供应商产品进料
进料的规章制度怎么写

进料的规章制度怎么写为了有效管理企业的进料流程,保证生产运营顺利进行,制定并执行规章制度是至关重要的。
本文将针对进料环节进行规章制度的详细介绍,以确保企业可以高效、有序地进行进料管理。
**一、进料流程**1. 进料申请:生产部门填写进料申请单,包括进料的品名、规格、数量、供应商等信息。
2. 供应商审核:采购部门审核供应商的合作资质和信誉度,确保选择优质的供应商。
3. 订单下达:采购部门根据进料申请单下达订单,与供应商达成交易协议,明确价格、交货期限等信息。
4. 接货验收:仓库人员根据订单准备接货,对接收到的货物进行验收,确认货物品质和数量是否符合要求。
5. 入库安放:验收合格的货物经过标识和分类后,由仓库管理员负责将货物按照规定的存放位置进行入库安放。
6. 数据录入:仓库管理员将进料信息录入系统,包括品名、数量、供应商、入库时间等,确保信息准确无误。
7. 结算付款:财务部门核对进料信息和货款金额,及时完成结算付款,保证供应商的合理权益。
**二、进料管理规定**1. 进料标准:规定进料的标准和要求,确保进料质量稳定可靠,不影响生产产品的质量。
2. 进料配额:设定进料的配额管理制度,合理控制进料用量,避免库存积压或过度使用。
3. 进料审核:建立进料审核机制,对供应商和货物进行严格审核,确保进料的合法性和安全性。
4. 进料追溯:建立进料追溯制度,记录进料来源、过程和去向,保证食品安全和生产质量。
5. 进料库存:对进料库存进行定期盘点和管理,确保库存数据准确无误,避免资产损失和浪费。
6. 进料保质:制定进料保质措施,保证进料在存储和使用过程中保持品质,避免变质和损坏。
7. 进料退货:设立进料退货制度,对质量不合格或超过保质期的货物进行及时处理和退货。
**三、进料管理优化**1. 自动化管理:引入物联网、大数据等技术,实现进料管理的自动化和信息化,提高管理效率和准确性。
2. 供应链优化:优化供应链协作机制,建立长期稳定的合作关系,确保供应链畅通和高效运作。
进料检验规定
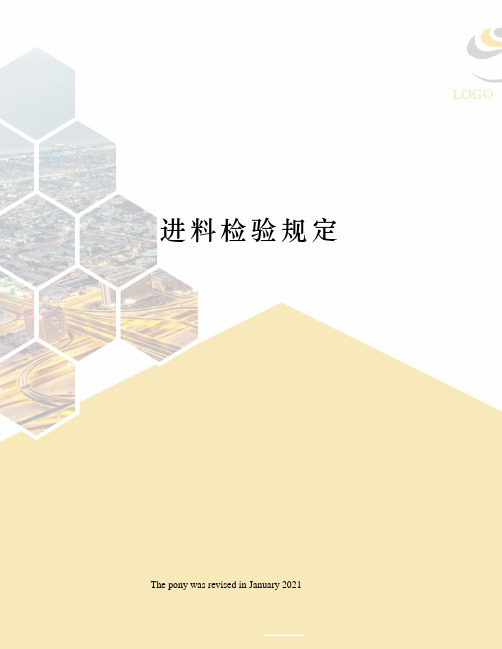
进料检验规定 The pony was revised in January 2021进料检验规定1.总则1.1.制定目的本公司为管制采购物料、委外加工物料品质,使其符合设计规格及允收品质水准,特制定本规定。
1.2.适用范围凡本公司采购物料、委外加工物料或本公司自制之零部件均适用本规定。
1.3.权责单位1)品管部负责本规定制定、修改、废止之起草工作。
2)总经理负责本规定制定、修改、废止之核准。
2.检验规定2.1.抽样计划依据GB2828(等同MIL-STD-105D)单次抽样计划。
2.2.品质特性品质特性分为一般特性与特殊特性。
2.2.1.一般特性符合下列条件之一者,属一般特性:1)检验工作容易者,如外观特性。
2)品质特性对产品品质有直接而重要之影响者,如电气性能。
3)品质特性变异大者。
2.2.2.特殊特性符合下列条件之一者,属特殊特性:1)检验工作复杂、费时,或费用高者。
2)品质特性可由其他特性之检验参考判断者。
3)品质特性变异小者。
4)破坏性之试验。
2.3.检验水准1)一般特性采用GB2828正常单次抽样一般II级水准。
2)特殊特性采用GB2828正常单次抽样特殊S-2水准。
2.4.缺陷等级抽样检验中发现之不符合品质标准之瑕疵,称为缺陷,其等级有下列三种:1)致命缺陷(CR)能或可能危害制品的使用者、携带者的生命或财产安全之缺陷,称为致命缺陷,又称为严重缺陷,用CR表示。
2)主要缺陷(MA)不能达成制品的使用目的之缺陷,称为主要缺陷,或重缺陷,用MA表示。
3)次要缺陷(MI)并不影响制品使用目的之缺陷,称为次要缺陷,或轻微缺陷,用MI表示。
2.5.允收水准(AQL)2.5.1.AQL定义AQL即Acceptable Quality Level,是可以接收的品质不良比率的上限,也称为允许接收品质水准,简称允收水准。
2.5.2.允收水准本公司对进料检验时各缺陷等级之进料允收水准为:1)CR缺陷,AQL=0。
进料检验流程

进料检验流程
1.
进料检验是指在供应商提供原材料和辅助材料进入公司生产车间之前对其进行
检查和测试的活动。
目的是确保供应商提供的材料符合公司的要求和标准,并且能够确保最终产品的质量和安全性。
2.目的
进料检验的主要目的是保证原材料和辅助材料的质量满足公司产品的要求和标准,同时可以预防所检材料的缺陷和问题对公司生产带来的风险和损失。
3.流程
进料检验流程一般由以下环节组成:
3.1 提交样品
供应商将样品交付给公司检测部门,并且提供相关的产地证明和检测报告。
3.2 样品检验
检测部门对样品进行检验和测试,检验内容包括外观、颜色、气味、纯度等多
个方面。
3.3 检验结果处理
检测部门根据检测结果进行处理,判断样品是否符合要求。
检测结果分为合格
和不合格两种情况。
3.4 报告输出
检测部门将测试报告交付质量控制部门,质量控制部门在确认检测结果合格后,才会安排原材料和辅助材料进入车间生产。
4. 风险控制
进料检验的主要风险包括:误检,漏检,错误判定,检测成本高等。
因此,需
要建立完整的质量管理体系,保障检测的准确性和效率,降低风险。
5.
进料检验是生产过程中不可或缺的环节,对原材料和辅助材料进行全面和规范的检验,有利于保证产品的质量和安全性,防止质量问题和风险的发生。
进料检验控制程序

进料检验控制程序1、目的为保证来料的质量、数量、规格等符合本公司的要求,提供良好的物料,满足生产之所需,特制定本程序。
2、范围适用于公司所有原材料、辅助材料,外发加工品的检验管理。
3、术语与定义来料检验:对供应商提供的原材料、辅助材料,或由外协加工商协助加工的产品进行的检验。
4、来料检验控制过程风险乌龟图5、工作流程和内容6、附加说明6.1控制措施:6.1.1供应商来料要附带产品质量检验报告。
6.1.2供应商与组织签订技术协议、质量保障协议等技术要求。
6.1.3出现质量索赔依据《质量索赔流程》进行处理。
6.2进货异常处理:A、来料检验批合格率低于99.73%时,采购工程师和质量工程师联系供应商来厂处理并制定处置方案。
B、来料为同一供应商同一物料检验连续3批拒收;不同物料,同一供应商物料检验连续5批拒收,采购要发《8D报告》给供应商进行改善。
质量检验员要对拒收物料进行加严检查。
C、供应商改善合格后要返回《8D报告》,改善后的物料检验连续五批合格方可恢复正常检验抽样。
D、如果供应商改善后连续五批中有一批不合格,则继续改善;五批次中有两批和两批以上物料拒收则重新考核供应商。
7、参考文件《不合格品管理程序》《库房管理程序》《记录管理程序》《文件管理程序》《产品标识和追溯程序》《检验抽样准则》《检验抽样表》8、使用表单8.1《采购订单》8.2《进货验证记录》8.3《采购入库单》8.4《合格标签》8.5《不合格标签》8.6《供应商物料检验反馈报告》8.7《不合格品处置单》8.8《8D报告》。
进料加工厂的操作方法

进料加工厂的操作方法
进料加工厂的操作方法包括以下几个步骤:
1. 原料采购:选择合适的供应商进行原料采购,确保原料的质量和供应的稳定性。
2. 原料贮存:将采购回来的原料进行分类、编号、验收和储存。
分类可以按照不同的性质和用途进行,比如食品类、化学品类等。
3. 原料预处理:对原料进行必要的预处理,比如清洗、去杂质等,以确保原料符合生产要求。
4. 进料加工:根据产品的不同要求,进行适当的加工处理,如切割、研磨、搅拌等。
5. 控制生产过程:对每个加工步骤进行控制,确保产品质量和加工效率。
可以通过设备设置、操作规程和工艺参数等方式进行控制。
6. 中间产品储存:对加工好的中间产品进行储存,在生产流程中,可能需要暂时储存一些中间产品。
7. 最终产品加工:将中间产品进行最终加工处理,以得到符合要求的最终产品。
8. 产品包装:对最终产品进行包装处理,包括选择合适的包装材料和方式,确保产品外观和质量。
9. 产品质检:对包装好的产品进行质量检验,确保产品符合相关标准和规定。
10. 产品储存和出库:将质检合格的产品进行储存,并根据订单或市场需求进行出库。
以上是进料加工厂的基本操作方法,具体操作还需根据不同的产品和企业的具体情况进行调整和优化。
供应商质量协议书
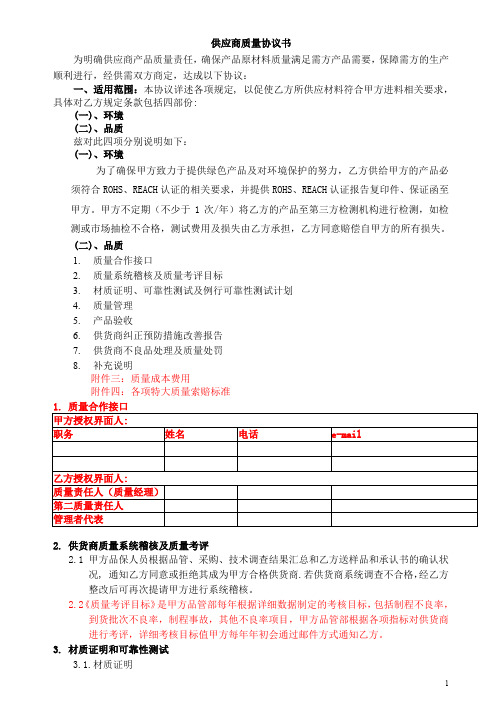
供应商质量协议书为明确供应商产品质量责任,确保产品原材料质量满足需方产品需要,保障需方的生产顺利进行,经供需双方商定,达成以下协议:一、适用范围:本协议详述各项规定, 以促使乙方所供应材料符合甲方进料相关要求,具体对乙方规定条款包括四部份:(一)、环境(二)、品质兹对此四项分别说明如下:(一)、环境为了确保甲方致力于提供绿色产品及对环境保护的努力,乙方供给甲方的产品必须符合ROHS、REACH认证的相关要求,并提供ROHS、REACH认证报告复印件、保证函至甲方。
甲方不定期(不少于1次/年)将乙方的产品至第三方检测机构进行检测,如检测或市场抽检不合格,测试费用及损失由乙方承担,乙方同意赔偿自甲方的所有损失。
(二)、品质1.质量合作接口2.质量系统稽核及质量考评目标3.材质证明、可靠性测试及例行可靠性测试计划4.质量管理5.产品验收6.供货商纠正预防措施改善报告7.供货商不良品处理及质量处罚8.补充说明附件三:质量成本费用附件四:各项特大质量索赔标准1.质量合作接口甲方授权界面人:职务姓名电话e-mail乙方授权界面人:质量责任人(质量经理)第二质量责任人管理者代表2. 供货商质量系统稽核及质量考评2.1 甲方品保人员根据品管、采购、技术调查结果汇总和乙方送样品和承认书的确认状况, 通知乙方同意或拒绝其成为甲方合格供货商.若供货商系统调查不合格,经乙方整改后可再次提请甲方进行系统稽核。
2.2《质量考评目标》是甲方品管部每年根据详细数据制定的考核目标,包括制程不良率,到货批次不良率,制程事故,其他不良率项目,甲方品管部根据各项指标对供货商进行考评,详细考核目标值甲方每年年初会通过邮件方式通知乙方。
3. 材质证明和可靠性测试3.1.材质证明乙方在送样品和承认书的时候必须附有材质证明,乙方必须使用甲方指定原材料,没有甲方的4M变更通知书或乙方提出4M变更通知书并且经过甲方的书面确认乙方不得做任何的更改,若在生产及销售过程中,甲方发现或实验证明乙方所供应产品与承认书标准不符,乙方承担因此引起的一切的损失。
分享 - 食品供应商审核步骤

分享| 食品供应商审核步骤对供应商的先审核应坚持实施,审核供应商的类别和目的:1、对供应商审核的重要程度取决于他所供应的产品的重要程度。
一般状况下:实施进料一级检验的供应商肯定要审核;实施进料二级检验的供应商可以有选择的审核;实施进料三级检验的供应商可以不进行限现场审核。
2、审核是强制性的,但审核方式可以协商。
3、不能由于供货的合格性或顾客的指定等因素而免除审核。
五、初次选择供应商要审核目的:为了证明供应商的生产力量及质量管理体系的有效性,确保准时供应质量稳定,数量牢靠和价格相宜的产品。
供应商审核流程包括:确定审核的日期,发送审核表,成立审核组指定组长,到供方现场审核,包括会议、参观工厂、文件审核、现场审核、结束会议、出具审核报告,向公司汇报审核结果。
审核结果分三种,合格的供应商可直接接受,不合格的供应商应放弃或在别无选择的特别状况下做特殊处理,待定的供应商责令改进,并跟进效果。
六、供应的产品要定期审核供应商的产品初次确认后批量生产时实施首次审核,以后按方案定期审核。
一般是年度方案,每个类别每年一次,详细实施状况取决于该产品的重要程度和品质状态。
审核的目的包括:1、确认新产品是否满意要求;2、定期确认批量供应的产品品质是否由于设备老化、工艺转变和环境变化等缘由发生退化;3、定期确认批量生产的产品是否满意顾客的要求,不要由于市场的进展而被淘汰。
产品审核的时机:按产品类别制定方案,审核因素包括重要原料、品质欠稳定的原料、欠佳的供应商。
首次审核时机为首次批量生产的供货产品,包括新原料和供应中断一年以上的原有原料。
定期审核时机为按年度排方案审核。
建立产品审核小组:小组由组长和组员组成。
组长由品管部主管担当,组员由品管员担当。
必要时可邀请研发部、生产部管理人员或外部专家。
产品审核的流程如下:由审核员随机抽样全包装产品的1-3件,对包装的式样和防护和标签标识进行检查,打开包装箱,检查包装,进行感觉检查。
查验该批次产品检验报告,做产品审核总结,建立评审报告。
公司进料出料管理制度

公司进料出料管理制度一、目的和范围制定本制度的目的在于规范公司的物料进出流程,确保物料的及时供应和有效利用,减少库存积压,降低物流成本,提高整体供应链效率。
本制度适用于所有涉及物料进出的部门和人员,包括但不限于采购部、仓库管理部、生产部等。
二、基本原则1. 准确性原则:所有物料信息必须准确无误,包括物料名称、规格、数量、供应商资料等。
2. 及时性原则:物料的进料和出料需按照生产计划和需求及时进行,避免影响生产进度。
3. 安全性原则:在物料搬运过程中,应采取适当措施保证人员和物料的安全。
4. 经济性原则:在保证物料质量和供应的前提下,尽可能降低物料成本。
三、进料管理(一)进料流程1. 采购申请:根据生产需求提出采购申请,明确物料种类、数量及预期到货时间。
2. 采购审批:相关部门负责审批采购申请,确保采购的必要性和经济合理性。
3. 供应商选择:选择合格的供应商,并签订合同,明确交货期限、质量标准等条款。
4. 收货检验:物料到货后,仓库管理人员需对物料进行检验,确保与订单相符。
5. 入库登记:检验合格后,将物料入库,并在系统中进行登记。
(二)质量控制1. 建立供应商评估体系,定期对供应商进行评审,确保物料来源的质量可靠性。
2. 对于关键物料,应建立更为严格的检验标准和流程。
四、出料管理(一)出料流程1. 出料申请:根据生产计划或销售订单,提出物料领用申请。
2. 审批流程:相关部门对出料申请进行审批,确保物料的合理分配。
3. 出库登记:审批通过后,仓库管理人员准备物料,并办理出库手续。
4. 使用跟踪:对于出库物料的使用情况进行跟踪,以便及时补充和调整。
(二)库存控制1. 定期盘点:定期对库存物料进行盘点,确保库存数据的准确性。
2. 安全库存:设定安全库存水平,防止因物料短缺而影响正常生产。
五、责任与考核1. 明确各岗位职责,确保每个环节都有人负责。
2. 定期对进料出料管理进行考核,以激励员工提高工作效率和质量。
- 1、下载文档前请自行甄别文档内容的完整性,平台不提供额外的编辑、内容补充、找答案等附加服务。
- 2、"仅部分预览"的文档,不可在线预览部分如存在完整性等问题,可反馈申请退款(可完整预览的文档不适用该条件!)。
- 3、如文档侵犯您的权益,请联系客服反馈,我们会尽快为您处理(人工客服工作时间:9:00-18:30)。
供应商产品进料规程
1、目的:本文件规定了供应商产品交货要求,以方便IQC检验及产品追溯
2、适用范围:本文件适用于提供新的样件的所有供应商.
3、提出时间:产品送样、正式量产.
4、送样及其文件要求:
4.1零件应按照XXXX授权的图纸、样板、模型和/或其它设计文件所规定的材料制做。
若与设计有偏差,供应商需向XXXX采购部联系以变更申请的方式获得正式授权.
4.2所有样件需提交以下资料已供评审
机加产品:《材质证明》《全尺寸检测报告》《检测图纸》《表面处理报告》必选项《第三方测试报告》《产品性能检测报告》《其他》必要时工模夹具:《产品设计图纸》《性能测试报告》《产品检测报告》《产品样件》
表面处理产品:《表面处理检测报告》《SGS报告》《ROHS报告》
标准件:《第三方测试报告》《力学测试报告》《盐雾测试报告》《ROHS报告》
粉末:《SGS报告》《产品检测报告》《ROHS报告》《色板》必要时
包材:《ROHS报告》《性能测试报告》《成分分析报告》《COC合格证》必要时
耗材:《产品检测报告》《COC合格证》必要时
其他:产品质量合格证明材料
(备注:所有产品供应商需提交产品质量合格证明材料,如未提交可直接视为不合格品依据《不合格品管制程序》执行退货处理)
4.3、所有量产产品需提交材质证明.检验报告等符合性证明材料已供IQC进行参考
5、包装标识要求:
产品周转送货过程中需对产品进行防护,因包装导致的产品缺陷,可自动视为不合格品每个独立包装需进行标识并由供应商品管进行检验盖章,箱体内不同产品需明显区分,利用包装材料或纸板隔开,标识内容包含不包括以下内容:生产日期、产品料号、版本号、数量、订单号码、检验员等内容.
上述产品任何一项缺失可视为不合格品
6、供应商资料存档.
IQC检验PASS后所接收的相应报告需进行统一存档分类管理,部分报告需以扫描电子挡进行存档存档日期为2年.重要资料保存时间为5年.
7、增减项目:(视特殊情况增减)
海宁XXXX发展有限公司
XXXX Technology Development Co., LTD.
TEL:
(供应商)来料送样、板样件提交清单
注:1、供应商来料送样需求暂定以上要求,如有其它要求再另行通知。
2、单件样品单价超过50元RMB时,样品数量改为1
执行日期:2011/06/01
编制:高俊毅审核:批准:版本:A 海宁XXXX发展有限公司
XXXX Technology Development Co., LTD.
TEL:。