QA016 Disposal of Samples (Rev03)
20090113 PI 030-1 PICS 原料药检查备忘(中英文)

2. INTRODUCTION 介绍2.1 The adoption of ICH Q7 as the first truly harmonised GMP guideline for active pharmaceutical ingredients (APIs) and the associated development of regulatory frameworks to implement the guideline as a regulatory standard mark the beginning of a new era of regulation for medicines.采用ICH Q7作为真正意义上的原料药统一GMP指南,并伴随着法规框架的发展以实施指南作为法规的标准,标志着药品法规的一个新纪元。
2.2 The adoption of ICH Q7 by PIC/S occurred in May 2001 with the current version of the guideline having been available since 1 September 2007 as GMP PE 009 (Part II).2001年5月PIC/S采用了ICH Q7,现行版本指南GMP PE 009(第二部分)在2007年9月1日公布.2.3 The primary objective for implementing ICH Q7 is the reduction of the risks associated with the manufacturing quality of APIs and this cannot be achieved without an effective inspection system which addresses the specific aspects of the global API industry.实施ICH Q7的基本目标是减少原料药生产质量所伴随的风险,要达到这个目标,必须制订有效的检查体系,以说明全球原料药行业的各个独特方面。
样品折射率及分散方法
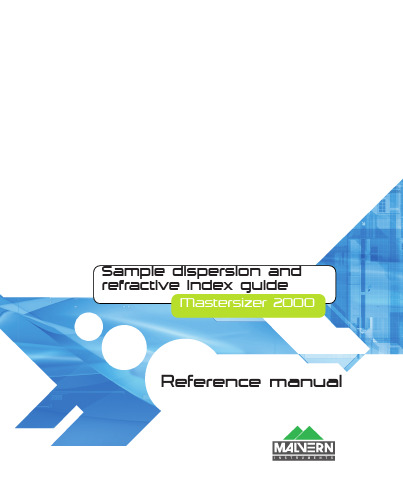
Sample dispersion and refractive index guideMastersizer 2000Reference manualSample Dispersion and RefractiveIndex GuideMAN0396 Issue 1.0 April 2007© Malvern Instruments Ltd. 2007Malvern Instruments makes every effort to ensure that this document is correct. However, due to Malvern Instruments’ policy of continual product development we are unable to guarantee the accuracy of this, or any other document after the date of publication. We therefore disclaim all liability for any changes, errors or omissions after the date of publication. No reproduction or transmission of any part of this publication is allowed without the express written permission of Malvern Instruments Ltd.Head office:Malvern Instruments Ltd.Enigma Business Park,Grovewood Road,Malvern,Worcestershire WR14 1XZUnited Kingdom.T el + [44] (0)1684-892456Fax + [44] (0)1684-892789Printed in EnglandT able of ContentsRefractive index list. . . . . . . . . . . . . . . . . . . . . . . . . . . . . . . . . . . . . . . 1-1Sample dispersion guide. . . . . . . . . . . . . . . . . . . . . . . . . . . . . . . . . . 2-1 Sample Dispersion and Refractive Index Page iT able of Contents Sample Dispersion and Refractive Index Page ii MAN 03961 Refractive index listCompound Formula Refractive indexAcanthite (Silver Sulphide)Ag2S 2.2Acetal 1.48Acetone 1.36Adipic Acid(CH2.CH2.COOH)2 1.433Agate SiO2 1.544-1.553Albite Na2O.AI2O3.6SiO2 1.529Albite (Feldspar)NaAlSi3O8 1.527-1.538Almandine (Garnet) 1.830Alumina AI2O3 1.760Alumina trihydrate AI2O33H20 1.577-1.595Aluminium Hydroxide (Nat. Boehmite)Al(OH)2AlO(OH)1.56 - 1.751.64 - 1.67Aluminium Oxide (Corundum)Al2O3 1.76 - 1.7681.765Aluminium Silicate Al2O3.SiO2 1.65Aluminium Stearate Al(C18H35O2)3 1.49Aluminum Sulphate AI2(SO4)3 1.47Ammonium Chloride NH4CI 1.642Ammonium Sulphate NH4SO4 1.523Ammonium Dihydrogen Phosphate(NH4)H2P2O6 1.52Anatase (Titanium Dioxide)TiO2 2.49 - 2.56Andesine (Feldspar)([NaSi]0.7-0.5 [CaAl]0.3-0.5)AlSi2O8 1.544 - 1.563Sample Dispersion and Refractive Index Page 1-1Chapter 1Refractive index list Page 1-2MAN 03961 Andradite (Garnet)1.887Anglesitte (Lead Sulphate)PbSO 4 1.8771 - 1.8937Anhydrite (Calcium Sulphate)CaSO 4 1.5698 - 1.6136Anhydrite (Gypsum)CaSO 4.2H 2O 1.57 - 1.61Anhydrous BoraxNa 2O.2B 2O 3 1.501Anorthite (Feldspar)CaAl 2Si 2O 8 1.577 -1.590Anorthoclase (Feldspar)(Na,K)AlSi 3O 8 1.523 - 1.529Antimony Trioxide(Nat. Semarnontite)(Nat. Valentine)Sb 2O 3 2.0872.18 - 2.35Antimony VermilionSb 2S 3 2.65Aragonite (Calcium Carbonate)CaCO 3 1.530 - 1.686Arsenic Sulphur Glass2.61Arsenous OxideAs 2O 3 1.76 (V)1.92 (I)Asphaltum (Bitumen)1.64 - 1.66Azurite2CuCO 3.Cu(OH)2 1.73 - 1.83Baddeyelite (Zirconium Oxide)ZrO 2 2.13 - 2.20Barite (Barytes)BaSO 4 1.6362 - 1.6482Barium Carbonate (Witherite)BaCO 3 1.529 - 1.677Barium ChlorideBaCI 2.2H 2O 1.642Barium Crown Glass(Light)(Medium)(Dense)1.540651.5761.613Barium FluorideBaF 2 1.47Barium OxideBaO 1.98Barium Sulphate (Barite, Barytes)BaSO 4 1.637 - 1.649Barium Mono-sulphideBaS 2.155Barium TitanateBaTiO 3 2.40Barium YellowBaCrO 4 1.94 - 1.98Barytes (Barite, Blanc Fixe)BaSO 4 1.636 - 1.649Benzene C 6H 6 1.50CompoundFormula Refractive indexRefractive index list Chapter 1Sample Dispersion and Refractive Index Page 1-3Benzyl AlcoholC 6H 5CH 2OH 1.538-1.541Benzyl Benzoate1.568-1.570Beryllium OxideBeO 1.719Biotite (Mica)K(Mg,Fe)3 AlSi 3O 10(OH,F)2 1.565 - 1.696Bitumen1.6500Black Pigments1.675 (average)Blanc Fixe (Artificial Barytes)BaSO 4 1.638 - 1.649Blue Pigments1.63 (average)BoehmiteAlO(OH) 1.64 - 1.67Bone BlackC + Ca 3(PO 4)2 1.65 - 1.70Boracic AcidB 2O 3.3H 2O 1.456BoraxNa 2B 4O 7 1.4466 - 1.4687BoraxNa 2O.2B 2O 3.10H 2O 1.469Boric OxideB 2O 3 1.459Boro-silicate Crown Glass(Soda lime glass)1.509701.513Boron OxideB 2O 3 1.61-1.64Boron Oxide GlassB 2O 3 1.485Brick Dust1.44Brookite (Titanium Dioxide)TiO 2 2.5831 - 2.7004Brown Pigments1.653 (average)N-butanolCH 3CH 2CH 2CH 2OH 1.3993ButanoneCH 3CH 2COCH 3 1.38Butter Fat1.4548Cadmium IodideCdI 2 2.7Calcium MetaborateCa(BO 2)2 1.660Cadmium OxideCdO 1.49Cadmium RedCdS(Se) 2.64 - 2.77Cadmium Red LithoponeCdS(Se) + BaSO 4 2.50 - 2.76Cadmium Sulfide (Greenockite)CaS 2.506 - 2.529Cadmium YellowCdS 2.35 - 2.48Cadmium Yellow Lithopone CdS + BaSO 4 2.39 - 2.40CompoundFormula Refractive indexChapter 1Refractive index list Page 1-4MAN 0396Calcite (Calcium Carbonate)CaCO 3 1.486 - 1.740Calcium CarbideCaC 2 1.750Calcium CarbonateCaCO 3 1.681 (IV)Calcium Carbonate(Aragonite)(Nat. Calcite)(Nat. Vaterite)CaCO 3 1.53 - 1.6851.4864 - 1.741.55 - 1.65Calcium Carbonate HexahydrateCaCO 3.6H 2O 1.460 - 1.545Calcium ChlorideCaCI 2 1.52Calcium ChloriteCa(ClO)2.2Ca(OH)2 1.51 - 1.585Calcium Fluoride (Fluorite)CaF 2 1.43 - 1.44Calcium Hydroxide (Hydrated Lime)Ca(OH)2 1.545 - 1.574Calcium HypochloriteCa(ClO)2 1.545 - 1.69Calcium Hypochlorite Tri-hydrateCa(ClO)2.3H 2O 1.535 - 1.63Calcium Magnesium Carbonate(Dolomite)CaCO 3, MgCO 3 1.5026-1.6817Calcium Metasilicate (a)CaSiO 3 1.6350Calcium Metasilicate (b)(Nat. Wollastonite)CaSiO 3 1.6145Calcium Molybdate (Pawellite)CaMoO 4 1.97Calcium Oxide (lime) (Calcia)CaO 1.838Calcium PeroxideCaO 2 1.895Calcium PhosphateCa 3(PO 4)2 1.629(tri) Calcium PhosphateCa 3(PO 4)2 1.627Calcium Meta Silicate (a)(Nat. Pseudowollastonite)CaSiO 3 1.610 - 1.664Calcium Meta Silicate (b)(Wollastonite)CaSiO 3 1.616 - 1.613Calcium Di-ortho Silicate ICa 2SiO 4 1.717 - 1.735Calcium Di-ortho Silicate IiCa 2SiO 4 1.717 - 1.735Calcium Di-ortho Silicate IiiCa 2SiO 4 1.642 - 1.654Calcium Tri-silicate (Nat. Alite)Ca 3SiO 5 or 3Ca.SiO 2α 1.718 - β 1.724CompoundFormula Refractive indexCalcium Sulphate(Nat. Anhydrite) (Nat. Gypsum)CaSO4.2H2OCaSO4.2H2O1.569 - 1.6131.521 - 1.53Calcium Sulphide (Nat. Oldhamite)CaS 2.137Calcium Titanate CaTiO3 1.57Calcium Tungstate CaWO4 1.9185Caraway Oil 1.485-1.492 Carbon (Lamp Black, Graphite)C 2.42Carbon Tetrachloride / Tetrachlo-romethaneCCl4 1.46Cardamom Oil 1.461-1.467 Castor Oil 1.4770Castrol 1.1000Cellulose Acetate 1.46-1.5 Cellulose Acetate Butpate 1.46-1.49Cement 1.68 (average) Cerium Compounds 1.8282Cerium (iii) Orthophosphate (nat.Monazite)CePO4 1.774-1.851 Cerulean Blue CoO.ηSnO2 1.84Cerussite PbCO3 1.804 - 2.079 Chalk (Whiting)CaCOSee Calcium Carbonate1.53 - 1.68Chalcedony (Fiberous, ImpureQuartz)SiO2 1.544- 1.553 Chazabite 1.482China Clay(Kaolinite)Al4Si4O10(OH)8 1.533 - 1.577 Chloroform CHCI3 1.446Chocolate 1.5900Chrome Alum Cr2(SO4)3.K2SO4.24H2O 1.481Chrome Orange PbCrO4.Pb(OH)2 2.42 - 2.7 Chrome Green (med.)Fe4[Fe(CN)6]3 + PbCrO4 2.4Chrome Yellow (med.)PbCrO4 2.31 - 2.49 Chromic Oxide Cr2O3 2.551 Compound Formula Refractive indexChromium Cr 3.51Chromium Oxide Green Cr2O3 2.5Cigarette Ash 1.53Cinnamon Oil 1.573-1.600Clofibrate 1.500-1.505Clove Oil 1.528-1.537Coconut Oil 1.448-1.450Cobalt Blue CoO.Al2O3 1.74Cobalt Carbonate(Nat. Spherocobaltite)CoCO3 1.60 - 1.855Cobalt Ii Per-chlorate Co(ClO4)2.6H2O 1.55Cobalt Ii Per-chlorate (Needles)Co(ClO4)2 1.490-1.51Cobalt Ll Chloride Di-hydrate CoCl2.2H2O 1.625 - 1.67Cobalt Fluosilicate CoSiF6.6H2O 1.382 - 1.387Cobalt Green CoO.πZnO 1.94 - 2.0Cobalt Yellow CoK3(NO2)6.H2O 1.72 - 1.76Cobalt II Oxide CoO 1.74Cobalt Violet Co3(PO4)2 1.65 - 1.81Cocoa Butter 1.4568Cobaltous Nitrate Co(NO3)2.6H2O 1.4Cobaltus Sulphate CoSO4.7H2O 1.483Coconut Oil 1.4493Cod-liver Oil 1.481Coffee Dust 1.53Copper Cu0.25Copper II Carbonate(Nat. Malachite) (Nat. Azurite, Chessylite)CaCO3.Cu(OH)22CaCO3.Cu(OH)21.655 - 1.9091.730 - 1.838Copper L Chloride (Nantokite)CuCl 1.93Copper II Chloride Di-hydrate CuCl2.2H2O 1.644 - 1.731 Copper I Oxide (Cuprite)Cu2O 2.705Copper II Oxide (Tenorite)CuO 2.63Copper III Oxide 1.93 Compound Formula Refractive indexCopper I Sulphate (powder)Cu2SO4 1.724 - 1.739 Copper II Sulphate(Nat. Hydrocianite)CuSO4 1.733Copper II Sulphate Basic(Nat. Brochantite)CuSO4.3Cu(OH)2 1.728 - 1.800Copper II Sulphate Pentahydrate(Nat. Chalcanthacite)(CuSO4.5H2O) 1.514 - 1.543 Copper II Sulphide (Nat. Covellite)CuS 1.45 Coriander Oil 1.462-1.472 Cork Dust 1.49 - 1.65 Corn Oil (Zea Mays) 1.4734 Corundum (Ruby, Saphire)Al2O3 1.759 - 1.772 Cotton 1.459 - 1.58 Cotton Seed Oil 1.4735 Covellite (Copper II Sulphide)CuS 1.45 Cristobalite (Quartz)SiO2 1.484 - 1.487 Crotamiton 1.540-1.542 Crown Glass(Soft) (Hard)1.51516 1.51899Cryolite3NaF.AIF3 1.339Cupric Oxide CuO 2.63Cuprite (Copper I Oxide)Cu2O 2.705 Cuprous Oxide Cu2O 2.705Cyclic Ketone Resin 1.60 Cyclohexane 1.4266 Cyclohexanone 1.45 Dandruff & Epithelial Cells 1.53N - Decane CH3, (CH2) 8CH3 1.4102 Dementholised 1.456-1.466 Diglyme (Dimethyldigol orDiethylene Glycol Dimethylether)(CH3, O,CH2, CH2)20 1.4070-1.4085 Diamond C 2.4175Diatomaceous Earth (Silicon Dioxide)SiO2 1.435Compound Formula Refractive indexDichloromethane 1.42Diethyl Phthalate 1.500-1.505 Dimethyl Sulphoxide 1.478-1.479 Dill Oil 1.481-1.492 Dimer Caprol 1.568-1.574 Dimethylformamide 1.4305 Dolomite CaCO3.MgCO3 1.5026-1.6817 Dover 1.4300 Eddingtonite 1.55 Egyptian Blue CaO.CuO.4SiO2 1.605 - 1.635 E.K.2 1.74338 Emerald Green (Paris green)Cu(C2H3O2)2.2Cu (OH)2 1.71 - 1.78 Epithelial Cells (Dandruff) 1.53Epoxy 1.58Epsom Salt (Epsomite)MgSO4.7H2O 1.433 - 1.461 Ethanol CH3CH20H 1.36 Ethanediol HOCH2CH2OH 1.43 Ethanolamine H2NCH2CH2OH 1.453-1.459 Ethyl Cinnamate 1.558-1.560 Ethylene Glycol HOCH2CH2OH 1.432 Eucalyptus Oil 1.458-1.470 Feldspar(Albite) (Andesine) (Anorthite) (Anorthoclase) (Microcline) (Oligoclase) (Orthoclase)NaAlSi3O8AlSi2O8CaAl2Si 2O8(Na,K)AlSi3O8KAlSi3 O8([Na,Si]0.9-0.7 [CaAl]0.1-0.3) AlSi2 O8KAlSi3 O81.527 - 1.5381.544 - 1.5631.577 - 1.5901.523 - 1.5291.514 - 1.5391.533 - 1.5521.518 - 1.539Ferric Oxide Fe2O3 3.01Ferric Sulphate Fe2(SO4)3 1.814Ferroso - Ferric Oxide Fe3O4 2.42 Compound Formula Refractive indexFerrous Carbonate FeCO3 1.875 Ferrous Oxide FeO 2.32 Ferrous Sulphate (Copperas)FeSO4.7H2O 1.471Flint(Impure Quartz) (Telescope) (Barium) (Barium light ) (Borate) (Special barium) (Extra light)SiO21.5531.530421.604831.567131.613261.744161.54769Flint Glass (Light)(Dense)(Extra dense) (Double extra dense)1.53 - 1.96 1.57838 1.62258 1.65108 1.80120Flour Crown 1.49429Fluorite (Fluorspar)CaF2 1.433 - 1.435 Fluorspar (Avorite)CaF2 1.433 - 1.435 Fractionated Coconut Oil 1.445-1.451 Fractionated Palm Kernel Oil 1.445-1.447 Furhairs 1.54 - 1.55Fused Quartz 1.45887Gallium Antimonide GaS6 3.8 (approximately) Gallium Arsenide GaAs 3.33 (approximately) Gallium Phosphide GaP 3.39Garnet (Almandine) (Andradite) (Grossularite) (Hydrogrossularite) (Pyro pe) (Spessartite) (Uvarovite)1.779 (average) 1.8301.8871.7341.675 - 1.734 1.7141.801.86Compound Formula Refractive indexGlass(Hardcrown) (Borosilicate crown) (Medium barium crown) (Dense barium crown) (Light flint)(Dense flint)(Extra dense flint) (Double extra dense flint)1.518 1.509 1.576 1.613 1.583 1.621 1.652 1.802Glass (crown) 1.48 - 1.61 Glass (flint) 1.53 - 1.96 Glasses & Mineral Wools 1.47 - 1.62 Glycerol 1.47D-Glucose Pentaamethylether C1,H22O6 1.4466 Glycine Soja (Soybean Oil) 1.4729 Gmelinite 1.481Goethite (Ochre, Yellow) (Sienna, Raw)Fe2O2.H2O2.0 - 2.41.87 -2.17Gold Au0.28 - 0.31Green Earth 1.62Greenockite CaS 2.506 - 2.529 Green Pigments 1.811 (average) Grossularite (Garnet) 1.734D-gulcitol (D-Sorbitol) 1.333Gum 1.54Gypsum(Calcium Sulphate Dihydrate)CaSO4.2H2O 1.519 - 1.531 Hafnium Hf 3.64Hair (human) 1.54 - 1.56Halite (Rock Salt)NaCl 1.544Hardcrown Glass 1.518 Harmotome 1.5078 Hausmannite (Manganese Oxide)Mn3O4 2.15 - 2.46 Helianthus (Annus) 1.4694HematiteCompound Formula Refractive index(Iron III Oxide)Fe2O3 2.94 - 3.22 Heptane C7H16 1.39Herring Oil 1.4610 Heulandite 1.500 Hexane C6H14 1.38 Hydroglossularite (Garnet) 1.675 - 1.734 Ibuprofen 1.4364 Iceland Spar (Calcite)CaCO3 1.658 - 1.486 Insect Parts 1.54 - 1.55 Illite (Clay Minerals)K(1-1.5) Al4SiAl(1-1.5)O20(OH)4 1.54 - 1.61 Indian Yellow C19H18O11Mg.5H2O 1.67Indium Antimonide InSb 4.3Indium Phosphide InP 3.42Ink 1.5Ink-orange 1.36 Intralipid 1.46Iriduim Ir 2.53Iron Fe 2.86Iron Oxide (Nat. Magnetite)Fe3O4 2.42Iron Ii Oxide (Nat. Wuestite)FeO 2.32Iron III Oxide (Nat. Hematite)Fe2 O3 2.94 - 3.22 Iron II Sulphate(Heptahydrate, Nat. Melanterite) (Pentahydrate, Nat. Siderotil) (Tetrahydrate)FeSO4.7H2OFeSO4.5H2OFeSO4.4H2O1.471 - 1.4861.526 - 1.5421.533 - 1.535Iron III Sulphate (Enneahydrate, Nat. Coquimbite)Fe2(SO4)3Fe2(SO4)3.9H2O1.8141.552 - 1.558Iron Sulphide(Nat. Marcasite, Pyrite, Pyrrhotite)FeS2 1.56Iso - Octane(CH3)3C,CH2,CH(CH3)2 1.3914Isopar G 1.42Isopar M 1.436Isoparaffin 1.429 Compound Formula Refractive indexIsopropyl Alcohol(CH3)2CHOH 1.377-1.378 Isopropyl Myristate 1.434-1.437 Jojoba 1.465Kalinite (Potassium AluminiumSulphate)KAl(SO4)2.12H2O 1.429 - 1.456 Kaolinite (China Clay)Al4 Si4 O10 (OH)8 1.533 - 1.570 Kieserite (Magnesium Sulphate)MgSO4.H2O 1.52 - 1.58 Lactose C12H22O11.1H2O 1.54 Lanthunum Fluoride LaF 1.60Latex Rubber 1.51 Laumontite 1.5148Lead Pb 2.01Lead Carbonate (Cerussite)PbCO3 1.8036 - 2.0786 Lead Chloride PbCl2 2.217Lead Chromate (Crocoite)PbCrO4 2.29 - 2.66 Lead Dioxide PbO2 2.3Lead Fluoride PbF2 1.75Lead Glass (20% lead content) 1.54Lead Molybdate (Nat. Wulfenite)PbMoO4 2.283 - 2.403 Lead Oxide (Litharge)PbO 2.665 - 2.535 Lead Oxide (mono)PbO 2.51-2.71Lead Oxide(minim)Pb3O4 2.51-2.71Lead (red)(Lead Oxide Pigment)PbO 2.420Lead Sulphate(Anglesite) (Nat. Lanarkite)PbSO4PbSO4PbO1.82 - 1.8941.93 -2.02Lead Sulphide (Galena)PbS 3.921 Lead (white)(Basic Carbonate)(Hydro-cerussite, Cerussite)2PbCO3.Pb(OH)2PbCO31.94 -2.091.804 -2.078Lead (white)(Basic Sulphate, Lanarkite)PbSO4.PbO 1.930 - 2.02 Leather Dust 1.54 Compound Formula Refractive indexLemon Oil 1.474-1.476 Lepidolite (Mica)Kl2(Li,Al)5-6 Si6-7Al2-2O20(OH,F)4 1.525 - 1.587 Levyn 1.498 Limonene (Opticlear) 1.470 Linseed Oil 1.4782 Liquid Paraffin (Light) 1.4680 Lithium Carbonate Li2CO3 1.567 Lithium Fluoride LiF 1.3915 Lithium Mica (Lepidolite)K2(Li,Al)5-6 Si6-7Al2-1O20 (OH,F)4 1.525 - 1.587 Lithium Mica 1.554 - 1.587 Lithium Oxide Li2O 1.644Lithopone(Zinc Sulphide a Nat. Wurtzite) (Zinc Sulphide b Nat. Sphalerite)ZnS2.356 - 2.3782.368Lodestone (Magnetite)Fe3O4 2.420 Macrogol 300 (Polyethylene Glycol300)1.462-1.466 Magnesite (Magnesium Carbonate)MgCO3 1.563 - 1.7 Magnesium Carbonate (Magnesite)MgCO3 1.563 - 1.7 Magnesium Chloride MgCI2.6H2O 1.59-1.675 Magnesium Fluoride (Sellaite)MgF2 1.378 - 1.390 Magnesium Hydroxide Mg(OH)2 1.559-1.58 Magnesium Oxide (Periclase)MgO 1.7350 Magnesium Sulphate Colourless, V MgSO4.H2O 1.535 Magnesium Sulphate Colourless, IV,VMgSO4.7H2O 1.455Magnesium Sulphate(Epsomite, Epsom Salt)MgSO4MgSO4.7H2O1.561.433 - 1.461Magnetite (Iron Oxide, Hematite)Fe3O4 2.42Malachite Cu2 (OH)2(CO3) 1.655 - 1.909 Manganese Mn 2.52Manganese Blue BaMnO4 + BaSO4 1.65Manganese Carbonate MnCO3 1.817 Compound Formula Refractive indexManganese Dioxide MnO2 2.4 Manganese Oxide(Manganosite)MnO 2.16 Manganese Oxide (OUS)MnO 2.16 Manganese Oxide Mn3O4 2.46 Manganese Sulphate MnSO4.4H2O 1.508 Manganese Violet(NH4)2Mn2(P2O7)2 1.67 - 1.75 Marcasite (Iron Di-sulphide)FeS2 1.87 Methanol CH3OH 1.33 Methylmethycrylate 1.48-1.501 - Methyl Naphthalene CH3C10H7 1.62 Methyl Salicylate 1.535-1.538 Mesolite 1.506Mica (Muscovite) (Paragonite) (Phlogopite) (Biotite) (Lepidolite)see individual compounds1.552 - 1.6161.564 - 1.6091.530 - 1.6371.565 - 1.6961.525 - 1.587Microcline (Feldspar)KAlSI3O8 1.514 - 1.539 Miglyol (Coconut Oil) 1.4493Milled Glass 1.55Milk Fat 1.46Milk Serum 1.34Millerite (Nickel Sulphide)NiS 1.81Minium (Lead Sulphide)Pb3O4 2.40 - 2.44 Molybdate, Orange Pb(Mo,S,Cr,P)O4 2.55 Molybdenum Mo 3.71Monazite (cerium (III)Orthophosphate)(CeLaTh)PO4 1.774-1.851Montmorillonite (Clay Minerals)(0.5Ca,Na)0.7(Al,MhFe)4(Si,Al)8020(OH)41.48 - 1.64 Mordenite 1.4798Muscovite (Mica)KAl2 Si3 AlO10(OH,F)2 1.552 - 1.616 Mustard Oil 1.475 Compound Formula Refractive indexCompound Formula Refractive index Natrolite 1.483Neat’s Foot Oil 1.464Nickel Ni 1.98Nickel Oxide NiO 2.182Nickel Oxide (Bunsenite)NiO 2.18Nickel Sulphate NiSO4 1.48Nickel Sulphate, Hexahydrate NiSO4.6H20 1.511Niobium Nb 1.80Nutmeg Oil 1.472-1.488Nylon 1.53Ochre, Yellow (Goethite)Fe2O2.H2O 2.0 - 2.4Olea Europa Sativa (Olive Oil) 1.4679 Oligoclase (triclinic)([NaSi]0.9-0.7[CaAl]0.1-0.3)AlSi2O8 1.533 - 1.552 Olive Oil (Olea europa sativa) 1.4679Orange Oil 1.472-1.476 Orange Pigments 2.593 (average) Orthoclase (Feldspar)KAlSi3O8 1.518 - 1.539 Osmium Os 3.88Palladium 1.80Palm Oil 1.4578Palm-kernel Oil 1.4569 Paragonite (Mica)NaAl2Si3AlO10(OH)2 1.564 - 1.609 Paraffin 1.43Paraffin Wax 1.446 Paraldehyde 1.403-1.406 Peanut Oil 1.4691 Peppermint Oil 1.460-1.467 Periclase (Magnesium Oxide)MgO 1.7350Perspex 1.495Phlogopite (Mica)KMg3AlSi3O10(OH,F)2 1.530 - 1.637 Phillipsite 1.498 Phosphorous (yellow)P4 2.144Phthalocyanine Blue(Copper phthalocyanine)1.38Phthalocyanine Green(Chloro-copper phthalocyanine)1.40 Phytomenadine (Vitamin K1) 1.526-1.528Pigments (Red) (Blue)(averages) 2.5221.63Platinum Pt 4.50Poly (1,2 - Butadiene) 1.50Poly (2 - Vinyltetrahydrofuran) 1.55Poly (2 - Vinylthiophene) 1.6376 Polycarbonate 1.60Pollens & Spores 1.5Polyester Resin 1.523 - 1.54 Polyethylene (Low Density) 1.50-1.54 Polyethylene (Med. Density) 1.52-1.54 Polyethylene (High Density) 1.54 Polymethylmethacrylate 1.4760 Polypropylene 1.49Polystyrene 1.59-1.6 Polystryene Acrylonitrile 1.56 - 1.57 Polytetrafluoroethylene (PTFE) 1.30 - 1.40 Polytrifluorochloroethylene 1.43Polyvinyl Acetate (PVA) 1.395 Polyurethane 1.5 - 1.6 Polyvinylchloride (rigid) (PVC) 1.54 Polyvinylchloride (Non-rigid) (PVC) 1.50 - 1.54Poppy-seed Oil 1.4685Potash Alum(Potassium Aluminium Sulphate)KAl(SO4)2.12H2O 1.429 - 1.456Potassium Aluminium SulphateNat. Kalinite (Potash Alum)KAl(SO4)2.12H2O 1.429 - 1.456 Potassium Bromide KBr 1.55Potassium Carbonate (Pearl ash)K2CO3 1.531 Compound Formula Refractive indexCompound Formula Refractive index Potassium Chromate K2CrO4 1.726Potassium Nitrate KNO3 1.504Potassium Phosphate KH2PO4 1.50Potassium Silico Fluoride K2SiF6 1.399Potassium Iodide KI 1.677Potassium Chloride (Sylvite)KCl 1.49Propan-2-ol (IPA)(CH3)2CHOH 1.39Propylene Glycol CH3CH(OH)CH2OH 1.431-1.433 Prussian Blue Fe[Fe(CN6)]3 1.56Pumice (Volcanic Glass)[Na,K,Al] 1.500PVC 1.53PVT 1.5500Pyrolusite (Manganese Oxide)MnO2 2.4Pyrope (Garnet) 1.714Pyrrhotite (Iron Sulphide)Fe(1-0.8)S 1.56QuartzSiO2 1.544 - 1.553 (Chalcedony, Cristobalite, Flintsilica,Silicon Dioxide, TridymiteQuinacridone Violet C20H12O2N2 2.02 (average) Rapeseed Oil 1.4706Red Lead Pb3O4 2.42Red Pigments 2.522 (average) Resins - See ‘epoxy’Resin (Cyclic Ketone) 1.60Rhodium Rh 2.14MnCO3 1.816 - 1.597 Rhodochrosite(Manganese Carbonate)Rice Bran (Refined) 1.469Rocksalt (Halite, Sodium Chloride)NaCl 1.544Rubber Gum (Soft / Hard) 1.33 - 1.540Ruby (Corundum)Al2O3 1.759 - 1.763 Ruthenium Ru 4.8Rutile (Titanium Dioxide)TiO2 2.605 - 2.901Safflower Oil 1.462 Sardine Oil 1.4660 Sapphire (Corundum)Al2O3 1.767 - 1.772 Saw Dust & Wood Flour 1.53 Scolecite 1.5156 Selenium Se 2.8 (approx) Selenium Glass 2.6 (approx) Sesame Oil 1.4646 Sienna, Burnt Fe2O3 1.85 Sienna, Raw (Goethite)Fe2O3.H2O 1.87 - 2.17Silica (Crisobalite) (Quartz) (tridymite)SiO21.4871.5441.469Silicon Si 3.5 (approx) Silicon Carbide SiC 2.64 - 2.65Silicon Dioxide (Nat. Cristobalite) (Nat. Lechatelierite) (Nat. Tridymite) (Nat. Quartz)SiO21.484 - 1.4871.45881.469 - 1.4711.544 - 1.533Silicon Nitride Si3N4 2.02Silicon Oil 1.4030Silver Ag0.2Silver Bromide (Bromyrite)AgBr 2.235Silver Chloride (Cerargyrite)AgCl 2.071Silver Cyanide AgCN 1.685 - 1.940 Silver Iodide (Iodyrite)AgI 2.21Silver Nitrate AgNO3 1.729 - 1.788 Soap (Powdered) 1.500Sodium Biborate (Borax)Na2O.2B2O3.10H2O 1.469Sodium Carbonate(White, Powder HYG)Na2CO3. 1.500Sodium Carbonate (White, V)Na2CO3.10H2O 1.500Sodium Bicarbonate NaHCO3 1.500 Compound Formula Refractive indexCompound Formula Refractive index Sodium Chloride NaCl 1.5442Sodium Chloride (colourless, V)NaCl 1.520Sodium (di) Silicate Na2Si2O5 1.5-1.51Sodium Fluoride (Villaumite)NaF 1.32NaHCO3 1.50Sodium Hydrogen Carbonate(Sodium Bicarbonate)Sodium Hydrogen Sulphite NaHSO3 1.526Sodium Metaphosphate NaPO3 1.478Sodium Metasilicate Na2SiO2 1.520Sodium Metal Na 4.22Sodium Nitrate NaNO3 1.336 - 1.587 Sodium Nitrate (colourless,IIIa)NaNO3 1.587Sodium (ortho) Silicate Na4SiO4 1.53Sodium Silicofluoride Na2SiF6 1.312Sodium Sulphate Na2SO4.10H2O 1.396Na2SO4.10H2O 1.396Sodium Sulphate(colourless, IV, V,EFF)Sodium Sulphite Na2SO3 1.515-1.565 Sodium Sulphate (Anhydrous)Na2SO4 1.471-1.484D-sorbitol (D-Gulcitol) 1.333Soya Oil 1.465-1.475 Soybean Oil At 40°C (glycine soja) 1.4729Spearmint Oil 1.484-1.491 Spessartite (Garnet) 1.80Spores & Pollen 1.5Sphalerite (Zinc Sulphide b)ZnS 2.368Spinel (Magnesium Aluminate)MgAl2O4 1.71 - 1.72SPS Clay 1.4600Stannic Oxide SnO2 1.997Starch (Amylum)(C6H10O5)n 1.53Stilbite 1.4983Strontium Carbonate SrCO3 1.664Strontium Oxide SrO 1.810Strontium Sulphate SrSO4 1.624 Strontium Titanate SrTiO3 2.39 Strontium Yellow SrCrO4 2.01 Sulphur S8 1.957 Sucrose (saccharose)C12H22O11 1.538 Sugars - See SucroseSunflower-seed Oil 1.4694 Sylvine KCl 1.49050 Sylvite (Potassium Chloride)KCl 1.49Talc3MgO,4SiO2,H2O 1.589 Tantalum Ta 1.70 Tartaric Acid 1.49Tea Dust 1.530 Terpeneless Lemon Oil 1.475-1.485 Tetrachloromethane CCl4 1.46 Tetrahydrofuran (THF)CH2.(CH2)2.CH2O 1.41 Thallium Bromide TlBr 2.40 - 2.8 Thallium Bromide-Thallium Chloride TlBr-TlCl3 2.33 Thallium Bromide-Thallium Iodide TlBr-TlI 2.57 Thallium Chloride TlCl3 2.33 Theobroma Oil (Cocoa Butter) 1.456-1.458 Thomasonite 1.5225Tin IV Chloride SnCl4 1.512Tin Iodide SnI2 2.106Tin IV iodide SnI4 2.106Tin IV Dioxide (Nat. Cassiterite)SnO2 1.997 - 2.093 Titanium Ti 2.15 Titanium Barium White TiO2 25%, BaSO4 75% 1.7-2.5 Titanium Calcium White TiO2 25%, CaSO4 75% 1.8-2.0Titanium Dioxide (Anatase) (Rutile)TiO22.493 - 2.5542.616 - 2.903Compound Formula Refractive indexCompound Formula Refractive index Titanium OxideTiO2 2.49 - 2.554 (Anatase) Brown or Black, IITiO2 2.586Titanium Oxide(Brookite) Brown, I, Black, IVTiO2 2.56 - 2.90 Titanium Oxide (Rutile) Colourless (ifpure), Brown IITitanium Dioxide + Calcium Sulfate TiO2 +CaSO4 1.98 - 2.605 Tobacco Dust 1.53Toluene C6H5CH3 1.49Toners 1.42 - 2.42Tri Aluminate Ca3AI2O6 or 3CaOAI2O2 1.710Tri Aluminate Hexahydrate3CoOAI2O3GH2O 1.603Tri Calcium Phosphate Ca3(Po4)2 1.627 Triethanolamine 1.482-1.4851,1,1- Trichloroethane CH3CCL3 1.49 Trichloroethylene CHCL:CCl2 1.48Tridymite (Silicon Dioxide)SiO2 1.471 - 1.483 Tungstic Acid H2WO4 2.24Tungsten acid (ortho)H2WO4 2.24Turpeneless Orange Oil 1.461-1.473 Turpentine Oil 1.467 - 1.477 Ultramarine Blue Na8-10 Al6Si6O24S2-4 1.51 - 1.63 Ultramarine Violet 1.56Umber, Burnt Fe2O3 + MnO2 2.2 - 2.3Umber, Raw Fe2O3 + MnO2 + H2O 1.87 - 2.17Urea-formaldehyde 1.54 - 1.56 Uvarovite (Garnet) 1.86Van Dyke Brown (Bitumous earth) 1.62 - 1.69 Vanadium V 2.35Vanadium Pentoxide V2O5 1.52Vermilion HgS 2.8 - 3.14Violet Pigments 1.739 (average)Compound Formula Refractive index Viridian (Chromium oxide,transpar-Cr2O3.2H2O 1.82 - 2.12ent)Volasil 244 1.394Volasil 245 1.394Volasil 344 1.397Volcanic Glass Na,K,Al silicate 1.500Vinyl Chloride Acetate 1.5-1.55Water H2O 1.33Waxes (Average) 1.458Whale Oil 1.460White Lead2PbCO3.Pb(OH)2 1.94 - 2.09White Pigments (Transparent) 1.566 (average) White Pigments (Opaque) 2.132 (average) White Spirit 1.43 - 1.44 Whiting (Chalk)CaCO3 1.510 - 1.645 Witherite (Barium Carbonate)BaCO3 1.529 - 1.677 Wood Flour 1.53Wool, Human Hair 1.54 - 1.56 Wurtzite (Zinc Sulphide a)ZnS 2.356 - 2.378 Xylene (1,2 - Dimethyl benzene)C6H4(CH3)2 1.496Yellow Pigments 2.187 (average) Yttrium Molybdate Y2(M0O4)3. 4H2O 2.03Yttrium Sulphate Y2(SO4)3 1.55Yttrium Sulphate (Octahydrate)Y2(SO4)38H2O 1.543-1.576Zea Mays (Corn Oil) 1.4734Zeolite 1.5026 (average) Zinc Ammonium Solenate Sn(Se04)(NH4)2.Se42 6H2O 1.52 - 1.53Zinc Bromate Zn(BrO3)2.6H2O 1.5452Zinc Carbonate (Smithsonite)ZnCO3 1.618 - 1.818Zinc Carbonate (White, IIIa)ZnCO3 1.818Zinc Cesium Sulfate 6H2O ZnCe3(SO4)3 1.50 - 1.50Zinc Chloride ZnCl2 1.68 - 1.71Zincite (Zinc Oxide)ZnO 2.01 - 2.02 Zinc (ortho) Phosphate Zn3(PO4)2.4H2O 1.572-1.665 Zinc Oxide (Nat. Zincite)ZnO 2.008Zinc Oxide White, AM, III ZnO 2.008Zinc Selenide ZnSe 2.631Zinc Silicate (Hemimorphite)2ZnO.SiO2.H2O 1.64 - 1.636Zinc Sulfide (Wurzite) (Sphalerite) (Cleartran™)ZnS2.356 - 2.3782.3682.368Zinc White ZnO 2.00, 2.02Zinc Yellow4ZnO.4CrO3.K2O.3H2O 1.84 - 1.9Zircon (Zirconium Orthosilicate)ZrSiO4 1.92 - 2.02 Zirconium 2.32Zirconium Oxide (Nat. Baddeyelite)ZrO2 2.13 - 2.2 Zirconium OxideWhite (pure), yellow-brown, V, H7.5ZrO2 2.19Zirconium (ortho) Silicate ZrSiO4 1.92-2.02 Zirconium Silicate (Zircon)ZrSiO2 1.92 - 1.96 Zirconium Sulfide ZrS2 1.923 - 2.015 Zircosil 1.9700 Compound Formula Refractive index2 Sampledispersion guideMaterial Dispersant Additives UltrasonicsAlbumen Methanol 1 minute in ultrasonic bath Albuterol Iso-octane 1 minute in ultrasonic bath Alkali Salts cyclohexanoln-butanal,n-butylamine,linseed oilxyleneAlumina (Al2O3)Water (de-ion-ised optional)None NoneWater Sodium Hexametaphos-phate5 mins. in ultrasonic bathWater Igepal CA-630Water Tetra-SodiumPyrophosphate15 mins. in ultrasonic bathWater Daxad 11 2 mins. via probe plus40% in ultrasonic bathcontinuously to tank.Aluminium Water Igepal CA-630Sodium Hexametaphosphate 5-10 mins. in ultrasonic bathAluminium Trihydrate Water Igepal CA-630 5 mins. in ultrasonic bath Amylodipin Berylate Sunflower oil12 mins. in ultrasonic bath Ammonium Perchlorate Butyl Acetate10 mins. in ultrasonic bath Ammonium Phosphate AcetoneAmoxycillin DimethyldigolChapter 2Sample dispersion guide 2Anthracite Water Trinatrium Phosphate orPerminal BXAntimony Oxide(Sb2O3)Water Igepal CA-630 3 mins. in ultrasonic bathAntimony Trioxide Water Mix powder in neatIgepal CA-630 beforediluting 30 secs - 2 mins. in ultra-sonic bathArsenates Water Sodium PyrophosphateArsenious Oxide Octyl AlcoholCyclohexanolLiquid Paraffin2% Fatty AcidAsh Water Sodium PyrophosphateAtecortin Liquid Paraffin 5 mins. in ultrasonic bath Azodicarbonanide IPA 5 mins. in ultrsonic bath Barium Carbonate Water SodiumHexametaphosphate3 mins. in ultrasonic bathBarium Hexaferrite(BaFe12O19)WaterBarium Strontium Carbonate Water-Ethanol mixtureBarium Sulphate WaterWater-Metha-nol mixture Sodium Hexametaphosphate or Lissapol NX (Alkylphe-nol/ Ethylene Oxide condensate) non ionic.Barium Titanate Water Igepal CA-630 5 mins. ultrasound byprobe.Barytes Water SodiumHexametaphosphate orSodium PyrophosphateBentonite Propan-2-olWater Make slurry in SodiumHexametaphosphatesolutionBeryl Water Sodium Silicate orSodiumHexametaphosphateMaterial Dispersant Additives Ultrasonics。
浅谈检验检测机构检毕样品处置

浅谈检验检测机构检毕样品处置■ 何婧芳〔山西省检验检测中心(山西省标准计量技术研究院)〕摘 要:随着检验检测实验室的现代化和精细化,检测机构面临着日益复杂的检测需求以及检测目的的变化,样品形态多样,检测需求变化多端,检毕样品处置要求也各不相同。
本文旨在通过探讨理化实验室检毕样品处置的原则、分类、要求等,对实验室的检毕样品,尤其是有害物质进行规范化处理,加强实验室安全检查与安全隐患的督促整改,提升安全意识,从源头上降低安全事故发生概率,并减轻环保压力,降低经济成本,推进检验检测实验室标准化建设进程。
关键词:检毕样品,处置要求,处置原则DOI编码:10.3969/j.issn.1002-5944.2024.01.032Discussion on the Disposal of Samples after Inspection by Inspection andTesting InstitutionsHE Jing-fang(Shanxi Inspection and Testing Center / Technology Institute of Standard and Metrology of Shanxi Province)Abstract:With the modernization and refinement of inspection and testing laboratories, testing institutions are facing increasingly complex testing needs, changes of testing objectives, diversity of samples, variable testing requirements, different requirements of disposal of samples after inspection. The purpose of this paper is to explore the principles, classifi cations, and requirements for the disposal of samples after tested by physics and chemistry laboratories. The paper requires conducting standardized operations to deal with samples after inspection, especially harmful substances. Also, the supervision of safety inspections and the rectifi cation of safety hazards in laboratory should be enhanced, safety awareness should be promoted, probability of safety accidents should be reduced from the source, the environmental pressure and economic costs should be reduced, and the standardization construction process of inspection and testing laboratories should be promoted.Keywords: sample after inspection, disposal requirement, disposal principle0 引 言检测样品对检验检测机构的重要性不言而喻,是检验检测机构赖以生存的重要基础,是一切检验工作的前提和必要条件。
SAES-A-206 Positive Material Identification

Engineering Standard SAES-A-206 31 May, 1998Positive Material IdentificationMaterials and Corrosion Control Standards CommitteeSaudi Aramco DeskTop Standards Table of Contents1 Scope2 Conflicts And Deviations3 References4 Definitions5 Responsibilities6 Extent Of Verification7 Procedures8 Methods9 Acceptance Criteria10 Rejection Procedures11 Records And Reports12 Inspection13 Marking And Color Coding1 Scope1.1This standard covers the minimum mandatory requirements for positive material identification (PMI) of ASME 831.3,831.4, and 831.8 piping components, including welds, and other piping or equipment where specified in the SAMS catalog description or purchase order. This standard is applicable if these components or weldments .are manufac.tured from.alloy ~teels, stainles~ ste~ls, or nonferrous alloys, and are In contact wIth the servIce fluIds, or as specIfied In the purchase order 1.2 The requirements in this standard shall apply to PMI of both new components and repair or replacement components. The requirements apply to plant, shop, and field fabrication.Commentary Note:Testing similar to that described in this standard should also be employed whenever it is suspected that anexisting system contains the wrong material.1.3 Unless specifically required in the purchase order or subcontractor requisition, the following components and materials are exempt from PMI:(1) Nonpressure components that are not welded to alloy pressure components.(2) Pressure and nonpressure components from carbon steel or cast irons.(3) Rotating equipment internals, and associated seal, lube oil, cooling water and steam equipment and piping.( 4) Valve internals, with the exceptions of critical service isolation valve, safety valve, and relief valve internals.(5) Piping components in ASME 831.3 Category D Service or equivalent.1.4 If specified in a purchase order or SAMS catalog description, PMI is required for operationally important nonpressure components. Also, PMI of replacement components shall be required.Commentary Note:Examples of important nonpressure components would include, but not be limited to, trays for distillationcolumns and certain load bearing supports.1.5 This standard is intended to ensure that the nominal composition of the base materials and associated welds have been correctly supplied and installed as specified. The testing methods outlined in this standard are not intended to establish the complete conformance of a material to the material specifications.1.6 Where applicable, this entire standard shall be attached to and made a part of purchase orders.2 Conflicts And Deviations2.1 Any conflicts between this standard and other applicable Saudi Aramco Engineering Standards (SAESs), Materials System Specifications (SAMSSs), Standard Drawings (SASDs), or industry standards, codes, and forms shall be resolved in writing by the Company or Buyer Representative through the Manager, Consulting Services Department of Saudi Aramco, Dhahran.2.2 Direct all requests to deviate from this standard in writing to the Company or Buyer Representative, who shall follow internal company procedure SAEP-302 a1!,.d forward such requests to the Manager, Consulting Services Department of Saudi Aramco, Dhahran. .3 ReferencesThe selection of material and equipment, and the design, construction, maintenance, and repair of equipment and facilities covered by this standard shall comply with the latest edition of the references listed below, unless otherwise noted.3.1 Saudi Aramco DocumentsSaudi Aramco Engineering ProcedureSAEP-302 Inst1'llctionsfor Obtahlhlga Waiver of a Mandatoly Saudi Aramco EnghleerhlgRequirementSaudi Aramco Inspection Requirements175-320300 Inspection Requirements: Positive Material Identification (PMI)3.2 Industry Codes and StandardsAmerican Society ofMechanical EngineersASMEBoiler and Pressure Vessel Code Section II: Parts A, B andC.ASMEB16.20 Spiral-WoundGasketsASMEB31.3 Chemical Plant and Petroleum Refinely PipingASME B31, 4 Pipelille Transportation Systems for Liqlfid Hydrocarbons and Other Liqlfids ASMEB31,8 Gas Transmission and Di.'itriblftion Piping SystemsAmerican Society for Testing and MaterialsASTM A 193 Standard Specification,for Alloy-Steel and Stainless Steel Bolting Material.'i for High- Temperaflfre ServiceASTM A 262 Detecting Susceptibility to Intergranular Attack in Austenitic Stainless Steels ASlM A 751 Standard Methods Practices and Tenninology.for Chemical Analysis of SteelProdlfctsPipe Fabrication Institute ...PFI ES-22 Recommended Practice for Color Coding of Piping Materials4 DefinitionsAlloy: A nonferrous alloy, alloy steel, or stainless steel. Also, an adjective referring to these materials.Alloy Steel: Any steel that contains specified quantities of elements, such as chromium, nickel or molybdenum, that are added to enhance mechanical or physical properties, and/or corrosion resistance. Alloy steels and stainless steels comprise ASME P-Nos. 3 through 11, or equivalent.PMI: Positive Material Identification --determination that the nominal chemical composition of a mechanical component is as specified and ordered.Equipment Manufacturer: The company responsible for the plant or shop fabrication of pressured equipment that is within the scope of this standard.Piping Fabricator: The company or agency responsible for the shop fabrication of piping that is within the scope of this standard.Field Fabricator: The company or agency responsible for the field fabrication of piping and pressured equipment within the scope of this standard.Material Specifications: ASME Section II, Parts A, Band C, or the relevant ASTM, or any other material specification required.Material Supplier: An organization that supplies pressure components and parts material to the Piping or Field Fabricator.Nonferrous Alloys: Metals that are not iron-based, including nickel alloys and other corrosion-resistant alloys. ASME P-No. 21 and higher, or equivalent.Nonpressure Components: Items that are not part of the pressure containing envelope, and, therefore, do not affect the pressure retaining capacity of pressured components.Pressure Product Components and Parts: Product forms used for the fabrication of pressured piping and equipment, including but not limited to: shells, heads, tubesheets, nozzles, tubes, stud bolts/nuts, gaskets, forging, flanges, pipe and fittings such as tees, elbows, reducers, and special pipe compoRents, valves (body and bonnets), and alloy "- welds joining pressure parts to nonpressure parts.Saudi Aramco Inspector: The person or company authorized by the Saudi Aramco Inspection Department to verify implementation of the requirements of this standard.SAMS: Saudi Aramco Material System. .,5 ResponsibilitiesThe Equipment Manufacturer, Piping Fabricator or Field Fabricator, as applicable, is responsiblefor ensuring that procedures are implemented in order to verify the nominal , chemical compositions of the alloy pressure containing components. The Saudi Aramco Inspector is responsible for verifying that the requirements of this SAES have been satisfied.6 Extent Of Verification6.1 The PMI program covers alloy pressure-containing components in shop and field fabricated equipment and piping (both base metal and welds) and materials used for repair or replacement of pressure containing components.6.2 One hundred percent PMI shall be performed on all pressure components and welds of alloy materials, within the scope of this standard, with the following exceptions:(1) Tubes for shell and tube and air-cooled heat exchangers and for fired process heaters and boilers: 10 tubes or 10%, whichever is greater, from .every heat number shall be chosen at random and tested prior to the installation of tubes into tubesheets.(2) This testing frequency shall also apply to any replacement tubes for equipment listed in 6.2 (1).6.3 PMI of weld material shall be performed in the same manner as for the adjacent base metal.6.4 The required number of PMI tests shall be as follows:(1) One test for each pipe spool component.(2) One test for any component that makes up part of the pressure boundary.(3) For nonpressure components, 10 pieces or 10%, whichever is greater, from each heat or lot.(4) One test for each pressure boundary weld and for all welds between nonpressure parts and pressure parts.6.5 The elements of the basic alloy materials to be verified shall be in accordance with Table 1. Table 1Basic Alloy Elements to be VerifiedCarbon-Molybdenum, Manganese-Molybdenum, Chromium and Molybdenumand Chromium-Molybdenum steelsNickel steels NickelRegular carbon grade stainless steels Chromium, Nickel, and MolybdenumLow-carbon stainless steels Chromium, Nickel, Molybdenum, and Carbon (or ASTM A 262-A) Stabilized stainless steels Chromium, Nickel, Molybdenum, Titanium and NiobiumNickel-based alloys Nickel, Iron, Copper, Chromium, and Molybdenum Copper-based alloys Copper, Zinc, and other elements specified in purchase order or SAMS catalog description 6.6 For alloys not covered in Paragraph 6.5, the Supervisor of the Materials Engineering Unit ofME&CCD/CSD shall be consulted.6.7 All field welds and any additional materials and welds made to modify prefabricated assemblies shall be PMI tested.7 Procedures7.1 The Equipment Manufacturer, Piping Fabricator or Field Fabricator, as applicable, shall implement a written PMI Procedure, covering testing and reporting, which shall be made available to the Saudi Aramco Inspector for review, acceptance, and verification of implementation.7.2 The Equipment Fabricator, Piping Fabricator, or Field Fabricator shall ensure that PMI is performed prior to completion of fabrication in the shop or at the site, for welds and for field-assembled items not previously positively identified.7.3 The Saudi Aramco Inspector shall have the option to witness any or all of the "' PMI testing. 7.4 PMI shall not be considered as a substitute for the required materials test reports.7.5 Material test reports shall not be considered as an alternative to PMI and the requirements of this standard.7.6 Each Equipment Fabricator, Piping Fabricator, and Field Fabricator shall use only trained, qualified, and experienced operators to perform PMI activities. Operator records attesting to such training, qualification and experience shall be available for Saudi Aramco review and approval. 7.7 For repair and maintenance work performed by Company personnel, alloy materials from the SAMS do not have to be retested if they are properly marked and color coded as indicated in Paragraph 13. Unidentified materials, for applications within the scope of this standard, are subject to PMI by the Inspection Department.8 Methods8.1 The instruments and methods used shall be suitable for identifying the material by quantitative measurement of the major alloying elements required in the ~ applicable material specification or welding procedure specification.8.2 The acceptable method is X-ray emission analysis, also known as X-ray fluorescence (XRF) analysis with a calibrated portable instrument such as the TN Technologies A11oy-Analyzer 9266, TN Technologies Metallurgist XR 9277, Cianflone Scientific Portaspec 2501, or Outokumpu Electronics X-MET 880 analyzer. Other instruments using the same analytical method may be used provided they are calibrated and they demonstrate equivalent performance.8.3 As an alternative, a chemical analysis of samples cut out from the pieces requiring PMI, in accordance with one of the methods in ASTM A 751, may be used to check for the alloying elements required by this standard.8.4 Low carbon stainless steels shall be alloy verified by both an ASTM A 262 (Practice A) test and X-ray emission analysis or chemical analysis of the major alloying elements. Alternatively, an optical emission spectrograph similar to an Arc-Met 930 SP, or similar equipment with proven capability, may be used to check for all the required elements, including carbon. All burn damage shall be removed by grinding.8.5 Prior to commencing PMI, instrument operators shall be qualified to operate approved equipment on a representative sample of the alloy materials with 100% correct assessment as the performance criteria. The instrument operator " shall work to a written procedure and shall have been trained to use the instrument in accordance with that procedure. Training shall be documented.8.6 If sample removal is used, a written procedure for identification and traceability to original material is required.8.7 PMI of welds shall be done after removal of slag and/or oxide from the weld surface. Where accessible, both inside and outside weld surfaces shall be alloy verified.8.8 The surface to be analyzed shall be clean.-bare metal, free of grease or oil, with a surface finish as specified by the instrument manufacturer.Commentary Note:Generally a fresh 60 grit finish is required for the Arc-Met, while no minimum surface finish is required for the Texas Nuclear, only that the surface be clean bare metal.9 Acceptance Criteria9.1 For acceptance, it must be demonstrated that materials contain the amounts of alloying elements shown in the material specification. Alloys shall be acceptable if the alloying elements are each within 10 percent of the specified range of values.9.2 Welds with consumables that match, or nearly match, the base metal composition shall be within +/-12.5 percent of the ranges allowed in ASME Section IIC for each element.9.3 Acceptance criteria for dissimilar metal alloy welds shall be in accordance with the welding consumable specified in the approved welding procedure. The effects of dilution between the different base metals and the filler metal shall be taken into account for determining the nominal as-deposited weld metal composition.10 Rejection Procedures10.1 If the PMI results fall outside the acceptable range using the methods described in Section 8, the Equipment Manufacturer, Piping Fabricator, or Field Fabricator, has the option to obtain a chemical analysis performed by an independent testing laboratory. The independent laboratory must be acceptable to the Saudi Aramco Inspector. The results of this independent chemical analysis shall govern.10.2 If any component or weld is found unacceptable, it shall be replaced and the replacement shall be alloy verified in accordance with this standard.10.3 Procedures shall be in place to ensure that rejected components are segregated and properly identified to prevent reuse.10.4 Where tubes for heat exchangers, fired process heaters, and boilers are found unacceptable, all tubes required of the particular alloy shall be tested for the individual equipment.10.5 All rejected tubes shall be replaced and the replacement tubes shall be subjected to PMI in accordance with this standard.10.6 If any of the samples of nonpressure components fail to meet the acceptance criteria, the full order shall be tested.11 Records And Reports11.1 Records11.1.1 Shop Fabrication11.1.1.1 A detailed recording/logging procedure shall be prepared by the Equipment Manufacturer or Shop Fabricator.11.1.1.2 The log shall identify each component and weld corresponding to an individual equipment item or piping spool and shall include the equipment or spool number and purchase order number.11.1.1.3 The log shall identify all components and welds that have been alloy verified and the results of testing.11.1.1.4 Test results shall include measured percentages of alloying elements for components that were accepted or rejected and for those components that were rejected but accepted based on independent chemical analysis.11.1.1.5 The Equipment Manufacturer shall prepare a detailed PMI map of the pressured equipment being fabricated. The map shall show the alloy material specification of each alloy component and the extent of PMI required in accordance with this standard.11.1.2 Field Fabrication11.1.2.1 At least two weeks prior to the commencement of fabrication, the Field Fabricator shall establish and present to the Saudi Aramco Inspector for review the proposed testing, logging, identification, and final installation procedures for all components requiring PMI testing onsite ( such as fabricated pressured equipment, piping, valves, and welds).11.1.2.2 Shop-fabricated alloy pressure equipment, assemblies, or piping that have been alloy verified by the Piping Fabricator need not be re-verified in the field. However, the Field Fabricator shall have available, for review, the Piping Fabricator's report of PMI. Material certificates are not allowable substitutes.11.2 Final Report11.2.1 Prior to final acceptance of alloy pressured equipment or piping, the Equipment Fabricator or Field Fabricator shall prepare a complete PMI Report containing all relevant data. For pressured equipment, the PMI , Report shall be included as part of the Equipment Data Book.11.2.2 The PMI Report shall be reviewed by the Saudi Aramco Inspector prior to final acceptance.12 InspectionMaterials shall be subject to inspection by the Saudi Aramco Inspector in accordance with Saudi Aramco Inspection Requirement 175-320300.12.1 The responsible Inspection Organization shall ensure and verify that the correct new materials ordered by local area Maintenance organizations have been verified by PMI as required. If the materials are not properly marked and color coded, they shall be verified by one of the methods in Paragraph 8.12.2 During repairs or alterations of materials required to be PMI tested, the responsible Inspection Organization shall verify the correct compositions of the shop and field welds made by local welding agencies by one of the methods in Paragraph 8.13 Marking And Color Coding13.1 Verification Marking13.1.1 Marking shall be done with water-insoluble material that contains no substances that harmfully affect the metal at ambient or elevated temperatures. In particular, the marking material shall be free of lead, sulfur, zinc, cadmium, mercury, chlorine, or other halogens.13.1.2 All components, and welds that are found unacceptable shall be marked immediately with a circled red "X" pending resolution in accordance with Section 10.13.1.3 All verified materials with an acceptable analysis shall be marked with the letter ‘PMI’ usinga certified low-stress stamp. The marking shall be placed as follows:Pipe: One mark, 75 mm from one end on the outer surface of the pipe. This marking shall be in addition to the requirements of PFI ES-22.Welds: Adjacent to the welder's mark on the weld. (Welds on tubes for heat transferequipment shall be marked by either stenciling or vibro-etching on the tubesheet).Fittings and Forgings: Adjacent to the manufacturer's markings.Valves: Adjacent to the valve manufacturer's markings on bodies and other pressure parts.Castings: Adjacent to the casting manufacturer's markings and heat numbers.Plates: 75 mm from one edge, adjacent to manufacturer's markings.Tubes: Stenciled, 300 mm from each end.13.1.4 When heat treating is performed after PMI, the identification marking must be recognizable after heat treatment. PMI markings shall be transferred when a plate or pipe is cut.13.2 Color Coding13.2.1 The color coding system for material identification described herein is intended to help prevent fabricators from using incorrect alloy material. The principal purpose of color coding is visual identification during storage and after the components have been cut for fabrication.13.2.2 Color coding is not a substitute for other, permanent manufacturers' markings required by ASTM or other specifications. Permanent manufacturers' markings shall not be obscured by color coding.13.2.3 A procedure shall be established in accordance with Section II to ensure that all alloys are verified before the color coding. Color coding need not be retained after painting.13.2.4 Prior to coding, surfaces shall be clean and free of dirt, loose scale, and oil. Paints used for coding shall be durable, bright, and distinctive and shall not contain substances that would harmfully affect the material at ambient or elevated temperatures. In particular, paints shall be free of lead, sulfur, zinc, cadmium, mercury, chlorine, and other halogens.13.2.5 Each component shall be coded in accordance PFI ES-22, and shall have painted characters indicating the specification number of the material if it is not permanently marked or tagged according to the applicable material specification.13.2.6 Valves, flanges, and fittings do not require color coding if these components are permanently stamped or tagged by the manufacturer. If the materials are not easily legible, valves, flanges, and fittings shall be coded with a stripe of 5 mm minimum width. The color coding on valves should indicate the valve body material.13.2.7 ASTM A 193, Grade 87 stud bolts do not require color coding if the grade of the material is stamped on one end of each bolt.13.2.8 Spiral-wound gaskets shall be color coded in accordance with ASME 816.20. Sheet type gaskets do not require color coding.13.2.9 Pipe and Fittings: Each length ofpipe and fitting shall have a 5 mm or larger stripe running full length. One inch NPS and smaller may have a 3 mm stripe running full length.13.2.10 Valves: When required, stripe across the body from flange to flange or end to end.13.2.11 Flanges: When required, stripe across edge up to hub.13.2.12 Bolting: When required, stripe around the midpoint of each bolt or stud.13.2.13 Plate, sheet, and strip: Stripe on surface near two perpendicular edges for entire length. 13.2.14 Tubes and Bars: Stripe entire length. ,Revision Summary31 May, 1998 Standard renumbered from SAES-L-O71 to SAES-A-206 "Positive Material Identification" and revised to apply to all components of pressured piping and equipment manufactured from alloy steels, stainless steels, or nonferrous alloys. Document responsibility transferred to Materials and Corrosion Control Standards Committee.。
LookOut Mycoplasma PCR Detection Kit 产品说明书

User GuideLookOut®One-Step Mycoplasma PCR Detection Kit MP0050-25TST (25 reactions)MP0050-100TST (100 reactions)Storage Temperature 2–8 °CProduct DescriptionThe LookOut® Mycoplasma PCR Detection Kit utilizes the polymerase chain reaction (PCR), which was established as the method of choice for highest sensitivity in the detection of Mycoplasma and Acholeplasma contamination in cell cultures and other culture-derived biologicals. Detection requires as little as 10-20 fg of mycoplasma DNA corresponding to10-20 mycoplasma per sample volume.The primer set is specific to the highly conserved rRNA operon, or the 16S rRNA coding region in the mycoplasma genome. This allows for detection of all Mycoplasma, Acholeplasma, and Ureaplasma species tested so far, which are typically encountered as contaminants in cell cultures.Eukaryotic and bacterial DNA are not amplifiedby this kit.Just one protocol is needed for the detection of all mycoplasma species. The detection procedure can be performed within 3 hours. The PCR mix also provides internal control DNA, which results in a 190 bp band on the agarose gel to indicate a successfully performed reaction.Precautions and DisclaimerThis product is for R&D use only, not for drug, household, or other uses. It is not for clinical diagnostics or testing of human samples. Please consult the Material Safety Data Sheet for information regarding hazards and safe handling practices. ComponentsDescription QuantityCatalogueNumberPCR Mix, aliquotedfor 25 reactions:1 vial MP0050-25TST4 vials MP0050-100TST Lyophilized Taq polymerase, primers and deoxynucleotide triphosphates dATP,dCTP, dGTP and dUTPReaction Buffer,1.3 mL1 vial MP0050-25TST2 vials MP0050-100TST Positive Control DNA 1 vialLyophilized syntheticDNA, non-infectiousWater, 2 mL 1 vialStorage/StabilityKit components are stable during shipping at ambient temperature. Upon receipt, store at 2-8 °C. After rehydration of the PCR mix, the positive control, and the internal control, store below –18 °C and avoid repeated freezing and thawing. For repeated testing of a few samples at a time, PCR mix and controls should be aliquoted after rehydration. By following these recommendations, the kit is stable until the expiration date stated on the label.Rehydration Buffer PCRMixWater PositiveControl DNAQuick Start GuideThis procedure overview is not a substitute for the detailed instructions.Reagent PreparationCentrifuge PCR Mix and Positive Control DNAPreparationof PCR ReactionsLoad the test tubes Aliquot 23 µL PCR MixCentrifuge brieflyStart PCR Reaction1 cycle 94 °C for2 min 39 cycles 94 °C for 30 sec 55 °C for 30 sec 72 °C for 30 sec Hold at 4-8 °CIncubate for 5 min at room temperatureVortex brieflyCentrifuge for 5 seconds600 µL300 µLAdd 2 µL Sample Add 2 µL Sample Add 2 µL Positive Control DNA Add 2 µL Fresh CellCultureMediumProcedurePreparation of Sample MaterialCell lines should be pre-cultured in the absence of antibiotics for several days to maximize test sensitivity. Samples should be derived from cultures that are at 90–100% confluence. PCR-inhibiting substances may accumulate in the medium of older cultures. For these sample materials a DNA extraction is strictly recommended prior to testing.To avoid false positive results, it is recommended to use deionized, DNA-free water, aerosol-preventive filter pipette tips, and gloves.Templates for PCR analysis are prepared by boiling the supernatant of cell cultures or other biologicals for 10 minutes as follows:1.Transfer 100 µL of supernatant from the test culture to asterile microcentrifuge tube (T0447). The lid should be tightly sealed to prevent opening during heating.2.Heat the sample supernatant at 95 °C for10 minutes.3.Briefly centrifuge (5 seconds) the sample supernatant to pelletcellular debris before adding to the PCR mixture. Rehydration of the Reagents1.Before rehydrating the tubes, centrifuge the tubes to ensurethat the lyophilized components are spun down (5 seconds at maximum speed).2.Add the appropriate amount of Rehydration/Reaction Buffer(blue cap)PCR Mix, 300 µL per portion of 25 reactions 3.Add the appropriate amount of Water (white cap) to PositiveControl DNA, 600 µL4.Incubate for 5 minutes at room temperature.5.Vortex and centrifuge again.6.Keep reagents on ice and store below -18 °Cafter rehydration. Thermal ProfileThe programming process of your cycler is explained in the instrument’s manual.Thermal Cycle Program1 cycle 94 °C for2 minutes39 cycles 94 °C for 30 seconds55 °C for 30 seconds72 °C for 30 secondscool down to 4–8 °CThe PCR MastermixTotal volume per reaction is 25 µL. When setting up reactions, calculations should also include positive and negative controls.1.The rehydrated PCR Mix can be prepared for25 reactions, aliquoted as needed, and stored b elow –18 °C forup to 3 months. Aliquot 23 µLof the rehydrated PCR Mix into each PCRreaction tube.2.Add 2 µL of deionized, DNA-free water as a negative controlinto negative control reaction tubes and seal t o avoidcontamination.3.Add 2 µL of sample (as previously described)to PCR reaction tube per sample being testedand seal.4.Pipette 2 µL of positive control DNA into positive controlreaction tube.5.Proceed to thermal cyclingAgarose Gel Rune 1.5% standard agarose gel (A9539)with 5 mm comb.2.Load 5 µL of each PCR reaction, mixed with gel trackingloading solution (G7654) per lane.3.Stop electrophoresis after 2 cm run distance (depending onthe electrophoresis chamber used e.g., run for 25 minutes at100 V).ResultsGel Evaluation1. A distinct 190 bp band should appear in every lane indicating asuccessfully performed PCR. This band may fade out with increased amounts of amplicons formed, caused by mycoplasma DNA loads of 5 × 106 copies/ml. 2. No amplification of positive control DNA maybe due to the following reasons:• positive control DNA tube has not been spun down before rehydration • programming mistake •pipetting mistake.3. Before rerun of a negative and a positivecontrol, please check thermocycler protocol and pipetting scheme.4. Nonspecific bands on the gel are extremely rare. Possibleprimer self-annealing produces another (primer dimer) band of 80-90 bp but does not affect the precision or results of the test. 5. If the PCR of a sample is inhibited, PCR inhibitors can easily beremoved from the sample by performing a DNA extraction with a commercially available kit (G1N10, G1N70, or NA2000).Sample Data← 270 bp positive control ← 190 bp internal controlR a i n b o w l a d d e rN e g a t i v e c o n t r o lP o s i t i v e c o n t r o lC o m p l e t e l y i n h i b i t e dI n h i b i t e dT y p i c a l c o n t a m i n a t i o nS t r o n g c o n t a m i n a t i o nR a i n b o w l a d d e rRelevant amplicon sizesInternal control 190 bpMycoplasma sp.(see Detectable Species)∼270 bpResults of successfully performed PCRPCR sample Band pattern Negative control Band at 190 bpPositive control Band at 267 bp,possibly an additionalband at 190 bp Interpretation of possible band patterns Band pattern InterpretationBand at 190 bp Negative sample Bands at 270 bpand 190 bpMycoplasma-positivesample with weakcontaminationStrong band at 270 bp Mycoplasma-positivesample with strongcontaminationNo band PCR inhibitionDetectable SpeciesA large number of Mollicutes sequences have been published. The primers of the kit were aligned againstthe NCBI data and scrutinized for homologies within the target region of the 16S rRNA. At least 1 Ureaplasma, 7 Acholeplasma and 85 Mycoplasma show highly relevant sequence homologies and are presumably detected as positive.Positive (Mollicutes)NegativeEP 2.6.7 listed bacteria Other microorganisms MammalsAcholeplasma laidlawii Clostridium acetobutylicum Chlamydia trachomatis Vero-B4 Mycoplasma arginini Lactobacillus acidophilus Legionella pneumophila Per.C6 Mycoplasma arthritidis Streptococcus pneumoniae Micrococcus luteus RK13 Mycoplasma fermentans Candida albicans CHO-K1 Mycoplasma gallisepticum Enterococcus faecalis Murine genomic DNA Mycoplasma genitalium Enterobacter aerogenes Calf thymus DNA Mycoplasma hominis Escherichia coli Proteus Fetal bovine serum Mycoplasma hyorhinis Proteus mirabilisMycoplasma orale Bacillus cereusMycoplasma penetransMycoplasma pneumoniaeMycoplasma salivariumMycoplasma synoviaeSpiroplasma citriUreaplasma urealyticumThe life science business of Merck operates as MilliporeSigma in the U.S. and Canada.Merck LookOut and Sigma-Aldrich are trademarks of Merck KGaA, Darmstadt, Germany or its affiliates. All other trademarks are the property of their respective owners. Detailed information on trademarks is available via publicly accessible resources.NoticeWe provide information and advice to our customers on application technologies and regulatory matters to the best of our knowledge and ability, but without obligation or liability. Existing laws and regulations are to be observed in all cases by our customers. This also applies in respect to any rights of third parties. Our information and advice do not relieve our customers of their own responsibility for checking the suitability of our products for the envisaged purpose.The information in this document is subject to change without notice and should not be construed as a commitment by the manufacturing or selling entity, or an affiliate. We assume no responsibility for any errors that may appear in this document.Technical AssistanceVisit the tech service page at /techservice .Terms and Conditions of SaleWarranty, use restrictions, and other conditions of sale may be found at /terms .Contact InformationFor the location of the office nearest you, go to /offices .。
产品中残留溶剂控制申明模板(国外审计)说课讲解

产品中残留溶剂控制申明模板(国外审计)
Statement of Residual solvents for产品名称/简称
For “对方企业名称(英文)”
Name of the material:化学名称
,short name:有产品名简称时适用(与出厂标签上一致)
Following are the solvents used in the manufacturing process of +化学名称/简称
ClassⅠResidual Solvents:
♦一类溶剂的名称/
♦如未用到一类溶剂的填N/A
ClassⅡResidual Solvents:
♦二类溶剂的名称/
♦如未用到二类溶剂的填N/A
Class ⅢResidual Solvents:
♦三类溶剂的名称/
♦如未用到三类溶剂的填N/A
Other Residual Solvents:
♦除了上述三类溶剂之外的溶剂名称
Other than above mentioned none of the residual solvents are used.
We confirm that,if tested the “产品名称/简称” will comply with the standards of current USP and supplements for Residual Solvents<467>.
QA经理或质量负责人签字/日期
Mr./Mrs.xxxx,(上述签字人员名字拼音)
职务,Quality Assurance
“自己企业名称(英文)”。
【行业资料】微生物偏差调查及实例介绍
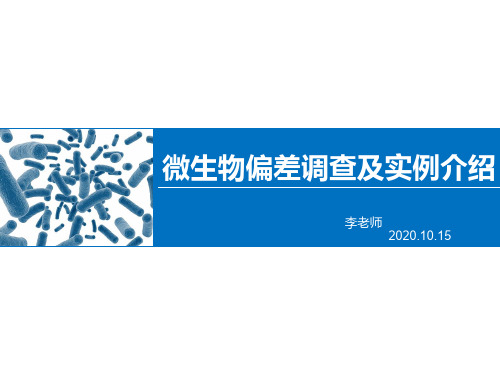
MDD调查组织
组织
QA
参与
其他部门
14
调查
MDD调查过程
15
调查
调查内容
1
2
仪器/设备
环境
3
微生物 种类
4 培养基
• 是否在校验/ 计量有效期
• 是否定期清 洁
• 是否得到正 确使用
• 使用同一仪 器的其他试 验是否出现 问题
• 是否定期进 行环境
• 是否环境监 控趋势异常。
未知微生物进行 鉴别,推断其可 能的出处,辅助 确定MDD原因。
调查
调查关闭过程必须是正式的。 第二阶段调查:
调查关闭
19
实例
简介
调查
实例
注意事项
20
实例
7月份,某中试车间制剂生产区域出现霉菌。
组织MDD
QA 2
1
启动MDD
QC
3
调查MDD
1、QC 2、QA 3、生产部门
霉菌MDD调查
21
实例
霉菌MDD调查第一阶段
人员
是否具备操作资质
培养基
是否在有效期内, 是否完成确效实验, 确效实验是否合格。
述。
温湿度: 清洁人员因无程序指导且经验不足,对特殊表面清
洁可能未进行彻底清洁消毒。
36
实例
霉菌MDD调查第二阶段
结论与CAPA
1、结论
可能原因: 相关清洁消毒人员对此门把手进行清洁消毒时,可能对其未进行彻底消毒清 洁; 清洁消毒SOP描述不全面,未涉及门把手等特殊部位清洁消毒程序。
2、CAPA
1、对清洁消毒SOP进行升级,加入相关部位清洁消毒流程描述 2、对清洁消毒人员依据升级后SOP进行培训。
生物样本分析

•流动相 (样品导入溶液) :100mM 醋酸钠缓冲液 <pH=4.7>
样品导入溶液对回收率的影响 1
•样品导入溶液 pH值变化对回收率的影响
Table. 血浆样品中药物回收率 (spiked 2ug/mL each, 50uLinj.)
样品导入溶液对回收率的影响 2
•样品导入溶液 离子强度变化对回收率的影响
• 使用新型色谱柱的自动浓缩系统实现了高灵敏度 • Co-Sense for BA + LCMS系统的特长
背景
样品前处理是目前分析化学的瓶颈,是分析化学研究的难点和 热点问题之一。由于样品数量极多,且分析物含量越来越低、 基体越来越复杂,迫切要求发展高通量、高选择性、高效率的
在线样品前处理技术。因此,开展这方面的研究具有极为重要
Table 血浆样品中各药物回收率结果 (spiked 0.5ug/mL each (Naproxen:2ug/mL), 50uLinj.)
10mM ammonium acetate 100mM ammonium acetate 200mM ammonium acetate Naproxen Lidocaine Noscapine Chlorpheniramine Propranolol Diphenhydramine Verapamil Acetohexamide Imipramine 100%< 96% 80% 87% 93% 80% 62% 78% 75% 99% 94% 99% 91% 96% 90% 100%< 80% 85% -
的意义。
HPLC/LC-MS广泛应用于血浆或血清的代谢物分析和原 药分析,一般的血浆和血清分析,需要对样本进行预 处理,以除去蛋白质,这样会降低精确度和工作效率。 引入了具有限制性通路媒介(restricted access media -RAM)的预柱,可对血浆样本进行直接分析, 而不必进行预处理。这样,可提高精确度、简化操作 和提高工作效率 。但是,使用限制性通路媒介柱, 也存在一些问题,需解决的问题:回收率、灵敏度、 耐用性。
- 1、下载文档前请自行甄别文档内容的完整性,平台不提供额外的编辑、内容补充、找答案等附加服务。
- 2、"仅部分预览"的文档,不可在线预览部分如存在完整性等问题,可反馈申请退款(可完整预览的文档不适用该条件!)。
- 3、如文档侵犯您的权益,请联系客服反馈,我们会尽快为您处理(人工客服工作时间:9:00-18:30)。
BY: WONDER WONG APPROVED: KEVIN WOO
DATE: DEC 4, 1996
PAGE 1 OF 2 ASSURANCE
PROCEDURE
1.0 PURPOSE
To provide a guideline how to dispose samples.
2.0 SCOPE
This procedure is applicable to all HFE QA locations. All samples shall be treated in a way described in this procedure.
3.0 PROCEDURES
3.1 Sample can only be discarded or processed for recycle if they have been severely destroyed
during tests such as flame or other abuse. Sample shall be either or both of lost of play value, serious damage in aesthetic / cosmetic, or parts / appendages broken apart as non-repairable condition. Sample shall then be locked up in a quarantine area where no unauthorized personnel can enter.
3.2 All tested samples, however, are best destroyed by grinder after test. Samples tested will be
grinded after three working days upon test job completed. The grinding machine must be operated by the two trained person at all time of operation. Scarps shall be collected by the recycle sub-contractor.
CAUTION: Samples contain liquid chemicals or chemical compounds in powder / liquid state, flammable and/or explosive substance, batteries or other dangerous
materials are prohibited to be scrapped in-house. Products or materials shall either be returned to manufacturing vendors or process through external certified contractor for disposal.
3.3 If grinding process is not possible or under requirement of the test requestor, it shall be
returned to corresponding vendor. Lab technician shall pack all samples properly in master cartons after tests and then seal with pkg. tape. A label having vendor’s name and attention shall be put on carton panel. All these cartons shall be kept in a particular return samples area pending the collection by vendor.
3.4 Supervisor is responsible to inform the vendor to collect those tested samples by e-mail/
phone and follow-up the status. Receipt note shall be prepared for contractor / courier signature upon collection of sample. Record shall be file accordingly.
3.5 In case of agreement reached by Lab Supervisor and the requestor. The tested samples may
be kept in segregated area for further evaluation / analysis.
3.6 Lab supervisor shall maintain record of sample in / out and dispose for record tracking.
BY: WONDER WONG APPROVED: KEVIN WOO
DATE: DEC 4, 1996
PAGE 2 OF 2 ASSURANCE
PROCEDURE
4.0 REVISION HISTORY
4.1 Initial Revision 00: New.
4.2 Revision 01: in 1.0, change “ To provide a guideline for HFE lab Technician & supervisors
how to handle these samples after being tested” as “ to provide a guideline how to dispose samples”. 2.0 , change “ both labs located in Shatin & China” as “all HFE QA locations”.
4.3 Revision 02: 3.3 replace “fax” by “e-mail”, 3.4 change “… an outside subcontractor shall be
involved to help destroy the samples, usually after accumulating to a certain volume, under the supervision of lab supervisor /technicians. This subcontractor may be any possible vendor nearby or local cleaning company.” as “…tested samples will be destroyed (by
grinding machines) after three working days upon test job completed. The grinding machine must be operated by the two trained people at all time of operation. Scarps shall be collected by the recycle sub-contractor”. 3.6 newly added.
4.4 Revision 03:
3.1 rewrite sequence to destroy sample by grinder as preferred progress.
3.2 ~ 3.6 revise section content to reflect event sequence in order.。