汽车轮毂轴承失效模式与分析方法
【精品】滚动轴承失效模式及研究方法

– 疲劳失效指滚道和滚动体上发生 碎裂,并随之产生材料碎片脱落
– 这种疲劳为逐渐发生,一旦开始 则迅速扩展,并伴随明显的振动 增加
– 更换轴承,和设计有更长疲劳寿 命的轴承
5
轴承故障原因及其解决
反向载荷
– 角接触轴承的设计只接受一个方 向的轴向载荷
– 当方向相反时,外圈的椭圆接触 区域被削平。。。
•第一阶段
•第二阶 段 •第三阶段
•第四阶段
14
滚 动 轴 承 故 障 发 展 的 四 个 阶
段•第一阶段•只是 Nhomakorabeag SE有明显指示
•第二阶段
•g SE明显增大,开始出现 轴承零件共振频率并伴有1X 转速频率边带
•第三阶段
•A.仅出现滚动轴承故障频 率(没有1X边带频率)
•B.滚动轴承跑道圆周上出 现轻微磨损时,便出现轴 承故障频率的谐波频率
障频率尖峰 轴 承 剩 余 寿 命 大 于 B-10 规 定 的 百 分
之十(注)
注:基于百分之九十的置信度
16
滚动轴承故障发展的第二阶段
噪声略增大
轴承温度正常
超声,声发射,振动尖峰能量有大的 增大,轴承外环有缺陷
振动总量略增大(振动加速度总量和振 动速度总量)
在对数频谱上可清楚地看到轴承故障 频率,而在线性频谱上难以看到;噪 声地平明显提高
轴 承 剩 余 寿 命 小 于 B-10 规 定 的 百 分 之 五 ( 注)
注:基于百分之九十的置信度
17
滚动轴承故障发展的第三阶段
可以听到噪声 轴承温度略升高 非常高的超声,声发射,振动尖峰能
量,轴承外环有故障 振动加速度总量和振动速度总量有大
的增大 在线性频谱上清楚地看出轴承故障频
SW803146轮毂单元轴承断裂失效分析

Fal r a y i o r c u e o b Un tBe rn s S 8 3 i e An lss n F a t r fHu i u a ig W 0 6 1 4
M I a i, N n E —l WA G Mig—zo J Z i jn Y hu ,I h — u
( . uyn er gS i c n ehooyC . Ld ,u yn 4 13 , hn ;.h in ot et X nh nG op 1L oagB a n c nea dT cnlg o , t. L oag 7 09 C ia2 Z  ̄ agC ni ns icu ru i e n
9
2 化 学成分
采用直读光谱仪 对外圈化学成分进行 测定 , 结果见表 1 符合 G / 2 -20 ( , B T1 2 07 弹簧钢》 2 ( 标准 的规 定 。
Байду номын сангаас
作 者简 介 : 梅亚 莉 , , 女 高级 工 程 师 , 主要 从 事 轴 承材 料 、 热 处理工艺研 究和轴 承失效分析 。
me r l n fo trrn .T e r s l h w t a h rcu e f i r fh b u i b ai g i man y c u e y t e r s t c p a e o u e i g h e u t s o h tt e f t r al e o u n t e rn s i s a u i l a s d b h e t s r k g oe h n a eh l. i Ke r s u e rn ;o trrn ;s e 5 y wo d :h b b ai g u e g t l Mn;i d ci n q e c ig;f cu e fi r i e 6 n u t u n hn o r tr al e;s rn a e h l a u h k g oe i
滚动轴承常见的失效形式和原因分析范文

滚动轴承常见的失效形式及原因分析+浪逐风尖2008-11-05 10:55滚动轴承在使用过程中,由于很多原因造成其性能指标达不到使用要求时就产生了失效或损坏.常见的失效形式有疲劳剥落、磨损、塑性变形、腐蚀、烧伤、电腐蚀、保持架损坏等。
一,疲劳剥落疲劳有许多类型,对于滚动轴承来说主要是指接触疲劳。
滚动轴承套圈各滚动体表面在接触应力的反复作用下,其滚动表面金属从金属基体呈点状或片状剥落下来的现象称为疲劳剥落。
点蚀也是由于材料疲劳引起一种疲劳现象,但形状尺寸很小,点蚀扩展后将形成疲劳剥落。
疲劳剥落的形态特征一般具有一定的深度和面积,使滚动表面呈凹凸不平的鳞状,有尖锐的沟角.通常呈显疲劳扩展特征的海滩装纹路.产生部位主要出现在套圈和滚动体的滚动表面.轴承疲劳失效的机理很复杂,也出现了多种分析理论,如最大静态剪应力理论、最大动态剪应力理论、切向力理论、表面微小裂纹理论、油膜剥落理论、沟道表面弯曲理论、热应力理论等。
这些理论中没有一个理论能够全面解释疲劳的各种现象,只能对其中的部分现象作出解释。
目前对疲劳失效机理比较统一的观点有:1、次表面起源型次表面起源型认为轴承在滚动接触部位形成油膜的条件下运转时,滚动表面是以内部(次表面)为起源产生的疲劳剥落。
2、表面起源型表面起源型认为轴承在滚动接触部位未形成油膜或在边界润滑状态下运转时,滚动表面是以表面为起源产生的疲劳剥落。
3、工程模型工程模型认为在一般工作条件下,轴承的疲劳是次表面起源型和表面起源型共同作用的结果。
疲劳产生的原因错综复杂,影响因素也很多,有与轴承制造有关的因素,如产品设计、材料选用、制造工艺和制造质量等;也有与轴承使用有关的因素,如轴承选型、安装、配合、润滑、密封、维护等。
具体因素如下:A、制造因素1、产品结构设计的影响产品的结构设计是根据使用性能目标值来确定的,这些目标值如载荷容量、寿命、精度、可靠性、振动、磨损、摩擦力矩等。
在设计时,由于各种原因,会造成产品设计与使用的不适用或脱节,甚至偏离了目标值,这种情况很容易造成产品的早期失效。
浅谈轴承失效原因分析

轴承失效原因分析滚动轴承在使用过程中,由于很多原因造成其性能指标达不到使用要求时就产生了失效或损坏.常见的失效形式有疲劳剥落、磨损、塑性变形、腐蚀、烧伤、电腐蚀、保持架损坏等。
一,疲劳剥落疲劳有许多类型,对于滚动轴承来说主要是指接触疲劳。
滚动轴承套圈各滚动体表面在接触应力的反复作用下,其滚动表面金属从金属基体呈点状或片状剥落下来的现象称为疲劳剥落。
点蚀也是由于材料疲劳引起一种疲劳现象,但形状尺寸很小,点蚀扩展后将形成疲劳剥落。
疲劳剥落的形态特征一般具有一定的深度和面积,使滚动表面呈凹凸不平的鳞状,有尖锐的沟角.通常呈显疲劳扩展特征的海滩装纹路.产生部位主要出现在套圈和滚动体的滚动表面.轴承疲劳失效的机理很复杂,也出现了多种分析理论,如最大静态剪应力理论、最大动态剪应力理论、切向力理论、表面微小裂纹理论、油膜剥落理论、沟道表面弯曲理论、热应力理论等。
这些理论中没有一个理论能够全面解释疲劳的各种现象,只能对其中的部分现象作出解释。
目前对疲劳失效机理比较统一的观点有:1、次表面起源型次表面起源型认为轴承在滚动接触部位形成油膜的条件下运转时,滚动表面是以内部(次表面)为起源产生的疲劳剥落。
2、表面起源型表面起源型认为轴承在滚动接触部位未形成油膜或在边界润滑状态下运转时,滚动表面是以表面为起源产生的疲劳剥落。
3、工程模型工程模型认为在一般工作条件下,轴承的疲劳是次表面起源型和表面起源型共同作用的结果。
疲劳产生的原因错综复杂,影响因素也很多,有与轴承制造有关的因素,如产品设计、材料选用、制造工艺和制造质量等;也有与轴承使用有关的因素,如轴承选型、安装、配合、润滑、密封、维护等。
具体因素如下:A、制造因素1、产品结构设计的影响产品的结构设计是根据使用性能目标值来确定的,这些目标值如载荷容量、寿命、精度、可靠性、振动、磨损、摩擦力矩等。
在设计时,由于各种原因,会造成产品设计与使用的不适用或脱节,甚至偏离了目标值,这种情况很容易造成产品的早期失效。
滚动轴承常见失效形式及原因分析
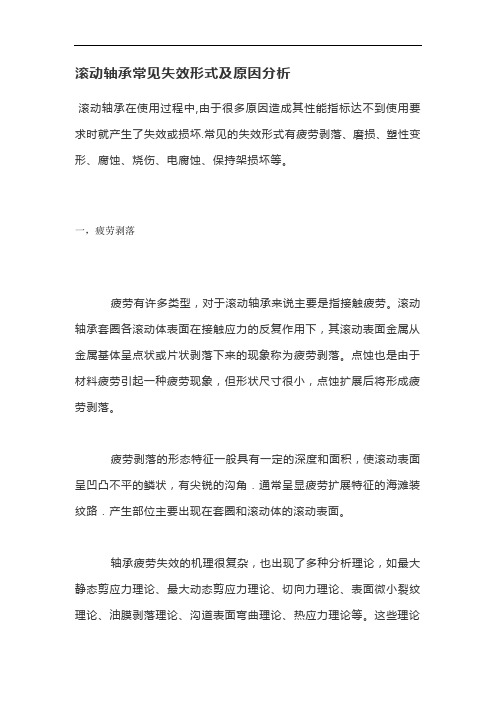
滚动轴承常见失效形式及原因分析滚动轴承在使用过程中,由于很多原因造成其性能指标达不到使用要求时就产生了失效或损坏.常见的失效形式有疲劳剥落、磨损、塑性变形、腐蚀、烧伤、电腐蚀、保持架损坏等。
一,疲劳剥落疲劳有许多类型,对于滚动轴承来说主要是指接触疲劳。
滚动轴承套圈各滚动体表面在接触应力的反复作用下,其滚动表面金属从金属基体呈点状或片状剥落下来的现象称为疲劳剥落。
点蚀也是由于材料疲劳引起一种疲劳现象,但形状尺寸很小,点蚀扩展后将形成疲劳剥落。
疲劳剥落的形态特征一般具有一定的深度和面积,使滚动表面呈凹凸不平的鳞状,有尖锐的沟角.通常呈显疲劳扩展特征的海滩装纹路.产生部位主要出现在套圈和滚动体的滚动表面。
轴承疲劳失效的机理很复杂,也出现了多种分析理论,如最大静态剪应力理论、最大动态剪应力理论、切向力理论、表面微小裂纹理论、油膜剥落理论、沟道表面弯曲理论、热应力理论等。
这些理论中没有一个理论能够全面解释疲劳的各种现象,只能对其中的部分现象作出解释。
目前对疲劳失效机理比较统一的观点有:>>>>1、次表面起源型次表面起源型认为轴承在滚动接触部位形成油膜的条件下运转时,滚动表面是以内部(次表面)为起源产生的疲劳剥落。
>>>>2、表面起源型表面起源型认为轴承在滚动接触部位未形成油膜或在边界润滑状态下运转时,滚动表面是以表面为起源产生的疲劳剥落。
>>>>3、工程模型工程模型认为在一般工作条件下,轴承的疲劳是次表面起源型和表面起源型共同作用的结果。
疲劳产生的原因错综复杂,影响因素也很多,有与轴承制造有关的因素,如产品设计、材料选用、制造工艺和制造质量等;也有与轴承使用有关的因素,如轴承选型、安装、配合、润滑、密封、维护等。
具体因素如下:(1)制造因素a.产品结构设计的影响产品的结构设计是根据使用性能目标值来确定的,这些目标值如载荷容量、寿命、精度、可靠性、振动、磨损、摩擦力矩等。
滚动轴承常见的失效形式及原因
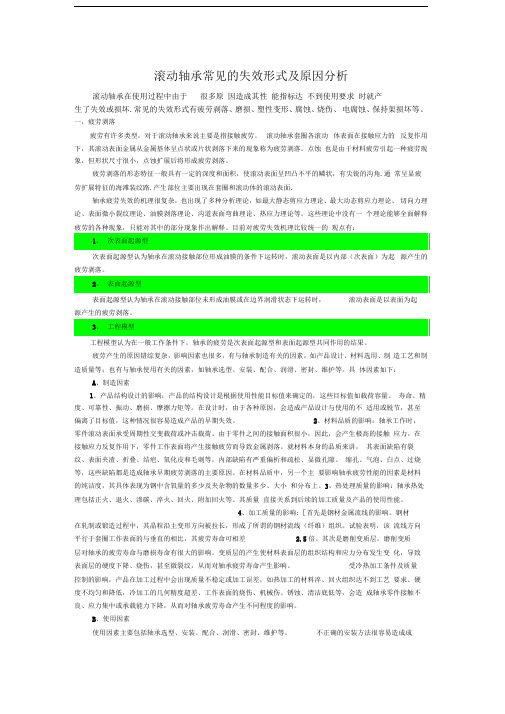
滚动轴承常见的失效形式及原因分析滚动轴承在使用过程中由于很多原因造成其性能指标达不到使用要求时就产生了失效或损坏.常见的失效形式有疲劳剥落、磨损、塑性变形、腐蚀、烧伤、电腐蚀、保持架损坏等。
一,疲劳剥落疲劳有许多类型,对于滚动轴承来说主要是指接触疲劳。
滚动轴承套圈各滚动体表面在接触应力的反复作用下,其滚动表面金属从金属基体呈点状或片状剥落下来的现象称为疲劳剥落。
点蚀也是由于材料疲劳引起一种疲劳现象,但形状尺寸很小,点蚀扩展后将形成疲劳剥落。
疲劳剥落的形态特征一般具有一定的深度和面积,使滚动表面呈凹凸不平的鳞状,有尖锐的沟角.通常呈显疲劳扩展特征的海滩装纹路.产生部位主要出现在套圈和滚动体的滚动表面.轴承疲劳失效的机理很复杂,也出现了多种分析理论,如最大静态剪应力理论、最大动态剪应力理论、切向力理论、表面微小裂纹理论、油膜剥落理论、沟道表面弯曲理论、热应力理论等。
这些理论中没有一个理论能够全面解释疲劳的各种现象,只能对其中的部分现象作出解释。
目前对疲劳失效机理比较统一的观点有:次表面起源型认为轴承在滚动接触部位形成油膜的条件下运转时,滚动表面是以内部(次表面)为起源产生的疲劳剥落。
表面起源型认为轴承在滚动接触部位未形成油膜或在边界润滑状态下运转时,滚动表面是以表面为起源产生的疲劳剥落。
工程模型认为在一般工作条件下,轴承的疲劳是次表面起源型和表面起源型共同作用的结果。
疲劳产生的原因错综复杂,影响因素也很多,有与轴承制造有关的因素,如产品设计、材料选用、制造工艺和制造质量等;也有与轴承使用有关的因素,如轴承选型、安装、配合、润滑、密封、维护等。
具体因素如下:A、制造因素1、产品结构设计的影响:产品的结构设计是根据使用性能目标值来确定的,这些目标值如载荷容量、寿命、精度、可靠性、振动、磨损、摩擦力矩等。
在设计时,由于各种原因,会造成产品设计与使用的不适用或脱节,甚至偏离了目标值,这种情况很容易造成产品的早期失效。
滚动轴承常见的失效形式及原因

滚动轴承常见的失效形式及原因滚动轴承常见的失效形式及原因分析滚动轴承在使用过程中由于很多原因造成其性能指标达不到使用要求时就产生了失效或损坏.常见的失效形式有疲劳剥落、磨损、塑性变形、腐蚀、烧伤、电腐蚀、保持架损坏等。
一,疲劳剥落疲劳有许多类型,对于滚动轴承来说主要是指接触疲劳。
滚动轴承套圈各滚动体表面在接触应力的反复作用下,其滚动表面金属从金属基体呈点状或片状剥落下来的现象称为疲劳剥落。
点蚀也是由于材料疲劳引起一种疲劳现象,但形状尺寸很小,点蚀扩展后将形成疲劳剥落。
疲劳剥落的形态特征一般具有一定的深度和面积,使滚动表面呈凹凸不平的鳞状,有尖锐的沟角.通常呈显疲劳扩展特征的海滩装纹路.产生部位主要出现在套圈和滚动体的滚动表面.轴承疲劳失效的机理很复杂,也出现了多种分析理论,如最大静态剪应力理论、最大动态剪应力理论、切向力理论、表面微小裂纹理论、油膜剥落理论、沟道表面弯曲理论、热应力理论等。
这些理论中没有一个理论能够全面解释疲劳的各种现象,只能对其中的部分现象作出解释。
目前对疲劳失效机理比较统一的观点有:1、次表面起源型次表面起源型认为轴承在滚动接触部位形成油膜的条件下运转时,滚动表面是以内部(次表面)为起源产生的疲劳剥落。
2、表面起源型表面起源型认为轴承在滚动接触部位未形成油膜或在边界润滑状态下运转时,滚动表面是以表面为起源产生的疲劳剥落。
3、工程模型工程模型认为在一般工作条件下,轴承的疲劳是次表面起源型和表面起源型共同作用的结果。
疲劳产生的原因错综复杂,影响因素也很多,有与轴承制造有关的因素,如产品设计、材料选用、制造工艺和制造质量等;也有与轴承使用有关的因素,如轴承选型、安装、配合、润滑、密封、维护等。
具体因素如下:A、制造因素1、产品结构设计的影响:产品的结构设计是根据使用性能目标值来确定的,这些目标值如载荷容量、寿命、精度、可靠性、振动、磨损、摩擦力矩等。
在设计时,由于各种原因,会造成产品设计与使用的不适用或脱节,甚至偏离了目标值,这种情况很容易造成产品的早期失效。
滚动轴承常见的失效形式及原因

滚动轴承常见的失效形式及原因滚动轴承常见的失效形式及原因分析滚动轴承在使用过程中由于很多原因造成其性能指标达不到使用要求时就产生了失效或损坏.常见的失效形式有疲劳剥落、磨损、塑性变形、腐蚀、烧伤、电腐蚀、保持架损坏等。
疲劳有许多类型,对于滚动轴承来说主要是指接触疲劳。
滚动轴承套圈各滚动体表面在接触应力的反复作用下,其滚动表面金属从金属基体呈点状或片状剥落下来的现象称为疲劳剥落。
点蚀也是由于材料疲劳引起一种疲劳现象,但形状尺寸很小,点蚀扩展后将形成疲劳剥落。
疲劳剥落的形态特征一般具有一定的深度和面积,使滚动表面呈凹凸不平的鳞状,有尖锐的沟角. 通常呈显疲劳扩展特征的海滩装纹路.产生部位主要岀现在套圈和滚动体的滚动表面.轴承疲劳失效的机理很复杂,也岀现了多种分析理论,如最大静态剪应力理论、最大动态剪应力理论、切向力理论、表面微小裂纹理论、油膜剥落理论、沟道表面弯曲理论、热应力理论等。
这些理论中没有一个理论能够全面解释疲劳的各种现象,只能对其中的部分现象作出解释。
目前对疲劳失效机理比较统一的观点有:次表面起源型认为轴承在滚动接触部位形成油膜的条件下运转时,滚动表面是以内部(次表面)为起源产生的疲劳剥落。
表面起源型认为轴承在滚动接触部位未形成油膜或在边界润滑状态下运转时,滚动表面是以表面为起源产生的疲劳剥落。
工程模型认为在一般工作条件下,轴承的疲劳是次表面起源型和表面起源型共同作用的结果。
疲劳产生的原因错综复杂,影响因素也很多,有与轴承制造有关的因素,如产品设计、材料选用、制造工艺和制造质量等;也有与轴承使用有关的因素,如轴承选型、安装、配合、润滑、密封、维护等。
具■体因素如下:A制造因素|1 、产品结构设计的影响:产品的结构设计是根据使用性能目标值来确定的,这些目标值如载荷容量、寿命、精度、可靠性、振动、磨损、摩擦力矩等。
在设计时,由于各种原因,会造成产品设计与使用的不适用或脱节,甚至偏离了目标值,这种情况很容易造成产品的早期失效。
- 1、下载文档前请自行甄别文档内容的完整性,平台不提供额外的编辑、内容补充、找答案等附加服务。
- 2、"仅部分预览"的文档,不可在线预览部分如存在完整性等问题,可反馈申请退款(可完整预览的文档不适用该条件!)。
- 3、如文档侵犯您的权益,请联系客服反馈,我们会尽快为您处理(人工客服工作时间:9:00-18:30)。
汽车轮毂轴承失效模式与分析方法摘要:汽车轮毂轴承开发阶段需要进行多种性能试验,通过轮毂轴承失效的案例,分析轴承早期失效模式,找出其根本原因,验证产品设计合理与否。
针对这些失效模式,归纳梳理了轮毂轴承失效分析的系列方法,为深入研究轮毂轴承的失效机理,改善产品质量提供参考。
关键词:轮毂轴承; 性能试验; 失效模式; 分析方法Failure Mode and Analysis Method for Automobile HubBearingsAbstract:The development stage of automobile hub bearings is required to conduct various performance tests.The initial failure mode for bearings is analyzed through failure case of hub bearings,and the root cause is found out to verify the rationality of product design.Aiming at these failure modes,a series method for failure analysis of hub bearings is summarized,which provides a reference for in-depth study of failure mechanism for hub bearings and improvement of product quality.Key words: hub bearing; performance test; failure mode; analysis method;0 引言轿车轮毂轴承是汽车底盘上的一个重要组件,其是否能够平稳可靠地运转直接关系到行车的安全。
普通轴承失效模式识别和分析方法的研究已有相关学者做过大量的工作[1-4]。
而轮毂轴承的失效分析起步较晚,近年来随着汽车工业的迅猛发展而逐渐受到重视。
文献[5]对轮毂轴承载荷谱和失效机理做了深入探索。
文献[6-7]分别就轮毂轴承的失效分析步骤及其对策与诊断方法进行了研究。
由于轮毂轴承失效模式多种多样,且相关研究工作存在一定的局限性,故在轮毂轴承开发阶段就需要进行各种性能试验,通过早期失效分析,找出其失效原因,为改善轮毂轴承的品质提供参考。
1 性能试验范围轮毂轴承开发验证的台架试验包括: 一般耐久性试验、高速耐久性试验、疲劳强度试验、密封试验、刚性试验、动摩擦试验及冲击试验等。
设计的样品只有顺利通过台架试验,才能在主机厂所指定的路试场进行道路试验。
道路试验综合了台架试验的各种考评项目,能够真实反映实际工况。
不同的主机厂有各自的台架试验和道路试验规范,并明确了评判标准。
当试验样品没有达到试验规范或标准的相关要求时,认为样品发生了早期失效,该样品便属于失效分析的对象,需查找出失效的原因。
2 失效模式根据国内、外著名轴承厂商,如洛阳轴研科技,浙江万向精工,SKF,FAG,NSK 及 NTN 等的统计,轮毂轴承早期失效模式有腐蚀、压痕、烧伤、裂纹和剥落等多种,现大致归纳如图 1 所示[6]。
通过大量失效分析工作的统计发现,同一种失效模式可能是由不同的单一原因引起的,也可能是由各种原因综合作用的结果,因此,为分析轮毂轴承的失效机理,需要具备较全面的分析手段。
3 失效分析过程开发阶段轮毂轴承的早期失效,即图1 所示的各种失效模式通常来源于5 个方面: (1) 产品设计不合理; (2) 工艺过程未能保证设计要求; (3)试验设备不稳定; (4) 轴承安装不当; (5) 工作载荷过大,超出产品承受能力。
针对这些方面,一般的分析过程如下。
3.1原始信息收集当失效轴承被委托给分析室进行分析时,非常重要的一环是分析者首先要收集失效件的原始信息。
原始信息一般包括: 设计图纸、工艺图纸、车型参数、试验规范、试验设备、工装信息、失效时试验员所做的轴承异常运转情况记录及失效样品原始检测报告。
其中失效样品原始检测报告应包括轮毂轴承组件中各零件(外圈、内圈、钢球、密封圈、保持架和润滑脂) 的材质报告和相关尺寸检测报告、装配件的相关检测结果等。
由于失效件的原始状态已经受到极大破坏,故原始信息的收集对分析者非常重要,可以说收集信息的完备性决定着分析结果的准确性。
3.2 设计确认设计确认的目的在于以现行轮毂轴承行业的水准来评判轴承设计的合理性。
为完成产品的设计确认,分析者需要对轮毂轴承设计理论[8]有一定深度的了解,并能够运用一些辅助工具,如数学计算方法、小程序编译,相关辅助软件MATALAB,ANSYS,ABAQUS 及MSC.FATIGUE 等; 根据所提供的设计图纸和试验载荷谱信息[9],对产品设计工程师所完成的设计进行确认。
需要确认的项目包括: 负游隙、静强度、刚性、滚道疲劳寿命、滚道挡边高、接触应力、疲劳强度和密封结构等。
由于目前广泛应用的第1代、第2代和第3代轮毂轴承结构大不相同,故在设计确认上也会存在一定的差异。
第1代、第2代和第3代轮毂轴承的装车差异如图2所示。
相比于第1代,集成程度较高的第2代和第3代轴承存在与凸缘心轴及转向节的配合,由于其通过锁紧螺母进行预紧,因此会影响到最终的装车游隙。
游隙的设计应以最终装车状态的游隙作为目标,通常装车状态的理想游隙为-0.03 ~-0.06 mm。
以带凸缘的第2代或第3代轮毂轴承为例,有些确认项是相互矛盾的。
在客户要求轮毂轴承质量控制在某一特定量的前提下,需要在滚道疲劳寿命与所需强度间进行有效的平衡。
通过增大钢球尺寸提高额定动载荷来强化滚道疲劳寿命就会降低轴承的强度,此时,应把轴承强度放在首位考虑,其属于关乎安全性的重要项目。
3.3 工艺过程确认在确定产品无设计缺陷后,需要以设计图纸和企业规范作为评价标准进行工艺过程确认,以明确设计是否得到保证。
对于轴承制造商而言,轮毂轴承套圈材料、密封圈和保持架一般为外购件,套圈较关键的终加工工艺则由轴承制造商完成。
工艺过程确认主要以相关检测报告为基础,根据检测报告逐一核实是否达到设计要求。
需要核实的项目主要有:( 1) 原材料信息。
所提供的钢材一般为热轧状态,需要对材料的元素成分、氧含量、非金属夹杂物、晶粒度及力学性能做出核实。
(2) 热处理信息。
原材料在加工过程中进行的相关热处理,如正火和淬火,需要核实其基体和滚道的组织、硬度( 梯度) 及锻造流线是否满足要求。
(3) 成品零件尺寸。
包括滚道沟曲率半径、沟径、沟间距、圆度、轮廓度、表面粗糙度、密封口径及其圆度、密封圈各唇口配合直径、唇口结构尺寸、滚道挡边高度和重要外轮廓尺寸等的核实。
(4) 外购件特性。
查看外购件的检测报告,确认其是否满足使用要求。
如密封圈的材质、拉伸特性、硬度,润滑脂的九大性能指标———黏度、高低温性能、极压性与抗磨性、抗水性、防腐性、胶体安定性、氧化安定性和机械安定性[10]。
(5) 装配件检测结果。
装配件的游隙和凸缘跳动均会对轴承滚道寿命产生较大影响; 装配件压装密封圈的平行差会影响到产品的密封性能,故均需要核实其是否满足设计要求。
在设计得到确认、失效样品原始状态的工艺信息核实无误及试验过程状态明确的前提下,基本能够推断出轮毂轴承是否具备通过各项性能试验的能力。
3.4 分析流程分析者接到失效件后,需要对失效件做相应的处理,从失效件的失效模式和损伤痕迹,并结合设计及工艺过程明确失效的原因。
失效件在试验前的原始状态通过收集的数据得到分析后,对试验失效件也要进行一些辅助检测,旨在对比试验前、后及设计标准之间的差异程度。
如果有差异,还需确定差异是否在可接受范围; 如果某项指标不在经验值范围内,则应作为失效的关注点有所侧重[11]。
失效轴承检查分析流程和所用仪器见表1。
根据国家标准、行业标准或企业标准进行相关检测。
针对某型号轮毂轴承进行的失效分析项目,即表1中的实施项目并非全部为必须的,而是需要根据逐步的观察、分析确定。
有些失效原因能够较早、较容易被发现,而有些则较复杂,隐藏较深,基本要经历整个过程才能够发现。
4 分析案例以M型轮毂轴承为例,安装于路试车辆上进行道路试验。
车辆行驶64 000 km(要求100 000km) 后左前轮出现异常声。
经拆套发现: 外圈滚道外侧剥落,润滑脂变成棕黄色。
按照上述流程逐步检测排查,最终确定为轴承密封失效。
轴承密封失效分析的主要信息如下。
4.1 润滑脂含水率按照卡尔费休法对提取的润滑脂含水率进行检测,发现其含水率严重超标,检测结果见表2。
4.2 沟道剥落通过观察轴承沟道情况(图3) 发现,的确是轴承密封发生了失效,导致泥水侵入轴承中,引起轴承润滑不良,最终导致沟道产生早期剥落。
4.3 密封圈磨损在体视镜下对密封圈进行放大观察,发现外密封圈存在明显的偏磨损情况(图4a和图4b) 。
对密封圈制样后在工具显微镜下检测其尺寸,也发现外密封圈存在偏磨损,图4c和图4d为密封圈上2个不同位置的磨损情况。
通过查看同批装车的外密封圈尺寸检测报告可知,密封圈尺寸精度较好,符合要求。
通过了解外密封圈的压装过程,经分析最终判定为外密封圈存在压装歪斜,导致平行差不好,使泥水经由密封圈缝隙侵入到轴承中,导致轴承提前失效。
为此,建议针对存在的超差问题改进密封圈压装装置,并且产品由抽检改为全检,确保外密封圈压装平行差符合要求。
5 结束语对轮毂轴承开发阶段涉及的各种性能试验及失效模式进行了归纳梳理,详细介绍了轮毂轴承失效分析的步骤与方法,并以某一密封失效的分析案例进行了验证。
结果表明,该分析方法可为相关人员开展轴承失效模式的机理研究提供参考。
[参考文献](References)[1]常晏铭,吴张永.浅析振动分析技术在滚动轴承故障诊断中的应用[J].维修与改造,2007( 4) : 56 -60.[2]赵传国.滚动轴承失效分析概论[J].轴承,1996(1) : 39 -45.[3]陆骥.滚动轴承的失效分析[D].上海: 复旦大学,2006.[4]张广.滚动轴承烧损的模式分析[J].内蒙古科技与经济,2007( 15) : 78 -79.[5]张雪萍.轿车轮毂轴承失效机理的理论与实验研究[D].上海: 上海交通大学,2002.[6]杨林.汽车轮毂轴承早期失效分析及试验研究[D].广州: 华南理工大学,2012.[7]董建鹏.乘用车前轮毂轴承失效分析[D].广州: 华南理工大学,2012.[8]Harris T A,Kotzalas M N.滚动轴承分析[M].罗继伟,马伟,杨咸启,等,译.北京: 机械工业出版社,2010.[9]黄德杰.轿车轮毂轴承耐久性计算与试验系统开发[D].杭州: 浙江工业大学,2011.[10]Schlobohm RT.Formulating Grease to Minimize Fret-ting Corrosion[J].NLGI Spokensman,1976,40 ( 4) :131 -135.[11]GB/T 6283—2008,化工产品中水分含量的测定卡尔.费休法( 通用方法)[S].。