[教育]油气集输工艺及设备进展
油气集输处理工艺发展现状及发展前景
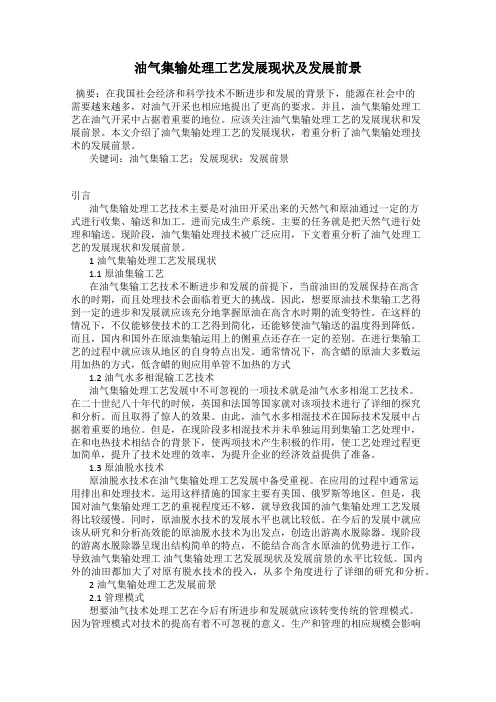
油气集输处理工艺发展现状及发展前景摘要:在我国社会经济和科学技术不断进步和发展的背景下,能源在社会中的需要越来越多,对油气开采也相应地提出了更高的要求。
并且,油气集输处理工艺在油气开采中占据着重要的地位。
应该关注油气集输处理工艺的发展现状和发展前景。
本文介绍了油气集输处理工艺的发展现状,着重分析了油气集输处理技术的发展前景。
关键词:油气集输工艺;发展现状;发展前景引言油气集输处理工艺技术主要是对油田开采出来的天然气和原油通过一定的方式进行收集、输送和加工。
进而完成生产系统。
主要的任务就是把天然气进行处理和输送。
现阶段,油气集输处理技术被广泛应用,下文着重分析了油气处理工艺的发展现状和发展前景。
1油气集输处理工艺发展现状1.1原油集输工艺在油气集输工艺技术不断进步和发展的前提下,当前油田的发展保持在高含水的时期,而且处理技术会面临着更大的挑战。
因此,想要原油技术集输工艺得到一定的进步和发展就应该充分地掌握原油在高含水时期的流变特性。
在这样的情况下,不仅能够使技术的工艺得到简化,还能够使油气输送的温度得到降低。
而且,国内和国外在原油集输运用上的侧重点还存在一定的差别。
在进行集输工艺的过程中就应该从地区的自身特点出发。
通常情况下,高含蜡的原油大多数运用加热的方式,低含蜡的则应用单管不加热的方式1.2油气水多相混输工艺技术油气集输处理工艺发展中不可忽视的一项技术就是油气水多相混工艺技术。
在二十世纪八十年代的时候,英国和法国等国家就对该项技术进行了详细的探究和分析。
而且取得了惊人的效果。
由此,油气水多相混技术在国际技术发展中占据着重要的地位。
但是,在现阶段多相混技术并未单独运用到集输工艺处理中,在和电热技术相结合的背景下,使两项技术产生积极的作用,使工艺处理过程更加简单,提升了技术处理的效率,为提升企业的经济效益提供了准备。
1.3原油脱水技术原油脱水技术在油气集输处理工艺发展中备受重视。
在应用的过程中通常运用排出和处理技术。
油气集输新技术、新工艺、新设备

第一部分油气混输技术一、多相流输送工艺在自然条件十分恶劣的沙漠油田和海洋油田开发建设过程中,油气集输系统的建设投资和运行管理费用要比常规的陆上油田开发高得多。
由于两相或多相混输,省去了一条管线,可节省开发工程投资和操作费用,另外还可使恶劣地域(或海域)内的油气田得到开发。
据预测,利用这种技术可使开发工程投资减少10~40%。
发达国家对这类油田已有采用长距离油气混输工艺技术的,并已取得了较好的经济效益(见表1)。
到目前为止,世界上的长距离混输管线已超过200条,其中大部分集中在北海、美国、澳大利亚、加勒比海,但这些混输管线多属于天然气-凝析液管道。
据报道北海Troll气田到Oseberg油田的混输管线长50Km,所输流体是未经处理的井流体,是油、气、水、砂等的混合物。
进入九十年代,随着我国海洋石油的开发,先后在渤海铺设了锦州20-2天然气/凝析液混输管线和东海平湖天然气/凝析液混输管线。
锦州20-2海底管道全长51km,水下部分约48.57km,采用12英寸管线,外敷5mm煤焦油瓷漆防腐层,50mm混凝土加重层。
管材为X52,立管区管材X56。
海管为开沟敷设,覆土高度2m以上,采用自然覆土法,只在离着陆点4km范围内采用局部覆土。
海管的最大水深为15.425m,每10个焊口设牺牲阳极一个,管道着陆点处有绝缘接头。
海管于92年5~10月施工,年底投产。
平均输气量为1.0×106m3 /d,凝析油为600m3/d,管道起点压力为6.0~6.5MPa,压降大约为1.0~1.3MPa。
平湖油气田位于东海大陆架西湖凹陷西斜坡,水深约87.5m。
处理过的天然气通过东海平湖凝析天然气管道从海上平台输送到陆上的油气处理场。
平湖油气田包括一座钻井采油平台及两条海底管线和陆上油气处理厂。
其中一条海管是长为386.14km,管子外径为355.6mm 的气管线,从平台至南汇嘴;另一条为长约305.8km,管子外径为254mm的油管线,从平台至岱山岛;陆上处理厂位于上海市的南汇嘴。
分析油气集输工艺技术在生产中的应用

分析油气集输工艺技术在生产中的应用随着全球能源需求的增长和技术的不断进步,油气集输工艺技术在油气生产中的应用越来越广泛,对于提高油气生产效率、降低成本、保障安全生产起到了至关重要的作用。
本文将从油气集输工艺技术的概念、发展现状和在生产中的应用方面进行分析。
一、油气集输工艺技术的概念及发展现状油气集输工艺技术是指将采油、采气、作业和输送等一系列生产过程综合起来,采用先进的工艺和设备,对原油和天然气进行处理、储存、运输的一种技术。
随着油气勘探开发的深入和对资源利用的要求越来越高,油气集输技术也在不断发展壮大。
目前,国际上较为先进的油气集输工艺技术主要包括:智能化管道系统、大型气液输送系统、多相流动技术等。
1. 智能化管道系统:利用先进的传感器技术、数据处理技术和物联网技术,实现对管道系统各项参数的实时监测和控制,提高管道的安全性和运行效率。
还能够对管道进行远程监控和智能化运维管理,大大降低了人工成本和维护成本。
2. 大型气液输送系统:采用高压气体压缩技术和超长距离输送技术,将采集到的气体压缩成液态,通过管道输送到地面处理站或者销售点,提高了天然气的运输效率和经济性。
3. 多相流动技术:通过对含油气体和水的多相流动进行分离处理,实现油气与水的有效分离和提取,提高了原油的采集效率和净化程度,减少了生产成本。
以上这些技术的应用大大提高了油气生产的效率和安全性,为油气开采提供了有力的技术支持。
1. 智能化管道系统在油气生产中的应用智能化管道系统是当前油气集输工艺技术的热点之一,其应用主要表现在以下几个方面:(1)实时监测:通过在管道系统中部署各类传感器,可以实时监测管道内的流体压力、流速、温度等参数,及时掌握管道的运行状态,对管道运行中的异常情况进行预警和报警处理,保障了管道的安全运行。
(3)运行维护:智能化管道系统可以实现对管道设备的远程诊断和维护,实现了设备的远程运维管理,减少了人工巡检和维护的频率,降低了运行成本。
油气集输工艺技术的发展与应用

油气集输工艺技术的发展与应用摘要:油气集输是对原油、天然气进行收集、存储、输送、加工、处理等的生产工艺过程。
油气集输具有三个重要方面的功能和作用:一是对采集液进行气体、液体分离和脱水;二是脱水后原油和天然气的输送;三是将原油、天然气从供给方输送给客户。
它具有面广、线长、点多的生产特征,同时又具有工艺复杂、高温高压、易燃易爆、生产连续性强以及火灾风险性大等特征。
随着油田建设的现代信息化,油气集输问题越来越受到重视,在某种程度上来讲一个油气田的油气集输工艺技术水平,影响和决定了整个油气田开发建设的综合技术水平和管理水平。
关键词:收集处理技术供应改进脱水一、油气集输工艺技术发展现状目前国内外油气集输方面工艺技术的发展情况主要有原油集输工艺方面对于含蜡量高、凝固性强的原油,国内外普遍采用多级布站、加热工艺、单井集中计量、大站集中处理等集输工艺,我国的辽河油田和华北油田等使用该项工艺,美国加拿大普遍采取添加化学药剂的方法来降低原油的稳定性和凝固点以进行单管集输对于含蜡量低、凝点低的原油一般采取加热的单管集输工艺。
随着油田进入高含水期原油的流变性增强相应的集输工艺也应该逐步降低输送温度或者进行常温输送。
二、油气水多相混输工艺技术方面油气水多相混输工艺集输属于一项行业前沿技术,对该项集输进行了大量研究多相混输技术不电热技术相配合可以大幅度地简化集输工艺和降低集输工程投资成本,在油气集输领域中该项集输具有较大的发展潜力和远景。
三、原油脱水技术方面对于含水量较高的原油,国内外目前普遍采用两阶段脱水工艺。
使用大罐沉降、聚结脱水等方法脱除原油中的游离水。
对于含水量高、凝点低、粘性低的原油,国内外较多地采用热化学脱水工艺。
国外对于原油脱水中间过渡层的处理十分重视幵采取了与项技术进行处理,在原油脱水技术方面趋向于高效游离水脱除器的研制。
四、现行油田油气集输工艺技术面临的问题随着油田开发进入到了高含水原油的开发阶段,油田挖潜效果和稳产难度逐渐变大,已经建设的集输设施负荷率逐年下降系统的效率和能耗存在很多问题具体表现如下:高含水的原油其油水分离特性的发生了变化,游离水的沉降时间和沉降温度都有所改变,使得现行的原油脱水工艺出现了不适应性,已经不能满足油田节能降耗的需要,需要对现有的原油集输工艺进行改进,集输流程节能的关键是如何降低集油阶段的热能消耗。
油气集输工艺过程

油气集输是一种重要的工艺,它是把油气从油田或天然气田带到销售点或加工厂的管
道输送过程。
油气集输工艺过程是由几个部分组成的,包括油气采收系统、油气加工系统
和油气输送系统。
首先,油气采收系统是油气集输工艺过程的第一部分。
它是把油气从油田或天然气田
采集而来的系统,采收系统分为采收站和主采收站两部分。
采收站需要设置泵站和控制系统,用于将油气从油田或天然气田抽取到管线中。
主采收站是采收系统的核心,它负责把油气从管线中抽取出来,并进行初步的净化和处理。
其次,油气加工系统是油气集输工艺过程的第二部分。
油气加工系统的目的是把采收
的油气进行进一步的清洁、分离、润滑、压缩等处理工作,以符合用户的要求。
油气加工
系统包括油气净化装置、油气分离装置、油气润滑装置和油气压缩装置等。
最后,油气输送系统是油气集输工艺过程的第三部分。
油气输送系统负责将加工处理
后的油气输送到用户点或加工厂。
油气输送系统由油气输送管线和油气泵站组成,油气管线是把油气从加工厂或用户点输送到销售点的管线。
油气泵站则负责把油气从管线中抽取出来,并送至用户点。
总之,油气集输工艺过程由油气采收系统、油气加工系统和油气输送系统三部分组成,它是把油气从油田或天然气田带到销售点或加工厂的管道输送过程,以确保油气的可靠供应。
海上油气集输工艺与设备

海底电缆输送:通过海底电缆将电力从陆地输送到海上油田,用于油气生产
05
海底光缆输送:通过海底光缆将数据从陆地输送到海上油田,用于油气生产监控和控制
06
油气处理技术
STEP4
STEP3
STEP2
STEP1
油气分离技术:利用物理和化学方法将油气分离
油气净化技术:去除油气中的杂质和水分
油气输送技术:将油气从海上平台输送到陆地
02
油气输送泵:用于将油气混合物输送至处理设备
03
油气处理设备:用于处理油气混合物,如脱水、脱硫等
04
油气计量设备:用于测量油气混合物的流量和压力
05
油气储存设备:用于储存处理后的油气
06
油气输送管道:用于将处理后的油气输送至陆地或海上平台
油气处理设备
油气分离器:用于分离油气混合物中的油和水
油气冷却器:用于冷却油气混合物,降低油气分离器的负荷
膜分离:利用膜材料的选择性渗透性进行分离
电化学分离:利用电化学反应进行分离
油气输送技术
海底管道输送:通过海底管道将油气从海上油田输送到陆地
01
油轮运输:通过油轮将油气从海上油田运输到陆地
02
液化天然气(LNG)运输:将天然气液化后,通过LNG运输船运输到陆地
03
压缩天然气(CNG)运输:将天然气压缩后,通过CNG运输船运输到陆地
演讲人
01.
02.
03.
04.
目录
海上油气集输工艺
海上油气集输设备
海上油气集输系统的优化
海上油气集输技术的发展趋势
油气分离技术
重力分离:利用油、气、水的密度差异进行分离
离心分离:利用高速旋转的离心力进行分离
油气集输主要专用设备的发展与现状
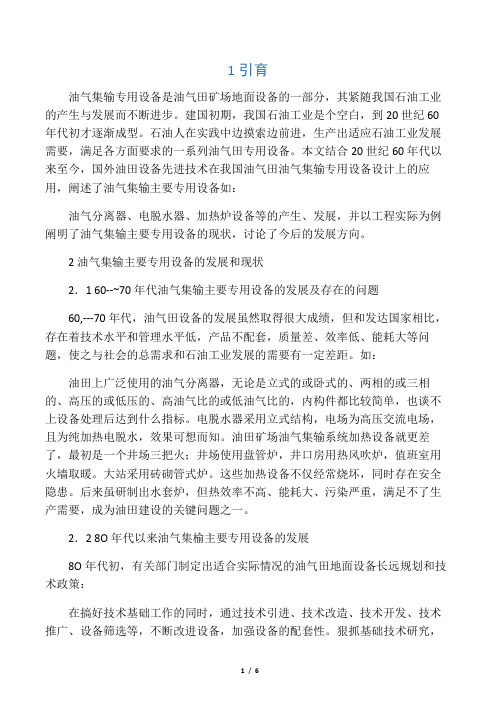
1引育油气集输专用设备是油气田矿场地面设备的一部分,其紧随我国石油工业的产生与发展而不断进步。
建国初期,我国石油工业是个空白,到20世纪60年代初才逐渐成型。
石油人在实践中边摸索边前进,生产出适应石油工业发展需要,满足各方面要求的一系列油气田专用设备。
本文结合20世纪60年代以来至今,国外油田设备先进技术在我国油气田油气集输专用设备设计上的应用,阐述了油气集输主要专用设备如:油气分离器、电脱水器、加热炉设备等的产生、发展,并以工程实际为例阐明了油气集输主要专用设备的现状,讨论了今后的发展方向。
2油气集输主要专用设备的发展和现状2.1 60--~70年代油气集输主要专用设备的发展及存在的问题60,---70年代,油气田设备的发展虽然取得很大成绩,但和发达国家相比,存在着技术水平和管理水平低,产品不配套,质量差、效率低、能耗大等问题,使之与社会的总需求和石油工业发展的需要有一定差距。
如:油田上广泛使用的油气分离器,无论是立式的或卧式的、两相的或三相的、高压的或低压的、高油气比的或低油气比的,内构件都比较简单,也谈不上设备处理后达到什么指标。
电脱水器采用立式结构,电场为高压交流电场,且为纯加热电脱水,效果可想而知。
油田矿场油气集输系统加热设备就更差了,最初是一个井场三把火;井场使用盘管炉,井口房用热风吹炉,值班室用火墙取暖。
大站采用砖砌管式炉。
这些加热设备不仅经常烧坏,同时存在安全隐患。
后来虽研制出水套炉,但热效率不高、能耗大、污染严重,满足不了生产需要,成为油田建设的关键问题之一。
2.2 8O年代以来油气集榆主要专用设备的发展8O年代初,有关部门制定出适合实际情况的油气田地面设备长远规划和技术政策:在搞好技术基础工作的同时,通过技术引进、技术改造、技术开发、技术推广、设备筛选等,不断改进设备,加强设备的配套性。
狠抓基础技术研究,加速油田设备更新改造;增加设备品种,使产品成龙配套;加强产品质量监督检验,提高质量全面改进技术水平,提高经济效益和社会效益,降低损耗。
探析油气集输工艺技术与发展趋势

探析油气集输工艺技术与发展趋势摘要:随着我国经济的飞速发展,油气能源的需要量与日俱增,然而在油气田开发工艺中油气集输是一项必不可少的工艺流程,可以说油气集输在原油的处理中起着不可替代的作用。
我国目前油气集输的现状是机遇与挑战并存,为促进我国油气集输处理技术的发展,本文系统的阐述了油气集输的工艺流程以及对未来油气集输工艺的展望。
关键词:油气集输能源油气田开发机遇挑战发展一、引言油气集输处理工艺就是将油田开采出来的天然气和原油进行收集、输送、储存和初步加工的系统生产工艺过程。
油气集输工艺主要是负责将分离出的天然气输送到天然气处理厂进行再次处理或深加工将油气处理站把合格的原油输送到油田原油库进行储备。
同时,将天然气、油田原油库压气站以不同的方式将处理合格的原油、天然气外输给用户。
油气收集处理工艺具有线长、油田点多、面广的生产特性,同时又集工艺复杂、易燃易爆、生产连不断深人,油气集输处理工艺将面临着新的挑战,生产越来越受到大家的重视,油气集输工艺技术在很大程度上决定油气田开发水平,并与油气企业的经济效益和社会效益息息相关。
当今国内外油气集输工艺技术有很多种,而且各有各的特点,他们的侧重点和发展趋势也不同。
油气集输生产和油田物资探、钻井等作业相比有着线长、压力容器集中等特点。
油气集输面广、工艺复杂,生产连续性强、火灾中出现危险的可能性大,因此,对于油气集输工艺现状及趋势的分析具有很重要的价值。
二、油气集输工艺技术1.原油脱水技术国外一直很重视在原油脱水过渡层的处理方面,采取的是排出和技术专项措施,典型的是美国和俄罗斯。
而我国在处理过渡层等问题方面不够关注和重视,其中原油脱水趋向于研发高能效的游离水脱除器。
但现行的游离水脱除器只是相对简单的卧式结构,并不能充分利用高含水原油的优势,可采取减小游离水脱除相关设施的规模大小。
投入精力研制高效的游离水脱除器。
国内外油田在原油脱水工艺方面都进行了大量的研究。
对于高含水原油,国内外采取的主要是两段脱水工艺。
- 1、下载文档前请自行甄别文档内容的完整性,平台不提供额外的编辑、内容补充、找答案等附加服务。
- 2、"仅部分预览"的文档,不可在线预览部分如存在完整性等问题,可反馈申请退款(可完整预览的文档不适用该条件!)。
- 3、如文档侵犯您的权益,请联系客服反馈,我们会尽快为您处理(人工客服工作时间:9:00-18:30)。
(
输主油,用下泵面种的类几众种多产,品主是要用以量离最心大泵、为用二)
途最广泛的泵设备。
输
油
泵
1、几种泵举例
ZA型石油化工流程泵
适合输送清洁或含有固体颗粒、低温或高 温、中性或有腐蚀性及气液两相流液体, 尤其对于输送各种温度的液态石油化工产 品,各种温度和浓度的酸、碱、盐溶液和 其他有腐蚀性的液体尤为适用。具体结构 如图1所示,该产品技术为瑞士苏尔寿泵公 司技术。
近年来,又兴起了无机复合热管,它跟传统的热 管(如钢—水热管)技术相比,其优点是:适 用温度范围广,使工作范围扩大到材料使用的温 度极限,可在350℃以上高温环境下工作,不易 产生爆管,结构紧凑,流动阻力小,不易堵塞, 其良好的均温性能可有效地防止烟气酸温度腐蚀 ,良好的耐热性能可有效地提高其使用寿命。
• 2.生产设备、管理和维护手段:差距更大。 • 国外油田在生产上普遍采用了先进的自动化数据采集与 控制技术,对生产工艺过程的实时监控已成为惯例,如输 油管道采用SCADA (数字采集与监控系统)系统,站内 采用DCS(分布式控制系统)系统,跟生产辅助的电力、 通讯系统也实现了自动化。 • 而我国特别是东部老油田在自动化方面还限于单件的自 动化仪表的使用,除了少数生产设施外,自动化基本上处 于起步阶段;加热炉、输油泵等生产设备陈旧落后,收发 油计量误差大,能耗也较大。 • 我们认为,我国油气集输专业的技术水平与国外相比有 相当大的差距,总体管理技术水平比发达国家落后10~ 20年左右,而且差距有继续拉大的趋势
时间的停输会酿成凝管事故。
输
1.2 密闭输送工艺
长距离输油管道是从开式输送发展到密闭 输送方式的。目前常用的有两种。
“旁接油罐”运行的优点是有缓冲过程, 允许调节的时间长,对自动化水平要求低 。
“从泵到泵”的密闭输油工艺改变了中间 站进旁接罐的开式运行方式,使全线成为 一个水力系统,可以充分利用上站压力, 节约能耗,可节约中间站储油设备投资, 而且也避免了旁接油罐的油气蒸发损耗。 密闭输油工艺取决于设备的可靠性、自动
• 原油输送方式
• 输送原油的粘度和凝固点比较低,可以采用不加热直接 输送的方式; • 具有较高凝固点和粘度的原油,就需要经过加热后输送 ,或者经过改性,采用不加热的常温输送方式。 • 北美国家的输油管道多是输送低凝点、低粘度原油,所 以多为不加热输送。对于凝点和粘度较高的原油均采用加 热输送(如美国全美管道和科林加管道)。 • 随着原油流变性的研究,原油添加化学降凝剂后常温输 送技术也应用于一些原油管道运行管理中。由于实际生产 需要和常温输送的工艺优越性,促使此项技术日趋成熟。 近20年来,我国有10多条原油管道试验研究了添加化学降 凝剂输送技术,取得的技术成果和经济效益是十分明显的 。
水套炉
水套炉是火筒式加热炉,间接加热,其工作原理 是燃料在炉体下部的火筒烟管内燃烧,热量通过 火筒烟管传递给中间传热介质“水”,水再加热 内有介质流动的盘管。
水套炉单台功率小,主要用于小流量加热,优点 是使用安全,不结焦。
炉体与炉管之间用密封填料密封,松紧程度由压 盖法兰调节。炉体上焊有温度计插孔及压力表和 安全阀接头。通过水箱、漏斗和平衡管给炉内加 水。炉体放在用耐火材料砌成的炉墙上,顶上敷 绝热材料保温。
热管加热炉
热管是一个密闭的、具有一定真空度的管 件,内部装有符合温度变化范围要求的工 质。热管利用内部工质的相变传热,极大 地提高了传热效果,其当量导热系数是紫 铜的数千倍,因此热管被称为“超导热体 ”。
热管加热炉结构示意图
加热炉发展现状及发展趋势
目前,我国在余热节能领域的应用,以碳钢— 水热管为主,如锅炉的省煤器、空气预热器等, 取得了明显的经济效益。但是碳钢—水热管在 高温下容易爆裂,限制了应用范围。
1. 3 优式化,运在S行C技AD术A是系国统外中多基采本取上的都运装行有方优优化 化运行控制软件,它可在不考虑调速运 的基础上,对管道的运行方案进行优行 化,使管道在最经济的状态下运行,技 减消小除低节输流量损时失的。不匹配性,减少乃至术
SCADA(数字采集与监控系统)
输油泵机组的优化运行
油气集输生产最常用的加热炉是燃油管式 加热炉,从炉型上多为方箱式。
现场运行的加热炉示意图
•管式加热炉
管式加热炉火焰直接加热,具有单台功率高、升 温速度快、加热温度高、耗钢量小等优点。管式 炉四周是用耐火砖砌筑的炉墙和成排的炉管,炉 管分两部分,直接受炉膛火焰辐射加热的为辐射 管,受烟道气对流加热的对对流管。炉子的燃烧 器是将燃油经机械雾化或蒸汽雾化(与水蒸汽混 合),在高压下通过油嘴喷出燃烧,空气从风门 进入。管式炉种类较多,目前油田应用比较多的 是卧式管式加热炉,热负荷规格有1000kW、 2000kW、2500kW。燃料以原油为主,采用轻 型快装结构,工厂预制,现场组装。加热炉热效 率为82%~85%。
40年代中期以后,开始敷设出油管线,用蒸汽管伴热,在 选油站进行油气分离、油罐计量原油和储存,油田气经计 量后,部分通过供气管线,作为工业和民用燃料,部分就 地放空。
50年代以后,随着新油田的不断出现,集输管网、油井产 物计量、分离、接转,原油脱水和原油储存等工艺技术亦 相应发展。
70年代,集输工艺不断完善,不加热(常温)集输、油罐 烃蒸气回收、原油稳定、油田气处理和外输油气计量等技 术都有所发展。
直接加热炉大部分是七十年代建设的,在新建加 热炉时已被淘汰,这类加热炉体积庞大,炉管易 结焦,热效率较低。效率低的主要原因是排烟温 度偏高,炉膛为负压,漏风多,体积大,炉体保 温性差,导致散热损失很大。方箱式加热炉不仅 效率低,另一个突出缺点是安全性差,炉管(特 别是处于底部的炉管)易发生腐蚀穿孔,炉内高 温火焰接触还容易造成油管高温强度降低而破裂 ,造成原油泄漏而极易引起火灾、爆炸事故。
高
凝
点
我国生产的原油多属高含蜡、高凝固点、、 高 油粘来度说原,油输。送对工于艺凝可固分点为、两粘种度类较型高:的一原是高 加热输送,另一是常温输送。我们在加热粘
输送高凝、高粘原油方面积累了丰富的经原 验 到热,力但条加件热的输制送约有,其二弱是点一,旦一发是生低事输故量停受油
输,必须立即抢修,及时恢复运行,较长的
对输油泵机组本身进行改造,可用拆级、 车削叶轮、改变泵转速、更新高效泵
大小泵搭配,即选配合适的不同规格的输 油泵
是合理确定输油量,使输量和泵额定输量 尽可能一致,减少节流损失,最大限度地 提高泵的运行效率
1.
4
改用先炉后泵流程
节
改造输油设备,提高运行效率
能
选用高效输油设备
改
输油泵调速
近年来,国内还研究了利用热管技术来改造传统加热 炉的结构,如辽河油田设计院设计了热管加热炉,即 运用“火筒壁—热管、盘管壁—热管”的复式传热 ,强化了传热,提高了炉效,减小了炉体体积。以 700Kw的regr 加热炉为例,与同负荷的常规水套炉 相比,热效率提高10%,达到85%以上,节约钢材 40%,降低造价21%,减少占地面积30%,节约投 资2万多元。
造
1.
5 S控C制AD中A心(的数主字机采、集设与在监各控站系的统远)程系控统制由终设端在S(C
R两T级U)的和分高布性式能控的制通系信统系。统构成了一个相当A于D 80年代以前,我国长输管道基本上是常规仪A表 检80测年,代就中地期控以制来。,在铁大线、东黄复线上安系装
了此从后美,国新R建e的xn长or输d管公道司大引多进配的备SC了AD我A国系或统引。统进
油气集输公司气井上使用的加热炉多为50KW的 水套炉,以生产的天然气为燃料。
水套炉结构示意图
热媒加热炉
热媒加热炉采用间接加热方式,即燃油先 加热一种载热介质—导热油,导热油再加 热原油。
由主炉体和换热器以及连接管路组成,主 炉体可以是卧式或立式圆筒式加热炉,加 热热媒,换热器是热媒与被加热介质换热 的装置。
胜利油田滨南采油厂二首站4台加热炉、稠油末站2 台加热炉全部燃用重油,采用蒸汽雾化燃烧方式,冬 季也由外来蒸汽加热和雾化原油。加热炉排烟温度为 260℃左右,采用无机导热热管回收余热后,排烟温 度降低到170℃左右。回收加热炉余热产生的蒸汽满 足了燃油加热和取暖需要,节约了能量,取得了显著 的经济效益和社会效益。
(二)油田集油流程举例
1、双管掺活性水流程
2、三级布站单管油气集输流程
3、单管环形集油流程
4、稠油集输流程
(1)高温集油流程:单管加热集油流程和掺稀 降粘流程。
(2)掺蒸汽集油流程
二.国内外油气集输技术差距
•1.生产工艺方面:原油管道输送方面的差距最大, 自50年代以来,世界上发达国家的输油管道基本上 普及了密闭输送工艺流程,而我国输油工艺还普遍 采用开式流程运行和加热输送工艺,能耗大。天然 气和油田气处理工艺相差不大。油田伴生气的回收 ,则靠管道将联合站进行原油处理生产的伴生气汇 集起来,由压缩机加压,然后进行轻烃回收。轻烃 回收一般采取辅助浅冷和高压膨胀制冷凝液分馏生 产工艺。天然气地面生产工艺比较简单,流程是: 天然气经井口采气树后,首先进加热炉加热、然后 由气嘴进行配产和节流降压、进集气站分离器分离 出水、砂、油等杂质,最后经计量后外输。
三.输油工艺及进展
• 1. 概述
• 长距离输油管道通常是指距离长、管径大、输 量高的原油管道,输送压力高而且平稳。由输油 站和管路两部分组成,输油站分为首站、若干中 间加压站、若干中间加热站及末站; • 其任务是供给油流一定的压力能和热能,将原 油安全、经济地输送给用户; • 管路上每隔一定距离设有为减少事故危害、便 于抢修,可紧急关闭的若干截断阀室以及阴极保 护站。
的SCADA系统。对于今后建设的长输管道, SCADA系统将成为必不可少的组成部分。
四.输油设备进展
加热炉 输油泵
(一)加热炉
加热炉是将燃料燃烧产生的热量传递给被 加热介质而使其温度升高的一种加热设备 。在油气集输系统中,它的作用是将原油 、天然气等加热至工艺所要求的温度,以 便进行加工和输送。