基于正交试验的汽车油箱口盒冲压成形工艺参数优化
发动机油箱底壳零件冲压工艺分析与模具设计毕业论文

发动机油箱底壳零件冲压工艺分析与模具设计毕业论文目录摘要 (I)Abstract (II)第一章序言 (1)1.1 概述 (1)1.2 冲压技术的发展 (1)1.3 模具的发展与现状 (2)1.4 模具CAD/CAE/CAM技术 (2)1.5设计的主要特点及意义 (4)1.6 汽车油底壳的相关知识补充 (4)1.6.1 前言 (4)1.6.2 汽车发动机油底壳材料的发展历史 (5)第二章发动机油底壳成型工艺的总体分析 (6)2.1油底壳结构及工艺难点分析 (6)2.2油底壳冲压工艺分析及方案确定 (7)2.2.1工艺流程初定 (7)2.2.2 拉深次数的确定 (7)2.2.2.1 常规计算模式: (7)2.2.2.2 有限元模拟分析 (10)2.2.2.3工艺流程的最终确定 (11)2.2.2.4 落料毛坯尺寸确定 (11)第三章拉深及法兰面冲孔的工艺分析和模具设计 (14)3.1落料 (14)3.1.1工艺分析 (17)3.1.2 工艺方案的确定 (18)3.1.3冲裁间隙的确定 (18)3.1.4凸模与凹模刃口尺寸的确定 (18)3.1.4.1凸、凹模具刃口尺寸计算原则 (18)3.1.4.2凸、凹模刃口尺寸计算方法 (20)3.1.5 冲裁工艺力的计算 (20)3.2 拉深 (23)3.2.1油底壳的拉深工艺分析 (24)3.2.1.1对拉深件形状的要求 (24)3.2.1.2对拉深件的圆角半径和拉深件精度的要求 (25)3.2.2拉深工艺力的计算 (25)3.2.2油底壳拉深模具设计及其结构设计要点 (27)3.2.2.1结构设计要点 (27)3.2.2.2模具工作过程 (28)3.2.2.3模具的导向 (28)3.2.2.4凹模圆角半径及凸凹模间隙参数的确定 (28)3.2.2.5成型凹模及顶件块的设计 (29)3.2.2.6模具材料及热处理要求 (29)3.3整形 (32)3.4切边 (32)3.5翻边、校平 (32)3.6冲法兰面孔 (33)3.6.1冲压模具的基本结构组成 (33)3.6.2 模具结构特点 (33)3.6.3 模具工作过程 (33)3.6.4 模具零部件的结构设计与相关冲裁力及部件尺寸的计算.. 343.6.4.1凸、凹模刃口尺寸的计算 (34)3.6.4.2凸、凹模的设计 (35)3.6.4.3模板的设计 (37)3.6.4.4卸料弹簧的选用 (38)3.6.4.5冲压设备的选用 (38)3.6.4.6 压力中心的计算 (41)3.7冲放油塞孔 (42)第四章总结 (43)第五章结束语 (43)参考文献 (44)附录 (45)附录一:外文文献 (45)附录二:外文翻译 (52)油箱底壳零件冲压工艺分析及模具设计材料学院成型061404 陈翔宇指导教师:曹建新摘要本设计应用本专业所学课程的理论和生产实际知识进行一次冷冲压模具设计工作的实际训练从而培养和提高学生独立工作能力,巩固与扩充了冷冲压模具设计等课程所学的内容,掌握冷冲压模具设计的方法和步骤,掌握冷冲压模具设计的基本的模具技能懂得了怎样分析零件的工艺性,怎样确定工艺方案,了解了模具的基本结构,提高了计算能力,绘图能力,熟悉了规范和标准,同时各科相关的课程都有了全面的复习,独立思考的能力也有了提高。
冲压工艺参数对零件成形质量的影响研究
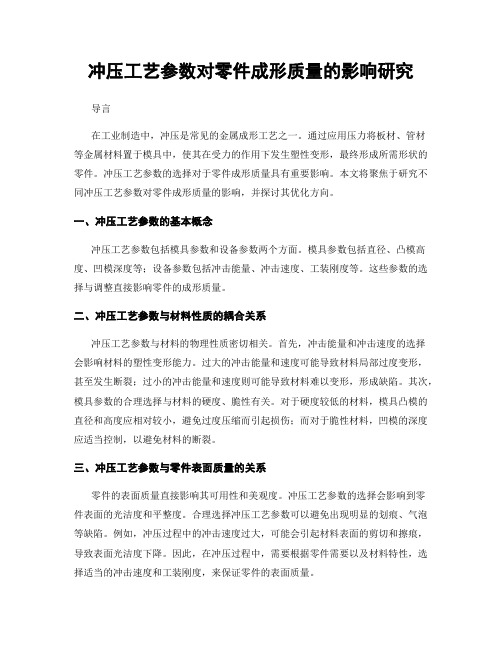
冲压工艺参数对零件成形质量的影响研究导言在工业制造中,冲压是常见的金属成形工艺之一。
通过应用压力将板材、管材等金属材料置于模具中,使其在受力的作用下发生塑性变形,最终形成所需形状的零件。
冲压工艺参数的选择对于零件成形质量具有重要影响。
本文将聚焦于研究不同冲压工艺参数对零件成形质量的影响,并探讨其优化方向。
一、冲压工艺参数的基本概念冲压工艺参数包括模具参数和设备参数两个方面。
模具参数包括直径、凸模高度、凹模深度等;设备参数包括冲击能量、冲击速度、工装刚度等。
这些参数的选择与调整直接影响零件的成形质量。
二、冲压工艺参数与材料性质的耦合关系冲压工艺参数与材料的物理性质密切相关。
首先,冲击能量和冲击速度的选择会影响材料的塑性变形能力。
过大的冲击能量和速度可能导致材料局部过度变形,甚至发生断裂;过小的冲击能量和速度则可能导致材料难以变形,形成缺陷。
其次,模具参数的合理选择与材料的硬度、脆性有关。
对于硬度较低的材料,模具凸模的直径和高度应相对较小,避免过度压缩而引起损伤;而对于脆性材料,凹模的深度应适当控制,以避免材料的断裂。
三、冲压工艺参数与零件表面质量的关系零件的表面质量直接影响其可用性和美观度。
冲压工艺参数的选择会影响到零件表面的光洁度和平整度。
合理选择冲压工艺参数可以避免出现明显的划痕、气泡等缺陷。
例如,冲压过程中的冲击速度过大,可能会引起材料表面的剪切和擦痕,导致表面光洁度下降。
因此,在冲压过程中,需要根据零件需要以及材料特性,选择适当的冲击速度和工装刚度,来保证零件的表面质量。
四、优化冲压工艺参数的方法为了获得更好的成形质量,优化冲压工艺参数是必要的。
一种常见的方法是设计合适的试验方案,通过实验数据和数学模型的拟合,找到最佳的参数组合。
例如,通过响应面法和正交试验设计,可以得到不同参数组合下零件表面形貌特性的数学模型,从而预测最优参数的取值范围。
此外,模拟仿真技术也是一种重要的工具。
通过建立合适的模型,在虚拟环境中模拟冲压过程,可以评估不同参数组合对零件成形质量的影响,为优化工艺参数提供指导。
基于正交试验的车身覆盖件冲压成形回弹分析

( 华东 交通大 学 机 电工程学 院 , 昌 3 0 1 ) 南 3 0 3 Sp ig a k a ay i f t m pn 0 mi g f r h u o o y p e r b c n lss o a n s i g f r n o e a t b d an l t b s d o t o o a s a e n or g n ly t t h i e t
表 1 回弹 正 交试 验 因素 及水 平
有的等效节点力都趋于零时 ,其板料形状即为回弹后板料 的形 状 。由于此方 法无需进 行接触判断 ,故计算 时问较有模法少 。
D nfr y a m软件分析回弹 的方法采用 的是无模法 。其进行回弹过 o 程模拟的计算流程 , 图 2 如 所示。
W ANG n , IZ - u n, HOU Ch n — u Ni g ME i y a Z aggo
(col f caiaadeetnc] nier gE sC ia i tn nvri , acag30 1 ,hn ) Shoo hncl n l r iaE g e n ,at hn a ogU iesyN nhn 30 3 C ia Me ci n i Jo t
图 1等 截 面 直 梁 的纯 弯 曲
都有重要价值 。因此 , 薄板冲压回弹仿真计算及其应用技术不仅
由于采用平截面假定 , 两个横截 面 A1 1 A B B 和 2 2在弯矩 M
是薄板冲压成形领域 的热点问题 , 而且该研究对 回弹仿真的发展 作用下作相对旋转但仍皆垂直于梁的对称平面, 于是凸面 A A 12 和工业应用都具有重要意义。 的纵 向纤维受拉深而凹面 B1 2的纵 向纤维受压缩。 B 在垂直与对
油箱注油口冲压工艺及模具设计
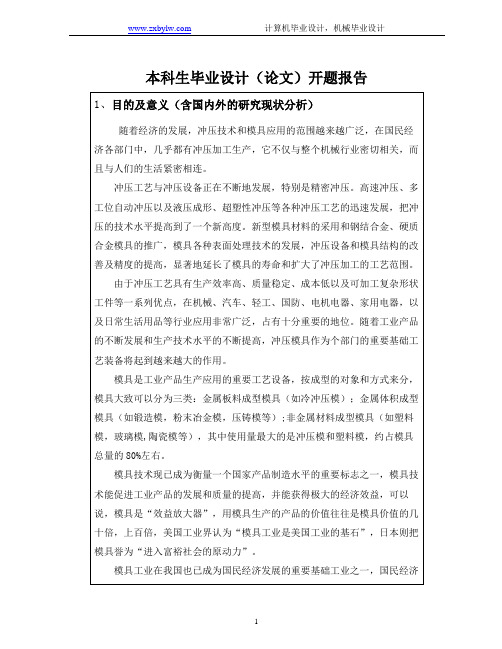
本科生毕业设计(论文)开题报告1、目的及意义(含国内外的研究现状分析)随着经济的发展,冲压技术和模具应用的范围越来越广泛,在国民经济各部门中,几乎都有冲压加工生产,它不仅与整个机械行业密切相关,而且与人们的生活紧密相连。
冲压工艺与冲压设备正在不断地发展,特别是精密冲压。
高速冲压、多工位自动冲压以及液压成形、超塑性冲压等各种冲压工艺的迅速发展,把冲压的技术水平提高到了一个新高度。
新型模具材料的采用和钢结合金、硬质合金模具的推广,模具各种表面处理技术的发展,冲压设备和模具结构的改善及精度的提高,显著地延长了模具的寿命和扩大了冲压加工的工艺范围。
由于冲压工艺具有生产效率高、质量稳定、成本低以及可加工复杂形状工件等一系列优点,在机械、汽车、轻工、国防、电机电器、家用电器,以及日常生活用品等行业应用非常广泛,占有十分重要的地位。
随着工业产品的不断发展和生产技术水平的不断提高,冲压模具作为个部门的重要基础工艺装备将起到越来越大的作用。
模具是工业产品生产应用的重要工艺设备,按成型的对象和方式来分,模具大致可以分为三类:金属板料成型模具(如冷冲压模);金属体积成型模具(如锻造模,粉末冶金模,压铸模等);非金属材料成型模具(如塑料模,玻璃模,陶瓷模等),其中使用量最大的是冲压模和塑料模,约占模具总量的80%左右。
模具技术现已成为衡量一个国家产品制造水平的重要标志之一,模具技术能促进工业产品的发展和质量的提高,并能获得极大的经济效益,可以说,模具是“效益放大器”,用模具生产的产品的价值往往是模具价值的几十倍,上百倍,美国工业界认为“模具工业是美国工业的基石”,日本则把模具誉为“进入富裕社会的原动力”。
模具工业在我国也已成为国民经济发展的重要基础工业之一,国民经济的支柱产业如机械,电子,汽车,石油化工和建筑业等都要求模具工业的发展与之相适应,都需要大量的模具,特别是汽车,电机,电器,家电和通信等产品中60%~80%的零件都要依靠模具成型。
基于正交试验法的注塑件成型工艺参数优化设计

基于正交试验法的注塑件成型工艺参数优化设计引言注塑成型是一种常见的加工工艺,用于制造各种形状复杂的塑料制品。
在注塑件成型过程中,工艺参数的优化设计对于产品质量的提高和生产效率的提升具有至关重要的作用。
本文将介绍一种基于正交试验法的注塑件成型工艺参数优化设计方法。
正交试验法的概述正交试验法是一种在多因素影响下进行试验的方法,通过选择一组经过科学设计的试验方案,可以在尽量少的试验次数内获取最全面的试验数据。
该方法能够通过独立变量的选择、合理的试验方案和统计分析的方法,确定各个因素对结果的影响程度以及相互之间的关系。
正交试验法在注塑件成型工艺参数优化设计中的应用在注塑件成型过程中,有许多因素会影响最终产品的质量,如注塑温度、注射速度、保压时间等。
通过正交试验法,可以确定这些因素的最佳设置,以获得最佳的注塑件成型工艺参数。
步骤一:确定影响因素首先,我们需要确定影响注塑件成型的各个因素。
基于经验和相关文献,我们可以列出一些可能的影响因素,如注塑温度、注射速度、保压时间、模具温度等。
步骤二:选择试验水平在进行正交试验之前,我们需要确定每个因素的试验水平。
试验水平的选择应该满足设计要求并尽可能简化试验过程。
一般来说,我们可以选择每个因素的三个水平进行试验。
步骤三:设计试验方案基于已确定的因素和试验水平,我们可以使用正交试验表设计试验方案。
通过正交试验表的选择,我们可以避免冗余试验和测试过程的复杂性。
步骤四:进行实验根据设计的试验方案,我们可以开始进行实验。
在每个试验点上,我们需要记录各个因素的设置和相应的试验数据。
通过多次试验,我们可以获得一系列试验数据,进一步分析每个因素的影响。
步骤五:数据分析通过对实验数据的分析,我们可以得到不同因素之间的相对重要性和相互之间的关系。
常用的数据分析方法包括方差分析、回归分析等。
通过这些分析方法,可以确定最佳的注塑件成型工艺参数。
结论基于正交试验法的注塑件成型工艺参数优化设计方法能够帮助我们快速、有效地确定最佳的工艺参数。
基于正交试验法的汽车保险杠注塑成型工艺参数多目标优化研究
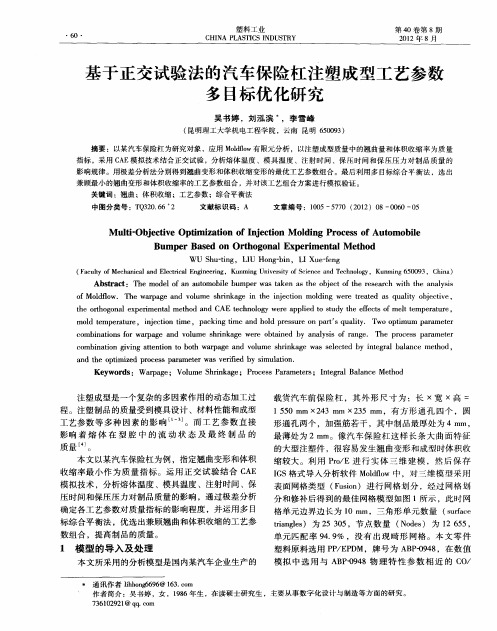
m l m eaue net nt e akn m n o rs r npr Sq a t.T oo t m p rme r o t p rtr,ijc o m ,p c i t ea dh l pes eo at uly w p mu aa t de i i gi d u i i e
c mb n t n o r a e a d v l me s rn a e wee o t i d b nay i fr ng . T r c s r me e o i a i sf rwa p g n ou h k g r b ane y a l ss o a e o i he p o e s pa a tr
t ah g n x e i ntlme h d a d CAE e hn lg r p le osu y t e ef cs o l t mp r t e, he o o o a e p rme a t o n l tc oo y we e a p id t t d h f t fmet e e aur e
c mb n t n gv n t n in t oh w r a e a d v l me s r k g a ee t d b n e r lb l n e meh d, o i a i i i g at t b t a p g n o u h n a e w s s l ce y i tg a aa c t o o e o o i a d t e o t z d p o e s p r mee s v r e y s lt n n h p i e r c s a a trwa e f d b i ai . mi i i mu o
载货 汽车前 保 险杠 ,其 外 形 尺寸 为 :长 ×宽 ×高 =
基于正交试验的汽车手套箱盖成型工艺参数优化

基于正交试验的汽车手套箱盖成型工艺参数优化作者:刘小星来源:《科技创新与应用》2017年第09期摘要:文章以某汽车仪表板手套箱盖为研究对象,利用Moldflow软件结合正交试验方法研究了不同成型工艺参数对手套箱翘曲变形量的影响规律。
研究结果表明,各参数对翘曲缺陷的影响程度的重要性依次为:保压时间>熔体温度>模具温度>注射时间;利用正交试验方法对汽车仪表板手套箱盖注塑成型工艺参数进行优化,研究表明汽车手套箱盖的注塑质量得到较大提高,翘曲变形量减小18.56%。
研究结果为汽车手套箱盖的注塑工艺参数提供了参考依据。
关键词:注塑成型;汽车手套箱;参数优化;翘曲变形量1 概述塑料凭借便于成型且质轻、强度高等优点而被广泛使用。
传统的注塑工艺参数设置采用尝试法,极为依赖工程师的设计经验。
运用仿真分析,对仿真计算结果进行分析,可获得最优的工艺参数组合。
本文以某车型仪表板手套箱盖为研究对象,利用Moldflow软件结合正交试验方法探究最佳工艺参数。
2 正交试验的设计及结果分析选择某车型手套箱盖模型,其尺寸为369.0mm×272.7mm×14mm,主体壁厚为2.0mm,采用注塑成型工艺。
为减少模拟试验次数,采用正交试验设计方法,对手套箱模型进行模拟分析。
根据实际经验,选取影响注塑成型的4个因素,每个因素安3个水平。
具体因素和水平如表1所示。
根据表1的变量和水平,利用Minitab软件设计一个包含9个样本的正交试验表L9(113),根据正交表所规定的试方案,利用Moldflow软件对手套箱盖的注塑成型过程进行仿真模拟分析,提取出各工艺参数下的翘曲量数据结果。
通过分析田口设计得到各变量对翘曲量的主效应图,如图1所示。
由图1可知,在所有的影响因素中,对翘曲量影响最大的是保压时间,其次是熔体温度、注射时间和模具表面温度。
根据模拟实验结果选取的最优工艺参数组合为:熔体温度230℃,注射时间1.8s,保压时间12s,模具温度40℃。
基于正交试验的壳结构冲压成型工艺参数优化

基于正交试验的壳结构冲压成型工艺参数优化以某壳结构为研究对象,通过UG建模软件对研究对象组件进行三维设计建模,借助Abaqus数值模拟软件对冲压过程进行模拟分析,选取冲压过程中的压边力,冲压速度,摩擦系数为实验影响参数,每种参数选取三个水平,采用正交试验法进行数值分析试验,将数值模拟和正交实验方法相结合,以板材减薄率、厚度极差为实验结果优劣指标。
分析四种参数的不同组合对模拟成型质量的影响。
结果表明,最优工艺组合为第七组,压边力600kg、冲压速度4m/s、摩擦系数0.13时,减薄率、厚度极差最小。
标签:冲压成形;数值模拟;正交试验;Abaqus 软件在如今产品轻量化的趋势下,大量的产品设计师设计零件时都采用板材冲压结构,例如:每辆汽车几乎80%的零件都采用了冲压结构,包含1000多套冲压模具,而冲压件的制造容易出现破裂起皱,所以这些冲压件的结构、质量就决定了汽车整体的安全性、美观性,本文采用的壳结构就是一种大变形,成型过程复杂的深压件。
把握冲压过程中的关键工艺参数就显得尤为重要,例如冲压速度、摩擦系数、压边力[1,2]等,本文对这些参数进行加权处理,利用正交试验法和数值分析对冲压过程进行模拟[3],研究壳结构在冲压过程中,以上三种参数对冲压成形质量的影响,选出最优组合方式,结果可用于实际工作参考,减少试模次数,提高成形率,具有很大的现实意义。
1 建立有限元模型1.1 零件结构设计如图1所示壳结构,该零件尺寸较大,并且较深,在冲压过程中,容易产生拉伸起皱,减薄破裂等现象,所以根据原始结构的冲压模型进行了重新设计,在UG软件中建立了结构三维壳体模型。
1.2 建立冲压有限元模型图1所示的模型经设计可直接作为凹模,根据凹模,通过偏置可以分别得到凸模,毛坯以及压边圈,图2为有限元软件Abaqus中建立的油底壳冲压工序的有限元模型。
根据宝钢公司最新的ST14钢材料的性能测试数据,数值模拟过程中的力学性能设置如表1所示[4]。
- 1、下载文档前请自行甄别文档内容的完整性,平台不提供额外的编辑、内容补充、找答案等附加服务。
- 2、"仅部分预览"的文档,不可在线预览部分如存在完整性等问题,可反馈申请退款(可完整预览的文档不适用该条件!)。
- 3、如文档侵犯您的权益,请联系客服反馈,我们会尽快为您处理(人工客服工作时间:9:00-18:30)。
基于正交试验的汽车油箱口盒冲压成形工艺参数优化*江龙廖荣华邱伟林(海南宇龙汽车部件有限公司,海南海口570226)引言汽车覆盖件的可成形程度和成形质量主要取决于其模具系统(凸模、凹模、压边圈、拉深筋等)和冲压工艺参数(润滑油、压边力、冲头速度、凸凹模间隙等)[1-2]。
实际生产中,当模具系统的参数已确定时,则仅能对冲压工艺参数进行调节。
由于冲压工艺参数对汽车覆盖件成形质量具有较大影响,人们对此已展开了大量的研究[3-5]。
以有限元为理论基础的金属板材冲压成形CAE分析技术已经在汽车设计制造中得到广泛应用,通过数值模拟技术可对汽车覆盖件冲压工艺做出定性指导并得出一些有益结论。
文献[6]运用Dy-naform进行有限元模拟分析了压边力、凹模圆角半径、凸模圆角半径对汽车油箱成形极限的影响。
文献[7]利用有限元模拟方法,研究了压边力、摩擦系数、冲压速度及板料尺寸对汽车后端板加强件成形质量的影响。
文献[8]利用自主开发的商品化冲压成形CAE软件研究了汽车外覆盖件表面破裂缺陷产生的原因并进行精确预示。
目前,汽车覆盖件冲压工艺数值模拟技术尚存在缺乏定量精度等不足,为获得质量优异的汽车覆盖件,仍然需要进行反复的试验调整,而合理的试验设计方法在一定程度上可以减少反复试凑的盲目性,能以较少的试验次数得到试验范围内较优的工艺组合。
文章以一汽海马汽车有限公司某车型的油箱口盒为例,采用正交试验进行优化研究,以提高产品的质量及合格率,从而降低生产成本。
1正交试验方案设计正交试验设计利用数理统计学与正交性原理从大量的试验点中挑选适量的具有代表性、典型性的点,应用正交表合理安排试验。
正交试验设计方法中所选择的试验对每个因素和因素的每个水平都为均匀分配,此外,还需保证每个因素的水平以相同的次数出现,且任何两个因素的搭配出现的次数相同。
冲压成形过程中,板料取决于设计要求,一般不会改变。
调整成形质量的工艺参数多考虑模具几何尺寸、板料尺寸、压边力、润滑和冲压速度等,文章主要研究压边力、凸凹模间隙及板料尺寸3个因素对成形质量的影响,根据生产实际情况,确定为3因素3水平,如表1所示。
2油箱口盒形状如图1所示。
板材选取宝山钢铁股份有限公司生产的冷连轧低碳钢板,其牌号、化学成分及力学性能如表2,在YQ32-100液压机上进行主要工序冲压的变形实验,采用PX-7DL超声波测厚仪对冲压件进行厚度测试。
3实验结果与分析板料冲压成形性能包括抗破裂性、贴模性和定形性等,由于冲压件一旦开裂则成为废品,所以文章在满足板料不发生破裂的前提下,将板料冲压成形后的减薄率作为正交试验的评价指标,其值越小则冲压件成形质量越好。
正交试验结果如表3所示。
由表3知,各因素对油箱口盒冲压件减薄率(反映开裂趋势)的影响,按从大到小的顺序排列为凸凹模间隙>压边力>板材尺寸。
表3油箱口盒冲压工艺正交试验结果板件拉伸时压应力过大而导致失稳将引起起皱现象的出现,当皱纹均匀分布在拉伸件的四周时,起皱原因主要是由于压边力过小而引起,故只需增加压边力或者通过在压边圈上增加拉延筋加以消除,而当压边力过大时,局部减薄率过大,容易在拉伸件的直壁上开裂,形成废品。
凸凹模间隙过大时,拉伸件容易局部失稳而产生起皱现象,此时应适当调整凸凹模间隙,以防止起皱产生,凸凹模间隙过小时,板料难以流入凹模,往往导致拉裂的出现。
板料尺寸增大将引起压料面与板料的接触面积增加,引起材料流动的变化,有利于减小拉伸件的减薄率,获得质量良好的制品,板料尺寸过小时,板料在冲压过程中迅速进入凹模,容易导致起皱出现,增加拉伸件厚度的波动,从实际应用的角度出发,在保障拉伸顺利进行的基础上,应尽可能减少板料尺寸以提高材料利用率。
摘要:采用正交试验设计方法综合评估了冲压过程中的压边力、模具间隙和板材尺寸对汽车油箱口盒冲压成形质量的影响,通过对试验数据的分析,找到最优的工艺参数组合,所得结论对汽车油箱口盒冲压工艺的设计具有指导意义。
关键词:汽车油箱口盒;冲压工艺参数;正交试验*基金项目:海南省产学研一体化专项资金项目(CXY20130056)。
图1油箱口盒表2板材成分及力学性能20--李广鑫王乾(洋石油工程股份有限公司,天津300451)引言管道设计中,当管道热胀或冷缩将使该支承点处有较大垂直位移时,使该点支架脱空或支架推力过大,刚性支架失去作用,该工况将造成管道一次应力增大或邻近支架(或设备)超载,或将使管道产生较大的二次应力,对管道和支吊架产生破坏,这时管道支承点处需要采用弹簧支吊架[1-2,5];在与敏感机械设备相连接的管道处,为减少对设备管口处的受力影响,亦采用弹簧支吊架[1-4]。
CAESARII 管道应力分析软件是由美国COADE 公司研发的压力管道应力分析专业软件,内置国际上通用的管道设计规范,可进行管系在承受自重、压力载荷、热载荷、地震载荷和其它静态和动态载荷作用下的管道应力分析。
同时,软件内置了Sinopec (China )、ANVIL 、LISEGA 等弹簧库,允许在多个热工况下,选择冷态或热态吊零,使用标准或扩充的载荷范围,对弹簧进行自动选型设计,并从弹簧库中选择合适的弹簧支吊架。
文章以LNG 超低温管道为例,应用CAESAR II 软件,以Sinopec (China )弹簧标准,给出管道用弹簧支架的快速选型设计方法。
1弹簧支吊架选用原则弹簧支架分为可变弹簧支架和恒力弹簧支架。
可变弹簧支架适用于支承点有垂直位移,用刚性支承会脱空或造成过大热胀推力的场合,可变弹簧会造成一定的荷载转移,为防止过大的荷载转移,要求可变弹簧荷载变化率小于或等于25%[6]。
可变弹簧支吊架设计时主要考虑弹簧的工作载荷、运行时的位移量和位移方向、管道的空间位置、弹簧的形式、工作范围位移、弹簧支吊架编号和安装载荷,在弹簧能够承受工作载荷、安装载荷,载荷变化率在满足要求的前提下,力求选用较小规格的弹簧。
当管道的垂直位移大于50mm ,或需要减小设备管口受力,亦或可变弹簧的载荷变化率超过25%时,应选择恒力弹簧[7]。
恒力弹簧的恒定度应小于或等于6%,以保证支吊点发生位移时,支承力的变化很小。
2CAESAR II 中弹簧支吊架设计CAESAR II 软件采用热态吊零法进行弹簧支架的设计,即操作工况(W+T1+P1+H ,OPE )下,按每个支吊点处管道自重产生的垂直位移为零的条件来分配载荷,用大刚度支吊架代替吊零处的弹簧支吊架,弹簧支吊架垂直位移为零。
2.1CAESARII 弹簧支吊架设计控制参数CAESARII 为用户进行自动弹簧设计时提供了很多控制参数,如图1所示,说明如下。
图1弹簧设置界面Hanger Table (弹簧表)———用来指定使用哪个制造商的弹簧。
Extended Range (极限范围):允许应用弹簧表中的弹簧极限范围。
Cold Load (冷态载荷):计算弹簧支架的实际安装载荷。
Hot Load centered (热态居中):当一个弹簧选定后,热态载荷落到整个载荷范围的中间位置。
Available Space (可用安装空间)———管顶和高处型钢之间、管底与底处基础之间的距离,决定弹簧允许安装空间。
Allowable Load Variation%(许用载荷变化率%)———对于可变弹簧,要求载荷变化率不超过25%,设计者可改变载荷变化率,设计弹簧。
Rigid Support Displacement Criteria (刚性支架的位移标准):当竖直位移小于给定值时,用刚性支架替换弹簧。
Max.Allowed Travel Limit (最大允许形成限制):当竖直位移大于给定值,选用恒力弹簧替代可变弹簧。
Allow Short Range Springs (允许短程弹簧)———CAESARII 的弹摘要:弹簧支吊架主要解决管道有垂直位移时的支撑和减小敏感设备管口的受力问题,弹簧支吊架的合理设置和正确选择,对管系的安全平稳运行起着决定性的作用。
文章应用CAESAR II 管道应力分析软件,以液化天然气超低温管道为例,讲解快速设计脱空管道弹簧支架方法,并对管道进行应力分析校核,管道应力及支架受力满足要求,弹簧选择合理。
关键词:CAESAR II ;管道;弹簧支架;应力分析基于正交试验结果并经上述分析,选择优化后的油箱口盒冲压件工艺参数为:压边力300KN ,凸凹模间隙0.5mm ,板材尺寸370mm ×370mm 。
在该组工艺参数下油箱口盒冲压件成形质量较好,结果令人满意。
4结束语文章以板料成形压边力、凸凹模间隙和板材尺寸作为可调整工艺参数,通过正交试验对某汽车油箱口盒冲压件工艺参数进行优化,以减薄率(反映开裂趋势)为评价指标,得到各参数对成形质量的影响程度为:凸凹模间隙>压边力>板材尺寸,并分析了各个参数对成形质量的影响规律。
在此基础上得到优化后的油箱口盒冲压件工艺参数,使板料减薄率有一定的减小,且成形质量较好,获得了令人满意的结果,这为提高零件的冲压成形质量,减少生产成本创造了有利条件。
该方法为油箱口盒冲压件冲压工艺参数的调节提供了指导,具有一定的工程应用价值。
参考文献[1]林忠钦,李淑慧.车身覆盖件冲压成形仿真[M].北京:机械工业出版社,2005.[2]郑燕平,闫盖,何镇罡.冲压工艺参数对成形质量的影响分析[J].热加工工艺,2012,42(23):146-149.[3]LAN F ,LIN J ,CHEN J.An integrated numerical technique in determining blank shape for net shape sheet metal forming [J].Jour -nal of Materials Processing Technology ,2006,177(1/3):72-75.[4]陈吉清,王玉超,兰凤崇.基于正交试验的汽车覆盖件冲压工艺参数优化[J].计算机集成制造系统,2007,13(12):2433-2440.[5]魏阿梅,白振江,曹彪.浅谈汽车外覆盖件冲压成型关键缺陷以及解决方法[J].装备制造技术,2014(3):68-70,85.[6]陆广华,秦丁益,张跃,等.汽车油箱冲压成形有限元分析与研究[J].热加工工艺,2012,40(23):94-96.[7]闫盖,郑燕萍,张文彦,等.基于正交试验的板料冲压成形工艺参数优化[J].热加工工艺,2012,42(17):94-97.[8]王金武,胡平,付争春,等.汽车覆盖件破裂试验及基于广义成形技术仿真[J].农业机械学报,2009,40(11):228-231.作者简介:江龙(1979-),男,广东普宁人,助理工程师,本科学历,主要从事汽车覆盖件冲压工艺研究。