船体外板水火加工成型技术
船体曲面水火弯板加工工艺算法研究

第20卷 第8期 中 国 水 运 Vol.20 No.8 2020年 8月 China Water Transport August 2020收稿日期:2020-03-30作者简介:曹文馨(1986-),男,研发设计院,工程师,从事船体结构设计等工作。
船体曲面水火弯板加工工艺算法研究曹文馨,樊洪良,冉建华(研发设计院,上海 200136)摘 要:水火弯板是船舶曲面外板成型的主要工艺,可靠的成型预测方法是板件成形自动化系统研究的基础。
本文研究了水火弯板加工的机理及加工工艺参数确定的算法。
在建立并以实验验证了水火弯板的数值模拟模型的基础上,确定了火焰成形的温度场和变形场等主要影响参数,提出了温度场及变形场的描述方案,并通过计算得出了板的温度场及变形场与主要加工参数之间的关系,最后对给定帆形板典型船体结构曲面板的水火成型过程进行了热弹性有限元模拟并确定加工工艺参数算法。
关键词:水火弯板;数值模拟;加热路径;温度场;变形场中图分类号:U671.3 文献标识码:A 文章编号:1006-7973(2020)08-0050-03一、引言造船过程中有大量的船体曲面外板需要成型加工,对于较为复杂的给定型值的双曲率曲面板采用的是水火弯板进行加工。
水火弯板是一种曲面板成形的重要方法,该方法需预先布置加热线方案并采用火焰热源沿加热线加工并跟踪水冷的方式实现板件成形。
目前水火弯板的加工单纯是依靠人工和经验来确定加热线的位置和长度以及加热和冷却时间直至最终曲面的成形。
随着造船模式的转变,水火弯板自动加工设备的研制和应用日益成为一项急待解决的课题。
水火弯板自动加工设备是以水火弯板加工参数确定的理论为基础研制的。
加工参数的确定,是指对于一给定型值的双曲度船体外板,如何确定外板展开形状,加热线位置和长度,氧及丙烷的流量,喷嘴高度,加热温度,冷却方式及支撑形式等各种加工工艺参数。
只有在对以上各加工参数及最终变形之间的关系有了明确的认识之后,才能反过来根据这一关系确定,能够获得所需最终形状的加工参数。
船体水火矫正工艺

2 7 4 ・
工 程 科 技
船体水火矫正工艺
程宝亮 张志荣 乔 东旭
( 扬州大洋造船有限公 司, 江苏 扬州 2 2 5 0 0 0 ) 摘 要: 分析了火工矫正常用基本方法及技术要求, 并介绍了修造船中常用的几种典型矫正工艺。 关键词: 修船 ; 技 术要求 ; 矫正工艺 1概述 厚度烧透。 1 . 1 本文适用于修船中焊接过程所产生的应力与变形 , 或 由于海损 b 。 面板凸起纵 向弯曲。 局部变形 ; 而无须进行挖补修理时可采用 火矫正的方法进行修复。 1 - 2矫正变形的方法很多, 如辊 、 压校正 , 锤击校正, 水火校正等。 目 前, 船厂以水火矫正应用较多, 该方法甚为简便、 灵活。 水火校正时利用 氧乙炔焰将钢材弯曲或凹凸变形的部位的有限区域进行局部加热, 随 即用水冷却 , 使之收缩, 以便达到消除变形的 目的。 h ≤( 1 , 2 ) H 1 - 3本文同时适用于造船中部件的合拢及分段合拢 中的分段矫正 及船台合拢后的局部矫正工作。 用楔形法, 自 尖角处开始加热至面板, 接着在面板的同 一位置用宽 2火工矫正常用基本方法及技术要求 条法沿全宽度内加热, 以较高温度加热必须全厚度烧透。 2 . 1长条形加热法。 c . 横向弯曲。 2 . 1 . 1用于钢板变形区,用氧乙炔作直线或曲线形状的加热带 , 施 于骨架背面或骨架背面的两侧。 2 . 1 . 2对于厚度大于 6 m m以上的钢板加热带要尽量靠近骨架。 z 1 . 3加热温度常用 7 0 0 ~ 8 0 O %, 最高 8 5 0 ℃。 对板厚 2 — 4 a r m薄板 , 加热温度不大于 7 0 0  ̄ C 为宜。 2 . 1 . 4长条也可烧成 口字形或 r ~ 形。根据变形部位及变形特点灵 活掌握。 用短条法 从 腹板的端部开始加热 , 腹板凸 起 的一面冷却后 , 用楔形 2 . 2短条形加热法。 法以较高温度加热面板凸弯的一边 , 从面板宽度的中间开始。 2 . 2 . 1加热线施于变形凸起的一面。 3 . 1 . 2以上各形式加热法可辅以水冷却 , 变形较大时可用千斤顶外 2 . 2 . 2加热温度常用 7 0 0 8 o o ℃, 最高 8 5 0 ℃。 对板厚 2 - 4 a r m薄板 , 力加压。但注意不可加压过量, 要考虑冷却后的收缩。 加 热温度 不大 于 7 0 0  ̄ C 为宜 。 3 . 1 . 3质量检验 : 对构件长度不小于 5 m检验线直度为 3 a r m。对构 2 . 2 _ 3矫正变形时由近骨架处问中部变形大处移动, 加热温度则由 件长度大于 5 m时检验线直度为 5 a r m . 2 . 1在框架约四角隅 ̄ ' H J n 热, 也可采用楔形法。根据变形情况决 2 . 2 . 4矫正焊缝变形时, 宜成交角以改善应力分布、 仪= 3 5 — 4 0  ̄。 2 . 2 . 5适用于板厚为 2 ~ 6 a r m钢板及 T型构件。 定加热 温 , 在必 要时 可用锤 击 。 2 - 3楔形加热法。 3 . 2 . 2质量检验: 采用拉对角线的方法校正。 2 . 3 . 1适 用于 T型构 件 I 3 . 3对基座及吊杆等件的矫正。 型构件及其它型材的弯 曲变 3 . 3 . 1矫正方 法 。 形。也适用矫正分段 自由边缘 a 对基座矫正的方法基本上与 T型钢变形的矫正方法一样, 但是要 的变形 。 注意必须采用对称加热法 , 左右同时进行力 I I 热矫正, 以防止矫正变形不
船体外板冲压成形研究

1.国内外船体外板加工现状 金属板材是一种重要的结构件,它具有制作轻、材料利用率高、成形精度高、加工效率
高等特点,在汽车、飞机、船舶、高速列车等工业领域有广泛的应用。其成形方法多种多样。 对大批量生产的零件,可采用整体模具冲压成形。如汽车覆盖件的冲压成形成本低,易实现 机械化、自动化。但对于小批量甚至单件的船舶制造,其船体外板形状各异,受成本及时间 限制,不宜采用固定模具冲压成形。
为其推广应用创造了条件。
为了验证该项新技术的有效性,我们进行了 10×10 压头矩阵(压头支柱横截面为 58
×58 mm2)的弯板实验,通过双曲度船体帆形板、鞍形板冲压试验,已发现该技术在抑制压
痕、起皱方面具有良好的作用。压制的双曲度板材表面光顺。如图 5 所示。
通过进一步的理论及关键技术研究,将为该项技术应用于双曲度船体外板以及其他行业
国内的多点成形研究工作主要集中在吉林大学,李明哲教授带领的团队延续其在日本的 研究工作,并将这种技术命名为“多点成形”法(multi-point forming)[9],它包括多点 模具成形及多点压力机成形两种形式。1999 年成功研制了自动调形的多点成形机。从多点 成形设备制造、调形控制、成形工艺方法、成形精度、抑制压痕及起皱、分段多点成形、成 形过程数值模拟等方面开展了大量理论及实验研究,并取得一系列成果,扩大了其应用范围。 提出了采用弹性垫及增加压沿边,减小压痕及皱折的方法。如图 3 所示。
194
由于没有很好解决变形较大的板材成形时的压痕、皱折,且调整压头成形目标曲面的时间长、 效率低等原因,该压力机最终未能应用于实际生产。20 世纪 70 年代西冈富仁雄(F. Nishioka)等[6]在日本造船协会资助下试制了万能式压力机,但未解决成形曲面的光滑度、 回弹等问题,且制造成本高,未能实现实用化。
船体外板成形自动加工系统与关键技术研究

2018年8月第46卷第15期机床与液压MACHINETOOL&HYDRAULICSAug 2018Vol 46No 15DOI:10.3969/j issn 1001-3881 2018 15 011收稿日期:2017-02-22基金项目:广东省应用型科技研发专项基金项目(2015B090922013);广东省产学研合作项目(2016B090918017)作者简介:徐金雄(1990 ),男,博士研究生,研究方向为自动化装备及技术,数字图像处理㊂E-mail:1007405679@qq com㊂船体外板成形自动加工系统与关键技术研究徐金雄,程良伦,丘文波,林嘉华(广东工业大学自动化学院,广东广州510006)摘要:针对船体外板自动加工问题,设计了一种水火弯板自动加工系统,并对系统中的关键技术进行了研究㊂该自动加工系统采用龙门式5轴联动设计,从而满足大曲率外板的加工需求㊂此外在三维激光测量技术的基础上,通过坐标系变换㊁轨迹规划和5轴控制量计算方法,实现外板曲面的定位和加工㊂实验测试结果表明:该系统能代替工人进行实际的外板成形加工工作,具有一定的实际应用价值㊂关键词:水火弯板机器人;激光扫描;运动控制中图分类号:TP273㊀㊀文献标志码:A㊀㊀文章编号:1001-3881(2018)15-045-5ResearchonAutomaticMachiningSystemandKeyTechnologyofShipHullPlateFormingXUJinxiong,CHENGLianglun,QIUWenbo,LINJiahua(SchoolofAutomation,GuangdongUniversityofTechnology,GuangzhouGuangdong510006,China)Abstract:Aimingattheproblemofautomaticprocessingofshiphullplate,akindofautomaticprocessingsystemofwaterfirebendingplatewasdesigned,andthekeytechnologyofthesystemwasstudied.The5⁃axisgantry⁃linkeddesignwasusedinthissystem,soastomeettheprocessingrequirementsoflargecurvatureshiphullplate.Besides,basedonthe3Dlasermeasurementtechnology,thecoordinatesystemtransformationmethod,trajectoryplanningand5⁃axiscontrolquantitycalculationmethodwereresearchedtoreal⁃izethepositioningandmachiningofthehullplate.Theexperimentalresulstshowthatthissystemcanreplacetheworkersforprocessingworkofthehullplate,whichhascertainpracticalapplicationvalue.Keywords:Waterfirebendingrobot;Laserscanning;Motioncontrol0㊀前言船体外板曲面的成形加工是船舶制造的关键及重要环节之一㊂目前国内外船厂主要采用水火弯板工艺对船体外板进行加工,即采用燃气火焰在钢板表面进行局部线状加热,当加热区达到一定温度后再用水或空气降温,利用金属的热弹塑性收缩变形原理,以获得良好的整体变形㊂由于成形的影响因素较多,有板材的形状参数㊁加工参数㊁热源㊁边界条件㊁冷却方式等,使得这门工艺只能依靠经验丰富的工人来手工实施㊂这种依赖于经验的加工工艺方法,存在生产效率低㊁加工时间长㊁质量波动大㊁精度难以控制等问题[1-4]㊂因此,在数字化造船和中国制造2025的环境下,各船厂都希望实现水火弯板工艺过程的自动化㊂要实现工艺过程的自动化,关键在于如何在加工钢板上自动规划出加热轨迹让机器人执行㊂针对这一问题,陈尤力[5]和黄浩坚[6]提出了一种加热轨迹专家规划方法㊂该方法先对目标曲面的焰道经验规则进行总结,然后通过规则推理的方式实现加热轨迹的自动规划㊂由于规则库不完善,该方法只适用于小部分船体外板的加热轨迹规划㊂SEONG等[7]提出了一种几何高度差加热轨迹规划方法㊂该方法先比较目标曲面和加工曲面之间的偏差,然后通过迭代方式找到偏差量最大的点作为焰道点,实现了波浪形钢板曲面的自动加工㊂但该方法只能对单向曲率变化的外板进行加工,而大部分船体外板都具有双向曲率,所以实际应用价值较低㊂SEONG等[8]和陈伟[9]提出了一种基于曲面展开的加热轨迹规划方法㊂该方法的原理是把船体外板曲面看成由许多足够小的平面连接而成,然后保持每块小平面形状不变,按一定规律把整张曲面展开铺平,展开后出现的裂缝,即为加热轨迹的位置,其大小即为目标收缩量㊂但该方法难以解决部分可展外板曲面的加热轨迹规划问题㊂目前国内外还没有一种完全能解决各种船体加热轨迹自动规划的方法,导致现有弯板机器人难以实现对各种类型的船体外板进行自动加工㊂与上述研究不同,作者打算采用一种折中方法来实现水火弯板工艺的自动化㊂该方法先利用三维激光测量技术,获取加工外板曲面的三维信息,并在计算机中进行三维重构㊂然后工人根据自身的知识经验,在计算机中画出加热轨迹㊂最后将轨迹坐标转化为机器人的控制量,让机器人执行㊂该方法回避了目前加热轨迹规划方法所存在的问题,减轻了工人90%的劳动量,并从某种程度上实现了工艺流程的自动化㊂1 硬件系统设计文中所研制的船体复杂外板成形自动加工系统,其硬件主要包括三维激光扫描仪和龙门式水火弯板机器人㊂其中,三维激光扫描仪主要用于获取加工钢板的三维轮廓信息,运动控制系统则负责控制末端的火枪头对钢板实施加工㊂1 1㊀扫描检测系统设计扫描检测系统由三维激光扫描仪和防尘装置组成㊂其中,扫描仪采用美国某公司生产的型号为Focus3D120的三维激光扫描仪㊂该扫描仪通过对红外波段频率的激光幅度进行正弦调制,然后根据调制光往返扫描仪与目标物间距离所产生的相位差计算出待测距离㊂测量速度达97 6万点/s,测量精度达为25m内的系统误差不大于ʃ2mm㊂而扫描仪的安装位置和工作方式,如图1所示,安装在龙门架的横梁中部位置,并通过倒挂方式采集加工钢板的轮廓信息㊂图1㊀扫描检测系统实物图防尘装置是扫描仪的附加装置,主要作用是避免扫描仪长时间暴露在粉尘较大的工作环境下从而降低测量精度㊂如图1所示,该装置的组成包括:防尘罩㊁底板㊁气动装置㊁伺服电机和PLC等㊂其中防尘罩与气动装置相连接,并通过PLC控制气动装置带动防尘罩上升和下降㊂在底板上安装扫描仪,通过齿轮与伺服电机相连接,并通过PLC控制伺服电机实现底板的正向和反向旋转㊂当扫描仪待机时,底板与水平面平行,防尘罩下降完全罩住扫描仪;当扫描仪工作时,防尘罩先上升到最高位置,然后伺服电机带动底板旋转180ʎ,使扫描仪处于倒挂状态㊂1 2㊀龙门式水火弯板机器人设计(1)机器人本体设计结合实际加工需求,此运动控制系统采用龙门式五轴联动设计(X,Y,Z,RX,RZ),并在末端安装带有火枪头的十字滑块(L1,L2)和带有水枪的跟踪轴H,如图2所示㊂各轴的功能设计和参数如下:X轴移动装置㊂X轴的功能是控制整台装置沿X方向平移,行程设定为12m㊂考虑到装置的质量和驱动问题,X轴采用2个功率为3500W的伺服电机作为驱动单元,分别安装在轨道的两侧㊂此外在两侧路轨上,各安装了2个接近式限位开关(共4个),起安全保护和定位校准作用㊂Y轴移动装置㊂Y轴的功能是控制整台装置沿Y方向平移,行程设定为4 5m㊂采用1500W的伺服电机作为驱动单元,并在龙门架横梁的两端各安装了1个接近式限位开关,起安全保护和定位校准作用㊂Z轴移动装置㊂Z轴的功能是控制整台装置沿Z(高度)方向平移,行程设定为2 7m㊂伺服电机功率为1500W㊂滑轨端头要有2个接近式限位开关,起安全保护和校准定位作用㊂RX轴旋转装置㊂RX轴可以控制火枪头部分绕X轴旋转ʃ60ʎ,伺服电机功率为500W㊂此外,在行程的末端装有2个接近式限位开关,起安全保护和定位校准作用㊂RZ轴旋转装置㊂RZ轴可以控制火枪头部分绕Z轴旋转ʃ90ʎ,伺服电机功率为500W㊂此外,在行程的末端装有2个接近式限位开关,起安全保护和定位校准作用㊂十字滑块(L1轴,L2轴)㊂十字滑块由2个行程方向相互垂直的直线伺服电机组成,2个伺服电机的功率为400W㊂该模块通过圆弧插补技术,带动火枪头在空间平面上做圆弧运动㊂水枪跟踪轴H㊂H轴的作用是调整水枪头的位置,其运动方式为绕火枪头旋转ʃ150ʎ,伺服电机功率为400W㊂图2㊀龙门式水火弯板机器人实物图㊃64㊃机床与液压第46卷(2)控制系统设计运动控制系统的控制部分,主要由工业计算机㊁控制器和伺服系统控制器组成㊂其中,工业计算机主要作用是提供人机交互界面,为用户提供服务,与成形装备控制器相连接输出控制命令和接收反馈信息;成形装备控制器主要为Trio运动控制器和PLC控制器,实际中根据控制指令对各个轴进行控制,并通过脉冲编码机制获取各轴的位置信息;伺服系统控制器与伺服电机驱动器相连接,根据设定的程序直接输出脉冲,控制各轴的电机运动㊂2 关键技术研究2 1㊀坐标系转换方法由于三维扫描仪的测量坐标系与弯板机器人的运动坐标系不一致㊂因此在进行相关处理前,需要将测量数据的三维坐标系转换到机器人的运动坐标系下㊂为实现这一流程,取加工平台上的3个角点作为公共点,用于计算测量坐标系到运动坐标系的旋转平移矩阵㊂具体的转换过程如下:(1)公共点坐标提取㊂任意取水火弯板加工平台上的3个角点作为坐标系变换的公共点㊂然后分别在机器人运动坐标系下和三维测量坐标系下,提取这3个公共点的三维空间坐标㊂(2)公共坐标系建立㊂以3个公共点其中的一点作为公共坐标系的原点,以原点和另外一个公共点的连线方向作为公共坐标系的X轴方向,以垂直于3个公共点形成平面的方向作为公共坐标系的Z轴方向,建立直角坐标系㊂(3)正㊁逆变换矩阵计算㊂假设在运动坐标系或测量坐标系中,3个公共点的坐标分别为(xi,yi,zi)(i=1㊁2㊁3),则将其坐标系转换到公共坐标系的正变换矩阵为:xᶄiyᶄizᶄiéëêêêùûúúú=xi-x1yi-y1zi-z1éëêêêêùûúúúúTcosγ1sinγ10-sinγ1cosγ10001éëêêêùûúúú㊃cosβ10-sinβ1010sinβ10cosβ1éëêêêùûúúú1000cosα1sinα10-sinα1cosα1éëêêêùûúúú(1)式中:γ1=-arctany2-y1x2-x1æèçöø÷,㊀β1=-arctanz2-z1x2-x1æèçöø÷,α1=-arctanz3-z1y3-y1æèçöø÷㊂公共坐标系到运动坐标系或测量坐标系的逆变换矩阵为:xiyiziéëêêêêùûúúúú=xᶄiyᶄizᶄiéëêêêùûúúúT1000cosα2sinα20-sinα2cosα2éëêêêùûúúú㊃cosβ20-sinβ2010sinβ20cosβ2éëêêêùûúúúcosγ2sinγ20-sinγ2cosγ20001éëêêêùûúúú+x1y1z1éëêêêêùûúúúú(2)式中:α2=arctanz3-z1y3-y1æèçöø÷,㊀β2=arctanz2-z1x2-x1æèçöø÷,γ2=arctany2-y1x2-x1æèçöø÷㊂(4)坐标系变换㊂将所有测量数据的三维坐标乘以测量坐标系到公共坐标系的正变换矩阵,使测量数据转到公共坐标系下㊂然后,将测量数据乘以运动坐标系到公共坐标系的逆变换矩阵,使测量数据转换到运动坐标系下㊂具体过程如图3所示㊂图3㊀测量坐标系到运动坐标系变换示意图2 2㊀加热轨迹规划方法在所设计的船体外板成形自动加工系统中,加热轨迹的规划主要通过工人在人机界面进行规划㊂这样可以充分利用丰富的经验知识,解决轨迹规划这一难题㊂具体的规划过程如图4所示,包括以下4个步骤:(1)工人通过人机交互界面中的三维图形操作按钮调整加工曲面的视角坐标系,然后通过轨迹绘制工具在屏幕上绘制出若干条平面曲线;(2)按一定的距离间隔在每一条绘制曲线上抽取若干个轨迹点的平面坐标,即轨迹的X㊁Y坐标;(3)在视角坐标系下,通过投影方式找到外板曲面上与轨迹点X㊁Y坐标相同的点,并提取出来,从而得到每条加工轨迹的三维坐标;(4)将加热轨迹的三维坐标变换到运动坐标系下,从而得到加热轨迹的实际坐标㊂㊃74㊃第15期徐金雄等:船体外板成形自动加工系统与关键技术研究㊀㊀㊀图4㊀焰道绘制过程其中,屏幕上的曲线生成方式是通过多段Bezier曲线平滑衔接而成㊂而每一段Bezier曲线的生成只需在屏幕相应位置点击鼠标4次即可㊂这4次所对应的动作效果如图5所示,分别为:第1次点击,确定分段曲线起点位置;第2次点击,确定分段曲线终点位置;第3次点击后,确定分段起点附近的Bezier控制点的位置;第4次点击,确定分段终点附近的Bezier控制点的位置,生成曲线㊂图5㊀Bezier曲线的生成过程2 3㊀机器人控制量计算方法(1)机器人运动建模根据图1和图6的弯板机器人各运动轴的设计可知,对X轴㊁Y轴和Z轴进行联动控制,可实现弯板机器人末端的火枪在三维空间中平移;对RX轴和RZ轴进行联动控制,可调整火枪在空间中的摆角,即火枪的指向㊂假设,火枪长度为L(含火枪长度和火焰内焰长度),各轴的位置量为(Px,Py,Pz,θrx,θrz),则火枪末端的三维空间坐标值为:x+Px+Lsinθrx㊃cosθrzy=Py+Lsinθrx㊃sinθrzz=Pz-Lcosθrxìîíïïï(3)火枪的指向,即火枪所在的单位法向量:nL=(sinθrx㊃cosθrz,sinθrx㊃sinθrz,-cosθrx)(4)图6㊀龙门式5轴弯板机器人结构图(2)5轴位姿计算假设加工轨迹上各点的三维坐标为Si=(xi,yi,zi),(i=1,2,......,N),各点在钢板曲面上对应的单位法向量为nSi=(Fxi,Fyi,Fzi),(i=1,2,......,N)㊂在水火弯板技工过程中为保证加工效率,一般需要保持火枪垂直于钢板曲面,此时有nLi=nSi㊂则根据式(4)可得到:Fxi=sinPrxi㊃cosPrziFyi=sinPrxi㊃sinPrziFzi=-cosPrxiìîíïïï(5)对式(5)进行变换,可得RX轴和RZ轴在轨迹各点上的位姿为:θrxi=ʃarccos(-Fzi)θrzi=arcsin(Fyi/sinθrxi){(6)式中:当Fyiȡ0时θrxi取正号;当Fyi<0时θrxi取负号㊂确定RX轴和RZ轴的位姿后,根据式(3)反推出X轴㊁Y轴和Z轴在轨迹各点上的位姿为:Pxi=xi-Lsinθrxi㊃cosθrziPyi=yi-Lsinθrxi㊃sinθrziPzi=zi+Lcosθrxiìîíïïï(7)(3)5轴分速度计算假设火枪末端的线速度目标设定值为va㊂为计算各轴的分速度,文中采用微积分思想,将加工轨迹分割成M条非常短的曲线段,每条曲线段都可近似看作是一条直线㊂则火枪在每条曲线段的运动时间可通过下式进行近似计算:Δti=Δdi/va(i=1,2,3,......,M)(8)式中:Δdi为曲线段首尾点的直线距离㊂然后,根据式(6)和(7),可计算出5个轴在每条曲线段首尾点处的位移量(ΔPxi,ΔPyi,ΔPzi,Δθrxi,Δθrzi),此时5个轴在每条曲线段内的移动速度可近似为:vxi=ΔPxi/Δtivyi=ΔPyi/Δtivzi=ΔPzi/Δtivrxi=Δθrxi/Δtivrzi=Δθrzi/Δtiìîíïïïïïï㊀(i=1,2,......,M)(9)㊃84㊃机床与液压第46卷3㊀实验测试为验证文中所提出的方法,以编号为D32-CAS的外板作为实验测试对象,其形状如图7所示㊂然后开启激光扫描仪对钢板的三维轮廓进行测量,获取加工外板的三维数据,其测量过程如图8所示㊂然后根据上述内容对测量数据进行坐标系转换,并通过工人在人机界面中画出加热轨迹,结果如图9所示㊂接着根据上述内容计算出弯板机器人的运动控制量,并输入到机器人控制系统中让机器人执行,结果如图10所示㊂由现场加工图片可知,此系统和方法能满足船厂的外板加工需求,减轻工人90%的工作量㊂图7㊀D32-CAS外板实物图图8㊀加工外板的扫描检测图9㊀焰道规划结果图10㊀成形自动加工4㊀总结水火弯板成形加工是船体外板加工的重要工艺,也是整个船舶生产制造中的一个不可或缺环节㊂研制新一代水火弯板自动化装备及突破相关关键技术,将提高船体外板加工效率和质量,促进船舶业的转型升级㊂实际测试表明,所研制的船体复杂外板成形加工装备具备数字化测量和非接触式自动加工能力,能满足船体的大部分外板的加工需求㊂参考文献:[1]刘平革,胡怀建,程利民,等.船舶三维数控弯板的研究现状及实际应用[J].船舶标准化工程师,2016,49(4):27-29.LIUPG,HUHJ,CHENGLM,etal.ResearchStatusandPracticalApplicationofShip3DNumericalControlBen⁃dingPlate[J].ShipStandardizationEngineer,2016,49(4):27-29.[2]PARKJ,KIMD,HYUNC,etal.ThermalFormingAutoma⁃tionSystemforCurvedHullPlatesinShipbuilding:Analy⁃sisandDesign[J].InternationalJournalofComputerInte⁃gratedManufacturing,2016,29(3):287-297.[3]汪骥.水火弯板自动化加工工艺的关键技术研究[D].大连:大连理工大学,2006.[4]潘伟杰,程良伦,王涛,等.一种水火弯板外板曲面表面火路定位算法[J].图学学报,2015,36(5):697-702.PANWJ,CHENGLL,WANGT,etal.ALocalizationAlgorithmforPlateSurfaceinLineHeating[J].JournalofGraphics,2015,36(5):697-702.[5]陈尤力.水火弯板专家系统研究[D].镇江:江苏科技大学,2015.[6]黄浩坚.智能水火弯板成形机器人专家系统[D].广州:广东工业大学,2016.[7]SEONGWJ,AHNJ,NASJ,etal.GeometricalApproachforFlameFormingofSingleCurvedShipHullPlate[J].JournalofMaterialsProcessingTechnology,2010,210(13):1811-1820.[8]SEONGWJ,JEONYC,NASJ.ShipHullPlateFormingofSaddleShapebyGeometricalApproach[J].JournalofMaterialsProcessingTechnology,2013(11):1885-1893.[9]陈伟.船体板水火弯板成形焰道布置优化研究[D].大连:大连理工大学,2013.(责任编辑:卢文辉)㊃94㊃第15期徐金雄等:船体外板成形自动加工系统与关键技术研究㊀㊀㊀。
4-4-1+船体板材构件的成形加工

⑤ 经常注意钢板上所划的素线与下轴辊上的纵向槽是否 平行,并用内卡样板检查钢板弯制曲度,以便调节上 轴辊的升降,直至弯曲成形到与样板型线相符合为止。
3、普通三辊弯板机弯板功能的缺点
缺点: 在弯制圆柱形或圆锥形板件时,板的边缘有一段无法进 行辊压。 解决办法:. 加垫块先辊弯好板边部分或先用液压机压好板边部分。 这种工艺措施既浪费工时又浪费材料。
4、几种新型的辊式弯板机
三根轴辊均可上下升降调节的三辊弯板机; 轴辊可作横向调节的三辊弯板机; 四辊弯板机; 能进行矫平的四辊弯板机。
四辊弯板机
四辊卷板机关键技术及创新点:
全密闭设计,防止灰尘进入; 一改国产卷板机到处漏油的现象,整体外观达到国外水
平。维护保养方便,效率高,寿命长,环保效果好。 全钢焊接结构,设备刚性强,并采用计算机有限元计算分析
(三)数控弯板简介
1、应用数控技术进行自动化弯板的优点
① 大幅度提高弯板工作效率,减轻劳动强度; ② 提高弯板精度,从而减少装配和校正工作量; ③ 同其它数控加工装置一起使用,则能实现船体加工车间综合机械化、
自动化,提高综合生产能力。
2、典型数控弯板机样机:多压头式数控弯板机
多压头式数控弯板机在弯板前,运用数控程序将其下模的各个 压头逐个自动加以调节,使其改变高度,形成与所要求的构件的形 状相同的局面(考虑回弹)。当被弯曲的板材定位好后,上模的各 个压头下降,将板材弯成所需要的形状。
② 正面跟踪水冷法:在加热面用冷水喷射正在冷却 的金属,加快它们的收缩,从而强化对正在加热金属的 压缩作用,使其产生较大的附加塑性变形。
优点:收缩较快,其横向收缩变形比空冷法大,成 形加工所不需要的加热线纵向收缩变形远比空冷法小。
船体外板水火成型工艺参数预报系统设计与实现
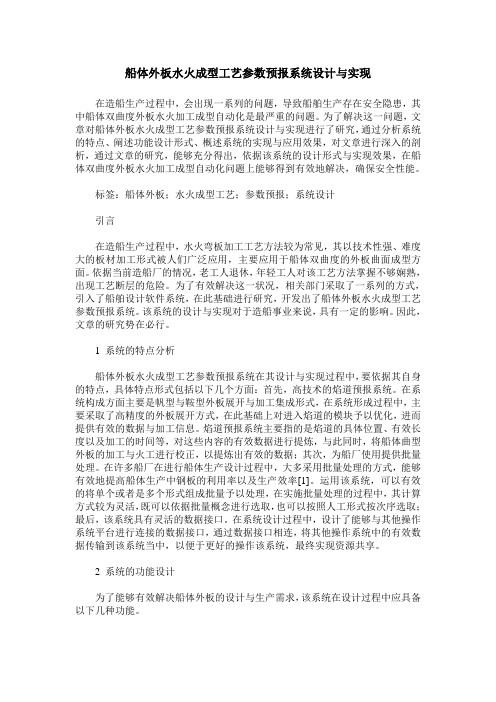
船体外板水火成型工艺参数预报系统设计与实现在造船生产过程中,会出现一系列的问题,导致船舶生产存在安全隐患,其中船体双曲度外板水火加工成型自动化是最严重的问题。
为了解决这一问题,文章对船体外板水火成型工艺参数预报系统设计与实现进行了研究,通过分析系统的特点、阐述功能设计形式、概述系统的实现与应用效果,对文章进行深入的剖析,通过文章的研究,能够充分得出,依据该系统的设计形式与实现效果,在船体双曲度外板水火加工成型自动化问题上能够得到有效地解决,确保安全性能。
标签:船体外板;水火成型工艺;参数预报;系统设计引言在造船生产过程中,水火弯板加工工艺方法较为常见,其以技术性强、难度大的板材加工形式被人们广泛应用,主要应用于船体双曲度的外板曲面成型方面。
依据当前造船厂的情况,老工人退休,年轻工人对该工艺方法掌握不够娴熟,出现工艺断层的危险。
为了有效解决这一状况,相关部门采取了一系列的方式,引入了船舶设计软件系统,在此基础进行研究,开发出了船体外板水火成型工艺参数预报系统。
该系统的设计与实现对于造船事业来说,具有一定的影响。
因此,文章的研究势在必行。
1 系统的特点分析船体外板水火成型工艺参数预报系统在其设计与实现过程中,要依据其自身的特点,具体特点形式包括以下几个方面:首先,高技术的焰道预报系统。
在系统构成方面主要是帆型与鞍型外板展开与加工集成形式,在系统形成过程中,主要采取了高精度的外板展开方式,在此基础上对进入焰道的模块予以优化,进而提供有效的数据与加工信息。
焰道预报系统主要指的是焰道的具体位置、有效长度以及加工的时间等,对这些内容的有效数据进行提炼,与此同时,将船体曲型外板的加工与火工进行校正,以提炼出有效的数据;其次,为船厂使用提供批量处理。
在许多船厂在进行船体生产设计过程中,大多采用批量处理的方式,能够有效地提高船体生产中钢板的利用率以及生产效率[1]。
运用该系统,可以有效的将单个或者是多个形式组成批量予以处理,在实施批量处理的过程中,其计算方式较为灵活,既可以依据批量概念进行选取,也可以按照人工形式按次序选取;最后,该系统具有灵活的数据接口。
水火弯板工艺力学

当加热过程终了,加热部位开始冷却时,恰巧与加 热时的情况相反,该部位要开始收缩。为叙述方便, 分两种情况加以讨论。 一、当加热温度在100一200℃范围内,加热、冷 却时变形和应力的变比情况如图所示(图中剖面线部 分为弹性变形区)。当冷却开始后首先是加热区的弹 性变形量回复,使 E 部分消失;温度继续下降,加 热部位继续收缩,由于冷却时的线胀系数与加热时 的线胀系数相等,加热和冷却终了的相对变形量的 绝对值也应该相等,即:
E 全部消失,继续冷却,加热点 当温度降低100℃, 将继续向里收缩,周围的钢材却又会进一步阻碍这 种收缩,而使加热部位产生拉应力,以及弹性拉伸 变形。从田中可以看出,冷却终了时,加热部位的 拉伸变形量正好是加热时所产生的塑性变形量。
热
当加热温度超过200℃时,由于加热时的塑性变形 量 热 E E ,那么冷却终了时不仅会产生弹性变 形 E ,而且会产生塑性变形 E 。
因此,当加热温度在100一200℃之间时,弹性变形 量 E 为一恒值,塑性变形量T E 和温度呈线性关 系,而在200一700℃范围内加热时,总的相对变形 量依然和温度呈线性关系,可是 E 却随温度升高急 剧下降,导致弹性变形量急剧下降,而塑性变形量 急剧增加;当温度守700℃以上加热时,钢材便处 于全塑性状态( E 趋向于零),随之弹性变形量及 热应力也全部消失,塑性变形部分由于受到周围常 温钢材的制约也无法变形,加热点在径向既不受应 力,也没有尺度的变化。
在加热过程中,当:
s ——钢材达到屈服极限时的相对伸长量。 式中: 加热部位相对伸长变形纯粹是弹性变形,受到周围 钢板的制约所产生的压缩变形也在弹性范围以内, 加热部分冷却以后,依然可以回复到加热以前的初 始状态。 而温度进一步升高,使
船体变形处理以及火工矫正原则工艺-LYY

船体火工矫正原则工艺1. 火工矫正的作用原理船体结构的火工矫正,就是利用金属局部受热后,所引起的新的变形去矫正原先的变形。
而非始4)利用刚性约束能加大热塑变形量的原理进行矫正。
如果取水冷却的火工矫正办法,让周围的金属尽量保持冷却以提高周围约束的刚性,从而增大矫正效果;5)利用预应力进行矫正。
如果用辅助工夹具等,以使冷金属区域预先有一个附加的应力压缩加热区金属,促使压缩应力提早达到屈服点,而加快热塑变形以增大矫正效果。
2.2 加热方法方 法优缺点、适用范围线状加热法加热线宽度一般为钢板厚度的0.5~2倍,矫正质量好、效率高,适用于矫正板架、变形“瘦马”变形,板架的起伏波浪变形等.点状加热法各点直径一般不小于15mm,变形量越大,点与点距离越小,一般为50~100mm,加热参数易掌握、但速度慢、工效低.三角形加热法适用于矫正较大构件的弯曲变形.2.3 按冷却方法划分方 法优点、适用范围常规矫正法(空冷法)用于矫正各种钢结构。
水火矫正法用于矫正低碳钢等。
2.4 火工矫正参数1)火工矫正参数包括火焰性质、火焰功率、加热温度、加热区规格、火焰至工件表面距离;火焰一般采用氧-乙炔焰。
2)钢板四边波浪变形时,加热长度一般为板宽的1/2~1/3,加热距离视变形越大,距离越近,一般50~200mm。
矫正厚钢板弯曲变形时,加热深度不超过板厚的1/3。
3)加热点至工件表面的距离应以能获得最高的热效率为宜。
水火矫正厚度为5~6mm 钢板时,水火间距离为约25~30mm。
4)低碳钢火焰矫正时,常采用600°C~800°C的加热温度,一般不超过850°C。
一般凭钢材的颜色判断加热温度,见下表:颜色温度(°C)深褐红色 550~580褐红色 580~650暗樱红色 650~730深樱红色 730~770樱红色 770~800淡樱红色 800~830亮樱红色 830~900橘黄色 900~1050暗黄色 1050~11503. 火工矫正的时机、范围及处理方法4. 火工矫正的工艺要求4.1矫正前工作状态的要求。