精馏塔设计流程
化工原理课程设计——精馏塔设计

南京工程学院课程设计说明书(论文)题目乙醇—水连续精馏塔的设计课程名称化工原理院(系、部、中心)康尼学院专业环境工程班级K环境091学生姓名朱盟翔学号240094410设计地点文理楼A404指导教师李乾军张东平设计起止时间:2011年12月5日至 2011 年12月16日符号说明英文字母A a——塔板开孔区面积,m2;A f——降液管截面积,m2;A0——筛孔面积;A T——塔截面积;c0——流量系数,无因此;C——计算u max时的负荷系数,m/s;C S——气相负荷因子,m/s;d0——筛孔直径,m;D——塔径,m;D L——液体扩散系数,m2/s;D V——气体扩散系数,m2/s;e V——液沫夹带线量,kg(液)/kg(气);E——液流收缩系数,无因次;E T——总板效率,无因次;F——气相动能因子,kg1/2/(s·m1/2);F0——筛孔气相动能因子,kg1/2/(s·m1/2);g——重力加速度,9.81m/s2;h1——进口堰与降液管间的距离,m;h C——与干板压降相当的液柱高度,m液柱;h d——与液体流过降液管相当的液柱高度,m;h f——塔板上鼓泡层液高度,m;h1——与板上液层阻力相当的高度,m液柱;h L——板上清夜层高度,m;h0——降液管底隙高度,m;h OW——堰上液层高度,m;h W——出口堰高度,m;h'W——进口堰高度,m;Hσ——与克服表面张力的压降相当的液柱高度,m液柱;H——板式塔高度,m;溶解系数,kmol/(m3·kPa);H B——塔底空间高度,m;H d——降液管内清夜层高度,m;H D——塔顶空间高度,m;H F——进料板处塔板间距,m;H P——人孔处塔板间距,m;H T——塔板间距,m;K——稳定系数,无因次;l W——堰长,m;L h——液体体积流量,m3/h;L S——液体体积流量,m3/h;n——筛孔数目;P——操作压力,Pa;△P——压力降,Pa;△P P——气体通过每层筛板的压降,Pa;r——鼓泡区半径,m,t——筛板的中心距,m;u——空塔气速,m/s;u0——气体通过筛孔的速度,m/s;u0,min——漏气点速度,m/s;u'0——液体通过降液管底隙的速度,m/s;V h——气体体积流量,m3/h;V s——气体体积流量,m3/h;W c——边缘无效区宽度,m;W d——弓形降液管宽度,m;W s——破沫区宽度,m;x——液相摩尔分数;X——液相摩尔比;y——气相摩尔分数;Y——气相摩尔比;Z——板式塔的有效高度,m。
分离乙醇水精馏塔设计(含经典工艺流程图和塔设备图)

分离⼄醇⽔精馏塔设计(含经典⼯艺流程图和塔设备图)分离⼄醇-⽔的精馏塔设计设计⼈员:所在班级:化学⼯程与⼯艺成绩:指导⽼师:⽇期:12化⼯原理课程设计任务书⼀、设计题⽬:⼄醇---⽔连续精馏塔的设计⼆、设计任务及操作条件(1)进精馏塔的料液含⼄醇35%(质量分数,下同),其余为⽔;(2)产品的⼄醇含量不得低于90%;(3)塔顶易挥发组分回收率为99%;(4)⽣产能⼒为50000吨/年90%的⼄醇产品;(5)每年按330天计,每天24⼩时连续运⾏。
(6)操作条件a)塔顶压强 4kPa (表压)b)进料热状态⾃选c)回流⽐⾃选d)加热蒸汽压⼒低压蒸汽(或⾃选)e)单板压降 kPa。
三、设备形式:筛板塔或浮阀塔四、设计内容:31、设计说明书的内容1)精馏塔的物料衡算;2)塔板数的确定;3)精馏塔的⼯艺条件及有关物性数据的计算;4)精馏塔的塔体⼯艺尺⼨计算;5)塔板主要⼯艺尺⼨的计算;6)塔板的流体⼒学验算;7)塔板负荷性能图;8)精馏塔接管尺⼨计算;9)对设计过程的评述和有关问题的讨论;2、设计图纸要求;1)绘制⽣产⼯艺流程图(A2 号图纸);2)绘制精馏塔设计条件图(A2 号图纸);五、设计基础数据:1.常压下⼄醇---⽔体系的t-x-y 数据;2.⼄醇的密度、粘度、表⾯张⼒等物性参数。
4⼀、设计题⽬:⼄醇---⽔连续精馏塔的设计⼆、设计任务及操作条件:进精馏塔的料液含⼄醇35%(质量分数,下同),其余为⽔;产品的⼄醇含量不得低于90%;塔顶易挥发组分回收率为99%,⽣产能⼒为50000吨/年90%的⼄醇产品;每年按330天计,每天24⼩时连续运⾏。
塔顶压强4kPa (表压)进料热状态⾃选回流⽐⾃选加热蒸汽压⼒低压蒸汽(或⾃选)单板压降≤0.7kPa。
三、设备形式:筛板塔四、设计内容:1)精馏塔的物料衡算:原料⼄醇的组成 xF==0.1740原料⼄醇组成 xD0.7788塔顶易挥发组分回收率90%平均摩尔质量 MF =由于⽣产能⼒50000吨/年,.则 qn,F所以,qn,D562)塔板数的确定:甲醇—⽔属⾮理想体系,但可采⽤逐板计算求理论板数,本设计中理论塔板数的计算采⽤图解法。
精馏塔的设计

第一章生产工艺流程的确定本设计的任务为分离正庚烷和正辛烷混合物的精馏塔设计。
对于此二元混合物的分离,采用常压下的连续精馏操作装置。
本设计采用饱和蒸汽进料,将原料以饱和蒸汽状态送人精馏塔内。
塔顶上升蒸汽采用全凝器冷凝,冷凝液体在泡点下一部分经回流装置回流至塔内,其余的部分经产品冷凝冷却器冷凝冷却后送人储罐。
塔釜采用间接蒸汽加热,塔底产品经冷却后送至储罐。
该物系属于易分离物系,最小回流比较小,操作回流比为最小回流比的2倍。
本设计带控制点的生产工艺流程图见附图-1。
第二章精馏塔2.1 精馏塔的物料衡算通过查阅资料知,一个大气压下,正庚烷的沸点为98.4℃,正辛烷的沸点125.6℃,所以混合液中,正庚烷是易挥发成分。
2.1.1已知条件:混合液的流量:F=12t/h正庚烷的含量:x F=0.42正庚烷的回收率:φ=0.98釜残夜中正庚烷的含量:x w =0.032.1.2物料衡算过程:混合液的平均相对分子质量:M F=0.42*100+0.58*114=108.12Kg/kmol混合液的流量:F=12*1000/108.12=110.99Kmol/h总物料衡算:110.99=D+W110.99*0.42=D* x D +W* x w0.98=D* x D /F*x F计算结果:D=79.77 W=31.22 x D=0.5732.2 塔板数的确定2.2.1塔板理论数N T的求取正庚烷—正辛烷属于理想物系,采用图解法求理论板层数。
(1)由资料查得正庚烷—正辛烷在101.3KPa的气液平衡数据如下:温度(℃):98.4 105 110 115 120 125.6X: 1.0 0.656 0.487 0.311 0.157 0.0y: 1.0 0.810 0.673 0.491 0.280 0.0绘出x-y图,见附图2。
(2)求最小回流比及操作回流比采用作图法求最小回流比。
在附图2中对角线上,自点e(0.42,0.42)作垂线ef即为进料线,该线与平衡线的交点坐标y q = 0.42 x q=0.26最小回流比为R min= (x D- y q )/ (y q - x q)=(0.573-0.42) / ( 0.42-0.26) = 0.96取操作回流比为R=2 R min=2*0.96=1.92(3)求精馏塔的气液负荷线L=RD=1.96*79.77=156.35V=(R+1)D=(1+1.96)*79.77=232.93L=L=156.35V=V-F=232.93-110.99=122.0(4) 求操作线方程精馏段操作线方程为y=L x /V + D x D /V =0.658x+0.196提馏段操作线方程为y=L x /V -W x W /V =1.282x-0.008(5)图解法取理论板层数采用图解法取理论板层数,如附图2所示。
精馏塔课程设计--苯-甲苯板式精馏塔的工艺设计

第一章绪论1.1精馏的特点与分类精馏是分离液体混合物的典型单元操作。
它是通过加热造成气液两相物系,利利用物系中各组分挥发度的不同的特性来实现分离的。
按精馏方式分为简单精馏、平衡精馏、精馏和特殊精馏。
1.1.1蒸馏分离具有以下特点(1)通过蒸馏分离,可以直接获得所需要的产品。
(2)适用范围广,可分离液态、气态或固态混合物。
(3)蒸馏过程适用于各种浓度混合物的分离。
(4)蒸馏操作耗能较大,节能是个值得重视的问题。
1.1.2平衡蒸馏将混合液在压力p1下加热,然后通过减压阀使压力降低至p2后进入分离器。
过热液体混合物在分离器中部分汽化,将平衡的气、液两相分别从分离器的顶部、底部引出,即实现了混合液的初步分离。
1.1.3简单蒸馏原料液在蒸馏釜中通过间接加热使之部分汽化,产生的蒸气进入冷凝器中冷凝,冷凝液作为馏出液产品排入接受器中。
在一批操作中,馏出液可分段收集,以得到不同组成的馏出液。
1.1.4连续精馏操作流程化工生产以连续精馏为主。
操作时,原料液连续地加入精馏塔内,连续地从再沸器取出部分液体作为塔底产品(称为釜残液);部分液体被汽化,产生上升蒸气,依次通过各层塔板。
塔顶蒸气进入冷凝器被全部冷凝,将部分冷凝液用泵(或借重力作用)送回塔顶作为回流液体,其余部分作为塔顶产品(称为馏出液)采出。
1-精馏塔 2-全凝器3-储槽 4-冷却器5-回流液泵 6-再沸器 7-原料液预热器图1连续精馏装置示意图1.2精馏塔的踏板分类1.2.1塔板的结构形式1.泡罩塔板泡罩塔板是工业上应用最早的塔板,它由升气管与泡罩构成。
泡罩安装在升气管的顶部,分圆形和条形两种,以前者使用较广。
泡罩有φ80mm、φ100mm和φ150mm三种尺寸,可根据塔径大小选择。
泡罩下部周边开有很多齿缝,齿缝一般为三角形、矩形或梯形。
泡罩在塔板上为正三角形排列。
它的优点是操作弹性适中塔板不易堵塞。
缺点是生产能力与板效率较低结构复杂、造价高。
图2泡罩塔板(a)操作示意图 (b)塔板平面图 (c)圆形泡罩2.筛孔塔板筛孔塔板简称筛板,其结构特点是在塔板上开有许多均匀小孔,孔径一般为3~8mm。
化工原理精馏塔设计完善版
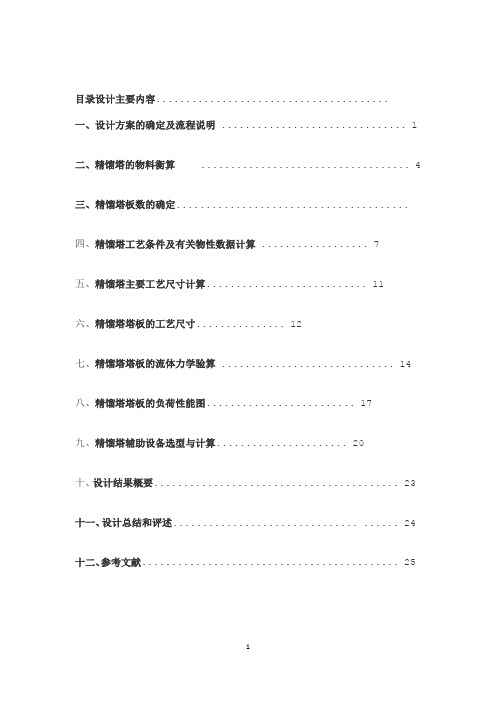
目录设计主要内容.......................................一、设计方案的确定及流程说明 (1)二、精馏塔的物料衡算 (4)三、精馏塔板数的确定.......................................四、精馏塔工艺条件及有关物性数据计算 (7)五、精馏塔主要工艺尺寸计算 (11)六、精馏塔塔板的工艺尺寸 (12)七、精馏塔塔板的流体力学验算 (14)八、精馏塔塔板的负荷性能图 (17)九、精馏塔辅助设备选型与计算 (20)十、设计结果概要 (23)十一、设计总结和评述............................... (24)十二、参考文献 (25)设计主要内容一、设计方案的确定及流程说明1、操作压力蒸馏操作可在常压,加压,减压下进行。
应该根据处理物料的性能和设计总原则来确定操作压力。
例如对于热敏感物料,可采用减压操作。
本次设计为一般物料因此,采用常压操作。
2、进料状况进料状态有五种:过冷液,饱和液,气液混合物,饱和气,过热气。
但在实际操作中一般将物料预热到泡点或近泡点,才送入塔内。
这样塔的操作比较容易控制。
不受季节气温的影响,此外泡点进料精馏段与提馏段的塔径相同,在设计和制造上也叫方便。
本次设计采用泡点进料即q=1。
3、加热方式蒸馏釜的加热方式一般采用间接加热方式,若塔底产物基本上就是水,而且在浓度极稀时溶液的相对挥发度较大。
便可以直接采用直接加热。
直接蒸汽加热的优点是:可以利用压力较低的蒸汽加热,在釜内只需安装鼓泡管,不需安装庞大的传热面,这样,操作费用和设备费用均可节省一些,然而,直接蒸汽加热,由于蒸汽的不断涌入,对塔底溶液起了稀释作用,在塔底易挥发物损失量相同的情况下。
塔釜中易于挥发组分的浓度应较低,因而塔板数稍微有增加。
但对有些物系。
当残液中易挥发组分浓度低时,溶液的相对挥发度大,容易分离故所增加的塔板数并不多,此时采用直接蒸汽加热是合适的。
精馏塔的原理和流程

精馏塔的原理和流程一、引言精馏塔是一种常用于化工领域的分离设备,其具有高效且可控的分离性能。
本文将介绍精馏塔的原理和流程,包括其基本结构、工作原理、操作流程以及应用领域等。
二、精馏塔的基本结构精馏塔由塔身、填料层、留液器、塔盘等组成。
其中,塔身是塔的主要部分,填料层用于增加表面积和接触机会,留液器用于收集液体,塔盘用于改变气体和液体的流动方向。
三、精馏塔的工作原理精馏塔是利用物质在不同温度下蒸发和凝结的特性进行分离的。
其基本工作原理是通过对混合液体进行加热,使其蒸发产生蒸汽,蒸汽与冷凝介质接触后凝结为液体。
在塔内,液体从上方往下滴流,气体从下方往上冒泡,两相之间通过填料层或塔盘的接触进行质量传递和热量传递,从而实现不同物质的分离。
四、精馏塔的操作流程精馏塔的操作流程包括四个主要步骤:进料、加热、分离和收集。
具体操作如下:1. 进料首先将混合液体通过进料口进入精馏塔,进料的速度和方式需要根据具体情况进行调整。
2. 加热通过加热设备对塔内的混合液体进行加热。
加热温度需要根据待分离物质的沸点来确定,以确保液体能够蒸发。
3. 分离在塔内,混合液体被加热后产生蒸汽,蒸汽通过填料层或塔盘与下方的冷凝介质接触,凝结为液体。
在这个过程中,不同物质由于具有不同的挥发性和热稳定性,会在塔内产生不同程度的蒸发和凝结,实现物质的分离。
4. 收集经过分离的液体会被收集到留液器中,通过排液口进行排放。
收集的液体可以进一步处理或进行其他用途的利用。
五、精馏塔的应用领域精馏塔广泛应用于化工、石油、制药、食品等行业中,用于分离和提纯不同物质,以满足不同领域的需求。
1. 化工领域在化工生产中,精馏塔常用于各类化工原料的分离和纯化,例如分离石油产品、分离有机化合物、提纯合成氨等。
2. 石油领域精馏塔在石油炼制过程中起到至关重要的作用,可用于分离石油中的不同成分,如汽油、柴油、煤油、液化气等。
3. 制药领域在制药行业中,精馏塔用于药物的提取和纯化,可分离出目标药物并去除其他杂质物质。
精馏塔工艺流程
精馏塔工艺流程
《精馏塔工艺流程》
精馏塔是一种用于分离混合物的设备,通常用于分离液体混合物中的组分。
精馏塔工艺流程是指进行精馏过程时所采取的步骤和操作方法,下面将简单介绍精馏塔的工艺流程。
首先,混合物被加热至沸点,进入精馏塔内。
一般情况下,精馏塔内设有填料或板式结构,用于增加表面积以便更好地分离混合物。
加热后,混合物的不同组分会根据其沸点的不同在塔内升华,并在塔内上升。
随着混合物向上升华,不同组分开始在塔内逐渐分离。
高沸点的组分会在塔的底部凝结成液体,低沸点的组分则会在塔的顶部凝结成液体。
这样,就实现了混合物的分离。
在整个精馏过程中,操作人员需不断监控塔内的温度和压力。
当塔内产生过多的高沸点组分时,需要调节温度或其他参数以保持分离效果。
而在低沸点组分产生过多时,也需要对塔内操作进行调整。
最后,分离完成后,产生的不同组分液体会经过不同的管道被收集起来,以便后续的处理或利用。
总的来说,精馏塔工艺流程是一个通过控制温度和压力,利用不同组分沸点的特性实现混合物分离的过程。
通过严格的操作
和监控,可以有效地分离出混合物中的不同组分,为各种工业和化工应用提供了重要的技术支持。
精馏塔(浮阀塔)的设计
课程设计(论文)浮阀精馏塔的工艺设计说明书题目名称苯—甲苯溶液精馏装置精馏塔设计课程名称化工原理学生姓名雷素兰学号**********系专业生化系2010级化学工程与工艺指导教师胡建明2012年12月25 日目录一、设计任务书 (3)二、概述 (4)三、设计方案的确定和流程说明 (4)四、物料衡算 (5)1.设计条件 (5)2.全塔物料衡算 (6)五、设备设计与选型 (7)1. 精馏塔工艺设计 (7)2.塔内气液负荷 (11)3.计算塔径、确定板间距 (13)六、塔板结构设计 (14)1.溢流装置 (14)2.塔板布置 (15)七、浮阀塔流体力学验算 (17)1.塔板压降 (17)2.塔板负荷性能 (19)八、精馏塔结构尺寸设计 (23)九、参考文献 (26)十、总结 (27)十一、致谢 (27)十二、附工程图纸 (28)概述塔设备是化学工业,石油化工,生物化工,制药等生产过程中广泛采用的传质设备。
根据塔内气液接触构件的结构形式,可分为板式塔和填料塔两大类。
板式塔为逐级接触式气液传质设备,塔内设置一定数量的塔板,气体以鼓泡形式或喷射形式通过塔板上的液层,正常条件下,气相为分散相,液相为连续相,气相组成呈阶梯变化,它具有结构简单,安装方便,压降低,操作弹性大,持液量小等优点,被广泛的使用。
本设计的目的是分离苯—甲苯的混合液,故选用板式塔。
设计方案的确定和流程说明1.塔板类型:精馏塔的塔板类型共有三种:泡罩塔板,筛孔塔板,浮阀塔板。
浮阀塔板具有结构简单,制造方便,造价低等优点,且开孔率大,生产能力大,阀片可随气流量大小而上下浮动,故操作弹性大,气液接触时间长,因此塔板效率较高。
本设计采用浮阀塔板。
2. 加料方式:加料方式共有两种:高位槽加料和泵直接加料。
采用泵直接加料,具有结构简单,安装方便等优点,而且可以引入自动控制系统来实时调节流量及流速。
故本设计采用泵直接加料。
3. 进料状况:进料方式一般有两种:冷液进料及泡点进料。
《化工原理》乙醇-水混合液精馏塔设计
《化工原理》乙醇-水混合液精馏塔设计一、设计任务:完成精馏塔工艺优化设计、精馏塔结构优化设计以及有关附属设备的设计和选用,绘制精馏塔的工艺条件图及塔板性能负荷图,并编制工艺设计说明书。
二、操作条件:年产量:7500t。
料液初温:30℃料液浓度:43%(含乙醇摩尔分数)塔顶产品浓度:97%(含乙醇摩尔分数)乙醇回收率:99.8%(以摩尔分数计)年工作日:330天(24小时运行)精馏塔塔顶压力:4kPa(表压)冷却水温度:30℃饱和蒸汽压力:2.5kgf/cm2(表压)单板压降:不大于0.7kPa全塔效率:52%回流比是最小回流比的1.8倍进料状况:泡点进料三、设计内容:(1)设计方案简介:对确定的工艺流程及精馏塔型式进行简要论述。
(2)工艺参数的确定基础数据的查取及估算,工艺过程的物料衡算及热量衡算,理论塔板数,塔板效率,实际塔板数等。
(3)主要设备的工艺尺寸计算板间距,塔径,塔高,溢流装置,塔盘布置等。
(4)主要附属设备设计计算及选型塔顶全凝器设计计算:热负荷,载热体用量。
(5)用坐标纸绘制乙醇-水溶液的y-x图一张,并用图解法求理论塔板数(贴在说明书中对应的地方)。
(6)绘制精馏塔设计条件图。
附:汽液平衡数据表1一、总体设计计算1.1 汽液平衡数据(760mm Hg)1.2塔的物料衡算=43/46.07/(43/46.07+57/18.01)=0.2277XF=97/46.07/(97/46.07+31/18.01)=0.9267XDM=0.2277⨯46.07+(1-0.2277)⨯18.02=24.399kg/kmol F同理可得M=44.013 D,=7.5*106/7920=946.97DD=946.97/44.013=21.516η=0.998=DXD /FXF=21.516*0.9267/0.2277FF=87.742 由 F=D+WFXF =DXD+WXW得:Xw=0.03998W=66.226 Kmol/h1.3塔板计算tF=(0.2277-0.1661/0.2337-0.1661)*(82.7-84.1)+84.1=82.82°CtF=82.82℃乙醇不同温度的饱和蒸气压乙醇的饱和蒸气压o={[(82.82-80)/(90-80)]*(158.27-108.32)}+108.32=122.41 PA水不同温度的饱和蒸气压由图数据通过内插法得P B O =53.0525 α =122.41/53.0525=2.31 泡点进料q=1R min =1/α-1[X D /X F -α(1-X D )/1-X F ]=2.94 R=1.8R min =5.292精馏段操作线方程1111n n D R y x x R R +=+++=0.841x+0.1473提馏段操作线方程W m m x WqF L W x W qF L qF L y -+--++=+''1=1.503x-0.000849实际塔板数N pE T =0.52精馏段Np1=11/0.52=21块提馏段Np2=3/0.52=6块总板数21+6=27块二、塔的工艺条件及物性数据计算2.1精馏段的数据1.平均压力Pm单板降压不大于0.7Kpa所以等于0.7Kpa塔顶:PD=4+101.3=105.3Kpa加料板:PF=105.3+0.7*21=120Kpa平均压力:Pm=(105.3+120)/2=112.65Kpa2.平均温度tD={[(0.9267-0.08943)/(1-0.8943)]*(80.02-78.15)}+78.15=78.72℃tF=82.82℃精馏段tm=(82.82+78.72)/2=80.77℃3.平均分子量塔顶:M VDM = XD×M轻组分+(1-XD)×M重组分=46.07*0.9267+(1-0.9267)*18.01=44.01kg/kmolM LDM = x1×M轻组分+(1-x1)×M重组分=46.07*0.743+(1-0.743)*18.01=38.86kg/kmol进料板的平均分子量:进料板对应的组成Xn 和ynM VFM = yn×M轻组分+(1-yn)×M重组分=46.01*0.512+(1-0.512)*18.01=32.38kg/kmolM LFM = Xn×M轻组分+(1-Xn)×M重组分=46.07*0.2277+(1-0.2277)*18.01=24.4kg/kmol 精馏段:MVm=(44.01+32.38)/2=38.2kg/kmolMLm=(38.36+24.4)/2=31.63kg/kmol4.平均密度塔顶:aA =0.97 aB=0.03查物性数据:易挥发组分密度ρ1= 763.42 Kg/m3难挥发组分密度ρ2= 972.58 Kg/ m3塔顶液相密度:ρLD =1/[a1/ρ1+(1-a1) /ρ2]= 741.84Kg/ m3进料板:aA =0.43 aB=0.53查物性数据:易挥发组分密度ρ1= 733.59 Kg/m3难挥发组分密度ρ2= 969.97 Kg/ m3进料液相密度:ρLF =1/[a2/ρ1+(1-a2) /ρ2]= 851.93Kg/ m3精馏段的平均液相密度:ρLM =(ρLD+ρLF)/2=796.88Kg/ m3精馏段平均汽相密度:TM =(TF+TD)/2=80.77℃ρVM =PM V /RT M =1.463Kg/ m 35. 液体的平均表面张力 (1)塔顶t D =78.72℃ бO =17.26 бW =62.8V O =46.07/737=0.06251m 3/kmol V w =18.01/973=0.01851m 3/kmol X o =X D =0.9267 X W =1-0.9267=0.0733 φo =X o V O /(X W V w +X o V O )=0.977 φW =1-0.977=0.023 B=lg(φW q /φo )=-3.266Q=0.041(q/T)(бO V O 2/3/q-бW V w 2/3)=-0.0007 A=B+Q=-3.266-0.0007=-3.2667lg(φs W q /φso )=-3.2667和φs W +φso =1解得 φs W =0.021 φso =0.979бm 1/4=φs W бW 1/4+φso бO 1/4=2.05 бDm =17.81N/m2. 进料板t F =82.82℃ бO =16.88 бW =62.04V O =46.07/733=0.06285m 3/kmol V w =18.01/969.3=0.01858m 3/kmol X o =X F =0.2277 X W =1-0.2277=0.7723 φo =X o V O /(X W V w +X o V O )=0.499φW =1-0.499=0.501 B=lg(φW q /φo )=-0.298Q=0.041(q/T)(бO V O 2/3/q-бW V w 2/3)=-0.00748A=B+Q=-0.298-0.00748=-0.3055lg(φs W q /φso )=-0.3055和φs W +φso =1解得 φs W =0.498 φso =0.502бm 1/4=φs W бW 1/4+φso бO 1/4=2.415 бFm =34.01N/m(3) 精馏段бm =(17.81+34.01)/2=25.91N/m 6. 液体的平均黏度,L D μ=0.44⨯0.9267+(1-0.9267)⨯0.357=0.434.a mP s,L F μ=0.12⨯0.33+(1-0.12)⨯0.30=0.3904.a mP s,L M μ精=0.435*0.3904+0.357*(1-0.3904)=0.387.a mP s 7. 精馏段的汽液负荷计算V=(R+1)D=(5.292+1)⨯21.516=135.38/kmol hS V =,,3600V V m V M ρ精精=135.38*38.2/(3600*1.463)=0.91m 3/sV h =3600*0.91=3262.96m 3/hL=RD=50292⨯21.516=113.86/kmol h,3600L s L m LM L ρ=精精=113.86*31.63/(3600*796.88)=0.001255L h =3600*0.001255=4.52m 3/h2.2 提馏段的数据1.平均温度t W ={[(0.03998-0.019)/(1-0.019)]*(89-95.5)}+95.5=92.93℃ t F =82.82℃提馏段t m =(82.82+92.93)/2=87.88℃2.平均分子量 塔底:M VWM = X W ×M 轻组分+(1-X W )×M 重组分=46.07*0.414+(1-0.414)*18.01=29.63kg/kmol M LWM = x 1×M 轻组分+(1-x 1)×M 重组分=46.07*0.03998+(1-0.03998)*18.01=19.13kg/kmol 提馏段:M Vm =(29.63+32.38)/2=31kg/kmol M Lm =(19.13+24.4)/2=21.77kg/kmol 3.平均密度塔底:a A =0.64 a B =0.36查物性数据: 易挥发组分密度ρ1= 725.87 Kg/m 3 难挥发组分密度ρ2= 963.23 Kg/ m 3塔底液相密度:ρLD =1/[a 1/ρ1+(1-a 1) /ρ2]= 963.15Kg/ m 3 提馏段的平均液相密度:ρLM =(ρLW +ρLF )/2=907.54Kg/ m 3 提馏段平均汽相密度:T M =(T F +T D )/2=87.88℃ ρVM =PM V /RT M =1.16Kg/ m34.液体的平均表面张力 (1)塔底t W =92.93℃ бO =13.27 бW =60.16V O =46.07/737=0.06251m 3/kmol V w =18.01/973=0.01851m 3/kmol X o =X W =0.03998 X W =1-0.03998=0.96 φo =X o V O /(X W V w +X o V O )=0.123φW =1-0.123=0.877B=lg(φW q /φo )=0.796Q=0.041(q/T)(бO V O 2/3/q-бW V w 2/3)=-0.000163 A=B+Q=0.796-0.000163=0.794lg(φs W q /φso )=0.794和φs W +φso =1解得 φs W =0.634 φso =0.366бm 1/4=φs W бW 1/4+φso бO 1/4=2.46 бWm =36.62N/m提馏段бm =(36.62+34.01)/2=35.32N/m 5.液体的平均黏度μlw =0.03998⨯0.324+(1-0.03998)⨯0.324=0.393.a mP s ,L F μ=0.12⨯0.33+(1-0.12)⨯0.30=0.3904.a mP s μL,M 提=0.393*0.084+0.393*(1-0.084)=0.33.a mP s 6.精馏段的汽液负荷计算V=(R+1)D=(5.292+1)⨯21.516=135.38/kmol hS V ==135.38*31/(3600*1.16)=1m 3/sV h =3600*1=3600m 3/hL=RD=50292⨯21.516=113.86/kmol hL s =113.86*21.77/(3600*907.54)=0.00154L h =3600*0.00154=5.508m 3/h三、塔和塔板主要工艺尺寸计算 3.1 塔径首先考虑精馏段:参考有关资料,初选板音距T H =0.5m 取板上液层高度L h =0.06m 故 T H -L h=0.5-0.06=0.44ms s L V ⎛ ⎝查图可得 20C =0.097校核至物系表面张力为9.0mN/m 时的C ,即C=20C 0.220σ⎛⎫⎪⎝⎭=0.0102max u =CL VVρρρ-可取安全系数0.7,则 u=0.7max u =0.7⨯2.378=1.665m/s故4sV uπ按标准,塔径圆整为1.2m ,则空塔气速为0.805m/s3.2 精馏塔有效高度的计算精馏段有效高度为1Z N =-T 精精()H =(21-1)⨯0.5=10m提馏段有效高度为1Z N =-T 提提()H =(6-1)⨯0.5=2.5mZ 总=10+2.5=12.5m3.3 溢流装置采用单溢流、弓形降液管⑴ 堰长 w l 取堰长 w l =0.6Dw l =0.6⨯1.2=0.72m⑵ 出口堰高w h =L ow h h -选用平直堰,堰上液层高度ow h 由下式计算ow h =2/32.841000h w L E L ⎛⎫ ⎪⎝⎭近似取E=1.03,则ow h =0.00995故 w h =0.06-0.00995=0.05m ⑶ 降液管的宽度d W 与降液管的面积f A 由L D /D T =0.6《化工设计手册》 得dW D =0.1,f TA A =0.053 故 d W =0.12 f A =0.0722()24D π=0.062m留时间 f T sA H L τ==23.9s (>5s 符合要求)提馏段t=A d H T /Ls=33.11=>5s⑷ 降液管底隙高度 h ο u o ,=0.08h ο=L s /w l u o ,=0.022m3.4 塔板布置(1)取边缘区宽度c W =0.06,安定区宽度s W =0.075(2)计算开孔面积212sin 180a x A R R π-⎡⎤=⎢⎥⎣⎦=0.7992m 其中 x=2D-(d s W W +)=0.405m R=2D-c W =0.54m 3.5 筛板数n取筛孔的孔径0d 为39mm,正三角形排列,一般碳钢的板厚δ为3mm,孔中心距t=75.0mm 浮阀数目 取阀动能因数11F =,则由式o υ=o υ=计算塔板上的筛孔数n,即 n=4V s /πd o 2u o =83.75=84提馏段的筛口气速和筛孔数用上述公式计算, 提馏段 u 0=10.21m/s, n=82个取边缘区宽度c W =0.06,安定区宽度s W =0.075,板厚δ为3mm, 做等腰三角形叉排h=Aa/0.075n=0.127m=120mm 阀孔气速μo =4V s /πnd o 2=9.12m/s F 0=10.97四、筛板的流体力学性能 1. 塔板压降校核 h f =h c +h e(1)气体通过干板的降压h c临界孔速 u 0c =(73/ρv )1/1.825=8.52m/s<u 0 所以h c =5.34(ρv /ρL )(u 02/2g)=0.0411m (2)气体通过班上液层的压降h e h e =β(h w +h ow )=0.05*0.06=0.03 (3)h б克服表面张力的压降 h б=0.00034m(4)气体通过筛板压降h f 和∆p f h f =h c +h e +h б=0.07144m∆p f =ρl *g*h f =558.5kpa<0.7kpa 2. 雾沫夹带量校核泛点率1100%F bF =板上液体流经长度 Z L =D T -2W D =0.96m F=40.72%<80%不会发生过量的雾沫夹带 3. 漏液校核=4.134m/s k=u 0/u'0=2.19=>2提馏段用同样的方法得,k=u 0/u'0==>2 4. 降低管液泛校核为防止降液管液泛的发生,应使降液管中清液层高度()d T w H H h ≤Φ+d P L d H h h h =++ 即h d =0.153(L s /L w h o )2=0.00096m取 取校正系数Φ=0.5,H d =0.1324,Φ(H T +h w )=0.275m可见(),d T W H H h φ≤+符合防止淹塔的要求。
精馏塔设计流程
在一常压操作的连续精馏塔内分离水—乙醇混合物。
已知原料的处理量为2000吨、组成为36%(乙醇的质量分率,下同),要求塔顶馏出液的组成为82%,塔底釜液的组成为6%。
设计条件如下:操作压力5kPa(塔顶表压);进料热状况自选;回流比自选;单板压降≤;根据上述工艺条件作出筛板塔的设计计算。
【设计计算】(一)设计方案的确定本设计任务为分离水—乙醇混合物。
对于二元混合物的分离,应采用连续精馏流程。
设计中采用泡点进料,将原料液通过预料器加热至泡点后送入精馏塔内。
塔顶上升蒸气采用全凝器冷凝,冷凝液在泡点下一部分回流至塔内其余部分经产品冷却器冷却后送至储罐。
该物系属易分离物系,最小回流比较小,故操作回流比取最小回流比的倍。
塔釜采用间接蒸汽加热,塔底产品经冷却后送至储罐。
(二)精馏塔的物料衡算1. 原料液及塔顶、塔底产品的摩尔分率M=46.07kg/kmol乙醇的摩尔质量AM=18.02kg/kmol水的摩尔质量BF x =18.002.1864.007.4636.007.4636.0=+= D x =64.002.1818.007.4682.007.4682.0=+= W x =024.002.1894.007.4606.007.4606.0=+=2.原料液及塔顶、塔底产品的平均摩尔质量F M =×+×=23.07kg/kmolD M =×+×=35.97kg/kmolW M =×+×=18.69kg/kmol3.物料衡算以每年工作250天,每天工作12小时计算原料处理量 F =90.281225007.2310002000=⨯⨯⨯kmol/h 总物料衡算 =W D +水物料衡算 ×=+W联立解得 D =hW =h (三)塔板数的确定1. 理论板层数T N 的求取水—乙醇属理想物系,可采用图解法求理论板层数。
①由手册查得水—乙醇物系的气液平衡数据,绘出x —y 图,如图。
- 1、下载文档前请自行甄别文档内容的完整性,平台不提供额外的编辑、内容补充、找答案等附加服务。
- 2、"仅部分预览"的文档,不可在线预览部分如存在完整性等问题,可反馈申请退款(可完整预览的文档不适用该条件!)。
- 3、如文档侵犯您的权益,请联系客服反馈,我们会尽快为您处理(人工客服工作时间:9:00-18:30)。
在一常压操作的连续精馏塔内分离水—乙醇混合物。
已知原料的处理量为2000吨、组成为36%(乙醇的质量分率,下同),要求塔顶馏出液的组成为82%,塔底釜液的组成为6%。
设计条件如下:操作压力 5kPa(塔顶表压);进料热状况 自选 ;回流比 自选;单板压降 ≤;根据上述工艺条件作出筛板塔的设计计算。
【设计计算】(一)设计方案的确定本设计任务为分离水—乙醇混合物。
对于二元混合物的分离,应采用连续精馏流程。
设计中采用泡点进料,将原料液通过预料器加热至泡点后送入精馏塔内。
塔顶上升蒸气采用全凝器冷凝,冷凝液在泡点下一部分回流至塔内其余部分经产品冷却器冷却后送至储罐。
该物系属易分离物系,最小回流比较小,故操作回流比取最小回流比的倍。
塔釜采用间接蒸汽加热,塔底产品经冷却后送至储罐。
(二)精馏塔的物料衡算1. 原料液及塔顶、塔底产品的摩尔分率乙醇的摩尔质量 A M =46.07kg/kmol水的摩尔质量 B M =18.02kg/kmolF x =18.002.1864.007.4636.007.4636.0=+= D x =64.002.1818.007.4682.007.4682.0=+= W x =024.002.1894.007.4606.007.4606.0=+=2.原料液及塔顶、塔底产品的平均摩尔质量F M =×+×=23.07kg/kmolD M =×+×=35.97kg/kmolW M =×+×=18.69kg/kmol3.物料衡算以每年工作250天,每天工作12小时计算原料处理量 F =90.281225007.2310002000=⨯⨯⨯kmol/h 总物料衡算 =W D +水物料衡算 ×=+W联立解得 D =hW =h(三)塔板数的确定1. 理论板层数T N 的求取水—乙醇属理想物系,可采用图解法求理论板层数。
①由手册查得水—乙醇物系的气液平衡数据,绘出x —y 图,如图。
②求最小回流比及操作回流比。
采用作图法求最小回流比。
在图中对角线上,自点e , 作垂线ef 即为进料线(q 线),该线与平衡线的交点坐标为q y = q x =故最小回流比为min R =q q qD x y y x --=35.018.0-52.052.0-64.0=3 取操作回流比为R =min R =×=③求精馏塔的气、液相负荷L =RD =17.532.753.0=⨯=kmol/hV =D R )1(+=(+1)20.1132.7=⨯kmol/h'L =F L +=+= kmol/h'V =V =h④求操作线方程精馏段操作线方程为y =x V L +D x V D =418.0462.064.020.1132.720.1117.5+=⨯+=x x 提馏段操作线方程为 W x V W x V L '''''y -===⨯-024.020.1158.21x 20.1107.34''x ⑤图解法求理论板层数 采用图解法求理论板层数,如图1所示。
求解结果为总理论板层数 T N =16(包括再沸器)进料板位置 F N =52. 实际板层数的求取精馏段实际板层数 精N =2055.011= 提馏段实际板层数 提N =1009.955.05≈= (四)精馏塔的工艺条件及有关物性数据的计算以精馏段为例进行计算。
1. 操作压力计算塔顶操作压力 D P =+5=每层塔板压降 ΔP =进料板压力 F P =+×20=精馏段平均压力 m P =+/2=2. 操作温度计算依据操作压力,由泡点方程通过试差法计算出泡点温度,其中水、乙醇的饱和蒸气压由安托尼方程计算,计算过程略。
计算结果如下:塔顶温度 D t =79.3°C进料板温度 F t =95.4°C精馏段平均温度 m t =4.872)4.953.79(=+°C3. 平均摩尔质量计算塔顶平均摩尔质量计算由D x =1y =,查平衡曲线(见图1),得1x =m VD M =×+×=35.97kg/kmolm LD M =×+×=38.05kg/kmol进料板平均摩尔质量计算由图解理论板(见图1),得F y =查平衡曲线(见图1),得F x =m VF M =×+×=32.61kg/kmolm LF M =×+(1-2)×=23.63kg/kmol精馏段平均摩尔质量m V M =+/2=34.29kg/kmolm L M =+/2=30.84kg/kmol4. 平均密度计算(1)气相平均密度计算由理想气体状态方程计算,即m m m RT Vm V M P =ρ=30.1)15.2734.87(314.829.343.113=+⨯⨯kg/m 3 (2)液相平均密度计算液相平均密度依下式计算,即i i t a m ρρ//1∑=塔顶液相平均密度的计算由D t =79.3°C ,查手册[3]得 A ρ=741.6kg/m 3 B ρ=971.8kg/m 3=m LD ρ63.774)8.97118.06.74182.01=+kg/m 3 进料板液相平均密度的计算由F t =95.4°C ,查手册得A ρ=731.5kg/m 3B ρ=961.9kg/m 3=m LD ρ5.764)9.18.05.73182.01=+kg/m 3 进料板液相的质量分率39.002.188.007.462.007.462.0=⨯+⨯⨯=A α m LF ρ=7.8569.96161.05.73139.01=+kg/m 3精馏段液相平均密度为6.8102/)7.8565.764(m =+=L ρkg/m3 5.液体平均表面张力计算液体平均表面张力依下式计算,即i i L x σσ∑=m塔顶液相平均表面张力的计算由D t =79.3°C ,查手册得=A σm =B σm2.345.6236.03.1864.0m =⨯+⨯=LD σmN/m进料板液相平均表面张力的计算由F t =95.4.0°C ,查手册得=A σm =B σm00.5278.5982.0.053.1618.0=⨯+⨯=LFm σmN/m精馏段液相平均表面张力为1.432/)0.522.34(m =+=L σmN/m6. 液体平均粘度计算液体平均粘度依下式计算,即lg m L μ=ii x μlg ∑ 塔顶液相平均粘度的计算由D t =79.3.0°C ,查手册得=A μs pa ⋅m =B μs pa ⋅m)355.0lg(36.0)436.0lg(64.0lg m +=LD μ解出405.0m =LD μs pa ⋅m进料板液相平均粘度的计算由F t =95.4°C ,查手册得=A μs pa ⋅m =B μs pa ⋅m)299.0lg(8.0)386.0lg(2.0lg +=LFm μ解出=m LF μs pa ⋅m精馏段液相平均粘度为360.02/)315.0405.0(m =+=L μs pa ⋅m(五)精馏塔的塔体工艺尺寸计算1. 塔径的计算精馏段的气、液相体积流率为=⨯⨯==30.1360029.3420.113600vm vm VM Vs ρ0.082m 3/s=⨯⨯==6.810360084.3017.53600Lm Lm LM Lh ρ0.000055 m 3/s 由 VV L C u ρρρ-=max 式中C 计算中的C 20由《化工原理课程设计》P105图5-1查取,图的横坐标为 =⨯⨯=2121)30.16.810(3600335.0360000032.0)(V L h h V L ρρ 取板间距30.0=T H m ,板上液层高度06.0=L h m ,则24.006.030.0=-=-L T h H m查图5-1得C 20=0968.0)202.34(074.0)20(2.02.020===LC C σ 415.230.130.16.8100968.0max =-=u m/s 取安全系数为,则空塔气速为69.1415.27.07.0max =⨯==u u m/s25.069.1082.044=⨯⨯=⨯⨯=ππu Vs D m 按标准塔径圆整后为 D=0.3m塔截面积为=⨯==223.044ππD A T 0.0707 m 2实际空塔气速为16.10707.0082.0==u m/s 2. 精馏塔有效高度的计算精馏段有效高度为7.53.0)120()1(=⨯-=-=T H N Z 精精m提馏段有效高度为7.23.01-101-=⨯==)()(提提T H N Z m在进料板上方开一人孔,其高度为0.8m故精馏塔的有效高度为=++=8.0提精Z Z Z ++=9.2m(六)塔板主要工艺尺寸的计算1. 溢流装置计算因塔径D=0.3m ,可选用单溢流弓形降液管,采用凹形受液盘。
各项计算如下:(1)堰长W l取 21.03.07.070.0=⨯==D l W m(2)溢流堰高度W h由 OW L W h h h -=选用平直堰,堰上液层高度依下式计算,即32)(100084.2Wh OW l L E h = 近似取E=1,则=⨯⨯⨯=32)21.03600000055.0(1100084.2OW h 0.0027m 取板上清夜层高度 60=L h mm故 0573.00027.006.0=-=W h m(3)弓形降液管宽度d W 和截面积f A由 7.03.021.0==D l W 查《化工原理课程设计》P112图5-7,得0722.0=T fA A 124.0=DW d 故 ==T f A A 0722.0=⨯0707.00722.00.0051m 2=⨯==3.0124.0124.0D W d 0.0372 m依下式验算液体在降液管中停留时间,即=⨯⨯⨯==3600000055.030.00051.036003600h Tf L H A θ〉5s 故降液管设计合理。
(4)降液管底隙高度0h03600u l L h W h '=取 08.00='u m/s =⨯⨯⨯=21.0396.036003600000055.00h 0.00066m =-=-00066.00573.00h h W 0.05664m> 0.006m故降液管底隙高度设计合理。
选用凹形受液盘,深度50='wh mm 。
2. 塔板布置(1)塔板的分块因mm D 300=,故塔板采用分块式,查表得,塔板分为3块。