MSA测量系统分析报告材料作业指导书
(MSA)作业指导书
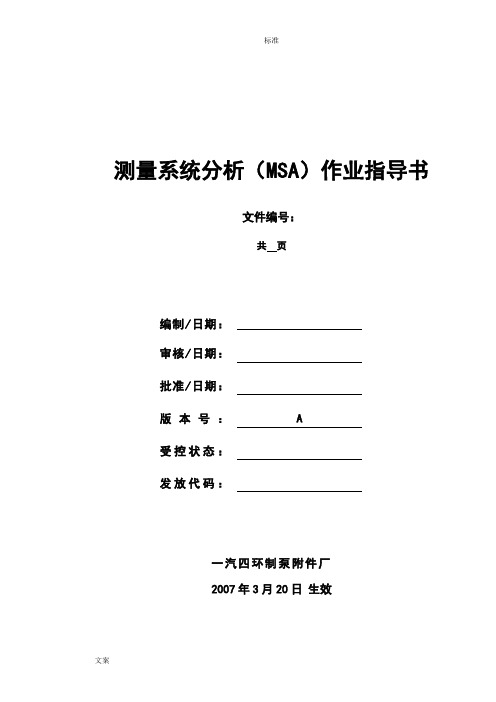
标准文案错误!未找到引用源。
文件编号:共页编制/日期:审核/日期:批准/日期:版本号: A受控状态:发放代码:一汽四环制泵附件厂2007年3月20日生效目录一、目的 (2)二、参考文件 (2)三、术语 (2)四、测量系统分析 (2)(一)分析的原则 (2)(二)稳定性分析 (3)(三)偏倚分析 (3)(四)线性分析 (5)(五)双性(GRR或R&R)分析 (7)(六)计数型量具的测量系统分析 (14)一、目的为公司各类简单的计量型、计数型量具的测量系统分析提供指导。
二、参考文件测量系统分析参考手册第三版三、术语1、测量系统误差模型:本作业指导书采用的误差模型为S.W.I.P.E模型,该模型指出测量系统变差来源于以下几大方面:标准(Standard)、零件(Work)、仪器(I)、人员/程序(Person/Procedure)、环境(E)2、测量系统:对测量单元进行量化或对被测的特性进行评估,所使用的仪器或量具、标准、操作、方法、夹具、软件、人员、环境及假设的集合。
3、分辨力:测量装置和标准的测量解析度、刻度限制、或最小可检出的单位。
与最小可读单位研究,即通常所说的最小刻度值,但当仪器刻度较粗略时,允许将最小刻度值估读为原来的一半作为仪器的可视分辨力。
4、重复性:当测量条件已被确定和定义——在确定的零件、仪器、标准、方法、操作者、环境和假设之下,测量系统内部的变差。
5、再现性:传统上将再现性称为“评价人之间”的变差(AV)。
指的是不同评价人使用相同的仪器对同一产品上的同一特性,进行测量所得的平均值的变差。
但对于操作者不是变差的主要原因的测量过程,上述说法是不正确的。
ASTM的定义为:现现性是指测量的系统之间或条件之间的平均值变差。
它不但包括评价人的变差,同时还可能包括:量具、试验室及环境的不同,除此之外,还包括重复性。
6、偏倚:对相同零件上同一特性的观测平均值与真值(参考值)的差异。
7、线性:在测量设备预期的工作(测量)量程内,偏倚值的差异。
MSA测量系统分析作业指导书
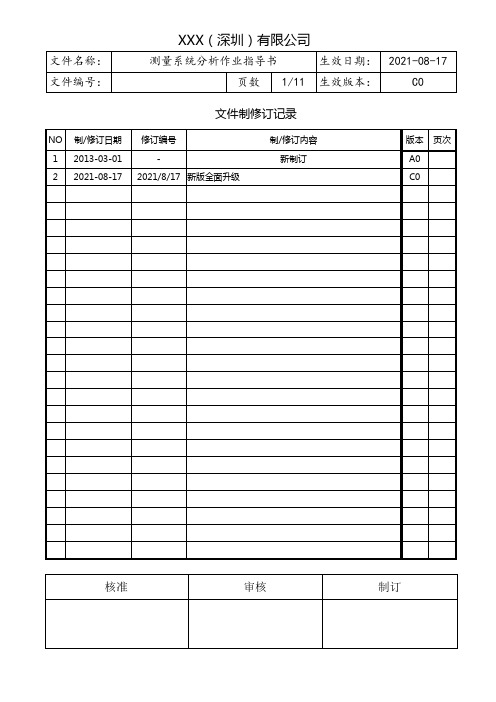
文件制修订记录1.0目的评估测量系统的变差,确保测量系统能够满足测量产品的要求;通过测是系统的分析,对不可接受或风险较大的测量系统,提出相应的改进措施并实施,努力减少测量的变差2.0范围适用于公司测量系统分析;控制计划涉及的所有检测器具控制计划涉及的所有检测器具。
3.0职责4.04.1测量系统分析计划的制订4.1.1确定要采用的研究方法;4.1.2在考虑图下因素基础上确定测量者的数量、样件数量和重复测量次数。
➢特性重要性—如研究测量关键特性的测量系统需要采用更多的样件或增加对每个样件的重复测量次数,以保证分析结果的置信水平。
➢被测对象的结果特点—对尺寸大或重量大的零件采用较少数量的样件,增加对每个样件重复测量次数来保证分析结果的置信水平。
4.1.3选择日常使用过程的测量系统人员参加研究。
4.1.4在过程中选择能够代表过程的整个工作范围的样件。
4.1.5量具最小刻度应该不超过预期的过程变差的十分之一(特殊情况下,经过小组评审,虑费用,五分之一也可接受)。
4.1.6规定测量所应遵循的程序,确定要测量的特性。
4.1.7设计测量系统分析的研究方式。
➢确保各次读数的统计独立性;➢测量读数应该顾及到可能获得的最接近数值;➢规定专人对测量系统分析的过程进行监督;➢每个测量者都应以使用同样的方法和步骤获取读数(根据测量特性,可能需要相同环境测量)。
5.0重复性和再现性(均值法)。
5.1术语5.1.1重复性——又称设备变差(符号EV),是指在固定和规定的测量条件下由一位测量者使用一种测量仪器,连续(短期)多次测量同一试样的同一特性时获得的测量变差。
它是系统内变差。
5.1.2再现性——又称评价人变差(符号AV),是指由不同的评价人使用相同的测量仪器,测量同一试样的同一特性时测量平均值的变差。
它是系统间变差。
5.1.3GRR——又称量具重复性和再现性,它是对测量系统重复性和再现性合成变差的估计5.1.4零件变差——符号PV,指零件与零件之间的变差。
MSA作业指导书
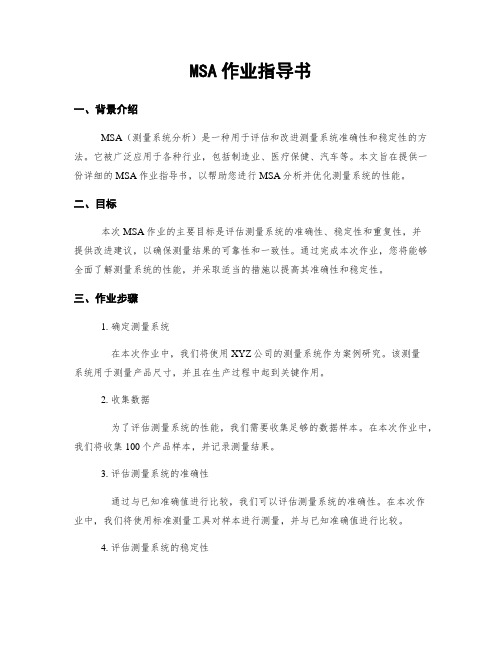
MSA作业指导书一、背景介绍MSA(测量系统分析)是一种用于评估和改进测量系统准确性和稳定性的方法。
它被广泛应用于各种行业,包括制造业、医疗保健、汽车等。
本文旨在提供一份详细的MSA作业指导书,以帮助您进行MSA分析并优化测量系统的性能。
二、目标本次MSA作业的主要目标是评估测量系统的准确性、稳定性和重复性,并提供改进建议,以确保测量结果的可靠性和一致性。
通过完成本次作业,您将能够全面了解测量系统的性能,并采取适当的措施以提高其准确性和稳定性。
三、作业步骤1. 确定测量系统在本次作业中,我们将使用XYZ公司的测量系统作为案例研究。
该测量系统用于测量产品尺寸,并且在生产过程中起到关键作用。
2. 收集数据为了评估测量系统的性能,我们需要收集足够的数据样本。
在本次作业中,我们将收集100个产品样本,并记录测量结果。
3. 评估测量系统的准确性通过与已知准确值进行比较,我们可以评估测量系统的准确性。
在本次作业中,我们将使用标准测量工具对样本进行测量,并与已知准确值进行比较。
4. 评估测量系统的稳定性测量系统的稳定性是指在重复测量相同样本时,测量结果的一致性。
我们将使用重复测量方法来评估测量系统的稳定性。
5. 评估测量系统的重复性重复性是指在不同操作员、不同时间和不同测量设备下,测量结果的一致性。
我们将通过多个操作员和多个测量设备来评估测量系统的重复性。
6. 分析结果并提出改进建议在完成数据收集和评估后,我们将对结果进行分析,并提出改进建议。
这些建议可能涉及调整测量设备、改进操作流程或提供员工培训等。
四、数据收集和分析在本次作业中,我们将收集100个产品样本的测量数据,并使用统计软件对数据进行分析。
通过分析数据,我们可以得出以下结论:- 测量系统的准确性在可接受范围内,与已知准确值的差异不超过0.1毫米。
- 测量系统的稳定性良好,重复测量结果的差异不超过0.05毫米。
- 测量系统的重复性较差,不同操作员和不同测量设备下的测量结果差异较大。
MSA作业指导书

MSA作业指导书一、引言MSA(测量系统分析)是一种用于评估和改进测量系统的方法。
它能够帮助我们确定测量系统的准确性、稳定性和重复性,从而确保我们所使用的数据是可靠的。
本指导书旨在为您提供关于MSA的详细信息和指导,以便您能够正确地执行和应用MSA方法。
二、背景在制造和生产过程中,测量系统扮演着至关重要的角色。
它们用于测量和评估产品的特性,从而确保产品的质量符合要求。
然而,如果测量系统本身存在问题,那么所得到的数据将是不准确的,从而导致错误的判断和决策。
因此,对测量系统进行评估和改进是至关重要的。
三、MSA的目的MSA的主要目的是评估测量系统的能力和稳定性,以确保其能够提供准确、一致和可靠的测量结果。
通过使用MSA方法,我们可以识别和消除测量系统中的误差和变异,从而提高测量系统的性能。
四、MSA的步骤1. 确定测量系统的类型:首先,我们需要确定所使用的测量系统的类型。
常见的测量系统类型包括计量工具、传感器、显微镜等。
不同类型的测量系统可能需要不同的评估方法。
2. 收集测量数据:接下来,我们需要收集一组样本数据,以便对测量系统进行评估。
这些数据应该是真实的、充分的,并且涵盖了测量系统可能遇到的各种情况。
3. 分析数据:在此步骤中,我们将对收集到的数据进行统计分析,以评估测量系统的准确性、稳定性和重复性。
常用的统计指标包括均值、方差、标准偏差等。
4. 评估测量系统的能力:基于数据分析的结果,我们可以评估测量系统的能力。
常用的评估方法包括测量系统能力指数(Cpk)、测量系统误差(ME)等。
这些指标可以帮助我们判断测量系统是否满足要求。
5. 改进测量系统:如果评估结果显示测量系统存在问题,我们需要采取相应的措施来改进测量系统的性能。
可能的改进方法包括校准仪器、更换传感器、调整测量方法等。
五、MSA的工具和技术在执行MSA过程中,我们可以使用一些常见的工具和技术来帮助我们进行数据分析和评估。
这些工具和技术包括直方图、散点图、方差分析、回归分析等。
测量系统分析(MSA)作业指导书
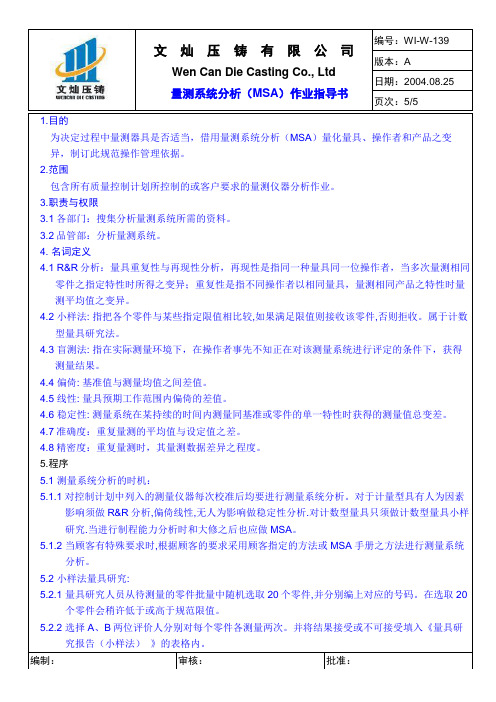
Ⅲ. %R&R>30%,表示该测量系统不可接收,必须加以改进。
Ⅳ.判定结果记录于《量具重复性和再现性报告》判定栏内。
D ndc(区别分类数)
ndc应该四舍五入到整数,要能大于或等于5。
5.4偏倚&线性分析:
5.4.1基于过程变差,在测量系统工作范围内选5个零件,确定它们的基准值,由一位评价人对每个零
件测量大于10次,零件随机抽取.将数据填入偏倚/线性分析表。
5.4.2计算零件偏倚,分析偏倚与基准的线性关系
5.4.3判别与原因分析:偏倚受控及具有线性关系则可以接受
5.4.4 A当偏差过大可分析下面几种原因: B当系统为非线性时可分析下面几种原因:
A1标准或基准值误差B1仪器没有正确校准
A2仪器磨损B2仪器磨损
A3操作不当B3标准量具误差
5.5稳定性分析:
挑选3-5个样品在规定的时间内(一般为一个月)观察其随时间变化偏倚的总变差。将数据填入
稳定性分析表。如变差受控则接受.如有超控或周期性变化则查找分析原因直到受控为止。
5.6 MSA分析相关记录之保存应依照《记录管理程序》执行。
6.记录
6.1量具重复性和再现性报告WI-W-139-01
1.目的
为决定过程中量测器具是否适当,借用量测系统分析(MSA)量化量具、操作者和产品之变
异,制订此规范操作管理依据。
2.范围
包含所有质量控制计划所控制的或客户要求的量测仪器分析作业。
3.职责与权限
3.1各部门:搜集分析量测系统所需的资料。
3.2品管部:分析量测系统。
4.名词定义
4.1 R&R分析:量具重复性与再现性分析,再现性是指同一种量具同一位操作者,当多次量测相同
MSA作业指导书
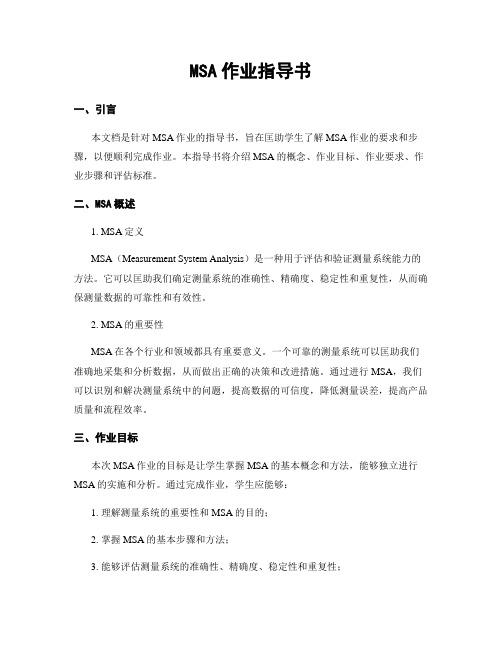
MSA作业指导书一、引言本文档是针对MSA作业的指导书,旨在匡助学生了解MSA作业的要求和步骤,以便顺利完成作业。
本指导书将介绍MSA的概念、作业目标、作业要求、作业步骤和评估标准。
二、MSA概述1. MSA定义MSA(Measurement System Analysis)是一种用于评估和验证测量系统能力的方法。
它可以匡助我们确定测量系统的准确性、精确度、稳定性和重复性,从而确保测量数据的可靠性和有效性。
2. MSA的重要性MSA在各个行业和领域都具有重要意义。
一个可靠的测量系统可以匡助我们准确地采集和分析数据,从而做出正确的决策和改进措施。
通过进行MSA,我们可以识别和解决测量系统中的问题,提高数据的可信度,降低测量误差,提高产品质量和流程效率。
三、作业目标本次MSA作业的目标是让学生掌握MSA的基本概念和方法,能够独立进行MSA的实施和分析。
通过完成作业,学生应能够:1. 理解测量系统的重要性和MSA的目的;2. 掌握MSA的基本步骤和方法;3. 能够评估测量系统的准确性、精确度、稳定性和重复性;4. 能够根据MSA结果提出改进建议。
四、作业要求1. 选择测量系统学生需要选择一个测量系统进行MSA分析。
这个测量系统可以是实际生产中使用的测量设备,也可以是实验室中的测量仪器。
学生需要提供测量系统的详细说明,包括测量对象、测量方法和测量数据的采集方式。
2. 实施MSA分析学生需要按照MSA的步骤进行实施。
具体步骤包括:a. 采集测量数据:学生需要采集一定数量的测量数据,确保数据的可靠性和代表性。
b. 分析测量系统的准确性:学生需要使用统计方法,如均值、方差等,评估测量系统的准确性。
c. 分析测量系统的精确度:学生需要使用统计方法,如重复性和再现性,评估测量系统的精确度。
d. 分析测量系统的稳定性:学生需要使用统计方法,如控制图、稳健性指标等,评估测量系统的稳定性。
e. 提出改进建议:学生需要根据MSA结果,提出改进测量系统的建议和措施。
测量系统分析(MSA)作业指导书
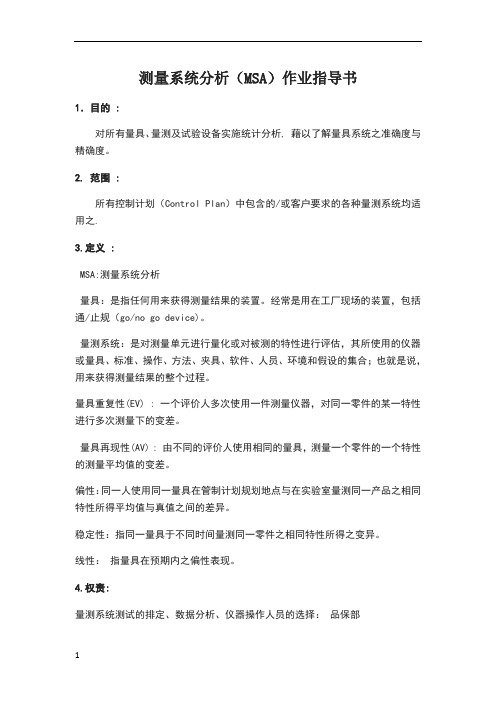
测量系统分析(MSA)作业指导书1.目的 :对所有量具、量测及试验设备实施统计分析, 藉以了解量具系统之准确度与精确度。
2. 范围 :所有控制计划(Control Plan)中包含的/或客户要求的各种量测系统均适用之.3.定义 :MSA:测量系统分析量具:是指任何用来获得测量结果的装置。
经常是用在工厂现场的装置,包括通/止规(go/no go device)。
量测系统:是对测量单元进行量化或对被测的特性进行评估,其所使用的仪器或量具、标准、操作、方法、夹具、软件、人员、环境和假设的集合;也就是说,用来获得测量结果的整个过程。
量具重复性(EV) : 一个评价人多次使用一件测量仪器,对同一零件的某一特性进行多次测量下的变差。
量具再现性(AV) : 由不同的评价人使用相同的量具,测量一个零件的一个特性的测量平均值的变差。
偏性:同一人使用同一量具在管制计划规划地点与在实验室量测同一产品之相同特性所得平均值与真值之间的差异。
稳定性:指同一量具于不同时间量测同一零件之相同特性所得之变异。
线性:指量具在预期内之偏性表现。
4.权责:量测系统测试的排定、数据分析、仪器操作人员的选择:品保部测试执行:各相关单位MSA操作人员的培训:品保部5. 执行方法QA工程师人员依公司PCP文件建立《xx年MSA实施计划表》或客户要求,并依据计划表之排程进行对仪器做量测系统分析。
取样方法:计量型取样:从代表整个工作范围的过程中随机抽取10件样品,但所抽取的10件样品其数值必须涵盖该产品过程分布(也可用之前类似过程的过程能力或者过程标准差代表TV进行计算)。
计数型取样:取50PCS样品,其中包含临近值,不良品与合格品。
测量过程中需要考虑盲测,由2或3个测量者随机抽取对每个产品各测量取一定数量样品.计数型:被评价的零件的选定随机抽取50个零件,把零件编号,由研究小组给出该50个零件的标准,必须含合格,不合格,模糊品,条件允许的情况下最好各占1/3。
MSA作业指导书

MSA作业指导书一、背景介绍MSA(测量系统分析)是一种用于评估和改进测量系统的方法。
它匡助我们了解测量系统的稳定性和准确性,从而确保我们的测量结果可靠和一致。
本文档将提供一份详细的MSA作业指导书,以匡助您进行MSA分析。
二、目标本次MSA分析的目标是评估一个用于测量某个特定尺寸的测量系统的准确性、稳定性和重复性。
通过这个分析,我们将能够确定系统中的潜在问题,并采取相应的措施进行改进。
三、数据采集1. 确定样本数量:根据实际情况,确定需要采集的样本数量。
通常情况下,我们建议至少采集30个样本以获得可靠的结果。
2. 采集样本数据:使用合适的测量设备,对所需尺寸进行测量,并记录每一个样本的测量值。
四、数据分析1. 测量系统稳定性分析:a. 计算每一个样本的平均值:将所有样本的测量值相加,然后除以样本数量,得到平均值。
b. 计算每一个样本的极差:将每一个样本的最大值减去最小值,得到极差。
c. 计算平均极差:将所有样本的极差相加,然后除以样本数量,得到平均极差。
d. 计算极差的标准差:对所有样本的极差进行统计分析,计算标准差。
e. 根据标准差的大小,判断测量系统的稳定性。
标准差越小,表示测量系统越稳定。
2. 测量系统准确性分析:a. 将每一个样本的测量值与实际值进行比较,计算偏差。
b. 计算偏差的平均值和标准差。
c. 根据标准差的大小,判断测量系统的准确性。
标准差越小,表示测量系统越准确。
3. 测量系统重复性分析:a. 对每一个样本进行多次测量,记录每次测量的结果。
b. 计算每一个样本的测量值的平均值和标准差。
c. 根据标准差的大小,判断测量系统的重复性。
标准差越小,表示测量系统的重复性越好。
五、结果解释与改进措施1. 根据稳定性、准确性和重复性的分析结果,判断测量系统的整体性能。
2. 如果发现测量系统存在问题,可以采取以下改进措施:a. 校准或者调整测量设备,以提高准确性。
b. 培训操作人员,以提高稳定性和重复性。
- 1、下载文档前请自行甄别文档内容的完整性,平台不提供额外的编辑、内容补充、找答案等附加服务。
- 2、"仅部分预览"的文档,不可在线预览部分如存在完整性等问题,可反馈申请退款(可完整预览的文档不适用该条件!)。
- 3、如文档侵犯您的权益,请联系客服反馈,我们会尽快为您处理(人工客服工作时间:9:00-18:30)。
MSA测量系统分析作业指导书
1. 目的
为正确进行测量系统分析工作提供操作指导。
2. 工作程序
2.1 编制测量系统分析计划
2.1.1 确定测量系统分析项目,根据技术部的控制计划和特殊特性清单编制《测量系统分析计划》。
2.1.2确定评价人,由于目的是评价全部的测量系统,评价人应该从那些正常操作该检测设备的人员中选择。
2.1.3 确定被测特性,当一个检测设备使用于较多个产品测量特性时,应选择被测产品特性要求最严格的特性进行测量系统分析。
2.1.4 确定分析方法,根据测量系统实际使用要求选择适宜的研究方法。
2.2 测量系统的研究工作
2.2.1 选择基准样件,基准样件的选择对适当的分析是很关键的,对计量型检测设备,被测零件的选择应尽可能覆盖整个预期的过程变差。
2.2.2根据《测量系统分析计划》中规定的日期、评价人、分析方法等,由品质部组织测量系统使用部门实施测量系统分析。
当实际情况偏离年度计划时,根据实际情况进行适当调整。
2.2.3计量型检测设备宽度误差的分析方法,主要是采用平均值和极差法(X&R)研究测量系统的重复性与再现性(GRR)。
2.2.
3.1确定评价人,为了增加试验结果的可比性,通常情况下选择3个评价人并编号A、B、C三人;
2.2.
3.2 选取10个样件(大型样件除外),样件的选择可以是在许多天中每天抽取一件,
并在比较隐秘的位置书写编号,编号不要被评价人看到。
2.2.
3.3 对被测样件、检测设备和检测环境进行清洁,减少变差影响,并对检测设备进行校准。
2.2.
3.4 通过测量收集数据:
1)评价人C随机顺序取10个样件给评价人A测量,B将结果记录在《GRR数据记录表》第一行适当的栏位中。
2)让评价人B和C依次测量这10个样件的相同被测特性,不要让他们知道别人的读值;然后将结果分别的记录在第6行和第11行。
3)用不同的随机测量顺序重复以上循环,并将数据记录在第2、7、和12行;如果需要进行三次测量,则重复以上循环,并将数据记录在第3、8和13行。
4)当测量大型样件或不可能同时获得数个样件时,可让评价人A、B、C依次测量第一个样件,并将读值分别记录在第1 、6、11行;让评价人A、B、C再次重新测量第1个样件,并将读值分别记录在第2 、7、12行;如果需要进行3次测量,则重复以上循环,并将数据记录在第3、8和13行。
5)也可采用其他可靠的方法代替上述的推荐方法,原则是评价人不要受到别人读值或自己记忆读值的影响。
2.2.
3.5根据数据表计算后绘制出X&R控制图,作出测量系统重复性和再现性报告。
◆%GRR低于10%的误差测量系统可接受;
◆%GRR 10%~30%的误差根据应用的重要性,量具成本,维修的费用等可能是可接受的;
◆%GRR 30%的误差测量系统需要改进。
1)如果重复性大于再现性,原因可能是:
◆检测设备需要维修;
◆可能需要对检测设备进行重新设计,以获得更好的严格度;
◆需要对量具的夹紧或固定装置进行改进;
◆零件内变差太大。
2)如果再现性大于重复性,原因可能是:
◆需要更好的对评价人如何使用和判读该检测设备进行培训;
◆检测设备的校准,刻度的不清晰;
2.2.4 计量型检测设备位置误差的分析方法采用:偏倚、稳定性、线性。
2.2.4.1偏倚
A. 偏倚的独立样件法
①取得一个样件,计量室对其进行精密测量(或全尺寸测量)确定为参考值。
如果不能得到样件则选择一件落在生产测量范围中间的中限生产件作为偏倚分析的基准件。
该零件测量次数n≥10次,计算平均值,该平均值视为参考值。
②让一个评价人以正常方式测量样件n≥10次。
③计算读数的平均值X=∑X /n
偏倚=平均值X-基准值X
偏倚占过程变差%=%偏倚=100[│偏倚│/过程变差]
偏倚占公差%=偏倚%=100[│偏倚│/公差]
B. 偏倚的控制图法
①同上所述取得参考值
②从控制图上获得平均值
③偏倚=-基准值X
过程变差=6δ极差
%偏倚=100[偏倚/过程变差]
如果0落在偏倚值附近得1-α自信度界限内,则偏倚在α=0.05(95%置信度)水准上是可接受的。
如果偏倚在统计上明显异于0,可能存在的原因:
◆基准件或参考值有误,检查确定基准件的程序
◆检测设备磨损。
主要会在稳定性分析呈现出来,应制定维护或重新修理的计划;
◆制造的检测设备尺寸不对;
◆检测设备测量了错误的特性;
◆检测设备标准不当。
复查校准方法;
◆评价人使用检测设备的方法不正确,对测量指导书进行评审。
◆检测设备修正计算不正确。
2.2.4.2稳定性的控制图法
①取得一样件并建立其可追溯到相关标准的参考值。
如果无法取得这样的样件,则选择一件落在生产测量范围中间的生产零件,指定它为基准样件以进行稳定性分析。
跟踪测量系统稳定性时,不要求该已知的参考值。
如果有可能拥有位于预期测量结果的下限、上限和中间位置的基准件,推荐对每种基准件单独的进行测量和画控制图。
②每天(或每周)测量基准件3-5次,应该在一天的不同时间内取得多次读值,以代表测量系统的实际使用情况。
③样本容量和抽样频率应根据测量系统的特性,如对环境的敏感程度、重新校准或维修的频率、使用频率等因素确定。
④建立控制限,使用控制图分析法来评价是否有不受控或不稳定的情况。
2.2.4.3线性
①由于存在过程变差,选择5个零件,使测量值要涵盖这测量设备整个工作量程。
对每个零件进行全尺寸测量,确定其参考值。
②让经常使用该检测设备的操作者之一测量每个零件15次。
按随机的顺序选择零件,减小评价人对测量中偏倚的“记忆”。
③计算每个零件平均值和偏倚平均值、回归直线、拟合优度R2、%线性。
偏倚平均值=零件平均值-基准值
回归直线=b+ax
拟合优度R2=(∑xy-∑x∑y/n)2÷{[∑x2-(∑x)2/n][∑y2-(∑y)2/n]}
%线性=100[线性/过程变差]
④根据作出的线性图分析测量系统线性的可接受性。
2.2.5计数型测量系统分析
2.2.5.1计数型量具的分析采用风险分析法。
选取50个零件,3位评价人(检验员、操作者、质量控制人员),分别对50个零件进行测量,并进行记录。
2.2.5.2对于50个零件,3位评价人的测量结果如果一致性良好,即Kappa≥0.75,判定%GRR 满足要求,如果结果不一致Kappa<0.75,则判定%GRR不满足要求
2.3 测量系统分析报告
2.3.1品质部对使用部门收集的数据进行分析,作出分析报告。
测量系统分析研究的报告由执行此研究的人员填写,由质量管理部统一存档。
3. 测量系统改进
3.1 当测量系统的双性分析结果10%≤GRR ≤30%时,由产品工程师、工艺工程师、质量工程师,基于检测设备应用的重要性、成本、维修的费用和所承担的风险等因素,组织对可接受性做出判断。
报告中注明接受或拒收的依据并签字。
3.2当测量系统因为GRR、偏倚、线性或稳定性误差未被接受时,品质部负责组织相关人员确定问题根源,制定改进措施,规定期限和责任人,必要时按部门职责的分工重新设计或购置检测设备。
4. 记录存档
4.1 所有测量系统分析记录由品质部负责存档。