塑性成形过程中相场法及其应用
塑性成形重要知识点总结
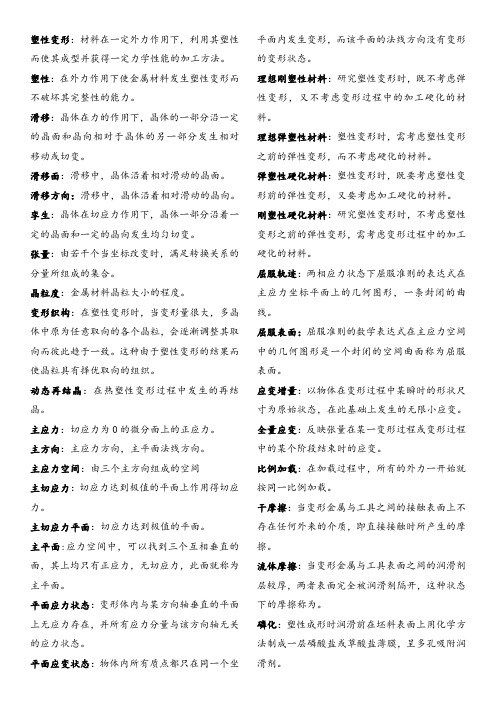
塑性变形:材料在一定外力作用下,利用其塑性而使其成型并获得一定力学性能的加工方法。
塑性:在外力作用下使金属材料发生塑性变形而不破坏其完整性的能力。
滑移:晶体在力的作用下,晶体的一部分沿一定的晶面和晶向相对于晶体的另一部分发生相对移动或切变。
滑移面:滑移中,晶体沿着相对滑动的晶面。
滑移方向:滑移中,晶体沿着相对滑动的晶向。
孪生:晶体在切应力作用下,晶体一部分沿着一定的晶面和一定的晶向发生均匀切变。
张量:由若干个当坐标改变时,满足转换关系的分量所组成的集合。
晶粒度:金属材料晶粒大小的程度。
变形织构:在塑性变形时,当变形量很大,多晶体中原为任意取向的各个晶粒,会逐渐调整其取向而彼此趋于一致。
这种由于塑性变形的结果而使晶粒具有择优取向的组织。
动态再结晶:在热塑性变形过程中发生的再结晶。
主应力:切应力为0的微分面上的正应力。
主方向:主应力方向,主平面法线方向。
主应力空间:由三个主方向组成的空间主切应力:切应力达到极值的平面上作用得切应力。
主切应力平面:切应力达到极值的平面。
主平面:应力空间中,可以找到三个互相垂直的面,其上均只有正应力,无切应力,此面就称为主平面。
平面应力状态:变形体内与某方向轴垂直的平面上无应力存在,并所有应力分量与该方向轴无关的应力状态。
平面应变状态:物体内所有质点都只在同一个坐平面内发生变形,而该平面的法线方向没有变形的变形状态。
理想刚塑性材料:研究塑性变形时,既不考虑弹性变形,又不考虑变形过程中的加工硬化的材料。
理想弹塑性材料:塑性变形时,需考虑塑性变形之前的弹性变形,而不考虑硬化的材料。
弹塑性硬化材料:塑性变形时,既要考虑塑性变形前的弹性变形,又要考虑加工硬化的材料。
刚塑性硬化材料:研究塑性变形时,不考虑塑性变形之前的弹性变形,需考虑变形过程中的加工硬化的材料。
屈服轨迹:两相应力状态下屈服准则的表达式在主应力坐标平面上的几何图形,一条封闭的曲线。
屈服表面:屈服准则的数学表达式在主应力空间中的几何图形是一个封闭的空间曲面称为屈服表面。
塑性成形原理知识点总结
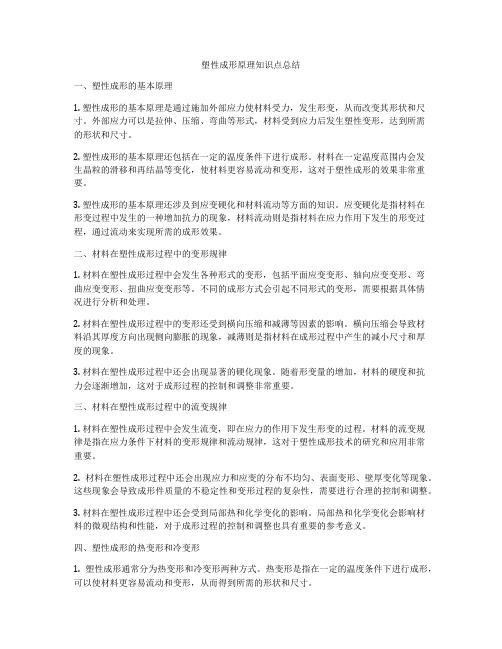
塑性成形原理知识点总结一、塑性成形的基本原理1. 塑性成形的基本原理是通过施加外部应力使材料受力,发生形变,从而改变其形状和尺寸。
外部应力可以是拉伸、压缩、弯曲等形式,材料受到应力后发生塑性变形,达到所需的形状和尺寸。
2. 塑性成形的基本原理还包括在一定的温度条件下进行成形。
材料在一定温度范围内会发生晶粒的滑移和再结晶等变化,使材料更容易流动和变形,这对于塑性成形的效果非常重要。
3. 塑性成形的基本原理还涉及到应变硬化和材料流动等方面的知识。
应变硬化是指材料在形变过程中发生的一种增加抗力的现象,材料流动则是指材料在应力作用下发生的形变过程,通过流动来实现所需的成形效果。
二、材料在塑性成形过程中的变形规律1. 材料在塑性成形过程中会发生各种形式的变形,包括平面应变变形、轴向应变变形、弯曲应变变形、扭曲应变变形等。
不同的成形方式会引起不同形式的变形,需要根据具体情况进行分析和处理。
2. 材料在塑性成形过程中的变形还受到横向压缩和减薄等因素的影响。
横向压缩会导致材料沿其厚度方向出现侧向膨胀的现象,减薄则是指材料在成形过程中产生的减小尺寸和厚度的现象。
3. 材料在塑性成形过程中还会出现显著的硬化现象。
随着形变量的增加,材料的硬度和抗力会逐渐增加,这对于成形过程的控制和调整非常重要。
三、材料在塑性成形过程中的流变规律1. 材料在塑性成形过程中会发生流变,即在应力的作用下发生形变的过程。
材料的流变规律是指在应力条件下材料的变形规律和流动规律,这对于塑性成形技术的研究和应用非常重要。
2. 材料在塑性成形过程中还会出现应力和应变的分布不均匀、表面变形、壁厚变化等现象。
这些现象会导致成形件质量的不稳定性和变形过程的复杂性,需要进行合理的控制和调整。
3. 材料在塑性成形过程中还会受到局部热和化学变化的影响。
局部热和化学变化会影响材料的微观结构和性能,对于成形过程的控制和调整也具有重要的参考意义。
四、塑性成形的热变形和冷变形1. 塑性成形通常分为热变形和冷变形两种方式。
材料的塑性成形工艺

材料的塑性成形工艺引言塑性成形是一种常见的材料加工工艺,通过施加力量使材料发生形变,以获得所需的形状和尺寸。
塑性成形工艺包括冷拔、冷加工、锻造、挤压、拉伸等多种方法。
本文将介绍几种常见的材料塑性成形工艺及其特点。
一、冷拔1.1 工艺流程冷拔是一种拉伸加工的方法,主要用于金属材料。
其工艺流程包括以下几个步骤:1.选材:选择合适的原材料进行冷拔加工。
2.加热:将材料加热至适当的温度,以提高其塑性。
3.均质化处理:通过变形和退火等处理方法,使材料组织更加均匀。
4.拉拔:将材料拉伸至所需的形状和尺寸。
5.精整:通过切割、修整等方法,使成品达到要求的尺寸。
1.2 特点冷拔工艺具有以下特点:•成品尺寸精度高,表面质量好。
•可加工各种材料,包括金属和非金属材料。
•可以提高材料的强度和硬度。
二、冷加工2.1 工艺流程冷加工是一种在常温下进行的成形加工方法,常用于金属材料。
其工艺流程包括以下几个步骤:1.选材:选择合适的原材料进行冷加工。
2.切削:通过刀具对材料进行切削加工。
3.成型:通过冷加工设备对材料进行压制、弯曲、卷曲等成型操作。
4.精整:通过修整、研磨等方法,使成品达到要求的尺寸和表面质量。
2.2 特点冷加工具有以下特点:•成品尺寸精度高,表面质量好。
•可以加工多种材料,包括金属和非金属材料。
•部件形状复杂度高,适用于精密加工要求较高的产品。
三、锻造3.1 工艺流程锻造是一种通过施加压力将材料压制成所需形状的工艺方法。
其工艺流程包括以下几个步骤:1.选材:选择合适的原材料进行锻造。
2.加热:将材料加热至适当的温度,以提高其塑性。
3.锻造:通过锻造设备施加压力,将材料压制成所需形状。
4.精整:通过修整、热处理等方法,使成品达到要求的尺寸和性能。
3.2 特点锻造具有以下特点:•可以加工各种金属材料,包括高温合金和非金属材料。
•成品强度高,韧性好。
•高生产效率,适用于大批量生产。
四、挤压4.1 工艺流程挤压是一种将材料挤压成所需截面形状的塑性成形工艺。
塑性成形的特点与基本生产方式

塑性成形的特点与基本生产方式塑性成形是一种广泛应用于工程领域的加工技术,它通过对热软化塑料材料进行塑性变形,以获得各种复杂的形状和尺寸。
本文将介绍塑性成形的特点以及常见的基本生产方式。
1. 塑性成形的特点塑性成形具有以下几个特点:1.1 灵活性塑性成形可以根据需要灵活地加工出各种复杂形状的产品,例如各种外壳、管道、容器等。
通过改变模具和调整加工参数,可以满足不同产品的加工需求。
1.2 生产效率高相比于其他加工方法,塑性成形具有较高的生产效率。
一次成型可以同时加工多个产品,且生产周期较短。
同时,还可以进行自动化生产,提高生产效率。
1.3 材料利用率高塑性成形能够使材料得到充分利用。
由于材料在加工过程中可以被塑性拉伸、薄化,可以最大限度地减少材料的损耗。
1.4 加工成本低由于塑性成形生产工艺简单,设备投资与维护成本相对较低。
同时,生产过程中材料利用率高,可以降低材料成本。
2. 基本生产方式2.1 挤出成形挤出成形是最常见的塑性成形方式之一。
它通过将塑料材料加热熔融后,通过挤压机将熔融塑料挤出成型。
挤出成形常用于生产管道、板材、型材等产品。
2.2 注塑成形注塑成形是另一种常见的塑性成形方式。
它通过将塑料材料加热熔融后,将熔融塑料注入到闭合的模具中,并施加一定的压力进行冷却固化。
注塑成形适用于生产各种复杂形状的产品,如塑料零件、玩具等。
2.3 吹塑成形吹塑成形是一种特殊的塑性成形方式,常用于生产空心容器,例如瓶子、桶等。
它通过将熔融塑料放置在模具中,通过压缩空气将塑料吹膨为模具形状。
2.4 压延成形压延成形是将塑料热融化后,通过双辊或多辊挤压机将塑料挤压成特定形状和厚度的薄膜或板材。
压延成形适用于生产各种包装薄膜、塑料薄板等产品。
2.5 热压成形热压成形是将加热熔融的塑料放置于模具中,施加一定的压力进行冷却固化。
常用于生产较厚的塑料零件和产品。
总结塑性成形作为一种常见的加工技术,具有灵活性、高生产效率、材料利用率高和加工成本低的特点。
塑性成形技术讲解

塑性成形技术讲解第⼆章塑性成形技术※塑性成形技术:利⽤外⼒使⾦属材料产⽣塑性变形,使其改变形状、尺⼨和改善性能,从⽽获得各种产品的加⼯⽅法。
※主要应⽤:1)⽣产各种⾦属型材、板材和线材;2)⽣产承受较⼤负荷的零件,如曲轴、连杆等;※塑性成形特点:1)产品⼒学性能优于铸件和切削加⼯件;2)材料利⽤率⾼,⽣产率⾼;3)产品形状不能太复杂;4)易实现机械化、⾃动化※分类:1)轧制2)挤压3)拉拔4)锻压:a锻造(⾃由锻,模锻)。
b 冲压第⼀节⾦属塑性成形的物理基础⼀、塑性变形的实质●宏观:外⼒,弹性变形,塑性变形(分切应⼒作⽤)●微观(晶体内部):位错滑移和孪晶●多晶体:晶粒变形、晶界滑移、晶粒转动⼆、塑性变形的分类●冷塑性变形:低于再结晶温度以下时发⽣的变形钨的再结晶温度在1200度。
●热塑性变形:⾼于再结晶温度以上时发⽣的变形铅、锡等⾦属再结晶温度在零度以下。
三、冷塑性变形对⾦属组织和性能的影响产⽣加⼯硬化:随着变形程度的提⾼,⾦属的强度和硬度提⾼,塑性和韧性下降的现象。
原因:位错密度提⾼,亚结构细化2. 产⽣内应⼒:变形开裂,抗腐蚀性能降低,采⽤去应⼒退⽕进⾏消除。
3. 晶粒拉长或破碎,可能产⽣各向异性的塑性变形→晶格畸变→加⼯硬化→内能上升(不稳定)→加热→原⼦活⼒上升→晶格重组→内能下降(温度低时,回复。
温度⾼时,再结晶)四、热塑性变形对⾦属组织和性能的影响⼀)、五种形态:静态回复;静态再结晶;动态回复;动态再结晶;亚动态再结晶1、静态回复、静态再结晶:变形之后,利⽤热变形后的余热进⾏,不需要重新加热。
2、动态回复、动态再结晶:热变形过程中发⽣的。
3、亚动态再结晶:动态再结晶进⾏的热变形过程中,终⽌热变形后,前⾯发⽣的动态再结晶未完成⽽遗留下来的,将继续进⾏⽆孕育期的再结晶。
⼆)、热变形对⾦属组织和性能的影响1. 使铸锭或⽑坯中的⽓孔和疏松焊合,晶粒细化,改善夹杂物和第⼆相等形态和分布,偏析部分消除,使材料成分均匀。
塑性成形技术
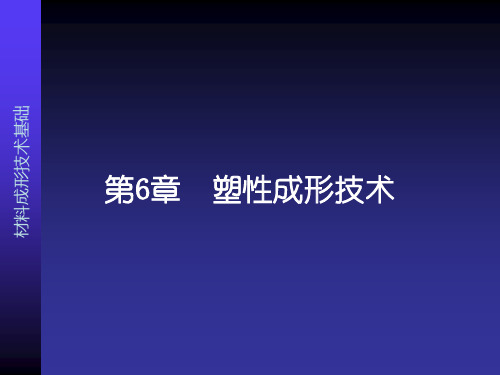
(4)拉深力-行程曲线
由图6-14可见,变形初到中期, 硬化使拉深力增大的速度超过法兰面 积减小使拉深力降低的速度,拉深力 增加。二者对于拉深力增、减速度影 响处于均衡的瞬时,力达到最大值。 此后,面积减小使拉深力降低的速度 超过加工硬化使拉深力增大的速度,
拉深力下降。
图6-14 拉深力-行程曲线
(2)主要变形区
如图所示,冲裁加工时,板料的 主要变形区是以凸模与凹模刃口连 线为中心的纺锤形区域。变形区的 大小与材料特性、模具间隙和约束 条件等因素有关。
a ) v场
b) u场
图6-3 变形区云纹图
(3)变形区应力状态
图6-4显示了无压料冲变形区的应 力状态,由于刃口侧面的轴向应力 为拉应力,故裂纹往往先从侧面产 生,形成毛刺。
图6-16 胀形变形过程
(2)主要变形区
如图6-16所示,在胀形变形过程 中,毛坯被带有凸筋的压边圈压紧, 变形区被限制在凸筋以内的局部区域 内。与拉深不同,胀形时,变形区是 在不断扩大的。
(3)变形区应力、应Байду номын сангаас状态
如图6-17所示,在变形区内,坯料 在双向拉应力作用下,沿切向和径 向产生伸长变形,厚度变薄,表面 积增大。生产中的起伏成形、压凸 包、压筋、圆柱形空心毛坯的鼓肚 成形、波纹管及平板毛坯的张拉成
弯曲加工中,相对弯曲半径r/t反 映弯曲变形程度,当r/t≤(r/t)min时, 弯曲件会开裂;r/t大时,回弹严重, 制件形状与尺寸难控制。生产中, r/t是弯曲工艺计算和模具设计最主 要工艺参数。(r/t)min表示弯曲加工
极限。
6.1.3 拉深 1)拉深变形特点 (1)拉深变形过程
如图6-12所示,凸模与毛坯接触时, 毛坯首先弯曲,与凸模圆角接触处的 材料发生胀形。凸模继续下降,法兰 部分坯料在切向压应力、径向拉应力 作用下通过凹模圆角向直壁流动,进 行拉深变形。拉深是弯曲、胀形、拉 深的变形过程。
超塑性成形的原理及应用
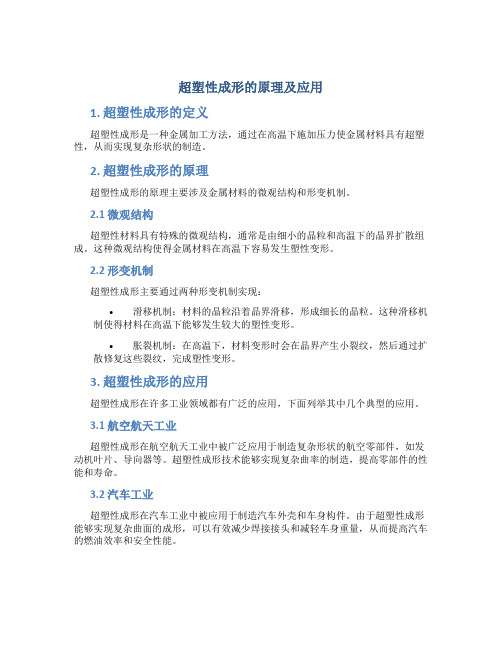
超塑性成形的原理及应用1. 超塑性成形的定义超塑性成形是一种金属加工方法,通过在高温下施加压力使金属材料具有超塑性,从而实现复杂形状的制造。
2. 超塑性成形的原理超塑性成形的原理主要涉及金属材料的微观结构和形变机制。
2.1 微观结构超塑性材料具有特殊的微观结构,通常是由细小的晶粒和高温下的晶界扩散组成。
这种微观结构使得金属材料在高温下容易发生塑性变形。
2.2 形变机制超塑性成形主要通过两种形变机制实现:•滑移机制:材料的晶粒沿着晶界滑移,形成细长的晶粒。
这种滑移机制使得材料在高温下能够发生较大的塑性变形。
•胀裂机制:在高温下,材料变形时会在晶界产生小裂纹,然后通过扩散修复这些裂纹,完成塑性变形。
3. 超塑性成形的应用超塑性成形在许多工业领域都有广泛的应用,下面列举其中几个典型的应用。
3.1 航空航天工业超塑性成形在航空航天工业中被广泛应用于制造复杂形状的航空零部件,如发动机叶片、导向器等。
超塑性成形技术能够实现复杂曲率的制造,提高零部件的性能和寿命。
3.2 汽车工业超塑性成形在汽车工业中被应用于制造汽车外壳和车身构件。
由于超塑性成形能够实现复杂曲面的成形,可以有效减少焊接接头和减轻车身重量,从而提高汽车的燃油效率和安全性能。
3.3 石油化工工业超塑性成形在石油化工工业中常用于制造反应器、换热器和塔器等设备。
超塑性成形技术能够制造出更大尺寸的设备,降低焊接接头的数量和风险,提高设备的可靠性和安全性。
3.4 电子工业超塑性成形在电子工业中被应用于制造微型零部件,如手机外壳、导电网格等。
超塑性成形技术能够制造出更细小、复杂的零部件,满足电子产品越来越小型化、轻量化和高性能化的需求。
4. 超塑性成形的优点和挑战超塑性成形具有以下优点: - 可以制造出复杂形状的零部件,减少后续加工工序; - 可以提高材料的力学性能和耐腐蚀性能; - 可以减少材料的残余应力。
然而,超塑性成形也面临一些挑战: - 高温下的材料处理复杂,需要精确控制温度和应力; - 高温下的工艺条件对设备要求较高; - 需要选择合适的超塑性材料。
塑性成形原理的应用

塑性成形原理的应用1. 引言塑性成形是一种广泛应用于工程领域的加工方法,通过对金属等材料进行压力或应变的加工,使其发生塑性变形,从而得到所需形状和尺寸的零件。
本文将介绍塑性成形原理的应用领域和相关的工艺技术。
2. 塑性成形原理及分类塑性成形是利用材料的塑性变形性质,通过施加外力,使材料产生塑性变形,最终得到所需形状的加工方法。
常见的塑性成形方法包括锻造、拉伸、压力成形、挤压等。
2.1 锻造锻造是利用金属材料的塑性变形特性,通过施加巨大的压力将材料塑性变形成所需形状的一种成形方法。
锻造被广泛应用于制造汽车零部件、航空航天部件等领域。
2.2 拉伸拉伸是利用外力使金属材料发生塑性变形,逐渐延长材料的长度,从而得到所需形状的一种加工方法。
拉伸被广泛应用于制造金属管材、绳索等产品。
2.3 压力成形压力成形是利用外力使金属材料在模具中受到均匀的压力,从而塑性变形成所需形状的一种成形方法。
压力成形常用于制造汽车车身、家电外壳等产品。
2.4 挤压挤压是将金属材料放置在挤压机中,在受到挤压头的作用下,使材料逐渐通过模具产生塑性变形,最终得到所需形状的一种成形方法。
挤压被广泛应用于制造铝合金型材、塑料管材等产品。
3. 塑性成形的应用领域塑性成形在各个工程领域都有广泛的应用,以下列举了几个典型的应用领域。
3.1 汽车制造汽车制造是塑性成形的重要应用领域之一。
例如,汽车车身的制造过程中,采用压力成形和挤压工艺,将金属材料塑性变形成所需的车身零部件。
3.2 航空航天航空航天行业对材料的性能要求极高,因此塑性成形在航空航天领域的应用十分广泛。
例如,飞机的机身、结构件等都需要通过压力成形和锻造等工艺进行加工。
3.3 家电制造在家电制造领域,塑性成形被广泛应用于制造家电外壳。
例如,冰箱、洗衣机等家电产品的外壳都是通过压力成形或拉伸等工艺进行制造的。
3.4 金属制品金属制品制造领域是塑性成形的重要应用领域之一。
例如,金属管材的制造过程中,常采用挤压工艺,将金属材料产生塑性变形成所需形状的管材。
- 1、下载文档前请自行甄别文档内容的完整性,平台不提供额外的编辑、内容补充、找答案等附加服务。
- 2、"仅部分预览"的文档,不可在线预览部分如存在完整性等问题,可反馈申请退款(可完整预览的文档不适用该条件!)。
- 3、如文档侵犯您的权益,请联系客服反馈,我们会尽快为您处理(人工客服工作时间:9:00-18:30)。
塑性成形过程中相场法及其应用学生姓名:学号:学生所在院(系):第1章相场法的特点1.1 相场法的概念相场法是一种基于经典热力学和动力学理论的半唯象方法[1]。
该方法具有以下优点: 可以通过场变量简单明了地表征出任何一种复杂组织的几何形貌,包括单个区域或晶粒的几何形状,区域或晶粒的空间分布、体积分数等;可以考虑内部场和外加场(如应变场、电场和磁场) 对组织变化的影响;并且在2维和3维系统的应用并不增加模型的复杂性[2]。
相场法已经十分成熟地应用于模拟凝固过程[1,3,4],但是在固相-固相转变模拟的应用正处在活跃发展的阶段[5]。
1.2 相场法的特点微观组织演化的经典动力学通过将有着固定结构和成分的晶粒严格区分的尖锐界面的几何形状来描述多相微观组织。
然后微观组织的演化可以通过求解一系列非线性偏微分方程获得,其中移动界面满足自相容边界条件[6]。
然而,对于复杂的微观组织,利用传统方法无法求出移动或自由界面的解析解,即使是其数值解也很难求出[7]。
因此有关粒子形状、粒子数量的问题无法利用传统方法解决。
为了解决大部分传统方法面临的困难,最近人们越来越有兴趣利用场动力学理论描述任意介观和微观组织以及其随时间的演化,其主要原因就是与其它模拟方法相比相场法具有一些其它模拟方法所不具备的独特之处:首先,相场法通过场变量可以简单明了地表征出任何一种复杂组织的几何形貌,而且包括单个区域或晶粒的几何形状,区域或晶粒的空间分布、体积分数、局部表面曲率(如表面的坡口角和二面角)和内界面这样的细节在内[8]。
其次,相场法可以对与长程和短程相互作用有关的各种热力学驱动力加以考虑,所以利用相场法可以研究内部场和外加场(如应变场、电场和磁场)对组织变化的影响。
第三,相场法可以在相同的物理和数学模型下模拟诸如:形核、长大、粗化和外场诱发的组织变化等不同的现象。
第四,相场法中的时间,尺寸和温度的标度可以根据卡恩一希利阿德扩散方程和金兹博格一朗道方程中采用的半唯象常数来确定。
从原理上来说,这些标度可以和所研究系统的实验测量数据或者更基本的模拟数据相对应。
第五,相场法是一种相对简单的方法而且它在二维和三维系统的应用并不增加模型的复杂性。
第2章相场法的理论基础2.1 相场法模拟的理论基础相场法的理论基础是经典的热力学和动力学理论。
例如:总体自由能的减少是组织变化的驱动力,原子和界面的迁移速率决定组织变化的速率。
在组织变化的过程中,总自由能的减少通常包括以下的一个或几个部分:体化学自由能的降低;表面能和界面能的减少;弹性应变能的松弛以及与外作用场相关的能量的降低(如:外加应变场、电场和磁场)。
在这些因素的驱动下,组织的各个组成部分(如各相和各区域)将通过扩散和界面控制的动力学过程发生变化,达到一种能量较低的新的状态,这种变化通常包括新相或新区域的形核(或连续分解)和新的多相/多区域组织随后的长大和粗化。
与传统的方法相比,相场法也是用偏微分方程来描述组织的变化,但是该方法是通过引入一套与时间和空间有关的场变量把复杂的组织作为一个整体来研究[9]。
最熟悉的场变量的例子就是表征成分分布的浓度场和表征多相材料和多晶材料中结构变化的长程有序化参数场[10]。
这些场变量随时间和空间的变化提供了关于介观尺寸的组织变化的全部信息。
场变量的变化可以通过求解半唯象的动力学方程来获得。
在大多数固态相变中,除了结构的变化外还有成分的变化,因此还需要引入成分场c()作为场变量来描绘组织成分的变化。
根据朗道理论可知以上所定义的场变量随时间的变化与系统的热力学驱动力成正比,可以通过这一原理确定一系列偏微分方程,求解这些偏微分方程可得出场变量随时间的变化,从而可以描述出合金组织随时间的变化。
2.1.1朗道相变理论相场模型的理论基础是朗道(Landau)相变理论[11],该理论是建立在统计理论的平均场近似基础上的理论,具有形式简单、理论性强等特点。
1937年,朗道建立了二级相变的唯象理论,把体系的自由能作为温度和序参量的函数展开为幕级数。
该理论强调了相变时对称性改变的重要性,并采用一个反映体系内部状态的热力学变量即序参量来描述相变时的对称破缺。
序参量反映了系统内部的有序化程度,它在高对称相等于零,而在低对称相则不等于零。
对称破缺意味着出现了有序相,其序参量不为零。
因此,序参量可以为某一物理量的平均值,既可以是标量也可以是矢量,在高温相中为零,在低温相中为一个有限值。
相变则意味着序参量从零向非零的过渡,或其逆过程。
朗道二级相变理论假设自由能(f)为序参量(∅)、温度(T)和压强(P)的函数,并将f按∅的幂级数展开f(P,T,∅)=f0+α∅+A1∅+A2∅+A3∅+式中,系数α,A1,A2,A3為都是P和T的函数。
2.1.2 扩散界面模型在相转变和微结构演变的传统模拟方法中,不同畴之间的界面是尖锐的,多畴结构可以用界面的位置来描述[12]。
每一个畴都可以通过求解一系列微分方程来得到其结构。
因此,尖锐界面需要直接跟踪动态界面的演化过程。
对于具有十分复杂的界面结构的问题,釆用经典尖锐界面模型去跟踪界面演化,给计算带来很大的困难。
真实材料中的相界或晶界实际上并不是严格的零厚度界面,而是具有一定厚度的边界层,这层厚度控制着材料相变动力学(如凝固中的非平衡效应,溶质截流效应等现象。
在扩散界面模型中,微结构是通过一系列相场变量来描述。
引入在空间和时间上都连续变化的相场变量可以把尖锐界面问题转变为弥散界面问题。
在相场模型中,系统的自由能在整个模拟区域内用统一的形式来描述,因此在组织模拟过程中不再需要追踪复杂的相界面。
2.2 相场法模型的基本方程连续场法的基本思想是选择一些场变量,这些场变量的动力学演化速度远远慢于微观系统中大量的微观自由度,使其在当前计算机处理能力范围内[13]。
场变量的选择很重要,其原则是既不忽略必要的物理因素也不引入无关的因素。
一般来讲,场变量应该代表系统的主要动力学特征并且在演化过程中起主要作用。
场变量随时间的演化可以通过解偏微分方程获得,并假设场变量随时间的变化率正比于热力学驱动力(线性动力学理论)。
在相场法中,场变量随时间的变化通过唯象的与时间相关的金兹博格一朗道动力学方程求得:其中,ψp是所选的场变量,其准确选择取决于具体情况并且需要能反映系统的特征。
一般说来,场变量可以是可测量的物理量,例如合金成分,而在有的情况下则很难定义这样的物理量,例如在液-固凝固的系统中,需要定义一定数量的取向场变量来表示凝固后各个取向的晶体结构[14]。
场变量可以是标量、矢量、张量,这取决于具体的系统特征,此外我们所提到的标量场变量在像磁场这样的系统中可以表示有三个空间分量的矢量磁矩;该变量也可能是二阶张量例如表示液晶中确定的序列。
第3章相场法的主要步骤及数值解法3.1计算机模拟的主要步骤如下:(1)为所研究的特定的组织特征选择合适的慢速变量。
(2)根据系统的对称性和基本的热力学行为求出经晶粒粗化近似的自由能表达式且该表达式要以慢速变量为自变量[15]。
(3)根据实验数据或更基本的计算结果确定自由能函数中的唯象参数。
(4)确定合适的初始条件和边界条件并用数值方法对场动力学方程(一系列偏微分方程)求解。
3.2相场法的数值解法针对研究对象的特征,构建好物理模型后,就需要求解模型的基本方程,并将基本方程所涉及的区域在时间和空间上进行离散化处理[]16]。
求解物理模型通常有两种方法:(1)解析法,其主要特点是通过严格的数学推导求出问题的精确解(又称解析解);(2)数值法,它通过一定的算法和程序,利用计算机计算出问题的近似解(又称数值解)。
在相场模型中,材料微结构演化的问题最终转化为求解一系列相场方程。
由于体系总自由能f通常是非线性方程,使得相场方程成为了一系列高度非线性的偏微分方程,而这类偏微分方程通常难以得到解析解[17]。
因此,采用计算机数值计算方法对相场方程进行求解就显得十分必要。
目前,求解偏微分方程的数值计算方法主要包括有限差分法、傅里叶谱方法和有限元方法。
3.2.1 有限差分法有限差分法是一种以差分原理为基础的数值计算方法。
其基本思想是将整个连续的空间离散成小网格,然后用网格节点中的差商代替原微分方程中的微分,用网格节点中的函数求和代替原方程中的积分[18],由此就把原来求解偏微分方程的问题转换为求解相邻网格点上差分方程组的问题。
将整个连续空间离散为许多小网格,原则上讲,网格分割是可以任意的。
但在实际应用中,通常是根据边界形状,釆用最简单、最有规律的方法来分割。
常用的有矩形分割法,三角形分割法和极坐标网格分割法。
3.2.2 傅里叶谱方法傅里叶谱方法是另一种重要的求解偏微分方程的数值计算方法[19]。
该方法在求解偏微分方程方面具有很大潜力,因为有快速傅里叶变换而具有强大的威力。
相场法在处理边界问题时,通常釆用周期性边界条件[20],而快速傅里叶变换在处理周期性边界条件时非常方便。
第4章相场法的应用由于相场法所具备的各种独特优点,目前相场法已经在各种不同的材料研究领域内得到了应用[21-23],主要包括以下几个方面:凝固过程、晶粒长大过程、固态相变和位错演化过程。
4.1 凝固模拟凝固过程微观组织模拟己日趋成为当前材料学科的研究热点,目前主要有确定性模型、随机性模型和相场模型。
凝固过程中枝晶的生长是一种分形生长,其固液界面异常复杂,而采用一般的方法都必须精确跟踪这一复杂界面的运动,因此使得计算非常复杂,难以编程实现。
相比之下相场法无需跟踪界面的特点就显得异常吸引人。
Wheeler[24]等人建立二元合金等温凝固的 WBM 模型,后经Warren修正,模拟得到了 Ni-Cu 等温凝固的枝晶形貌。
Kim[25]等将薄界面处理方法应用于合金的相场模型中,提出了 KKS 模型。
4.2 晶粒长大模拟晶粒长大是纯金属、合金、陶瓷等多晶材料在制备和热加工中最普遍的现象,通过相场法可以拟形核,长大,粗化等转变过程[26]。
对材料的性能有着很重要的影响。
Chen[27]首先提出的以相场模型描述晶粒长大过程的多晶相场模型,该模型的特点是将晶界作弥散化(在含晶界的区域晶体几何结构和物理性质上连续过渡)处理,通过构造具有多个势阱形式的自由能密度函数,模拟了二维理想晶粒长大过程,不必直接跟踪复杂的动态界面演化过程,克服了用Potts[28]等尖锐界面模型模拟晶粒长大时存在的问题。
且易于将物理场与晶界几何形态等复杂因素对晶粒长大过程的影响考虑进来,物理意义更加明确,更适合从热力学角度唯象描述晶粒长大过程方面的模拟计算工作。
第二相颗粒钉扎作用也是材料学中常见的现象之一,弥散分布的第二相粒子已经成为控制晶粒尺寸的常用手段。
Moelans[29]等人提出了加入第二相颗粒的连续相场模型,采用额外的自由能密度函数来描述第二相,模拟研究了二维和三维空间下第二相钉扎晶粒长大的现象[30],指出成分和结构影响作用较小,起决定性作用的是第二相颗粒的尺寸。