典型零件的数控车削编程
数控车床零件的工艺分析及编程典型实例

数控车床零件的工艺分析及编程典型实例更新日期:来源:数控工作室根据下图所示的待车削零件,材料为45号钢,其中Ф85圆柱面不加工。
在数控车床上需要进行的工序为:切削Ф80mm 和Ф62mm 外圆;R70mm 弧面、锥面、退刀槽、螺纹及倒角。
要求分析工艺过程与工艺路线,编写加工程序。
图1 车削零件图1.零件加工工艺分析(1)设定工件坐标系按基准重合原则,将工件坐标系的原点设定在零件右端面与回转轴线的交点上,如图中Op点,并通过G50指令设定换刀点相对工件坐标系原点Op的坐标位置(200,100)(2)选择刀具根据零件图的加工要求,需要加工零件的端面、圆柱面、圆锥面、圆弧面、倒角以及切割螺纹退刀槽和螺纹,共需用三把刀具。
1号刀,外圆左偏刀,刀具型号为:CL-MTGNR-2020/R/1608 ISO30。
安装在1号刀位上。
3号刀,螺纹车刀,刀具型号为:TL-LHTR-2020/R/60/1.5 ISO30。
安装在3号刀位上。
5号刀,割槽刀,刀具型号为:ER-SGTFR-2012/R/3.0-0 IS030。
安装在5号刀位上。
(3)加工方案使用1号外圆左偏刀,先粗加工后精加工零件的端面和零件各段的外表面,粗加工时留0.5mm的精车余量;使用5号割槽刀切割螺纹退刀槽;然后使用3号螺纹车刀加工螺纹。
(4)确定切削用量切削深度:粗加工设定切削深度为3mm,精加工为0.5mm。
主轴转速:根据45号钢的切削性能,加工端面和各段外表面时设定切削速度为90m/min;车螺纹时设定主轴转速为250r/min。
进给速度:粗加工时设定进给速度为200mm/min,精加工时设定进给速度为50mm/min。
车削螺纹时设定进给速度为1.5mm/r。
2.编程与操作(1)编制程序(2)程序输入数控系统将程序在数控车床MDI方式下直接输入数控系统,或通过计算机通信接口将程序输入数控机床的数控系统。
然后在CRT 屏幕上模拟切削加工,检验程序的正确性。
第三讲典型轴类零件数控车削加工工艺及编程

B
准确定位
B
英制O米制OB:基本功能 0:选购功能 数控车设定—— A功能
2. 进给功能(F功能)
F 功能指令用于在程序中控制切削进给量,有两种指令模式: (1)每转进给模式(G99)
编程格式: G99 F ___; F后面的数字表示主轴每转一转刀具的进给量。 单位:mm/r。
说明:模态指令,一经指定直到被G98取代,一直有效。 系统默认状态,车床上一般常用此种进给量指令方式。
A’ 65,2
B’ 10.01,2
C‘ 18.01,-2
D’ 18.01,-20
E‘ 24,-25
F’ 28,-25 G‘ 48.016,-35 H’ 48.016,-51 I‘ 58.023,-51 J‘ 58.023,-58 K’ 62,-58
符号
含义
编程原点
零件外轮廓走刀路线
工序号 程序段号
工步号 加工内容
粗车左端外轮廓,X轴留0.4、 Z轴留0.1精加工余量
精加工左端面外轮廓,各加工 表面符图示要求
审核
产品名称或代号
零件名称
材料 零件图号
XXX
夹具名称
三爪卡盘
刀具号
刀具规格/ (mm)
主轴转速/ (r/min)
T01
25×25
粗600 精1000
螺纹轴
45钢
XXX
使用设备
车间
CK6132
数控车
进给速度/ 背吃刀量/ 备注 (mm/r) (mm)
恒转速控制 编程格式: S ~
S后面的数字表示主轴转速,单位: r/min。
注意:
在具有恒线速功能的机床上, S 功能指令可限制主轴最高转速
(1)主轴最高转速限制(G50)
轴类零件数控车削的工艺分析及编程

螺纹及倒角等表 面组成 ,其 中多个 直径 尺寸与轴 向尺 寸有 较 高 的尺寸精度要求。 件图尺寸标注完整 , 零 符合数 控加工尺寸 标注要求 ; 轮廓 描述清楚完整 ; 零件材料 为 4 5钢 , 切削加 工性 能较好 , 热处 理和硬度要求。零件图样上带公差 的尺寸 , 无 因 公差值较小 , 编程 时不必取其平均值 , 故 而取 基本尺寸 即工 质量和提高生 产率 的重要 环节 。粗车 时选 用强度高 、 耐磨度好 的刀具 , 以满
足大 背吃刀量 、 大进 给量 的要求 ; 车时 选用精度 高 、 精 耐磨度 好 的刀具 , 以保证 精度的要求 。根据零件 的外形 和加工要求 ,
选 用 选 用 4把 刀 :
量 的选择 原则 是 : 保证零件加 工精度和表 面粗糙 度 , 分发 挥 充
作者简介 : 芳(93 )女 , 廖 16一 , 广西南 宁人 , 讲师 。 研究方 向为数控加工技术 。
14 O
《 装备制造技术} 00 2 1 年第 4 期
刀具切削性 能 , 保证 合理 的刀具耐用度 ; 充分发挥机床 的性 并 能, 最大 限度提 高生产率 , 降低 成本 。根据 本例 中零件 的加工
心线为工艺基准 ,使用 三爪 自动定心卡盘夹住 3 m外 圆 0m
一
路线等 , 按规定 的代码格 式编制成 数控加工程序 , 数控车床在 程序的控制下 , 自动加工 出各种形 状不同的零件。轴类 零件是
各种机械设备 中最主要和最基本 的典 型零 件 ,本文 以轴类零 件为例 , 对数控车削加工 中的工艺分析及 编程做 些探讨。
重要设 备 , 已广泛应 用于机械 加工中。在数控车削加 工前 , 要 对所加 工的零件进行工艺分析 , 定正确的加工方案 , 确 将车床
数控车床典型零件加工实例
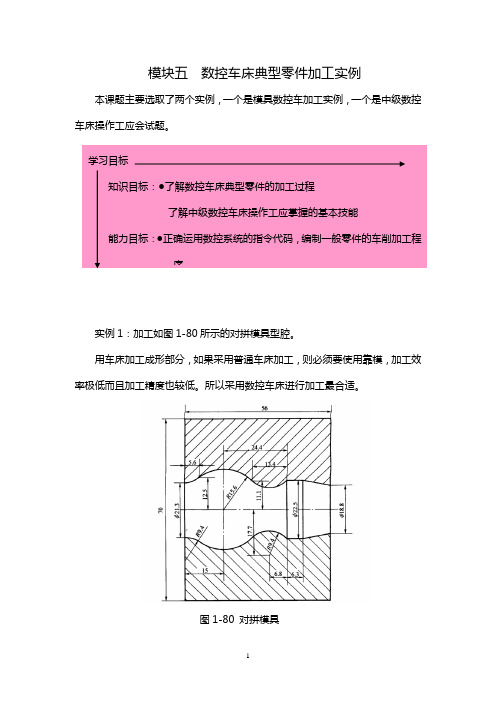
模块五数控车床典型零件加工实例本课题主要选取了两个实例,一个是模具数控车加工实例,一个是中级数控车床操作工应会试题。
学习目标知识目标:●了解数控车床典型零件的加工过程了解中级数控车床操作工应掌握的基本技能能力目标:●正确运用数控系统的指令代码,编制一般零件的车削加工程序。
实例1:加工如图1-80所示的对拼模具型腔。
用车床加工成形部分,如果采用普通车床加工,则必须要使用靠模,加工效率极低而且加工精度也较低。
所以采用数控车床进行加工最合适。
图1-80 对拼模具1.加工准备1)将两拼块分别加工成形。
2)在两拼块上装导钉,一端与下模板过渡配合,另一端与上模板间隙配合。
3)两拼块合装后外形尺寸磨正,对合平面磨平并保证两拼块厚度一致。
4)在花盘上搭角铁,将下模板固定在角铁上,拼合上模板并压紧,用千分表校正后固定角铁,安装示意图如图1-81所示。
图1-81 安装示意图2.所需刀具本工件需要通过钻孔、粗车、精车三个工步加工,钻孔时采用在尾架上装夹φ16mm的钻头手动进给,而粗车和精车则采用自动运行的办法。
粗车时用55°的内孔车刀,刀具号为T01,刀补号为01;精车时用35°的内孔车刀,刀具号为T02,刀补为02。
3.编写加工程序N10 M03 S500N20 T0101N30 G00 X0 Z3.0N40 G01 Z-30.0 F0.5N60 G01 Z-57.0N70 G00 X0N80 G00 Z-31.6N90 G01 X24.4 F0.2N100 G01 Z-50.4N110 G00 X0N120 Z3.0N130 G01 X18.3 Z3.0 F0.3N140 Z0N150 X22.0 Z-10.1N160 W-6.3N170 G02 X21.7 W-13.4 I6.45 J-6.8 N180 G03 X24.5 Z-50.4 I-11.1 J-11.0 N190 GO2 X20.8 Z-56.0 I7.55 J-5.6 N200 G01 X0N210 G00 Z200.0N220 G00 X200.0 T0100N230 T0202N240 G00 Z3.0N250 G01 X18.8 Z3.0 F0.3N260 Z0N280 W-6.3N290 G02 X22.2 W-13.4 I6.45 J-6.8N300 G03 X25.0 Z-50.4 I-11.1 J-11N310 G02 X21.3 Z-56.0 I7.55 J-5.6N320 G01 Z-58.0N330 G00 X0N340 G00 Z100.0N350 G00 X200.0 T0200N360 M05N370 M304.加工过程1)在尾架上装φ16mm的钻头,手动进给钻穿工件。
数控车床典型零件编程与仿真加工

实践与探索Exploration数控车床典型零件编程与仿真加工文/张耀明 唐六元定要事先考虑周全,设计好软、硬件交换方案,准确无误后再进行交换检查。
(8)特殊处理法。
当今的数控系统已进入PC基、开放化的发展阶段,其中软件含量越来越丰富,有系统软件、机床制造者软件,甚至还有使用者自己的软件,由于软件逻辑的设计中不可避免的一些问题,会使得有些故障状态无从分析,例如死机现象。
对于这种故障现象则可以采取特殊手段来处理,比如整机断电,稍作停顿后再开机,有时此法可能将故障消除。
维修人员可以在自己的长期实践中摸索其规律或者采取其他有效的方法。
二、电气维修与故障的排除 电气故障的分析过程也就是故障的排除过程。
因此电气故障的一些常用排除方法在上述的分析方法中已综合介绍过了,下面列举几个常见电气故障供维修者参考。
1.电源故障电源是维修系统乃至整个机床正常工作的能量来源,它的失效或者故障,轻者会丢失数据,重者会造成停机重者会毁坏系统局部甚至全部。
发达国家由于电力充足,电网质量高,因此其电气系统的电源设计考虑较少,这对于我国有较大波动和高次谐波的电力供电网来说就略显不足,再加上人为因素,难免出现由电源而引起的故障。
2.数控系统位置环故障 (1)位置环报警。
可能是位置测量回路开路、测量元件损坏、位置控制建立的接口信号不存在等。
(2)坐标轴在没有指令的情况下产生运动。
可能是漂移过大、位置环或速度环接成正反馈、反馈接线开路、测量元件损坏。
3.机床坐标找不到零点可能是零方向在远离零点、编码器损坏或接线开路、光栅零点标记移位、回零减速开关失灵。
4.机床动态特性变差如果机床动态特性变差,工件加工质量下降,甚至在一定速度下机床发生振动。
这其中有很大一种可能是机械传动系统间隙过大甚至磨损严重,或者导轨润滑不充分甚至磨损造成的。
对于电气控制系统来说则可能是速度环、位置环和相关参数已不在最佳匹配状态,应在机械故障基本排除后重新进行最佳化调整。
典型轴类零件加工与软件编程

典型轴类零件加工与软件编程江苏工贸08技师摘要:轴类零件是各种机械设备中最主要最基础的典型零件,本文通过对典型轴类零件加工工艺分析,从装夹、刀具选择、切削用量、精度控制、软件使用等方面对零件批量生产工作进行优化,从而提高生产效率。
关键词:【轴类零件】、【数控车削】、【工艺分析】一、机械图纸分析1)以图1所示工件为基础,在数控车床上加工时应首先进行图纸分析,确定加工内容图12)图纸分析根据图纸标示,该零件长度160mm,最大直径56mm,材料选用45号碳素钢,故毛坯选用φ60×165尺寸,零件含有梯形螺纹、椭圆、V形槽等要素。
该零件的加工有一定精度要求,有一定加工难度表一二、工艺方案分析2.1 机床选择及装夹分析采用CK6140数控车床加工该零件夹具采用数控车床上最常用的三抓自定心卡盘,需调头装夹一次来完成整个零件的加工。
首先加工工件右端至V形槽结素,掉头装夹,加持φ44台阶轴,但因为加持部分较短工件在加工过程中会产生震动影响工件同轴度,并且可能出现加工事故。
所以在加工工件左端时应实用顶尖,进行一夹一顶的装夹方式,保证同轴度。
2.2 刀具选择与普通机床相比,数控车床对刀具要求更高,不仅要求刚性好,精度高,而且要求尺寸稳定、耐用度好、排屑断屑性能好,同时要求安装调整方便、以满足数控机床的高速切削。
对于本例中工件加工选择刀具,分别为:1、端面车刀--T01012、 45°外圆车刀--T02023、宽度为5mm的外切槽刀--T03034、 30°外梯形螺纹刀—T04042号刀用来加工外圆,因采用较大角度的刀具在加工椭圆时会产生干涉,影响工件形状精度故而选择45°外圆车刀以保证精度2.3 切削用量的选择数控编程时编程人员必须确定每道工序的切削用量并以指令的形式写入程序序中。
切削用量包括切削速度、进给速度及背吃刀量等。
对于不同加工方法,需要选用不同的切削用量。
切削用量的选择原则是:保证零件加工精度和表面粗糙度,充分发挥刀具切削性能,保证合理的刀具耐用度;并充分发挥机床的性能,最大限度提高生产率,降低成本。
典型零件外轮廓的数控车削
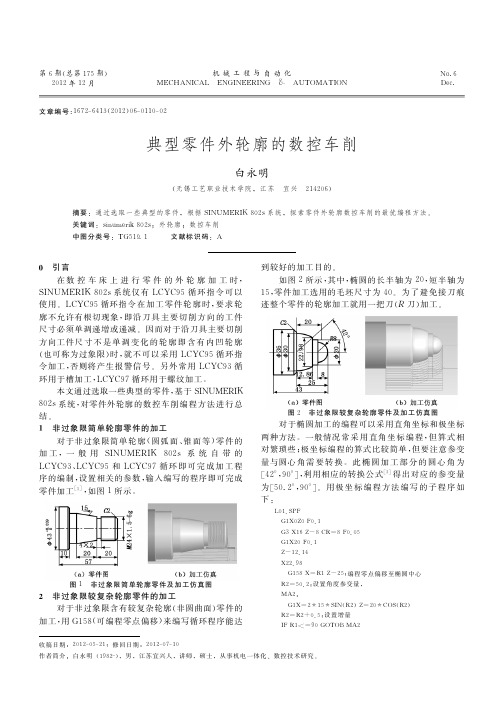
摘要:通过选取一些典型的零件,根据 SINUMERIK 802s系统,探索零件外轮廓数控车削的最优编程方法。 关 键 词 :sinumerik 802s; 外 轮 廓 ; 数 控 车 削 中 图 分 类 号 :TG519.1 文 献 标 识 码 :A
0 引 言 在数 控 车 床 上 进 行 零 件 的 外 轮 廓 加 工 时,
本文通过选取一些典型的零件,基于 SINUMERIK 802s系统,对零件外轮廓 的 数 控 车 削 编 程 方 法 进 行 总 结。 1 非 过 象 限 简 单 轮 廓 零 件 的 加 工
对于非过象限简单 轮 廓 (圆 弧 面、锥 面 等)零 件 的 加 工,一 般 用 SINUMERIK 802s 系 统 自 带 的 LCYC93、LCYC95 和 LCYC97 循 环 即 可 完 成 加 工 程 序 的 编 制 ,设 置 相 关 的 参 数 ,输 入 编 写 的 程 序 即 可 完 成 零 件 加 工 [1],如 图 1 所 示 。
15,零件加工选用的毛坯尺寸为 40。 为 了 避 免 接 刀 痕 迹整个零件的轮廓加工就用一把刀(R 刀)加工。
图 2 非 过 象 限 较 复 杂 轮 廓 零 件 及 加 工 仿 真 图
数控车床基本编程指令

数控车床基本编程指令
数控车床(Computer Numerical Control Lathe)的基本编程指令通常是用来描述加工轴向、径向、切削速度、进给速度等方面的操作。
下面是一些常见的数控车床基本编程指令:
G代码:用于指定不同的功能和动作。
例如:
G00:快速定位
G01:直线插补
G02:圆弧顺时针插补
G03:圆弧逆时针插补
G04:暂停(延时)
G28:回零点
G71:开启公制单位
G72:开启英制单位
M代码:用于控制机床的辅助功能和动作。
例如:
M03:主轴正转
M04:主轴反转
M05:主轴停止
M08:冷却液开启
M09:冷却液关闭
M30:程序结束
X、Y、Z轴坐标控制:用于控制工件在不同轴向上的移动。
例如:
X10.0:将X轴移动到坐标10.0处
Y5.0:将Y轴移动到坐标5.0处
Z-2.0:将Z轴移动到坐标-2.0处
F代码:用于设定进给速度(切削速度)。
例如:
F100:设定进给速度为每分钟100毫米(或英寸)
S代码:用于设定主轴转速。
例如:
S1000:设定主轴转速为每分钟1000转
T代码:用于选择工具。
例如:
T0101:选择编号为0101的刀具
这些是最基本的数控车床编程指令,实际上还有更多用于高级功能和特定应用的指令。
正确理解和使用这些指令对于确保数控车床操作的准确性和效率至关重要。
- 1、下载文档前请自行甄别文档内容的完整性,平台不提供额外的编辑、内容补充、找答案等附加服务。
- 2、"仅部分预览"的文档,不可在线预览部分如存在完整性等问题,可反馈申请退款(可完整预览的文档不适用该条件!)。
- 3、如文档侵犯您的权益,请联系客服反馈,我们会尽快为您处理(人工客服工作时间:9:00-18:30)。
典 型 零 件 的 数 控 车 削 编 程 举 例
若假想刀尖加工如图3-74所示工件轮廓AB移动,即P1P2与AB 重合,并按AB尺寸编程,则必然产生图a中欠切的区域ABCD,造 成残留误差。因此按图b所示,使车刀的切削点移至AB,并沿AB 移动,从而可避免残留误差,但这时假想刀尖轨迹P3P4与轮廓在X 方向和Z方向分别产生误差ΔX和ΔZ。
典 型 零 件 的 数 控 车 削 编 程 举 例
图3-76 按刀尖圆弧中心轨迹编程
典 型 零 件 的 数 控 车 削 编 程 举 例
(2)具有刀具半径补偿功能的系统补偿 在现在高级的数控车床控制系统,为使编程简单方便,数控车床一般 都设置了刀尖圆弧半径补偿功能,而且可以根据刀尖的实际情况,选择刀 位点轨迹,编程和补偿都十分方便。对于具有刀具半径补偿功能的数控系 统,在编程时,只要按零件的实际轮廓编程即可,而不必按照刀具中心运 动轨迹编程。使用刀具半径补偿指令,并在控制面板上手工输入刀具半径, 数控装置便能自动地计算出刀具中心轨迹,并按刀具中心轨迹运动。即执 行刀具半径补偿后,刀具自动偏离工件轮廓一个刀具半径值,从而加工出 所要求的工件轮廓。
从以上分析可以看出,数控系统进行刀具位置补偿,就是用刀补 值对刀补建立程序段的增量值进行加修正,对刀补撤销段的增量值 进行减修正。 这里的1号刀是标准刀,我们只要在加工前输入与标准刀的差I∆、K∆ 就可以了。在这种情况下,标准刀磨损后,整个刀库中的刀补都要 改变。为此,有的数控系统要求刀具位置补偿的基准点为刀具相关 点。因此,每把刀具都要输入I∆、K∆,其中I∆、K∆是刀尖相对刀具相 关点的位置差(图3-71)。
图3-70
刀具位置补偿示意
如图3-70所示,车床的刀架 装有不同尺寸的刀具。设图示刀 架的中心位置为各刀具的换刀点, 并以l号刀具的刀尖B点为所有刀 具的编程起点。 当换2号刀具加工时,2号刀 具的刀尖在C点位置,要想运用A、 B两点的坐标值来实现从C点到A 点的运动,就必须知道B点和C点 的坐标差值,利用这个差值对B 到A的位移量进行修正,就能实 现从C到A的运动。
图3-71 刀具位置补偿
按基准刀尖编程
按刀架中心编程
当前车刀 刀架转位
X1
基准 车刀
磨损补偿 Zm
Xm
几何补偿
Xj
Z1
X 2
Zj
Z2
典 型 零 件 的 数 控 车 削 编 程 举 例
2.刀具半径补偿 (1)不具备刀具半径补偿功能的系统补偿 在通常的编程中,将刀尖看作是一个点,然而实际数 控切削加工中为了提高刀尖的强度,降低加工表面粗糙度, 刀尖处成圆弧过渡刃。在切削内孔、外圆及端面时,刀尖 圆弧不影响其尺寸、形状,但在切削锥面和圆弧时,则会 造成过切或少切现象(见图3-72)。此时可以用刀尖半径 补偿功能来消除误差。 简易数控系统不具备半径补偿功能,因此,当零件精度 要求较高且又有圆锥或圆弧表面时,要么按刀尖圆弧中心 编程,要么在局部进行补偿计算,来消除刀尖半径引起的 误差。
图3-72
刀尖圆弧产生过切和少切的现象
典 型 零 件 的 数 控 车 削 编 程 举 例
1)按假想刀尖编程加工锥面 数控车床总是按“假想刀尖”点来对刀,使刀尖位置与程序中的起 刀点(或换刀点)重合。所谓假想刀尖如图3-73所示,b为圆头车刀, P点为圆头刀假想刀尖,相当于a图中尖头刀的刀尖点。
图3-73 圆头车刀刀尖半径和假象刀尖
典型零件的数控车削编程
1 数控车床刀具补偿
典 型 零 件 的 数 控 车 削 编 程 举 例
数控机床中刀具补偿有两种:刀具位置尺寸补偿和刀具半径尺寸 补偿。 1.刀具位置补偿 当采用不同尺寸的刀具加工同一轮廓尺寸的零件,或同一名义尺 寸的刀具因换刀重调、磨损以及切削力使工件、刀具、机床变形引起 工件尺寸变化时,为加工出合格的零件,必须进行刀具位置补偿。
(a) 补偿前产生过切现象 (b)加入补偿后的切削 图3-74圆头车刀加工锥面补偿示意图
典 型 零 件 的 数 控 车 削 编 程 举 例
2)按假想刀尖编程加工圆弧 如果按假想刀尖编程车削半径为R的凸凹圆弧表面AB时,会出 现如图3-75所示的情况。图中(a)为车削半径为R的凸圆弧,由于 r的存在,则刀尖P点所走的圆弧轨迹并不是工件所要求的圆弧形状。 其圆心为“O‘”,半径为“R+r”,此时编程人员仍按假想刀尖P 点进行编程,不考虑刀尖圆弧半径的影响,即粗实线轮廓应按图中 虚实线参数进行编程。但要求加工前应在刀补拔码盘上给 z向和x 向分别加一个补偿量r。同理,在切削凹圆弧,如图3-75(b)时, 则在x向和z向分别减一个补偿量r。
典 型 零 件 的 数 控 车 削 编 程 举 例
(a)凸圆弧加工 (b)凹圆弧加工 图3-75 圆头车刀加工凸凹圆弧刀补示意图
典 型 零 件 的 数 控 车 削 编 程 举 例
3)按刀尖圆弧中心轨迹编程 不具备刀具半径补偿功能的数控系统,除按假想刀尖轨迹数据编 程外,还可以按刀心轨迹编程。如图4-76所示手柄零件是由3段凸圆 弧和凹圆弧构成的,这时可用轮廓虚线轨迹所示的3段等距线迹进行 编程,即O1圆半径为R1+r,O2圆半径为R2+t,O3圆半径为R3-r,三 段圆弧的终点坐标由等距的切点关系求得。这种方法编程比较直观, 常被使用。
典 型 零 件 的 数 控 车 削 编 程 举 例
利用机床自动进行刀尖半径补偿时,需要使用G40、G41、G42指令。 当系统执行到含T代码的程序指令时,仅仅是从中取得了刀具补偿的 寄存器地址号(其中包括刀具几何位置补偿和刀具半径大小),此时并不会 开始实施刀尖半径补偿。只有在程序中遇到G41、G42、G40指令时,才开 始从刀库中提取数据并实施相应的刀径补偿。
2 典型零件的数控车削编程举例
典 型 零 件 的 数 控 车 削 编 程 举 例
一、典型零件数控车削编程的步骤: 1、零件图样分析 2、加工工艺性分析(含基点、节点坐标的计算及
编程原点的确定)
3、确定工序和装夹方式 4、选择刀具和确定走刀路线
5、选择切削用量