az91d镁合金压铸件之表面缺陷分析nb上盖
AZ91D镁合金压铸样品仿真分析及腐蚀行为研究

AZ91D镁合金压铸样品仿真分析及腐蚀行为研究王全乐;郭艳萍;董兆博;王琳;霍少达;亢太萧;刘宝胜【摘要】通过铸造仿真软件(MAGMA)对AZ91D镁合金笔记本电脑底外壳压铸过程进行仿真分析,采用压铸方法及表面化学转化后处理制备样品.利用扫描电镜及能谱仪分析了样品的表面及亚表面的结构特征,极化曲线和盐雾实验用来研究样品的腐蚀行为.仿真分析结果表明,样品的填充时间为0.012 1 s.实验结果表明,在浇口位置附近基体微孔含量较低,而在填充远端,即排气孔位置,微孔含量明显增多.通过对样品内部气体含量的仿真分析进一步验证了这一结果.微孔主要是由熔融镁合金的高温使模具表面喷涂的脱模剂水分呈爆炸式膨胀导致的.另外,相对浇口位置样品而言,填充远端样品的耐腐蚀性严重降低,这是由于远端样品的化学转化膜不连续和不完整导致的,而这恰恰与微孔有直接的关系.【期刊名称】《铸造设备与工艺》【年(卷),期】2018(000)001【总页数】5页(P20-24)【关键词】AZ91D镁合金;压铸仿真分析;化学转化处理;腐蚀行为【作者】王全乐;郭艳萍;董兆博;王琳;霍少达;亢太萧;刘宝胜【作者单位】太原科技大学材料科学与工程学院,山西太原030024;太原科技大学材料科学与工程学院,山西太原030024;太原科技大学材料科学与工程学院,山西太原030024;太原科技大学材料科学与工程学院,山西太原030024;太原科技大学材料科学与工程学院,山西太原030024;太原科技大学材料科学与工程学院,山西太原030024;太原科技大学材料科学与工程学院,山西太原030024【正文语种】中文【中图分类】TG174.4压铸工艺之所以能在镁合金、锌合金及铜合金产品中得到广泛的应用,主要是因为其可以生产出形状较复杂的产品,而且保持较高的生产率。
但是一些内部缺陷是不可避免的,例如疏松、中心孔洞、缩陷等。
有时还会出现外表面的缺陷,如冷接纹、表面流痕及裂纹、充填不饱满等[1]。
铝合金压铸件表面铸造缺陷11类问题分析及解决办法

铝合⾦压铸件表⾯铸造缺陷11类问题分析及解决办法⼀、表⾯铸造缺陷1.1拉伤(1)特征:①沿开模⽅向铸件表⾯呈线条状的拉伤痕迹,有⼀定深度,严重时为整⾯拉伤;②⾦属液与模具表⾯粘黏,导致铸件表⾯缺料。
(2)产⽣原因:①模具型腔表⾯有损伤;②出模⽅向⽆斜度或斜度过⼩;③顶出不平衡;④模具松动:⑤浇铸温度过⾼或过低,模具温度过⾼导致合⾦液粘附;⑥脱模剂使⽤效果不好:⑦铝合⾦成分含铁量低于O.8%;⽬冷却时间过长或过短。
(3)处理⽅法:①修理模具表⾯损伤;②修正斜度,提⾼模具表⾯光洁度;③调整顶杆,使顶出⼒平衡;④紧固模具;⑤控制合理的浇铸温度和模具温度180-250 ;⑥更换脱模剂:⑦调整铝合⾦含铁量; @调整冷却时间;⑨修改内浇⼝,改变铝液⽅向。
1.2⽓泡(1 )特征:铸件表⾯有⽶粒⼤⼩的隆起表⽪下形成的空洞.(2)产⽣原因①合⾦液在压室充满度过低,易产⽣卷⽓,压射速度过⾼;②模具排⽓不良;③熔液未除⽓,熔炼温度过⾼;④模温过⾼,⾦属凝固时间不够,强度不够,⽽过早开模顶出铸件,受压⽓体膨胀起来;⑤脱模剂太多;⑥内浇⼝开设不良,充填⽅向交接。
(3)处理⽅法①改⼩压室直径,提⾼⾦属液充满度;②延长压射时间,降低第⼀阶段压射速度,改变低速与⾼速压射切换点;③降低模温,保持热平衡;④增设排⽓槽、溢流槽,充分排⽓,及时清除排⽓槽_上的油污、废料;⑤调整熔炼⼯艺,进⾏除⽓处理;⑥留模时间适当延长:⑦减少脱模剂⽤量。
1.3裂纹(1)特征:①铸件表⾯有呈直线状或波浪形的纹路,狭⼩⽽长,在外⼒作⽤下有发展趋势;②冷裂隙开裂处⾦属没被氧化;③热裂-开裂处⾦属已被氧化。
(2)产⽣原因:①合⾦中铁含量过⾼或硅含量过⾼;②何孚有害杂质的含量过⾼,降低了合⾦的塑性;③铝硅铜合⾦含锌量过⾼或含铜量过低;④模具,特别是模腔整体温度太低;⑤铸件壁厚、薄存有剧烈变化之处收缩受阻,尖⾓位形成应⼒;⑥留模时间过长,应⼒⼤;⑦顶出时受⼒不均匀。
航空镁合金铸件常见铸造缺陷的分析及克服方法

航空镁合金铸件常见铸造缺陷的分析及克服方法摘要:总的来说,航空镁合金铸件生产工艺和传统铝合金铸件生产工艺之间存在很大区别,实际铸件废品类型以及形成原因也存在很大不同,人们可以根据航空镁合金铸造理论,以及生产事件,对铸造过程中容易出现缺陷的地方进行研究。
本文以某型航空机匣壳体铸件为研究对象,对其缺陷产生机理以及克服方式进行总结,希望能够对相关工作起到一定帮助作用。
关键词:航空;镁合金铸件;铸造缺陷本文所研究的铸件是国内浇铸重量较大的镁合金铸件,在浇铸过程中,准备了很多模具和数套测具,这其中还包括冷铁。
更为重要的是,该铸件从制芯到浇铸的整个周期为几天,但由于准备周期很长,砂芯吸湿严重,为后续浇铸操作带来了极大难度,熔化量也能达到几吨。
在该铸件铸造过程中,常见缺陷基本上均能体现出来,代表性极强,如氧化夹杂、缩孔以及憋气等等。
1.缩孔的克服1.1缩孔产生机理当合金液浇入铸型之后,会吸收很多热量,此时,合金液温度大幅下降,进而出现液态收缩问题。
一般来说,液态收缩以及凝固收缩产生的体积缩减,与外壳尺寸缩小所造成的体积缩减相近,便不会出现缩孔问题。
如果合金液态收缩以及凝固收缩全部超过硬壳固态收缩,会出现缩孔问题,具体产生的条件是铸件凝固,该种凝固顺序是由表及里,缩孔出现地点为最终凝固位置。
1.2产生部位和克服手段具体铸件示意图为图1所示,缩孔产生部位主要集中在1号和2号位置,具体克服手段如下:第一,在有缩孔缺陷的部位,工作人员可以选择在2号部位增加暗冒口。
第二,在组芯合箱时,应保证铸件内部存在一定温度,最佳温度范围为40到50℃。
第三,增加冷铁,主要设计在1号位置处。
通过上述措施的应用,除了暗冒口补缩效果较差外,其他方面均满足要求。
为了将暗冒口作用全面展示出来,除了增加暗冒口之外,还要使得该冒口向保温冒口转变。
总的来说,加大暗冒口显得十分困难,所以,工作人员可以使用保温棉沿着冒口内壁,使其充分贴合,强化其保温特性,而且这种保温冒口完全能够将缩孔问题克服[1]。
AZ91D镁合金表面复合镀层局部腐蚀现象解析及化学镀Ni_P_Cu的研究
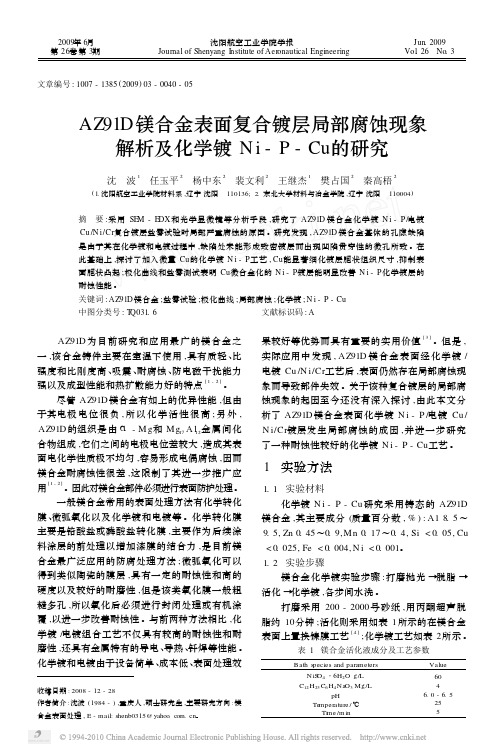
文章编号:1007-1385(2009)03-0040-05AZ91D镁合金表面复合镀层局部腐蚀现象解析及化学镀N i-P-Cu的研究沈 波1 任玉平2 杨中东2 裴文利2 王继杰1 樊占国2 秦高梧2(1.沈阳航空工业学院材料系,辽宁沈阳 110136; 2.东北大学材料与冶金学院,辽宁沈阳 110004)摘 要:采用SE M-E DX和光学显微镜等分析手段,研究了AZ91D镁合金化学镀N i-P/电镀Cu/N i/Cr复合镀层盐雾试验时局部严重腐蚀的原因。
研究发现,AZ91D镁合金基体的孔隙缺陷是由于其在化学镀和电镀过程中,缺陷处未能形成致密镀层而出现凹陷贯穿性的微孔所致。
在此基础上,探讨了加入微量Cu的化学镀N i-P工艺,Cu能显著细化镀层胞状组织尺寸,抑制表面胞状凸起;极化曲线和盐雾测试表明Cu微合金化的N i-P镀层能明显改善N i-P化学镀层的耐蚀性能。
关键词:AZ91D镁合金;盐雾试验;极化曲线;局部腐蚀;化学镀;N i-P-Cu中图分类号:T Q031.6文献标识码:A AZ91D为目前研究和应用最广的镁合金之一,该合金铸件主要在室温下使用,具有质轻、比强度和比刚度高、吸震、耐腐蚀、防电磁干扰能力强以及成型性能和热扩散能力好的特点[1-2]。
尽管AZ91D镁合金有如上的优异性能,但由于其电极电位很负,所以化学活性很高;另外, AZ91D的组织是由α-Mg和Mg17A l12金属间化合物组成,它们之间的电极电位差较大,造成其表面电化学性质极不均匀,容易形成电偶腐蚀,因而镁合金耐腐蚀性很差,这限制了其进一步推广应用[1-2]。
因此对镁合金部件必须进行表面防护处理。
一般镁合金常用的表面处理方法有化学转化膜、微弧氧化以及化学镀和电镀等。
化学转化膜主要是铬酸盐或磷酸盐转化膜,主要作为后续涂料涂层的前处理以增加漆膜的结合力,是目前镁合金最广泛应用的防腐处理方法;微弧氧化可以得到类似陶瓷的膜层,具有一定的耐蚀性和高的硬度以及较好的耐磨性,但是该类氧化膜一般粗糙多孔,所以氧化后必须进行封闭处理或有机涂覆,以进一步改善耐蚀性。
压铸件在表面处理后易出现缺陷问题的分析报告
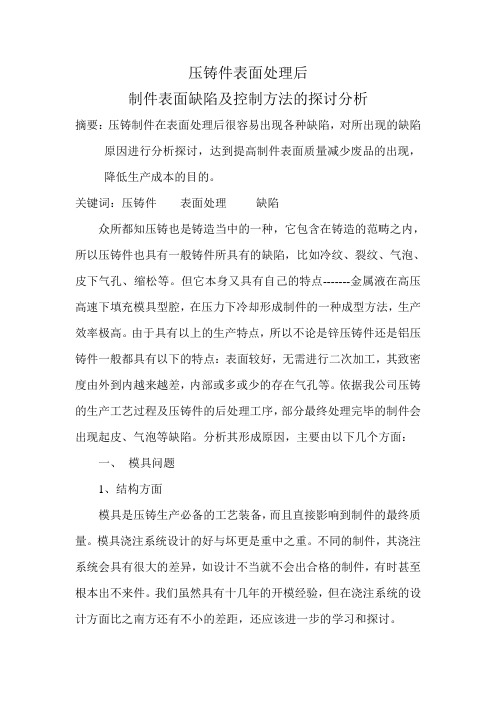
压铸件表面处理后制件表面缺陷及控制方法的探讨分析摘要:压铸制件在表面处理后很容易出现各种缺陷,对所出现的缺陷原因进行分析探讨,达到提高制件表面质量减少废品的出现,降低生产成本的目的。
关键词:压铸件表面处理缺陷众所都知压铸也是铸造当中的一种,它包含在铸造的范畴之内,所以压铸件也具有一般铸件所具有的缺陷,比如冷纹、裂纹、气泡、皮下气孔、缩松等。
但它本身又具有自己的特点-------金属液在高压高速下填充模具型腔,在压力下冷却形成制件的一种成型方法,生产效率极高。
由于具有以上的生产特点,所以不论是锌压铸件还是铝压铸件一般都具有以下的特点:表面较好,无需进行二次加工,其致密度由外到内越来越差,内部或多或少的存在气孔等。
依据我公司压铸的生产工艺过程及压铸件的后处理工序,部分最终处理完毕的制件会出现起皮、气泡等缺陷。
分析其形成原因,主要由以下几个方面:一、模具问题1、结构方面模具是压铸生产必备的工艺装备,而且直接影响到制件的最终质量。
模具浇注系统设计的好与坏更是重中之重。
不同的制件,其浇注系统会具有很大的差异,如设计不当就不会出合格的制件,有时甚至根本出不来件。
我们虽然具有十几年的开模经验,但在浇注系统的设计方面比之南方还有不小的差距,还应该进一步的学习和探讨。
2、毛刺方面模具去毛刺是每个公司都想要达到的高度,如果制件无毛刺,不但节约了生产成本,也提高了表面质量。
但就压铸的生产工艺,要想完全的去除毛刺是根本办不到也是不现实的,而且有些结构较复杂的制件,去掉毛刺后反而会增加其他补救不了的缺陷-------冷纹、气孔,特别是看不到的皮下气孔(喷塑、电镀后会看到)。
这是因为金属液在高压高速填充型腔的同时,把未来得及排出型腔的气体(由于模具达到了去毛刺的状态,影响到了模具的排气)卷入到制件中所造成的。
二、原材料问题国家研究人员通过大量的实验证明,金属具有遗传性。
通俗的说就是在原材料中所具有的缺陷(比如气孔),生产出来的制件也会有。
AZ91D镁合金表面富镁涂层改性研究的开题报告

AZ91D镁合金表面富镁涂层改性研究的开题报告一、研究背景和意义AZ91D镁合金是一种常用的镁合金,具有与铝合金相当的轻量化和高机械性能的特点,因此在车辆制造、航空航天、电子等领域得到广泛应用。
然而,AZ91D镁合金表面易受到外界环境的影响,例如潮湿、高温等,容易产生腐蚀和氧化等问题,从而降低其使用寿命和性能。
因此,通过表面改性处理来提高AZ91D镁合金的耐腐蚀性和氧化防护效果是必要的。
在目前的研究中,富镁涂层因具有良好的抗腐蚀和氧化性能等特点,成为改性AZ91D镁合金表面的一种有效方法。
因此,开展AZ91D镁合金表面富镁涂层改性研究具有重要的科学意义和应用前景。
二、研究内容和方法本研究将以AZ91D镁合金表面为研究对象,采用化学镀和物理镀等方法制备不同厚度的富镁涂层,并分析其表面形貌、成分组成、抗腐蚀性能、氧化防护效果等性能指标。
具体研究内容如下:1. AZ91D镁合金表面富镁涂层的制备方法研究通过对不同制备方法的对比,选择出适合AZ91D镁合金表面富镁涂层制备的最优方法。
2. AZ91D镁合金表面富镁涂层的结构表征采用扫描电镜(SEM)、X射线衍射(XRD)等表征手段,分析不同厚度的富镁涂层的表面形貌和成分组成。
3. AZ91D镁合金表面富镁涂层的抗腐蚀性能研究采用电化学测试等方法,分析富镁涂层对AZ91D镁合金表面抗腐蚀性能的影响。
4. AZ91D镁合金表面富镁涂层的氧化防护效果研究采用热重分析(TGA)等方法,分析富镁涂层对AZ91D镁合金表面氧化防护效果的影响。
三、研究应用前景本研究可为改善AZ91D镁合金的表面性能、提高其使用寿命和性能提供科学的理论基础和实验依据。
同时,本研究所得的结论也可为其他镁合金表面改性研究提供借鉴和启示。
该研究成果具有重要的实际应用价值和工程意义。
AZ91D镁合金挤压铸造组织与性能的研究
挤压铸造设备为 国 产 四 立 柱 油 压 机 # 其主要技术 参数及挤压成形工艺参数见表 !) 镁合金挤压铸造工艺流 程见 图 %) 从 铸 件 不 同 部 位切取试样 # 经粗磨 & 细磨后 # 用 #[ 硝 酸 酒 精 腐 蚀 # 在 8 J : ( 型高级金相显微镜上进行金相组织观察 ) D! 试验结果及分析 !* %! 挤压铸件不同部位的凝固组织 从而使 挤压铸造中由于 液 态 金 属 在 压 力 下 结 晶 # 得该工艺具有一系列优点 ) 然而 # 挤压铸造时 # 即使是 施加恒定的机械压力 # 在铸件各处的压力分布也是不 均匀的 # 而且 # 随着凝固过程的进行是不断变化的 ) 这 主要是由于铸件中 固 相 和 液 相 传 递 压 力 的 特 点 不 同 # 在凝固过程中固相和 液 相 体 积 比 & 固相形状不断发生 变化所致 ) 此外 # 铸件 铸型间摩 擦力的 存在 也是一 个 $ 重要因素 # 铸件形状和加压方式也有一定的影响 ) 铸件的平均壁厚为 % 其挤压充 型过程 "00 左右 # 如图 ! 所示 ) 由于铸件各处的压 力分 布不一 样 #在压 力下结晶 的 铸 件 的 不 同 部 位 的 组 织 势 必 也 会 受 到 影 响 ) 考察图 ! 中 G& F& B& = 和 A 等 # 处的铸态组织 #
收稿日期 ! ! " " # $ " ’ $ ! 3" ! " " # $ % " $ " % !! 修订日期 ! 作者简介 ! 李东南 ! # 江西南昌人 # 博士 # 副教授 * 研究方向 $ 半固 % ) 3 6 $ !" 态成形技术 # 镁合金压铸 # 镁合金挤压铸造 * $ ! " # $ % / , V . 1 1 1 ! " " "!K , 1 * 4 . 0% V / / / V 1!% 3 (* 4 . 0 2 k
压铸件的常见缺陷及预防和解决
第一章压铸件的缺陷特征,产生原因,防止方法名称流痕及花纹网状毛翅脆性裂纹缩孔缩松特征及检查方法外观检查:铸件表面上有与金属液流动方向一致的条纹,有明显可见的与金属基体颜色不一样无方向性的纹路,无发展趋势。
外观检查:压铸件表面上有网状发丝一样凸起或凹陷的痕迹,随压铸次数增加而不断扩大和延伸外观检查或金相检查:合金晶粒粗大或极小,使铸件易断裂或碰碎外观检查:将铸件放在碱性溶液中,裂纹处呈暗灰色金属基体的破坏与裂开呈直线或波浪形,纹路狭小而长,在外力作用下有发展趋向裂纹有穿透和不穿透两种解剖外观检查或探伤检查;缩孔表面呈暗色并不光滑,形状不规则的孔洞,大而集中的为缩孔,小而分散的为缩松产生原因1,首先进入型腔的金属液形成一个极薄的而又不完全的金属层后,被后来的金属液所弥补而留下的痕迹。
2,模温过低3,内浇道截面积过小及位置不当产生喷溅。
4,作用于金属液上的压力不足花纹:涂料用量过多。
1,压铸模型腔表面龟裂2,压铸模材质不当或热处理工艺不正确3,压铸模冷热温差变化太大4,浇注温度过高5,压铸模预热不足6,型腔表面粗糙7,压铸模壁薄或有尖角1,合金过热太大或保温时间过长2,激烈过冷,结晶过细3,铝合金含有锌铁等杂质太多4,铝合金中含铜超出规定范围在铸件上由于应力或外力而产生的裂纹1,锌合金铸件的裂纹(1)锌合金中有害杂质铅,锡,铁和镉的含量超过了规定范围(2)铸件从压铸模中取出过迟(3)型芯的抽出或推出受力不均(4)铸件的厚薄相接处转变剧烈(5)熔炼温度过高2,铝合金铸件的裂纹(1)合金中铁含量过高或硅含量过低(2)合金中有害杂质的含量过高,降低了合金的的可塑性(3)铝硅合金:铝硅铜合金含锌或含铜量过高;铝镁合金中含镁量过多(4)模具,特别是型芯温度太低(5)铸件壁厚有剧烈变化之处(6)留模时间过长(7)顶出时受力不均3,镁合金铸件的裂纹(1)合金中铝硅含量高(2)模具温度低(3)铸件壁厚薄变化剧裂(4)顶出和抽芯受力不均匀4,铜合金铸件的裂纹(1)黄铜中锌的含量过高(冷裂)或过低(热裂)(2)硅黄铜中硅的含量高(3)开模时间晚,特别是型芯多的铸件缩孔是压铸件在冷凝过程中,内部补偿不足而造成的孔穴1,浇注温度过高2,压射比压低3,铸件在结构上有金属积聚的部位和截面变化剧烈4,内浇道较小防止方法1,提高模温2,调整内浇道截面积或位置3,调整内浇道速度及压力4,适当地选用涂料及调整用量1,正确选用压铸模材料及热处理工艺2,浇注温度不宜过高尤其是高熔点合金3,模具预热要充分4,压铸模要定期或压铸一定次数后退火,打磨成型部分表面1,合金不宜过热2,提高模具温度,降低浇注温度3,严格控制合金成分在允许的范围内1,合金材料的配比要注意杂质含量不要超过起点要求2,调整好开模时间3,要使推杆受力均匀4,改变壁厚不均匀性1,正确控制合金成分,在某些情况下:可在合金中加纯铝锭以降低合金中含镁量;或在合金中加铝硅中间合金以提高硅含量2,提高模具温度3,改变铸件结构4,调整抽芯机构或使推杆受力均匀1,合金中加纯镁以降低铝硅含量2,模具温度要控制在要求的范围内3,改进铸件结构消除厚薄变化较大的截面4,调整好型芯和推,杆使之受力均衡1,保证合金的化学成分合金元素取其下限:硅黄铜在配制时,硅和锌的含量不能同时取上限2,提高模具温度3,适当控制调整开模时间1,改变铸件结构消除金属积聚及截面变化大处2,在可能条件下降低浇注温度3,提高压射比压4,适当改善浇注系统,使压力更好的传递第二章铸造铝合金缺陷及分析[size=3]一氧化夹渣缺陷特征:氧化夹渣多分布在铸件的上表面,在铸型不通气的转角部位。
显微特征与缺陷对铸造镁合金AZ91D力学性能的影响
T em e h ia r p riso AZ9 wi tt o l edvd dit e v l c o d gt i ee t h c a c l o e e f n p t 1 D t T6s ec udb ii e ot el e c r i df rn h a n h r e a n o
mi o t cua faue dd fcs ()L g hi a ep rs r e eo dp ae U S 2 0MP ; c s u trl e trsa ee t 1 a esr g ooi o f sc n h s, T < 3 a r r n . r k n y t l t ()Ltesr a ep r s r e eo dp ae 2 0MP < T < 5 a () hi a ep rs 2 il hi g oo i o f scn h s, 3 a U S 2 0MP ; 3 Nosr g oo i t n k y t lt k n y t
Efe t fM i r sr c u a a u e nd De e t n t eM e ha i a o r i so a iy Ca t f c so c o t u t r l Fe t r sa f c so h c n c lPr pe te fGr v t s
UTS >27 Pa 0M .
Ke r s M i r s u t r l e t r ; f c ; e h i a r p r ; y wo d : c o t cu a au e De e t M c a c l o e t AZ9 D ; a n s m l y r f n p y 1 M g e i al u o
镁合金真空低压消失模铸造常见缺陷分析
l 引言
优化结 构设 计 、 选用 轻质 材料使产 品轻 量 化是 世界 制
充 型 时金 属液 的静压 头较 小 . 并且 高温 液态 镁合 金易 氧 化 燃 烧 的特性 又使 它难 以像 铝 合金 那 样 通 过 提 高浇 注 温 度
来改 善其充 型能 力 ] 因此 , 合 金 采 用 消 失模 铸 造 工 艺 , 镁
艺 因素 等限制 , 不能 满足现 代工业 的需 要 。 也
在充 型上所 面临 的挑 战 主要 表 现 为 充 型 能 力差 。抽 真 空
或浇 注时施 以外压 是 改善 镁 合金 消失 模 铸 造 的 重要 工 艺 措施 。合金 成 分 、 注 温度 、 样 密度 和 几 何形 状 、 料 、 浇 模 涂
维普资讯
・
9 ・ 8
文 章 编 号 :0 2 8 6 2 0 ) 5 0 8 O 1 0 —6 8 ( 0 6 0 …0 9 3
镁 合 金真 空低 压 消 失模 铸 造 常见 缺 陷分 析 *
李继 强 , 自 田 , 大 付 , 选 普 , 乃 瑜 樊 张 董 黄
o e u i go v i i g d fc swhc a e n t e ea a y e r u o wa d . ei t o u t n a d t e a a y i c n c n u t o fr d cn ra o dn ee t ih b s d o h s n l s swe e p tf r r Th n r d c i n h n l ss a o s l f r o e f i n p l ai n o h o tf a c s ig p o e s a d p e e tt e e d fc s fi e ta p i t ft e l s o m a t r c s n r v n h s e e t . c c o n Ke r s ma n su al y o p e s r x e d b e p te n c s i g ee t ;p e e t e me h d y wo d : g e i m lo ;lw- r s u e e p n a l a t r a t ;d fc s r v n i t o s n v
- 1、下载文档前请自行甄别文档内容的完整性,平台不提供额外的编辑、内容补充、找答案等附加服务。
- 2、"仅部分预览"的文档,不可在线预览部分如存在完整性等问题,可反馈申请退款(可完整预览的文档不适用该条件!)。
- 3、如文档侵犯您的权益,请联系客服反馈,我们会尽快为您处理(人工客服工作时间:9:00-18:30)。
AZ91D 镁合金压铸件之表面缺陷分析— NB 上盖
由于镁合金具有优异的刚性、散热能力和良好的电磁遮蔽效果等好处,所以现在已被广泛运用在3C 电子产品上。
而在众多的镁合金成形制程中又以压铸制程最被广为采用,因此本文将针对以热室机压铸法所制造NB 上盖产品(AZ91D) ,由现场取得具表面缺陷的不良品,如热裂模、表面氧化、热裂、顶出变形、流纹等,然后藉由外观和微观分析找出各个缺陷确切的形态,再配合上统计缺陷位置分布和成分分析,以证实缺陷发生的原因。
前言镁合金具有质轻、高比强度、耐震等优点,以此在航空器材、运输工具、信息产品上均有相当广泛的应用实例;另外,镁合金与工程塑料比较,也具有优异的刚性、散热能力和良好的电磁遮蔽效果,所以近年来在3C (计算机、通讯、消费性电子) 可携式产品大展光芒。
目前镁合金零组件制造方式大多是以压铸法为主,例如:热室机压铸法或冷室机压铸法,虽然近年来还有以半固态射出成形为主的触变成形(Thixo-molding) 及流变成形(Rheo-molding) 等新制程的推出,但由于技术上仍无法突破,所以一般还是以压铸法生产镁合金为主。
在各种不同镁合金种类当中,都含有相当比例的铝元素(铝含量约介于1-10% )以作为主要添加合金元素,它与镁元素会析出的B相,使基地具有散布强化的效果,以便提升铸造性能、抗腐蚀能力以及机械性能。
其它次要添加合金元素,例如:锌元素的添加亦会提升机械性质和铸造性能;锰元素则会和铝形
成化合物,同时固溶铁、钴、镍元素,可将Fe+Ni+Co/Mn 控制在一定值之下,并改善耐蚀性;添加铍元素则可以有效减少熔融时氧化物的形成,提升熔汤的清净度。
此外,控制少量重金属元素的添加,也可有效提升镁合金抗腐蚀的效果。
而目前利用镁合金作成的3C 产品(NB 机壳、手机外壳、PDA 等),仍以
AZ91D(Mg-9%Al-1%Zn) 镁合金为主,主要是因为其机械性、铸造性、耐蚀性均能满足产品的需求,所以最常被采用。
但在以压铸法生产此类镁合金产品时,却面临了良率无法提升的重大问题,其最主要原因是表面的质量不良,必须靠后段表面研磨修整、补土等程序来补正,而耗费大量成本与时间。
因此,本文将针对AZ91D 的压铸缺陷做探讨,包括成因、种类与对策等,期能对镁合金压铸产品的缺陷有所了解,并提升镁合金产品的竞争力。
表一AZ91D 铸锭成分实验方法本次压铸用镁合金AZ91D 成分如表一,产品为笔记型计算机LCD 上盖,采用热室机压铸法(HotChamberMa- chine) 制造,压铸参数如表二所示。
压铸后收集现场各种含表面缺陷的不良品来加以统计分析。
表二压铸参数首先以现场初步巨观判定不良品缺陷种类,再由SEM 观察试片缺陷的微观形态,并使用EDS 作定性分析,得知缺陷位置的元素成分。
透过SEM 和EDS 的观察分析再与现场判定作一比对,然后配合巨观以及微观的方式得知各个缺陷真正的形态、发生原因和最常发生位置,并提出解决表面缺陷发生的对策。
结果与讨论
针对从现场所收集到的压铸镁合金产品,归纳分析后发现其常见
的缺陷有:热裂模、表面氧化、热裂、顶出变形、流纹等,以下就这些铸造缺陷做分析讨论。
1.热裂模
其巨观形态如图一所示,铸件表面具有类似网状的结构,而从统计分析发现此类缺陷最常发生的位置大多集中在进模口附近。
若从微观上观察,可以明显看出有凸起的连续网状组织形成,如图二所示。
若以EDS 分析热裂模发生的区域与基地的成分,发现两者的成分几乎相同,如图三(b) ,(c) 所示。
推究此缺陷发生的原因,可能是因为近模口附近的金属熔液流速较快且温度高,容易造成铸模的冲蚀,或因为温度的变动,发生交替的压张应力而产生表面裂纹。
图三热裂模区域之显微结构与成分分析2. 表面氧化在镁合金的NB 压铸件表面常可发现有许多小黑点,并散布在表面的任何位置,如图四所示。
藉由SEM 观察表面黑色位置的组织,则呈现出许多白色的颗粒,如图五。
若再以EDS 分析这些白色小颗粒并与基地作比对分析,发现在颗粒上的氧元素比例相对的高出许多,如图六所示,因此很有可能是一些氧化物的生成,如MgO 、Al2O3 等。
由于镁的活性极高,容易与氧元素键结反应,所以在镁锭熔解炉内会通入保护气体,目前通常是以
SF6+CO2 当作保护气氛,Mg 和SF6 的反应式:SF6+ Mg(1)+ A ir — MgO(s)+MgF2(s)+SF6 f 其中Mg 和SF6 反应会产生MgO 和MgF2 的氧化层在镁汤表面,以防止熔融镁液遭受氧化。
一旦保护气氛SF6 浓度不够,镁汤会很容易氧化,而在浇铸过程将这些氧化物带入铸件中。
3. 热裂从巨观来看,此缺陷有着深浅不一且不规则外形的黑色裂缝(图七) ,有时甚至会穿透过铸件的背面(图八) ,因此对于铸件的质量有很大的影响。
进一步以SEM 观察裂缝,则可以很明显看到裂缝是沿着晶粒界破坏,如图九,而且在裂缝边缘的组织也较为松散,有许多小的微裂缝。
依据统计分析发现,热裂大都发生在铸件断面改变处或凹角的地方,这是因为此处在凝固收缩时容易受到模具的局限而产生应力使之变形,而若这个区域又是较晚凝固的部分,则很容易产生松缩组织,使得材料强度降低,因而产生热裂。
此外,从裂缝显微组织来看,也常发现夹杂有非镁材料基地相的元素之颗粒存在,而其可能的来源有如:模具表面
涂模剂中的有机化合物、保护气体SF6 与镁材料反应生成的MgS 或MgF2 、氧化生成物MgO 或CaO、防止镁汤液面燃烧加入的助熔剂等等,任何会与镁反应生成的不纯物。
因此其真正的原因相当复杂,仍待进一步研究。
由图十裂缝中的夹杂物及EDS 分析结果得知,其具有相当高含量的
Ca 存在。
综合以上论点,热裂发生位置大多都是在凝固收缩时受限于模具然后产生应力之处,而在这些位置若又是最后凝固或充填的区域,其本身就较容易形成松缩组织或夹杂物,再配合应力的促使,使铸件从晶界上开始变形生成裂缝。
4.顶出变形由于缺陷巨观型态与热裂相当类似,所以通常此类缺陷易与热裂混淆。
其巨观上与热裂最明显的不同点在于它的裂缝大部分看似白白亮亮,并不像热裂的黑色裂缝,但若顶出变形的裂缝很深,则无法
第一时间判断出为何种缺陷。
此外,其发生位置多集中在顶出销附近,与热裂不同。
若从微观组织来看就可以清楚分辨出来,如图十一所示,在靠近裂缝两旁的基地有层状的迭纹,而且裂缝中也没有明显的白色颗粒;反观,在靠近热裂的裂缝两旁 (图九),它的基地均沿着晶粒间破断并且向下延伸,所以才有不规则的破断面。
另外,顶出变形造成的裂缝深度一般也比热裂来得浅,甚至还可以看见裂缝底部的晶粒。
图十热裂纹中夹杂特成分分析利用EDS 分析裂缝附近成分元素,其成分也与基地相成分一致,如图十一(b) 所示,所以在此也可以与热裂做一个分野。
虽然有时无法从现场直接分辨出热裂或顶出变形,但藉由观察显微组织和成分分析即可确切地辨识出为何种缺陷。
5. 流纹对于本次取样的NB
压铸薄件来说,流纹为发生机率较高的表面缺陷,通常发生在薄件之水平表面。
从巨观照片来看,其缺陷所在位置具有不规则的折纹,痕迹犹如流线波浪一般,如图十二所示,是为镁液在模内流动所造成的纹路,有时严重的话,表面还会有凹凸不平。
从SEM 观察发现,这些流纹亦会造成微小的裂缝,如图十三,虽然它的裂缝破断方式也是沿着晶界方向行进(与热裂裂缝破断方式一致),但是裂缝的深度相当浅。
而且在裂缝中并没有发现类似热裂的夹杂氧化物存在,所以流纹所产生的裂缝成因并不是夹杂氧化物所造成。
从现场经验得知,当喷洒离型剂不足的话,容易造成流纹产生,或是以模具设
计来看,当浇道设计不良,转角太直,镁液在流动到转角时会形成
乱流,亦会产生流纹的缺陷。
结论虽然至目前为止镁合金压铸品已被大量的应用在各种3C 产品上,但因受镁合金的高活性、热含量低及产品厚度极薄等因素的影响,其压铸技术仍有待改进,以提升产品的良品率。
因此我们有必要针对现场的产品缺陷做一有系列的收集、统计,再经由研究分析找出个中的原因。
本次讨论压铸镁合金的表面缺陷包括有:热裂模、表面氧化、热裂、顶出变形以及流纹。
其中热裂模缺陷发生的可能原因是在进模口的金属熔液流速较快且温度高,容易造成模具冲蚀,或是因温度变动发生交替的压张应力;表面氧化发生有可能是因为镁汤内含的氧
化物或与铸模涂模剂的反应物;
热裂缺陷主要发生在容易形成松缩组织或夹杂物且应力集
中的位置;顶出变形成因在于顶出销顶出的时间不当,才
造成顶出销附近形成裂缝;流纹缺陷的成因则为喷洒离型剂不足或浇道设计不良造成转角太直,使镁液流动时会形
成乱流。
经由以上分析,我们知道压铸镁合金的缺陷种类相当多,其发生原因也很复杂,常常是多项因素造成;因此如果可以配合现场制程参数、缺陷收集及学理研究,做有系列的探讨,应该对镁合金压铸技术的提升有所帮助。
本文作者:卓学渊、黄士龙、林惠娟。