齿轮传动设计
齿轮齿条传动设计计算
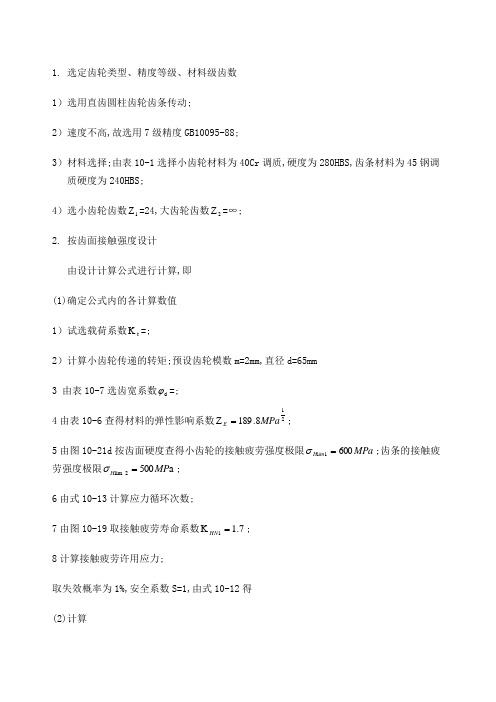
1. 选定齿轮类型、精度等级、材料级齿数1)选用直齿圆柱齿轮齿条传动;2)速度不高,故选用7级精度GB10095-88; 3)材料选择;由表10-1选择小齿轮材料为40Cr 调质,硬度为280HBS,齿条材料为45钢调质硬度为240HBS;4)选小齿轮齿数1Z =24,大齿轮齿数2Z =∞;2. 按齿面接触强度设计由设计计算公式进行计算,即(1)确定公式内的各计算数值1)试选载荷系数t K =;2)计算小齿轮传递的转矩;预设齿轮模数m=2mm,直径d=65mm3 由表10-7选齿宽系数d ϕ=;4由表10-6查得材料的弹性影响系数218.189MPa E =Z ;5由图10-21d 按齿面硬度查得小齿轮的接触疲劳强度极限MPa im H 6001l =σ;齿条的接触疲劳强度极限a 5002 lim MP H =σ;6由式10-13计算应力循环次数;7由图10-19取接触疲劳寿命系数7.11=K HN ;8计算接触疲劳许用应力;取失效概率为1%,安全系数S=1,由式10-12得(2)计算1)试算小齿轮分度圆直径1d t ,代入[]1H σ;2)计算圆周速度v;3计算齿宽b;4计算齿宽与齿高之比;模数齿高5)计算载荷系数;根据,7级精度,由图10-8查得动载荷系数1=V K ;直齿轮,1==ααF H K K ;由表10-2查得使用系数5.1=A K ;由表10-4用插值法查得7级精度、小齿轮为悬臂布置时250.1=βH K ; 由33.5=hb ,250.1=βH K 查图10-13得185.1=βF K ;故载荷系数 6)按实际的载荷系数校正所算得的分度圆直径,由式10-10a 得7计算模数m;3. 按齿根弯曲强度设计由式10-5得弯曲强度设计公式为(1) 确定公式内各计算数值1)由图10-20c 查得小齿轮的弯曲疲劳强度极限a 5501MP FE =σ;齿条的弯曲强度极限a 3802MP FE =σ;2)由图10-18取弯曲疲劳寿命系数1.11=FN K ,2.12=FN K ;3)计算弯曲疲劳许用应力;取弯曲疲劳安全系数S=,由式10-12得4计算载荷系数K;5查取齿形系数;由表10-5查得65.21a =F Y ,06.22a =F Y ;6查取应力校正系数;由表10-5查得58.11a =S Y ,97.12a =S Y ;7)计算齿轮齿条的[]F Sa Fa Y Y σ并加以比较;齿条的数值大;(2) 设计计算由于齿轮模数m 的大小主要决定弯曲强度,而齿面接触疲劳强度主要取决于齿轮直径;可由弯曲强度算得的模数并就近圆整为标准值m=4mm,按接触强度算得的分度圆直径mm d 84.771=,算出齿轮齿数以上计算过程验证了模数m=2,直径d=65的齿轮是符合强度要求的。
齿轮齿条传动设计计算
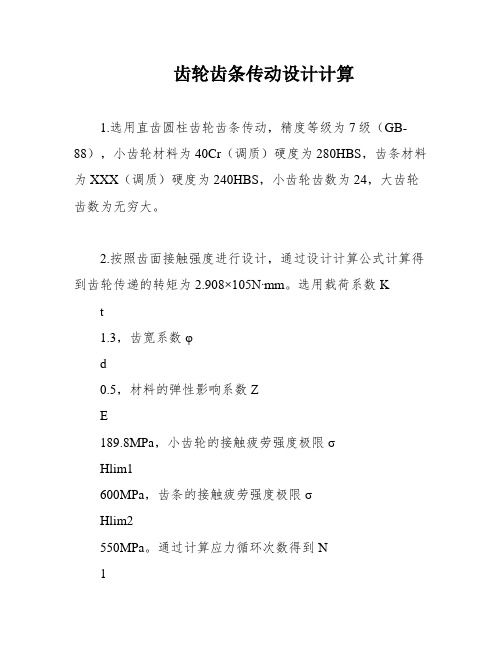
齿轮齿条传动设计计算1.选用直齿圆柱齿轮齿条传动,精度等级为7级(GB-88),小齿轮材料为40Cr(调质)硬度为280HBS,齿条材料为XXX(调质)硬度为240HBS,小齿轮齿数为24,大齿轮齿数为无穷大。
2.按照齿面接触强度进行设计,通过设计计算公式计算得到齿轮传递的转矩为2.908×105N∙mm。
选用载荷系数K t1.3,齿宽系数φd0.5,材料的弹性影响系数ZE189.8MPa,小齿轮的接触疲劳强度极限σHlim1600MPa,齿条的接触疲劳强度极限σHlim2550MPa。
通过计算应力循环次数得到N16.113×104,接触疲劳寿命系数KHN11.7.根据失效概率为1%和安全系数S=1,计算得到接触疲劳许用应力[σH11020MPa。
3.计算小齿轮分度圆直径dt1为68.89mm,圆周速度v为0.029m/s,齿宽b为34.445mm,齿宽与齿高之比为2.87,齿高为6.46mm。
计算载荷系数根据速度v=0.029m/s、精度为7级,查图10-8得动载荷系数KV=1;由于是直齿轮,故KHα=KFα=1;根据表10-2得使用系数KA=1.5;根据表10-4用插值法得到7级精度、小齿轮为悬臂布置时的KHβ=1.250.再根据h=5.33和KHβ=1.250查图10-13得KFβ=1.185.因此,载荷系数K=KA×KV×KHα×KHβ=1.5×1×1×1.250=1.875.按实际的载荷系数校正所算得的分度圆直径,由式(10-10a)得d1t=31.875K/d1=68.89mm,因此d1=77.84mm。
计算模数m根据齿根弯曲强度设计,由式(10-5)得弯曲强度设计公式为:m≥(2KT1YFaYSa)/(φdz1[σF]3)确定公式内各计算数值:1.根据图10-20c,小齿轮的弯曲疲劳强度极限σFE1=500MPa,齿条的弯曲强度极限σFE2=380MPa。
齿轮传动设计

齿轮传动设计主要内容1、齿轮传动的失效形式,各种失效的机理和特点,预防止措施及齿轮传动计算准则。
2、齿轮材料的基本要求,软齿面与硬齿面的常用热处理方法及材料选用原则。
3、齿轮传动的受力分析,计算载荷,各种载荷系数的物理意义与影响因素。
4、直齿圆柱齿轮传动的齿面接触强度计算与齿根弯曲疲劳强度计算、斜齿圆柱齿轮传动和直齿锥齿轮传动的计算特点。
5、齿轮传动设计中主要参数的选择原则及影响因索,各参数间的相互影响关系。
基本要求1、掌握齿轮传动的失效形式(轮齿折断、点蚀、磨损、胶合、塑性变形)的特点、失效部位、失效机理、防止或减轻失效的惜施,以及针对不同失效形式的设计计算准则。
2、掌握选用齿轮材料的基本要求,软齿面与硬齿面的常用材料与热处理方法,合理地选用齿轮的配对材料及热处理方法。
3、熟练掌握齿轮传动的受力分析方法。
4、理解齿轮计算中要用计算载荷而不用名义载荷的道理,了解四个载荷系数的物理意义及其影响因素,采取哪些措施可减小载荷系数。
5、掌握直齿圆柱齿轮的接触疲劳强度计算与齿根弯曲疲劳强度计算的理论依据,以及力学模型、应力的类型与变化特性;掌握公式中各参数的意义。
对斜齿圆柱齿轮与直齿锥齿轮的强度计算,应根据它们的传动特点,由相应的当量齿轮转化为直面圆柱齿轮后再进行强度计算,但须注意它们的计算与直齿圆柱齿轮计算的异同点。
重点难点1、各类齿轮传动的失效形式;2、各类齿轮传动的受力分析及各分力的对应关系,尤其是斜齿圆柱齿轮轴向力方向的判定及力大小计算;3、载荷系数的影响因素及减小措施;影响齿轮强度的因素分析及主要参数的选择。
§3-1 概述齿轮传动是机械传动中最重要、应用最广泛的一种传动。
齿轮传动的主要优点有:传动效率高,工作可靠,寿命长,传动比准确,结构紧凑。
主要缺点是:制造精度要求高,制造费用大,精度低时振动和噪声大,不宜用于轴间距离较大的传动。
齿轮传动可做成开式、半开式和闭式齿轮传动。
开式齿轮传动:齿轮完全外露,易落入灰砂和杂物,不能保证良好的润滑,轮齿易磨损,多用于低速、不重要的场合。
齿轮传动设计计算实例.docx

各类齿轮传动设计计算实例例1设计铳床中的一对标准直齿圆柱齿轮传动。
C 知:传递功率P = 7.5kw .小齿轮转速 m=1450r/mm 、传动比< = 2.08.小齿轮相对轴乐为不对称布誉,两班制,毎年I •作300d (天),使用 期限为5a (年九解,(1)选择齿轮材料及粘度等级考應此对齿轮传递的功率不大,故大、小齿轮都选用软齿而。
小齿轮选用4OCr,调质•齿而峡度为240〜260HBS ;大齿轮选用45钢,调质,齿而硬度为220HBS (表8.5)•因是机床用齿轮,由表8.10选7精度,要求齿山丙1糙度R a < 1.6〜3.2“” .(2)按齿面接触疲劳强度设讣因两齿轮均为钢制齿轮,所以山(8.28)式得2叫S 誹确定冇关参数如下:1) 齿数乙和齿宽系数Pd収小齿轮齿轮勺=30,则大齿轮齿数z 2=i Zl =2.08x30 = 62.4・圆整z 2 = 62 o 实际传动比i 0 = — = — = 2.067◎ 30传动比误基 = 2 08-2.067 = 0 6%<2-5% 町用。
i2.08齿数比u = /0 = 2.067由表8.9 取忆= 0.9 (因非对称布置及软齿而)2) 转矩T,P7 5T. =9.55xl06—= 9.55xl06x —/nw = 4.94xl04mm“I 14503) 載荷系数K由表8.6取K = 1.35I )许用接触应力0〃]曲图 8. 33c 査得 o Hhmi = 775M/U o Hhml = 520M 內 由式(8.33)计算应力循环次数NzN u = 6叽5 = 60 x 14 50 x 1 x (16x 300 x 5)= 2.09xl09N"由图& 34査得接傩疲劳的寿命系数Z 灯i =0.89 , Z 附2 =0.93 通过齿轮和一般匚业齿轮,按一般可靠度要求选取A S Z/ =1.0-所以计算两轮的许用接触卜/故得笛胖689.81叭1.0MFd = 483・6MFd520x0.93心"6处竺怦=7643』站心仆心x (2.076 + l)〃吩59.40MV <Pd lt \pH F V 0.9x2.076x483 62I )许用弯曲应力\a F ]由式(8.34)由图& 35c 森得:= 290MPa 厂 2L0MPa由图8. 36査得试验齿轮的咸力修正系数 按一般可靠度选取安全系数 计算阳轮的许用弯曲应力[J =叽上/ f = 290X 2X 0.SS = 40&32M 〃1 h S N1.25[]=m = 210x2x09 Mpa = 302.4M 九 1 J - S N 1.2、将求得的各参数代入式(8.29〉2K1\F 严厂亠丫刖bnrzi= 2x1.35x4.94x2 x2 52x1.625咖55X 22 X 30= 82・76MFa<E[= 80 18MF% 订 2故轮齿齿根穹曲彼劳强度足够。
机械设计基础中的齿轮传动设计
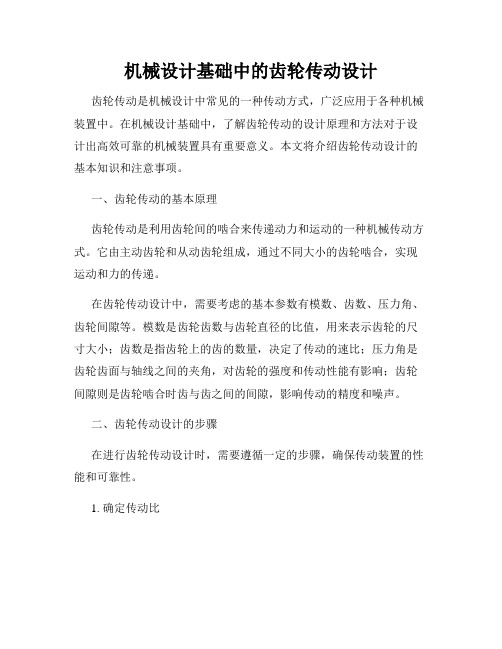
机械设计基础中的齿轮传动设计齿轮传动是机械设计中常见的一种传动方式,广泛应用于各种机械装置中。
在机械设计基础中,了解齿轮传动的设计原理和方法对于设计出高效可靠的机械装置具有重要意义。
本文将介绍齿轮传动设计的基本知识和注意事项。
一、齿轮传动的基本原理齿轮传动是利用齿轮间的啮合来传递动力和运动的一种机械传动方式。
它由主动齿轮和从动齿轮组成,通过不同大小的齿轮啮合,实现运动和力的传递。
在齿轮传动设计中,需要考虑的基本参数有模数、齿数、压力角、齿轮间隙等。
模数是齿轮齿数与齿轮直径的比值,用来表示齿轮的尺寸大小;齿数是指齿轮上的齿的数量,决定了传动的速比;压力角是齿轮齿面与轴线之间的夹角,对齿轮的强度和传动性能有影响;齿轮间隙则是齿轮啮合时齿与齿之间的间隙,影响传动的精度和噪声。
二、齿轮传动设计的步骤在进行齿轮传动设计时,需要遵循一定的步骤,确保传动装置的性能和可靠性。
1. 确定传动比传动比是指主从动齿轮的齿数比值,决定了传动装置的输出速度和扭矩。
根据所需的输出速度和扭矩,选择合适的齿轮齿数组合,计算得出传动比。
2. 选择模数和齿轮参数根据传动比和要求的齿轮尺寸,选择合适的模数和齿数。
在进行选型时,需要考虑齿轮的强度、噪声和传动精度等要求。
3. 计算齿轮尺寸根据所选的模数和齿数,计算得出齿轮的尺寸和几何参数。
包括齿轮的外径、根圆直径、齿宽等。
4. 进行强度校核根据所选的齿轮尺寸和材料,进行强度校核。
通过计算齿轮的接触应力、弯曲应力和疲劳寿命等参数,判断齿轮的强度是否满足要求。
5. 进行传动效率计算根据齿轮的啮合条件和传动设计参数,计算传动的效率。
传动效率是指输入功率和输出功率之间的比值,可以评估传动装置的能量转换效率。
三、齿轮传动设计的注意事项在进行齿轮传动设计时,需要注意以下几点,以确保传动装置的性能和可靠性。
1. 合理选择齿轮材料齿轮传动中,对材料的选择要满足一定的强度和硬度要求。
常用的齿轮材料有合金钢、碳素钢等。
齿轮传动的特点和设计原理
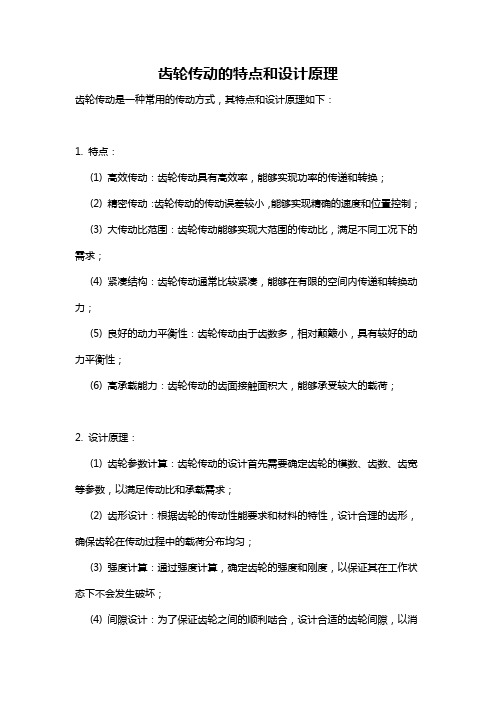
齿轮传动的特点和设计原理
齿轮传动是一种常用的传动方式,其特点和设计原理如下:
1. 特点:
(1) 高效传动:齿轮传动具有高效率,能够实现功率的传递和转换;
(2) 精密传动:齿轮传动的传动误差较小,能够实现精确的速度和位置控制;
(3) 大传动比范围:齿轮传动能够实现大范围的传动比,满足不同工况下的需求;
(4) 紧凑结构:齿轮传动通常比较紧凑,能够在有限的空间内传递和转换动力;
(5) 良好的动力平衡性:齿轮传动由于齿数多,相对颠簸小,具有较好的动力平衡性;
(6) 高承载能力:齿轮传动的齿面接触面积大,能够承受较大的载荷;
2. 设计原理:
(1) 齿轮参数计算:齿轮传动的设计首先需要确定齿轮的模数、齿数、齿宽等参数,以满足传动比和承载需求;
(2) 齿形设计:根据齿轮的传动性能要求和材料的特性,设计合理的齿形,确保齿轮在传动过程中的载荷分布均匀;
(3) 强度计算:通过强度计算,确定齿轮的强度和刚度,以保证其在工作状态下不会发生破坏;
(4) 间隙设计:为了保证齿轮之间的顺利啮合,设计合适的齿轮间隙,以消
除传动误差和噪声;
(5) 轴布置和连接:设计齿轮传动的轴布置和连接方式,确保各部件之间的协调和传递力矩的可靠性;
(6) 润滑和冷却设计:为了保证齿轮传动的运转稳定和寿命,设计合适的润滑和冷却系统,以降低传动过程中的摩擦和温度。
综上所述,齿轮传动具有高效传动、精密传动、大传动比范围、紧凑结构、良好的动力平衡性和高承载能力等特点,其设计原理主要包括齿轮参数计算、齿形设计、强度计算、间隙设计、轴布置和连接、润滑和冷却设计等。
齿轮传动设计

从动轮2:vs背离节线,Ff指向节线,塑 变后在齿面节线处形成凸脊。 改善措施:1)↑齿面硬度; 2)采用η↑的润滑油。
二、齿轮传动的设计准则 失效形式→相应的设计准则 1、闭式齿轮传动 主要失效为:点蚀、轮齿折断、胶合 软齿面:主要是点蚀、其次是折断,按齿面接触疲劳强度设 计计算、校核齿根的弯曲疲劳强度。 硬齿面:主要是折断、其次是点蚀,按齿根的弯曲疲劳强度 设计计算、校核齿面的接触疲劳强度。 高速重载还要进行抗胶合计算 2、开式齿轮传动 主要失效为:齿面磨损、轮齿折断,按齿根弯曲疲劳强度设 计,但适当降低(20%)许用应力以考虑磨损 的影响。 3、短期过载传动 过载折断 齿面塑变 静强度计算
4.齿面胶合——严重的粘着磨损 现象:齿面沿滑动方向粘焊、撕脱,形成沟痕。 原因:高速重载——v↑,Δt ↑,油η↓,油膜破坏,表 面金属直接接触,融焊→相对运 动→撕裂、沟痕。 低速重载——P↑、v ↓,不易形成油膜→冷胶合。
后果:引起强烈的磨损和发热,传动不平稳,导致齿 轮报废。
改善措施:
1)↓m→↓齿高h→↓齿面vs(必须满足σF); 2)采用抗胶合性能好的齿轮材料对; 3)降低齿面压力,采用良好的润滑方式及润滑剂; 4)提高接触精度,采用角变位齿轮,↓啮合开始和
现象:节线靠近齿根部位出现麻点状小坑。
原因:σH>σHP 脉动循环应力 1)齿面受多次交变应力作用,产生接触疲劳裂纹;
2)节线处常为单齿啮合,接触应力大; 3)节线处为纯滚动,靠近节线附近滑动速度小,油膜不易形 成,摩擦力大,易产生裂纹;
4)润滑油进入裂缝,形成封闭高压油腔,楔挤作用使裂纹扩 展。(油粘度越小,裂纹扩展越快)
FP
Flim YST
SFmin
YN
式中: бFlim——试验齿轮齿根的弯曲疲劳极限,查图11-12;
机械设计中的齿轮传动系统设计
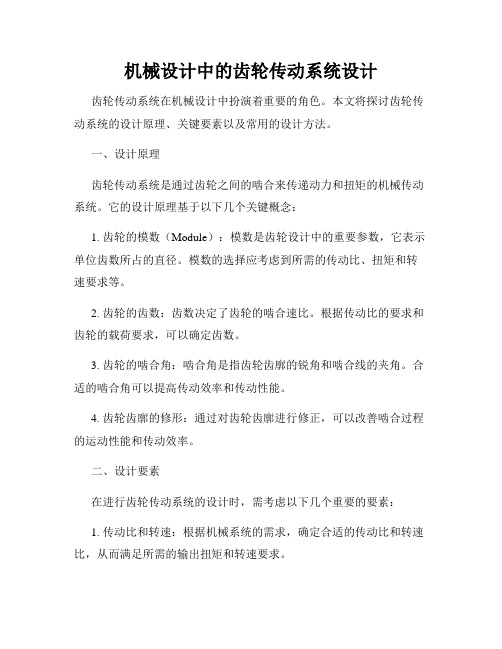
机械设计中的齿轮传动系统设计齿轮传动系统在机械设计中扮演着重要的角色。
本文将探讨齿轮传动系统的设计原理、关键要素以及常用的设计方法。
一、设计原理齿轮传动系统是通过齿轮之间的啮合来传递动力和扭矩的机械传动系统。
它的设计原理基于以下几个关键概念:1. 齿轮的模数(Module):模数是齿轮设计中的重要参数,它表示单位齿数所占的直径。
模数的选择应考虑到所需的传动比、扭矩和转速要求等。
2. 齿轮的齿数:齿数决定了齿轮的啮合速比。
根据传动比的要求和齿轮的载荷要求,可以确定齿数。
3. 齿轮的啮合角:啮合角是指齿轮齿廓的锐角和啮合线的夹角。
合适的啮合角可以提高传动效率和传动性能。
4. 齿轮齿廓的修形:通过对齿轮齿廓进行修正,可以改善啮合过程的运动性能和传动效率。
二、设计要素在进行齿轮传动系统的设计时,需考虑以下几个重要的要素:1. 传动比和转速:根据机械系统的需求,确定合适的传动比和转速比,从而满足所需的输出扭矩和转速要求。
2. 动力传递和承载能力:根据工作条件和载荷要求,选择合适的齿轮材料和热处理工艺,确保齿轮传动系统能承受所需的载荷和传递所需的动力。
3. 齿轮啮合的几何要求:通过几何参数的选择,确保齿轮啮合过程的顺利进行,同时避免齿轮齿面的过度磨损和损坏。
4. 齿轮传动的噪声和振动控制:通过合理的齿轮设计和优化,减少齿轮传动过程中产生的噪声和振动,提高传动系统的运行平稳性和寿命。
三、设计方法在实际的齿轮传动系统设计过程中,可以采用以下几种常用的设计方法:1. 标准化设计:根据已有的标准齿轮模型和参数,选择合适的齿轮尺寸和几何参数,简化设计过程,提高效率。
2. 计算机辅助设计:借助计算机辅助设计软件,进行齿轮传动系统的三维建模和力学分析,快速得到设计结果。
3. 优化设计:通过设计参数的优化选择,使齿轮传动系统满足最佳的传动性能和经济指标。
4. 实验验证:设计完成后,进行实验验证,测试齿轮传动系统的性能和可靠性,发现潜在问题并进行改进。
- 1、下载文档前请自行甄别文档内容的完整性,平台不提供额外的编辑、内容补充、找答案等附加服务。
- 2、"仅部分预览"的文档,不可在线预览部分如存在完整性等问题,可反馈申请退款(可完整预览的文档不适用该条件!)。
- 3、如文档侵犯您的权益,请联系客服反馈,我们会尽快为您处理(人工客服工作时间:9:00-18:30)。
机械原理 课程设计说明书
设计题目:齿轮传动设计 学 院:工程机械学院 专 业:机械设计制造及其自动化 班 级:25040808 设 计 者:刘 春(学号:25) 指导教师:张老师
2011-01-13 课程设计说明书 一、设计题目:齿轮传动设计 如图所示,齿轮变速箱中,两轴中心距为80㎜,
各轮齿数为Z1=35,Z2=45,Z3=24,Z4=55,Z5=19,Z6=59,模数均为m=2㎜,试确定各对齿轮
的传动传动类型,并设计这三对齿轮传动。
二、全部原始数据: Z1=35,Z2=45,Z3=24,Z4=55,Z5=19,Z6=59,
m=2mm, ha*=1, c*=0.25, α=20, a'=80mm
三、设计方法及原理: (一)传动的类型及选择: *按照一对齿轮的变位因数之和(X1+X2)的不同,齿轮传动可分为三种类型。
1. 零传动(X1+X2=0)
a. 标准齿轮传动:X1=X2=0 传动特点:设计简单,便于互换。 b. 高度变为齿轮传动:X1=-X2≠0,X1+X2=0。一般小齿轮
采用正变位,大齿轮采用负变位。 传动特点:互换性差,需成对设计和使用,重合度略有降低。
2. 正传动(X1+X2>0) 传动特点: ① 可以减小齿轮机构的尺寸。 ② 可以减轻齿轮的磨损程度。 ③ 可以配凑中心距。 ④ 可以提高两轮的承载能力,由于两轮都可以采用正变。位,可以增加两齿轮的齿根厚度,从而提高两齿轮的抗弯能力。 ⑤ 互换性差,需成对设计,制造和使用。 ⑥ 重合度略有降低。
3. 负传动(X1+X2<0) 传动特点: ① 重合度略有降低。 ② 互换性差,需成对设计,制造和使用。 ③ 齿厚变薄,强度降低,磨损增大。 综上所述,正传动的优点突出,所以在一般情况下,采用正传动;负传动是最不理想的传动,除配凑中心距的不得已情况下,尽量不用;在传动中心距等于标准中心距时,为了提高传动质量,可采用高度变位齿轮传动代替标准齿轮传动。
(二)变位因数的选择: *根据设计要求,可在封闭图上选择变位因数。 封闭图内容解释: 1. 封闭图中阴影区是不可行区 ,无阴影区是可行区。所选择的变位因数的坐标点必须在可行区内。 2. 根据不发生根切的最小变位因数算出两个齿轮不发生根切的限制线X1min,X2min分别平行于两坐标轴,若变位因数X1在X1min线的右边,变位因数X2在X2min线的上方,则所设计的齿轮完全不发生根切。 曲线①和②是允许两齿轮有微量根切的限制线。当这种微量跟切得跟切点不进入不进入齿廓工作段时,将不会降低重合度。如果允许微量根切,则变位因数可取在曲线①右侧和曲线②的上方。 3. 曲线③是重合度位1的曲线,还有一条是重合度为1.2的
曲线。当在曲线③的左下方选取变位因数时,则εα≥1,当在εα
=1.2曲线左下方选取变位因数时,εα>1.2。
4. 曲线④是齿顶厚sa1=0的限制曲线,还有两条限制曲线分别是sa1=0.25m和sa2=0.4m。 例:所设计齿顶厚sa1>0.4m,则应在sa1=0.4m曲线左上方选取X1值。 5. 曲线η'=η"是等滑动磨损曲线。表示两齿轮材质相同,齿根部分磨损相同。 6. 节点位置曲线,曲线δ1=0.0表示节点正好位于两齿轮啮合图中靠近B1点的C点位置。(注:C为一对齿轮单齿啮合区和双
齿啮合区的分界点)曲线δ1=0.6表示节点位于靠近B1点的双齿啮合区内,与C点相距0.6m;曲线δ2=0.0表示节点正好位于另一单齿啮合与双齿啮合的分界点D;δ2=0.6m的曲线表示节点位于靠近B2的点的双齿啮合区内离D点距离为0.6m。 如果在曲线δ1=0.0与δ2=0.0之间的区域内选择变位因数,则节点位于单齿啮合区内。 7. 两轮齿根弯曲疲劳强度相等的曲线是: ① 点划线a:两轮材料相同,小齿轮为主动轮时; ② 点划线b:两轮材料相同,大齿轮为主动轮时; 由上述论述可知,对于两齿轮齿数不同的组合,就有不同的封闭图。但是,封闭图册上的齿数组合是有限的。当所设计的齿轮其齿数组合与图册上的不同时,可参考齿数相近的封闭图。
四、设计及计算过程: (一)齿轮Z1和齿轮Z2 1. 求标准中心距a: a=m(Z1+Z2)/2=80㎜ 2. 求啮合角α' cosα'=acosα/a' α'=20°
3. 求变位因数之和X1+X2; 由无侧隙啮合方程式可得: X1+X2=(Z1+Z2)(invα'-invα)/2tanα=0.0 4. 在封闭图上做直线 X1+X2=0.0,此直线上所有点均满足变位 因数之和为0,中心距为80㎜的要求。此直线与等滑动磨损曲
线η'=η"的交点坐标为 X1=0.165,X2=-0.165满足两齿根磨损相等要求。 5. 计算几何尺寸: 参考变位系数值,选该齿轮传动为零传动。 中心距变动系数:y=(a'-a)/m=0
齿顶高变动系数:σ=X1+X2-y=0 齿顶高:ha1=(ha*+X1-σ)m=2.33㎜ ha2=(ha*+X2-σ)m=1.67㎜ 齿根高:hf1=(ha*+c*-X1)m=2.17㎜ hf2=(ha*+c*-X2)m=2.83㎜ 全齿高:h1=ha1+hf1=4.50㎜ h2=ha2+hf2=4.50㎜ 分度圆直径:d1=mz1=70㎜ d2=mz2=90㎜ 齿顶圆直径:da1=d1+2ha1=74.66㎜ da2=d2+2ha2=93.34㎜ 齿根圆直径:df1=d1-2hf1=65.66㎜ df2=d2-2hf2=84.34㎜ 基圆直径:db1=d1cosα=65.778㎜ db2=d2cosα=84.572㎜ 齿顶圆压力角:αa1=arccos(db1/da1)=28.231。 αa2=arccos(db2/da2)=25.032。
重合度:εa=[z1(tanαa1-tanα')+z2(tanαa2-tanα')]/2π=1.701 分度圆齿厚:s1=πm/2+2X1mtanα=3.381㎜ s2=πm/2+2X2mtanα=2.901㎜ 齿顶厚:sa1=s1ra1/r1-2ra1(invαa1-invα)=1.422㎜ sa2=s2ra2/r2-2ra2(invαa2-invα)=1.591㎜ (二)齿轮Z3和齿轮Z4 1.求标准中心距a: a=m(Z3+Z4)/2=79㎜ 2.求啮合角α' cosα'=acosα/a' α'=21.883°
3.求变位因数之和X1+X2; 由无侧隙啮合方程式可得: X3+X4=(Z3+Z4)(invα'-invα)/2tanα=0.5229 4.在封闭图上做直线 X3+X4=0.5229,此直线上所有点均满足变位因数之和为0.5229,中心距为79㎜的要求。此直线与等滑动磨损曲线η'=η"的交点坐标为 X3=0.315,X4=0.208满足两齿轮磨损相等要求。 5.计算几何尺寸: 参考变位系数值,选该齿轮传动为正传动。 中心距变动系数:y=(a'-a)/m=0.5
齿顶高变动系数:σ=X3+X4-y=0.0229 齿顶高:ha3=(ha*+X3-σ)m=2.584㎜ ha4=(ha*+X4-σ)m=2.37㎜ 齿根高:hf3=(ha*+c*-X3)m=1.87㎜ hf4=(ha*+c*-X4)m=2.084㎜ 全齿高:h3=ha3+hf3=4.454㎜ h4=ha4+hf4=4.454㎜ 分度圆直径:d3=mz3=48㎜ d4=mz4=110㎜ 齿顶圆直径:da3=d3+2ha3=53.168㎜ da4=d4+2ha4=114.74㎜ 齿根圆直径:df3=d3-2hf3=44.26㎜ df4=d4-2hf4=105.832㎜ 基圆直径:db3=d3cosα=45.105㎜ db4=d4cosα=103.366㎜ 齿顶圆压力角:αa3=arccos(db3/da3)=31.968。 αa4=arccos(db4/da4)=25.727。 重合度:εa=[z3(tanαa3-tanα')+z4(tanαa4-tanα')]/2π=1.5516 分度圆齿厚:s3=πm/2+2X3mtanα=3.600㎜ s4=πm/2+2X4mtanα=3.444㎜ 齿顶厚:sa3=s3ra3/r3-2ra3(invαa3-invα)=1.264㎜ sa4=s4ra4/r4-2ra4(invαa4-invα)=1.536㎜ (三)齿轮Z5和齿轮Z6 1.求标准中心距a: a=m(Z5+Z6)/2=78㎜ 2.求啮合角α' cosα'=acosα/a' α'=23.623°
3.求变位因数之和X1+X2; 由无侧隙啮合方程式可得: X5+X6=(Z5+Z6)(invα'-invα)/2tanα=1.0892 4.在封闭图上做直线 X5+X6=1.0892,此直线上所有点均满足变位因数之和为1.0892,中心距为78㎜的要求。此直线与等滑动磨损曲线η'=η"的交点坐标为 X5=0.535,X6=0.554满足两齿根磨损相等要求。