锂电池碰撞安全性分析模型(英文)
autodyn (2)
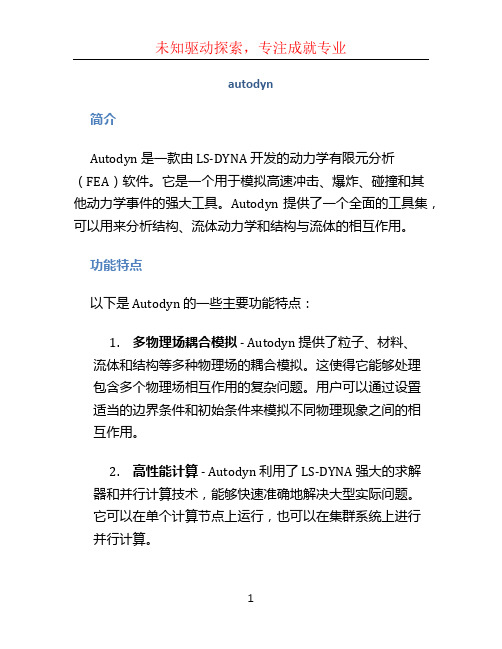
autodyn简介Autodyn 是一款由 LS-DYNA 开发的动力学有限元分析(FEA)软件。
它是一个用于模拟高速冲击、爆炸、碰撞和其他动力学事件的强大工具。
Autodyn 提供了一个全面的工具集,可以用来分析结构、流体动力学和结构与流体的相互作用。
功能特点以下是 Autodyn 的一些主要功能特点:1.多物理场耦合模拟 - Autodyn 提供了粒子、材料、流体和结构等多种物理场的耦合模拟。
这使得它能够处理包含多个物理场相互作用的复杂问题。
用户可以通过设置适当的边界条件和初始条件来模拟不同物理现象之间的相互作用。
2.高性能计算 - Autodyn 利用了 LS-DYNA 强大的求解器和并行计算技术,能够快速准确地解决大型实际问题。
它可以在单个计算节点上运行,也可以在集群系统上进行并行计算。
3.材料建模和损伤模型 - Autodyn 支持各种材料的建模和损伤模型。
用户可以根据自己的需要选择合适的材料模型,并设置材料的强度、刚度和损伤特性。
4.自定义求解方案 - Autodyn 具有灵活的求解方案配置选项,用户可以根据问题的特点和求解目标进行配置。
它提供了多种时间积分方法、网格划分方法和后处理选项,以便用户能够获得满足自己需求的求解结果。
5.结果可视化 - Autodyn 提供了丰富的结果可视化功能,用户可以通过动画、图表和图像等方式直观地展示分析结果。
它还支持与其他后处理软件和可视化工具的数据交换。
应用领域Autodyn 在多个领域都有广泛的应用,包括但不限于以下几个方面:1.汽车碰撞分析 - Autodyn 可以模拟汽车碰撞过程,包括车辆与障碍物的碰撞、车身组件的变形和受力分析等。
这些分析可用于改进汽车的安全性能和设计。
2.航空航天 - Autodyn 在航空航天领域的应用十分广泛。
它可以用于模拟飞行器的撞击、爆炸和其他动力学事件,以评估结构的强度和稳定性。
3.爆炸和爆破 - Autodyn 的强大爆炸和爆破模拟功能使得它在国防、民用爆炸物处理和石油化工等领域得到了广泛应用。
锂电池PACk DFMEA

锂电池PACk DFMEADFMEA(Design Failure Mode and Effects Analysis)是一种用于识别和评估产品设计中潜在故障模式和其对系统性能的影响的方法。
下面是一个可能的锂电池Pack DFMEA的示例:1. 设计功能:锂电池Pack的主要功能是存储和提供电能供应。
2. 潜在故障模式:a) 电池过热:可能由于过充、过放、过充电、短路等原因引起。
b) 电池过充:可能由于充电过程中控制系统失效、充电器故障等原因引起。
c) 电池过放:可能由于放电过程中控制系统失效、负载过大等原因引起。
d) 电池短路:可能由于电池内部短路、外部短路等原因引起。
e) 电池内部损坏:可能由于振动、冲击、温度变化等原因引起。
f) 电池泄漏:可能由于包装材料破损、电池内部损坏等原因引起。
g) 电池容量下降:可能由于循环次数增加、使用条件不当等原因引起。
3. 故障模式的影响:a) 电池过热:可能导致电池损坏、甚至爆炸。
b) 电池过充:可能导致电池损坏、容量下降。
c) 电池过放:可能导致电池损坏、容量下降。
d) 电池短路:可能导致电池损坏、甚至爆炸。
e) 电池内部损坏:可能导致电池损坏、容量下降。
f) 电池泄漏:可能导致电池失效、环境污染。
g) 电池容量下降:可能导致使用时间缩短、性能下降。
4. 风险评估:a) 根据潜在故障模式和其影响的严重程度,对每个故障模式进行评估,确定其风险等级(如高、中、低)。
b) 根据潜在故障模式发生的概率和探测性能,对每个故障模式进行评估,确定其风险等级(如高、中、低)。
5. 预防措施:a) 电池过热:设计温度控制系统,加装温度传感器,设置过热保护装置。
b) 电池过充:设计电池管理系统,加装电压保护装置。
c) 电池过放:设计电池管理系统,加装电压保护装置。
d) 电池短路:设计电池管理系统,加装短路保护装置。
e) 电池内部损坏:加强电池包装材料的抗振动、抗冲击性能。
f) 电池泄漏:设计密封性能好的包装材料,加装泄漏检测装置。
LS-DYNA实例分析报告

LS-DYNA实例分析报告合普科技2010年07月目录(一)LS-DYNA基本介绍03 (二)某电动玩具的跌落分析06 (三)汽车保险杠的碰撞分析17 (四)总结22(一)LS-DYNA的基本介绍LS-DYNA是一个以显式求解为主、兼有隐式求解功能,以Lagrange算法为主、兼有ALE和Euler算法,以结构分析为主、兼有热分析和流体-结构耦合功能,以非线性动力分析为主、兼有静力分析功能,军用和民用相结合的通用非线性结构动力分析有限元程序,主要用于求解各种非线性结构的高速碰撞、爆炸和金属成型等结构非线性问题。
DYNA程序系列最初是1976年在美国Lawrence Livermore National Lab.由J.O.Hallquist主持开发完成的,主要目的是为武器设计提供分析工具,后经1979、1981、1982、1986、1987、1988年版的功能扩充和改进,成为国际著名的非线性动力分析软件,在武器结构设计、内弹道和终点弹道、军用材料研制等方面得到了广泛的应用。
1988年J.O.Hallquist创建LSTC公司,自此开始DYNA程序的商业化开发,LSTC陆续将DYNA的显式、隐式、热分析等系列程序组合在一起,形成一个整体的LS-DYNA软件包,并逐步增加汽车安全性分析、薄板冲压成型过程模拟、流体与固体耦合(ALE和欧拉算法)等功能,使LS-DYNA程序系统在国防和民用领域的应用范围不断扩大,并建立了完备的质量保证体系。
因此LS-DYNA一经推出,即在显式有限元分析领域引起轰动效应,大大拓展了LS-DYNA的用户领域,在中国地区,LS-DYNA的用户数在短短的几年时间内即超过了200家,远远领先于其它显式分析程序。
LS-DYNA程序的主要强项在于:历史悠久、应用广泛。
该软件是全世界范围内最知名的有限元显式求解程序。
LS-DYNA程序开发的最初目的是为北约组织的武器结构设计、防护结构设计服务,是该组织的Public Domain程序,后来商业化后广泛传播到世界各地的研究机构。
三种常用动力锂电池模型分析与比较

三种常用动力锂电池模型分析与比较姬伟超;傅艳;罗钦【摘要】To figure out how to choose battery models for the state of charge estimation of electric vehicles, modeling, parameter identification and simulation were respectively carried out with Matlab/Simulink to three types of non-linear models namely PNGV model, Thevenin model and Universal model suitable for Lithium-ion battery SOC estimation in special work conditions, and the precision, response characteristics and availability for application were analyzed and compared based on the experiment results. Finally,it was concluded that PNGV model was more precise and more suitable for application.%为了获得更优的用于电动汽车荷电状态(SOC)估计的动力锂电池模型,分别针对美国新一代汽车合作伙伴计划(PNGV)模型、Thevenin模型、Universal模型三种常用的适合于锂电池SOC估计的非线性模型在特定放电工况下利用matlab/simulink进行建模、参数辨识和仿真,依据实验结果分析比较其模型精确度、响应特性以及应用可行性。
最终综合比较得出PNGV模型精度更高、鲁棒性强,也更加适合实践应用的结论。
锂电池安全性能无损检测技术研究进展

节能环保的新能源汽车是汽车行业发展的一个方向,也是我国的未来发展战略,电池作为新能源汽车的储能元件和供电电源,在新能源汽车上具有核心作用。
锂电池由于具有能量密度大、自放电率低、循环寿命长等优点,在新能源汽车领域得到了广泛应用。
但受应用环境、电池材料和生产工艺等不够完善等因素影响,电池组会出现能量效率降低、寿命缩短、电动汽车的续驶里程减小等问题,甚至导致燃烧、爆炸事故的发生,存在安全隐患。
NO.1锂电池安全隐患分析锂离子电池一般由正极、负极、正极引线、负极引线、中心管子、隔膜、电解质和电池外壳等组成。
电池正极为金属氧化物、掺杂化合物等,电池负极为碳素材料,电池电解液由无机锂盐和有机溶剂组成。
锂电池属于二次电池,通过锂离子在正负极之间的移动实现电池的充放电。
锂电池工作原理示意如图1所示。
图1 锂电池工作原理示意锂电池分为柱形锂电池与方形锂电池,又根据电池外包材料的不同分为铝壳锂电池、钢壳锂电池和软包锂电池。
近几年国内外锂电池的安全事故、召回数据表明,锂离子电池的安全事故主要表现为过热、燃烧和爆炸。
锂离子电池发生安全事故的主要原因是热积聚或热失控,表现为无法正常、及时散热或压力局部突增,进而导致电池失控,引起起火、爆炸等事故,一定程度上会威胁人身安全。
内部材料、制造工艺、非正常使用、使用疲劳等因素均有可能导致电池发生故障。
锂电池的生产包含极片制作、电芯组装、后处理等多个复杂工序,在生产过程中,可能出现划痕、颗粒、边缘破损、极片穿孔等十几种缺陷,因此,在出厂使用前,需要对锂电池进行缺陷检测,评估其安全性能。
笔者将锂电池存在的缺陷分为表面缺陷、电极缺陷以及内部缺陷三部分进行阐述,分别介绍其缺陷种类及其相应的检测方法。
NO.2锂电池安全性能检测方法01表面缺陷检测锂电池的表面缺陷主要是由原材料本身受损或仅生产线上受到误碰产生的,其主要表现为划痕、褶皱、鼓包、凹痕、凹坑、针眼、露铝、脏污等,其中针眼、露铝等严重缺陷会影响电池的安全性能。
电池包侧面碰撞仿真响应特性和安全性分析

第42卷第4期2020年12月南昌大学学报(工科版)Journal of Nanchang University( Engineering & Technology)Vol.42 No.4Dec.2020文章编号:1006-0456(2020)04-0386-06电池包侧面碰撞仿真响应特性和安全性分析董晴雯,王丽娟,陈宗渝,程晨,吴波(南昌大学机电工程学院,江西南昌330031)摘要:为了探究电池包箱体及其内部结构的安全性问题,结合企业某款纯电动汽车的电池包几何模型,采用均质化的建模方法建立包含电池箱体、电池模组、模组固定支架、连接螺钉、电芯连接铜片及其他结构件的精细化电池包有限元模型,并考虑电池包的实际安装位置,进行整车侧面碰撞仿真分析。
从车体结构、电池箱体、电池包内部模组等多个层面综合评价电池包碰撞安全性,结果表明,在侧面碰撞过程中电池包没有短路风险,满足法规中对碰撞后电池包安全性的相关要求。
关键词:纯电动汽车;碰撞安全分析;动力电池包;响应特性中图分类号:U469.72 文献标志码:AAnalysis of response characteristics and safety ofbattery pack side impact simulationD O N G Q i n g w e n,W A N G L i j u a n,C HE N Z o n g y u,C H E N G C h e n,W U B o(School of Mechatronics Engineering,Nanchang University,Nanchang 330031,China) Abstract:In order to explore the impact of the battery pack box and i t s internal structure on the safety of the battery pack,a modeling method as homogeneous was used to establish a detailed finite element model of the batterypack including the battery box,battery module,module fixing bracket,connecting screws,copper sheet connecting- battery core and other structural parts. A n d the simulation analysis of the vehicle,s side collision was performed. Comprehensively evaluated the safety of the battery pack from the car body structure,battery box,internal module of the battery pack,etc.The results showed that there was no risk of short circuit during the side collision,which metthe relevant requirements of the regulations on the safety of the battery pack after the collision.Key Words:pure electric vehicle;crash safety analysis;power battery pack ;response characteristics我国汽车行业发展还处于迅速发展时期,面临能 源紧缺和环境污染两大难题,在国家政策的支持下, 电动汽车获得迅猛的发展。
锂离子电池PFMEA

1 15
粘度高
粘度
常温下,粘度值 为15000±2000CP
粘度低
浆料稠,涂 布难操作
6
来料不良
粘结性差, 易掉料
8
来料不良
3 粘度计 4 粘度计
外包装无破裂、
外观
损伤,粘结剂为 乳白色,无沉淀
、杂质
有沉淀、杂质
浆料有颗 粒,涂布划 痕
5
运输破损、来 料不良
2 目视
过高
黏结剂失效 8 来料不良
1 pH精密试纸
责任及目标 完成日期
第3页,共35页
措施结果 采取的措施 S O D RPN
1 42
1 16 5 120 325目钢筛
石墨来料
振实 密度
≥0.5g/cm3
振实密度偏低 压实比低 7 来料不良
6
检
吸湿 性
相对湿度≥40%, 压片后≥6hr,不 掉料
容易吸水
极片易掉料 6 来料不良
6
比表 面
〈5m2/g
偏窄
电芯入壳难 5 来料不良
短路、爆炸 9 来料不良
盖板卡不进 4 来料不良
露极片,易 短路、电芯 7 来料不良 安全性能差
2 千分尺 2 千分尺 1 钢尺
5 钢尺
9 90 MSA
9 162
14
MSA 1 35
热缩 横向≤1%;纵向 性 ≤5%
高温性能差
隔膜纸来 料检验
耐腐 蚀性
用电解液浸泡12H 后不腐蚀、不变 形
1 16
10 160 增加此项 10 140 IQC检 2 36
过程名称
过程 特性
控制要求
潜在失效模式
潜在的失效 后果
动力电池包模拟碰撞试验方法

动力电池包模拟碰撞试验方法There are several important factors to consider when simulating a collision test for a power battery pack.在模拟动力电池包碰撞试验时,有一些重要的因素需要考虑。
Firstly, it is essential to accurately replicate real-world collision scenarios in the testing environment. This involves understanding the typical impact forces and angles that a battery pack may experience in a collision, and creating a test setup that can mimic these conditions.首先,需要在测试环境中准确复制真实世界的碰撞场景。
这涉及到理解动力电池包在碰撞中可能经历的典型冲击力和角度,以及创建一个可以模拟这些条件的测试装置。
Additionally, the structural integrity and safety features of the battery pack must be evaluated during the simulation. This includes assessing the effectiveness of the pack's housing and any additional components designed to protect it during a collision.此外,在模拟中必须评估电池包的结构完整性和安全特性。
这包括评估电池包的外壳和任何其他设计用于在碰撞中保护其的附加部件的有效性。
- 1、下载文档前请自行甄别文档内容的完整性,平台不提供额外的编辑、内容补充、找答案等附加服务。
- 2、"仅部分预览"的文档,不可在线预览部分如存在完整性等问题,可反馈申请退款(可完整预览的文档不适用该条件!)。
- 3、如文档侵犯您的权益,请联系客服反馈,我们会尽快为您处理(人工客服工作时间:9:00-18:30)。
Detecting Location of Short Circuit in Simulation and Comparison with CT Scan of Cells Tested
Location of short circuit
CT Scans courtesy of Exponent
Impact and Crashworthiness Lab (ICL)
Tested Samples Uniaxial Test Biaxial Loading Fixture
Current Collectors Electrodes
Separator
SEMs
Impact and Crashworthiness Lab (ICL)
List of ICL Publications on Battery Research
c c b b a
Impact and Crashworthiness Lab (ICL)
Prediction of Crack Location and Orientation, Indicating Short Circuit Area
Small Lithium-ion Pouch Cell
Impact and Crashworthiness Lab (ICL)
Characterization Plasticity and Fracture of Shell Casing of Cylindrical Cell
Impact and Crashworthiness Lab (ICL)
Jellyroll Components Tests and Scanning Electron Microscopies (SEM)
Six Length Scales in a Battery Pack This set of slides presents selected important results of tests and simulations performed at Impact and Crashworthiness Lab at three different scales: • Battery Pack level • Cell level • Component (Micro-Scale) level
Impact and Crashworthiness Lab (ICL)
Battery Pack with Cylindrical Cells, Simulation of Ground Impact
Impact and Crashworthiness Lab (ICL)
Prediction of Onset of Electric Short Circuit
Onset of Short Circuit
Finite Elerical Cell and Validation
Onset of Short Circuit
Impact and Crashworthiness Lab (ICL)
Simulation of UNDOT Test of a Cylindrical Cell
Modeling Lithium-ion Batteries and Packs for Crash Safety
MIT Impact and Crashworthiness Lab
Impact and Crashworthiness Lab (ICL)
Content of this Presentation
• • • • Xia Y., Wierzbicki T., Sahraei E., Zhang X., “Damage of Cells and Battery Packs Due to Ground Impact”, Journal of Power Sources (Impact Factor: 4.95), 2014 Sahraei E., Meier J., Wierzbicki T., “Characterizing mechanical properties and onset of short circuit for three types of lithium-ion pouch cells,” vol.247, pp. 503-516, 2014. , Journal of Power Sources (Impact Factor: 4.95), 2013. Wierzbicki T., Sahraei E., “Homogenized mechanical properties for the jellyroll of cylindrical Lithium-ion cells,” Journal of Power Sources (Impact Factor: 4.95), Volume 241, pp 467-476 2013. Sahraei E., Campbell J., Wierzbicki, T., “Detection of Short Circuit in 18650 Li-ion Cells under Mechanical Abuse: Experiments, Finite Element Modeling, and Validation,” Journal of Power Sources (Impact Factor: 4.95), Volume 220, pp 360–372, 2012. Sahraei E., Hill R., Wierzbicki, T., “Calibration and Finite Element Simulation of Pouch Li-ion Batteries for Mechanical Integrity,” Journal of Power Sources (Impact Factor: 4.95), Vol. 201, pp 307– 321, 2012. Sahraei E., Wierzbicki T., “Testing and Constitutive Modeling of Four Types of Lithium-ion Batteries,” Battery Safety 2013, San Diego, CA, Nov. 14-15, 2013. Sahraei E., Wierzbicki T., “Crashworthiness and Internal Short Modeling for Pouch and Cylindrical Lithium-ion Cells,” Proceeding od Batteries 2013, Nice, France, Oct. 14-16, 2013. Meier J., Sahraei E., Salk M., Kisters T., Huberth F, “State of Charge vs. Thermal Runaway for Lithium Ion Large Pouch Cells”, Proceedings of 3rd Battery Congress, East Lansing, MI, 2013. Campbell J., Sahraei E., and Wierzbicki T., “Detecting and modeling the onset of short circuit in a Li-ion cell under mechanical loading,” Proceedings of 2nd Battery Congress, Ann Arbor, MI, 2012. Sahraei E., Hill R., and Wierzbicki T., “Modeling of Lithium-ion Cylindrical Batteries for Mechanical Integrity: Experiments, Calibrations, and Validation,” Proceedings of 1st Battery Congress, Ann Arbor, MI, 2011. Sahraei E., Wierzbicki T., Hill R., Luo, M., “Crash Safety of Lithium-Ion Batteries, Towards Development of a Computational Model,” SAE World Congress, Detroit, MI, SAE Technical Paper 2010-01-1078, 2010. Sahraei E., Hill R., and Wierzbicki T., “Modeling of Lithium-ion Batteries for Crash Safety,” Proceedings of International Auto Body Congress (IABC), November 3-4, Troy, MI, 2010.
9 kg mass dropped from a 61 cm height on a rigid cylinder of 15.8 mm in diameter
Impact and Crashworthiness Lab (ICL)
Finite Element Models of Three Types of Pouch Cells and Validation
• • • • • •
•
•