压铸模具基础知识60页PPT
合集下载
《压铸安全知识》课件

减少企业财产损失
压铸设备和其他相关设施 昂贵,一旦发生事故可能 导致重大财产损失。
提高生产效率
安全的工作环境有助于员 工集中精力,提高工作效 率。
压铸生产中的主要危险源
高温金属液体
压铸过程中会产生高温金 属液体,如果防护措施不 当,可能导致烫伤。
高压射流
高压射流在将金属注入模 具时具有很高的动能,如 果不加以控制,可能对人 员和设备造成伤害。
01
压铸模具应安装安全防护装置
如机械手、气动夹具等,以防止操作员接触高温模具和熔融金属。
02
压铸模具应定期检查和维护
确保模具处于良好状态,防止因模具故障导致的事故。
03
压铸模具周围应设置安全警示标识
提醒操作员和其他人员注意安全,避免进入危险区域。
压铸工件后处理安全防护措施
工件后处理设备应安装安全防护装置
压铸机故障,造成人员伤亡。
事故原因
操作人员未经过专业培训,对压 铸机操作不熟悉,导致误操作。
事故教训
加强员工培训,确保操作人员熟 悉压铸机操作规程,提高安全意
识。
案例二:某公司压铸模具事故分析
事故经过
某公司生产过程中,压铸模具突然破裂,造成人 员伤亡。
事故原因
模具质量不过关,使用过程中出现疲劳裂纹。
压铸工件后处理操作规程
工件清理
对压铸完成的工件进行表面清 理,去除毛刺、飞边等杂质。
质量检查
对工件进行质量检查,包括尺 寸、外观、性能等方面,确保 符合要求。
涂装与包装
根据需要,对合格工件进行涂 装或包装,以保护表面不受损 伤或污染。
安全注意事项
在后处理过程中,应注意工件 温度,避免烫伤;操作人员应 佩戴防护用品,如口罩、手套
一讲压铸基本概念-PPT课件
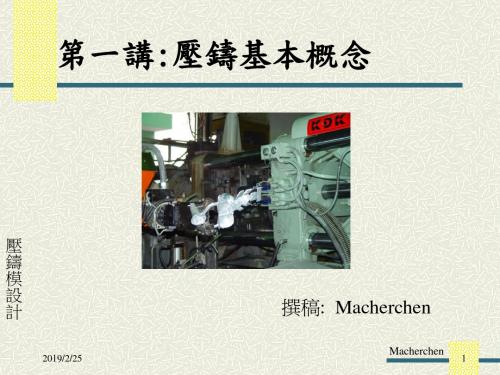
鋁: 2.0~2.5(最小直徑)
(六)文字: 凸凹紋﹐直紋
壓 鑄 模 設 計
例:平行紋(直紋)高0.7MM﹐間距1MM﹐角度60.5。 外俓Φ34.5mm 共104牙
2019/2/25
Macherchen
11
四.成型工藝
(七)螺紋﹐齒輪
合金 最小螺距(P) 最小螺紋外徑 最大螺紋長度
鋅
壓 鑄 模 設 計
二. 壓鑄概論
壓力鑄造概念: (鋁,錫,鋅,镁,鉛,銅,合金)
即將溶融合金在高壓,高速條件下充型並在高壓下冷卻凝固成型的一 種精密鑄造方法, 簡稱壓鑄,其最終產品是壓鑄件.
1.
壓力鑄造特性: 高速充填:通常澆口速度達30~60m/s之間. 充填時間很短:中小型件通常為0.02~0.2s之間. 高壓充填:熱室機壓力通常為70~350kg/c㎡ 溶湯的冷卻速度快
No.7 -Z33522 -Aged 24.5 -18 -67 28.8 -65.1 鑄 件 3.5~4.3 .005~.020 .25max .075
機 械 性
壓 強 度 (Kg/mm )
Al Mg
3.9~4.3 3.5~4.3
.025~.50 .02~.05
3.9~4.3 .03~.06 .075
最大壁厚與最小壁厚之比不要大于3﹕1(應設計壁厚 均勻﹐保証足夠強度與剛度的前提)
2019/2/25
Macherchen
7
四.成型工藝
(二)加強肋﹕大于或等于2.5MM﹐會降低抗拉強度﹐易產生氣孔﹐
縮孔。
設計原則﹕1﹐受力大﹐減小壁厚﹐改善強度.
2﹐對稱布置﹐壁厚均勻﹐避免縮孔氣孔.
壓 鑄 模 設 計
β
压铸模具基础知识介绍
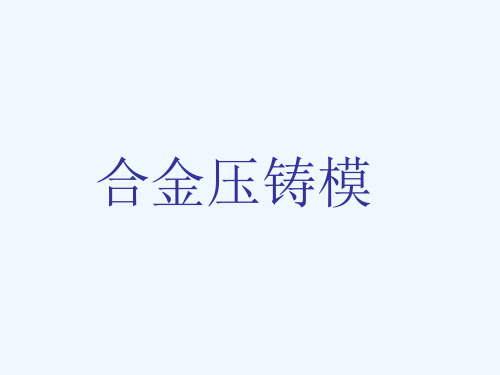
参数: 滑块的高度B ,宽度C按型芯尺寸决定,.滑块的长 度A与B, C有关,为使滑块工作时稳定要求 A≥0.7C A≥B
材料: T8A、T10A、H13 热处理: HRC 42~47
(6).限位块
作用: 滑块抽出后要求稳固保持在一定位置上,以便于再
次合模时斜销准确插入滑块斜孔,使滑块准确复位.
横浇道长度:取(直浇道)1/2 +(35~50) 横浇道长度尺寸不可以过短小,否那么使金属液起稳流和导
向作用不明显。
横浇道
3、内浇口:
内浇口应使金属液以最正确的流动状态充填型腔应先充填
型腔深腔部位,最后流向分型面,防止先封闭分型
面,防止金属液对型芯等薄弱部位冲击,易导致型
芯变形。
内浇口调整着从横浇道输送过来金属液速度,其位置和方向最
二 溢排系统:
据熔融金属在模具内填充情况,而开设排气通道。 用于容纳液态金属在充填过程中排出气体、杂物冷污合金等。
溢流槽
溢流槽的结构形式: (1)布置在模具分型面上的溢流槽 (2)布置在模具型腔内部的溢流槽。 其形式有: 杆形溢流槽 管形溢流槽 环形溢流槽 双级溢流槽 波纹状溢流槽
第二局部 压铸模浇排系统
一、 浇注系统:
引导金属液以一定的方式充填型腔,对金属液流动方向、 压力传递、充填速度、排气条件、模具的热平衡都能起 到控制和调节作用。 包括三个方面:
1。 直浇道 :
要求:有利压射力传递和金属液充填
平稳,。
对于冷室压铸模一般由压室和浇口套组成。
直浇道尺寸确实定是跟据铸件结构和重量等要 求来选择确立。
三 加热和冷却系统: 压铸模具在压铸生产前应进行充分地预热,并在压
铸过程中保持在一定温度范围内。 压铸生产中模具的温度由加热与冷却系统进行控制
材料: T8A、T10A、H13 热处理: HRC 42~47
(6).限位块
作用: 滑块抽出后要求稳固保持在一定位置上,以便于再
次合模时斜销准确插入滑块斜孔,使滑块准确复位.
横浇道长度:取(直浇道)1/2 +(35~50) 横浇道长度尺寸不可以过短小,否那么使金属液起稳流和导
向作用不明显。
横浇道
3、内浇口:
内浇口应使金属液以最正确的流动状态充填型腔应先充填
型腔深腔部位,最后流向分型面,防止先封闭分型
面,防止金属液对型芯等薄弱部位冲击,易导致型
芯变形。
内浇口调整着从横浇道输送过来金属液速度,其位置和方向最
二 溢排系统:
据熔融金属在模具内填充情况,而开设排气通道。 用于容纳液态金属在充填过程中排出气体、杂物冷污合金等。
溢流槽
溢流槽的结构形式: (1)布置在模具分型面上的溢流槽 (2)布置在模具型腔内部的溢流槽。 其形式有: 杆形溢流槽 管形溢流槽 环形溢流槽 双级溢流槽 波纹状溢流槽
第二局部 压铸模浇排系统
一、 浇注系统:
引导金属液以一定的方式充填型腔,对金属液流动方向、 压力传递、充填速度、排气条件、模具的热平衡都能起 到控制和调节作用。 包括三个方面:
1。 直浇道 :
要求:有利压射力传递和金属液充填
平稳,。
对于冷室压铸模一般由压室和浇口套组成。
直浇道尺寸确实定是跟据铸件结构和重量等要 求来选择确立。
三 加热和冷却系统: 压铸模具在压铸生产前应进行充分地预热,并在压
铸过程中保持在一定温度范围内。 压铸生产中模具的温度由加热与冷却系统进行控制
压铸模具绪论优选经典PPT

① 压铸机分类 按压室结构和布置方式分:卧式、立式 小型压铸机(热室<630KN,冷室<2500KN)
功率 中型(热室630KN-4000KN,冷室2500KN-6300KN) (锁模力)大型(热室>4000KN,冷室>6300KN)
Introduction
第一篇:压铸原理及常用压铸合金
② 热室压铸机压铸的基本原理与工艺过程
压铸成形工艺与模具设计
1
内容
简 介 考勤及考试 课程内容
2
第一篇 压铸原理及常用压铸合金 第二篇 压铸机的选用 第三篇 压铸件结构设计及压铸工艺 第四篇 压铸模设计
Introduction
第一篇:压铸原理及常用压铸合金
一、压铸的基本原理
1.压铸的实质及工艺过程 ① 压铸
⑴ 基本概念 压铸是压力铸造的简称,属于特种铸造,是在压铸机压射机构高压作用 下,使液态或半液态金属以较高的速度充填压铸模型腔,并在压力作用下成 形和凝固获得铸件的方法。 ⑵分类 按压铸材料分:单金属压铸、合金压铸(铁合金压铸、非铁合金压铸、 复合材料压铸) 按压铸机分:热室压铸(压室浸在保温坩埚内)、冷室压铸(压室与保 温炉分开) 按合金状态分:全液态压铸、半固态压铸 ⑶ 特点 高压:一般20—200MPa,最高500MPa 高速:0.5—120m/s
(3)巴顿的理论
Introduction
第一篇:压铸原理及常用压铸合金
⑥ 压铸缺陷 ⑴ 缺陷类型 几何缺陷:压铸件形状、尺寸与技术要求有偏离,尺寸超差、挠曲、变形等。 表面缺陷: 压铸件外观不良,出现花纹、流痕冷隔、斑点、缺肉、毛刺、飞边、缩痕、拉伤。 内部缺陷: 气孔、缩孔、缩松、裂纹、夹杂等、内部组织、机械性能不符合要求。 ⑵ 影响因素 压铸机引起:压铸机性能,所提供的能量能否满足所需要的压射条件(压射力、压射速度、锁模力)。压铸 工艺参数选择及调控是否合适,包括压力、速度、时间、冲头行程等。 压铸模引起:模具设计(模具结构、浇注系统尺寸及位置、顶杆及布局、冷却系统);模具加工(模具型腔表 面粗糙度、加工精度、硬度);模具使用(温度控制、表面清理、保养); 压铸件设计引起:压铸件壁厚、弯角位、拔模斜度、热节位置、深凹位); 压铸操作引起:合金浇注温度、熔炼温度、涂料喷涂量及操作、生产周期等; 合金料引起:原料及回炉料的成分、干净程度、配比、熔炼工艺等。
功率 中型(热室630KN-4000KN,冷室2500KN-6300KN) (锁模力)大型(热室>4000KN,冷室>6300KN)
Introduction
第一篇:压铸原理及常用压铸合金
② 热室压铸机压铸的基本原理与工艺过程
压铸成形工艺与模具设计
1
内容
简 介 考勤及考试 课程内容
2
第一篇 压铸原理及常用压铸合金 第二篇 压铸机的选用 第三篇 压铸件结构设计及压铸工艺 第四篇 压铸模设计
Introduction
第一篇:压铸原理及常用压铸合金
一、压铸的基本原理
1.压铸的实质及工艺过程 ① 压铸
⑴ 基本概念 压铸是压力铸造的简称,属于特种铸造,是在压铸机压射机构高压作用 下,使液态或半液态金属以较高的速度充填压铸模型腔,并在压力作用下成 形和凝固获得铸件的方法。 ⑵分类 按压铸材料分:单金属压铸、合金压铸(铁合金压铸、非铁合金压铸、 复合材料压铸) 按压铸机分:热室压铸(压室浸在保温坩埚内)、冷室压铸(压室与保 温炉分开) 按合金状态分:全液态压铸、半固态压铸 ⑶ 特点 高压:一般20—200MPa,最高500MPa 高速:0.5—120m/s
(3)巴顿的理论
Introduction
第一篇:压铸原理及常用压铸合金
⑥ 压铸缺陷 ⑴ 缺陷类型 几何缺陷:压铸件形状、尺寸与技术要求有偏离,尺寸超差、挠曲、变形等。 表面缺陷: 压铸件外观不良,出现花纹、流痕冷隔、斑点、缺肉、毛刺、飞边、缩痕、拉伤。 内部缺陷: 气孔、缩孔、缩松、裂纹、夹杂等、内部组织、机械性能不符合要求。 ⑵ 影响因素 压铸机引起:压铸机性能,所提供的能量能否满足所需要的压射条件(压射力、压射速度、锁模力)。压铸 工艺参数选择及调控是否合适,包括压力、速度、时间、冲头行程等。 压铸模引起:模具设计(模具结构、浇注系统尺寸及位置、顶杆及布局、冷却系统);模具加工(模具型腔表 面粗糙度、加工精度、硬度);模具使用(温度控制、表面清理、保养); 压铸件设计引起:压铸件壁厚、弯角位、拔模斜度、热节位置、深凹位); 压铸操作引起:合金浇注温度、熔炼温度、涂料喷涂量及操作、生产周期等; 合金料引起:原料及回炉料的成分、干净程度、配比、熔炼工艺等。
压铸培训教程.pptx

r最大= h
R=r+h
压
铸
當h1=h時﹕
模
r≧ h+h1
设
3
计
R=r+ h+h1
2
2020/8/16
K值
鋅﹕1/4 鋁﹕1/2
Macherchen
10
四.成型工艺
(五)孔
鋅:0.8~1.5(最小直径)
鋁:2.0~2.5(最小直径)
(六)文字:凸凹纹﹐直纹
压
铸 例:平行纹(直纹)高0.7MM﹐间距1MM﹐角度60.5。
压 铸 模 设 计
2020/8/16
由喷射﹑喷射流转变为压力流
Macherchen
5
三.压铸制程溶汤的流动方式
(二)压力流
因冲撞,磨擦和气体阻力等(抽象),运动能量耗尽(常发生在加强筋,
凸台,远离浇口之部位),具有接受后继金属液中供给的压力能,从而使金
属液沿着型腔内壁前进的特性.利用这特性,可便以型腔排气.在压力流充
13
五.压铸合金及其性能
压 铸 模 设 计
2020/8/16
鋅合金種類
合 商業習用編號
No.3
金
ASTM
AG40A
代
UNS
Z33251
號
SAE
903
Die Cast Aged
抗拉強度(Kg/mm2) 28.8 24.6
機 降伏強度(Kg/mm2) --
--
伸長率(%)
10
16
械 剪切強率(Kg/mm2) 21.8
铸
模 均匀﹐保证足够强度与刚度的前提)
设
计
2020/8/16
Macherchen
压铸模具基础知识介绍ppt

材料检验
对采购的材料进行质量检验,确保材料符合设计 要求。
材料储存与保管
对检验合格的原材料进行储存和保管,确保材料 在制造过程中不受损坏或变质。
模具加工阶段
粗加工
对模具毛坯进行粗加工,去除多余 的材料,初步形成模具的形状和结 构。
中间检查
对粗加工完成的模具进行中间检查 ,确保模具的形状和结构符合设计 要求。
02
压铸模具制造过程
设计阶段
1 2
模具设计
根据产品需求,进行模具的结构设计,确定模 具的形状、结构、尺寸等参数。
模具材料选择
根据模具的使用条件和寿命要求,选择合适的 材料,如铸铁、铸钢、铝合金等。
3
模具零件的标准化
对模具的零件进行标准化设计,以提高制造效 率和降低成本。
备料阶段
材料采购
根据模具设计要求,采购合适的材料,如钢材、 铝合金等。
04
压铸模具的使用与维护
压铸模具的使用方法
模具安装
根据模具尺寸、形状和压铸机型 号,正确安装模具,确保定位准 确、紧固可靠。
模具预热
使用前对模具进行预热,提高模 具温度,降低成型难度,提高产 品质量。
模具调试
根据产品要求和工艺参数,调试 模具压力、温度、时间等参数, 确保压铸件质量符合要求。
压铸模具的维护保养
压铸模具基础知识介绍ppt
xx年xx月xx日
contents
目录
• 压铸模具概述 • 压铸模具制造过程 • 压铸模具材料选择与处理 • 压铸模具的使用与维护 • 压铸模具的设计案例分析 • 总结与展望
01
压铸模具概述
定义与特点
定义
压铸模具是一种金属铸造工艺中使用的模具,通过将熔融的 金属注入到模具型腔中,冷却凝固后得到所需形状的零件。
对采购的材料进行质量检验,确保材料符合设计 要求。
材料储存与保管
对检验合格的原材料进行储存和保管,确保材料 在制造过程中不受损坏或变质。
模具加工阶段
粗加工
对模具毛坯进行粗加工,去除多余 的材料,初步形成模具的形状和结 构。
中间检查
对粗加工完成的模具进行中间检查 ,确保模具的形状和结构符合设计 要求。
02
压铸模具制造过程
设计阶段
1 2
模具设计
根据产品需求,进行模具的结构设计,确定模 具的形状、结构、尺寸等参数。
模具材料选择
根据模具的使用条件和寿命要求,选择合适的 材料,如铸铁、铸钢、铝合金等。
3
模具零件的标准化
对模具的零件进行标准化设计,以提高制造效 率和降低成本。
备料阶段
材料采购
根据模具设计要求,采购合适的材料,如钢材、 铝合金等。
04
压铸模具的使用与维护
压铸模具的使用方法
模具安装
根据模具尺寸、形状和压铸机型 号,正确安装模具,确保定位准 确、紧固可靠。
模具预热
使用前对模具进行预热,提高模 具温度,降低成型难度,提高产 品质量。
模具调试
根据产品要求和工艺参数,调试 模具压力、温度、时间等参数, 确保压铸件质量符合要求。
压铸模具的维护保养
压铸模具基础知识介绍ppt
xx年xx月xx日
contents
目录
• 压铸模具概述 • 压铸模具制造过程 • 压铸模具材料选择与处理 • 压铸模具的使用与维护 • 压铸模具的设计案例分析 • 总结与展望
01
压铸模具概述
定义与特点
定义
压铸模具是一种金属铸造工艺中使用的模具,通过将熔融的 金属注入到模具型腔中,冷却凝固后得到所需形状的零件。
单元1-5压铸模具制造基础课件

压铸模具制造基础
4.电极加工工艺 石墨电极在压型后,它的大小和形状就已经确定,但是压型后的生制品经过焙烧和石墨化
后,由于产生了一定程度的变形,表面上还粘附一些填充料等杂质,显得形状不规则,表面 粗糙不平,无法满足使用要求,必须经过机械加工,才能使用。
石墨电极的机械加工包括镗孔、车外圆和铣螺纹,与金属制品的加工相似。根据石墨电极 加工的生产特点,数控电极加工机床一般采用3机组的结构,分别完成镗孔、车外圆和铣螺 纹。
(1)模芯、滑块:H13、 DIEVAR(进口材料); (2)模套(翻砂、铸铁)、45钢;标准模套(日本40C); (3)滑块座:40Cr; (4)分流锥:H13; (5)顶板、压条:45钢。
不同材料,采用不同的刀具,进给速度、主轴转速和吃刀量来保证加工精度和效率。
压铸模具制造基础
2.引导孔加工 模芯引孔:确认材料尺寸,基准面、正反面。 (1)基准面一律向外与磨床加工,线切割,电火花、基准面一致,避免累积误差; (2)引孔注意压板位置在加工程序单上标注、位置及压板高度,必要时增加安全高度点以防刀 具撞压板; (3)模芯加工R角,有效面保持25-30mm反面加工R角要过切进去2mm,使模具装配简单。(注:模 芯毛胚余量一般0.7-1mm)反面R角实际最后过切1mm左右,引孔分中一般四面分中,除特殊情 况外。 (4)引孔刀具用φ10中心钻,划线刀具用φ6尖刀,加工R角用(刀尖圆角端铣刀),引孔深度3mm 划线深度0.2mm。 (5)编程工序;引孔用钻孔程序。划线与铣R角用轮廓走刀程序。
(5)加工工序: a. 先使用等高环绕方式精加工——加工整个工件。 b. 曲面投影精加工——加工曲面。 c. 区域精加工——加工滑块过道等要求比较高,电极加工不到的地方。
压铸模具制造基础
《压铸基本知识》课件

航空航天领域
压铸技术逐渐应用于航空航天领域,如飞机零部件、卫星结构件等 。
环保要求
1 2
环保法规
随着全球环保意识的提高,各国政府对压铸行业 的环保法规日益严格,要求企业采取有效措施降 低环境污染。
节能减排
压铸企业应积极采取节能减排措施,如余热回收 、废弃物再利用等,以降低能耗和减少排放。
3
绿色生产
项参数。
02
操作过程
按照工艺流程,依次完成合模 、填充、增压、保压、开模等 步骤,确保压铸件的质量和稳
定性。
03
注意事项
注意安全操作,避免烫伤和机 械伤害,同时要定期维护和保 养设备,确保设备的正常运行
和使用寿命。
03
压铸模具
模具设计
03
模具结构设计
分模面选择
浇注系统设计
根据产品需求,设计合理的模具结构,确 保产品成型效果和生产效率。
推广绿色生产技术,使用环保材料和工艺,从源 头减少污染物的产生,促进压铸行业的可持续发 展。
THANKS
模具维护
定期检查
维修与更换
定期对模具进行检查,确保其处于良 好状态。
Hale Waihona Puke 对于损坏的模具部件,应及时进行维 修或更换。
保养与润滑
定期对模具进行保养和润滑,延长其 使用寿命。
04
压铸工艺
压铸温度
压铸温度
压铸过程中,模具和金属液的温 度是影响压铸件质量的重要因素 。合适的温度可以提高金属液的 流动性,减少气孔和裂纹等缺陷
《压铸基本知识》ppt课件
目录
• 压铸简介 • 压铸机 • 压铸模具 • 压铸工艺 • 压铸产品缺陷及防止措施 • 压铸行业发展趋势
压铸技术逐渐应用于航空航天领域,如飞机零部件、卫星结构件等 。
环保要求
1 2
环保法规
随着全球环保意识的提高,各国政府对压铸行业 的环保法规日益严格,要求企业采取有效措施降 低环境污染。
节能减排
压铸企业应积极采取节能减排措施,如余热回收 、废弃物再利用等,以降低能耗和减少排放。
3
绿色生产
项参数。
02
操作过程
按照工艺流程,依次完成合模 、填充、增压、保压、开模等 步骤,确保压铸件的质量和稳
定性。
03
注意事项
注意安全操作,避免烫伤和机 械伤害,同时要定期维护和保 养设备,确保设备的正常运行
和使用寿命。
03
压铸模具
模具设计
03
模具结构设计
分模面选择
浇注系统设计
根据产品需求,设计合理的模具结构,确 保产品成型效果和生产效率。
推广绿色生产技术,使用环保材料和工艺,从源 头减少污染物的产生,促进压铸行业的可持续发 展。
THANKS
模具维护
定期检查
维修与更换
定期对模具进行检查,确保其处于良 好状态。
Hale Waihona Puke 对于损坏的模具部件,应及时进行维 修或更换。
保养与润滑
定期对模具进行保养和润滑,延长其 使用寿命。
04
压铸工艺
压铸温度
压铸温度
压铸过程中,模具和金属液的温 度是影响压铸件质量的重要因素 。合适的温度可以提高金属液的 流动性,减少气孔和裂纹等缺陷
《压铸基本知识》ppt课件
目录
• 压铸简介 • 压铸机 • 压铸模具 • 压铸工艺 • 压铸产品缺陷及防止措施 • 压铸行业发展趋势