6 粗甲醇的精制解析
甲醇合成的工艺方法介绍

甲醇合成的工艺方法介绍自1923年开始工业化生产以来,甲醇合成的原料路线经历了很大变化。
20世纪50年代以前多以煤和焦碳为原料;50年代以后,以天然气为原料的甲醇生产流程被广泛应用;进入60 年代以来,以重油为原料的甲醇装置有所发展。
对于我国,从资源背景来看,煤炭储量远大于石油、天然气储量,随着世界石油资源的紧缺、油价的上涨和我国大力发展煤炭洁净利用技术的背景下,在很长一段时间内煤是我国甲醇生产最重要的原料。
下面简要介绍一下甲醇生产的各种方法。
按生产原料不同可将甲醇合成方法分为合成气(CO+H2方法和其他原料方法。
一、合成气(CO+H2生产甲醇的方法以一氧化碳和氢气为原料合成甲醇工艺过程有多种。
其发展的历程与新催化剂的应用,以及净化技术的进展是分不开的。
甲醇合成是可逆的强放热反应,受热力学和动力学控制,通常在单程反应器中,CO和CO2的单程转化率达不到100%,反应器出口气体中,甲醇含量仅为6~12%,未反应的CO、CO2和H2需与甲醇分离,然后被压缩到反应器中进入一步合成。
为了保证反应器出口气体中有较高的甲醇含量,一般采用较高的反应压力。
根据采用的压力不同可分为高压法、中压法和低压法三种方法。
1、高压法即用一氧化碳和氢在高温(340~420℃高压(30.0~50.0MPa下使用锌-铬氧化物作催化剂合成甲醇。
用此法生产甲醇已有八十多年的历史,这是八十年代以前世界各国生产甲醇的主要方法。
但高压法生产压力过高、动力消耗大,设备复杂、产品质量较差。
其工艺流程如图所示。
经压缩后的合成气在活性炭吸附器1中脱除五羰基碳后,同循环气一起送入管式反应器2中,在温度为350℃和压力为30.4MPa下,一氧化碳和氢气通过催化剂层反应生成粗甲醇。
含粗甲醇的气体经冷却器冷却后,迅速送入粗甲醇分离器3中分离,未反应的一氧化碳与氢经压缩机压缩循环回管式反应器2。
冷凝后的粗甲醇经粗甲醇储槽4进入精馏工序,在粗分离塔5顶部分离出二甲醚和甲酸甲酯及其他低沸点不凝物,重组分则在精分离塔6中除去水和杂醇,得到精制的甲醇。
粗甲醇精制的操作技术原理
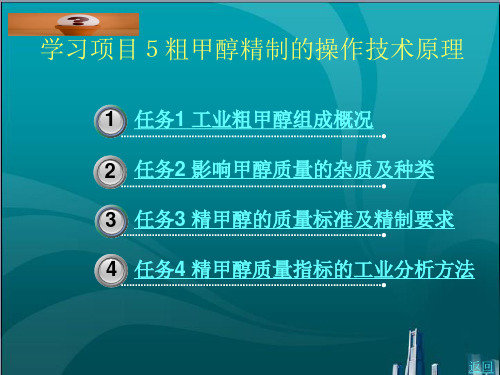
但水与其中许多有机杂质混溶,或形成水-甲醇-有机物的多元恒沸物, 使彻底分离水分变得困难,同时难免与有机杂质甚至甲醇一起被排除, 而造成精制过程中甲醇的流失。
三、有机杂质 有机杂质包含醇、醛、酮、醚、酸、烷烃等有机物,根据其沸点,将其
分为轻组分和重组分。精制的关键就是怎样将甲醇与这些杂质有效地进 行分离,使精甲醇中含有少量的有机杂质。 1.异丁醛 亦称2-甲基丙醛,其分式
上一页 下一页 返回
任务6 甲醇精馏操作的基本原理
以一定压力下混合液的沸点组成图,形象地表示甲醇-水系统的气液相 平衡关系,来分析上述的精馏原理。甲醇-水为非理想溶液, 图1.5. 1为常压下甲醇-水的沸点组成(由实验测得)。曲线1为气相线,线 上每一点均为饱和蒸汽;曲线2为液相线,线上每一点均为饱和液体。
4.甲酸 甲酸俗称蚁酸,是无色有刺激性气味的液体,沸点100.5℃,能与水、
乙醇、乙醚混溶。甲酸的结构较特殊,是一个羰基和一个氢原子直接相 连,所以可以把它看作在分子中即含有羰基又具醛基。
上一页 下一页 返回
任务2 影响甲醇质量的杂质及种类
甲酸既有羰基的一般性质,也有醛的某些性质,如甲酸具有较强的酸性, 又具有还原性。甲酸可被一般氧化剂氧化生成二氧化碳和水:
粗甲醇的合成不论采用锌铬催化剂或铜基催化剂,从热力学角度分析都 是最不利的反应。因此,粗甲醇纯度受催化剂选择性的限制,在生成主 产品甲醇外,还伴随着一系列副反应。粗甲醇的组成相当复杂,用色谱 或色谱-质谱联用仪器对粗甲醇的组成进行分析,其组成主要是甲醇和 水,还含有醇、醛、酮、醚、酸、酯、烷烃、有机胺等四十多种有机杂 质。
下一页 返回
任务3 精甲醇的质量标准及精制要求
一、酸碱度分析方法 1.测定原理 甲醇试样用不含二氧化碳的水稀释,加入溴百里香酚兰指示剂,试样呈
粗甲醇精制的生产工艺流程及主要设备

上一页 下一页 返回
第一节 常见症状、体征的辨识
(1 ① 腹膜急性炎症:最常由胃肠穿孔引起。特点是有定位的持续性锐痛,
腹部加压、改变体位可使疼痛加剧,病变部位有压痛、反跳痛与肌紧张, ② ③ 空腔脏器梗阻或扩张:如肠梗阻、胆道蛔虫症、泌尿道或胆道结石梗
精甲醇的采出口在塔顶侧,有四处,可根据塔的负荷及质量状况调节其 高度。一般采出口上端保留8层板,以确保降低精甲醇中的轻组分含量。 精甲醇液相采出,经冷却至常温后送至仓库。
上一页 下一页 返回
任务1 传统高压法粗甲醇的精制工艺流 程
在塔下部第6~10块板处,于85℃ ~92℃采出异丁基油馏分,其 采出量为粗甲醇采出量的2%左右。
上一页 下一页 返回
第一节 常见症状、体征的辨识
② 大学生另一常见的胸痛病因是胸部皮肤的带状疱疹。此病最先出现的 症状是胸痛,甚至很剧烈,痛后3天左右局部皮肤出现疹子。未出疹之 前易误诊为其他疾病。带状疱疹是一种嗜神经病毒感染,常沿肋间神经
③ 胸痛发生后,需寻求病因,以免延误原发病的诊治。青年学生的胸膜 炎、气胸常常以胸痛为主,需到医院求诊,胸透是必不可少的检查项目。
从预蒸馏塔塔底出来的预后甲醇,经第一主精馏塔(即加压塔) 进料泵 加压后,进入加压塔精馏,加压塔为85块浮阀塔。塔顶蒸气进入冷凝 再沸器中,这样即可用加压塔气相甲醇的冷凝潜热来加热第二精馏塔 (即常压塔) 的塔釜,被冷凝的甲醇进入回流槽,在其中稍加冷却,一 部分由加压塔回流泵升压至0.8MPa送至加压塔塔顶作回流液,其余 部分经加压塔甲醇冷却器冷却到40℃后作为成品送至精甲醇计量槽。
冷凝以后,大部分的甲醇、水汽和挥发性较低的组分冷凝下来,经回流 罐4以泵送回塔顶回流。
粗甲醇的精馏
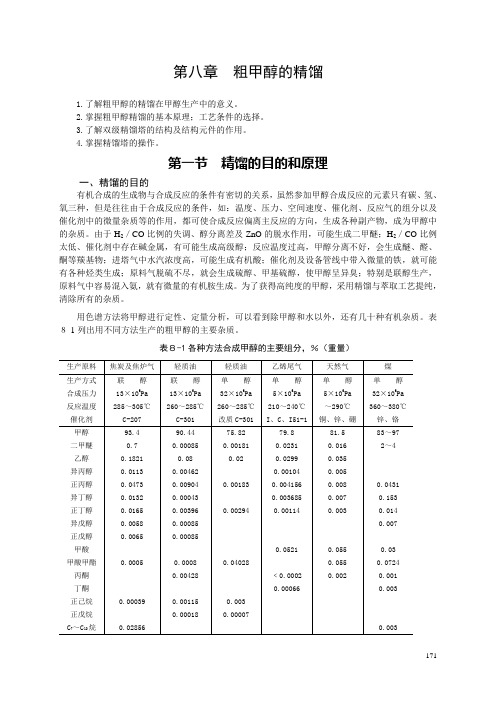
第八章粗甲醇的精馏1.了解粗甲醇的精馏在甲醇生产中的意义。
2.掌握粗甲醇精馏的基本原理;工艺条件的选择。
3.了解双级精馏塔的结构及结构元件的作用。
4.掌握精馏塔的操作。
第一节精馏的目的和原理一、精馏的目的有机合成的生成物与合成反应的条件有密切的关系,虽然参加甲醇合成反应的元素只有碳、氢、氧三种,但是往往由于合成反应的条件,如:温度、压力、空间速度、催化剂、反应气的组分以及催化剂中的微量杂质等的作用,都可使合成反应偏离主反应的方向,生成各种副产物,成为甲醇中的杂质。
由于H2/CO比例的失调、醇分离差及ZnO的脱水作用,可能生成二甲醚;H2/CO比例太低、催化剂中存在碱金属,有可能生成高级醇;反应温度过高,甲醇分离不好,会生成醚、醛、酮等羰基物;进塔气中水汽浓度高,可能生成有机酸;催化剂及设备管线中带入微量的铁,就可能有各种烃类生成;原料气脱硫不尽,就会生成硫醇、甲基硫醇,使甲醇呈异臭;特别是联醇生产,原料气中容易混入氨,就有微量的有机胺生成。
为了获得高纯度的甲醇,采用精馏与萃取工艺提纯,清除所有的杂质。
用色谱方法将甲醇进行定性、定量分析,可以看到除甲醇和水以外,还有几十种有机杂质。
表8-1列出用不同方法生产的粗甲醇的主要杂质。
表8-1各种方法合成甲醇的主要组分,%(重量)生产原料焦炭及焦炉气轻质油轻质油乙烯尾气天然气煤生产方式合成压力反应温度催化剂联醇13×106Pa285~305℃C-207联醇13×106Pa260~285℃C-301单醇32×106Pa260~285℃改质C-301单醇5×106Pa210~240℃I、C、I51-1单醇5×106Pa~290℃铜、锌、硼单醇32×106Pa360~380℃锌、铬甲醇二甲醚乙醇异丙醇正丙醇异丁醇正丁醇异戊醇正戊醇甲酸甲酸甲酯丙酮丁酮正己烷正戊烷C 7~C10烷93.40.70.18210.01130.04730.01320.01650.00580.00650.00050.000390.0285690.440.000850.080.004620.009040.000430.003960.000850.000850.00080.004280.001150.0001875.820.001810.020.001830.002940.040280.0030.0000779.80.02310.02990.001040.0041560.0036850.001140.0521﹤0.00020.0006681.50.0160.0350.0050.0080.0070.0030.0550.0550.00283~972~40.04310.1530.0140.0070.030.07240.0010.0030.003171水 5.6 8.56 23.18 24.473 18.37 6~13从表中可以看出,除水之外,各种杂质的量都很少,而从色谱图上看,杂质的峰多达40~50个。
甲醇精馏的方法

甲醇精馏的方法文件排版存档编号:[UYTR-OUPT28-KBNTL98-UYNN208]甲醇精馏的典型工艺流程甲醇精馏产生工艺有多种,分为单塔精馏,双塔精馏,三塔精馏与四塔精馏(即三塔加回收塔)(1) 单塔流程描述采用铜系催化剂低压法合成甲醇,由于粗甲醇中不仅还原性杂质的含量大大减少,而且二甲醚的含量几十倍地降低,因此在取消化学净化的同时,可将预精馏及甲醇-水-重组分的分离在一台主精馏塔内同时进行,即单塔流程,就能获得一般工业上所需要的精甲醇。
单塔流程更适用于合成甲基燃料的分离,很容易获得燃料级甲醇。
单塔流程(见图为粗甲醇产品经过一个塔就可以采出产品。
粗甲醇塔中部加料口送入,轻组分由塔顶排出,高沸点的重组分在进料板以下若塔板处引出,水从塔底排出,产品甲醇在塔顶以下若干块塔板引出。
(2) 双塔流程描述双塔工艺是由脱醚塔,甲醇精馏塔或者主塔组成。
主塔在工厂中产量在100万吨/年以下,仅仅能提供简单的过程,所以设备和投资较低。
传统的工艺流程,是最早用于30MPa压力下以锌铬催化剂合成粗甲醇的精制。
主要步骤有:中和、脱醚、预精馏脱轻组分杂质、氧化净化、主精馏脱水和重组分,最终得到精甲醇产品。
在传统工艺流程上,取消脱醚塔和高锰酸钾的化学净化,只剩下双塔精馏(预精馏塔和主精馏塔)。
其高压法锌铬催化剂合成甲醇和中、低压法铜系催化剂合成甲醇都可适用。
从合成工序来的粗甲醇入预精馏塔,此塔为常压操作。
为了提高预精馏塔后甲醇的稳定性,并尽可能回收甲醇,塔顶采用两级冷凝。
塔顶经部分冷凝后的大部分甲醇、水及少量杂质留在液相作为回流返回塔,二甲醚等轻组分(初馏分)及少量的甲醇、水由塔顶逸出,塔底含水甲醇则由泵送至主精馏塔。
主精馏塔操作压力稍高于预精馏塔,但也可以认为是常压操作,塔顶得到精甲醇产品,塔底含微量甲醇及其它重组分的水送往水处理系统(见图)。
(3) 三塔流程描述三塔工艺是由脱醚塔,加压精馏塔和常压精馏塔组成,形成二效精馏与二甲醇精馏塔甲醇产品的镏出物的混合物。
粗甲醇精制的生产工艺流程及主要设备

最早在30MPa压力下,以锌铬催化剂合成的粗甲醇的精制,其工艺 流程如下:中和、脱醚、预精馏脱轻组分杂质、氧化净化、主精馏脱水 和重组分杂质,最终得到精甲醇产品,如图2.5.1所示。
由脱醚塔底出来的脱醚甲醇,利用脱醚塔2的压力,经换热器5被预精 馏塔7的塔底液体和再沸器的冷凝水加热后,进入预精馏塔7的上部。 塔顶部加入冷凝水(或软水)进行萃取蒸馏,主要是分离不易除去的杂 质,加水后,由于水的挥发性较低,改变了关键组分在液相中的活度系 数;加水量根据粗甲醇中的杂质含量而定,一般为粗甲醇量的10%~ 20%,同时,还要参考产品的质量要求。
2.主精馏塔 主精馏塔的作用:① 将甲醇组分与水和重组分分离,得到产品精甲醇;
② 将水分离出来,并尽量降低其有机杂质的含量,排出系统;③ 分离 出重组分—异丁基油;④ 采出乙醇,制取低乙醇含量的精甲醇。
上一页 下一页 返回
任务5 精甲醇精制的主要设备
主精馏的入料口有四个,在塔的中下部(一般为第26块塔板以下), 可根据物料状况调节入料高度。精甲醇采出料口也有四个,一般在塔顶 向下数第七层板以下成品中。重组分采出在塔下部第6~12块塔板处,也 有四个采出口,可选择重组分浓集处进行采出。乙醇采出口一般在接近 入料口上方塔板上。主精馏塔的结构如图2.5.7所示。
上一页 下一页 返回
任务4 节能型粗甲醇的精制工艺流程
加压塔用低压蒸汽加热的再沸器向塔内提供热量,通过低压蒸汽的加入 量来控制塔的操作温度。加压塔操作压力约0.57MPa,塔顶操作温 度约121℃,塔底操作温度约127℃。
从加压塔塔底排出的甲醇溶液送至常压塔下部,常压塔也采用85块浮 阀塔板。由常压塔塔顶出来的甲醇蒸气经常压塔冷凝器冷凝后,进入常 压塔回流槽,一部分由常压塔回流泵加压后,送至常压塔顶作回流,其 余部分经常压塔冷却器进一步冷却后,送至精甲醇计量槽。常压塔塔顶 操作压力约0.006MPa,塔顶操作温度约65.9℃,塔底操作温 度约94.8℃。
甲醇的制备分析解析

生产现状
我国甲醇工业的发展情况我国甲醇工业始于20世纪50年代,主要是由原苏联援建的以煤为原料采用高压 法锌铬催化剂合成甲醇技术。1957年第一套锌铬催化剂高压法甲醇合成装置在吉林化学工业公司投产,设计 能力为100t/d,然后在兰州、太原、西安等地陆续建厂投产。60年代上海吴泾化工厂先后自建了以焦炭和 石脑油为原料的甲醇装置;同时南京化学工业公司研究院研制了联醇用中压铜基催化剂,推动了具有我国特色 的合成氨联产甲醇工业的发展。自2002年年初以来,我国甲醇市场受下游需求强力拉动,以及生产成本的提 高,甲醇价格一直呈现一种稳步上扬走势。甲醇市场价格最高涨幅超过100%,甲醇生产的利润相当丰厚, 效益好的厂家每吨纯利超过了1000元,因而甲醇生产厂家纷纷扩产和新建,使得我国甲醇的产能急剧增加。 2002年,我国甲醇生产能力达到4.5Mt,产量为2.31Mt,进口1.8Mt,出口量为10kt,表观消费量 为4.1Mt,占市场需求的56%;2003年生产能力5Mt,产量为3Mt,进口量为1.4Mt,出口量为50kt, 表观消费量为4.35Mt,占市场需求的69%;2004年生产能力达到7Mt,产量4.4Mt,进口量为 1.36Mt,出口量约30kt,表观消费量为5.73Mt,占市场需求的77%;2005年生产能力为10Mt,产 量达到5Mt,进口量为1.15Mt,表观消费量为6.15Mt,占市场需求的80%。2006年上半年我国共生 产甲醇3.4Mt比2005年同期增长29.7%,下半年又有2Mt的新建甲醇装置陆续竣工投产,使得2006年 我国甲醇产量突破7Mt大关,比2005年增加2Mt。同时,2006年我国的甲醇需求量仍将保持较高速度的增 长,消费量将超过7 Mt,再创历史新高。2006年我国甲醇出口(主要出口到韩国)量已超过100kt。我国现 在已成为世界第二大甲醇消费国,同时也是甲醇生产增长最快的国家,并将继续高速发展。 目前国内甲醇工业已经是供过于求,且发展趋头越来越“猛烈”,在未来5年内我国甲醇产量将新增26~ 30Mt,总生产能力将达到36~40Mt。国内许多甲醇生产企业将面临巨大的生存和发展压力。建议有关部 门加强宏观调控,适当控制国内甲醇工业建设过热的势头,应从长远角度考虑,加大甲醇下游产品的开发力度。 建议优化甲醇资源,加大甲醇出口力度,把我国甲醇企业的注意力尽快转移到甲醇下游产品的开发。
《化工生产技术》项目6 甲醇的生产

20世纪60年代中期由英国ICI公司开
发成功了铜基催化剂,根据加入助剂的
不同可分为Cu-Zn- Cr系列和Cu-Zn- Al系 列。铜基催化剂活性高、性能好,而且活 性可调(铜含量增加,催化活性提高), 适宜的反应温度为220~270℃,但铜基催 化剂对硫极为敏感,遇硫易中毒失活,且 热稳定性较差。
甲烷部分氧化 法生产甲醇, 原料便宜,工 艺流程简单, 但因生产技术 比较复杂,副 反应多,产品 分离困难,原 料利用率低, 工业上尚未广 泛应用。
由一氧化碳和 氢合成甲醇, 称为合成气法。 根据所使用的 催化剂、反应 温度和反应压 力不同,合成 气法又可分为 高压法、中压 法和低压法, 现在的大型甲 醇装置均采用 中、低压法。
反应中放出的热量必须及时移除,否则易使 催化剂温升过高,使催化剂发生熔结现象而使 催化活性下降。
铜基催化剂的热稳定性较差,控制反应温度 尤为重要。
4.2反应压力的确定
一氧化碳加氢合成甲醇的主反应是体 积缩小的反应,增加压力,有利于向正反 应方向进行。在铜基催化剂作用下,反应 压力与甲醇生成量的关系如图6-5所示。
图片6-1罐装甲醇
图片6-2煤制甲醇资源综合
国内甲醇生产企业主 要分布在具有资源优势的 西部地区,内蒙古、山东、 宁夏、陕西等地产能占比 较大,而消费市场主要集 中在东部沿海地区。
01 甲醇工业现状及发展趋势
图6-3甲醇储罐利用项目现场
国外甲醇生产能力主要分布在北美、 中南美、中东、亚洲、东欧、西欧、大洋 洲及非洲等地,美洲是世界上最大的甲醇 生产地,约占世界总生产能力的40%。
04 工艺条件的确定
一氧化碳加氢合成甲醇是放热反应,温度不同,热效应也不同。温度 越高,反应的热效应也越大。
- 1、下载文档前请自行甄别文档内容的完整性,平台不提供额外的编辑、内容补充、找答案等附加服务。
- 2、"仅部分预览"的文档,不可在线预览部分如存在完整性等问题,可反馈申请退款(可完整预览的文档不适用该条件!)。
- 3、如文档侵犯您的权益,请联系客服反馈,我们会尽快为您处理(人工客服工作时间:9:00-18:30)。
9
1、蒸汽量小 2、精甲醇采出量小 3、入料量过大 蒸汽量小 重馏分上移 轻馏份下移
10 11
12
加压塔入料 指示不准确
入料仪表损坏
13
加压塔底压力高
1、蒸汽量过大2、入料 量过大 3、泵出量过小4、塔内 产生液泛
1、减小蒸汽量2、减少入料量 3、加大泵出量4、减少蒸汽及入料量
14
运转设备停止
断电
冷凝器
冷凝器的作用是将塔顶上升的蒸汽进行冷凝,使 之成为液体,之后将一部分冷凝液从塔顶回流入 塔,以提供塔内下降的液流,使其与上升气流进 行逆流传质接触。
换 热 器
冷凝器一般安装在塔顶。
冷却器
•
再沸器 预热器
再沸器的作用是将塔内最下面的一块塔板留下的 液体进行加热,使其中的一部分液体发生气化变成 蒸汽重新会流入塔,以提供塔内上升的气流,从而 保证塔板上气、液两相的传质。 再沸器一般安装在塔底外部。
(1)给料量的调节
① 每次调节 流量变化幅度小 于1m3/h ② 当粗甲醇槽液位 下降较快时,要迅速 查找原因,若因合成 来料不足可减量生产。 ③ 当进料含水多时,塔釜温 度也较高但要用回流量和回 流液温度等手段来保证加压 塔,常压塔顶温度正常。
④ 加减给料量的同时要向塔釜加减蒸汽量,应遵循以下原则:
3 粗甲醇精馏操作与工艺调节
粗甲醇的精馏主要操作参数
(1) 温度指标
指标名称 冷却水上水温度: 冷却水回水温度: 低压蒸汽温度: 预塔进料温度: 预精馏塔顶温度: 不凝气温度: 预塔回流槽温度: 预塔塔釜温度: 加压塔温度塔顶: 加压塔塔釜温度: 加压塔回流槽温度: 常压塔顶温度: 常压塔塔釜温度: 常压塔再沸器冷凝甲醇温度: 常压塔回流液温度: 杂醇采出温度: 杂醇冷凝后温度: 残液冷凝后温度: 精甲醇贮槽温度: 粗甲醇贮槽温度: 指标 32 42 158 65 75 50 50 85 122 134 117 63-65 105 117 40 85 40 40 40 40 单位 ℃ ℃ ℃ ℃ ℃ ℃ ℃ ℃ ℃ ℃ ℃ ℃ ℃ ℃ ℃ ℃ ℃ ℃ ℃ ℃
a. 预塔加给料量时应先加蒸汽量后 加给料量,减量时应先减给料量后 减蒸汽量以保证轻组分脱除干净。
b. 加压塔常压塔应先加给料量再加回流量后加 蒸汽量。减量时应减蒸汽量再减给料量后减回 流量。这样才能保证两塔的塔顶产品质量。
⑤ 加减给料量时,碱液量也 随之调整,保证塔底的PH= 7-9。
⑥ 随时注意合成工况及粗甲醇槽 的库存,有预见性的进行工况调 节,控制好入料量是保证的前提, 是稳定精馏操作的基础。
(2) 压力指标
指标名称 冷却水上水: 冷却水回水: 低压蒸汽: 指标 0.35 0.25 0.5 单位 MPa MPa MPa
预精馏塔顶:
预塔塔釜: 加压塔温度塔顶: 加压塔塔釜: 加压塔回流槽
0.05
0.08 0.56 0.65 0.55
MPa
MPa MPa MPa MPa 指标名称 预塔回流槽液位: 指标 30 单位 %
0.10
151ppm 0.54 67ppm
粗甲醇精馏的原理
精馏的原理:
根据在相同的温度下,同一液体混合物中不同组分的挥 发度不同,经多次部分汽化和多次部分冷凝最后得到较 纯的组分,是实现混合物的分离过程。
粗甲醇精馏方法
精馏是一种利用回流使液体混合物得到高纯度分离的蒸馏方法,是工业 上应用最广的液体混合物的分离操作。 两塔流程 粗甲醇的精馏有两种流程: 三塔流程
2 粗甲醇精馏的工艺流程
双塔精馏工艺流程
第一塔为预精馏塔,第二塔为主精馏塔,二塔再沸器的热源均为低压蒸汽。 预精馏塔的作用:脱除二甲醚;加 水萃取,脱除与甲醇沸点相近的轻 组分以及除去有机杂质中的轻组分。 主精馏塔的作用:将甲醇组分与水和重组分 分离,将水分离出来,尽量减少有机杂质含 量;分离重组分、杂醇油;采出精甲醇产品。
17
泵不上量
1、泵入口管线 阀门未开 2、入口管线堵塞 3、泵带气
18
泵打不起压
泵带气或 泵的机械故障
1、停泵、关进出口阀 2、关压力表根部阀,卸下压力表 3、开泵进口阀,从压力表根部阀排气 4、泵打不起压、倒泵
加大回流量或稍减速蒸汽量
19
冷凝器发生水击
回流槽液位满
4 粗甲醇精馏的岗位操作法
岗位职责 岗位操作技术规程
精甲醇质量标准
项 目 色度(铂-钴)/号 ≤ 3 密度(20℃)/(g/cm ) 温度范围(0℃,101325Pa)/℃ 沸程(包括64.6℃±0.1℃)/℃ ≤ 高锰酸钾试验/min ≥ 水溶性试验 水分含量/% ≤ 酸度(以HCOOH计)/% ≤ 或碱度(以NH3 O计)/% ≤ 羰基化合物含量(以NH3 O计)/% ≤ 蒸发残渣含量/% ≤ 指标 优等品 一等品 5 5 0.791-0.792 0.791-0.793 64.0-65.5 0.8 1 50 30 澄清 澄清 0.1 0.15 0.0015 0.003 0.0002 0.0008 0.002 0.001 0.005 0.003
%
% % % % %
Байду номын сангаас
加压塔回流泵出口: 1.12 预塔回流泵出口: 液下泵出口: 碱液泵出口: 残液泵出口: 0.4 0.4 0.4 0.4
常压塔回流泵出口: 0.65 杂醇泵出口: 精甲醇泵出口: 0.4 0.45
粗甲醇泵出口压力: 0.55
影响甲醇精馏的因素及控制
精馏主要操作是维持系统的物料平衡、热量平衡和汽液平衡,三 者互相影响。
•原始开车准备
(1) 预精馏塔的开车 (2) 加压精馏塔的开车 (1)煮塔 (2)系统置换 (3)开车准备工作 (1)长期停车
•开车
(3) 常压精馏塔的开车 (4) 排放槽的开车 (5) 精甲醇中间槽的开车 (6) 粗甲醇槽的开车
•停车步骤
(2)短期停车 (3)紧急停车
谢谢聆听!
1、关塔再沸器蒸汽阀 2、关采出阀 3、关常压塔残液排放阀 1、停加压塔、常压塔入料泵 2、关常压塔残液排放阀 3、关精甲采出阀 4、关蒸汽管入口阀 1、关再沸器蒸汽阀 2、停各泵 3、关排残液阀 4、关采出阀 1、开泵入口阀 2、疏通入口管线 3、按泵带气处理方法处理
15
无蒸汽
断蒸汽
16
无冷却水
断冷却水
(2) 温度的调节
① 蒸汽量增大塔温上升,对重组分上移,影响甲醇的质量,同时蒸汽加入 量过大,上升气速过快,有可能造成液泛,因此精馏塔升温应小于1℃/次 ② 蒸汽量加入量减少,塔温下降,轻组份下移,对于预塔来说可能将轻组 分带到后面产品塔,造成产品的KMnO4试验和水溶性试验不合格。
(3) 回流的调节
(3)液位指标
常压塔顶:
常压塔塔釜: 预后甲醇泵出口:
0.03
0.08 0.8
MPa
MPa MPa MPa MPa MPa MPa MPa MPa MPa MPa MPa
缓冲槽液位:
预塔塔釜液位: 加压塔回流槽液位: 加压塔塔釜液位: 常压塔回流槽液位: 常压塔塔釜液位:
30
60-90 30 60-90 30 60-90
压力若不足,塔顶甲醇蒸汽量下降,影响常压塔再沸器下降,废水含量超标。 压力调节是通过加压塔塔釜蒸汽加入量及回流量的大小及温度来调节塔压。 常压塔的压力调节是通过冷凝器冷却水量、回流量、回 流温度共同作用实现,一般常压塔回流比控制在2-3。
③ 对常压塔
压力不足有可能引起负压,使设备受到损害; 压力过高,使甲醇在塔底的分压增高,造成塔底废水水含量超标。
生产事故及处理
序 号 1 现 象 事 故 原 因 处 理 措 施 1、增大入料量3、检查、 校核液位 2、减小采出量4、减小 蒸汽量 1、减小入料量 2、增 大蒸汽量 3、增大采出量 1、减小蒸汽量 2、降低放空温度 1、减小蒸汽量 2、加大软水入量 3、稳定塔底液位 4、清洗冷凝器 5、加大冷却水量 6、提高水压,降低水量 1、增加软水量 2、减小软水量
(5)液位调节
① 塔釜液位 •塔釜液位给定太低,造成釜液蒸发过大,釜温升高,釜液停留时间 较短,影响换热效果; •塔釜液位给定太高,液位高至再沸器回流口,液相阻力增大,不仅 会影响甲醇汽液的热循环,还容易造成液泛,导致传质、传热效果差。
各塔液位应保持在60%-90%。
② 回流槽液位 开车初期,为了使生产出的不合格甲醇回流液尽快置换,回 流槽液位可给定20%,分析产品合格后,液位在给定30%。 正常生产时,回流槽应有足够的合格甲醇以供回流及调节工况, 回流槽给定30%,投自动。 当液位自动 调节阀故障 失灵时,应 关闭前后切 断阀,用旁 路阀控制, 现场液位应 尽量稳定, 同时通知仪 表工处理。
当回流不足,塔温上升重组分上移,影响精甲醇的产品质量,这时就 应减少采出,增加回流。尤其是在产品质量不合格时应增大回流量。
(4) 压力调节
①对预精馏塔压力增大 一方面对安全不利;
压力对系统的影响非常大。 预精馏塔压力调节 •塔顶阀门开启度 •冷凝器的冷却水量 •再沸器蒸汽加入量
另一方面,压力升高使不凝气不能顺利排放,带 入下面几个塔,影响精甲醇的酸度和水溶性试验。 ② 对加压塔
第六章 粗甲醇的精制
1
粗甲醇精馏的原理和方法
2
粗甲醇精馏工艺流程
3 4
粗甲醇精馏操作与工艺控制
粗甲醇精馏的岗位操作法
1粗甲醇精馏的原理和方法
粗甲醇的组成
组份 含量(wt%) CH3OH 81.1 H2O 17.9 CH3OCH
3
高沸 点醇 0.33
H2 38pp m
CO
CO2
CH4
N2 48pp m
预精馏塔塔底无液位
1、入料量小3、液面指示失真 2、采出量大4、蒸汽量大
1、入料量大2、蒸汽量小 3、采出量小 1、蒸汽量大 2、放空温度高