压铸工艺教程
压铸教程
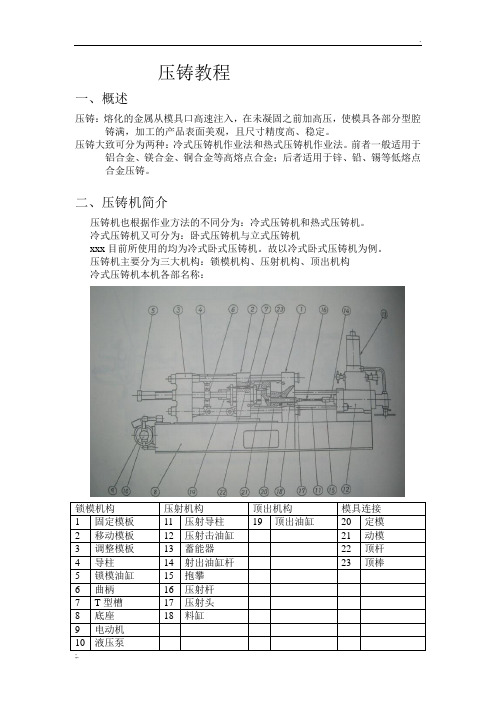
压铸教程一、概述压铸:熔化的金属从模具口高速注入,在未凝固之前加高压,使模具各部分型腔铸满,加工的产品表面美观,且尺寸精度高、稳定。
压铸大致可分为两种:冷式压铸机作业法和热式压铸机作业法。
前者一般适用于铝合金、镁合金、铜合金等高熔点合金;后者适用于锌、铅、锡等低熔点合金压铸。
二、压铸机简介压铸机也根据作业方法的不同分为:冷式压铸机和热式压铸机。
冷式压铸机又可分为:卧式压铸机与立式压铸机xxx目前所使用的均为冷式卧式压铸机。
故以冷式卧式压铸机为例。
压铸机主要分为三大机构:锁模机构、压射机构、顶出机构冷式压铸机本机各部名称:锁模机构压射机构顶出机构模具连接1 固定模板11 压射导柱19 顶出油缸20 定模2 移动模板12 压射击油缸21 动模3 调整模板13 蓄能器22 顶杆4 导柱14 射出油缸杆23 顶棒5 锁模油缸15 抱攀6 曲柄16 压射杆7 T型槽17 压射头8 底座18 料缸9 电动机10 液压泵下面是冷式压铸机各装置的典型布局主要有压铸机本机、给汤机、喷涂机、取出机等组成。
三、压铸安全操作注意事项1、开机作业前,必须确认“安全门”、“非常停止按钮”、“操作电源开关”、的功能是否正常。
2、必须确认开合模、与取出机、喷雾机之间的安全互锁关系是否正常。
3、严禁两人或更多的人同时操作按钮。
当有帮手时(换模),必须在相互确认,高声呼喊,方可下一步动作。
4、压铸作业时,模具分型面前方严禁站人。
下面是铸造作业时发生灾害事故的分析:(数据来源日本)a 模具分型面最容易飞散铝液引起烫伤事故。
43%b 开模时候的料饼裂碎会引起烫伤事故。
7%c 被顶出板夹住引起事故。
6%d 被曲柄夹住引起事故。
2%e 其他的灾害事故42%5、取出机活动范围内严禁站人。
6、清理或修理模具时,必须关闭“操作电源开关”或按下“非常停止”按钮。
7、给汤机勺子作业前要预热、涂钛白粉、烘干,以免造成爆炸。
熔解炉中严禁注水。
严禁站人铸造运行中不要靠近模具的分型面8、压铸机、模具修理时,如有身体一部分要进入动作结构时,必须切断电源开关,以免机械误动造成人身伤害。
压铸简易教程.

简易压铸教程一、压射过程的阶段及运动方式和作用1.卧式压铸机压射过程典型的三阶段压射过程经过不断的发展,演变为多点压射过程。
多点压射的实质则是对该三个阶段分别各自进行分解为若干小段(或称为“转换点”)卧式冷室压铸典型的三阶段压射过程示意图压射过程解析卧式冷室压铸典型的三阶段奔压射曲线示意图二、压铸合金压然合金通常为有色金属,按目前的用量来说,依次为铝合金,锌合金、镁合金和铜合金。
黑色金属中的铸铁也可以采用压铸,但用量很少。
在几种压铸机中,卧式冷室压铸机具有技术含量高,通用性大、性能参数宽、型号规格多(特别是大型)等特点,上述的压铸合金都可以在卧式冷室压铸机上生产。
1.压铸铝合金压铸铝合金的密度为2.5~2.9g/cm3。
压铸铝合金的特点:优点:比强度大(强度/密谋=9~15);烦蚀性、烦磨性好;导热性、导电性好;切削性能好缺点:铝硅系合金易粘模;对金属坩埚有较强的腐蚀;体收缩大,易产生缩孔。
2.压铸锌合金压铸用锌合金密度为6.6~6.7g/cm3压铸锌合金的特点:优点:熔点低,不易粘模、填充性能良好、电镀性好多用于常温场合。
缺点:锌合金易老化、抗腐蚀性差且易生成晶间腐蚀导致强度和尺寸发生变化。
3.压铸镁合金压铸镁合金的密度为1.77~1.81g/cm3压铸镁合金的特点优点:比强度大(强度/密度=14~15);刚度和减震性好。
缺点:易氧化,要求熔化、保温设备结构复杂、工艺性复杂;高温脆性,热裂倾向大;高温强度稍差;耐蚀性差。
4.压铸铜合金压铸铜合金的密度为8.2~8.5g/cm3压铸铜合金的特点优点:力学性能好;导电导热好;耐磨性好;耐蚀性好。
缺点:熔点高,模具和压机的寿命低;成本高。
三、压铸工艺参数压铸工艺参数(1)----压力参数压力是取得铸件组织致密和轮廓清晰的主要因素。
1.压射力1.1 压射力及其计算压射力是压铸机压射机构中推动压射活塞的力。
压射力的计算公式为:p y=P g(П*D*D/4)。
压铸的工艺流程

压铸的工艺流程
《压铸工艺流程》
压铸是一种常用的金属成型工艺,通过在高压下将熔融金属注入模具中,以获得所需形状的零件。
压铸工艺具有生产效率高、成型精度高以及表面光洁度好等优点,因此在汽车制造、家电制造等行业得到了广泛应用。
下面将介绍一下压铸的工艺流程。
首先,准备模具。
根据产品的形状和尺寸,设计并制作成型模具。
模具的材质通常选用高强度的合金钢或耐磨耐蚀的材料,以满足高压注射的要求。
其次,准备熔铸金属。
通常压铸采用的是铝合金、锌合金等金属,需要将其熔化成液态,在一定的温度和精确的成分下进行配料。
然后,进行压铸成型。
将熔融金属注入模具中,施加高压使其充分填充模具腔,并在一定的时间内凝固成型。
压铸机通常采用液压系统,能提供足够的压力和控制,以保证成型的精确度和表面光洁度。
最后,脱模和处理。
待零件完全凝固后,打开模具,取出成品。
接着进行去毛刺、打磨、清洗等处理工序,使零件表面光洁,满足产品要求。
总的来说,压铸工艺流程包括模具准备、熔铸金属准备、压铸成型和零件处理等环节。
在整个过程中需要注意控制温度、压
力和成分等参数,以确保成品的质量和精度。
压铸工艺是一种高效、精密的金属成型工艺,对于提高产品质量和生产效率有着重要的作用。
压铸产品工艺流程

压铸产品工艺流程
《压铸产品工艺流程》
压铸是一种将液态金属注入到模具中,在高压下进行固化的制造工艺。
该工艺可以生产出高精度、高强度的金属零件,被广泛应用于汽车、电子、航空航天等领域。
下面是压铸产品的典型工艺流程:
1. 模具设计:首先根据产品的要求设计出合适的模具。
这包括模具的结构、尺寸、排气系统等方面的设计。
2. 液态金属注入:将金属材料(如铝合金、镁合金等)加热至液态状态后,将其注入到模具腔室中。
这一步需要严格控制金属的温度和注入速度,以确保成型品的质量。
3. 高压固化:在金属注入后,用高压将金属材料压实并固化。
这一过程能够在较短的时间内将金属冷却定型,从而保证产品的精度和表面质量。
4. 除模和清洁:成型后的产品需要进行除模处理,将其从模具中取出。
然后可能需要进行表面清洁和修整,以去除可能存在的瑕疵和毛刺。
5. 后处理:对产品进行表面处理、机加工、组装等后续工序,以满足不同产品的使用要求。
以上就是压铸产品的典型工艺流程,通过严格管理每个环节,
可以生产出高质量、精密的压铸产品,满足各种应用领域的需求。
压铸件工艺流程
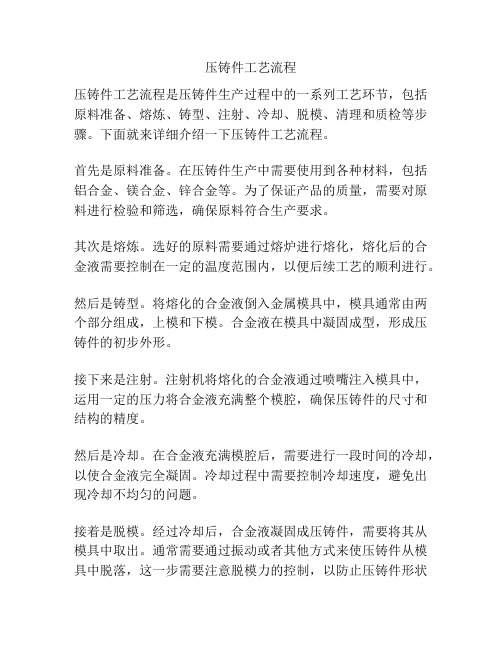
压铸件工艺流程压铸件工艺流程是压铸件生产过程中的一系列工艺环节,包括原料准备、熔炼、铸型、注射、冷却、脱模、清理和质检等步骤。
下面就来详细介绍一下压铸件工艺流程。
首先是原料准备。
在压铸件生产中需要使用到各种材料,包括铝合金、镁合金、锌合金等。
为了保证产品的质量,需要对原料进行检验和筛选,确保原料符合生产要求。
其次是熔炼。
选好的原料需要通过熔炉进行熔化,熔化后的合金液需要控制在一定的温度范围内,以便后续工艺的顺利进行。
然后是铸型。
将熔化的合金液倒入金属模具中,模具通常由两个部分组成,上模和下模。
合金液在模具中凝固成型,形成压铸件的初步外形。
接下来是注射。
注射机将熔化的合金液通过喷嘴注入模具中,运用一定的压力将合金液充满整个模腔,确保压铸件的尺寸和结构的精度。
然后是冷却。
在合金液充满模腔后,需要进行一段时间的冷却,以使合金液完全凝固。
冷却过程中需要控制冷却速度,避免出现冷却不均匀的问题。
接着是脱模。
经过冷却后,合金液凝固成压铸件,需要将其从模具中取出。
通常需要通过振动或者其他方式来使压铸件从模具中脱落,这一步需要注意脱模力的控制,以防止压铸件形状变形。
然后是清理。
脱模后的压铸件表面通常会有一些余渣和污垢,需要进行清理工作。
可以通过切削、喷砂等方式对压铸件表面进行处理,以获得光洁的表面。
最后是质检。
生产完成的压铸件需要进行质量检验,以确保产品符合设计要求。
对压铸件的尺寸、外观和物理性能等方面进行检测,如果发现不合格的情况需要重新制作。
以上就是压铸件工艺流程的主要步骤。
整个工艺流程中需要密切配合各个环节,保证每一步都严格按照要求进行,以获得高质量的压铸件产品。
同时,工艺流程中需要注意安全和环保等要求,确保生产过程的安全和环境的可持续发展。
压铸工艺设计培训教材

05:36
11
3.2.2 压射比压
压射比压P比可由压射力或工作压力P压和驱动(压射)缸及压射冲头直径求得,即
05:36
12
压射比压的作用和影响
(1)对压铸件力学性能的影响 压射比压大合金结晶细,细 晶层增厚。由于填充特性改善,压射比压大,压铸件表面质量提 高,气孔缺陷减轻,从而抗拉强度提高,但伸长率有所降低。
通常在保证压铸件成形和满足质量要求的前提下选用较低的压射 比压。选择设定压射比压所考虑的因素见表3.1,备种压铸合金 的计算压射比压见表3.2,通常实际压射比压低于计算压射比压, 其压力损失折算系数K见表3.3。
05:36
14
05:36
15
05:36
16
3.3 压射速度与充填速度
3.3.1 压射速度
( 2)对填充条件的影响 金属液在高的压射比压作用下填充 型腔动能加大,流动性改善,有利于克服浇注系统和充填簿壁压 铸件型腔的阻力,提高簿壁压铸件质量。
是否压射比压越高越好?
05:36
13
压射比压的选择
当压铸机上的压射系统没有增压机构时,Ill、IV两个阶段的压射 比压是相同的。当压铸机上的压射系统设有增压机构时,这两个 阶段的比压不同。这时,填充比压用来克服浇注系统和型腔中金 属液的流动阻力(特别是内浇口处的阻力),使金属液流保证达 到所需要的内浇口速度;而增压比压则决定了正在凝固的金属液 受到的压力及这时所形成的胀型力的大小。
1.压射速度的概念 压室内压射冲头推动金属液的移动速度称为压射速度(又称冲头速度)。一般压射
速度有二级和三级两种。压射速度由压铸机的特性所决定,压铸机所给定的压射速度 一般在0.1-7m/s范围内可调。
2.压射速度的作用 (1)压射冲头以一定的速度较慢地推动金属液,使金属液充满压室前端并堆聚在内
压铸生产培训教程
压铸生产培训教程一、引言压铸是一种将熔融金属在高压下注入模具型腔,并在压力作用下快速凝固成型的精密铸造方法。
作为一种先进的金属成型技术,压铸具有高效、精密、复杂等特点,广泛应用于汽车、摩托车、电子、通讯、家电等行业。
本教程旨在为从事压铸生产的技术人员提供系统的培训,使其掌握压铸工艺的基本原理、设备操作、模具设计、质量控制等方面的知识,提高生产技能和产品质量。
二、压铸工艺基本原理1. 压铸过程(1)熔化金属:将金属原料熔化成液态金属,并通过过滤去除杂质。
(2)注入模具:将液态金属在高压下注入模具型腔。
(3)冷却凝固:金属在模具型腔内快速冷却凝固,形成铸件。
(4)开模取出铸件:待铸件完全凝固后,打开模具,取出铸件。
(5)后处理:对铸件进行去毛刺、抛光、热处理等后处理工序。
2. 压铸设备压铸设备主要包括压铸机、熔化炉、模具、冷却系统等。
压铸机是压铸生产的核心设备,根据压铸力大小可分为热室压铸机和冷室压铸机。
3. 压铸模具(1)模具结构:包括型腔、浇注系统、排溢系统、冷却系统等。
(2)模具材料:要求具有良好的导热性、耐磨性和抗热疲劳性能。
(3)模具加工:采用高精度加工设备,确保模具尺寸精度和表面质量。
三、压铸生产操作1. 开机准备(1)检查设备:确保设备正常运行,无异常声响和漏油现象。
(2)检查模具:确认模具完好无损,安装到位。
(3)检查熔化炉:确保熔化炉内金属熔化均匀,温度适中。
2. 压铸操作(1)合模:将模具合拢,确保模具闭合严密。
(2)注射:启动压铸机,将熔融金属注入模具型腔。
(3)保压:在金属凝固过程中保持一定的压力,以防止缩孔、气孔等缺陷。
(4)开模:待铸件完全凝固后,打开模具,取出铸件。
3. 安全注意事项(1)遵守设备操作规程,严禁违章操作。
(2)穿戴好劳动保护用品,防止烫伤、割伤等事故。
(3)保持现场整洁,及时清理废料和油污。
四、压铸质量控制1. 铸件质量检验(1)尺寸精度:通过测量工具检验铸件尺寸是否符合要求。
铝合金压铸工艺流程
铝合金压铸工艺流程
铝合金压铸工艺流程:铝合金压铸是指将铝合金熔体注入铝合金活塞式压铸机的熔炉中,通过压力将熔体注入铸型腔中形成铸件的一种工艺。
下面就铝合金压铸工艺流程进行详细介绍。
首先,准备工作。
确定产品的设计图纸,包括产品尺寸、形状、工艺要求等。
根据图纸确定压铸机的型号和参数,并调整好压铸机的各项参数。
其次,准备原料。
选择合适的铝合金材料,将其加入熔炉中进行熔化。
在熔炉中需要注意控制熔化温度和熔化时间,确保原料完全熔化均匀。
然后,准备模具。
根据产品的形状和尺寸,制作合适的模具。
模具要经过精确的加工和处理,以保证铸件的质量。
将模具安装在压铸机上,并根据需要调整模具的开合间距和顶出力。
接下来,注入熔体。
当熔体达到合适的温度和流动性时,用熔体桶将熔体送到压铸机的溶池中。
在注入过程中,需要控制注入速度和压力,以保证熔体能够充分填充模具的每个腔体。
然后,填充模具腔体。
当熔体注入到模具腔体中后,通过压力将熔体充分填充并冷却固化。
在填充过程中,需要注意控制压铸机的压力和注射速率,以避免产生气孔、缩孔等缺陷。
最后,取出铸件。
待铸件充分冷却固化后,打开模具,将铸件从模具中取出。
在取出过程中,需要注意避免铸件变形或损坏。
整个铝合金压铸工艺流程结束后,还需要进行一些后续处理,包括去毛刺、修磨、抛光等,以提高铸件的表面质量和尺寸精度。
以上就是铝合金压铸工艺流程的详细介绍。
压铸工艺在制造业中应用广泛,可以生产出形状复杂、尺寸精确的铝合金铸件,广泛应用于汽车、电子、航空航天等领域。
压铸工艺及操作规程(3篇)
第1篇一、压铸工艺概述压铸是一种将金属熔体在高压下注入到铸模中,冷却凝固后得到所需的铸件的金属成型方法。
压铸工艺具有生产效率高、尺寸精度好、表面光洁度高等优点,广泛应用于汽车、家电、电子等行业。
二、压铸工艺流程1. 铝合金熔炼:将铝锭或铝合金锭放入熔炼炉中,通过加热熔化成铝液。
2. 模具准备:根据产品图纸制作或选用合适的模具,并对模具进行预热。
3. 铝液准备:将熔化的铝液过滤、除气、去除杂质,使其达到压铸要求。
4. 压射成型:将铝液注入到预热的模具中,在高压下使铝液充满模具型腔。
5. 冷却凝固:铝液在模具中冷却凝固,形成铸件。
6. 取件:将铸件从模具中取出。
7. 清理:对铸件进行去毛刺、抛光等表面处理。
8. 检验:对铸件进行尺寸、表面质量、机械性能等检验。
三、压铸操作规程1. 安全操作:操作者必须穿戴好劳保用品,如工作服、手套、眼镜等,确保人身安全。
2. 设备检查:开机前,检查设备是否正常运行,如油压、冷却系统、控制系统等。
3. 模具准备:根据产品图纸制作或选用合适的模具,并对模具进行预热。
4. 铝液准备:将熔化的铝液过滤、除气、去除杂质,使其达到压铸要求。
5. 压射成型:将铝液注入到预热的模具中,在高压下使铝液充满模具型腔。
6. 冷却凝固:铝液在模具中冷却凝固,形成铸件。
7. 取件:将铸件从模具中取出。
8. 清理:对铸件进行去毛刺、抛光等表面处理。
9. 检验:对铸件进行尺寸、表面质量、机械性能等检验。
10. 设备维护:定期对设备进行保养、检修,确保设备正常运行。
四、注意事项1. 铝液温度:铝液温度应控制在合适的范围内,过高或过低都会影响铸件质量。
2. 压射压力:压射压力应根据产品材质、厚度等因素进行调整,确保铸件成型质量。
3. 模具预热:模具预热温度应控制在合适的范围内,过高或过低都会影响铸件质量。
4. 铝液过滤:铝液过滤可有效去除杂质,提高铸件质量。
5. 模具维护:定期对模具进行检查、清洗、维护,确保模具使用寿命。
压铸操作流程
压铸操作流程压铸机操作规范1.机床启动;2.启动机床前,必须全面检查机床确保机床处于正常状态;3.手动润滑后再开机;4.点动启动机床并观察机床运转情况,如有异常立即停机;5.机床启动后,应开冷却水,以防油温升高;6.机床发生故障或报警信号响起,应立即查看原因后报修,严禁机床带病工作;压铸操作工艺流程模具安装→调试→清理预热模具→喷刷涂料→合模→涂料准备→涂料配制→压铸→冷却与凝固→开模→顶出铸件→质量检验→成品→废品→合金溶化一、模具安装模具安装前,压铸工必须全面了解模具结构状况,包括:1.模具有无抽芯;动模抽芯,还是静模抽芯;润滑抽芯,还是液压抽芯。
2.是否需要安装复位拉杆。
3.浇口套大小,熔杯大小,结合尺寸是否一致。
4.是否中心浇口。
5.顶棒位置、大小、长短是否合适。
二、操作规范1.根据模具情况更换熔杯冲头,必要时调节压射升降机构。
2.检查动静模板,确保表面无异物、无高点。
3.正确安装吊具,在确保安全的情况下起吊,并确保模具进入机床前无摇动,以免撞伤机床。
4.根据模具情况,正确安装模具。
特别注意,带有液压抽芯的模具,必须将机床相对应抽芯状态调到“选择”并且抽芯在动模的,要调到“锁模前”抽芯。
5.压紧模具,接好油管及冷却水管完成模具安装。
三、模具调试1.调节机床开档选择合适的锁模力。
2.调节压射跟出行程,检查冲头冷却水,确保无泄漏。
四、压铸生产1.压铸生产前,对模具型腔、顶杆、复位杆、导柱、导套、型芯、滑道等全面刷油。
2.在冷模状态下,在工艺无特殊规定情况下应将机床二快和增压关闭。
3.根据零件重量,合理选择浇注量进行试压,并相应调节,确保料饼厚度。
4.模具在冷模的状态下,多刷油少喷涂,模具热起来按正常喷涂料。
5.模具到了正常温度后,将二快和增压打开,按正常程序生产。
6.生产的首件产品,必须进行全面的检查,做好记录,并保留由检验员检验。
7.在正常生产过程中,压铸工要根据压铸工艺要求,正确控制并及时调整如下要素:①喷涂②料温控制③模温控制④料饼厚度控制⑤分型面清洗⑥滑动部位润滑8.在正常生产过程中,要按要求检查铸件质量,如有异常,及时停止生产做好修理或更换模具工作。