主流方向的速度分布.测量点从低到高,主流速度由大变小.3.2 焦炭颗粒的速度矢量分布图6为粒子的三维速度矢量图.由图可见,越靠近风口轴线,速度越高,边缘速度迅速降低,最边缘地带速度增高是由于粒子与壁面的碰撞所致.可以看出在靠近漩涡中心的地方,气流的主运动速度梯度较大,如果这一点符合实际工况,风口的速度脉动将有助于回旋区的焦炭颗粒扩散燃烧.平行风口方向测量点(—主流速度U ;----垂直轴向速度W ;……平行轴向速度V )图3 平行风口轴向粒子三维速度分布Fig.3 32D velocity distribution of particles in the directionparallell to twyer axis垂直风口方向测量点图4 垂直风口轴向粒子三维速度分布Fig.4 32D velocity distribution of particles in the directionperpendicular to twyeraxis主流方向测量点图5 主流方向粒子三维速度分布Fig.5 32D velocity distribution of particlesin main direction 30 山 东 大 学 学 报 (工 学 版)第35卷 图6 三维粒子速度矢量分布图Fig.6 Distribution of 32D velocity vectors of paricles3.3 热态模拟结果讨论图7为计算得到的回旋区内温度大体分布,采用不同的步长后,模拟计算结果更趋合理.图8为风口轴线方向上温度和气体的分布,图中可以看到回旋区的“燃烧焦点”,这与用风口取样器从高炉燃烧带的取样数据是一致的.图7 回旋区内的温度分布示意图Fig.7 Distribution of temperaturein raceway图8 风口燃烧带的气体温度和成分变化Fig.8 The changes of gas composition and temperaturein blast ignition belt4 结论(1)分析了回旋区内的物理及化学过程,建立了高炉回旋区三维综合数学模型;(2)模拟结果给出了炉内三维气粒两相流动和焦炭燃烧多物理、化学过程的详尽信息.(3)冷态两相流动实验测量结果表明数模冷态两相流场的预报结果是合理的;热态模拟预报得到了回旋区以及燃烧带的温度分布.参考文献:[1]K AMBARA K.Dissection of blast furnace and their insidestate[J ].Tetsu 2to 2Hagane.1972,58:1023.[2]DURNOV B K.Heat and mass transfer in layer and chan 2nels[J ].Collection of Research Paper of the All 2union Sci 2entific Research Institute of Metallurgical Thermotech 2nology.1970,2:23240.[3]福武刚.高炉回旋区和炉缸工作文集[M ].北京:冶金工业出版社,1986.FU W G.Blast furnace raceway and hearth symposium [M ].Beijing :Metallurgy Industry Press ,1986.[4]秦民生,杨天钧.炼铁过程的解析与模拟[M ].北京:冶金工业出版社,1991.Q IN M S ,Y AN G T J.Analysis and simulation of pudding process[M ].Beijing :Metallurgy Industry Press ,1991.[5]ZHOU L X.Theory and modeling of turbulent gas 2particleflows and combution[M ].Beijing :Science Press ,19931[6]ZHOU L X ,L IL ,L I R X.Simulation of 32D gas 2particleflows and coal combustion in a tangentially fired furnace us 2ing a two 2fluid 2trajectory model [J ].Power Technology ,2002,125:22622331[7]SMOO T L D ,SMITH P J ,ABBAS A bust [J ].Sci and Technol ,1998,158:5223.[8]周力行.多相湍流反应流体力学[M ].北京:国防工业出版社,2002ZHOU L X.Dynamics of multiphase turbulent reactingfluid flows[M ].Beijing :National Defence Press ,2002.(编辑:陈燕) 第1期陈举华,等:高炉回旋区的机理分析及三维数值模拟31。
基于计算流体动力学的高炉数学建模与仿真

0 引言在矿料下降的过程中,铁水和炉渣逐渐形成,从而发生固态和液态之高炉是一种多相态物质相互作用的化学反应容器,它被称为化工领域间的传热。
固态-液态之间的热传递系数通过下面的公式计算,它适用于最复杂的冶金反应器之一[1]。
为了更好地控制和改进高炉的生产过程,建立高炉的数学模型是非常必要的。
随着计算机技术的发展,更大的矩阵得以解决,模型的控制方程可以采用偏微分方程来描述,大量实用的高炉模型被开发[2]。
其中,基于计算流体力学的高炉数学模型能够详细分析通过上述一系列公式,可建立高炉内相态之间的基本传热数学描述气炉内状态并且精确预测高炉的操作性能,得到了更广泛的发展,成为目前态和固态间的动量传递可通过Ergun 公式[8]导出:国内外研究和应用的热点[3]。
为了准确地仿真高炉内部状态,本文对炉内相态间的动量、质量传输现象进行了数学描述[4],建立了化学反应模型和高炉整体二维动态模 1.3 化学反应的描述型。
确立了数学模型的数值求解方法,完成了对高炉动态过程的仿真,仿高炉的实质是一种化学反应容器,最核心的内容就是化学反应的发真结果较好地反应了实际工况,为高炉自动化的实现打下基础。
生。
高炉内的主要化学反应可以归为三类:还原反应,碳的气化反应和水1 高炉数学模型煤气变换反应。
其中铁矿石内氧化铁的还原反应是最重要的化学反应。
为高炉过程和其他现象一样都必须遵循自然规律(质量守恒定律、动量了研究铁矿石的还原机理,我们采用三界面未反应核模型理论。
此理论认守恒定律和能量守恒定律),可以用流体力学和传热学的基本方程来描述为还原反应只发生在界面上,随着反应的一步步深入,未反应部分向中心[5]。
方向收缩,最后形成一个未反应的核心[9]。
由于氧化铁分级反应的特1.1 基本方程点,在一个矿球反应到一定程度的时候,就会形成明显的三界面,四层,模型的控制方程就是流体流动的质量、动量和能量守恒方程,采用一由外向内分别是:Fe-FeO-Fe3O4-Fe2O3。
- 1、下载文档前请自行甄别文档内容的完整性,平台不提供额外的编辑、内容补充、找答案等附加服务。
- 2、"仅部分预览"的文档,不可在线预览部分如存在完整性等问题,可反馈申请退款(可完整预览的文档不适用该条件!)。
- 3、如文档侵犯您的权益,请联系客服反馈,我们会尽快为您处理(人工客服工作时间:9:00-18:30)。
1 摘 要 本文利用高炉无钟布料实物模型,依据相似理论模拟邯钢5#高炉(2000m3)目前使用的两种典型装料制度,解析了两种料制的料面形状、径向矿焦比、径向透气性分布等参数,为优化高炉装料制度,提供了一种直观量化的研究手段。 关键词 邯钢5#高炉;料制;实物模型;径向参数分析
Physical model simulation and analysis of radical parameters on typical charging system of Han Steel Blast Furnace Abstract in this paper ,according to BF no-bell charging physical model and similarity theory simulating the two typical current changing systems of Han Steels's BF5 ,the burden surface 、radial ore coke ratio 、radial permeating distribution and other parameters are analyzed which provides an intuitive and quantitative research means for optimizing the BF charging system. Keywords Han Steels's BF5;charging system; physical model; radial parameter analysis.
前言 无钟炉顶在高炉布料方面的优越性已被炼铁界广泛认知,虽经30年的发展和研究,时至今日,无钟布料这一技术在高炉操作方面仍有较大潜力可挖。深刻认识这一技术并应用好其优越的布料特性,对高炉改善操作指标、节能降耗、保持顺行长寿仍有十分重要的意义。
图1 按邯钢5#高炉(2000m3)缩小的实物布料模型 目前的高炉操作者主要通过监控十字测温、炉顶煤气分析等间接手段,来掌控煤气流的变化。对于炉料在炉内的分布,操作人员仍主要通过理论知识和开炉时测得料面形状及操作经验估计炉料的分布情况。如果高炉操作人员能获得所布料制的直观量化的料面形状,操作更加有的放矢,就会获得更好的操作指标。 本文通过按邯钢5#高炉(2000m3)缩小的实物布料模型,模拟生产现场目前使用的典型料制,并利用实物模型试验的便利条件,解析了两种料制的料面形状、径向矿焦比分布、径向透气性分布等参数,为高炉操作者提供了直观、量化的料制分布参数,对于推行高炉操作精细化,提供了一种有力的技术支撑。 实物布料模型见图1,模型依据5#高炉炉顶设备及炉身尺寸按10:1比例缩小,模型形状为棱台型,模型的外围用透明玻璃制作,便于测量和观察,所用试验炉料为现场实际的炉料按一定比例缩小的炉料,缩小的比例符合相似定理的要求,所以模拟布料操作有针对性和适用性[1]。 1 邯钢5#高炉目前使用的两种典型料制
1.1 第一种料制 2
邯钢5#高炉目前使用第一种料制如下,本文称此料制为1#料制: O1234533332 C123456322222
矿批:42t;焦批:9t;料线:1.3m 本模拟试验采用布料角度不变,矿批根据相似定理确定为: 矿批10kg ;焦批:2.1kg;料线:13cm 1#料制各角度的布料量见表1。 表1 1#料制各角度的布料量 α0 48 45.5 42.5 39.5 35.5 17 圈 O 2 3 3 3 3 11圈
C 2 2 2 2 2 3 13圈
O(kg) 1.44 2.14 2.14 2.14 2.14 C(kg) 0.324 0.324 0.324 0.324 0.324 0.486 1.2第二种料制 邯钢5#高炉目前使用第二种料制,本文称此料制为2#料制: O1234522333 C123456122222
矿批:53.5t;焦批:10.9t;料线:1.2m 本模拟试验采用布料角度不变,矿批根据相似定理确定为: 矿批10.45kg;焦批:2.129kg;料线:12cm 2#料制各角度的布料量见表2。 表2 2#料制各角度的布料量 α0 50 48 46 43.5 41 37 圈 O 3 3 3 2 2 13 C 2 2 2 2 2 1 11 O(kg) 2.41 2.41 2.41 1.61 1.61 C(kg) 0.39 0.39 0.39 0.39 0.39 0.2 2 模型试验测定两种料制径向参数对比 2.1 料面形状
两种料制焦炭层在炉内的形状
01234567
510152025303540距中心距离cm
料面高度cm1#C2#C 3
两种料制矿石层在炉内的料面形状0123456789
510152025303540距中心距离cm
料面高度cm1#O2#O
图2 两种料制焦炭层在炉内的料面形状 图3 两种料制矿石层在炉内的料面形状 料面断面形状实质是一批料布入炉内后沿高炉径向断面的变化曲线,沿圆周的料面形状是高炉上部煤气流的调节分配器,可以通过其形状的稳定程度和煤气经过料柱行程的不同,调节煤气流的“物理分布”;所以合理的料面形状对高炉操作而言是至关重要的。那么怎样才算是合理的的料面形状呢?。 一般将炉喉料面形状划分为三部分:即边缘环带、中间环带、中心焦堆。边缘环带即边缘平台,中间环带即中间漏斗,中心焦堆即高炉中心区域的焦炭量。 焦炭平台的宽度、漏斗的深度是非常关键的参数,平台宽度过宽,漏斗深度过浅容易使料面过于平坦,造成中心边缘气流难于控制;平台宽度过窄,漏斗深度过深容易造成料面不稳定,料面容易发生塌陷变形现象,影响气流的合理分布。根据经验一般大型高炉焦炭平台宽1.5m左右,原燃料质量好,可适当加宽,原燃料质量差应适当缩小。漏斗的深度对于大型高炉以漏斗斜边的坡度要求小于17°[2]。 中心焦堆的焦炭量少,中心气流难以保证,如不及时调整,时间长则风量萎缩,会形成炉缸中心堆积,而焦炭量过多则会产生管道、崩料,煤气利用率低等问题。一般2000m3级高炉中心焦量都控制在30%~35%。 采用多环布料建立稳定的焦炭平台,形成平台漏斗形的料面形状,保持炉喉边缘及中心一定厚度的焦炭,炉况能够长期稳定顺行, 对邯钢5#高炉两种典型的料制进行模拟试验,利用所测的料面高度的数据绘图,两种料制焦炭层在炉内的形状见图2,矿石层在炉内的形状见图3,由图可见: (1)焦炭平台:2#料制基本上形成了靠近炉墙的焦炭平台,焦炭平台长度实测值为17cm,按相似比例放大应为1.7m;1#料制没有形成焦炭平台,在距炉墙1.3m左右形成堆尖。 (2)漏斗坡度:2#料制焦炭漏斗坡度30°,1#料制焦炭漏斗坡度25°,1#料制的坡度比2#料制的坡度缓。 (3)中心焦量:2#料制的中心焦量占边缘的26%,1#料制的的中心焦量占边缘的53%。 (4)矿的料面形状主要差别是边缘环带2#料制布矿多,1#料制布矿少,约少25%。 通过上述数据结合合理料面形状理论可知:2#料制比1#料制更符合合理料面形状的要求,但也存在着漏斗坡度大,焦炭平台相对较宽;中心焦量少,长时间采用此料制也会出现风量萎缩,中心堆积的问题。 2.2 径向矿焦比分布 矿焦比分布是炉喉纵断面中心到边缘矿层与焦层厚度之比,它代表着高炉径向各部位焦炭负荷的轻重程度,其径向分布曲线即为装料制度的特性曲线,通过曲线变化的幅度,可判 4
断其对煤气流分布影响的程度,通过控制矿焦比分布 可以调节炉内化学反应和气—固—液三相之间热传导进行的程度。[3]
两种料制的径向矿焦比分布
00.511.52
510152025303540距中心距离
O/C1#料制2#料制
图4 两种料制的径向矿焦比分布 图5提料布袋示意图 模型试验模拟两种料制所测得的径向矿焦比分布见图4,从图4可以看出,中间坏带区2#料制的O/C(矿焦比)大于1#料制,因此2#料制与1#料制相比中心负荷稍轻,边缘次之,中间环带重,有利于获得两股煤气流分布,并获得较好的煤气利用;1#料制是中心负荷稍重,中间环带和边缘负荷较轻,煤气利用不好。但是2#料制在中间环带显得比较重,在焦炭质量较好时可以保持顺行,如果焦炭质量下降,就会出现风量减少、煤气流不稳的现象,这时可以采用减轻中间环带负荷的操作方法解决。 2.3 透气性指数分布: 透气性指数分布是直接衡量所布的炉料沿高炉径向的透气性好坏的参数,依据的计算公式如下[4]: ε= Vε/V (1) de=1/∑(xi/di) (2) φ= ∑(xiφi) (3) K=0.57〔ε3φde/(1-ε)〕 (4) 式中炉料孔隙度ε的测量根据炉料吸附饱和水后,原有体积与所注水体积之比的计算[5];de为比表面平均直径;φ为形状系数;xi为第i级别颗粒的质量分数;di为第i级别颗
粒的直径(mm),φi为第i级别颗粒的形状系数,采用从试验炉料中随机取样20次求平均值炉料最小直径和最大直径之比;K为透气性指数。 对试验炉料采用提料布袋方式分隔所布的散状颗粒料,提料布袋示意图见图5,试验证明,提料布袋可以很好的切割炉料,提料布袋是沿高炉径向做成方格,这样在布料前预先放好,当料布完后从模型上口提出,取出每个方格中的炉料完成上述ε、de、φ的测量工作,将每个方格中的参数带入公式(4)即可计算出该方格中代表的炉料透气性指数K。试验所测得1#、2#料制的透气性指数分布见图6。