硝酸工艺流程简介电子版本
硝酸工艺流程简介

1. 双加压法稀硝酸生产工艺流程1.1工艺流程示意图如图1-1:1、2—液氨蒸发器,3—辅助蒸发器,4—氨过热器,5—氨过滤器,6—空气过滤室,7—空压机,8—混合器,9—氧化炉、过热器、废热锅炉,10—高温气气换热器,11—省煤器,12—低压反应水冷器,13—氧化氮分离器,14—氧化氮压缩机,15—尾气预热器,16—高压反应水冷器,17—吸收塔,18—尾气分离器,19—二次空气冷却器,20—尾气透平,21—蒸汽透平,22—蒸汽分离器,23—汽包,24—蒸汽冷凝器。
图1-1 工艺流程示意图1.2流程简述:合成氨厂来的液氨进入有液位控制的A、B两台氨蒸发器中,氨在其中蒸发,正常操作时,大部分液氨被A台蒸发器中来至吸收塔的冷却水所蒸发(吸收塔上部冷却水与A蒸发器形成闭路循环),蒸发温度11.5 ℃;其余的液氨被冷却水在B台蒸发器中蒸发,蒸发温度为14 ℃,两台氨蒸发器的蒸发压力均维持在0.52 Mpa;其中的油和水在辅助蒸发器中被分离,蒸发出的气氨进入氨过热器,气氨温度由TV31022控制,温度为110 ℃,然后再经氨过滤器进入氨─空气混合器。
空气从大气中吸入,经过三级过滤进入空气压缩机入口(冬季在经过空气过滤器前由空气预热器预热),经过空气压缩机加压至0.35 Mpa后分为一次空气和二次空气两股气流,一次空气进入氨─空混合器,二次空气进入漂白塔。
氨和空气在氨─空混合器中混合以后,进入氧化炉,经过铂网催化剂氧化生成NO等混合气体,铂网氧化温度为860 ℃,然后经过蒸汽过热器、废热锅炉,再经高温气─气换热器、省煤器、低压反应水冷器,再进入氧化氮分离器,在此将稀酸分离下来,气体则与漂白塔来的二次空气混合后进入氧化氮压缩机,进气温度为60 ℃,压力为0.3 Mpa;出口温度为200 ℃,压力为1.0 Mpa。
再经尾气预热器、高压反应水冷却器进入吸收塔,进入吸收塔时的氮氧化物气体温度为40℃,氮氧化物气体从吸收塔底部进入,工艺水从吸收塔顶部喷淋而下,二者逆流接触,生成58 %—60 %的硝酸,塔底酸温度为40 ℃,从吸收塔出来的硝酸进入漂白塔,用来自二次空气冷却器的约120 ℃的二次空气在漂白塔中逆流接触,以提出溶解在稀酸中的低价氮氧化物气体,完成漂白过程,漂白后的成品酸经酸冷却器冷却到40 ℃,进入成品酸贮罐,再用成品酸泵送往硝铵和间硝装置。
硝酸生产工艺

硝酸生产工艺一、中压法制稀硝酸工艺流程硝化法制硫酸的一种方法,硫酸工业发展史上最古老的工业生产方法,因以铅制的方形空室为主要设备而得名。
铅室法曾作为硫酸的唯一制造法盛行于世,历时100多年。
20世纪起,逐渐被塔式法和接触法(见硫酸)取代。
铅室法的基本原理与塔式法相同,实质上是利用高级氮氧化物(主要是三氧化二氮)使二氧化硫氧化并生成硫酸:SO+NO+HO─→HSO+2NO生成的一氧化氮又迅速氧化成高级氮氧化物:2NO+O─→2NONO+NO─→NO因此,在理论上,氮氧化物仅起着传递氧的作用,本身并无消耗。
英国人J.罗巴克于1746年创建了世界上第一个铅室法制造硫酸的工厂。
至19世纪50年代,铅室法生产工艺才臻于完善。
典型的铅室法的生产流程(图2[ 铅室法生产硫酸工艺流程]),是使300~500℃的含二氧化硫气体(见硫酸原料气)进入充有填料的脱硝塔,与淋洒的含硝硫酸逆流接触。
由于酸温升高,含硝硫酸中的氮氧化物得以充分脱除。
塔顶引出的含二氧化硫、氮氧化物、氧和水蒸气的混合气体,依次通过若干个铅室。
在铅室中,二氧化硫充分氧化而成硫酸。
最终通过两座串联的填料式吸硝塔,塔内淋洒经过冷却的脱硝硫酸,以吸收氮氧化物,所得的含硝硫酸送往脱硝塔。
由于部分氮氧化物会随废气和产品带出,需不断补充。
早期是将硝石加入焚硫炉内使受热分解,取得二氧化硫和氮氧化物的混合气体。
后来,都是将氨氧化成氮的氧化物,再将后者引入第一个铅室,或将硝酸直接补加在含硝硫酸中,用以淋洒脱硝塔。
潮湿的二氧化硫氮氧化物的混合气体和浓度在70%以下的稀硫酸具有很强的腐蚀性,设备需用铅制。
在铅室中,二氧化硫的氧化与成酸反应大部分是在气相中进行,因而不可避免地会形成大量的硫酸雾。
这种气溶胶状态的细微颗粒需经较长进间才能凝聚成液滴,坠落至铅室底部。
为此必须拥有很大的反应空间,才能保持较高的生产效率。
再者,生产过程中释放的大量反应热也须经铅室表面及时散去。
因此,铅室法工厂往往采用多个串联的铅室,耗铅量大,这是历史上人们力求革新铅室法的主要原因。
硝酸生产工艺技术简介

C硝酸生产工艺技术简介1建设规模及产品方案1.1产品方案利用本公司生产的液氨生产硝酸,最终产品为98%浓硝酸。
1.2生产规模1.2.1设计规模:公称能力为日产浓硝酸350吨(以100%HNO 3计)(公称能力产浓硝酸10万吨/年,计算产能10.5万吨/年,配套建10.5 万吨/年稀硝酸装置)。
年运行时间:7200小时。
1.2.2确定本装置设计规模依据以下因素:结合耀隆集团原材料供应、辅助工程条件以及市场需求,将本工程浓硝酸生产规模定为10万吨/年(以100%HNO 3计)。
2工艺技术方案及技术来源2.1工艺技术方案选择2.1.1稀硝酸2.1.1.1国内外稀硝酸工艺技术概况目前,国内外工业上生产稀硝酸的方法有常压法、综合法、全中压法、高压法、双加压法,现分述如下:(1)常压法:氨氧化和吸收均在常压下进行的生产工艺。
早期硝酸生产多采用这种方法,该工艺流程的特点为系统压力低,设备结构简单,工艺操作稳定,氨氧化率高,铂耗较低。
但吸收比容积大(20~25m3),酸吸收率较低(仅为92%左右)。
为减少对大气的污染并提高氨利用率,需附有碱吸收N OX尾气装置并副产硝盐,即便如此尾气中N OX浓度仍很高,不符合目前日益严格的环境要求。
加上设备相对台数较多,设备体积大,装置占地面积多,投资大,成品酸浓度低等因素,国家经贸委已明文规定禁止采用此种流程新建硝酸装置。
(2)综合法常压氨氧化和中压(0.25~0.5MPa)酸吸收的稀硝酸生产工艺。
这种方法在一定程度上弥补了常压酸吸收的缺点,我国在本世纪50年代末引进该流程进行稀硝酸的工业生产。
该方法主要缺点是常压氨氧化、设备庞大、占地多,需要配备较昂贵的不锈钢材质的氧化氮压缩机,其投资高于下面介绍的中压法,且吸收压力低仅0.35MPa(A),因此酸浓度低及尾气排放不能达到环保要求,不适用于规模较大的硝酸装置,国家经贸委也明文规定了不能采用此种流程建设硝酸装置。
(3)全中压法氨氧化和酸吸收均在中压下进行的稀硝酸生产工艺。
硝酸工艺流程简介

中压蒸
92
11 Βιβλιοθήκη 34582液氨 6
1
1 2
1
1 1
2 尾气
空气
7
2
1
1
1
至漂白
1
1、2—液氨蒸发器, 3—辅助蒸发器, 4—氨过热器, 5—氨过滤器, 6—空气
过滤室, 7—空压机, 8—混合器, 9—氧化炉、过热器、废热锅炉, 10—高温
氨和空气在氨─空混合器中混合以后,进入氧化炉,经过铂网催化剂氧 化生成 NO等混合气体,铂网氧化温度为 860 ℃,然后经过蒸汽过热器、废热 锅炉,再经高温气─气换热器、省煤器、低压反应水冷器,再进入氧化氮分 离器,在此将稀酸分离下来,气体则与漂白塔来的二次空气混合后进入氧化 氮压缩机,进气温度为 60 ℃,压力为 Mpa;出口温度为 200 ℃,压力为 Mpa。 再经尾气预热器、高压反应水冷却器进入吸收塔,进入吸收塔时的氮氧化物 气体温度为 40℃,氮氧化物气体从吸收塔底部进入,工艺水从吸收塔顶部喷 淋而下,二者逆流接触,生成 58 %—60 %的硝酸,塔底酸温度为 40 ℃,从 吸收塔出来的硝酸进入漂白塔,用来自二次空气冷却器的约 120 ℃的二次空 气在漂白塔中逆流接触,以提出溶解在稀酸中的低价氮氧化物气体,完成漂 白过程,漂白后的成品酸经酸冷却器冷却到 40 ℃,进入成品酸贮罐,再用成 品酸泵送往硝铵和间硝装置。
后进入碱吸收塔,经碱吸收后排入大气,排放的尾气中 400ppm。
NOX 的含量最低约
3.常压法稀硝酸生产工艺流程: 空气通过过滤器除去机械杂质和粉尘后经过鼓风机,进入混合器与过滤
后的氨气混合,然后进入氧化炉,反应生成高温的氧化氮工艺气体,工艺气 体经过锅炉、冷却器降温至 40℃,进入吸收塔底部,在常压下经过多个酸吸 收塔吸收,从吸收塔顶部出来的尾气进入多个碱吸收塔,经碱吸收后排入大 气,排放的尾气中 NOX 的含量最低约 2000ppm。
硝酸工艺流程简介
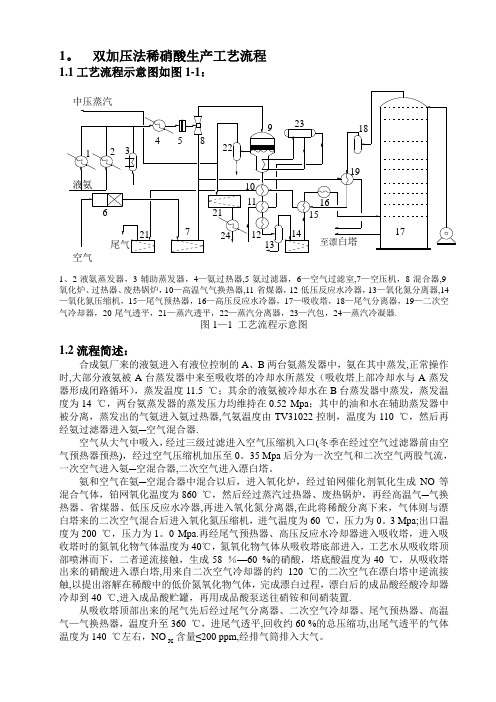
1。
双加压法稀硝酸生产工艺流程1.1工艺流程示意图如图1-1:1、2-液氨蒸发器,3-辅助蒸发器,4—氨过热器,5-氨过滤器,6—空气过滤室,7—空压机,8-混合器,9-氧化炉、过热器、废热锅炉,10—高温气气换热器,11-省煤器,12-低压反应水冷器,13—氧化氮分离器,14—氧化氮压缩机,15—尾气预热器,16—高压反应水冷器,17—吸收塔,18—尾气分离器,19—二次空气冷却器,20-尾气透平,21—蒸汽透平,22—蒸汽分离器,23—汽包,24—蒸汽冷凝器.图1—1 工艺流程示意图1.2流程简述:合成氨厂来的液氨进入有液位控制的A、B两台氨蒸发器中,氨在其中蒸发,正常操作时,大部分液氨被A台蒸发器中来至吸收塔的冷却水所蒸发(吸收塔上部冷却水与A蒸发器形成闭路循环),蒸发温度11.5 ℃;其余的液氨被冷却水在B台蒸发器中蒸发,蒸发温度为14 ℃,两台氨蒸发器的蒸发压力均维持在0.52 Mpa;其中的油和水在辅助蒸发器中被分离,蒸发出的气氨进入氨过热器,气氨温度由TV31022控制,温度为110 ℃,然后再经氨过滤器进入氨─空气混合器.空气从大气中吸入,经过三级过滤进入空气压缩机入口(冬季在经过空气过滤器前由空气预热器预热),经过空气压缩机加压至0。
35 Mpa后分为一次空气和二次空气两股气流,一次空气进入氨─空混合器,二次空气进入漂白塔。
氨和空气在氨─空混合器中混合以后,进入氧化炉,经过铂网催化剂氧化生成NO等混合气体,铂网氧化温度为860 ℃,然后经过蒸汽过热器、废热锅炉,再经高温气─气换热器、省煤器、低压反应水冷器,再进入氧化氮分离器,在此将稀酸分离下来,气体则与漂白塔来的二次空气混合后进入氧化氮压缩机,进气温度为60 ℃,压力为0。
3 Mpa;出口温度为200 ℃,压力为1。
0 Mpa.再经尾气预热器、高压反应水冷却器进入吸收塔,进入吸收塔时的氮氧化物气体温度为40℃,氮氧化物气体从吸收塔底部进入,工艺水从吸收塔顶部喷淋而下,二者逆流接触,生成58 %—60 %的硝酸,塔底酸温度为40 ℃,从吸收塔出来的硝酸进入漂白塔,用来自二次空气冷却器的约120 ℃的二次空气在漂白塔中逆流接触,以提出溶解在稀酸中的低价氮氧化物气体,完成漂白过程,漂白后的成品酸经酸冷却器冷却到40 ℃,进入成品酸贮罐,再用成品酸泵送往硝铵和间硝装置.从吸收塔顶部出来的尾气先后经过尾气分离器、二次空气冷却器、尾气预热器、高温气—气换热器,温度升至360 ℃,进尾气透平,回收约60 %的总压缩功,出尾气透平的气体含量≤200 ppm,经排气筒排入大气。
硝酸工艺流程方框图
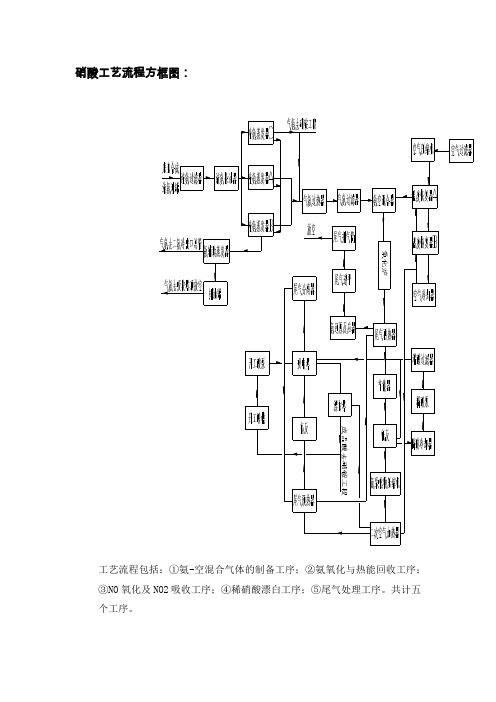
硝酸工艺流程方框图:工艺流程包括:①氨-空混合气体的制备工序;②氨氧化与热能回收工序;③NO氧化及NO2吸收工序;④稀硝酸漂白工序;⑤尾气处理工序。
共计五个工序。
1. 氨空混合气的制备工序由界区来的原料液氨警告液氨过滤器除去液氨中的机械杂质,然后进入液氨除油器除油,一部分送入氨蒸发器C,蒸发后送入硝铵装置。
另一部分送入氨蒸发器A和B,大部分液氨在氨蒸发器A中蒸发,剩余的液氨在氨蒸发器B中蒸发。
蒸发压力维持在约0.6Mpa(G)左右。
氨蒸发器A及B蒸发温度分别为11.5℃及14℃,当液氨中水和油在氨蒸发器B中累积起来时,可将水和油排至氨辅助蒸发器,在该设备中通入低压蒸汽,在105℃下将氨蒸发,此过程可间断或连续操作。
由氨蒸发器A及B来的气氨与氨辅助蒸发器来的热气氨在此混合送至气氨过滤器过滤除杂,然后送至气氨过热器,氨过热到180℃左右,进入氨-空混合器,再去氨氧化反应-余热回收器(亦称:氧化炉-废热锅炉)。
空气经四级立式过滤器后入空气压缩机,出压缩机的空气经过1#温度恢复器、2#温度恢复器和空气冷却器,在空气冷却器中空气温度降到40℃左右,空气中的水冷凝出来,除水后的空气分为一次和二次空气两股气流,一次空气去1#、2#温度恢复器与总空气换热后进入氨-空气混合器,二次空气去氧化和漂白工序。
2、氨氧化与热能回收工序氨-空气混合气体进入氨氧化反应器,经其内部分布器均匀分布于铂网上,进行氨氧化反应,反应方程式为:4NH3+ 5O2= 4NO + 6H2O +Q氨氧化反应,生成一氧化氮、水蒸气,所释放出的热量及氨-空气混合气的显热使一氧化氮气体温度升至860~880℃,此NOx气流经安装在氨氧化炉下部的蒸汽过热器和废热锅炉以回收其热量,混合气体(一氧化氮、二氧化氮、空气中的氮气和氧气、生成的水蒸气)出废热锅炉的温度降至400℃左右。
3、NO的氧化和NO2的吸收工序出废热锅炉的NOx气体流经串联的尾气再热器E-1108、节能器E-1109,当温度降低时,混合气中的NO氧化为NO2。
硝酸生产工艺
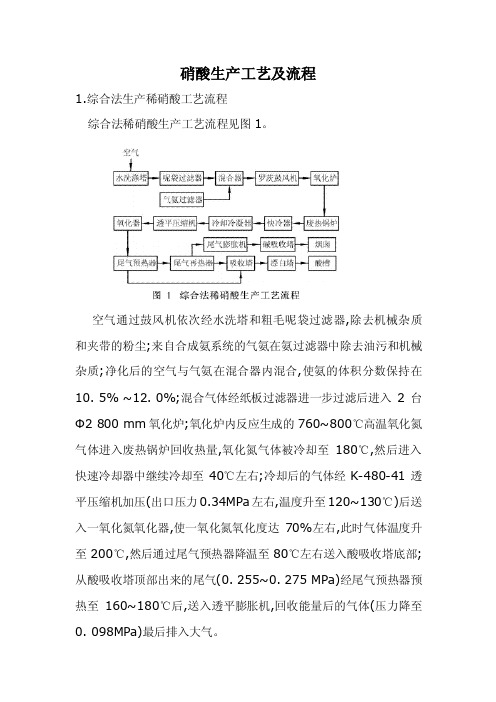
硝酸生产工艺及流程1.综合法生产稀硝酸工艺流程综合法稀硝酸生产工艺流程见图1。
空气通过鼓风机依次经水洗塔和粗毛呢袋过滤器,除去机械杂质和夹带的粉尘;来自合成氨系统的气氨在氨过滤器中除去油污和机械杂质;净化后的空气与气氨在混合器内混合,使氨的体积分数保持在10. 5% ~12. 0%;混合气体经纸板过滤器进一步过滤后进入2台Φ2 800 mm氧化炉;氧化炉内反应生成的760~800℃高温氧化氮气体进入废热锅炉回收热量,氧化氮气体被冷却至180℃,然后进入快速冷却器中继续冷却至40℃左右;冷却后的气体经K-480-41透平压缩机加压(出口压力0.34MPa左右,温度升至120~130℃)后送入一氧化氮氧化器,使一氧化氮氧化度达70%左右,此时气体温度升至200℃,然后通过尾气预热器降温至80℃左右送入酸吸收塔底部;从酸吸收塔顶部出来的尾气(0. 255~0. 275 MPa)经尾气预热器预热至160~180℃后,送入透平膨胀机,回收能量后的气体(压力降至0. 098MPa)最后排入大气。
2中压法生产稀硝酸工艺流程中压法稀硝酸生产工艺流程见图2。
利用K-480-41透平压缩机作为空气压缩机,将来自空气过滤器的空气压缩至0. 35MPa,然后经素瓷过滤器进一步除去空气中的灰尘和杂质去氨空混合器;来自合成氨系统的气氨经气氨缓冲罐调节压力至0. 3~0. 6MPa,再经氨过滤器除去机械杂质和油污后进入气氨加热器,加热后的气氨经流量调节阀进入氨空混合器;混合后控制氨体积分数为9% ~11%,自上而下通过上部为Φ1 600 mm的氧化炉和下部直径为Φ900 mm的联合体废热废锅,氨空混合气经铂网催化高温氧化生成800~820℃的氧化氮气体,再经废热锅炉回收热量后温度降至240~260℃,进入尾气再热器和尾气预热器与尾气换热,当温度降至125~145℃与来自漂白塔的二次空气混合后进入氧化器,使一氧化氮被进一步氧化;温度升至180~200℃的氧化氮气体进入软水预热器与软水换热后,再与快冷器中的冷却水换热,气体温度降至30~50℃;出快冷器的氧化氮气体进入吸收塔底部,与自上而下的软水逆流接触,被吸收生成质量分数为45% ~50%的稀硝酸。
硝酸生产工艺
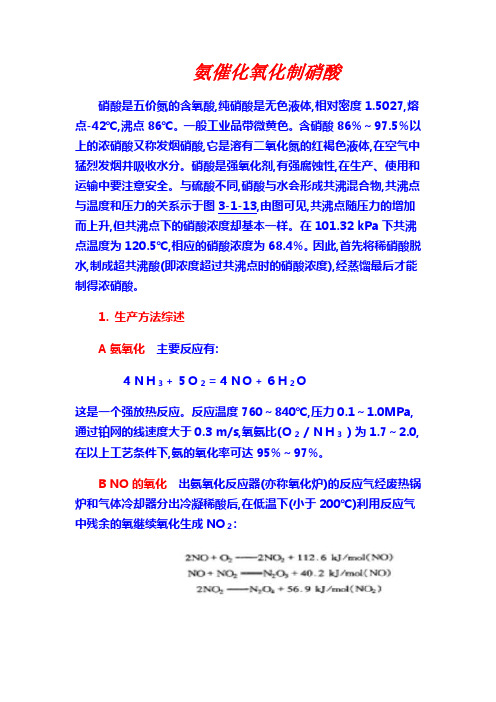
氨催化氧化制硝酸硝酸是五价氮的含氧酸,纯硝酸是无色液体,相对密度1.5027,熔点-42℃,沸点86℃。
一般工业品带微黄色。
含硝酸86%~97.5%以上的浓硝酸又称发烟硝酸,它是溶有二氧化氮的红褐色液体,在空气中猛烈发烟并吸收水分。
硝酸是强氧化剂,有强腐蚀性,在生产、使用和运输中要注意安全。
与硫酸不同,硝酸与水会形成共沸混合物,共沸点与温度和压力的关系示于图3-1-13,由图可见,共沸点随压力的增加而上升,但共沸点下的硝酸浓度却基本一样。
在101.32 kPa下共沸点温度为120.5℃,相应的硝酸浓度为68.4%。
因此,首先将稀硝酸脱水,制成超共沸酸(即浓度超过共沸点时的硝酸浓度),经蒸馏最后才能制得浓硝酸。
1. 生产方法综述A氨氧化主要反应有:4NH3+5O2=4NO+6H2O这是一个强放热反应。
反应温度760~840℃,压力0.1~1.0MPa,通过铂网的线速度大于0.3 m/s,氧氨比(O2/NH3)为1.7~2.0,在以上工艺条件下,氨的氧化率可达95%~97%。
B NO的氧化出氨氧化反应器(亦称氧化炉)的反应气经废热锅炉和气体冷却器分出冷凝稀酸后,在低温下(小于200℃)利用反应气中残余的氧继续氧化生成NO2:其中生成N2O3和N2O4的反应,速度极快(分别为0.1 s和10-4s),而生成NO2的反应则慢得多(约20 s左右),因此是整个氧化反应的控制步骤。
上列三个反应是可逆放热反应,反应后,摩尔数减少,因此降低反应温度,增加压力有利于NO氧化反应的进行。
NO的氧化程度α-NO与温度和压力的关系示于图3-1-14。
由图3-1-14可见,当温度低于200℃,压力为0.8MPa时α-NO接近100%,常压时α-NO也能达到90%以上,实际操作时α-NO在70%~80%之间,反应气即可送吸收塔进行吸收操作。
NO的氧化是一个非催化氧化反应,反应时间比氨氧化反应长得多,前者为20 s左右,而后者仅为2×10-4s。
- 1、下载文档前请自行甄别文档内容的完整性,平台不提供额外的编辑、内容补充、找答案等附加服务。
- 2、"仅部分预览"的文档,不可在线预览部分如存在完整性等问题,可反馈申请退款(可完整预览的文档不适用该条件!)。
- 3、如文档侵犯您的权益,请联系客服反馈,我们会尽快为您处理(人工客服工作时间:9:00-18:30)。
硝酸工艺流程简介
1. 双加压法稀硝酸生产工艺流程
1.1工艺流程示意图如图1-1:
空
1、2—液氨蒸发器,3—辅助蒸发器,4—氨过热器,5—氨过滤器,6—空气过滤室,7—空压机,8—混合器,9—氧化炉、过热器、废热锅炉,10—高温气气换热器,11—省煤器,12—低压反应水冷器,13—氧化氮分离器,14—氧化氮压缩机,15—尾气预热器,16—高压反应水冷器,17—吸收塔,18—尾气分离器,19—二次空气冷却器,20—尾气透平,21—蒸汽透平,22—蒸汽分离器,23—汽包,24—蒸汽冷凝器。
图1-1 工艺流程示意图
1.2流程简述:
合成氨厂来的液氨进入有液位控制的A、B两台氨蒸发器中,氨在其中蒸发,正常操作时,大部分液氨被A台蒸发器中来至吸收塔的冷却水所蒸发(吸收塔上部冷却水与A蒸发器形成闭路循环),蒸发温度11.5 ℃;其余的液氨被冷却水在B台蒸发器中蒸发,蒸发温度为14 ℃,两台氨蒸发器的蒸发压力均维持在0.52 Mpa;其中的油和水在辅助蒸发器中被分离,蒸发出的气氨进入氨过热器,气氨温度由TV31022控制,温度为110 ℃,然后再经氨过滤器进入氨─空气混合器。
空气从大气中吸入,经过三级过滤进入空气压缩机入口(冬季在经过空气过滤器前由空气预热器预热),经过空气压缩机加压至
0.35 Mpa后分为一次空气和二次空气两股气流,一次空气进入氨─空混合器,二次空气进入漂白塔。
氨和空气在氨─空混合器中混合以后,进入氧化炉,经过铂网催化剂氧化生成NO等混合气体,铂网氧化温度为860 ℃,然后经过蒸汽过热器、废热锅炉,再经高温气─气换热器、省煤器、低压反应水冷器,再进入氧化氮分离器,在此将稀酸分离下来,气体则与漂白塔来的二次空气混合后进入氧化氮压缩机,进气温度为
60 ℃,压力为0.3 Mpa;出口温度为200 ℃,压力为1.0 Mpa。
再经尾气预热器、高压反应水冷却器进入吸收塔,进入吸收塔时的氮氧化物气体温度为40℃,氮氧化物气体从吸收塔底部进入,工艺水从吸收塔顶部喷淋而下,二者逆流接触,生成58 %—60 %的硝酸,塔底酸温度为40 ℃,从吸收塔出来的硝酸进入漂白塔,用来自二次空气冷却器的约120 ℃的二次空气在漂白塔中逆流接触,以提出溶解在稀酸中的低价氮氧化物气体,完成漂白过程,漂白后的成品酸经酸冷却器冷却到40 ℃,进入成品酸贮罐,再用成品酸泵送往硝铵和间硝装置。
从吸收塔顶部出来的尾气先后经过尾气分离器、二次空气冷却器、尾气预热器、高温气—气换热器,温度升至360 ℃,进尾气透平,回收约60 %的总压缩功,出尾气透平的气体温度为140 ℃左右,NO
含量≤200 ppm,经排气筒排入大气。
X
在废热锅炉中产生4.0MPa的湿饱和蒸汽,经蒸汽过热器加热到温度440 ℃、压力为3.9 Mpa过热蒸汽进入蒸汽分离器,过热蒸汽用于驱动蒸汽透平,蒸汽过剩送至外界蒸汽管网。
锅炉系统采用强制循环,用锅炉水循环泵(J31002/A/B)使锅炉水在汽包和锅炉间循环。
1.3流程特点:
1.氧化压力为0.45 MPa(A),吸收压力为1.1 MPa(A)。
2.氨的氧化率高达96 %以上,铂耗较低,为120 mg/t100%HNO3 (回收前)。
二氧化氮吸收率高,硝酸浓度可达60 %,排放的尾气的含量在200 ppm以下。
中NO
X
3.采用中温(360 ℃)回收装置尾气能量,使压缩机组的蒸汽透平和尾气膨胀透平之间达到经济匹配,与高温回收相比不必采用耐高温的尾气透平和尾气加热器,工作条件不苛刻,操作稳定可靠。
4.合理利用氨蒸发的冷量,制得18℃低温冷却水去吸收塔冷却盘
气体的含量。
管移走吸收反应热,有效降低尾气中NO
X
5.装置副产中压过热蒸汽,除驱动压缩机组蒸汽透平外还可以外
(不含循环水用
送,装置耗电量小,仅为11.1 kw/t100%HNO
3
电)。
6.采用DCS控制系统,使操作更加方便和安全。
2.综合法稀硝酸生产工艺流程:
空气通过鼓风机依次经过水洗塔和过滤器,除去机械杂质和粉尘,进入混合器与过滤后的氨气混合,然后进入氧化炉,反应生成高温的氧化氮工艺气体,工艺气体经过锅炉、冷却器降温至40℃,经压缩机加压至0.35Mpa,经过换热降至40℃进入吸收塔底部与塔顶加入的水反应,稀酸从塔底排出进入漂白塔漂白后送入酸罐,从吸收塔顶部出来的尾气经过换热进入透平膨胀机回收能量后
的含量最进入碱吸收塔,经碱吸收后排入大气,排放的尾气中NO
X
低约400ppm。
3.常压法稀硝酸生产工艺流程:
空气通过过滤器除去机械杂质和粉尘后经过鼓风机,进入混合器与过滤后的氨气混合,然后进入氧化炉,反应生成高温的氧化氮工艺气体,工艺气体经过锅炉、冷却器降温至40℃,进入吸收塔底部,在常压下经过多个酸吸收塔吸收,从吸收塔顶部出来的尾气
的含进入多个碱吸收塔,经碱吸收后排入大气,排放的尾气中NO
X
量最低约2000ppm。