第三章压力加工成型技术
合集下载
第三编金属压力加工

第三编 金属的塑性成形
教学目的: 掌握金属塑性成形的机理及各种塑性
成形的方法,熟悉金属塑性成形工艺设计。
教学重点: 1. 金属塑性成形的机理、工艺;
2. 金属塑性成形性及其影响因素。
教学难点:自由锻与模锻工艺设计 教学内容:3.1 金属塑性成形基础;
3.2 金属塑性成形方法; 3.3 金属塑性成形工艺设计; 自学内容:3.4 金属塑性成形技术的发展趋势。
压力机上模膛成型常用的设备有曲柄压力机、 摩擦压力机和平锻机、模锻水压机等。
74
3.3.2 锻模模膛及其功用
●
模膛 种类
镦粗
制坯模膛(体积分配)
拔长 滚挤★
弯曲 …
模锻模膛(锻件成形) 预锻→初步成形
终锻→最终成形
切断模膛(锻件与坯料切离) 设飞边槽★
放收缩率
75
3.3.2.1 预锻模膛 预锻模膛的作用是:使坯料变形到接近于锻件的 形状和尺寸,终锻时,金属容易充满终锻模膛。 同时减少了终锻模膛的磨损,以延长锻模的使用 寿命。
43
冷变形和热变形
冷变形 —— 再结晶温度以下的塑性变形。
热变形 —— 再结晶温度以上的塑性变形
冷变形
加工硬化 冲压、冷弯、冷挤、冷轧
塑性材料
热变形
加工硬化+再结晶 锻造、热挤、轧制
变形量大,易氧化
44
消除加工硬化,提高 塑性。 在结晶速度取决于加 热温度和变形程度。 再结晶是一个形核、 长大过程。
68
半轴自由锻工艺
锻出头部
拔长
拔长及修整 台阶
锻件图
材料: 18CrMnTi 坯料尺寸:Ф130×240 坯料重量:25kg 锻造设备:0.5T自由锻锤
教学目的: 掌握金属塑性成形的机理及各种塑性
成形的方法,熟悉金属塑性成形工艺设计。
教学重点: 1. 金属塑性成形的机理、工艺;
2. 金属塑性成形性及其影响因素。
教学难点:自由锻与模锻工艺设计 教学内容:3.1 金属塑性成形基础;
3.2 金属塑性成形方法; 3.3 金属塑性成形工艺设计; 自学内容:3.4 金属塑性成形技术的发展趋势。
压力机上模膛成型常用的设备有曲柄压力机、 摩擦压力机和平锻机、模锻水压机等。
74
3.3.2 锻模模膛及其功用
●
模膛 种类
镦粗
制坯模膛(体积分配)
拔长 滚挤★
弯曲 …
模锻模膛(锻件成形) 预锻→初步成形
终锻→最终成形
切断模膛(锻件与坯料切离) 设飞边槽★
放收缩率
75
3.3.2.1 预锻模膛 预锻模膛的作用是:使坯料变形到接近于锻件的 形状和尺寸,终锻时,金属容易充满终锻模膛。 同时减少了终锻模膛的磨损,以延长锻模的使用 寿命。
43
冷变形和热变形
冷变形 —— 再结晶温度以下的塑性变形。
热变形 —— 再结晶温度以上的塑性变形
冷变形
加工硬化 冲压、冷弯、冷挤、冷轧
塑性材料
热变形
加工硬化+再结晶 锻造、热挤、轧制
变形量大,易氧化
44
消除加工硬化,提高 塑性。 在结晶速度取决于加 热温度和变形程度。 再结晶是一个形核、 长大过程。
68
半轴自由锻工艺
锻出头部
拔长
拔长及修整 台阶
锻件图
材料: 18CrMnTi 坯料尺寸:Ф130×240 坯料重量:25kg 锻造设备:0.5T自由锻锤
金属塑性成形(压力加工)详解

§1 压力加工工艺基础
§ 1— 1 金属的塑性变形与再结晶
一、金属塑性变形的实质
1.单晶体的塑性变形 1)滑移: 晶体的一部分相对一部分沿一定的晶面发生相对滑动。
τ
τ
τ
τ
但实际金属的滑移是靠位错的移动来实现的。
2)孪晶: 晶体的一部分相对一部分沿一定的晶面发生相对转动。
2. 多晶体的塑性变形 滑移 晶内变形 孪晶 滑动 晶间变形 转动
第三章 金属塑性成形(压力加工)
§1 压力加工工艺基础
§2 金属的塑性成形方法
§3 锻件与冲压件结构工艺性
第三章 金属塑性成形(压力加工)
概 述
一、压力加工(金属塑性成形)
金属材料在外力作用下产生塑性变形,获得具有一定形
状、尺寸和力学性能的毛坯或零件的生产方法。
二、压力加工的基本生产方式
1.轧制 4.自由锻造 2.挤压 5.模型锻造 3.拉拔 6.板料1. 体积不变定律 2. 最小阻力定律
§2 金属的塑性成形方法
§2-1 自由锻造
65~750Kg
一、自由锻设备
锻锤 空气锤 水压机 油压机 蒸汽—空气锤 630Kg~5T
压力机
锻锤吨位 = 落下部分总重量 = 活塞+锤头+锤杆 压力机吨位 = 滑块运动到下始点时所产生的最大压力
4 . 锻造温度范围及加热火次的确定
5 . 锻造设备的选择
6 . 确定工时
7 . 填写工艺卡
§2-2
模型锻造
模型锻造 — 将金属坯料放在具有一定形状的模锻模膛 内受压、变形,获得锻件的方法。 特点: 1)生产率高; 2)锻件的尺寸精度和表面质量高;
3)材料利用率高; 4)可锻造形状较复杂的零件; 5)模具成本高、设备昂贵; 6)锻件不能任意大。一般不得超过150kg。
第三章 压力加工
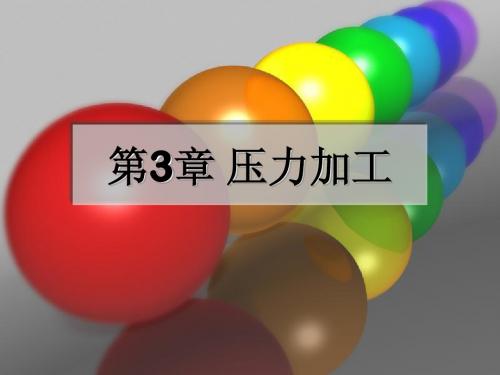
第二节 自由锻
自由锻是利用冲击力或压力使金属在上、下两个铁 自由锻是利用冲击力或压力使金属在上、 是利用冲击力或压力使金属在上 砧间产生变形, 砧间产生变形,从而获得所需形状及尺寸的锻件的一 种加工方法。 种加工方法。
自 由 锻 优 点
自 由 锻 缺 点
一、自由锻工序
自由锻造的工序可以分为三类, 基本工序、 自由锻造的工序可以分为三类,即基本工序、辅助 工序和修正工序。 工序和修正工序。 基本工序:改变坯料形状和尺寸以获得锻件, 基本工序:改变坯料形状和尺寸以获得锻件,如镦 拔长、冲孔、芯轴扩孔、芯轴拔长、弯曲、切割、 粗、拔长、冲孔、芯轴扩孔、芯轴拔长、弯曲、切割、 错移、扭转和锻接。 错移、扭转和锻接。 辅助工序: 辅助工序:为了完成基本工序而使坯料预先产生某 一变形,如钢锭倒棱、预压钳拔和分段压痕。 一变形,如钢锭倒棱、预压钳拔和分段压痕。 修正工序:使锻件完全达到锻件图要求, 修正工序:使锻件完全达到锻件图要求,精整锻件 尺寸和形状,消除锻件平面不平、歪扭位置, 尺寸和形状,消除锻件平面不平、歪扭位置,如鼓形 滚圆、端面平整、弯曲校直。 滚圆、端面平整、弯曲校直。
第3章 压力加工
什么是金属压力加工? 什么是金属压力加工?
借助外力的作用,使金属坯料产生 塑性变形,从而获得具有一定形状、尺 寸和性能的锻压件。
也就是:锻压 锻压
二次塑性加工
二次塑性加工
一次塑性加工
自由锻 一次/ 一次/二次塑性加工
模锻
轧制 一次塑性加工 二次塑性加工
正挤压
反挤压
拉拔
冲压
优点: 优点: 组织细化致密、力学性能提高; ⑴组织细化致密、力学性能提高; 体积不变的材料转移成形,材料利用率高; ⑵体积不变的材料转移成形,材料利用率高 生产率高,易机械化、自动化等。 ⑶生产率高,易机械化、自动化等。 可获得精度较高的零件或毛坯, ⑷可获得精度较高的零件或毛坯,可实现少无切削 加工。 加工。 缺点: 缺点: 不能加工脆性材料; ⑴不能加工脆性材料; 难以加工形状特别复杂(特别是内腔)、 )、体积特 ⑵难以加工形状特别复杂(特别是内腔)、体积特 别大的制品; 别大的制品; 设备、模具投资费用大。 ⑶设备、模具投资费用大。
03-2加力加工成型技术

2自 由锻 件结 构设 计注 意的
问题
2自 由锻 件结 构设 计注 意的
问题
避免加强筋、工字形、椭圆形等 复杂表面
避免叉形件内部的台阶
3
板 料 冲 压
利用冲模对金属板料施加压力,使其产生分离或 变形获得所需零件的工艺方法。
3
冷冲压:t < 8 mm
冲
压
4 冲
1. 剪床:下料设备
压 设
2. 冲床:冲压设备
变形工序
成形
5-2
变
形
工
序
神洲五号返回仓
5-3
冲 模 简 介
冲模 简单
冲模
连续 冲模
复合 冲模
冲床在一次行程中只完成一 个冲压工序。如冲孔或落料
冲床在一次行程中在不同的 工位同时完成两个以上的冲 压工序。
冲床在一次行程中在同一工 位同时完成两个以上的冲压 工序。
5-4
冲压 方法 对结 构工 艺性 的要 求
序
拉深
多次拉深
控制拉深系数m
m = d/D ≥(0.5-0.8) 例 D=100; d=20;h=42 1. d1=55,m=55/100=0.55 2. d2=32,m= 32/55=0.58 3. d3=20,m= 20/32=0.628 由拉深系数反推每次拉深的直径
变形工序
5-2 变 形 工 序
序 要合理
冲裁模设计
z/2
分离工序
冲裁
5-1
分 离 工 序
凸凹 尺寸
落料: D凹 = d落
冲孔: D凸 = d孔
模刃口 要正确
D凸= D凹 - Z
D凹 = D凸 + Z
冲裁模设计
第三篇金属压力加工

• 上述理论所描述的滑移运动,相当于滑移上下两部分晶 体彼此以刚性整体作相对运动。要实现这种滑移所需的 外力要比实际测得的数据大几千倍,这说明实际晶体结 构及其塑性变形并不完全如此。
近代物理学证明,实际晶体内部存在大最缺陷。其中,以 位错(图3-2a对金属塑性变形的影响最为明显。由于位 错的存在,部分原子处于不稳定状态。在比理论值低得 多的切应力作用下,处于高能位的原子很容易从一个相 对平衡的位置上移动到另一个位置上(图3-2b),形成 位错运动。位错运动的结果,就实现了整个晶体的塑性 变形(图3-2c)。
4、多晶体的塑性变形:金属都是由大量微小晶粒组成的 多晶体。其塑性变形可以看成是由组成多晶体的许多单个 晶粒产生变形(称为晶内变形)的综合效果。 由于构成晶体的晶粒位向不同,还有晶界的阻碍,在其滑 移,变形时,分先后次序逐批进行。同时晶间的滑动和转 动(称为晶间变形)。如图,每个晶粒内部都存在许多滑 移面,因此整块金属的变形量可以比较大。低温时,多晶 体的晶间变形不可过大,否则将引起金属的破坏。
(2)拉拔 金属坯料被拉过拉拔模的模孔而变形的加工方法。
(3) 挤压 金属坯料在挤压模内被挤出模也而变形的加工方法。
(4) 锻造 金属坯料在抵铁或锻模模膛内变形而获得产品的方法。
(5)板料冲压 金属板料在冲模间受外力作用而产生分离或变形 的加工方法。
• 一般常用的金属型材、板材、管材和线材等原材料,大都是通过 轧制、挤压、拉拔等方法制成的。机械制造业中的许多毛坯或零 件,特别是承受重载荷的机件,如机床的主轴、重要齿轮、连杆、 炮管和枪管等,通常采用锻件作毛坯。板料冲压广泛用于汽车、 电器、仪表零件及日用品工业等方面。
2、变形速度的影响 变形速度即单位时间的变形程度。 (1)随着变形速度的增大,回复和再结晶不能及时克服 冷变形强化现象,金属则表现出塑性下降、变形抗力增大 (图3-9中a点以左),可锻性变差。
近代物理学证明,实际晶体内部存在大最缺陷。其中,以 位错(图3-2a对金属塑性变形的影响最为明显。由于位 错的存在,部分原子处于不稳定状态。在比理论值低得 多的切应力作用下,处于高能位的原子很容易从一个相 对平衡的位置上移动到另一个位置上(图3-2b),形成 位错运动。位错运动的结果,就实现了整个晶体的塑性 变形(图3-2c)。
4、多晶体的塑性变形:金属都是由大量微小晶粒组成的 多晶体。其塑性变形可以看成是由组成多晶体的许多单个 晶粒产生变形(称为晶内变形)的综合效果。 由于构成晶体的晶粒位向不同,还有晶界的阻碍,在其滑 移,变形时,分先后次序逐批进行。同时晶间的滑动和转 动(称为晶间变形)。如图,每个晶粒内部都存在许多滑 移面,因此整块金属的变形量可以比较大。低温时,多晶 体的晶间变形不可过大,否则将引起金属的破坏。
(2)拉拔 金属坯料被拉过拉拔模的模孔而变形的加工方法。
(3) 挤压 金属坯料在挤压模内被挤出模也而变形的加工方法。
(4) 锻造 金属坯料在抵铁或锻模模膛内变形而获得产品的方法。
(5)板料冲压 金属板料在冲模间受外力作用而产生分离或变形 的加工方法。
• 一般常用的金属型材、板材、管材和线材等原材料,大都是通过 轧制、挤压、拉拔等方法制成的。机械制造业中的许多毛坯或零 件,特别是承受重载荷的机件,如机床的主轴、重要齿轮、连杆、 炮管和枪管等,通常采用锻件作毛坯。板料冲压广泛用于汽车、 电器、仪表零件及日用品工业等方面。
2、变形速度的影响 变形速度即单位时间的变形程度。 (1)随着变形速度的增大,回复和再结晶不能及时克服 冷变形强化现象,金属则表现出塑性下降、变形抗力增大 (图3-9中a点以左),可锻性变差。
第三章压力加工成型技术

3. 常用合金的锻造特点 (1)合金钢
首先,选择坯料时,表面不允许有裂纹存在,锻前需进行退火; 其次,先加热至800℃保温,再加热到始锻温度,采用低温装炉及
缓慢升温;
另外,始锻温度较低,终锻温度高。
合金钢的锻造需注意:
(1)控制变形量;“两轻一重”
(2)增大锻造比;
(3)保证温度、变形均匀;勤翻坯料,送进量均匀,砧铁预热
3. 加工硬化
概念:金属发生塑性变形, 随变形度的增大, 金属的强度和硬
度显著提高, 塑性和韧性明显下降。这种现象称为加工硬化, 也叫 形变强化。
产生原因: 金属发生塑性变形时, 位错密度增加, 位错间的
交互作用增强, 相互缠结, 造成位错运动阻力的增大, 引起塑性 变形抗力提高。
滑移面上产生许多晶格方向混乱的细小碎晶,它们的晶界 是严重的晶格畸变区,增加了滑移阻力,加大了内应力。
第三章 压力加工成型技术
本章主要内容
► 压力加工成型方法 ► 金属材料的塑性成型基础 ► 锻造 ► 冲压
压力加工
塑性成形(plasticity forming) —— 在外力作用下,金属发生塑性变形,
从而获得具有一定形状、尺寸、组织和力学性 能的工件的生产方法,又叫塑性加工或压力加 工。
常见的塑性成形方法: 锻造、冲压、挤压、轧制、拉拔等。
自由锻件的结构工艺性自由锻件的结构工艺性11尽量避免锥体或斜面结构尽量避免锥体或斜面结构轴类锻件结构a工艺性差的结构b工艺性好的结构2避免几何体的交接处形成空间曲线避免几何体的交接处形成空间曲线杆类锻件结构a工艺性差的结构b工艺性好的结构33避免加强肋凸台工字形椭圆形或其它非规则截面避免加强肋凸台工字形椭圆形或其它非规则截面及外形及外形盘类锻件结构a工艺性差的结构b工艺性好的结构44合理采用组合结构合理采用组合结构复杂件结构a工艺性差的结构b工艺性好的结构三模型锻造和胎模锻造三模型锻造和胎模锻造模型锻造概念
机械制造基础课件—第三章压力加工

多晶体金属的塑性变形抗力总是高于单晶体。 晶粒越细小,变形抗力越大,但能提高金属的 塑性。
4
3.1.2 塑性变形对组织和性能的影响
金属在常温下经过塑性变形后,内部组织和性能将发生变化: ①晶粒沿变形方向伸长,性能趋于各向异性; ②晶粒破碎,位错密度增加,产生加工硬化 ; ③产生内应力 。
金属发生冷塑性变形时,随着 变形量的增加,强度和硬度提 高,塑性和韧性下降的现象称为 加工硬化,又称冷变形强化。
拔长时的锻造比为:Y拔= A0/A =L/L0 镦粗时的锻造比为:Y镦= A/A0 =H0/H
纤维组织的稳定性很高,不能用热处理的方法消除,只有经过压力 加工使金属变形,才能改变其方向和形状。
为了获得具有最好力学性能的零件,在设计和制造零件时,都应使 零件在工作中产生的最大正应力方向与纤维方向重合,最大切应力方向 与纤维方向垂直。并使纤维沿零件轮廓分布而不被切断。
20
3.避免加强筋、凸台、工字形截面或空间曲线形表面 4.合理采用组合结构
21
3.3 模锻
模锻是在高强度金属锻模上预先制出与锻件形状一致的 模膛,使坯料在模膛内受压变形,由于模膛对金属坯料流动的 限制,因而锻造终了时能得到和模膛形状相符的锻件。
与自由锻相比,模锻的优点是:操作简便,生产率高;可 以锻造形状较复杂的锻件;锻件的尺寸精确、表面较光洁,因 而机械加工余量小,材料利用率高,成本较低;而且可使锻件 的金属纤维组织分布更加合理,进一步提高了零件的使用寿 命。
1)长轴类模锻件 常用的工步 有拔长、滚压、弯曲、预锻和终锻 等。
2)盘类模锻件 常用镦粗、终 锻等工序。 (4)确定修整工序
包括切边、冲孔、热处理、清 理、校正等。
30
3. 模锻件的结构工艺性
4
3.1.2 塑性变形对组织和性能的影响
金属在常温下经过塑性变形后,内部组织和性能将发生变化: ①晶粒沿变形方向伸长,性能趋于各向异性; ②晶粒破碎,位错密度增加,产生加工硬化 ; ③产生内应力 。
金属发生冷塑性变形时,随着 变形量的增加,强度和硬度提 高,塑性和韧性下降的现象称为 加工硬化,又称冷变形强化。
拔长时的锻造比为:Y拔= A0/A =L/L0 镦粗时的锻造比为:Y镦= A/A0 =H0/H
纤维组织的稳定性很高,不能用热处理的方法消除,只有经过压力 加工使金属变形,才能改变其方向和形状。
为了获得具有最好力学性能的零件,在设计和制造零件时,都应使 零件在工作中产生的最大正应力方向与纤维方向重合,最大切应力方向 与纤维方向垂直。并使纤维沿零件轮廓分布而不被切断。
20
3.避免加强筋、凸台、工字形截面或空间曲线形表面 4.合理采用组合结构
21
3.3 模锻
模锻是在高强度金属锻模上预先制出与锻件形状一致的 模膛,使坯料在模膛内受压变形,由于模膛对金属坯料流动的 限制,因而锻造终了时能得到和模膛形状相符的锻件。
与自由锻相比,模锻的优点是:操作简便,生产率高;可 以锻造形状较复杂的锻件;锻件的尺寸精确、表面较光洁,因 而机械加工余量小,材料利用率高,成本较低;而且可使锻件 的金属纤维组织分布更加合理,进一步提高了零件的使用寿 命。
1)长轴类模锻件 常用的工步 有拔长、滚压、弯曲、预锻和终锻 等。
2)盘类模锻件 常用镦粗、终 锻等工序。 (4)确定修整工序
包括切边、冲孔、热处理、清 理、校正等。
30
3. 模锻件的结构工艺性
材料成形技术课件3金属压力加工

性变形。因此,塑性变形过程中一定有弹性变形存在。 • 5.只有经过塑性变形的钢才会发生回复和再结晶。没有经过塑性变形的钢,即使把它加热
到回复或再结晶温度以上也不会产生回复或再结晶。 • 6.塑性是金属可锻性中的一个指标。压力加工时,可以改变变形条件;但不能改变金属的
塑性。
第二十页,共78页。
• 7.冷变形不仅能改变金属的形状,而且还能强化金属,使其强度、硬度 升高。冷变形也可以使工件获得较高的精度(jīnɡ dù)和表面质量。
• 铅 T再 =0.4T熔点(K) (327+273) ×0.4 =600×0.4 = 240(-33℃) • 所以铅在室温(20℃)进行(jìnxíng)变形为热变形
• 2.圆钢拔长前直径为φ100mm,拔长后为φ50mm,试计算锻造 比y。
• y=F0/F=(100/50)2=4
第二十三页,共78页。
第三章 锻造(duànzào)方法
• §3-1 自由锻 • 自由锻 利用冲击力或压力,使放在上下砧之间的金属坯
• 过热 加热温度过高,导致晶粒急剧长大的现象。该缺陷可以通过重新的热处理加以消除。
• 过烧 加热温度过高(过热之后),导致晶界严重氧化,甚至局部熔化的现象。 产生(chǎnshēng)该缺陷后,性能极脆,并不能挽 救,只能报废。
• 停止锻造的温度称为终锻温度,指金属热变形允许的最低温度。终锻温度过低,金属的加工硬化严重,变形抗力急剧增加,使加 工难于进行。
• 横向(垂直于纤维方向)上的塑性、韧性则降低。
• 纤维组织的稳定性很高,不能用热处理或其它方法加以消除,只有经过 锻压使金属变形,才能改变其方向和形状。
第十三页,共78页。
合理(hélǐ)利用纤维组织
• 1、应使零件在工作中所受的最大正应力方向与纤维方向 重合,2、最大切应力方向与纤维方向垂直(chuízhí),3、 并使纤维分布与零件的轮廓相符合,尽量不被切断。
到回复或再结晶温度以上也不会产生回复或再结晶。 • 6.塑性是金属可锻性中的一个指标。压力加工时,可以改变变形条件;但不能改变金属的
塑性。
第二十页,共78页。
• 7.冷变形不仅能改变金属的形状,而且还能强化金属,使其强度、硬度 升高。冷变形也可以使工件获得较高的精度(jīnɡ dù)和表面质量。
• 铅 T再 =0.4T熔点(K) (327+273) ×0.4 =600×0.4 = 240(-33℃) • 所以铅在室温(20℃)进行(jìnxíng)变形为热变形
• 2.圆钢拔长前直径为φ100mm,拔长后为φ50mm,试计算锻造 比y。
• y=F0/F=(100/50)2=4
第二十三页,共78页。
第三章 锻造(duànzào)方法
• §3-1 自由锻 • 自由锻 利用冲击力或压力,使放在上下砧之间的金属坯
• 过热 加热温度过高,导致晶粒急剧长大的现象。该缺陷可以通过重新的热处理加以消除。
• 过烧 加热温度过高(过热之后),导致晶界严重氧化,甚至局部熔化的现象。 产生(chǎnshēng)该缺陷后,性能极脆,并不能挽 救,只能报废。
• 停止锻造的温度称为终锻温度,指金属热变形允许的最低温度。终锻温度过低,金属的加工硬化严重,变形抗力急剧增加,使加 工难于进行。
• 横向(垂直于纤维方向)上的塑性、韧性则降低。
• 纤维组织的稳定性很高,不能用热处理或其它方法加以消除,只有经过 锻压使金属变形,才能改变其方向和形状。
第十三页,共78页。
合理(hélǐ)利用纤维组织
• 1、应使零件在工作中所受的最大正应力方向与纤维方向 重合,2、最大切应力方向与纤维方向垂直(chuízhí),3、 并使纤维分布与零件的轮廓相符合,尽量不被切断。
- 1、下载文档前请自行甄别文档内容的完整性,平台不提供额外的编辑、内容补充、找答案等附加服务。
- 2、"仅部分预览"的文档,不可在线预览部分如存在完整性等问题,可反馈申请退款(可完整预览的文档不适用该条件!)。
- 3、如文档侵犯您的权益,请联系客服反馈,我们会尽快为您处理(人工客服工作时间:9:00-18:30)。
离或变形的压力加工方法。
冲压
3.2 金属材料的塑性成型基础
一.金属塑性变形的实质
塑性成型:在外力作用下金属材料通过塑性变形,获得具
有一定形状、尺寸和力学性能的零件或毛坯的加工方法。 1.单晶体的塑性变形
滑移:单晶体中最主要的一种塑性变形方式。所谓滑移是晶
体的一部分相对于另一部分沿一定晶面发生相对的滑动。
特点:滑移只能在切应力的作用下发生;
滑移常沿晶体中原子密度最大的晶面和晶向发生。
单晶体试样拉伸变形的示意图
晶体中通过位错运动而造成滑移的示意图
位错:即原子的局部不规则排列;即晶体中已滑移部分与 未滑移部分的分界线。 是晶体中典型的线缺陷
2.多晶体的塑性变形
多晶体的塑性变形:即每个晶粒的塑性变形仍以滑移或孪生
冷变形:又叫冷成形过程,是指金属在进行塑性变形时的温
度低于该金属的再结晶温度
特点:金属变形后具有加工硬化现象,即金属的强度、硬度
升高,但塑性及韧度下降。冷变形制成的产品尺寸精度高、表面 质量好。
(a)拉拔示意图 (b)部分拉拔产品截面形状
二、机械零件的毛坯及产品生产
1. 锻造
概念:在加压设备及模具的作用下,使坯料、铸锭产生局部或
全部的塑性变形,以获得具有一定几何尺寸、形状和质量的锻件 的加工方法,按所用的设备和工模具不同,可分为自由锻造和模 型锻造两类。
2. 冲压
概念:将金属板料放在冲模之间,使其受冲压力作用产生分
方式进行。其变形过程比单晶体复杂得多。 具有较大的变形抗力 总是一批一批晶粒逐步发展的,从少量晶体开始逐步扩大到 大晶粒发生滑移,从不均匀变形逐步发展到较均匀变形。
多晶体的晶间变形情况
二、塑性变形对金属组织和性能的影响
1. 组织变化 (a)晶粒沿变形方向拉长,宏观:金属外形压扁或拉长;微观: 晶粒破碎、拉长。 (b)产生形变织构 (c)晶体缺陷大量增加,空位浓度增加。位错密度增加。
轧制示意图 1-轧辊、2-轧件
轧制型材
轧制产品形状
主要用于生产各种规格的钢板、型钢和钢管等钢材
2. 挤压生产
将金属坯料放入挤压模内,使其受压被挤出模孔而变形的加 工方法。
(a)挤压示意图;(b)部分挤压产品截面图
冷挤压产品
单螺杆挤压机
3. 拉拔生产 将金属条料或棒料拉过拉拔的模孔而变形的压力加工方法。
锻造、冲压、挤压、轧制、拉拔等。
轧制
拉拔
上砧铁 坯料
下砧铁
自由锻 模锻 冲压
压力加工产品
齿轮
金属棒材
某东风汽车大梁
压力加工的特点:
(1)改善金属的内部组织,提高金属的力学性能 (2)具有较高的劳动生产率 (3)节约金属材料 (4)适用范围广 压力加工可生产出各种不同截面的型材和各种机器零件的毛 坯或成品。它在机械、电力、交通、航空、国防等工业部门以至 生活用品的生产中占用重要的地位。
3. 加工硬化
概念:金属发生塑性变形, 随变形度的增大, 金属的强度和硬
度显著提高, 塑性和韧性明显下降。这种现象称为加工硬化, 也叫 形变强化。
产生原因: 金属发生塑性变形时, 位错密度增加, 位错间
的交互作用增强, 相互缠结, 造成位错运动阻力的增大, 引起塑 性变形抗力提高。 滑移面上产生许多晶格方向混乱的细小碎晶,它们的晶界 是严重的晶格畸变区,增加了滑移阻力,加大了内应力。
加工硬化是强化金属的重要方法之一
加工硬化的利:
提高强度
使变形均匀 提高安全性
利用缺陷实现金属强化的重要方法之一,
尤其是对不能热处理强化的金属材料。
加工硬化的弊:进一步塑性变形困难。
4. 消除加工硬化的工艺方法:回复与再结晶
回复:加热温度较低,变形金属中的一些点缺陷和位错在某
些晶内发生迁移变化,使原子回复到平衡位置,晶内残余应力 大大减小的现象,称为回复。 特点: 使晶格畸变减轻或消除,但晶粒的大小和形状并无改变。 消除了晶格扭曲及大部分内应力。力学性能变化不大,强度、 硬度稍有降低;塑性略有提高;内应力大大降低。
晶粒长大:
如温度继续升高或保温时间延长,晶粒会长大,使塑性、韧性 明显下降。
T再=0.4T熔 T再:金属再结晶的绝对温度(K)
保持加ቤተ መጻሕፍቲ ባይዱ硬化,消 除内应力。如冷卷弹簧
进行去应力退火。
消除加工硬化,提高 塑性。 再结晶速度取决于加 热温度和变形程度。 再结晶是一个形核、 长大过程。
5.冷变形和热变形
3.1 压力加工成型方法
一、型材生产方法 型材(extrudate):铁或钢以及具有一定强 度和韧性的材料(如塑料、铝、玻璃纤维等) 通过轧制,挤出,等工艺制成的具有一定几何 形状的物体。 其断面形状又可分为工字钢、槽钢、角钢、圆 钢等
一、型材生产方法
1. 轧制生产 借助于坯料与轧辊之间的摩擦力,使金属坯料连续地通过 两个旋转方向相反的轧辊的空隙而受压变形的加工方法。
回复处理:低温退火或去应力退火。
纯金属的回复温度: T回 =(0.25~0.3)T熔 T回:金属回复的绝对温度(K); T熔:金属熔点的绝对温度(K)
再结晶:变形金属加热到较高温度时,原子具有较强的活
动能力,有可能在破碎的亚晶界处重新形核和长大,使原来 破碎拉长的晶粒变成新的、内部缺陷较少的等轴晶粒。这一 过程,使晶粒的外形发生了变化,而晶格的类型无任何改变, 故称为“再结晶”。 特点: 再结晶通过形核、长大的方式进行,得到细小均匀等轴晶粒。 完全消除了残余应力和加工硬化现象,塑性提高。再结晶退火。
第三章 压力加工成型技术
本章主要内容
► 压力加工成型方法 ► 金属材料的塑性成型基础 ► 锻造
► 冲压
压力加工
塑性成形(plasticity forming)
—— 在外力作用下,金属发生塑性变形, 从而获得具有一定形状、尺寸、组织和力学性 能的工件的生产方法,又叫塑性加工或压力加 工。
常见的塑性成形方法:
等轴晶粒
拉长晶粒
2、性能变化 (a)机械性能 金属材料在冷塑性变形时,其强度、硬度升 高,而塑性、韧性下降的现象——冷变形强化 (b)物理、化学性能的变化,物理性能:电磁性下降;电阻 升高;导磁率下降等。化学性能:耐腐蚀性下降。
(c)内应力,经过塑性变形,外力对金属所作的功90%以上 在变形过程中变为热量消耗了,使金属温度升高。<10%的功 转化为内应力残留在金属中,使金属内能升高。
冲压
3.2 金属材料的塑性成型基础
一.金属塑性变形的实质
塑性成型:在外力作用下金属材料通过塑性变形,获得具
有一定形状、尺寸和力学性能的零件或毛坯的加工方法。 1.单晶体的塑性变形
滑移:单晶体中最主要的一种塑性变形方式。所谓滑移是晶
体的一部分相对于另一部分沿一定晶面发生相对的滑动。
特点:滑移只能在切应力的作用下发生;
滑移常沿晶体中原子密度最大的晶面和晶向发生。
单晶体试样拉伸变形的示意图
晶体中通过位错运动而造成滑移的示意图
位错:即原子的局部不规则排列;即晶体中已滑移部分与 未滑移部分的分界线。 是晶体中典型的线缺陷
2.多晶体的塑性变形
多晶体的塑性变形:即每个晶粒的塑性变形仍以滑移或孪生
冷变形:又叫冷成形过程,是指金属在进行塑性变形时的温
度低于该金属的再结晶温度
特点:金属变形后具有加工硬化现象,即金属的强度、硬度
升高,但塑性及韧度下降。冷变形制成的产品尺寸精度高、表面 质量好。
(a)拉拔示意图 (b)部分拉拔产品截面形状
二、机械零件的毛坯及产品生产
1. 锻造
概念:在加压设备及模具的作用下,使坯料、铸锭产生局部或
全部的塑性变形,以获得具有一定几何尺寸、形状和质量的锻件 的加工方法,按所用的设备和工模具不同,可分为自由锻造和模 型锻造两类。
2. 冲压
概念:将金属板料放在冲模之间,使其受冲压力作用产生分
方式进行。其变形过程比单晶体复杂得多。 具有较大的变形抗力 总是一批一批晶粒逐步发展的,从少量晶体开始逐步扩大到 大晶粒发生滑移,从不均匀变形逐步发展到较均匀变形。
多晶体的晶间变形情况
二、塑性变形对金属组织和性能的影响
1. 组织变化 (a)晶粒沿变形方向拉长,宏观:金属外形压扁或拉长;微观: 晶粒破碎、拉长。 (b)产生形变织构 (c)晶体缺陷大量增加,空位浓度增加。位错密度增加。
轧制示意图 1-轧辊、2-轧件
轧制型材
轧制产品形状
主要用于生产各种规格的钢板、型钢和钢管等钢材
2. 挤压生产
将金属坯料放入挤压模内,使其受压被挤出模孔而变形的加 工方法。
(a)挤压示意图;(b)部分挤压产品截面图
冷挤压产品
单螺杆挤压机
3. 拉拔生产 将金属条料或棒料拉过拉拔的模孔而变形的压力加工方法。
锻造、冲压、挤压、轧制、拉拔等。
轧制
拉拔
上砧铁 坯料
下砧铁
自由锻 模锻 冲压
压力加工产品
齿轮
金属棒材
某东风汽车大梁
压力加工的特点:
(1)改善金属的内部组织,提高金属的力学性能 (2)具有较高的劳动生产率 (3)节约金属材料 (4)适用范围广 压力加工可生产出各种不同截面的型材和各种机器零件的毛 坯或成品。它在机械、电力、交通、航空、国防等工业部门以至 生活用品的生产中占用重要的地位。
3. 加工硬化
概念:金属发生塑性变形, 随变形度的增大, 金属的强度和硬
度显著提高, 塑性和韧性明显下降。这种现象称为加工硬化, 也叫 形变强化。
产生原因: 金属发生塑性变形时, 位错密度增加, 位错间
的交互作用增强, 相互缠结, 造成位错运动阻力的增大, 引起塑 性变形抗力提高。 滑移面上产生许多晶格方向混乱的细小碎晶,它们的晶界 是严重的晶格畸变区,增加了滑移阻力,加大了内应力。
加工硬化是强化金属的重要方法之一
加工硬化的利:
提高强度
使变形均匀 提高安全性
利用缺陷实现金属强化的重要方法之一,
尤其是对不能热处理强化的金属材料。
加工硬化的弊:进一步塑性变形困难。
4. 消除加工硬化的工艺方法:回复与再结晶
回复:加热温度较低,变形金属中的一些点缺陷和位错在某
些晶内发生迁移变化,使原子回复到平衡位置,晶内残余应力 大大减小的现象,称为回复。 特点: 使晶格畸变减轻或消除,但晶粒的大小和形状并无改变。 消除了晶格扭曲及大部分内应力。力学性能变化不大,强度、 硬度稍有降低;塑性略有提高;内应力大大降低。
晶粒长大:
如温度继续升高或保温时间延长,晶粒会长大,使塑性、韧性 明显下降。
T再=0.4T熔 T再:金属再结晶的绝对温度(K)
保持加ቤተ መጻሕፍቲ ባይዱ硬化,消 除内应力。如冷卷弹簧
进行去应力退火。
消除加工硬化,提高 塑性。 再结晶速度取决于加 热温度和变形程度。 再结晶是一个形核、 长大过程。
5.冷变形和热变形
3.1 压力加工成型方法
一、型材生产方法 型材(extrudate):铁或钢以及具有一定强 度和韧性的材料(如塑料、铝、玻璃纤维等) 通过轧制,挤出,等工艺制成的具有一定几何 形状的物体。 其断面形状又可分为工字钢、槽钢、角钢、圆 钢等
一、型材生产方法
1. 轧制生产 借助于坯料与轧辊之间的摩擦力,使金属坯料连续地通过 两个旋转方向相反的轧辊的空隙而受压变形的加工方法。
回复处理:低温退火或去应力退火。
纯金属的回复温度: T回 =(0.25~0.3)T熔 T回:金属回复的绝对温度(K); T熔:金属熔点的绝对温度(K)
再结晶:变形金属加热到较高温度时,原子具有较强的活
动能力,有可能在破碎的亚晶界处重新形核和长大,使原来 破碎拉长的晶粒变成新的、内部缺陷较少的等轴晶粒。这一 过程,使晶粒的外形发生了变化,而晶格的类型无任何改变, 故称为“再结晶”。 特点: 再结晶通过形核、长大的方式进行,得到细小均匀等轴晶粒。 完全消除了残余应力和加工硬化现象,塑性提高。再结晶退火。
第三章 压力加工成型技术
本章主要内容
► 压力加工成型方法 ► 金属材料的塑性成型基础 ► 锻造
► 冲压
压力加工
塑性成形(plasticity forming)
—— 在外力作用下,金属发生塑性变形, 从而获得具有一定形状、尺寸、组织和力学性 能的工件的生产方法,又叫塑性加工或压力加 工。
常见的塑性成形方法:
等轴晶粒
拉长晶粒
2、性能变化 (a)机械性能 金属材料在冷塑性变形时,其强度、硬度升 高,而塑性、韧性下降的现象——冷变形强化 (b)物理、化学性能的变化,物理性能:电磁性下降;电阻 升高;导磁率下降等。化学性能:耐腐蚀性下降。
(c)内应力,经过塑性变形,外力对金属所作的功90%以上 在变形过程中变为热量消耗了,使金属温度升高。<10%的功 转化为内应力残留在金属中,使金属内能升高。