BE-1RV320-A4中文资料
LF315 LF320 - LF320A LF323 - LF323A LF350 使用手册说明书

Manuale di istruzione perlavastovigliepourd’utilisation pour NoticeNotice d’utilisationlave-vaissellefür Gebrauchsanweisung fürGebrauchsanweisungGeschirrspülerforInstructionmanual forInstruction manualdishwashers Manual de instrucciones paralavavajillasLF315LF320 - LF320ALF323 - LF323ALF350FOREWORD1. Read the instructions contained in the enclosed booklet carefully, because it contains important information on installation, operation and maintenance safety. Store this booklet carefully for any further consultation by other operators.2. Having removed the packing material, check that all the equipment is present.If there is any doubt, do not use it and contact qualified personnel.The packing elements (plastic bags, foam polystyrene, nails, etc.) should be kept away from children, because they are dangerous.3. Before switching the equipment on, make sure that the model plate data conforms to that of the electrical and water distribution network.4. Installation should be carried out by qualified personnel according to the manufacturer's instructions.5. This equipment should be destined to the use which it has been conceived for. Any other application should be considered improper and consequently dangerous.6. The equipment should only be used by personnel trained for its use.7. Operators must strictly follow all hygienic requirements in the handling of clean dishware and cutlery.8. Do not leave the machine in an environment at temperatures lower than 0°C.9. The protection of the machine is IP X4, therefore it should not be washed with high pressure directed water jets.10. Q ualified personnel only can access the control panel, after having disconnected the machine from the primary current supply.11. T he appliance is made according to EEC 89/336 regarding radio noise suppression and electromagnetic compatibility.12. A ccording to EEC directive nr.23 of 19/02/1973 and the law of actuation nr.791 of 18/10/1987, our appliances are built-up according to the good technique norms in force in Italy and abroad.13. N oise level of the machine, less than 63dB(A)INSTRUCTIONS FOR USEOPERATION AND USE1)Before washing make sure that:• the wall-mounted on/off switch is switched on;• the water tap is open;• water is present in the distribution network;• the pump protection filters are installed in their respective positions;• the overflow in inserted;• all rotating parts are free;• the rinse aid dispenser is full;• make sure that dishware is in good conditions as it may cause cleaning difficulty and haven bacteria.2)Set switch “A1” to position 1 to enable the automatic wash tank filling and the consequent triggering of the heating element. The lamp “B1” is on.3)As soon as visual indicator “B2” is ON, pour about 30 gr. of detergent directly into the tank, paying attention to distribute it uniformly on the filters, the quantity being according to supplier's instructions. Add 15 gr. every 7 cycles to achieve a concentration of 1,5 gr./lt. In order to respect our environment, use only the correct amount of detergent.When using chlorinated detergent, it is suggested to use an automatic dispenser; otherwise, brownish spots might appear on the surfaces due to chlorine reactions. Detergent should always be placed near the pump filter.4)Then, introduce the glasses or the cups to wash, after having removed the solid waste and having placed them into the proper racks. The cups and the glasses should be turned upside down, while the cutlery should be put vertically into the proper container, and the same applies to dishware.5)By means of switch “A1” select the wash cycle according to conditions of the dishware (except LF315 models):• with particularly dirty dishes or deep dishes select the long cycle (pos.2)• with normally dirty dishes select the short cycle (pos.1)6)Close the door and press the “A2” button to start cycle, the end of which will be indicated by the switching off of the “B3” lamp.N.B.: Machine in conformity with the existing hygienic standards, guaranteeing a final rinse at 82°C. Wash cycle automatically lengthened if final rinse temperature is not reached.7)Remove the rack and slightly incline it to permit a perfect drain; allow dishware to dry and after having washed one’s hands, handle the rack in order not to touch the dishware inside then place the rack on hygienically clean shelves.8)At the end of washing, switch “A1” in position "0"; empty out the tank by taking out the overflow tube, then close the door and put the switch “A1” in position "1" for a few minutes to wash the machine. Then again put the switch “A1” in position "0" and wait until the tank is completely empty. Machines with drain pump, with switch “A1” in position "1" and the door open, simply push the “A5” button for the drain cycle and wait until the button is off. At this point, the tank filter can be taken out, in order to be washed, then replace it with the overflow in its place. For any further information concerning equipment cleaning, read chapter "USEFUL SUGGESTIONS".9)When the washing is finished, switch off the equipment by turning off the main supply through the general wall switch and close the water supply.INSTRUCTIONS DURING THE WASHING1)Do not plunge bare hands into the water containing the detergent. If this happens, wash them immediately and abundantly with fresh water.2)When the machine is operating, do not open the door too rapidly.3)Use only specific anti-foaming detergents.4)Disconnect the equipment in case the machine is out of order or it does not work properly. For the repairs consult a technical assistance centre authorised by the manufacturer and ask only for an original spare parts.5)Never modify the thermostat settings.6)Check that lamp “B2” is on.7)Wash tank water should be changed at least twice a day or according to daily wash requirements.8)Do not subject clean dishware to any further cleansing treatment such as brushes or drying towels.If these instructions are not followed, the safety of the equipment can be compromised.USEFUL SUGGESTIONS1) MAINTENANCEIMPORTANT: Before carrying out the cleaning and maintenance operations, disconnect the equipment from the electric supply.Frequently check and clean the nozzles. The frequency of this operation will depend on the quantity of residues, which may result in an unsatisfactory washing result.For the inside and outside cleaning of the machine, do not use corrosive products such as sodium hypochlorite (bleach) savelling water and hydrochloric acid, acids, steel wool or steel brushes.The presence of calcium and magnesium salt in the water can compromise machine performance, thus ask qualified personnel to remove the deposits periodically.In order to avoid some oxidation risks, or chemical reactions, generally the stainless steel surfaces have to be well cleaned.2) OPTIMAL RESULTS:A possible wash deficiency can be noticed when residue remains.Marks can be caused by an insufficient rinse: in this case checkthat the rinse nozzles are clean and that there is sufficient water supply pressure.In case of dishware residue check that:• the washing nozzles are clean• the water temperature is around 60°C• there is detergent• the pump suction filter is clean• the racks are suitable for the dishes and cutlery that are to be washed • the position of the cutlery and the dishes in the racks are correct3) TEMPORARY MACHINE NON-USEIn case the machine is stopped for some weeks, it is recommended before closing it to fill the tank and run the machine with clean water, then empty it out, in order to avoid the forming of bad odour and that any residue remains in the pump.If necessary repeat this operation until the water leaving the machine is clean. If the machine is stopped for many weeks, it is recommended to oil the stainless steel surfaces with paraffin oil and to discharge the water from the boiler and the electric pump.4)SANITIZING THE MACHINESanitizing the machine at least once a week is of the utmost importance in order to guarantee hygiene even when the machine is not in use.It is advisable to use a disinfecting product suggested by an authorised detergent dealer.The use of this product will satisfy hygienic requirements, even during machine non use.Before switching off the machine run the machine briefly with cleanwater.5)HARD WATER CONDITIONSIf a hard water supply is present, mineral deposits will form within the machine and also on dishware.In order to avoid the above conditions a periodic removal of these deposits is necessary.The frequency and method of this operation upon consultation by your detergent supplier.6)RESINS REGENERATION OF THE WATER SOFTENER (only for machines with built-in water softener)The resins regeneration of the water softener is completely automatic. The medium frequency of this operation is about every 40 baskets (referred to an initial hardness of 24° Clark). In any case, this value can change according to the water hardness; some opaque spots on the glasses will show that it is necessary to start the regeneration. This operation has to be carried out at the end of working day and with full tank.First of all, make sure that in the designated tank container “S” there is some coarse salt (1 Kg. is enough for about 5 regenerations). Set the switch “A1” to position "1", then push the button “A4” till the lamp “B4” is on.At this point the machine automatically performs all the necessary operations for about 20 minutes, during this operation the machine cannot be used. When the lamp is off, it means that the regeneration is finished. At this point, it is recommended to switch off the machine, to empty the tank and the equipment is ready to be used.CONTROL PANELSA1Main switch0Machine off1Short cycle2Long cycleA2Push button “CYCLE START”A4Push button “REGENERATION” (models LF320A and LF323A) A5Push button “DRAIN CYCLE” (if required)B1Pilot lamp “MACHINE ON"B2Pilot lamp “MACHINE READY"B3Pilot lamp “MACHINE WORKING"B4Pilot lamp “REGENERATION” (models LF320A and LF323A) B5Pilot lamp “DRAIN CYCLE” (if required)I Regulating screw for rinse aid injectorS Salt container (models LF320A and LF323A)S Plug (models LF320, LF323 and LF350)INSTALLATION AND MAINTENANCEINSTRUCTIONSThe following instructions are addressed to a qualified personnel the only one authorised to carry out checks and repairs, if any.The manufacturer declines any responsibility in the case of interventions made by a non qualified personnel or the use of spare parts other than those supplied by the Manufacture.INSTALLATIONDuring installation, carry out proper machine levelling, which is a prerequisite for a correct operation thereof (max. tolerance 2°).In order to prevent any damage caused by steam going out of the machine, make sure that the surrounding materials do not deteriorate in its presence. After machine installation check thermostat settings, booster 85°C, tank 60°C.1)ELECTRICAL CONNECTIONThe electrical safety of this equipment is only assured if it is connected as follows. It is necessary to connect the equipment to an effective earthing as specified by the electrical safety regulations in force. Check that this basic requirement is complied with, in case of any doubt ask for a careful check of the installation by a qualified personnel. In the case the earthing is not efficient there will be a dispersion due to the suppresser.The machine shall be included in a correctly dimensioned equipotential, whose effectiveness is to be very tight in accordance to the procedures set for in the applicable safety standards. The connection shall be performed through a screw marked by the plate near the rear side of the appliance.The manufacturer declines any responsibility for any damages caused by lack of an effective ground installation. For three phase 380/400V hook-up, have available a wall circuit breaker switch with multiple phase protection (20A for models LF315, LF320 and LF320A; 16A for models LF323, LF323A and LF350) with contact aperture distance, equal to or not exceeding 3mm and a supply cable no less than 2.5mm². For other supplies the cable cross section must be calculated according to voltage and length of cabling. If cabling too long adjust cable size to Amp rating; do not pull on supply cable or install it under tension. If cable needs to be replaced use type H07RN-F.2)WATER CONNECTIONInstall a 55°C water tap in a well accessible place, terminating in a 3/4" fitting, which the pipe strainer and inlet hose shall be connected to.Carefully comply with any national or regional regulations in force.The operating pressure should be neither less than 2 bars or greater that 4 bars (200/400 kPa). If water pressure is inferior then 2 bar, a pressure increase pump is necessary. If water pressure exceeds 4 bar, a pressure reducer is necessary.In order to obtain best results, it is suggested that the water supply have a hardness not greater that 8 Clarke.3)WATER DRAINArrange a water drain towards the floor with siphon and connect the machine with the flexible tube given with the machine, so that it leans towards the drain. Moreover, make sure that the hose does not have constrictions.Make sure that the building drain tubing withstands temperatures up to 70°C.4)RINSE AID DOSAGEMake sure that rinse aid suction hose is correctly installed in it’s proper container. The dosage is automatic with the adjusting of the screw "I", which after screwing to a full stop unscrew two turns. At this point the machine automatically takes the necessary liquid for every rinse: during the washing operations, check that the liquid of the container does not run short.For filling the dosing tube, start the machine without plugging the overflow in: at that point switch the machine on (pos.1) and off (pos.0). Repeat this operation several times at intervals of few seconds, until the rinse aid reaches the injector. Wait until the machine reaches the correct temperature (lamp “B2” on). Make some empty cycles, then try to wash: if the objects washed show some drops, this means that the rinse aid is insufficient. On the contrary, the presence of marks can mean that there is too much rinse aid or the water is too hard. The regulation can change according to the kind of rinse aid.5)DETERGENT DOSAGE (for machines with built-in detergent dispenser)With the screw on the side of the detergent pump, close completely the product intake, then slowly open the screw until the desired intake quantity has been reached. The correct quantity is indicated by the detergent supplier. Check that the intake of the pipe during the rinse cycle is as preset. (1cm = 1g approximately). Maximum intake or delivery distance: 2 meters.ENERGY CONSUMPTIONModel Wash tankcapacity(l)Rinse waterconsumpt.(l)Tankheater(W)Rinseheater(W)Washpump(W)Totalelectric load(W)Output inracks perhour with55°C inletwaterOutput inracks perhour with12°C inletwaterLF31518 3.520003000400350024--LF32018 3.520003000400350030/2010LF320A18 3.520003000400350030/2010LF32318 3.520004200450440036/2412LF323A18 3.520004200450440036/2412LF35018 4.020006000750675040/3017In the event of low water supply temperature, the will be a subsequent machine output drop.WIRING DIAGRAMA1Main switchA2Start switchA4Regeneration switch (mod.LF320A and LF323A only)A5Drain pump switch (if required)B1Pilot lamp power onB2Pilot lamp machine readyB3Pilot lamp machine workingB4Pilot lamp regeneration (mod.LF320A and LF323A only)B5Pilot lamp drain pump (if required)C2Booster heater contactorC2bis Safety contactor of booster heaterD1Wash timerD2Wash timerD4Regeneration timer (mod.LF320A and LF323A only)D5Drain pump timer (if required)E1Hot rinse solenoid valveE4Regeneration solenoid valve (mod.LF320A and LF323A only)F1Door switchG1CondensatorG2Anti noise filterH1JunctionM1Wash pumpM2Drain pump (if required)M3Detergent dispenser (if required)M6Rinse booster pump (if required)P1Pressure switchR2Booster heaterR3Tank heaterT2Booster thermostatT2A2nd contact of booster thermostatT2bis Booster safety thermostatT3Tank thermostatThe manufacturer declines any responsibility for any printing errors contained in this booklet. The manufacturer also reserves the right to make any modifications to its products that do not affect the basic characteristics thereof.REFER TO ELECTRICAL DRAWING。
AXE326124;AXE426124;AXE324324;中文规格书,Datasheet资料

Panasonic Corporation Automation Controls Business Unit /ac/eACCTB26E 201201-TORDERING INFORMATIONFEATURES1. 0.6 mm mated height low profile two-piece connectors2. Space-saving (3.0 mm widthwise)Smaller compared to F4 series (40 pin contacts):Socket — 40% smaller, Header — 43% smaller3. Low profile and highly resistant to various environments possible with the use of highly reliable“” connector design.4. Simple lock structure provides tactile feedback to ensure excellent mating/unmating operation feel.5. Gull-wing-shaped terminals to facilitate visual inspections.6. Connectors for inspection availableAPPLICATIONSMobile devices, such as cellular phones, digital still cameras and digital video cameras.SocketHeader2.4m m 3.0m m RoHS compliantBellows contact constructionNi barrier constructionV notch and Double contact constructions(Against foreign particles and flux!)Surface treatment (Contact portion / Terminal portion)<Socket>4: Ni plating on base, Au plating on surface (for Ni barrier available)<Header>4: Ni plating on base, Au plating on surface3: Narrow Pitch Connector A4F (0.4 mm pitch) Socket 4: Narrow Pitch Connector A4F (0.4 mm pitch) Header Mated height<Socket> / <Header>1: For mated height 0.6 mm AXE124Number of pins (2 digits)Functions2: Without positioning bosses/Panasonic Corporation Automation Controls Business Unit /ac/eAXE3, 4ACCTB26E 201201-TPRODUCT TYPES/Panasonic Corporation Automation Controls Business Unit /ac/e AXE3, 4ACCTB26E 201201-TDIMENSIONS (Unit: mm)ⅥSocket and Header are matedThe CAD data of the products with a CAD Data mark can be downloaded from: /ac/eⅥ Socket (Mated height: 0.6 mm)0.30±0.03(0.86)0.572.703.001.40C ±0.10.80(S u c t i o n f a c e )A B ±0.10.40±0.050.15±0.03Z noteY note(0.39)2.223.00Terminal coplanarity(Contact andsoldering terminals)0.08General tolerance: ±0.2Note:Since the soldering terminals has a single-piece construction,sections Y and Z are electrically connected.CAD DataⅥ Header (Mated height: 0.6 mm)Soldering terminalsS o l d e r i n g t e r m i n a l s0.15±0.030.461.901.221.94(0.36)C ±0.11.10(S u c t i o n f a c e )A B ±0.10.40±0.050.15±0.03Terminal coplanarity(Post andsoldering terminals)0.08(0.33)1.742.40General tolerance: ±0.2CAD Data0.60±0.1SocketHeader /Panasonic Corporation Automation Controls Business Unit /ac/eAXE3, 4ACCTB26E 201201-TEMBOSSED T APE DIMENSIONS (Unit: mm) (Common for respective contact types, sockets and headers)Ⅵ Specifications for taping(In accordance with JIS C 0806-1990. However, not applied to the mounting-hole pitch of some connectors.)Ⅵ Specifications for the plastic reel (In accordance with EIAJ ET -7200B.)Tape IT ape IIf t e r p a c k ag i n g/Panasonic Corporation Automation Controls Business Unit /ac/eACCTB26E 201201-TTABLE OF PRODUCT TYPESNote:When placing an order, substitute the “∗” (asterisk) in the above part number with the number of pins for the specific connector.NOTESFEATURES1. 3,000 mating and unmating cycles2. Same external dimensions and foot pattern as standard type.3. Improved matingInsertion and removal easy due to a reduction in mating retention force. This is made possible by a simple locking structure design.Note: Mating retention force cannot be warranted.APPLICATIONSIdeal for module unit inspection and equipment assembly inspectionSocket Header2.4m m 3.0m m Ⅵ Recommended PC board and metal mask patternsConnectors are mounted with high pitch density, intervals of 0.35 mm, 0.4 mm or 0.5 mm.In order to reduce solder bridges and other issues make sure the proper levels of solder is used.The figures to the right are recommended metal mask patterns. Please use them as a reference.• Socket (Mated height: 0.6 mm)Recommended PC board pattern (TOP VIEW)Recommended metal mask opening patternMetal mask thickness: When 120µm (T erminal opening ratio: 70%)(Metal-part opening ratio: 100%)• Header (Mated height: 0.6 mm)Recommended PC board pattern (TOP VIEW)Recommended metal mask opening patternMetal mask thickness: When 120µm (T erminal opening ratio: 70%)(Metal-part opening ratio: 100%)0.40±0.030.23±0.030.90±0.031.45±0.033.40±0.031.40±0.03(1.00)2.40±0.030.20±0.03(0.50)C 0.30: Insulation area0.40±0.010.20±0.010.90±0.013.40±0.011.40±0.01 1.45±0.01(1.00)2.50±0.013.30±0.01(0.40)C 0.300.40±0.030.23±0.030.45±0.030.80±0.032.06±0.031.00±0.03(0.53)1.50±0.032.80±0.03(0.65)0.40±0.010.20±0.010.45±0.012.06±0.011.00±0.010.80±0.01(0.53)1.66±0.012.70±0.01(0.52)Please refer to the latest product specifications when designing your product./Panasonic Corporation Automation Controls Business Unit /ac/eACCTB11E 201201-TNOTES FOR USING ADVANCED SERIES NARROW-PITCH CONNECTORS (Common)Ⅵ Connector mountingExcessive mounter chucking force may deform the molded or metal part of the connector. Consult us in advance if chucking is to be applied.Ⅵ Soldering1) Manual soldering.• Due to the connector’s low profile, if an excessive amount of solder is applied during manual soldering, the solder may creep up near the contact points, or solder interference may cause imperfect contact.• Make sure that the soldering iron tip is heated within the temperature and time limits indicated in the specifications.• Flux from the solder wire may adhere to the contact surfaces during soldering operations. After soldering, carefully check the contact surfaces and clean off any flux before use.• Be aware that a load applied to the connector terminals while soldering may displace the contact.• Thoroughly clean the iron tip.2) Reflow soldering• Screen-printing is recommended for printing paste solder.• T o determine the relationship between the screen opening area and the PC-board foot pattern area, refer to the diagrams in the recommended patterns for PC boards and metal masks. Make sure to use the terminal tip as a reference position when setting. Avoid an excessive amount of solder from being applied, otherwise, interference by the solder will cause an imperfect contact.• Consult us when using a screen-printing thickness other than that recommended.• Depending on the size of the connector being used, self alignment may not be possible. Accordingly, carefully position the terminal with the PC board pattern.• The recommended reflow temperature profile is given in the figure belowRecommended reflow temperature profile• The temperature is measured on the surface of the PC board near the connector terminal.• Some solder and flux types may cause serious solder creeping. Solder and flux characteristics should be taken into consideration when setting the reflow soldering conditions.• When performing reflow soldering on the back of the PC board after reflow soldering the connector, secure the connector using, for example, anadhesive (Double reflow soldering on the same side is possible)3) Reworking on a soldered portion • Finish reworking in one operation.• For reworking of the solder bridge, use a soldering iron with a flat tip. Do not add flux, otherwise, the flux may creep to the contact parts.• Use a soldering iron whose tiptemperature is within the temperature range specified in the specifications.Ⅵ Do not drop or handle theconnector carelessly. Otherwise, the terminals may become deformed due to excessive force or appliedsolderability may be degraded during reflow.Ⅵ Do not insert or remove the connector when it is not soldered. Forcibly applied external pressure on the terminals can weaken the adherence of the terminals to themolded part or cause the terminals to lose their evenness.Ⅵ Excessive prying-force applied to one end may cause product breakage and separation of the solder joints at the terminal.When removing the connector, be sure not to tilt the connectorexceeding 15 degrees widthwise. Excessive force applied for insertion in a pivot action as shown may also cause product breakage.Align the header and socket positions before connecting them.Ⅵ When cutting or bending the PC board after mounting the connector, be careful that the soldered sections are subjected to excessive forces.Ⅵ Notes when using a FPC.• When the connector is soldered to an FPC board, during insertion and removal forces may be applied to the terminals and cause the soldering to come off. It is recommended to use a reinforcement board on the backside of the FPC board to which the connector is beingconnected. Make sure that the reinforcing plate is larger than the outline of therecommended PC board pattern (Outline + approx. 1 mm). The reinforcing plate is made of SUS, glass epoxy or polyimide that is 0.2 to 0.3 mm thick.This connector employs a simple locking structure. However, the connector may come off depending on the size and weight of the FPC, layout and reaction force of FPC, or by drop impact. Make sure to fully check the equipment’s condition. T o prevent any problem with loose connectors, adopt measures to prevent the connector from coming off inside the equipment.Ⅵ Other NotesWhen coating the PC board aftersoldering the connector (to prevent the deterioration of insulation), perform the coating in such a way so that the coating does not get on the connector.The connectors are not meant to be used for switching.Time°C °C Upper limit (Soldering heat resistance)260°230°180°150°Lower limit (Solder wettability)Please refer to the latest product specifications when designing your product./分销商库存信息:PANASONICAXE326124AXE426124AXE324324。
CD3200中文手册-b前言

前言欢迎您成为CELL-DYN 3200系统的操作人员。
我们采用超凡脱俗的工艺技术,设计出供您使用的仪器,向您提供日常不间断的功能及可靠性。
CELL-DYN 3200系统得到了在工程、培训以及技术领域专业人员的大力支持。
由于您是我们尊贵的客户,我们将向您传授如何进行系统操作,维护及排除故障。
在可持续性服务方面,如您需要额外信息或在诊断方面遇到问题时需要协助,我们提供了电话技术支持服务。
该项服务在美国向您提供每周7天,每天24小时的服务保障。
如果有问题无法通过电话解决,则由雅培区域服务代理向您提供在线支持。
我们的区域服务代理接受过有关雅培使用仪器的全方位的培训,从而确保他们在诊断,隔离以及排除故障的熟练程度。
雅培实验室致力于从事生产最高质量、最为可靠的仪器。
我们希望能够最大限度地为您提供满意的服务。
客户支持美国:1(800)CELL DYN或1(800)235-5396雅培诊断客户支持中心200 Abbott Park RoadAbbott Park, Il 60064加拿大:1(800)387-8378在美国以外的客户,请与您所在地的血液学客户支持代理联系。
用途CELL-DYN 3200是多参数血液分析仪,用于在临床实验室中进行体外诊断。
所有权声明全部内容是在1995,1998,1999以及2001年经雅培实验室授权的。
雅培实验室软件程序受版权保护。
保留所有权力。
该软件是为雅培实验室设备而专门开发的,正如操作说明所述,是用于体外诊断的应用程序。
在未得到雅培实验室书面允许的情况下,不能对本文件中的任何部分以任何形式或任何方式(电子,机械,影印,记录或其他)进行复制,储存,或进行传播。
CELL-DYN 3200 System Operator’s ManualK —July 20022专利权声明以下为与CELL-DYN 3200仪器相关的美国所有权: 5,017,497; 5,378,633; 5,510,267; 以及 5,733,784仪器拒绝承诺必须执行所有操作说明。
[最新]瑞典多美达房车集成系统定制空调b3200中文说明
![[最新]瑞典多美达房车集成系统定制空调b3200中文说明](https://img.taocdn.com/s3/m/d5433f17df80d4d8d15abe23482fb4daa58d1d79.png)
中文说明书(Dometic顶置空调B3200)产品规格基本信息A.本说明书中描述的产品性能及相关参数进行调整时,本公司将不另行通知。
B.本空调/热泵(以下称“本产品”)主要用于:1.对出厂后的房车进行加装,以提高其舒适性能。
2.安装于房车的顶部。
C.安装基本要求1.开放式安装:安装前,需切空去除车顶至天花之间的材料。
2.电源要求:220-240伏交流电,50赫兹,10安培。
3.空调启动时电压不得低于198伏交流电,电源频率必须维持50赫兹不变。
D.空调的性能与房车本身的受热情况有关。
车主可以采取相关措施降低房车的受热,以提高空调的制冷性能。
在室外温度极高的情况下,以下方法可以降低房车受热:1.将房车停放阴凉处。
2.使用遮阳布将车窗盖住(不透明的,同时将窗帘放下)。
3.将车门、车窗关闭或减少使用频率。
4.车内不使用任何产生热量的电器设备。
在湿度和室外温度都很高的情况下,使用“制冷”模式的“高风”档,空调的性能将会发挥至最佳状态。
如果事先知道当天的气温会很高,那么可以在早晨早些时候将空调打开,进行“预冷”,这样就可以在您上车时,车内就已经达到您满意的温度。
另外,一个更好的解决房车受热的办法就是,使用户外帐篷和窗户遮阳罩,以减少太阳直射带来的受热。
同时,在比较冷的晚上,这些东西还可以给您提供一个良好的空间享受派对。
E.关于冷凝水注意:如果本产品由于天花板及其它表面凝聚湿气太多而造成损坏,生产厂家将不负任何责任。
空气潮湿后,湿气很容易在冷的物体表面凝结。
所以,潮湿的空气进入车内后,天花、窗户及金属部件等表面就会出现凝聚的水汽。
空调正常工作时,能够对潮湿的空气进行除湿。
空调工作时,请关闭车门、车窗,以减少冷的物体表面凝聚水汽的形成。
主要参数。
ATV320_安装手册_CN_NVE41294_01
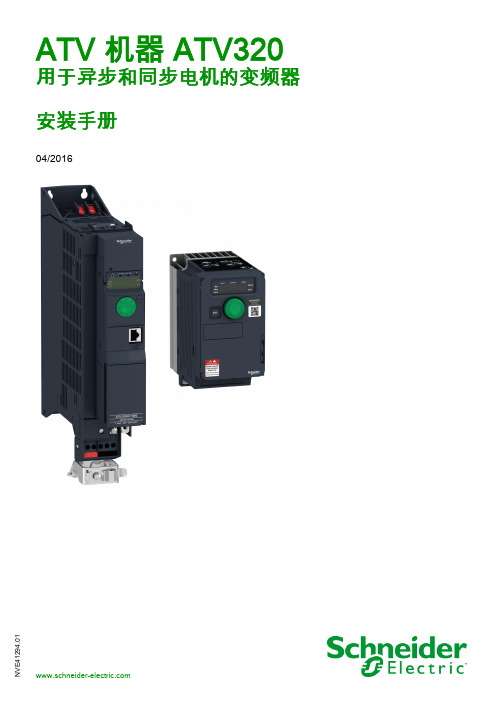
18
尺寸与重量. . . . . . . . . . . . . . . . . . . . . . . . . . . . . . . . . . . . . . . . . . . . . . . . . . . . . . . . . . . . . . .
19
变频器额定值 . . . . . . . . . . . . . . . . . . . . . . . . . . . . . . . . . . . . . . . . . . . . . . . . . . . . . . . . . . . . .
40
线缆长度说明 . . . . . . . . . . . . . . . . . . . . . . . . . . . . . . . . . . . . . . . . . . . . . . . . . . . . . . . . . . . . .
42
接线图 . . . . . . . . . . . . . . . . . . . . . . . . . . . . . . . . . . . . . . . . . . . . . . . . . . . . . . . . . . . . . . . . . .
43
漏型 / 源型开关配置 . . . . . . . . . . . . . . . . . . . . . . . . . . . . . . . . . . . . . . . . . . . . . . . . . . . . . . . .
47
电源接线端子的特性 . . . . . . . . . . . . . . . . . . . . . . . . . . . . . . . . . . . . . . . . . . . . . . . . . . . . . . .
ATV320调试参数

施耐德ATV320变频器起升(运行)机构的调试参数(英文部分,为无中文面板时对应菜单参数)主菜单(中文面板)
主菜单(简易LED)
标准电机频率,用自带简易LED设置时,初次会显示,之后不在此显示。
可在drc中
寻找。
速度给定
监视
设置
我的菜单
出厂设置
宏设置
全部简单启动
设置
电机控制
输入/输出设置
基本功能参数设置:
1.变频器菜单
StS
对于锥形电机,请设为
默认
UnS
nSP
tFr
tUn
自整定状态tUS
HSP
1.3设置(CONF )→全部(FULL)→设置(SET )
UUC
大小车,锥形电机)Std
(nO)
外部故障
EtF
未分配(nO)
如果电机控制方式为是压频比,抱闸设置如下:
2个预置速度PS2
SP2
SP4
SP8
如果是压频比控制或
no
bSt HOr/垂直升降
正向制动释放电流
SFC
SPG
制动器闭合频率
4位7段码对应LI9到PR的值,详见编程手册P52。
inovance MD320 MD320N变频器 说明书

MD320/MD320N用户手册
前言
表 1 MD320与MD300功能模块的区别
输入输出端子
控制方式 模拟给定方式
MD320
MD300
5个DI(双向输入,1个高速口),2个AI, 2个DO(1个高速口),1个AO,1个继电 器(可扩展I/O)
4个DI(单向输入,1个高速口),2个 AI,1个DO,1个AO,1个继电器
第一章 安全信息及注意事项 ………………………………………………………………… 10 1.1 安全事项 …………………………………………………………………………………………… 10 1.2 注意事项 …………………………………………………………………………………………… 13
第二章 产品信息 ……………………………………………………………………………… 16 2.1 命名规则 …………………………………………………………………………………………… 16 2.2 铭牌 ………………………………………………………………………………………………… 16 2.3 MD320N变频器系列 ……………………………………………………………………………… 17 2.4 技术规范 …………………………………………………………………………………………… 19 2.5 产品外型图、安装孔位尺寸 ……………………………………………………………………… 21 2.6 选配件 ……………………………………………………………………………………………… 32 2.7 变频器的日常保养与维护 ………………………………………………………………………… 33 2.8 变频器的保修说明 ………………………………………………………………………………… 34 2.9 选型指导 …………………………………………………………………………………………… 34 2.10 制动组件选型指南 ……………………………………………………………………………… 35
LNS Alpha 320 S3 自动送料系统说明书

Diameter range: 3 mm to 23 mmAUTOMATIC BAR FEEDING SYSTEM FOR FIX AND SLIDING HEADSTOCK LATHESYOUR ONE-STOP-SHOP FOR MACHINE-TOOL PERIPHERALS2INCREASE YOUR PRODUCTIVITYWith the Alpha 320 S3, LNS is offering a cost-effective solution for feeding bar material for fix and sliding headstock. The Alpha 320 S3 is designed to withstand any production process at optimum speeds. High-quality guidance, low noise emissions and effective vibration dampening are ensured by wear-resistant guide channels. In terms of its price-performance ratio, the Alpha 320 S3 is an ideal bar feeding system for the diameter range from 3 mm to 23 mm. MOBILE REMOTE CONTROL WITH TOUCHSCREENThe remote control with a colour, operator-friendly touchscreen (HMI) allows an easy setting and interface via menu-controlled icons, the bar feeder and the lathe. This ensures that the production process can be performed reliably and efficiently.The HMI is impressive due to its simple layout and ease of operation. It displays setting parame-ters, alarm descriptions and operating faults.SIMPLE AND RAPID CONVERSIONBar diameters on the side load rack of the bar feeder are changed over by a centrally controlled, manual setting using an adjusting lever.A position scale enables clear visualisation of the setting and prevents setting errors.• Two minutes for a diameter changeover in the area of the guide channels• Ten minutes for a diameter changeover of all guiding elementsPERFECT BAR GUIDANCEThe guide channels made from cast polyurethane are essential components for achieving opti-mum performance and withstanding the highest loads.The housings for the Alpha 320 S3's guide channels consist of a solid steel structure in order to dampen vibrations during the production processes. Combined with the servo-controlled drive, the bar material is guided through the entire machining process accurately and reliably.The quick-change guiding elements are secured in place by fixing pins. For a full diameter change-over, the elements can be replaced quickly and easily without needing to use any tools. The pusher can be released simply and quickly by unlocking the manual levers.Settings can be easily configured in less than one minute.The operator simply enters theparameters for the material into the HMI:• Bar diameter• Size of guide channel• Feeding lengthThe HMI automatically sets thefollowing parameters:• Feed force• Feed rate• Feeding length3POWERFUL REMNANT EXTRACTION SYSTEM WITH SELF-CEN-TRING CLAMPING JAWSThe sturdy design of the system not only provides enough force to insert and remove the material, but also ensures that the material can be reliably detected thanks to the mon-itoring system. This prevents failure during insertion or when the remnant is withdrawn. To optimally clamp bars with smaller diameters, soft materials or thin-walled tubes, the clamping force of the self-centring clamping jaws can be set using a pressure regulator.INCREASED RELIABILIT Y DURING OPERAT ION AT OPT IMUM SPEEDS The tried-and-tested LNS connection with telescopic tube ensures improved bar guidance in the area between the bar feeder and the lathe's spindle entry point.This connection can be used to move the headstock forward to finish parts without the risk of the bar being able to swing out freely.The system is designed such that corresponding reduction tubes can be inserted into the telescopic tube. These tubes are used as spindle reduction tubes at the same time.The inside diameters of the reduction tubes are adapted to the diameter of the bar feeder's guide channels. Vibrations and oscillations of the bar are reduced in the critical area and for the area where there is usually no guidance.This allows the system to run at optimum speeds for improving tolerances, enables the surface quality to be improved and the life time of the tools to be extended.FRONT RESTPneumatically actuated, the oil-flooded, two-position front rest with V-shaped guiding elements dampens the residual vibrations of the rotating bar material.When closed, the front rest remains at the bar itself. When open, the front rest holds the pusher when plunging into the lathe's spindle.The blow-off ring supplied eliminates the residual oil on the bars.MAXIMUM CONVENIENCEAs standard, the Alpha 320 S3 is equipped with a longitudinal movement system which is moni-tored by a safety switch. This device facilitates access to the lathe for maintenance or repair work.For the lathes which operate with /without guide bush, an adjustable two-positions movement system can optionally be supplied.S ubjecttom o d i fi c a t i o n s / A l p h a 320 S 3 – E N / 11-2016FEATURES AND BENEFITS • Hydrobar ® technology, hydrodynamic guidance of the bar material • Two minutes for a diameter changeover in the area of the guide channels • Ten minutes for a full guiding element changeover • Guide channels and pusher with quick-change system• Ergonomic control panel with colour touchscreen for ease of operation • Capacity: Side load rack, 270 mm • Compact, sturdy design • Actuated via servomotor• A utomatic setting of the feed force and speed when the material diameter is input • Automatic, oil-flooded, two-position front rest • Remnant ejection system • Simple manual diameter setting for the bar selection• T ried-and-tested LNS connection with telescopic tube for machines with sliding headstock • Can be fitted to the right or left-hand side depending on the lathe model • Longitudinal movement system, 430 mm• T he following are available as an option for lathes which operate with or without guide bush 2-Positions longitudinal movement, adjustable up to 270 mm 2-Positions longitudinal movement 350 mm YOUR ONE-ST OP-SHOP FOR MACHINE-T OOL PERIPHERALS LNS provides a full range of bar feeders, chip conveyors, coolant manage-ment systems and air filtration systems which is second to none on the market. We are known in the industry for the solid expertise we have gained over several decades in an exceptionally wide range of applications, our excellent customer service and technical support. This support is ensured by highly qualified technicians who are available at key locations throughout2-Positions longitudinal movement 350 mm。