压缩成型工艺与模具设计概述
压缩成型工艺及模具设计

二、压缩成型设备 1. 设备的作用 合模 开模 顶件 提供所需的压力
2. 设备的种类
按传动方式分
机械式压机:螺旋式压力机 液压机:水压机和油压机
2. 设备的种类
液压机按机身结 构分
框架式 用于中小型压机 立柱式 用于大中型压机
液压机按加压 形式分
上压式:工作液缸位于上端,下 部是固定工作台。
力(单位MPa)
施加成型压力的目的: 使塑料充满型腔 使粘流态物质在一定压力下固化 克服塑料在成型过程中产生的各种顶模力
使模具闭合,防止飞边
1.成型压力
计算公式:
p = pbD2 4A
式中: p ——成型压力(MPa) pb——压力机工作液压缸压力(MPa) D——压力机主缸活塞直径(m) A——凸模与塑料接触部分在分型面上的 投影面积(mm)
成型压力与塑料种类、塑件结构、模具温度等因 素有关。
2.成型温度
成型温度 —— 指压缩时所需的模具温度,对塑件 质量、模压时间影响很大
热固性塑料的模内温度高于模具温度
太高
树脂、有机物分解;塑件外层先 硬化
模具 温度
高
成型周期短,生产率提高
硬化速度慢、周期长,硬化不足; 过低 塑件表面无光;物理、力学性能差
优点: 结构简单,成本低 塑件易取出,易排气 安放嵌件方便 加料量无严格要求 模具寿命长
又称敞开式压缩模
1.溢式压缩模
缺点: 合模太快时,塑料易溢出,浪费原料;合模太慢时, 易造成飞边增厚; 水平状的飞边难于去处,且影响塑件外观; 凸、凹模配合精度较低; 不适用于压制带状、片状或纤维填料的塑料和薄壁 或壁厚均匀性要求高的塑件。
③合理堆放塑料,粉料或粒料的堆放要做到 中间高四周低,便于气体排放。
压缩成型工艺及模具设计

压缩成型工艺及模具设计在压缩成型工艺中,模具起到了关键的作用。
模具的设计直接影响到成品的质量和生产效率。
因此,模具设计需要经过详细的计划和精确的制造。
下面将分别介绍压缩成型工艺及模具设计的要点。
首先,压缩成型工艺的基本步骤如下:1.材料准备:选取合适的材料,并进行预处理以满足成型要求。
2.模具设计:根据产品的形状和尺寸要求,设计合适的模具。
3.模具制造:根据模具设计图纸,进行模具的制造工艺,包括材料选择、加工工艺等。
4.模具调试:组装好模具后,进行调试,确保模具的精度和功能。
5.材料加入:将待加工材料放入模具中,根据需要施加压力。
6.加工成型:施加压力后,材料填充模具腔体,并进行固化或固结。
7.成品脱模:凝固后的成品从模具中取出,脱模。
8.后续处理:根据需要进行后续处理,如修整、涂装等。
接下来是模具设计的要点:1.产品形状和尺寸:根据产品的形状和尺寸要求,选择合适的模具结构和尺寸。
模具腔体的形状需要与产品形状相匹配,尺寸要准确。
2.材料选择:根据产品的材料要求,选择合适的模具材料。
例如,对于制造塑料制品的压缩成型,通常使用金属或塑料模具。
3.模具结构:根据产品特点和生产要求,确定模具的结构。
设计模具时应考虑到模具的拆装方便性和加工稳定性。
4.冷却系统:为了提高成型速度和确保成品质量,模具设计中应考虑冷却系统的设置。
冷却系统可以帮助快速冷却和固化材料。
5.寿命和维护:模具的寿命与模具材料、加工工艺、使用环境等因素有关。
模具设计中应考虑到寿命和维护的问题,使模具的使用寿命更长。
6.模具制造精度:模具的加工精度直接影响到成品的质量。
在模具制造过程中,要控制好加工精度,保证模具的准确性。
总之,压缩成型工艺及模具设计对于制造塑料制品和金属制品具有重要意义。
只有合理的压缩成型工艺和精确的模具设计,才能确保成品的质量和生产效率的提高。
模具设计与制造(压缩模)

3.4 压缩模设计压缩成型模具简称压缩模、压模,又称压制模,是塑料压缩成型所采用的模具,主要用于热固性塑料的成型。
其基本成型过程是将塑料粉料或粒料直接加在敞开的模具加料室内,再将模具闭合,通过加热、加压使塑料呈流动状态并充满型腔,然后由于化学或物理变化使塑料固化(或硬化)定型。
压缩成型的特点是塑料直接加入型腔内,压机压力通过凸模直接传递给塑料,模具是在塑料最终成型时才完成闭合。
其优点是无需设置浇注系统,耗料少,使用的设备和模具都比较简单,适用于流动性差的塑料,宜成型大型塑件,塑料的收缩率小,变形小,各向异性比较均匀;其缺点是生产周期长,效率低,不易压制形状复杂、壁厚相差较大、尺寸精度高且带有精细或易碎嵌件的塑件。
3.4.1 压缩模的结构组成及分类1.压缩模的结构组成压缩模的典型结构如图3-96所示。
模具的上模和下模分别安装在压力机的上、下工作台上,上、下模通过导柱导套导向定位。
上工作台下降,使上凸模3进入下模加料室4与装入的塑料接触并对其加热。
当塑料成为熔融状态后,上工作台继续下降,熔料在受热受压的作用下充满型腔。
塑件固化(或硬化)成型后,上工作台上升,模具分型,同时压机下面的辅助液压缸开始工作,脱模机构将塑件脱出。
压缩模按各零部件的功能作用可分为以下几大部分。
(1)成型零件成型零件是直接成型塑件的零件,加料时与加料室一同起装料的作用,模具闭合时形成所要求的型腔。
图3-96中模具型腔由上凸模3、凹模4、型芯8、下凸模9等构成。
(2)加料室图3-96中凹模4的上半部,为凹模截面尺寸扩大的部分。
由于塑料与塑件相比具有较大的比容,塑件成型前单靠型腔往往无法容纳全部原料,因此一般需要在型腔之上设有一段加料腔室。
(3)导向机构导向机构的作用是保证上模和下模两大部分或模具内部其他零部件之间准确对合。
图3-96中,由布置在模具上周边的四根导柱6和导套10组成导向机构,为保证推出机构上下运动平稳,该模具在下模座板15上设有两根推板导柱,在推板上还设有推板导套。
第四章-压缩成型工艺与模具设计

第四章压缩成型工艺与压缩模设计第一节压缩成型工艺⏹压缩模具又称压制模具或压塑模具(简称压模),主要用于成型热固性塑料,也可成型热塑性塑料。
⏹压缩模具没有浇注系统,直接将未塑化的塑料加入模腔,模具只能垂直安装。
一、压缩成型原理及特点将塑料加入高温的型腔和加料室,然后以一定的速度将模具闭合,塑料在热和压力的作用下熔融流动,并且很快地充满整个型腔,树脂和固化剂作用发生交联反应,生成不熔不溶的体型化合物,塑料因而固化,成为具有一定形状的制品,当制品完全定型并且具有最佳性能时,即开启模具取出制品。
压缩模塑原理图1—凸模固定板2—上凸模3—凹模4—下凸模5—凸模固定板6—垫板⏹与注射成型相比,压缩成型的优点是:⏹(1)没有浇注系统,料耗少,使用的设备为普通压力机,模具较简单,可以压制较大平面的塑件或利用多型腔模具,同时压制多个制品;⏹(2)压制时,由于塑料在型腔内直接受压成型,所以有利于模压成型流动性较差的或以纤维为填料的塑件,且塑件收缩小,变形小,各向性能较均匀;⏹但同时压缩成型也有着不可避免的缺点:⏹(1)生产周期长,效率低,特别是厚壁制品周期更长。
且不易压制形状复杂、壁厚相差较大的塑件;⏹(2)不易实现自动化,劳动强度较大,特别是移动式压缩模具。
由于模具要加热,原料常有粉尘纤维物飞扬,劳动条件差;⏹(3)塑件常有较厚溢边,且每模溢边值不同,因此会影响尺寸(尤其是高度尺寸)的准确性;⏹(4)厚壁制品和带有深孔、形状复杂的制品难于压制成型,不能压制带有精细和易断的嵌件的塑件;⏹(5)压缩模具要受到高温、高压的联合作用,对模具材料要求较高,重要零件均要进行热处理。
压缩成型中模具受到冲击较大,零件易磨损和变形,使用寿命较短,一般仅有20~30万次。
常见的用于压缩成型的塑料有:酚醛塑料、氨基塑料、不饱和聚酯塑料、聚酰亚胺等,其中酚醛塑料和氨基塑料使用最为广泛。
二、压缩成型工艺过程⏹1.压缩成型前的准备⏹(1)预压压缩成型前,为了成型时操作方便和提高塑件质量,可利用预压模具将粉状或纤维状的热固性塑料原料在预压机上压成重量一定、形状一致的锭料。
塑料成型工艺与模具设计名词解释

1名词解释1.注射成型:将粒状或粉状塑料从注射机的料斗送入高温的料筒内加热熔融塑化,使其成为粘流态熔体,然后在注射机柱塞或螺杆的高压推动下,以很大的流速通过喷嘴,注入模具型腔,经一定时间的保压冷却定型后,开启模具便可从型腔中脱出具有一定形状和尺寸塑料制件的成型方法,主要用于成型热塑性塑料件2.压缩成型:将粉状、粒状等的热固性塑料原料直接加入敞开的模具加料室内,然后在加热和加压的作用下,使塑料熔融充满型腔,并发生交联固化反应,硬化定型形成塑件,主要用于成型热固性塑料件3.压注成型:压注成型又称传递成型,其成型原理如图所示,先将固态成型物料加入加料腔内,使其受热软化转变为粘流态,并在压力机柱塞压力作用下,经过浇注系统充满型腔,塑料在型腔内继续受热受压,产生交联反应而固化定型4.挤出成型:挤出成型是将颗粒状塑料加入挤出机料筒内,经外部加热和料筒内螺杆机械作用而熔融成粘流态,并借助螺杆的旋转推进力使熔料通过机头里具有一定形状的孔道(口模),成为截面与口模形状相仿的连续体,经冷却凝固则得连续的塑料型材制品。
5.中空吹塑成型:将挤出或注射出来的熔融状态的管状坯料置于模具型腔内,借助压缩空气使管坯膨胀贴紧于模具型腔壁上,冷硬后获得中空塑件,这种成型方法称中空吹塑成型。
6.塑料:以高分子合成树脂为主要成份、在一定温度和压力下具有塑性和流动性,可被塑制成一定形状,且在一定条件下保持形状不变的材料。
7.热塑性塑料:具有线型分子链成支架型结构加热变软,冷却固化可逆的塑料。
8.热固性塑料:具有网状分子链结构加热软化,固化后不可逆。
9.塑化压力(背压)指螺杆式注射成型时,螺杆头部熔体在螺杆转动后退时所受到的阻力。
(背压一般不大于2MPa )10.注射压力:注射压力是指柱塞或螺杆顶部对塑料熔体所施加的压力。
11.保压压力型腔充满后,注射压力的作用在于对模内熔体的压实,此时的注射压力也可称为保压压力。
12.型腔压力型腔压力是注射压力在经过注射机喷嘴、模具的流道、浇口等的压力损失后,作用在型腔单位面积上的压力。
5.压缩成型工艺及模具设计
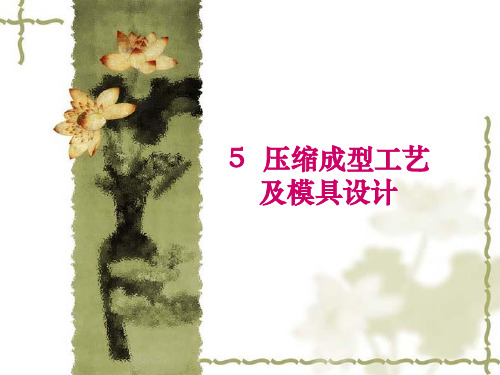
手柄头部件压缩模
(3)半固定式压缩模
上模固定在压机上,下模沿导轨移动,用定位块定位。 也可以将下模固定在压机上。 开合模在机内进行,成型后移出上模或下模,用手工 或机外卸模装置取出塑件。 与移动式压缩模具相比减小了工人劳动强度,并且容 易安放嵌件和加料。为了便于操作,当移动式压缩模 具太重或嵌件较多时,就可以采用此类模具。
用以限制凸模下行的位置 保证最薄的水平飞边,B不宜过大 主要用于半溢式和溢式压缩模
排气溢料槽
排出气体和余料
成型形状复杂塑件及流
动性较差的纤维填料的塑 件时应开设排气溢料槽.
槽深一般为0.2~0.3mm 应开到凸模的上端,使
合模后高出加料腔的上平 面
承压块(面)
保证凸模进入凹模的深度,使凹模不致受挤压而变形或损坏
1)溢式(敞开)压缩模
结构特点:
无加料室,型腔高度即为 制品高度
凸模与凹模无配合部分 有环形挤压面B
优点:
结构简单,成本低
塑件易取出,易排气 安放嵌件方便 加料量无严格要求 凹、凸模无摩擦,模具寿命长
缺点:
合模太快时,塑料易溢出,浪费原料;合模太慢时,易 造成飞边增厚; 凸、凹模配合精度较低; 不适用于压制带状、片状或纤维填料的塑料和薄壁或壁 厚均匀性要求高的塑件。
脱模:当制品完全定型并且具有最佳性能时,
即开启模具取出制品。
2.压缩成型特点
塑料直接加入型腔内,加料时模具是敞开的,即先加料后 合模。
结构简单,无浇注系统,不需复杂的推出机构
耗料少 生产周期长,效率低
不易压制形状复杂的塑件,不易获得尺寸精确的塑件
3.压缩成型工艺
压缩成型原理及工艺

压缩成型原理及工艺压缩成型又称为压塑成型、压制成型等,是将粉状或松散粒状的固态塑料直接加入到模具中,通过加热、加压的方法使它们逐渐软化熔融,然后根据模腔形状成型、经固化成为塑件,主要用于成型热固性塑料。
与注射模相比,压缩模没有浇注系统,使用的设备和模具比较简单,主要应用于日用电器、电信仪表等热固性塑件的成型。
一压缩成型原理及特点压缩成型原理如图2-2所示。
成型时,先将粉状、粒状、碎屑状或纤维状的热固性塑料原料直接加入到敞开的模具加料室内,如图2-2а所示;然后合模加热,使塑料融化,在合模压力的作用下,熔融塑料充满型腔各处,如图2-2Ь所示;这时,型腔中的塑料产生化学交联反应,使熔融塑料逐步转变为不熔的硬化定型的塑件,最后脱模将塑件从模具中取出,如图2-2c 所示。
图2-2 压缩成型原理压缩成型主要用于热固性塑料的成型。
与注射成型相比,压缩成型的优点是:可以使用普通压力机进行生产;因压缩模没有浇注系统,所以模具结构比较简单;塑件内取向组织少,取向程度低,性能比较均匀;成型收缩率小;可以生产一些带有碎屑状、片状或长纤维状填充剂、流动性很差且难于用注射方法成型的塑件和面积很大、厚度较小的大型扁塑件。
压缩成型的缺点是:成型周期长、劳动强度大、生产环境差、生产操作多用手工而不易实现自动化;塑件经常带有溢料飞边,高度方向的尺寸精度不易控制;模具易磨损,使用寿命较短。
压缩成型也可以成型热塑性塑料。
在压缩成型热塑性塑料时,模具必须交替地进行加热和冷却,才能使塑料塑化和固化,故成型周期长,生产效率低,因此,它仅适用于成型光学性能要求高的有机玻璃镜片、不宜高温注射成型的硝酸纤维汽车驾驶盘以及一些流动性很差的热塑性塑料(如聚酰亚胺等)。
二压缩成型工艺1. 成型前的准备热固性塑料比较容易吸湿,贮存时易受潮,所以,在对塑料进行加工前应对其进行预热和干燥处理。
同时,又由于热固性塑料的比容比较大,因此,为了使成型过程顺利进行,有时还要先对塑料进行预压处理。
第5章 压缩成型工艺及模具
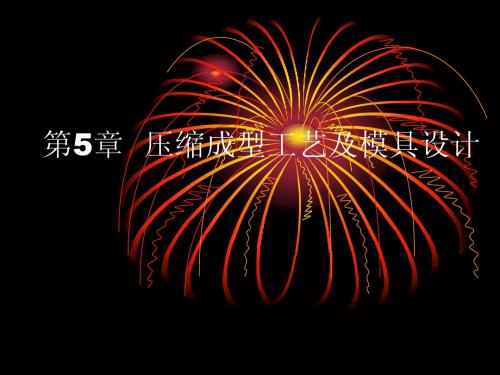
5.4.2 压缩成型设备参数校核 3 压缩模高度和开模行程校核 hmin≤h≤hmax hmax≥ h+L L=hs+ht+(10~30)
5.4.2 压缩成型设备参数校核 4 压力机工作台面有关尺寸校核
压缩模的宽度应小于压力机立柱或框架之间的距离 压缩模用螺钉与压力机连接 压缩模用压板螺钉与压力机压紧固定,则模具只需设有 宽15~30mm的凸缘台阶即可.
第六章 塑料压注成型工艺及 模具设计
6.1 压注成型工艺
又称传递成型, 压注成型 又称传递成型,它是成型热固性塑料制品 的常用方法之一. 的常用方法之一.
6.1.1 压注成型原理及特点
6.1.3 压注成型工艺参数 压注成型压力 模具温度 成型周期
�
5.1.2 压缩成型工艺过程 1 成型前准备 2 模压过程 预压 预热和干燥 加料 合模 排气 固化 脱模 模具清理 塑件后处理
3 模压后处理
5.1.3 压缩成型工艺参数
成型压力
成型温度
成型时间
5.1.3 压缩成型工艺参数 (1) 压缩成型压力
成型压力 压缩成型时压力机通过凸 模对塑料熔体充满型腔和固化时在单 位投影面上施加的力
5.5 压缩模设计 5.5.1 塑件在模具内加压方向的选择 便于加料 有利于压力传递 便于安装和固定嵌件 保证凸模的强度 便于塑料流动 便于抽拔长型芯 保证重要尺寸精度
5.5.3 凹模加料腔高度尺寸计算 (1) 计算塑件的体积 (2) 计算塑件所需塑料的原体积 V料=(1+f)KV件 (3) 加料腔高度的计算 表5-4
P成 =
πD
2
4A
P表
成型压力大小决定于塑料工艺性能和其他工 艺条件.
5.1.3 压缩成型工艺参数 (2) 压缩成型温度
- 1、下载文档前请自行甄别文档内容的完整性,平台不提供额外的编辑、内容补充、找答案等附加服务。
- 2、"仅部分预览"的文档,不可在线预览部分如存在完整性等问题,可反馈申请退款(可完整预览的文档不适用该条件!)。
- 3、如文档侵犯您的权益,请联系客服反馈,我们会尽快为您处理(人工客服工作时间:9:00-18:30)。
(二)、压缩模具分类
➢分类:
▪按模具在压机上固定方式分:移动式、半固定式和固定式; ▪按上、下模闭合形式分:溢式、不溢式和半溢式; ▪按分型面特征分:水平分型面和垂直分型面压缩模; ▪按型腔数分:单腔式和多腔式压缩模。
固定式
多型腔
不溢式 水平分型面
多分型面
单加料室 共用加料室
热固性塑料压缩模
半固定式
二、 压缩模具的结构与分类
压缩模结构 压缩模分类
(一) 压缩模结构
➢压缩模组成:型腔、加料室、导向机构、侧向分型抽
芯机构、脱模机构、加热系统等。
加料室
➢加热方式:电加热、蒸 汽加热、煤气或天然气 加热等。
➢热塑性料成型:模具开 设温度控制通道,在塑 化和定型阶段,分别通 入蒸汽加热和通入冷却 水进行冷却。
(二)、压缩模具分类
➢溢式压模缺点:
▪凸模和凹模配合完全靠导柱定位,成型制品壁厚均匀性差; ▪因合模时各型腔溢料量不均匀,成型件的精度和质量不均匀; ▪加料量应超出制品重量的5%以内,原料有一定浪费; ▪有时可不设脱模机构,而由手工取出或用压缩空气吹出制品。
➢优点:
▪无加料室,便于嵌件的安放; ▪结构简单,价廉耐用; ▪特别适合成型扁平小型薄壁制品(如钮扣、装饰品及各种小零 件)。
半溢式 复合分型面
移动式
单型腔
溢式
垂直分型面
单分型面
1、移动式压缩模移动式压缩模
(按压模在压力机上的固定方式分类)
图5-4 军衣扣压缩移动模 1—定位销;2—上模;3—手柄;4—下模;
5—嵌件;6—嵌件座;7—塑件
2、半固定式压缩模
(按压模在压力机上的固定方式分类)
二、压缩成型特点
➢热塑性料成型:模具既加热又冷却,成型周期长、效率低; 但制品内应力小,适合平整度高和光学性能好的大型制品。
二、压缩成型特点
➢压缩成型优点:
▪与注射相比,使用的设备和模具较为简单价廉; ▪适用于流动性差的塑料,较易成型大中型制品; ▪适宜成型热固性塑料制品,制品收缩率较小、变形小、各 向性能较均匀。
▪型腔上方设有断面尺寸较大的加料室(可简 化断面形状),加料室底部有环形挤压面 (约4~5mm),型芯与加料室间隙配合; ▪余料可通过配合间隙和溢料槽溢出,制品密 度较溢式压模的好; ▪操作方便,原料计量简单,制品尺寸由型腔 决定; ▪制品脱模容易,不易与侧壁刮擦; ▪不适宜成型以布片或长纤维作填料的塑料; ▪挤压面每次应清理干净,以免变形和破坏。
二、压缩成型特点
➢压缩成型缺点:
▪与注射相比,生产周期长,效率低,厚壁件生产周期更长; ▪生产自动化程度低,粉尘多,环境条件差,劳动强度大; ▪制品溢边多,去除难,影响高度方向尺寸精度; ▪深孔和形状复杂制品难以成型; ▪压模工作条件恶劣,磨损快、寿命低;成型零件需淬硬; ▪细长成型杆和细小嵌件在压缩成型时极易变形,不宜采用压 缩成型。
三、压缩成型工艺及参数
二、压缩成型特点
➢用途:主要用于热固性塑料制品成型,也可用于流动性差的热塑性塑
料成型(聚四氟乙烯、高透明的PS、PMMA制品、超高分子量聚乙烯 等),以及橡胶制品成型等。
➢热固性料成型:模具加热、效率低。
▪原料:热固性料除树脂外,含大量填料、固化剂、固化促进剂、润滑剂、 着色剂等,塑化前流动性差、填充难; ▪原料形状:粉状、粒状、片状、团状、碎屑状、纤维状等; ▪成型:模具敞开状态加料,边加热加压边合模,最终完全闭合,加压直 接、填充密实。
6、半溢式压缩模
➢半溢式压模改进: ▪将加料腔制成可移动式,方便挤压面和模具型腔的清理。
7、多型腔压缩模
➢多型腔压模:如图,可为溢式或半溢式结构,图a)、b) 需对每个型腔单独加料,个别型腔损坏不影响模具工作。
7、多型腔压缩模
➢为方便多腔模加料,可 采用右图所示的加料器 快速加料。
➢多腔共用加料室有利于 缩小模具尺寸,方便加料, 但边角的型腔易缺料。
图5-5 半固定式压缩模具 1—压板;2—凸模;3—导柱;4—型芯;5—手柄;
6—导轨;7—凹模
3、固定式压缩模
(按压模在压力机上的固定方式分类)
(二)、压缩模具分类
4、溢式压缩模
➢特点: ▪无加料室,模腔高度约等于制品高度; ▪凸、凹模无直接配合,多余料极易溢出; ▪挤压面对溢料阻力小,制品密度低,力 学性能差; ▪不适用于高压缩率的材料成型,最好用 粒料或预压锭料成型。
5、不溢式压缩模
➢不溢式压模缺点:
▪加料室为型腔上部断面的延伸,无挤压面,溢料量很少;
▪型芯与型腔配合间隙单边约0.025~0.075mm,配合高度不宜过大, 也可将型腔侧壁制成带15′~20′的斜度,方便开模。
➢优点:
▪制品成型压力大、密实度高,性能好; ▪适于压制形状复杂、壁薄、流程较长或 深形制品,也可用于流动性差、比压高、 比容大的塑料;
压缩模类型选用原则
塑件批量大 —— 固定式模具 批量中等 —— 固定式或半固定式模具 小批量或试生产 —— 移动式模具
水平分型面模具结构简单,操作方便,优先选用。
流动性差的塑料,塑件形状复杂 ——不溢式模具 塑件高度尺寸要求高,带有小型嵌件 —— 半溢式模具 形状简单,大而扁平的盘形塑件 —— 溢式压缩模
▪特别适合压制有棉布、玻璃布、长纤维 填充的制品; ▪飞边与分型面垂直分布,便于去除。
5、不溢式压缩模 ➢不溢式压模特点:
▪因溢料量很少,加料精度直接影响制品高度尺寸,要求准确计量; ▪型芯与型腔侧壁摩擦严重,制品脱模易刮擦,改进结构见图所示; ▪不溢式压模必须设脱模机构。
6、半溢式压缩模
➢半溢式压模特点:
财富不应当是生命的目的, 它只是生活的工具。
——比 才
第五章 压缩成型工艺及模具设计
成型压缩原理
一、 压缩成型原理及特点
压缩成型原理 压缩成型特点
压缩成型过程
原料放入模具
加热加压使材料成型硬化
取出塑件
一、 压缩成型原理:
将塑料加入高温的型腔和加料室,然 后以一定的速度将模具闭合,塑料在热和压 力的作用下熔融流动,并且很快地充满整个 型腔,树脂和固化剂作用发生交联反应,生 成不熔不溶的体型化合物,塑料因而固化, 成为具有一定形状的制品,当制品完全定型 并且具有最佳性能时,即开启模具取出制品.