发动机_变量泵功率匹配极限负荷控制
液压挖掘机功率匹配控制系统

液压挖掘机功率匹配控制系统摘要:液压挖掘机的功率控制是目前各主机厂的重点研究方向,也是挖掘机控制的核心问题。
本文从分析发动机工作特性出发,从转速反馈控制、压力反馈控制两方面对液压挖掘机功率控制系统进行了阐述。
两种反馈手段综合运用的方式,克服了但一方式的不足,整合了两者的优点,使整个控制系统更加成熟合理。
关键词:挖掘机;功率匹配;全功率;控制系统1 前言挖掘机在工作过程中,当遇到大负载时,会使发动机转速急剧下降,严重时甚至造成发动机熄火,影响系统的稳定性和发动机的寿命。
同时由于实际施工中负载变化非常剧烈和频繁,司机需要手动将油门开度调大,这虽然能解决大负载下发动机掉速的问题,但在轻载时却出现“大马拉小车”的情况,极大地浪费了能源。
所以对挖掘机而言,功率匹配控制不仅要具有准确性,达到“极限负荷匹配控制”状态,即发动机根据负载提供功率,同时要具有跟随性,能动态地根据负载变化实时改变发动机功率的输出。
有效地使发动机和液压传动系统与外部负荷之间始终保持最合理的匹配,进而提高能量利用率,是挖掘机控制系统的核心问题。
液压系统与发动机功率匹配系统性能不仅受发动机、液压元件自身性能的影响,而且还取决于各部分元件参数之间的合理匹配。
本文主要从发动机——泵的匹配控制方面对挖掘机功率控制系统进行阐述。
2 发动机工作特性曲线发动机作为挖掘机的动力系统,对其特性的研究直接关系到控制性能的好坏。
以下从发动机的外特性曲线及万有特性曲线对发动机特性进行阐述。
2.1 发动机外特性曲线图1是发动机外特性曲线图,图中曲线ABCD是发动机全负荷速度特性曲线,横坐标为发动机转速,纵坐标为发动机扭矩。
图中A、B、C、D点分别表示各个油门开度状态下对应的最大功率输出点。
图1 发动机外特性曲线图斜线1、2、3、4分别表示不同油门开度时的调速特性。
因为每一个油门位移S,对应一个最大功率输出点,所以两者存在映射关系,可用函数表示为Nm(M,n)=f1(S)因此选择不同的油门位移S,即选择了不同的功率模式。
基于全局功率匹配的液压挖掘机电控节能技术的研究

基于全局功率匹配的液压挖掘机电控节能技术的研究重庆大学硕士学位论文(学术学位)学生姓名:杨虎指导老师:陈进教授专业:机械设计及理论学科门类:工学重庆大学机械工程学院二O一三年五月Research on Energy-saving Technology of Electronic Control for Hydraulic Excavator Based on Global Power MatchingA Thesis Submitted to Chongqing Universityin Partial Fulfillment of the Requirement for theMaster’s Degree of EngineeringByYang HuSupervised by Prof. Chen JinSpecialty:Mechanical Design and TheoryCollege of Mechanical Engineering of ChongqingUniversity, Chongqing, ChinaMay, 2013中文摘要摘要液压挖掘机是一种高能耗的重要工程机械,应用十分广泛,在国民建设中占有重要地位。
我国自主研发的液压挖掘机的技术相对落后,其发动机功率利用率较低,能量损失较大,导致挖掘机整机工作效率降低,经济性能较差。
因此研究挖掘机的节能控制技术具有重要的工程实际意义。
目前,挖掘机节能技术应用较多的是发动机-泵和泵-负载的功率匹配控制,但是两者都是通过调节液压泵的排量来实现局部功率匹配,所以,两个环节的控制相互干涉,不能协调统一。
针对此种情况,论文基于发动机-液压系统-负载的全局功率匹配,研发液压挖掘机的电控节能技术,主要进行了如下几个方面的工作:①通过分析挖掘机的传动系统及能量传递路线,找出其能量损失途径,指出除了不可避免的损失外,大部分是由于发动机-液压系统-负载之间的功率匹配不合理造成的能量损失。
工程机械中的泵与发动机匹配
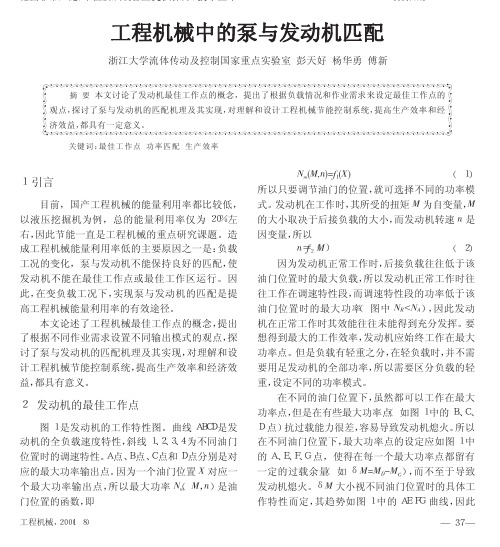
工程机械,2001(8)范围非常广泛,不但要从设备上提供保障,技术上不收稿日期1引言目前,国产工程机械的能量利用率都比较低,以液压挖掘机为例,总的能量利用率仅为20%左右,因此节能一直是工程机械的重点研究课题。
造成工程机械能量利用率低的主要原因之一是:负载工况的变化,泵与发动机不能保持良好的匹配,使发动机不能在最佳工作点或最佳工作区运行。
因此,在变负载工况下,实现泵与发动机的匹配是提高工程机械能量利用率的有效途径。
本文论述了工程机械最佳工作点的概念,提出了根据不同作业需求设置不同输出模式的观点,探讨了泵与发动机的匹配机理及其实现,对理解和设计工程机械节能控制系统,提高生产效率和经济效益,都具有意义。
2发动机的最佳工作点图1是发动机的工作特性图。
曲线ABCD是发动机的全负载速度特性,斜线1、2、3、4为不同油门位置时的调速特性。
A点、B点、C点和D点分别是对应的最大功率输出点。
因为一个油门位置X 对应一个最大功率输出点,所以最大功率N m (M ,I )是油门位置的函数,即N m (M,I >=f 1(X >(1)所以只要调节油门的位置,就可选择不同的功率模式。
发动机在工作时,其所受的扭矩M 为自变量,M 的大小取决于后接负载的大小,而发动机转速I 是因变量,所以I =f 2(M )(2)因为发动机正常工作时,后接负载往往低于该油门位置时的最大负载,所以发动机正常工作时往往工作在调速特性段,而调速特性段的功率低于该油门位置时的最大功率(图中N R !N ),因此发动机在正常工作时其效能往往未能得到充分发挥。
要想得到最大的工作效率,发动机应始终工作在最大功率点。
但是负载有轻重之分,在轻负载时,并不需要用足发动机的全部功率,所以需要区分负载的轻重,设定不同的功率模式。
在不同的油门位置下,虽然都可以工作在最大功率点,但是在有些最大功率点(如图1中的B、C、D点)抗过载能力很差,容易导致发动机熄火。
关于液压挖掘机全功率泵的动力匹配
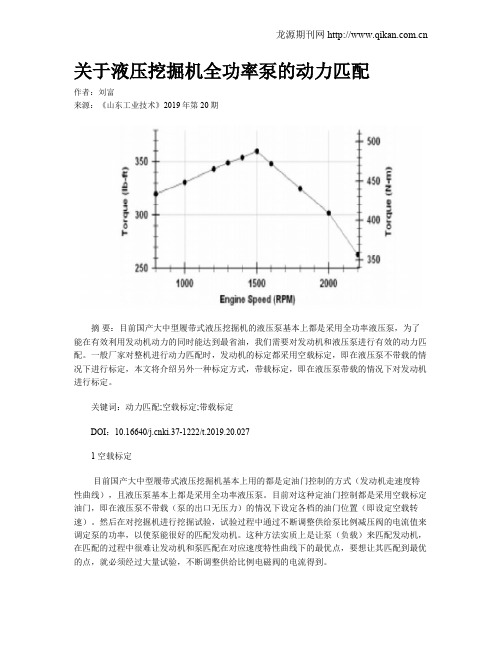
关于液压挖掘机全功率泵的动力匹配作者:刘富来源:《山东工业技术》2019年第20期摘要:目前国产大中型履带式液压挖掘机的液压泵基本上都是采用全功率液压泵,为了能在有效利用发动机动力的同时能达到最省油,我们需要对发动机和液压泵进行有效的动力匹配。
一般厂家对整机进行动力匹配时,发动机的标定都采用空载标定,即在液压泵不带载的情况下进行标定,本文将介绍另外一种标定方式,带载标定,即在液压泵带载的情况下对发动机进行标定。
关键词:动力匹配;空载标定;带载标定DOI:10.16640/ki.37-1222/t.2019.20.0271 空载标定目前国产大中型履带式液压挖掘机基本上用的都是定油门控制的方式(发动机走速度特性曲线),且液压泵基本上都是采用全功率液压泵。
目前对这种定油门控制都是采用空载标定油门,即在液压泵不带载(泵的出口无压力)的情况下设定各档的油门位置(即设定空载转速)。
然后在对挖掘机进行挖掘试验,试验过程中通过不断调整供给泵比例减压阀的电流值来调定泵的功率,以使泵能很好的匹配发动机。
这种方法实质上是让泵(负载)来匹配发动机,在匹配的过程中很难让发动机和泵匹配在对应速度特性曲线下的最优点,要想让其匹配到最优的点,就必须经过大量试验,不断调整供给比例电磁阀的电流得到。
2 带载标定我想介绍另一种匹配方式,它能很快使发动机和泵匹配在对应速度特性曲线下的最优点,能在全功率液压泵进入恒功率区后使发动机的负荷率达到最大,这样便能在充分发挥发动机动力的同时达到最省油。
这种匹配方式叫带载油门标定。
首先根据泵的P-Q曲线图,设定工作时泵所要达到的目标转速(非空载转速),同时设定此转速下需要向泵的比例电磁阀供给多少电流,将转速和电流都在控制器里设定好。
在油门标定的过程中,让控制器将设定好的每个档位的电流供给液压泵的比例减压电磁阀,同时操作操纵手柄使前后泵都达到溢流,这时液压泵进入对应电流的恒功率区。
根据全功率泵的扭矩曲线可知,一旦泵进入恒功率,泵的扭矩及功率便达到最大,而且近似恒定(全功率泵的特性决定)。
发动机_变量泵功率匹配极限负荷控制
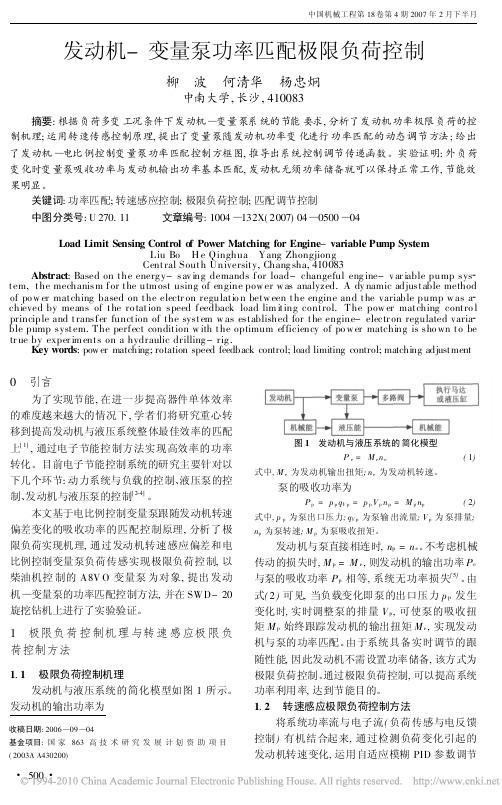
P e = Mene
( 1)
式中, M e 为发动机输出扭矩; ne 为发动机转速。
泵的吸收功率为
Pp = p p qV p = p p V p np = M p np
( 2)
式中, p p 为泵出口压力; qV p 为泵输 出流量; V p 为 泵排量;
np 为泵转速; M p 为泵吸收扭矩。
发动机与泵直接相连时, np = ne。不考虑机械
器, 通 过 自 适 应 模 糊
PID 参数整定[ 7] , 获得 控制 A8VO 泵 排量的
图 3 极限负荷 控制原理框图
电液比例减压阀的最优调节参数, 输出比例压力
控制信号, 调节控制变量缸的比例方向压力控制
阀的开口度大小, 改变变量缸驱动压力的大小和
方向, 最大限度吸收发动机功率而又保证发动机
1 极限负荷控制机理与转速感应极限负 荷控制方法
1. 1 极限负荷控制机理 发动机与液压系统的简化模型如图 1 所示。
发动机的输出功率为
收稿日期: 2006 09 04 基金项目: 国 家 863 高 技 术 研 究 发 展 计 划 资 助 项 目 ( 2003A 发动机与液压系统的 简化模型
0 引言
为了实现节能, 在进一步提高器件单体效率 的难度越来越大的情况下, 学者们将研究重心转 移到提高发动机与液压系统整体最佳效率的匹配 上[ 1] , 通过电子节能控制方法实现高效率的功率 转化。目前电子节能控制系统的研究主要针对以 下几个环节: 动力系统与负载的控制、液压泵的控 制、发动机与液压泵的控制[ 2 4] 。
A8VO 变量双泵调节原理如下( 以 1 号泵为 例, 下同) : 由负荷传感反馈到泵的 x 3 控制口的压 力 p x 3 和泵的出口压力 p b 控制变量缸的比例方向 压力控制阀开口度大小, 左位( 变量缸 1 无杆腔接
工程机械液压传动系统形式—变量泵的控制方式

功
率
曲
线
P有一个最大值,为溢流阀预设
定的压力值
Q有一个最大值,为液压泵最大
流量值
任一点的功率(N=PQ)始终不
变(恒功率)
2. 液压泵功率控制曲线
双
泵
合
流
总功率等于分泵功率之和
分泵可以单独控制,也可以互控
有总功率变量和分功率变量两种形式
3. 总功率控制
3.1 总功率控制目的
• 负荷传感压力Pls为系统的最高
负荷,由梭阀链选取
2. 负荷传感(LS)控制工作原理
• 主控阀为中位常闭
•
•
•
•
•
•
•
•
Q=KA√∆ ,∆=Pp-Pls
LS阀阀芯受力情况
液压泵输出压力Pp
负荷传感压力Pls
弹簧力Pk
Pk=ΔP=Pp-Pls
调节弹簧预压力Pk,可调整ΔP
一般取ΔP=2.2MPa左右
压力增大而增大,呈正比关
系
• 先导控制压力P↑,则输出流
量↑
第36页
2. 正流量控制信号采样点
• 先导控制压力Pi采用操纵阀
的先导控制阀油压
• 先导泵输出液压油经先导阀
输出后,一部分去控制主阀,
另一部分用来控制液压泵变
量机构
• 先导控制压力Pi为各先导油
中的最高压力
第37页
3. 正流量控制工作原理
Pk=ΔP=Pp-Pls
②主控阀动作
如果主控阀开度变大
动态∆P减小
LS阀阀芯左移活塞右移
排量增大
2. 负荷传感(LS)控制工作原理
•
•
变量泵变量调节与控制技术恒功率310-3

3.4.5 LR.D带压力控制的恒功率控制
压力控制阀的可变阀口与固定节流孔5组成了一个C型半桥, 用来控制变量泵活塞腔的压力。 在无压工况,泵处在排量最大Vgmax的初始位置。 这种控制方式,压力控制优先于功率控制,也就是在工作压力 低于设定压力情况下,变量泵变量控制装置跟随功率控制功能。 一旦泵的输出压力达到了压力控制设定值,此时压力阀 4下位 工作,泵出口压力油经阀口进入变量活塞的右腔,使泵的排量 减少,泵进入压力控制模式,并仅仅输送所需要的流量来保持 这个压力。 一般这个压力有一个设定范围,标准的设定值为 35MPa 。 也就是如果工作压力不超过 35MPa,为恒功率泵,一旦压力超 过了 35MPa ,就为恒压泵,其输出特性曲线参见图 3-46。其中 功率变量的起始点由功率控制阀 2 的弹簧调定,最高的工作压 力由压力阀4的弹簧调定。
a)特性曲线
a) b) 图3-44 LR3 静态特性曲线 b) 先导压力和功率之间的关系
3.4.5 LR.D带压力控制的恒功率控制
压力控制 35 变量起始点 恒功率控制
/MPa 压力设定范围
工作压力 p
2 0
Vgmin
排量
Vgmax
图3-46 LR.D 静态特性曲线
压力控制优先于功率控制
图3-45 LR.D调节原理职能原理图
3.4.3全功率控制,分功率控制,交叉功率控制
3.4.3全功率控制,分功率控制,交叉功率控制 交叉功率控制 由于分功率变量系统只是两个液压泵的简单组合,每一个液 压泵最多吸收柴油机50%的功率,当一个液压泵工作于起调压力之 下时,另外一个液压泵却不能吸收柴油机空余出来的功率。针对 此缺点,在分功率系统基础上,出现了交叉功率控制。交叉功率 控制从原理上讲是一种全功率调节,与上述全功率控制不同的是 两个液压泵的排量可以不同。通过交叉连接配置,两个液压泵的 工作压力互相作用在对方的调节器上,每个液压泵的输出流量不 仅与自身的出口压力有关,还与另一液压泵的出口压力有关。如 果一台液压泵不工作或者以小于50%的总驱动功率工作,则第二台 液压泵自动地利用剩余的功率,在极端情况下可达到100%总驱动 功率。交叉功率控制既具有根据每一液压泵的负载大小调整液压 泵输出的能力,又能充分利用柴油机的功率。
工程机械液压系统四种控制技术

工程机械液压系统四种控制技术液压系统动力匹配及控制技术在国外起步较早,发展较快,很多技术在国外使用后很快进入中国市场,目前国内主要停留在引进-模仿阶段,并没有自己的专有技术。
1、定量泵设计方法在早期的工程机械系统设计中,采用定量泵设计的原则是:系统的最大工作流量(Q)与最大工作压力(P)的乘积即系统的最大输出功率(N)不能超出柴油机额定功率(Nj)。
但在一般工况下功率利用系数太低,且无法施展较强的控制功能,因而性能不佳。
目前在小吨位(5~50t)汽车起重机和随车起重机等产品中仍在使用。
2、单泵恒功率控制技术在单泵控制系统中,一般通过变量控制机构实现对变量泵排量的控制,在最早的恒功率控制技术中,通过对变量机构两根弹簧弹力的不同设定,能实现对变量泵输出流量的控制,其工作曲线为折线,当系统压力达到第一根弹簧设定力后,变量泵排量开始减小。
当系统压力克服第二根弹簧设定力后,变量泵变量曲线斜度发生变化。
通过以上控制,使其变量曲线上P、Q乘积的离散值趋近于常数C。
通过以上控制大大提高了柴油机功率的利用系数,又能保证柴油机不会因过载熄火。
力士乐公司开发的恒功率控制技术中,通过杠杆原理对变量控制机构进行了改进,使其功率曲线近似为反比例曲线,功率利用系数更高。
3、双泵恒功率控制技术在双泵或多泵系统中,由于存在多泵之间功率分配的技术难题,如何使柴油机功率合理地分配到各泵,使各执行机构协调工作,尽可能发挥其最大效能,最大程度发挥出发动机功率成为关键。
目前,这方面的控制技术有不同的组合形式。
(1)分功率控制技术分功率控制是根据各泵所负责的执行机构实际需用功率,将柴油机功率按一定比例分配给各泵。
在分功率控制中,每个泵均有独立的变量控制机构,使执行机构在预先设定的工作曲线上工作。
但分功率控制的最大缺点是不能充分利用发动机功率,当某个泵因某种情况不需要工作时,其功率不能给另一个泵使用而白白浪费,因此极易出现“大马拉小车”的现象,无法满足大型工程机械的使用要求。
- 1、下载文档前请自行甄别文档内容的完整性,平台不提供额外的编辑、内容补充、找答案等附加服务。
- 2、"仅部分预览"的文档,不可在线预览部分如存在完整性等问题,可反馈申请退款(可完整预览的文档不适用该条件!)。
- 3、如文档侵犯您的权益,请联系客服反馈,我们会尽快为您处理(人工客服工作时间:9:00-18:30)。
制调节泵的吸收功率 与发动机输出 功率基本匹
配, 从而使发动机工作转速保持在节能效果突出 的转速范围内。系统控制简化框图如图 3 所示。因 为泵的吸收功率在发动机转速稳定时由泵压力和
泵排 量 决 定, 负 载 变 化, 泵压 力相应 变化, 泵吸 收扭矩 增大 或减
小, 发动机转速出现的 偏差 经转速 传感 器反 馈输 入极限 负荷 控制
ec( k) = e( k ) - e( k - 1)
其增量式为
u( k ) = kP e( k) + k Ie( k ) + k D[ ec( k) - ec ( k - 1) ]
( 4)
式中, u ( k) 为控制器的电压信号输出值; u ( k) 为控制
器电压信号的输出增 量; n 为发 动机给 定转速; n( k) 为 发
0 引言
为了实现节能, 在进一步提高器件单体效率 的难度越来越大的情况下, 学者们将研究重心转 移到提高发动机与液压系统整体最佳效率的匹配 上[ 1] , 通过电子节能控制方法实现高效率的功率 转化。目前电子节能控制系统的研究主要针对以 下几个环节: 动力系统与负载的控制、液压泵的控 制、发动机与液压泵的控制[ 2 4] 。
A8VO 变量双泵调节原理如下( 以 1 号泵为 例, 下同) : 由负荷传感反馈到泵的 x 3 控制口的压 力 p x 3 和泵的出口压力 p b 控制变量缸的比例方向 压力控制阀开口度大小, 左位( 变量缸 1 无杆腔接
通油箱) 时开口度随 p x 3 和 p b 增大而减小, 使无 杆腔压力增大, 推动变量泵调节机构减小泵排量, 从而降低泵的吸收功率; 右位( 变量缸无杆腔接通 1 号泵出口) 时, p x3 和 p b 的合力驱动比例方向压 力控制阀开口度增大, 使变量调节缸的无杆腔与 有杆腔接通, 并使阀口压力损失减小, 无杆腔压力 增大, 差动作用使输出排量变为最小, 极限情况下 可不输出液流。
( 5)
式中, p e( k) 为 比 例 减 压 阀 调 定 压 力; ku 为 减 压 阀 比 例
系数。
( 3) 由比例减压阀输出压力 p x3 、泵出口压力 p b 、先导控制调节压力 p x 1 与作用在比例方向压 力阀阀芯上的弹簧力的平衡关系, 得到比例减压
阀输出压力( p x3 ) 与阀开口度之间的函数关系为
本文基于电比例控制变量泵跟随发动机转速 偏差变化的吸收功率的匹配控制原理, 分析了极 限负荷实现机理, 通过发动机转速感应偏差和电 比例控制变量泵负荷传感实现极限负荷控制, 以 柴油机控 制的 A8V O 变量泵 为对象, 提出 发动 机 变量泵的功率匹配控制方法, 并在 SWD- 20 旋挖钻机上进行了实验验证。
整定的转速感应控制方法, 利用变量泵的电液比 例控制技术, 调节电液比例控制变量泵的吸收功 率[ 5, 6] , 可实现系统极限负荷控制。即发动机输出 功率设定后, 若负载增大, 则泵增大吸收功率, 发 动机降速, 系统检测 到转速变化后, 减小泵的排 量, 从而降低泵的吸收功率, 保证泵的吸收功率和 发动机输出功率相匹配; 若负载减小, 自动增大泵 的排量, 增加泵的吸收功率, 在发动机输出功率允 许范围内使作业速度加快, 提高作业效率, 使发动 机在负荷变化范围内既满足重载, 也满足轻载的 作业要求, 较好地匹配了负载、泵和发动机之间的 功率关系。
P e = Mene
( 1)
式中, M e 为发动机输出扭矩; ne 为发动机转速。
泵的吸收功率为
Pp = p p qV p = p p V p np = M p np
( 2)
式中, p p 为泵出口压力; qV p 为泵输 出流量; V p 为 泵排量;
np 为泵转速; M p 为泵吸收扭矩。
发动机与泵直接相连时, np = ne。不考虑机械
传动的损失时, Mp = M e , 则发动机的输出功率 Pe
与泵的吸收功率 Pp 相等, 系统无功率损失[ 5] 。由
式( 2) 可见, 当负载变化即泵的出口压力 p p 发生
变化时, 实时调整泵的排量 V p, 可使泵的吸收扭
矩 Mp 始终跟踪发动机的输出扭矩 Me , 实现发动
机与泵的功率匹配。由于系统具备实时调节的跟
与重载低速的渐进变化。 3. 2 转速感应控制策略与系统控制框图
根据发动机不同工作转速条件下的负荷特性
与速度特性, 其工作转速保持在一个兼顾经济性 与最大功率输出的转速范围内, 才能实现发动机 运行的节能目标, 而钻机较大范围的负荷变化会 引起泵实际吸收功率发生变化, 使发动机产生较 大转速偏差, 导致发动机燃油消耗率等性能变差。 系统转速感应控制策略就是利用转速偏差感应控
3 系统功率匹配极限负荷控制
3. 1 钻进过程负荷变化特性 旋挖钻机的钻进由动力头驱动钻杆完成, 液
压动力源为力士乐 A8V O 双泵, 采用正流量控制 实现变量调节; 钻孔取土时, 钻机依靠钻杆和钻斗 的自重切入土层, 斜向斗齿在钻斗回转时切下土 块并向斗内推进完成钻取土。钻孔时, 回填土等软 土层切削阻力小, 钻进速度可以很快; 卵石层等硬 土层切削阻力大, 甚至需要装上短螺旋钻头才能 进行钻孔工作, 因而需要大扭矩输入, 钻进速度受 到限制而较慢。泵的负荷变化特性即为轻载高速
器, 通 过 自 适 应 模 糊
PID 参数整定[ 7] , 获得 控制 A8VO 泵 排量的
图 3 极限负荷 控制原理框图
电液比例减压阀的最优调节参数, 输出比例压力
控制信号, 调节控制变量缸的比例方向压力控制
阀的开口度大小, 改变变量缸驱动压力的大小和
方向, 最大限度吸收发动机功率而又保证发动机
中国机械工程第 18 卷第 4 期 2007 年 2 月下半月
发动机- 变量泵功率匹配极限负荷控制
柳 波 何清华 杨忠炯
中南大学, 长沙, 410083
摘要: 根据负荷多变工况条件下发动机 变量泵系统的节能要求, 分析了发动机功率极限负荷的控
制机理; 运用转速传感控制原理, 提出了变量泵随发动机功率变化进行功率匹配的动态调节方法; 给出
用面积; p x3 为极限负荷反 馈控制压力, p x3 = p e(k) ; A 2 为 比例方向压力阀上极限 负荷反 馈压力 作用面 积; A 3 为 比
( ka - ky ) x v + p x1 A 1 = p x3 A 2 + p b A 3
( 6)
p=
k d/
x
2 v
( 7)
式中, ka 为比例方向压力阀弹簧刚度; ky 为 泵液压行程 调
节弹簧刚度; x v 为比例 方向压 力阀开 口度; p x1 为 比例 方 向压力阀先导控制压力; A 1 为泵液 压行程 调节液 压力 作
1 极限负荷控制机理与转速感应极限负 荷控制方法
1. 1 极限负荷控制机理 发动机与液压系统的简化模型如图 1 所示。
发动机的输出功率为
收稿日期: 2006 09 04 基金项目: 国 家 863 高 技 术 研 究 发 展 计 划 资 助 项 目 ( 2003A A430200)
500
图 1 发动机与液压系统的 简化模型
随性能, 因此发动机不需设置功率储备, 该方式为 极限负荷控制。通过极限负荷控制, 可以提高系统 功率利用率, 达到节能目的。
1. 2 转速感应极限负荷控制方法
将系统功率流与电子流( 负荷传感与电反馈 控制) 有机结合起来, 通过检测负荷变化引起的
发动机转速变化, 运用自适应模糊 PID 参数调节
发动机- 变量泵功率匹配极限负荷控制 柳 波 何清华 杨忠炯
了发动机 电比例控制变量泵功率匹配控制方框图, 推导出系统控制调节传递函数。实验证明: 外负荷
变化时变量泵吸收功率与发动机输出功率基本匹配, 发动机无须功率储备就可以保持正常工作, 节能效
果明显。
关键词: 功率匹配; 转速感应控制; 极限负荷控制; 匹配调节控制
中图分类号: U 270. 11
文章编号: 1004 132X( 2007) 04 0500 04
动机实际转速; ec( k) 为转 速偏差 增量; k P 为 比例系 数, k I 为积分系数; k D 为微分 系数。
其中, kP 、kI 、kD 的数值由模糊控制规则确定。
( 2) 考虑比例减压阀的响应频率远大于泵变
量调节缸的响应频率, 减压阀环节可看成比例环
节, 即
p e( k) = k uu( k)
Load Limit Sensing Control of Power Matching for Engine- variable Pump System L iu Bo H e Qinghua Yang Zhongjiong
Cent ral Sout h Universit y, Chang sha, 410083 Abstract: Based on t he energ y- sav ing demands f or load- changeful eng ine- v ar iable pump sys t em, t he mechanism f or t he utm ost using of engine pow er w as analyzed. A dy namic adjust able method of po w er mat ching based on t he electr on regulat io n bet w een t he engine and t he variable pump w as a chieved by means of t he ro tat ion speed f eedback load lim it ing cont rol. T he pow er mat ching cont ro l principle and t ransf er funct ion of t he syst em w as est ablished for t he engine- electr on regulated varia ble pump syst em. T he perf ect condit ion w ith t he optimum ef ficiency of po w er matching is sho wn t o be tr ue by exper im ent s on a hydraulic drilling - rig . Key words: pow er matching; rotation speed feedback control; load limiting control; matching adjust ment