一种零件的数控车削加工工艺分析
数控车削零件工艺分析举例

※T0404——螺纹刀:刀尖角60°,主轴转速400r/min,进给 速度2mm/r(螺距)。
数控车削加工工艺
※T0505——钻头:钻头直径16mm,主轴转速450r/min。
※T0606——内圆粗车刀:内轮廓粗加工,刀尖圆弧半径 0.8mm,切深1mm,主轴转速500r/min,进给速度100mm/min。 ※T0707——内圆精车刀:内轮廓精加工,刀尖圆弧半径 0.8mm,切深0.4mm,主轴转速800r/min,进给速度60mm/min。
*装夹Φ50外圆表面,探出65mm,粗加工零件左侧外轮廓:
2×45°倒角,Φ48外圆,R20,R16,R10圆弧。
*精加工上述轮廓。
数控车削加工工艺
*手工钻孔,孔深至尺寸要求。 *粗加工孔内轮廓。 *精加工孔内轮廓。 *调头装夹Φ48外圆,粗加工零件右侧外轮廓:2×45°倒
角,螺纹外圆,Φ36端面,锥面,Φ48外圆到圆弧面。
数控机床编程与操作
数控车削加工工艺
完成如图所示零件的加工。毛坯尺寸ф50×114,材料 45钢,零件的径向尺寸公差±0.01mm。
数控车削加工工艺
1.图纸分析 (1)加工内容: 此零件加工包括车端面,外圆,倒角,圆弧,螺纹,槽等。 (2)工件坐标系: 该零件加工需调头,从图纸上尺寸标注分析应设置2个坐标 系,2个工件零点均定于装夹后的右端面(精加工面)。
*精加工上述轮廓。 *切槽。 *螺纹加工。
数控车削加工Байду номын сангаас艺
(5)刀具的选择和切削用量的确定
※T0101——外圆粗车刀:外轮廓粗加工,刀尖圆弧半径 0.8mm, 切 深 2 mm, 主 轴 转 速 8 0 0 r/min , 进 给 速 度 150mm/min。 ※T0202——外圆精车刀:外轮廓精加工,刀尖圆弧半径 0.8mm, 切深0.5mm,主轴转速1500r/min,进给速度 80mm/min。
数控车削加工工艺分析
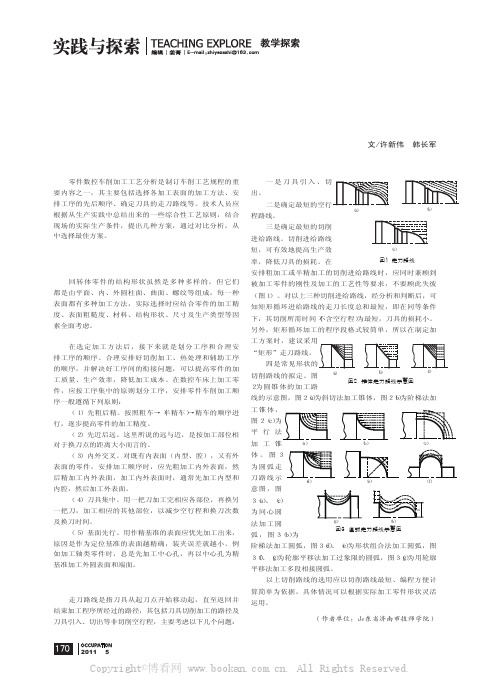
OCCUPATION2011 5170数控车削加工工艺分析文/许新伟 韩长军零件数控车削加工工艺分析是制订车削工艺规程的重要内容之一,其主要包括选择各加工表面的加工方法、安排工序的先后顺序、确定刀具的走刀路线等。
技术人员应根据从生产实践中总结出来的一些综合性工艺原则,结合现场的实际生产条件,提出几种方案,通过对比分析,从中选择最佳方案。
一、拟定工艺路线1.加工方法的选择回转体零件的结构形状虽然是多种多样的,但它们都是由平面、内、外圆柱面、曲面、螺纹等组成,每一种表面都有多种加工方法,实际选择时应结合零件的加工精度、表面粗糙度、材料、结构形状、尺寸及生产类型等因素全面考虑。
2.加工顺序的安排在选定加工方法后,接下来就是划分工序和合理安排工序的顺序。
合理安排好切削加工、热处理和辅助工序的顺序,并解决好工序间的衔接问题,可以提高零件的加工质量、生产效率,降低加工成本。
在数控车床上加工零件,应按工序集中的原则划分工序,安排零件车削加工顺序一般遵循下列原则:(1)先粗后精。
按照粗车→(半精车)→精车的顺序进行,逐步提高零件的加工精度。
(2)先近后远。
这里所说的远与近,是按加工部位相对于换刀点的距离大小而言的。
(3)内外交叉。
对既有内表面(内型、腔),又有外表面的零件,安排加工顺序时,应先粗加工内外表面,然后精加工内外表面,加工内外表面时,通常先加工内型和内腔,然后加工外表面。
(4)刀具集中。
用一把刀加工完相应各部位,再换另一把刀,加工相应的其他部位,以减少空行程和换刀次数及换刀时间。
(5)基面先行。
用作精基准的表面应优先加工出来,原因是作为定位基准的表面越精确,装夹误差就越小。
例如加工轴类零件时,总是先加工中心孔,再以中心孔为精基准加工外圆表面和端面。
二、确定走刀路线走刀路线是指刀具从起刀点开始移动起,直至返回并结束加工程序所经过的路径,其包括刀具切削加工的路径及刀具引入、切出等非切削空行程,主要考虑以下几个问题:一是刀具引入、出。
轴类零件数控车削工艺分析与数控加工编程
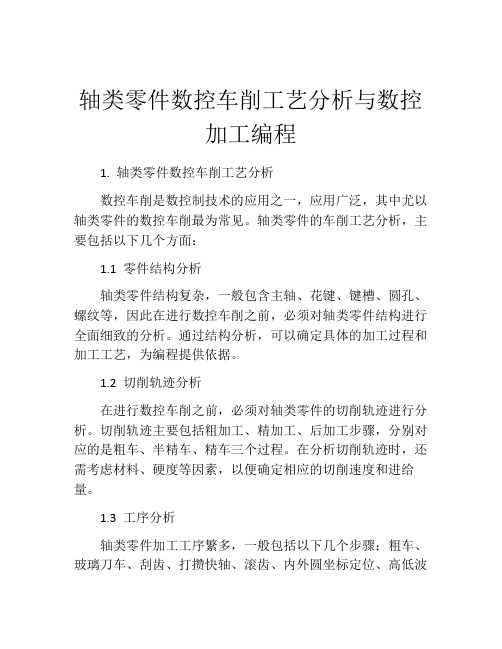
轴类零件数控车削工艺分析与数控加工编程1. 轴类零件数控车削工艺分析数控车削是数控制技术的应用之一,应用广泛,其中尤以轴类零件的数控车削最为常见。
轴类零件的车削工艺分析,主要包括以下几个方面:1.1 零件结构分析轴类零件结构复杂,一般包含主轴、花键、键槽、圆孔、螺纹等,因此在进行数控车削之前,必须对轴类零件结构进行全面细致的分析。
通过结构分析,可以确定具体的加工过程和加工工艺,为编程提供依据。
1.2 切削轨迹分析在进行数控车削之前,必须对轴类零件的切削轨迹进行分析。
切削轨迹主要包括粗加工、精加工、后加工步骤,分别对应的是粗车、半精车、精车三个过程。
在分析切削轨迹时,还需考虑材料、硬度等因素,以便确定相应的切削速度和进给量。
1.3 工序分析轴类零件加工工序繁多,一般包括以下几个步骤:粗车、玻璃刀车、刮齿、打攒快轴、滚齿、内外圆坐标定位、高低波形度测量、打热处理、喷油漆等,每个步骤都必须经过严格的工序分析。
1.4 工具选择在进行数控车削之前,必须选择适合的刀具。
刀具选择要根据零件的材料、硬度、形状、尺寸等因素进行。
此外,还要考虑要加工的零件数量、加工时的切削速度、进给量等因素。
2. 数控加工编程轴类零件的数控加工编程是一项极为关键的工作,其目的是实现数控机床对轴类零件进行自动化加工。
数控加工编程分为以下几个步骤:2.1 编写数控加工程序在进行数控加工编程之前,必须对轴类零件的结构和要求进行全面细致的分析。
在分析的基础上,可以编写出数控加工程序,并分别对应不同的加工工序。
2.2 编写刀具半径补偿程序在进行数控加工编程时,必须考虑刀具半径。
一般来说,刀具半径要比零件轮廓的半径小一定程度,为了解决这个问题,必须编写刀具半径补偿程序,以便更加准确地控制刀具的切削轨迹。
2.3 选择数字控制器数字控制器是控制数控机床的关键部分,必须选择适合的数字控制器。
数字控制器也分为多种类型,根据集成度的不同,可以分为单通道和多通道数字控制器。
轴类零件数控车削的工艺分析及编程

螺纹及倒角等表 面组成 ,其 中多个 直径 尺寸与轴 向尺 寸有 较 高 的尺寸精度要求。 件图尺寸标注完整 , 零 符合数 控加工尺寸 标注要求 ; 轮廓 描述清楚完整 ; 零件材料 为 4 5钢 , 切削加 工性 能较好 , 热处 理和硬度要求。零件图样上带公差 的尺寸 , 无 因 公差值较小 , 编程 时不必取其平均值 , 故 而取 基本尺寸 即工 质量和提高生 产率 的重要 环节 。粗车 时选 用强度高 、 耐磨度好 的刀具 , 以满
足大 背吃刀量 、 大进 给量 的要求 ; 车时 选用精度 高 、 精 耐磨度 好 的刀具 , 以保证 精度的要求 。根据零件 的外形 和加工要求 ,
选 用 选 用 4把 刀 :
量 的选择 原则 是 : 保证零件加 工精度和表 面粗糙 度 , 分发 挥 充
作者简介 : 芳(93 )女 , 廖 16一 , 广西南 宁人 , 讲师 。 研究方 向为数控加工技术 。
14 O
《 装备制造技术} 00 2 1 年第 4 期
刀具切削性 能 , 保证 合理 的刀具耐用度 ; 充分发挥机床 的性 并 能, 最大 限度提 高生产率 , 降低 成本 。根据 本例 中零件 的加工
心线为工艺基准 ,使用 三爪 自动定心卡盘夹住 3 m外 圆 0m
一
路线等 , 按规定 的代码格 式编制成 数控加工程序 , 数控车床在 程序的控制下 , 自动加工 出各种形 状不同的零件。轴类 零件是
各种机械设备 中最主要和最基本 的典 型零 件 ,本文 以轴类零 件为例 , 对数控车削加工 中的工艺分析及 编程做 些探讨。
重要设 备 , 已广泛应 用于机械 加工中。在数控车削加 工前 , 要 对所加 工的零件进行工艺分析 , 定正确的加工方案 , 确 将车床
数控车削加工工艺性分析

数控车削加工工艺性分析摘要本文结合当前数控机床发展的现状,阐述和分析了如何提高数控车床运行中的有效性,为准确加工合格的产品提供了一道技术保障,通过对目前最常见的数控车床的生产工艺进行比较与研究,讲述了如何才能合理的理顺工艺的顺序。
关键词数控车床;程序编制;车削加工中图分类号th18 文献标识码a 文章编号 1674-6708(2011)42-0134-02数控车削在加工过程中经常涉及到程序编制、工艺分析、装刀、对刀、装工件、半精加工、粗加工、精加工。
数控车削的加工是不是能有效地实现,主要就在于对数控车削全部工艺过程的合理分析。
1 数控车削的加工技术和方法数控车削的加工首先要选择其要加工的零件,这是整个加工过程的关键内容,然后就要对所要加工的零件图纸分析与研究,通过对整个数控车削的加工工艺路线的分析,才能准确的调整和选择具体的加工工具和夹具,对于切削用量也要进行具体的选择。
最后才是工步和工序的具体设计、加工轨迹的优化和计算以及编写整个数控加工的工艺技术制度及文件。
笔者在实践中曾观察过一些一线的数控车削的技术工人,发现总是有很多的使用者都是依据一个比较传统的路线进行工艺的分析。
其路线是:确定加工内容→研究图纸→选择工具→选择切削用量→划分和拟定工序→优化加工轨迹→编制技术文件。
然而经过笔者的分析和研究,发现如果依据上述路线,工步、工序的设计很多时候都是很难符合所需零件形位的公差要求,经常会导致一些产生次品的出现,针对这种现象,笔者提出以下的观点。
2 数控车削的加工技术的改进经过上述的分析和研究,笔者结合实际工作,对上述的加工路线做了如下的一些调整。
笔者感觉比较合理数控车削的工艺分析步骤为:确定加工内容→研究图纸→划分和拟定工序→选择工具→选择切削用量→优化加工轨迹→编制技术文件。
2.1 零件的图纸分析零件的图纸分析属于制定整个数控车削工艺的关键之所在。
要对所要加工的工件进行一个全面的摸底和评估,对具体的尺寸进行标注分析,对轮廓几何的要素和部件的加工技术和精度进行分析和研究。
数控车削加工工艺分析

浅谈数控车削加工工艺分析摘要:数控车床的使用的目的旨在加工出合格的零件,但是合格的零件的加工必须要依靠制定合理的加工工艺。
本文针对当前数控车床使用者的工艺分析的不合理来进行对比,讲述合理的工艺分析的顺序问题。
关键词:数控车床车削加工工艺工艺分析车削一、数控车削加工工艺的内容数控车削加工工艺是采用数控车床加工零件时所运用的方法和技术手段的总和.其主要内容包括以下几个方面:(一)选择并确定零件的数控车削加工内容;(二)对零件图纸进行数控车削加工工艺分析;(三)工具、夹具的选择和调整设计;(四)工序、工步的设计;(五)加工轨迹的计算和优化;(六)数控车削加工程序的编写、校验与修改;(七)首件试加工与现场问题的处理;(八)编制数控加工工艺技术文件;总之,数控加工工艺内容较多,有些与普通机床加工相似.二、数控车削加工工艺分析工艺分析是数控车削加工的前期工艺准备工作.工艺制定得合理与否,对程序的编制、机床的加工效率和零件的加工精度都有重要影响.为了编制出一个合理的、实用的加工程序,要求编程者不仅要了解数控车床的工作原理、性能特点及结构.掌握编程语言及编程格式,还应熟练掌握工件加工工艺,确定合理的切削用量、正确地选用刀具和工件装夹方法.因此,应遵循一般的工艺原则并结合数控车床的特点,认真而详细地进行数控车削加工工艺分析.其主要内容有:根据图纸分析零件的加工要求及其合理性;确定工件在数控车床上的装夹方式;各表面的加工顺序、刀具的进给路线以及刀具、夹具和切削用量的选择等.笔者观察了很多数控车的技术工人,阅读了不少关于数控车削加工工艺的文章,发现大部分的使用者采用选择并确定零件的数控车削加工内容、零件图分析、夹具和刀具的选择、切削用量选择、划分工序及拟定加工顺序、加工轨迹的计算和优化、编制数控加工工艺技术文件的顺序来进行工艺分析。
但是笔者分析了上述的顺序之后,发现有点不妥。
因为整个零件的工序、工步的设计是工艺分析这一环节中最重要的一部分内容。
数控加工工艺分析办法
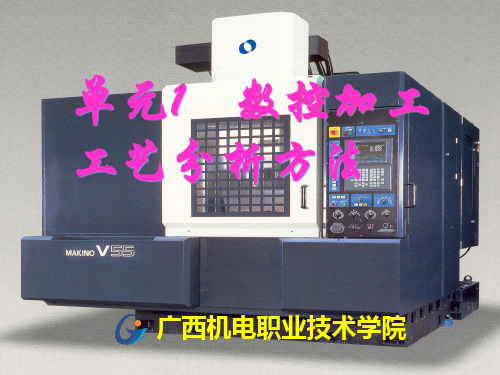
常用工件材料的高速切削速度范围表(m/min)
应用范围
目前,高速切削加工技术主要应用于车 削和铣削工艺,今后将涵盖所有的传统加工 范畴,从粗加工到精加工,从车削、铣削到 镗削、钻削、拉削、铰削、攻丝、滚齿等。
航空制造业、模具制造业、汽车制造业 等行业均已积极采用高速切削加工技术。
三、典型零件数控加工工艺分析实例
单元1 数控加工 工艺分析方法
广西机电职业技术学院
单元1 数控加工工艺分析方法
一、数控加工工艺分析方法
(一)零件图的工艺分析 (二)加工方法的选择 (三)工序的划分 (四)定位与夹紧方式的确定
(五)加工顺序的安排 (六)确定走刀路线和工步顺序 (七)切削用量的选择 (八)对刀点与换刀点的确定 (九)高速切削加工技术
二、典型零件数控加工工艺分析实例
(一)数控车削加工典型零件工艺分析实例 (二)数控铣削加工典型零件工艺分析实例
一、数控加工工艺分析方法
(一)零件图的工艺分析
1、零件图分析 (1)尺寸标注方法分析
注意基准统一原则,减少累积误差。 (2)零件图的完整性与正确性分析
几何图素条件要求充分。
(3)零件技术要求分析 尺寸精度、形状精度、位置精度、表面粗
(一)数控车削加工典型零件工艺分析实例
轴承套 数控车削加 工工艺(单 件小批量生 产),所用 机床为 CJK6240。
1、零件图工艺分析
采取以下工艺措施: 1)编程时取基本尺寸。 2)先加工左、右端面。 3)内孔尺寸较小,镗1﹕20锥孔、φ32孔及
15°斜面时需掉头装夹。
2、确定装夹方案
1)内孔加工时以外圆定位,用三爪自动 定心卡盘夹紧。
5、切削用量选择
根据被加工表面质量要求、刀具材料 和工件材料,参考切削用量手册或有关资 料选取切削速度与每转进给量,计算结果 祥见工序卡。
对于数控车削加工工艺分析

对于数控车削加工工艺分析数控车削加工是一种智能化的机械加工技术,它通过计算机程序控制旋转切削刃进行精密加工工艺。
这种工艺应用广泛,例如在机械零件加工、汽车零件加工、航空航天零件加工等领域都有广泛的应用,目前已经成为现代化生产制造的重要组成部分。
为了加深对数控车削加工工艺的了解,本文将对其原理、工艺特点以及影响加工质量的因素进行分析。
一、数控车削加工的原理数控车削加工采用计算机程序控制旋转切削刃的切入切出轨迹,在由精密控制系统控制旋转刀具和旋转工件期间,以非常高效和准确的方式切割材料,从而精密的完成机械零件的加工过程。
二、数控车削加工的工艺特点1. 具有良好的加工精度,能够加工出高精度的工件。
2. 高效率、高精度的加工速度和工艺性能,可适应不同工件的要求。
3. 可以对复杂的形状进行加工,不受常规工具的限制。
4. 可以进行多种立体加工,将一些复杂的形状在三维环境下加工成工件。
5. 可以进行长周期的连续加工,而且可靠性强。
三、影响加工质量的因素影响数控车削加工工艺质量的因素有很多,在设计和操作过程中需要进行充分考虑和控制,这样才能够保证加工出来的工件有稳定的质量、快速的加工速度、高效的生产效率。
1. 材料的性质材料的性质是决定加工工艺的一个重要因素。
因为不同材料的硬度和韧性特性不同,需要在数控车削加工过程中采用不同的切削参数。
材料越硬,加工难度越大,刀具寿命也会受到影响。
2. 设备选择设备选择是另一个影响加工质量的因素。
不同的数控车削加工设备有不同的处理能力,操作熟练程度也会影响最终的加工质量。
3. 加工环境加工环境是影响加工精度的另一个因素。
加工环境中产生的光、温、震动等因素都会对加工精度产生影响。
尤其是在高精度加工时,需要保持温度和光线等因素尽量稳定,以确保加工精度。
4. 物理和化学参数螺纹角、工件直径、转速、切削宽度等物理参数自然会影响到加工质量,需要根据具体情况调整。
此外,切削液、切削油等物化参数也是影响加工质量的因素,这会直接影响到工具的磨损和寿命。
- 1、下载文档前请自行甄别文档内容的完整性,平台不提供额外的编辑、内容补充、找答案等附加服务。
- 2、"仅部分预览"的文档,不可在线预览部分如存在完整性等问题,可反馈申请退款(可完整预览的文档不适用该条件!)。
- 3、如文档侵犯您的权益,请联系客服反馈,我们会尽快为您处理(人工客服工作时间:9:00-18:30)。
嘉兴职业技术学院
毕业论文
一种零件的数控车削加工工艺分析
学生姓名
学号 103053106
系别机电与汽车分院
专业机电一体化
指导教师
完成日期 2013.05.30
嘉兴职业技术学院
毕业设计综合实践任务书
岗位名称职工
岗位职责负责PLC程序编写以及相关电器电路图的绘制
岗位能力要求熟练掌握PLC编程软件的应用,以及编程指令的作用。
会使用绘图软件CAD 进行电器电路图的绘制。
课题任务名称基于三菱PLC的气动机械手机械手控制系统设计。
本课题完成的条件
1、按照自己所学的机电课程进行设计和开发;
2、永骏机床的工程师和学校辅导老师的帮助下完成此设计。
3、熟练运用PLC编程软件以及电路故障排除。
本课题任务要求
<一> 技术应用设计要求
熟悉机床的机电部分,以及相关台达和西门子的编程说明;
从设计实际需要出发,选择设计方案;
制作完成整个机械手;
撰写试验操作书一份。
<二> 工艺操作技能要求
气动机械手的设计实现,并实际操作通过;
企业现场设备安装、调试、维护、检测等操作实践训练,基本符合企业上岗要求。
设计与论文相关参考文献资料。
<三> 时间安排
1、毕业综合实践单位以及岗位的落实(2013年2月1日开始)
2、上传毕业综合实践任务书(2013年6月1日前)
3、毕业综合实践相关岗位顶岗实习过程并撰写实习周记(2013年3月1日-2013年5月30日期间,每月至少4篇)
<四>周记撰写与系统录入
1、每周登陆系统提交实习周记,内容要求与实习期间工作、生活相关,不少于200字;在实习单位工作满一月后要求提交一份企业所跟师傅或直属领导的评价(20字以上,包含评价人联系方式)。
2、参加或更换实习单位要求一周内登陆系统更新相关信息并主动联系指导教师备案。
嘉兴职业技术学院
机电与汽车分院毕业设计 (论文)开题报告
目录
引言 (6)
1 零件的结构分析 (6)
2 零件设备的选择 (7)
3 确定零件的定位基准和装夹方式 (7)
4确定加工顺序及进给路线 (7)
4.1 加工顺序 (7)
4.2 进给路线 (8)
5 刀具选择 (8)
6 切削用量选择 (8)
7填写数控加工工艺文件 (9)
参考文献 (9)
毕业设计(论文)进程检查评议表 (11)
毕业设计(论文)成绩考评表 (12)
一种零件的数控车削加工工艺及编程
103053106 冯旭辉
嘉兴职业技术学院机电与汽车分院指导教师:周志宏
摘要: 本文根据数控机床的特点,针对具体的零件,进行工艺方案的分析,工装方案的确定,刀具和切削用量的选择,确定加工顺序和加工路线,数控加工程序编制。
通过整个工艺的过程的制定,充分体现了数控设备在保证加工精度,加工效率,简化工序等方面优势。
关键词: 数控工艺分析加工方案加工路线编程
引言
数控机床是数字控制机床的(Computer numerical control machine tools)的简称,是一种装有程序控制系统的的自动化机床。
该控制系统能够逻辑地的处理具有控制编码或其他符号指令规定的程序,并将其译码,从而使机床动作并加工零件。
1 零件的结构分析
(1)零件的结构分析
图1-1 零件图
由图纸可知,该零件表面由圆柱、圆锥、逆圆弧及螺纹等表面组成。
该零件的径向加工部位有Φ85mm圆柱段、Φ80mm圆柱段、Φ62圆柱段、R70圆弧M48×1.5外螺纹。
零件符合数控加工尺寸标注要求,轮廓描述清楚完整,零件材料为45钢,毛坯为Φ85㎜×340㎜棒材。
(2)零件技术要求分析
1)在轮廓曲线上,有一处既过象限又改变进给方向的轮廓曲线,因此在加工时应进行机械间隙补偿,以保证轮廓曲线的准确性。
2)螺纹加工时,为保证其精度,在精车时选择改程序的方法,将螺纹的大径值扩大0.18-0.2mm,加工螺纹时利用螺纹千分尺或螺纹环规保证精度要求。
2 零件设备的选择
数控车床能对轴类或盘类等回转体零件自动地完成内外圆柱面、圆锥表面、圆弧面等工序的切削加工,并能进行切槽、钻、扩等的工作。
根据零件的工艺要求,可以选择经济型数控车床,一般采用步进电动机形式半闭环伺服系统。
此类车床机构简单,价格相对较低,这类车床设置三爪自定心卡盘、普通尾座或数控液压尾座,适合车削较长的轴类零件。
根据主轴的配置的要求选择卧式数控车床。
数控车床具有加工精度高,能做直线和圆弧插补,数控车床刚性良好,制造和对刀精度高,能方便和精确地进行人工补偿和自动补偿,能够加工尺寸精度要求较高的零件。
能加工轮廓形状特别复杂的表面和尺寸难于控制的回转体,而且能比较方便的车削锥面和内外圆柱面螺纹,能够保持加工精度,提高生产效率。
所以对加工时非常有利的。
3 确定零件的定位基准和装夹方式
(1)定位基准
工件的定位与基准应与设计基准保持一致,应防止过定位,对与箱体工件最好选择“一面两销”作为定位基准,定位基准在数控机床上要仔细找正。
图中Φ85㎜外圆不加工,毛坯为Φ85㎜×340,因此以Φ85的外圆和左端面作为定位基准。
(2)装夹方式
在数控车床上工件定位安装的基本原则与普通机床相同。
工件的装夹方法影响工件的加工精度和效率,为了充分发挥数控机床的工作特点,在装夹工件时,应考虑以下几种因素:
1.尽可能采用通用夹具,必须时才设计制造专用夹具;
2.结构设计要满足精度要求;
3.易于定位和装夹;
4.易于切削的清理;
5.抵抗切削力由足够的刚度;
4确定加工顺序及进给路线
4.1 加工顺序
(1)先粗后精先安排粗加工,中间安排半精加工,最后安排精加工和光整加工。
(2)先主后次先安排零件的装配基面和工作表面等主要表面的加工,后安排如键槽、紧固用的光孔和螺纹孔等次要表面的加工。
由于次要表面加工工作量小,又常与主要表面有位置精度要求,所以一般放在主要表面的半精加工之后,精加工之前进行。
(3)先面后孔对于箱体、支架、连杆、底座等零件,先加工用作定位的平面和孔的端面,然后再加工孔。
这样可使工件定位夹紧稳定可靠,利于保证孔与平面的位置精度,减小刀具的磨损,同时也给孔加工带来方便。
(4)基面先行用作精基准的表面,要首先加工出来。
所以,第一道工序一般是进行定位面的粗加工和半精加工(有时包括精加工),然后再以精基面定位加工其它表面。
综上所诉:该零件的加工顺序如下:
先从右到左进行粗车(留0.25mm精车余量),然后从右到左进行精车,最后车削螺纹。
4.2 进给路线
5 刀具选择
(1)选用Φ5mm中心钻钻削中心孔。
(2)粗车和端面选用硬质合金90°右偏刀,为防止副后刀面与工件轮廓干涉,副偏角不宜太小,选K'=35。
(3)精车时选用硬质合金90°右偏刀,车螺纹选用硬质合金 60°外螺纹车刀,刀尖圆弧半径应小于轮廓最小圆角半径,取rε=0.15-0.2mm。
(4)切槽时用切槽车刀
表 1 数控加工刀具卡片
6 切削用量选择
(1)背吃刀量的选择
轮廓粗车循环时选ap=4mm,精车时选ap=0.25;螺纹粗车时选ap=0.4,逐刀减少,精车时选ap=0.1。
(2)主轴转速的选择
主轴转速应根据允许的切削速度和工件(或刀具)直径来选择。
根据本例中零件的加工要求,考虑工件材料为45钢,刀具材料为硬质合金钢,查表1-7所得:粗加工选择转速
400r/min,精加工选择600r/min车削外圆,采用720r/min来车螺纹,而内孔由于刚性较差,采用粗车600 r/min,比较容易达到加工要求,切槽的切削刀较大,采用350 r/min更稳妥。
(3)进给速度
查表1-3、1-4选择粗车、精车每转进给量,再根据加工的实际情况确定粗车每转进给量为0.6mm/r,精车每转进给量为0.15mm/r,最后根据公式vf=nf计算粗车、精车进给速度分别为240mm/min和90mm/min。
7填写数控加工工艺文件
表2 数控加工工艺文件
参考文献
[ 1]詹华西.零件的数控车削加工.电子工业出版社,2011
[ 2] 蔡有杰. 数控编程及加工技术 . 中国电力出版社,2011 . [ 3] 耿国卿. 数控车削编程及加工 .北京:清华大学出版社.2011
毕业设计(论文)进程检查评议表
毕业设计(论文)成绩考评表
注:(1)评分满分为100分,小计以百分制计
(2)按院毕业(论文)评分标准,最后以优秀、良好、合格、不合格记入总评成绩。