硝酸工艺流程简介
硝酸生产工艺

硝酸生产工艺一、中压法制稀硝酸工艺流程硝化法制硫酸的一种方法,硫酸工业发展史上最古老的工业生产方法,因以铅制的方形空室为主要设备而得名。
铅室法曾作为硫酸的唯一制造法盛行于世,历时100多年。
20世纪起,逐渐被塔式法和接触法(见硫酸)取代。
铅室法的基本原理与塔式法相同,实质上是利用高级氮氧化物(主要是三氧化二氮)使二氧化硫氧化并生成硫酸:SO+NO+HO─→HSO+2NO生成的一氧化氮又迅速氧化成高级氮氧化物:2NO+O─→2NONO+NO─→NO因此,在理论上,氮氧化物仅起着传递氧的作用,本身并无消耗。
英国人J.罗巴克于1746年创建了世界上第一个铅室法制造硫酸的工厂。
至19世纪50年代,铅室法生产工艺才臻于完善。
典型的铅室法的生产流程(图2[ 铅室法生产硫酸工艺流程]),是使300~500℃的含二氧化硫气体(见硫酸原料气)进入充有填料的脱硝塔,与淋洒的含硝硫酸逆流接触。
由于酸温升高,含硝硫酸中的氮氧化物得以充分脱除。
塔顶引出的含二氧化硫、氮氧化物、氧和水蒸气的混合气体,依次通过若干个铅室。
在铅室中,二氧化硫充分氧化而成硫酸。
最终通过两座串联的填料式吸硝塔,塔内淋洒经过冷却的脱硝硫酸,以吸收氮氧化物,所得的含硝硫酸送往脱硝塔。
由于部分氮氧化物会随废气和产品带出,需不断补充。
早期是将硝石加入焚硫炉内使受热分解,取得二氧化硫和氮氧化物的混合气体。
后来,都是将氨氧化成氮的氧化物,再将后者引入第一个铅室,或将硝酸直接补加在含硝硫酸中,用以淋洒脱硝塔。
潮湿的二氧化硫氮氧化物的混合气体和浓度在70%以下的稀硫酸具有很强的腐蚀性,设备需用铅制。
在铅室中,二氧化硫的氧化与成酸反应大部分是在气相中进行,因而不可避免地会形成大量的硫酸雾。
这种气溶胶状态的细微颗粒需经较长进间才能凝聚成液滴,坠落至铅室底部。
为此必须拥有很大的反应空间,才能保持较高的生产效率。
再者,生产过程中释放的大量反应热也须经铅室表面及时散去。
因此,铅室法工厂往往采用多个串联的铅室,耗铅量大,这是历史上人们力求革新铅室法的主要原因。
稀硝酸生产工艺
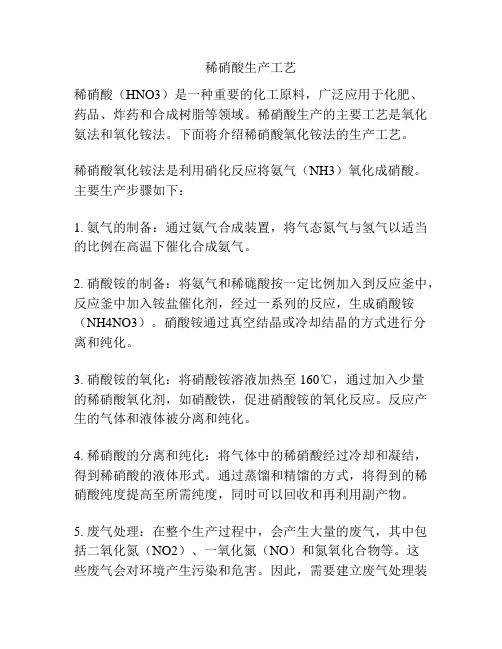
稀硝酸生产工艺稀硝酸(HNO3)是一种重要的化工原料,广泛应用于化肥、药品、炸药和合成树脂等领域。
稀硝酸生产的主要工艺是氧化氨法和氧化铵法。
下面将介绍稀硝酸氧化铵法的生产工艺。
稀硝酸氧化铵法是利用硝化反应将氨气(NH3)氧化成硝酸。
主要生产步骤如下:1. 氨气的制备:通过氨气合成装置,将气态氮气与氢气以适当的比例在高温下催化合成氨气。
2. 硝酸铵的制备:将氨气和稀硥酸按一定比例加入到反应釜中,反应釜中加入铵盐催化剂,经过一系列的反应,生成硝酸铵(NH4NO3)。
硝酸铵通过真空结晶或冷却结晶的方式进行分离和纯化。
3. 硝酸铵的氧化:将硝酸铵溶液加热至160℃,通过加入少量的稀硝酸氧化剂,如硝酸铁,促进硝酸铵的氧化反应。
反应产生的气体和液体被分离和纯化。
4. 稀硝酸的分离和纯化:将气体中的稀硝酸经过冷却和凝结,得到稀硝酸的液体形式。
通过蒸馏和精馏的方式,将得到的稀硝酸纯度提高至所需纯度,同时可以回收和再利用副产物。
5. 废气处理:在整个生产过程中,会产生大量的废气,其中包括二氧化氮(NO2)、一氧化氮(NO)和氮氧化合物等。
这些废气会对环境产生污染和危害。
因此,需要建立废气处理装置,通过吸收、吸附、催化和氧化等方式,对废气中的污染物进行处理和净化,以达到排放标准。
稀硝酸氧化铵法具有生产过程简单、原料充分利用、产品质量稳定等优点。
同时,还可以通过改变反应条件和催化剂的使用量等因素,来调整稀硝酸的浓度和纯度,以满足不同需求。
总之,稀硝酸氧化铵法是一种较为常用的稀硝酸生产工艺,通过氨气的制备、硝酸铵的制备、硝酸铵的氧化、稀硝酸的分离和纯化,最终得到所需纯度的稀硝酸。
此外,废气处理也是重要的环节,需要对产生的废气进行净化和处理。
硝酸生产工艺技术简介

C硝酸生产工艺技术简介1建设规模及产品方案1.1产品方案利用本公司生产的液氨生产硝酸,最终产品为98%浓硝酸。
1.2生产规模1.2.1设计规模:公称能力为日产浓硝酸350吨(以100%HNO 3计)(公称能力产浓硝酸10万吨/年,计算产能10.5万吨/年,配套建10.5 万吨/年稀硝酸装置)。
年运行时间:7200小时。
1.2.2确定本装置设计规模依据以下因素:结合耀隆集团原材料供应、辅助工程条件以及市场需求,将本工程浓硝酸生产规模定为10万吨/年(以100%HNO 3计)。
2工艺技术方案及技术来源2.1工艺技术方案选择2.1.1稀硝酸2.1.1.1国内外稀硝酸工艺技术概况目前,国内外工业上生产稀硝酸的方法有常压法、综合法、全中压法、高压法、双加压法,现分述如下:(1)常压法:氨氧化和吸收均在常压下进行的生产工艺。
早期硝酸生产多采用这种方法,该工艺流程的特点为系统压力低,设备结构简单,工艺操作稳定,氨氧化率高,铂耗较低。
但吸收比容积大(20~25m3),酸吸收率较低(仅为92%左右)。
为减少对大气的污染并提高氨利用率,需附有碱吸收N OX尾气装置并副产硝盐,即便如此尾气中N OX浓度仍很高,不符合目前日益严格的环境要求。
加上设备相对台数较多,设备体积大,装置占地面积多,投资大,成品酸浓度低等因素,国家经贸委已明文规定禁止采用此种流程新建硝酸装置。
(2)综合法常压氨氧化和中压(0.25~0.5MPa)酸吸收的稀硝酸生产工艺。
这种方法在一定程度上弥补了常压酸吸收的缺点,我国在本世纪50年代末引进该流程进行稀硝酸的工业生产。
该方法主要缺点是常压氨氧化、设备庞大、占地多,需要配备较昂贵的不锈钢材质的氧化氮压缩机,其投资高于下面介绍的中压法,且吸收压力低仅0.35MPa(A),因此酸浓度低及尾气排放不能达到环保要求,不适用于规模较大的硝酸装置,国家经贸委也明文规定了不能采用此种流程建设硝酸装置。
(3)全中压法氨氧化和酸吸收均在中压下进行的稀硝酸生产工艺。
硝酸工艺流程简介

中压蒸
92
11 Βιβλιοθήκη 34582液氨 6
1
1 2
1
1 1
2 尾气
空气
7
2
1
1
1
至漂白
1
1、2—液氨蒸发器, 3—辅助蒸发器, 4—氨过热器, 5—氨过滤器, 6—空气
过滤室, 7—空压机, 8—混合器, 9—氧化炉、过热器、废热锅炉, 10—高温
氨和空气在氨─空混合器中混合以后,进入氧化炉,经过铂网催化剂氧 化生成 NO等混合气体,铂网氧化温度为 860 ℃,然后经过蒸汽过热器、废热 锅炉,再经高温气─气换热器、省煤器、低压反应水冷器,再进入氧化氮分 离器,在此将稀酸分离下来,气体则与漂白塔来的二次空气混合后进入氧化 氮压缩机,进气温度为 60 ℃,压力为 Mpa;出口温度为 200 ℃,压力为 Mpa。 再经尾气预热器、高压反应水冷却器进入吸收塔,进入吸收塔时的氮氧化物 气体温度为 40℃,氮氧化物气体从吸收塔底部进入,工艺水从吸收塔顶部喷 淋而下,二者逆流接触,生成 58 %—60 %的硝酸,塔底酸温度为 40 ℃,从 吸收塔出来的硝酸进入漂白塔,用来自二次空气冷却器的约 120 ℃的二次空 气在漂白塔中逆流接触,以提出溶解在稀酸中的低价氮氧化物气体,完成漂 白过程,漂白后的成品酸经酸冷却器冷却到 40 ℃,进入成品酸贮罐,再用成 品酸泵送往硝铵和间硝装置。
后进入碱吸收塔,经碱吸收后排入大气,排放的尾气中 400ppm。
NOX 的含量最低约
3.常压法稀硝酸生产工艺流程: 空气通过过滤器除去机械杂质和粉尘后经过鼓风机,进入混合器与过滤
后的氨气混合,然后进入氧化炉,反应生成高温的氧化氮工艺气体,工艺气 体经过锅炉、冷却器降温至 40℃,进入吸收塔底部,在常压下经过多个酸吸 收塔吸收,从吸收塔顶部出来的尾气进入多个碱吸收塔,经碱吸收后排入大 气,排放的尾气中 NOX 的含量最低约 2000ppm。
硝酸工艺流程方框图
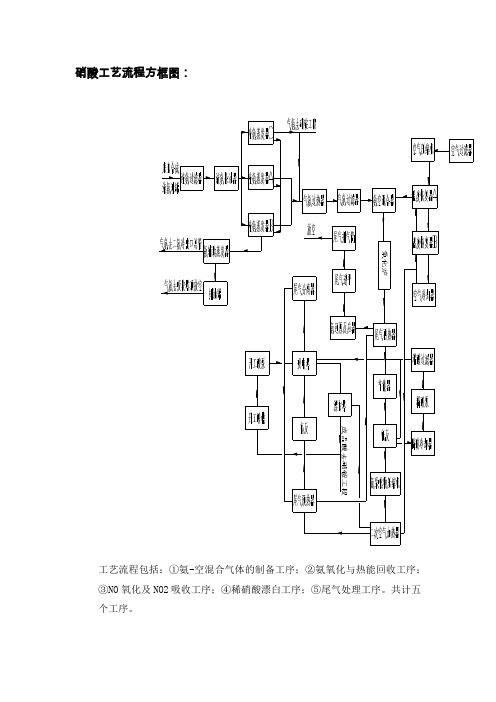
硝酸工艺流程方框图:工艺流程包括:①氨-空混合气体的制备工序;②氨氧化与热能回收工序;③NO氧化及NO2吸收工序;④稀硝酸漂白工序;⑤尾气处理工序。
共计五个工序。
1. 氨空混合气的制备工序由界区来的原料液氨警告液氨过滤器除去液氨中的机械杂质,然后进入液氨除油器除油,一部分送入氨蒸发器C,蒸发后送入硝铵装置。
另一部分送入氨蒸发器A和B,大部分液氨在氨蒸发器A中蒸发,剩余的液氨在氨蒸发器B中蒸发。
蒸发压力维持在约0.6Mpa(G)左右。
氨蒸发器A及B蒸发温度分别为11.5℃及14℃,当液氨中水和油在氨蒸发器B中累积起来时,可将水和油排至氨辅助蒸发器,在该设备中通入低压蒸汽,在105℃下将氨蒸发,此过程可间断或连续操作。
由氨蒸发器A及B来的气氨与氨辅助蒸发器来的热气氨在此混合送至气氨过滤器过滤除杂,然后送至气氨过热器,氨过热到180℃左右,进入氨-空混合器,再去氨氧化反应-余热回收器(亦称:氧化炉-废热锅炉)。
空气经四级立式过滤器后入空气压缩机,出压缩机的空气经过1#温度恢复器、2#温度恢复器和空气冷却器,在空气冷却器中空气温度降到40℃左右,空气中的水冷凝出来,除水后的空气分为一次和二次空气两股气流,一次空气去1#、2#温度恢复器与总空气换热后进入氨-空气混合器,二次空气去氧化和漂白工序。
2、氨氧化与热能回收工序氨-空气混合气体进入氨氧化反应器,经其内部分布器均匀分布于铂网上,进行氨氧化反应,反应方程式为:4NH3+ 5O2= 4NO + 6H2O +Q氨氧化反应,生成一氧化氮、水蒸气,所释放出的热量及氨-空气混合气的显热使一氧化氮气体温度升至860~880℃,此NOx气流经安装在氨氧化炉下部的蒸汽过热器和废热锅炉以回收其热量,混合气体(一氧化氮、二氧化氮、空气中的氮气和氧气、生成的水蒸气)出废热锅炉的温度降至400℃左右。
3、NO的氧化和NO2的吸收工序出废热锅炉的NOx气体流经串联的尾气再热器E-1108、节能器E-1109,当温度降低时,混合气中的NO氧化为NO2。
硝酸生产工艺

摘要:硝酸是基本化学工业的重要产品之一,也是一种重要的化工原料,产量在各类酸中仅次于硫酸。
工业上制取浓硝酸(HNO3浓度高于96%)的方法有三种:一是在有脱水剂的情况下,用稀硝酸蒸馏制取的间接法,习惯上称“间硝”;二是由氮氧化物、氧及水直接合成浓硝酸,称为’直硝’;三是包括:氨氧化、超共沸酸(75%—80%HNO3)生产和精馏的直接法。
本文仅探讨超共沸精馏法。
关键词:浓硝酸、氨氧化、超共沸精馏法前言硝酸是基本化学工业的重要产品之一,也是一种重要的化工原料广泛用于生产化肥、炸药、无机盐,也可用于贵金属分离、机械刻蚀等。
目前,我国有浓硝酸厂家20多家,年生产能力在80万吨以上。
1999年产量在73万~75万吨,到2005年稀硝酸生产能力达544。
7万吨,2004年浓硝酸产量130。
5万吨,2005年产量157万吨,2006年新增产能达300万吨.稀硝酸是合成氨的下游产品,与化肥生产紧密相关。
浓硝酸最主要用于国防工业,是生产三硝基甲苯(TNT)、硝化纤维、硝化甘油等的主要原料。
生产硝酸的中间产物——液体四氧化二氮是火箭、导弹发射的高能燃料。
硝酸还广泛用于有机合成工业;用硝酸将苯硝化并经还原制得苯胺,用硝酸氧化,苯可制造邻苯二甲酸,均用于染料生产。
此外,制药、塑料、有色金属冶炼等方面都需要用到硝酸。
我国硝酸的消费结构大致为:化学工业占65%左右,冶金行业占20%,医药行业占5%,其他行业占10%。
在化学工业中生产浓硝酸的工艺主要有多种大同小异的工艺流程,生产中是根据氨氧化和氮氧化物吸收操作压力的不同分为间接法、直硝法和直接法三种类型。
1 硝酸的性质、用途及生产方法1.1 硝酸的性质纯硝酸为带有窒息性与刺激性的无色液体,其相对密度1。
522,沸点83.4℃,熔点‐41。
5℃,分为浓硝酸和稀硝酸.无水硝酸极不稳定,一旦受热见光就会分解,生成二氧化氮和水.硝酸能与任意比例的水混合,形成浓硝酸(96%~98%HNO3)和稀硝酸(45%~70% HNO3)。
双加压法生产硝酸工艺流程

氧
氨-空气混合气
热量回收 NOX、H2O 气体 废热锅炉、省煤器、蒸汽过热器 860oC
化 炉
铂网触媒层,高温 4NH3+5O2---->4NO+6H2O 0.45MPa
NOX 气体 主要为 NO 400oC
三、氧化氮的氧化和吸收
漂白塔 二次空气 酸气混合物 NOX 气体 换热器 冷却至 156oC 2NO+O2---->2NO2 水冷器Ⅰ 冷却至 40oC 3NO2+H2O---->2HNO3+NO 稀硝酸浓度 34% 分离器 NOX 气体 压缩机 1.0MPa 194oC 冷凝稀硝酸 尾气 换热器 冷却至 126oC
分离器
尾气预热器 至 360oC
尾气膨胀机 回收 60% 总压缩功
排气筒
备注:双加压法,氧化为中压,吸收为高压。 主要设备: (1) 四合一机组:蒸汽透平机、氧化氮压缩机、空气压缩机、尾气透平机、变速箱以及附属设备。 (2) 氨氧化炉 (3) 吸收塔 (4) 漂白塔
双加压法生产硝酸工艺流程一Biblioteka 氨-空气混合气制备过滤空气
0.45MPa 236oC
二次空气 空气压缩机 一次空气
漂 白 塔
氨-空气混合气
气氨 液氨 1.2MPa 18oC 氨蒸发器 0.52MPa 氨过热器 加热至 100oC 氨过滤器
除杂质 氨-空气混合器 氨含量约 9.5%(V) 为
二、氨的氧化与废热回收
吸
硝酸溶液 浓度 66%
收 塔
NOX---水吸收--->HNO3 提高硝酸浓度
水冷器Ⅱ 冷却至 40oC
四、漂白
二次空气
硝酸溶液 浓度 66% 含大量 NOX
硝酸生产工艺

硝酸工艺——超共沸酸精馏法共沸酸法制浓硝酸流程示于下图。
它分为氧化工序,超共沸酸的制造和精馏工序三部分。
原料液氨从液氨贮槽(V101)用泵(P102)抽出,经液氨过滤器(S103)过滤后送至次共沸吸收塔(T202)作为冷却介质,同时将液氨气化为气氨。
空气经空气过滤器(S104、S105)进入“四合一”机组(C118)空气压缩机段,出口空气压力为0.45MPa,经气体换热器(E115)之后,与气氨一起进入氨 空气混合器(S106),经混合过滤器(S107)进入氧化炉(R108)。
在Pt-Rh催化剂的催化下生成NO。
出氧化炉的反应气温度约为820~850℃,经过尾气加热器(E109)、废热锅炉(E110)和快锅冷却器(E111),气体被冷却到49℃,反应过程中所产生的水被冷凝。
冷凝水含有少量硝酸和NOx气体,经冷凝酸分离器(V114)分离之后,稀酸水去漂白塔(T121)。
在此,溶解于酸中的NOx被送至塔底的二次空气气提出来,气提气与氧化塔(T116)出口气体合并。
酸水经减压送至酸水贮槽(V122),其中一部分经酸水泵(P203)进入次共沸吸收塔(T202)循环使用,其余送去酸水处理。
从冷凝酸分离器(V114)分离出来的气体,经气体换热器(E115)加热至160℃进入氧化塔(T116),浓度为58%的稀硝酸送至氧化塔的顶部,气液在氧化塔内接触,NO被氧化成N O2,硝酸则被分解为NO2。
反应后硝酸浓度降至25%,用酸泵(P117)打入次共沸塔(T202),制得58%的酸再循环到氧化塔(T116)。
在次共沸吸收塔中NO继续氧化成NO2,NO2被水吸收生成硝酸,此放热反应在1.15MPa下进行,塔内设有蛇管冷却器,冷却介质为液氨。
液氨在0.6MPa压力下气化吸收反应热,使该塔塔顶温度控制在20℃,排出的尾气中NOx含量小于200 ppm(国家规定的排放标准是500 ppm)。
出塔尾气经气体换热器(E120),进入尾气加热器(E109),再进入“四合一”机组(C118)的尾气透平回收段回收能量后,经烟囱(S119)排入大气。
- 1、下载文档前请自行甄别文档内容的完整性,平台不提供额外的编辑、内容补充、找答案等附加服务。
- 2、"仅部分预览"的文档,不可在线预览部分如存在完整性等问题,可反馈申请退款(可完整预览的文档不适用该条件!)。
- 3、如文档侵犯您的权益,请联系客服反馈,我们会尽快为您处理(人工客服工作时间:9:00-18:30)。
1. 双加压法稀硝酸生产工艺流程
1.1工艺流程示意图如图1-1:
1、2—液氨蒸发器,3—辅助蒸发器,4—氨过热器,5—氨过滤器,6—空气过滤室,7—空压机,8—混合器,9—氧化炉、过热器、废热锅炉,10—高温气气换热器,11—省煤器,12—低压反应水冷器,13—氧化氮分离器,14—氧化氮压缩机,15—尾气预热器,16—高压反应水冷器,17—吸收塔,18—尾气分离器,19—二次空气冷却器,20—尾气透平,21—蒸汽透平,22—蒸汽分离器,23—汽包,24—蒸汽冷凝器。
图1-1 工艺流程示意图
1.2流程简述:
合成氨厂来的液氨进入有液位控制的A、B两台氨蒸发器中,氨在其中蒸发,正常操作时,大部分液氨被A台蒸发器中来至吸收塔的冷却水所蒸发(吸收塔上部冷却水与A蒸发器形成闭路循环),蒸发温度11.5 ℃;其余的液氨被冷却水在B台蒸发器中蒸发,蒸发温度为14 ℃,两台氨蒸发器的蒸发压力均维持在0.52 Mpa;其中的油和水在辅助蒸发器中被分离,蒸发出的气氨进入氨过热器,气氨温度由TV31022控制,温度为110 ℃,然后再经氨过滤器进入氨─空气混合器。
空气从大气中吸入,经过三级过滤进入空气压缩机入口(冬季在经过空气过滤器前由空气预热器预热),经过空气压缩机加压至0.35 Mpa后分为一次空气和二次空气两股气流,一次空气进入氨─空混合器,二次空气进入漂白塔。
氨和空气在氨─空混合器中混合以后,进入氧化炉,经过铂网催化剂氧化生成NO等混合气体,铂网氧化温度为860 ℃,然后经过蒸汽过热器、废热锅炉,再经高温气─气换热器、省煤器、低压反应水冷器,再进入氧化氮分离器,在此将稀酸分离下来,气体则与漂白塔来的二次空气混合后进入氧化氮压缩机,进气温度为60 ℃,压力为0.3 Mpa;出口温度为200 ℃,压力为1.0 Mpa。
再经尾气预热器、高压反应水冷却器进入吸收塔,进入吸收塔时的氮氧化物气体温度为40℃,氮氧化物气体从吸收塔底部进入,工艺水从吸收塔顶部喷淋而下,二者逆流接触,生成58 %—60 %的硝酸,塔底酸温度为40 ℃,从吸收塔出来的硝酸进入漂白塔,用来自二次空气冷却器的约120 ℃的二次空气在漂白塔中逆流接触,以提出溶解在稀酸中的低价氮氧化物气体,完成漂白过程,漂白后的成品酸经酸冷却器冷却到40 ℃,进入成品酸贮罐,再用成品酸泵送往硝铵和间硝装置。
从吸收塔顶部出来的尾气先后经过尾气分离器、二次空气冷却器、尾气预热器、高温气—气换热器,温度升至360 ℃,进尾气透平,回收约60 %的总压缩功,出尾气透平的
气体温度为140 ℃左右,NO
含量≤200 ppm,经排气筒排入大气。
X
在废热锅炉中产生4.0MPa的湿饱和蒸汽,经蒸汽过热器加热到温度440 ℃、压力为3.9 Mpa过热蒸汽进入蒸汽分离器,过热蒸汽用于驱动蒸汽透平,蒸汽过剩送至外界蒸汽管网。
锅炉系统采用强制循环,用锅炉水循环泵(J31002/A/B)使锅炉水在汽包和锅炉间循环。
1.3流程特点:
1.氧化压力为0.45 MPa(A),吸收压力为1.1 MPa(A)。
2.氨的氧化率高达96 %以上,铂耗较低,为120 mg/t100%HNO3(回收前)。
二氧化氮吸
的含量在200 ppm以下。
收率高,硝酸浓度可达60 %,排放的尾气中NO
X
3.采用中温(360 ℃)回收装置尾气能量,使压缩机组的蒸汽透平和尾气膨胀透平之间达到经济匹配,与高温回收相比不必采用耐高温的尾气透平和尾气加热器,工作条件不苛刻,操作稳定可靠。
4.合理利用氨蒸发的冷量,制得18℃低温冷却水去吸收塔冷却盘管移走吸收反应热,有气体的含量。
效降低尾气中NO
X
5.装置副产中压过热蒸汽,除驱动压缩机组蒸汽透平外还可以外送,装置耗电量小,仅
(不含循环水用电)。
为11.1 kw/t100%HNO
3
6.采用DCS控制系统,使操作更加方便和安全。
2.综合法稀硝酸生产工艺流程:
空气通过鼓风机依次经过水洗塔和过滤器,除去机械杂质和粉尘,进入混合器与过滤后的氨气混合,然后进入氧化炉,反应生成高温的氧化氮工艺气体,工艺气体经过锅炉、冷却器降温至40℃,经压缩机加压至0.35Mpa,经过换热降至40℃进入吸收塔底部与塔顶加入的水反应,稀酸从塔底排出进入漂白塔漂白后送入酸罐,从吸收塔顶部出来的尾气经过换热进入透平膨胀机回收能量后进入碱吸收塔,经碱吸收后排入大气,排放的尾气中NO
的含量最低约400ppm。
X
3.常压法稀硝酸生产工艺流程:
空气通过过滤器除去机械杂质和粉尘后经过鼓风机,进入混合器与过滤后的氨气混合,然后进入氧化炉,反应生成高温的氧化氮工艺气体,工艺气体经过锅炉、冷却器降温至40℃,进入吸收塔底部,在常压下经过多个酸吸收塔吸收,从吸收塔顶部出来的尾气进
的含量最低约2000ppm。
入多个碱吸收塔,经碱吸收后排入大气,排放的尾气中NO
X。