镁合金热处理过程中组织与相的变化
镁合金热处理过程中组织与相的变化
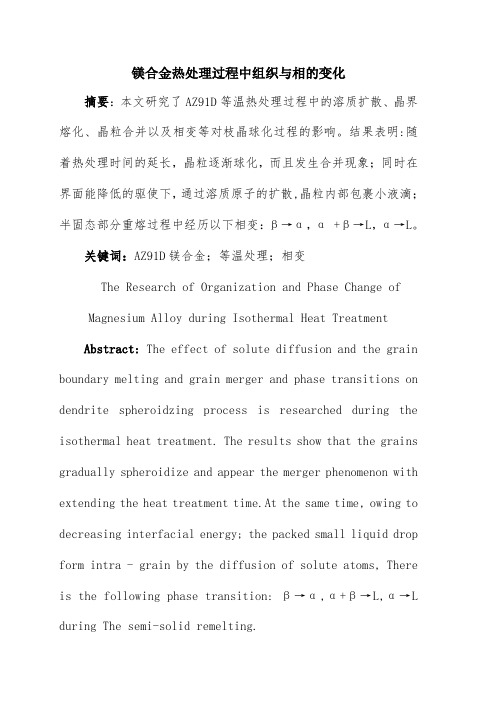
固-液界面的形态总是力图使界面吉布斯自由能最低,这样的形态才最稳定。在等温热处理过程中,组织变化的驱动力是体系自由能(表面能)的降低[5]。等温热处理过程中晶粒间表面能降低的方式有两种:(1)通过晶粒间的相对旋转,减小晶粒间的取向误差,减小晶界面积;(2)晶界迁移来增大二面角。通常等温热处理过程中,由于半固态金属的流动性差,通过晶粒旋转来降低界面能很困难,只能发生大晶粒吞噬小晶粒长大。随着时间的延长,晶粒发生合并。在等温热处理过程中,处于液固两相区内的合金铸态组织发生了次枝晶臂消失,固相颗粒发生Ostwald熟化以及合并现象,熟化和合并贯穿整个过程,只是熟化在早期占据着主要位置,随着时间的延长,合并又成了主要现象。
Key words:AZ91D magnesium alloy; isothermal treatment; phasetransition
1、概述
镁合金是现代金属结构材料中最轻的一种,以其密度低、比强度和比刚度高、尺寸稳定性好、电磁屏蔽好及价格稳定等优点,近年来在航空航天、仪器制造、国防和电子工业等领域,尤其是汽车工业中获得日益广泛的应用[1]。
镁合金半固态成具有成形温度低、凝固收缩小、缺陷和偏析减少、晶粒尺寸细小、模具寿命延长等优点,被专家学者誉为21世纪新一代新兴金属加工方法。但是,要实现镁合金的半固态成型,首先必须制备初生相为颗粒的非枝晶组织合金。国内外研究者常用的枝晶粒化方法为机械搅拌法或电磁搅拌法。由于机械搅拌法的工艺参数难以控制、搅拌设备易磨损和腐蚀、不适应与高熔点合金和易氧化合金,因此该法很难在工业上推广应用;国外已将电磁搅拌法应用于生产,但该法设备投资大,工艺复杂。半固态等温热处理作为20世纪90年代开发的一种半固态枝晶组织坯料制备方法,能够在半固态成形前的二次加热过程中直接把原材料锭坯变为半固态非枝晶组织坯料,具有工艺简单、成本低廉等优点[2-3]。本文采用半固态等温热处理法,对应用最广泛的AZ91D铸造镁合金进行了研究,观察了其在半固态等温热处理中的组织和相的变化。
镁合金的微观组织与性能研究

镁合金的微观组织与性能研究镁合金是一种重要的轻质结构材料,具有优异的轻量化、高比强度和良好的机械性能等特点,被广泛应用于汽车、航空、航天等领域。
但受到其自身的缺陷限制,如低的耐腐蚀性、易燃性等,镁合金的应用仍面临一些挑战。
因此,研究镁合金的微观组织与性能,对于进一步推广其应用具有重要意义。
镁合金的微观组织镁合金的织构镁合金的织构对其力学性能具有重要影响。
研究表明,在拉伸过程中,镁合金的晶粒会发生变形和旋转,从而形成某种织构。
基于织构的种类和大小,可以将镁合金分为不同的等级。
目前,常见的镁合金织构主要有蜡板织构、镇静轧制织构、晶粒外倾织构等。
镁合金的晶粒大小晶粒的大小也是影响镁合金力学性能的重要因素。
通常情况下,晶粒越小,组织缺陷越少,材料的塑性、韧性和强度都会得到改善。
对于镁合金的制备工艺而言,影响晶粒大小的因素主要有铸造温度、速度、冷却率等。
此外,合金化元素的添加也可以改变晶粒的大小和分布。
镁合金的传统凝固组织镁合金的传统凝固组织主要包括铸态组织和热处理组织。
铸态组织通常指在常温下通过铸造等方式形成的组织,包括粗大的单相镁晶粒以及含有比较多的亚晶粒和间晶。
热处理组织通常指在高温下进行加热处理后形成的组织,如时效组织、淬火组织等。
镁合金的协同凝固组织近期的研究表明,通过采用协同凝固方法,可以制备出更为理想的镁合金微观组织。
协同凝固是一种将铸造技术与变形加工技术进行结合的新型材料制备方法。
在这种方法下,可以通过控制加工参数和公差尺寸等,来控制晶粒大小和织构等微观组织结构。
镁合金的力学性能镁合金由于其较为独特的化学和物理结构,具有一定特殊的力学性能。
镁合金的拉伸性能镁合金的拉伸性能通常以它的拉伸强度、屈服强度、断裂延伸率等指标来衡量。
研究表明,镁合金在加工过程中,晶粒细化和织构会显著提高其拉伸强度和屈服强度,其断裂延伸率也会得到明显提升。
镁合金的耐疲劳性能镁合金的耐疲劳性能也是比较重要的力学性能指标之一。
镁合金热处理的研究现状及发展趋势
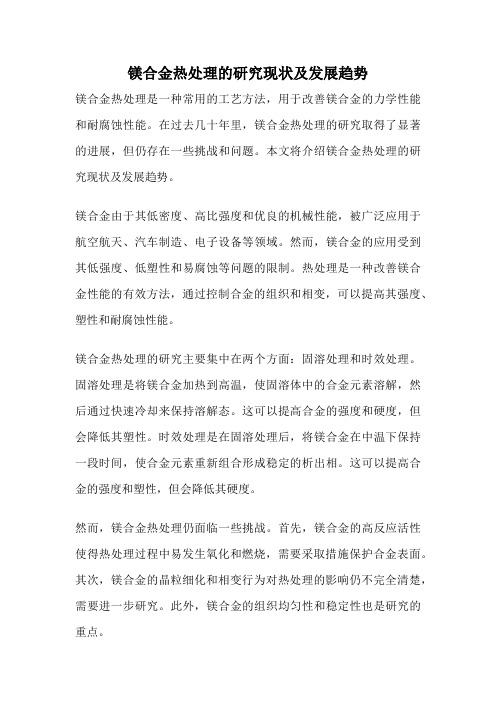
镁合金热处理的研究现状及发展趋势镁合金热处理是一种常用的工艺方法,用于改善镁合金的力学性能和耐腐蚀性能。
在过去几十年里,镁合金热处理的研究取得了显著的进展,但仍存在一些挑战和问题。
本文将介绍镁合金热处理的研究现状及发展趋势。
镁合金由于其低密度、高比强度和优良的机械性能,被广泛应用于航空航天、汽车制造、电子设备等领域。
然而,镁合金的应用受到其低强度、低塑性和易腐蚀等问题的限制。
热处理是一种改善镁合金性能的有效方法,通过控制合金的组织和相变,可以提高其强度、塑性和耐腐蚀性能。
镁合金热处理的研究主要集中在两个方面:固溶处理和时效处理。
固溶处理是将镁合金加热到高温,使固溶体中的合金元素溶解,然后通过快速冷却来保持溶解态。
这可以提高合金的强度和硬度,但会降低其塑性。
时效处理是在固溶处理后,将镁合金在中温下保持一段时间,使合金元素重新组合形成稳定的析出相。
这可以提高合金的强度和塑性,但会降低其硬度。
然而,镁合金热处理仍面临一些挑战。
首先,镁合金的高反应活性使得热处理过程中易发生氧化和燃烧,需要采取措施保护合金表面。
其次,镁合金的晶粒细化和相变行为对热处理的影响仍不完全清楚,需要进一步研究。
此外,镁合金的组织均匀性和稳定性也是研究的重点。
未来的发展趋势主要包括以下几个方面。
首先,研究人员将继续改进热处理工艺,以提高镁合金的性能。
例如,通过优化固溶处理和时效处理的工艺参数,可以获得更好的力学性能和耐腐蚀性能。
其次,研究人员将探索新的热处理方法,如等离子体处理、激光处理等,以进一步改善镁合金的性能。
此外,研究人员还将研究镁合金热处理对微观组织和相变行为的影响机制,以揭示热处理过程中的微观机制。
镁合金热处理是一种重要的工艺方法,可以改善镁合金的性能。
目前的研究主要集中在固溶处理和时效处理方面,但仍存在一些挑战和问题。
未来的发展趋势包括改进热处理工艺、探索新的热处理方法以及揭示热处理过程中的微观机制。
通过这些努力,镁合金热处理的研究将取得更大的进展,为镁合金的应用提供更好的支持。
镁合金的塑性变形及再结晶热处理对其组织性能的影响

4
轧制前的平均晶粒尺寸约40um, 15%压下量轧制并退火后平均晶粒
3.3 EX-AZ31B: tensile properties on different directions
TD 45
TD
orientation
σb/ MPa
σ0.2/ MPa
δ/ %
ED
280.0
200.4
13.2
ED
45°
258.0
125.2
19.0
TD
276.0
107.4
16.2
ED
350
➢ 有色金属材料制品中70%以上是板、带材,轧制变形 镁合金板材的研究和加工技术的突破对开发变形镁合 金产品有重要促进作用。
2、变形镁合金塑性变形原理
➢ 镁合金的塑性变形特征:HCP晶体结构及c/a轴比值造成镁的 塑性变形困难。
➢ 塑性变形机制:滑移、孪生、超塑性; ➢ 板材塑性加工方法:热加工、温加工、冷(常温)加工;
压下量
14
退火工艺
15%
30%
45%
55%
12
200度退火1h
8.9um
6.9um
5.8um
4.9um
10
400度退火5min
12.1um
8.2um
7.5umum
9.2um
7.8um
7.0um
6
annealing1h at 2000c annealing1h at 3500c
0.01 s-1
0.1 s-1
1 s-1
5s-1
10s-1
1
σ
1 0.0227
l 82
n
Z 5.5 5 1 01 2
AZ80A镁合金的均匀化处理及扩散动力学
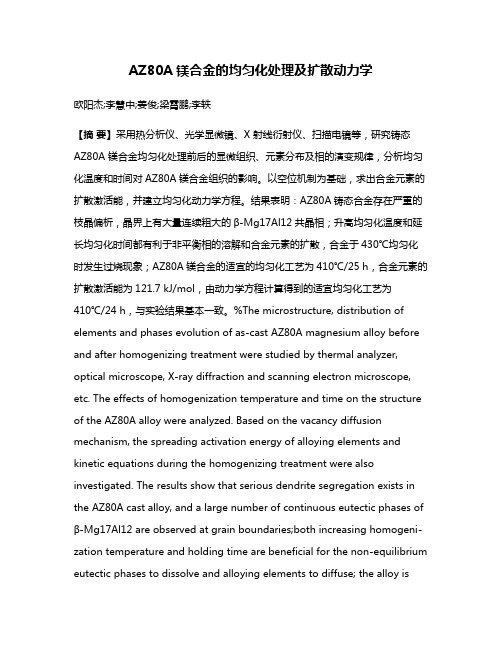
AZ80A镁合金的均匀化处理及扩散动力学欧阳杰;李慧中;姜俊;梁霄鹏;李轶【摘要】采用热分析仪、光学显微镜、X 射线衍射仪、扫描电镜等,研究铸态AZ80A 镁合金均匀化处理前后的显微组织、元素分布及相的演变规律,分析均匀化温度和时间对AZ80A镁合金组织的影响。
以空位机制为基础,求出合金元素的扩散激活能,并建立均匀化动力学方程。
结果表明:AZ80A铸态合金存在严重的枝晶偏析,晶界上有大量连续粗大的β-Mg17Al12共晶相;升高均匀化温度和延长均匀化时间都有利于非平衡相的溶解和合金元素的扩散,合金于430℃均匀化时发生过烧现象;AZ80A镁合金的适宜的均匀化工艺为410℃/25 h,合金元素的扩散激活能为121.7 kJ/mol,由动力学方程计算得到的适宜均匀化工艺为410℃/24 h,与实验结果基本一致。
%The microstructure, distribution of elements and phases evolution of as-cast AZ80A magnesium alloy before and after homogenizing treatment were studied by thermal analyzer, optical microscope, X-ray diffraction and scanning electron microscope, etc. The effects of homogenization temperature and time on the structure of the AZ80A alloy were analyzed. Based on the vacancy diffusion mechanism, the spreading activation energy of alloying elements and kinetic equations during the homogenizing treatment were also investigated. The results show that serious dendrite segregation exists in the AZ80A cast alloy, and a large number of continuous eutectic phases of β-Mg17Al12 are observed at grain boundaries;both increasing homogeni-zation temperature and holding time are beneficial for the non-equilibrium eutectic phases to dissolve and alloying elements to diffuse; the alloy isover-burnt when the temperature reached 430 ℃. It is concluded that the proper homogenizing parameters of AZ80A magnes ium alloy is 410 ℃ for 25 h and the spreading activation energy is 121.7 KJ/mol, which are in good agreement with the experiment results of the present paper.【期刊名称】《粉末冶金材料科学与工程》【年(卷),期】2014(000)001【总页数】7页(P8-14)【关键词】AZ80A镁合金;均匀化;组织演变;动力学方程【作者】欧阳杰;李慧中;姜俊;梁霄鹏;李轶【作者单位】中南大学材料科学与工程学院,长沙 410083;中南大学材料科学与工程学院,长沙 410083; 中南大学粉末冶金国家重点实验室,长沙 410083; 中南大学有色金属材料科学与工程教育部重点实验室,长沙 410083;中南大学材料科学与工程学院,长沙 410083;中南大学粉末冶金国家重点实验室,长沙 410083;中南大学材料科学与工程学院,长沙 410083【正文语种】中文【中图分类】TG146.2镁合金具有密度低、比强度和比刚度高等特点,在汽车、化工、3C 产品等行业中得到广泛应用[1−3]。
热处理工艺对于金属材料组织与性能的影响
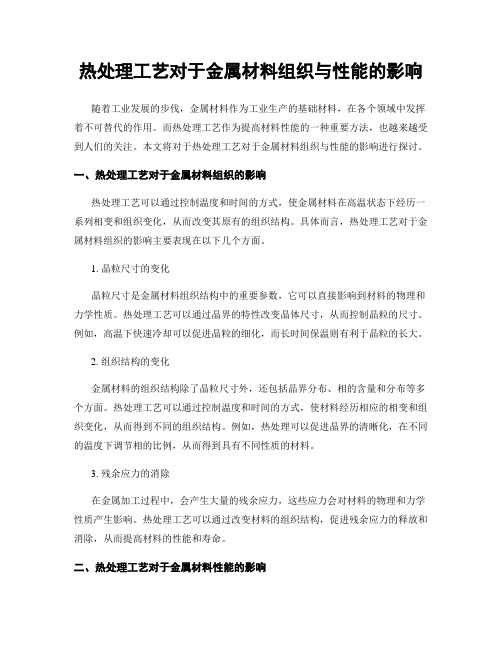
热处理工艺对于金属材料组织与性能的影响随着工业发展的步伐,金属材料作为工业生产的基础材料,在各个领域中发挥着不可替代的作用。
而热处理工艺作为提高材料性能的一种重要方法,也越来越受到人们的关注。
本文将对于热处理工艺对于金属材料组织与性能的影响进行探讨。
一、热处理工艺对于金属材料组织的影响热处理工艺可以通过控制温度和时间的方式,使金属材料在高温状态下经历一系列相变和组织变化,从而改变其原有的组织结构。
具体而言,热处理工艺对于金属材料组织的影响主要表现在以下几个方面。
1. 晶粒尺寸的变化晶粒尺寸是金属材料组织结构中的重要参数,它可以直接影响到材料的物理和力学性质。
热处理工艺可以通过晶界的特性改变晶体尺寸,从而控制晶粒的尺寸。
例如,高温下快速冷却可以促进晶粒的细化,而长时间保温则有利于晶粒的长大。
2. 组织结构的变化金属材料的组织结构除了晶粒尺寸外,还包括晶界分布、相的含量和分布等多个方面。
热处理工艺可以通过控制温度和时间的方式,使材料经历相应的相变和组织变化,从而得到不同的组织结构。
例如,热处理可以促进晶界的清晰化,在不同的温度下调节相的比例,从而得到具有不同性质的材料。
3. 残余应力的消除在金属加工过程中,会产生大量的残余应力,这些应力会对材料的物理和力学性质产生影响。
热处理工艺可以通过改变材料的组织结构,促进残余应力的释放和消除,从而提高材料的性能和寿命。
二、热处理工艺对于金属材料性能的影响热处理工艺可以通过改变材料的组织结构,从而影响材料的物理和力学性质。
具体而言,热处理工艺对于金属材料性能的影响主要表现在以下几个方面。
1. 强度和硬度热处理可以使金属材料得到更为细致和均匀的组织结构,从而提高其硬度和强度。
例如,通过快速冷却可以促进晶粒细化,增强材料的塑性和韧性,同时也可以提高材料的屈服强度和硬度。
2. 韧性和延展性金属材料的韧性和延展性与其晶界分布和相的含量有很大关系,热处理可以通过调节晶界的特性和改变相的比例,从而提高材料的韧性和延展性。
热处理对合金显微组织的演变规律
热处理对合金显微组织的演变规律热处理是一种用于改变合金材料显微组织的热力学过程。
通过控制材料的加热、保温和冷却过程,可以改变合金的晶粒尺寸、相比例和相形态,从而调整材料的性能。
合金的显微组织演变规律是指在热处理过程中,合金的晶粒尺寸、相比例和相形态的变化规律。
热处理对合金显微组织的演变规律可以分为三个阶段:加热阶段、保温阶段和冷却阶段。
在加热阶段,合金材料被加热到一定温度,晶粒开始长大。
晶粒的长大是由于晶界的运动和晶体内部的原子扩散。
晶界的运动是指晶界的位错运动和晶粒边界的迁移,晶界的运动可以促使晶体内部的原子扩散。
原子扩散是指原子在晶体内部的移动,当晶粒被加热到一定温度时,原子会具有足够的热能来克服晶体表面的能垒,从而在晶体内部扩散。
在保温阶段,合金材料保持在一定温度下,晶粒继续长大,晶粒的尺寸逐渐增大。
在冷却阶段,合金材料被快速冷却,晶粒的尺寸被固定下来。
热处理对合金显微组织的演变规律不仅取决于加热温度和保温时间,还与合金的成分和冷却方式有关。
不同的合金在相同的热处理条件下,其显微组织演变规律可能会有所不同。
例如,对于某些合金,加热温度过高或保温时间过长可能会导致晶粒长大过快,从而使材料的力学性能下降。
此外,合金的成分对其显微组织演变规律也有重要影响。
不同的合金成分会导致不同的相形态和相比例,从而影响材料的性能。
冷却方式也是影响合金显微组织演变规律的重要因素。
不同的冷却方式可以导致不同的晶粒尺寸和相形态。
热处理对合金显微组织的演变规律的研究对于合金材料的设计和应用具有重要意义。
通过控制热处理参数,可以调整合金的显微组织,从而改变材料的性能。
例如,通过细化晶粒尺寸可以提高合金的强度和硬度,提高材料的耐磨性和耐腐蚀性;通过调整相比例和相形态可以改善合金的韧性和塑性,提高材料的冲击韧性和延展性。
因此,热处理对于合金材料的制备和加工具有重要意义。
热处理是一种用于改变合金材料显微组织的热力学过程。
热处理对合金显微组织的演变规律可以分为加热阶段、保温阶段和冷却阶段。
热处理工艺对不同材料的显微组织和相变的影响
热处理工艺对不同材料的显微组织和相变的影响热处理工艺是材料科学中一个非常重要的工艺,通过控制材料的加热和冷却过程,可以显著改变材料的显微组织和性能。
不同材料的显微组织和相变受热处理工艺的影响也不尽相同。
首先,对于钢材来说,热处理工艺对其显微组织和相变的影响尤为明显。
钢材经过加热和冷却过程,可以通过不同的热处理方式,如退火、正火、淬火等,来调控其组织和性能。
退火处理可以通过连续加热至适当温度,然后慢慢冷却,使钢材结晶微观组织内部发生均匀化和再结晶,从而获得良好的塑性和韧性。
而正火处理则是将钢材加热至奥氏体区域,然后慢慢冷却,使其获得良好的硬度和强度。
淬火则是将钢材迅速冷却,使其形成马氏体组织,从而获得更高的硬度。
通过这些热处理工艺,可以使钢材在不同工程应用中具有理想的组织和性能。
此外,对于铝合金来说,热处理工艺也能对其显微组织和相变产生重要的影响。
铝合金中的合金元素通过热处理可以形成细小且均匀分布的相,如硬质相、溶固相等。
通过固溶处理,可以将整个合金加热至其固溶温度,然后迅速冷却,使溶固相得到均匀溶解,并使合金的形变能降低。
而时效处理则是将固溶态的合金加热至一定温度,在一定时间内静置,使溶固相再次析出,并进行相变。
这种时效处理能够调节合金的硬度和强度,提高其机械性能。
此外,对于陶瓷材料来说,热处理工艺同样会对其显微组织和相变产生影响。
常见的热处理工艺有烧结和再结晶等。
烧结是指将陶瓷颗粒加热至一定温度,使其表面熔化并熔结在一起,从而形成致密的陶瓷材料。
再结晶则是将陶瓷材料加热至足够高的温度,使其发生晶粒长大和再分布的过程,从而改善材料的晶界和性能。
总之,热处理工艺对不同材料的显微组织和相变产生着重要的影响。
通过合理选择热处理工艺和参数,可以调控材料的显微组织,从而实现对材料性能的优化和调整。
在实际应用中,热处理工艺在材料的制备和加工过程中扮演着重要的角色,为各行各业的发展提供了支撑。
因此,研究和掌握不同材料的热处理工艺,对于材料科学和工程领域的发展具有重要的意义。
不同退火条件下AZ31镁合金的组织和硬度分析
10
Hot Working Technology 2009, Vol.38, No.4
下半月出版
Material & Heat Treatment 材料热处理技术
280℃) 退火处理时,延长保温时间,晶粒变得更加 细小、更加均匀。 这是因为当保温时间延长后,静 态再结晶基本吞噬了所有的原始晶粒组织, 此时 晶粒达到最小。 当在较高温度时,晶粒出现了不 均匀分布和异常长大现象,见图 3(b)。 这可能是在 400 ℃时在很短时间内就完成了再结晶 , 随后开 始出现晶粒异常长大的情况, 部分区域甚至出现 超大晶粒组织 。 [7-8] 图 3(d)中晶粒的保温时间已达 7 h,可以看出,晶粒已明显存在超大的晶粒组织, 此时的力学性能最差,硬度应该最低,这与后面的 硬度试验的结果是相匹配的。
(b)
×50
×160
图 1 AZ31 在 350 ℃×15 min 去应力退火+350 ℃× 3 h 完全 退火后的微观组织(氢氟酸腐蚀)
Fig.1 The microstructure of AZ31 after relief annealing at 350 ℃ for 15min and full annealing at 350 ℃ for 3 h
淀方式析出,温度较高时, 通常以非连续方式析 出[4]。 图 1 和图 2 为析出的 Mg17Al12 相及其放大后 的形貌。 由于 350 ℃×3 h 的处理温度较 280 ℃×5 h
高,故其 Mg17Al12 相的析出为非连续析出,而非连 续析出相多呈粗大的层片状,见图 1(b),弥散度较
(a)
2009 年 2 月
表 1 AZ31 镁合金热处理工艺
(a)
(b)
等温处理半固态al—4cu—mg合金过程中的组织演化
等温处理半固态al—4cu—mg合金过程中的组织演化等温处理半固态Al-4Cu-Mg合金是一种重要的热处理工艺,通过该工艺可以获得良好的力学性能和耐腐蚀性能。
在等温处理的过程中,合金的组织会发生演化,因此研究并理解合金组织演化的规律对于正确操作等温处理具有重要意义。
1.初期固化阶段在等温处理的初期阶段,合金开始由液态向固态转变。
在这个阶段,合金中的固溶体溶解度逐渐减小,形成一些小的晶粒。
这些晶粒可以进一步长大,形成细小的初生晶体。
2.半固态阶段在固化阶段之后,合金进入半固态阶段。
在这个阶段,合金的温度保持在一个相对稳定的温度区间,固溶体晶粒的细化和再结晶现象开始发生。
由于固溶体的溶解度降低,溶解态的元素在晶界或晶内析出,形成相颗粒。
同时,由于晶粒的长大与再结晶现象的竞争,合金的组织结构会发生变化。
3.再结晶阶段半固态阶段之后,合金进入再结晶阶段。
在这个阶段,合金中的晶体继续长大,形成更大的再结晶晶粒。
同时,固溶体的溶解度继续降低,相颗粒不断增多。
再结晶过程是晶体重新排列的过程,从而形成稳定的组织结构。
在等温处理过程中,合金的组织演化过程是相互耦合的。
合金中的溶解度变化、相颗粒的形成和再结晶晶粒的长大都会相互影响,进而改变合金的力学性能和耐腐蚀性能。
此外,等温处理过程中的温度、时间和合金成分等因素都会对组织演化过程产生影响。
合适的温度和时间可以促使晶粒的长大和再结晶现象的进行,进而提高合金的力学性能。
合金成分的变化也会对组织演化过程产生影响,例如Cu和Mg元素的含量变化会改变相颗粒的种类和数量。
总之,等温处理半固态Al-4Cu-Mg合金的组织演化过程是一个复杂的过程,涉及到溶解度的变化、相颗粒的形成和再结晶晶粒的长大。
了解和掌握这些规律对于正确操作等温处理具有重要意义,并能够提高合金的力学性能和耐腐蚀性能。
- 1、下载文档前请自行甄别文档内容的完整性,平台不提供额外的编辑、内容补充、找答案等附加服务。
- 2、"仅部分预览"的文档,不可在线预览部分如存在完整性等问题,可反馈申请退款(可完整预览的文档不适用该条件!)。
- 3、如文档侵犯您的权益,请联系客服反馈,我们会尽快为您处理(人工客服工作时间:9:00-18:30)。
镁合金热处理过程中组织与相的变化Prepared on 24 November 2020镁合金热处理过程中组织与相的变化摘要:本文研究了AZ91D等温热处理过程中的溶质扩散、晶界熔化、晶粒合并以及相变等对枝晶球化过程的影响。
结果表明:随着热处理时间的延长,晶粒逐渐球化,而且发生合并现象;同时在界面能降低的驱使下,通过溶质原子的扩散,晶粒内部包裹小液滴;半固态部分重熔过程中经历以下相变:β→α,α +β→L,α→L。
关键词:AZ91D镁合金;等温处理;相变The Research of Organization and Phase Change of Magnesium Alloyduring Isothermal Heat TreatmentAbstract: The effect of solute diffusion and the grain boundary melting and grain merger and phase transitions on dendrite spheroidzing process is researched during the isothermal heat treatment. The results show that the grains gradually spheroidize and appear the merger phenomenon with extending the heat treatment the same time, owing to decreasing interfacial energy; the packed small liquid drop form intra - grain by the diffusion of solute atoms, There is the following phase transition: β→α,α+β→L,α→L during The semi-solid remelting. Key words:AZ91D magnesium alloy; isothermal treatment; phase transition1、概述镁合金是现代金属结构材料中最轻的一种,以其密度低、比强度和比刚度高、尺寸稳定性好、电磁屏蔽好及价格稳定等优点,近年来在航空航天、仪器制造、国防和电子工业等领域,尤其是汽车工业中获得日益广泛的应用[1]。
镁合金半固态成具有成形温度低、凝固收缩小、缺陷和偏析减少、晶粒尺寸细小、模具寿命延长等优点,被专家学者誉为21世纪新一代新兴金属加工方法。
但是,要实现镁合金的半固态成型,首先必须制备初生相为颗粒的非枝晶组织合金。
国内外研究者常用的枝晶粒化方法为机械搅拌法或电磁搅拌法。
由于机械搅拌法的工艺参数难以控制、搅拌设备易磨损和腐蚀、不适应与高熔点合金和易氧化合金,因此该法很难在工业上推广应用;国外已将电磁搅拌法应用于生产,但该法设备投资大,工艺复杂。
半固态等温热处理作为20世纪90年代开发的一种半固态枝晶组织坯料制备方法,能够在半固态成形前的二次加热过程中直接把原材料锭坯变为半固态非枝晶组织坯料,具有工艺简单、成本低廉等优点[2-3]。
本文采用半固态等温热处理法, 对应用最广泛的AZ91D铸造镁合金进行了研究, 观察了其在半固态等温热处理中的组织和相的变化。
2.镁合金热处理过程分析铸太组织AZ91D 镁合金初生相α相(灰色)以树枝晶形态存在,沿α相不连续分布的白色组织为(α+β)共晶组织。
组织形貌变化随着保温时间的延长,铸态组织中的枝晶臂逐渐消失,由不规则形状向球状转变。
晶界处的共晶组织和晶粒内部的富Al、Zn部分首先熔化,在两个晶粒间以液态薄膜形式存在,在多晶粒交界处以液态熔池形式存在,而在晶粒内部则以小液滴形态存在。
到10 min时,液态薄膜的厚度增加,熔池的体积增大,晶粒完全被液态金属层包围,而晶粒内部开始出现小液滴,初生晶粒全变为近球状的颗粒组织。
到20 min时,晶粒内的小液滴变大,同时数量减少。
可以看出,在20 min之前,随着保温时间的延长,晶粒逐渐长大[9]。
溶质原子扩散溶质原子的扩散行为在加热过程中可分为两个阶[4]:在温度升至共晶点温度之前,属于均质化扩散;当温度达到共晶点时,共晶化合物开始融化,周围的溶质原子向液态共晶化合物中富集,融化区域扩大,但是邻近区域成为溶质贫化区,这些区域的熔点升高,如果继续熔化,就必须升高温度。
在加热温度升至固相线温度前,只有富Al的共晶组织熔化,在多个晶粒交界处形成熔池,同时晶粒内部那些富Al、Zn的小质点开始熔化。
在温度升至固相线后的保温过程中,随着时间的推移,在界面能最小化的驱动下,晶粒内熔化的小质点通过溶质原子的扩散合并成小液滴,或向晶界处液态中扩散而消失。
枝晶组织球化分析枝晶组织球化过程包括二次枝晶臂消失、脱落、枝晶沉淀以及Ostwald 熟化过程。
T. Z. Kattamis,J. J. Reeves、Kuang-Ho Chen等人先后对二次枝晶臂粗化进行了研究,并分别提出了二次枝晶臂粗化的四种物理模型:径向融化模型、颈缩熔断模型、轴向融化模型与枝晶合并模型。
在枝晶生长过程中,二次枝晶臂由于他们的曲率不同,会造成各枝晶臂附近液相内的溶质浓度的差别,枝晶曲率半径越小,附近液相溶质浓度越低,这样溶质浓度梯度的存在将促使溶质从粗枝处向细枝处扩散,造成细枝熔化和粗枝变粗。
因此,在固、液两相区停留的时间愈长,上述过程进行的愈充分,枝晶球化愈明显。
随着保温时间的延长,晶粒由等轴晶→枝晶熔断→分裂成块状→球化。
对于镁合金半固态保温过程中组织的球化,可认为当组织中固相体积一定时,只有成球状或近球形才具有最小的表面能,所以从表面能较高的星状向球状转化,使系统的自由能下降,这是一个热力学自发过程,等轴晶组织能否球化,主要取决于原子的扩散。
当在两相区保温时,使原子具有足够的动力学条件发生聚集球化。
2. 5晶粒合并分析固-液界面的形态总是力图使界面吉布斯自由能最低,这样的形态才最稳定。
在等温热处理过程中,组织变化的驱动力是体系自由能(表面能)的降低[5]。
等温热处理过程中晶粒间表面能降低的方式有两种:(1)通过晶粒间的相对旋转,减小晶粒间的取向误差,减小晶界面积;(2)晶界迁移来增大二面角。
通常等温热处理过程中,由于半固态金属的流动性差,通过晶粒旋转来降低界面能很困难,只能发生大晶粒吞噬小晶粒长大。
随着时间的延长,晶粒发生合并。
在等温热处理过程中,处于液固两相区内的合金铸态组织发生了次枝晶臂消失,固相颗粒发生Ostwald熟化以及合并现象,熟化和合并贯穿整个过程,只是熟化在早期占据着主要位置,随着时间的延长,合并又成了主要现象。
2. 6液相变化分析热处理过程中液相以液态薄膜、熔池和晶内小液滴三种形式存在。
在形成液固相组织时,液相侵蚀晶界,形成包裹固相的液层。
但在固相体积分数极高的情况下,两固相颗粒间一般不能通过合并来降低界面能;同时,固相颗粒与熔池界面处的半径远小于与液态薄膜界面处的半径,从而产生曲率差效应;在这两种因素的综合作用下,根据Gibbs-Thomson效应[6]可知:当晶粒的局部半径趋于无限大时,其吉布斯自由能趋于最小,与液态薄膜接触的固相界面尽可能地发展成平面,从而在二维平面上薄膜以直线向熔池中推进,形成直线形貌的淬火共晶组织。
随着热处理加热时间的延长,液相体积增加和晶粒熟化,薄膜形状成为圆弧形,形成以大量液相为基体,球形颗粒分散其中的半固态浆料。
在半固态加工的后序成形过程中,液相的多少决定了合金浆料的流动性[7-8],从而决定充型速度和充型压力,晶内小液滴的多少对合金铸件的成形性能有着很大影响。
小液滴的形成有三种原因:(1)晶粒在凝固过程中吞没的富Al杂质或晶内偏析造成的,低熔点富Al质点经过熔化、扩散、合并形成较大液滴,而位于晶粒边部质点通过溶质原子扩散到液相组织中而消失,两者都促进了小液滴的数目减少;(2)等温热处理初期处于熔化与合并的动态平衡中,枝晶臂间发生合并衔接,而枝晶根部未扩散完的低熔点共晶组织发生熔化,形成晶内液池;(3)在次枝晶臂缩颈熔断后原位沉淀在主干上发生熟化过程中形成的,二次枝晶臂在主干上沉淀时发生搭桥现象,在熟化过程中形成晶粒内包裹液滴。
2. 7相变分析组织的变化是由相变引起的,为了更好地解释镁合金组织的演变过程,通过相的变化来分析该过程。
重熔是凝固的反过程,由于Mg-Al-Zn三元相只有在Zn与Al的质量比大于1 /3时才会形成,因此对于AZ91D合金而言,可不考虑少量Zn对AZ91D相图的影响[5],可以根据Mg-Al二元相图分析AZ91D镁合金在熔化过程中的组织演变。
从相图可以看出半固态部分重熔过程中势必经历以下相变:β→α,α+β→L,α→L。
图1 Mg-Al二元合金富镁相图图2 AZ91D镁合金在580℃加热不同时间后的XRD图谱AZ91D镁合金组织由富镁相α相和沿α相不连续分布的(α+β)共晶相组成。
图2所示为AZ91D镁合金在580℃加热不同时间后的X射线衍射谱。
可以看出,在加热初期,因进行β→α的相变,使β相的量减少,而α相的量增加。
因β→α相变使晶界处共晶组织中的β相向晶内扩散,一方面造成晶粒晶界的减少和晶粒的合并,另一方面使初生α相中的Al含量增加,β相中的Al含量减少。
因加热初期,试样温度升高很快而引发相变α+β→L,使β相的量减少。
α+β→L相变使未来得及扩散的共晶组织开始熔化,造成大块状组织分离,同时α相中的Al含量增加,β相中的Al含量减少。
随着加热时间的延长,因进行α+β→L的相变,使液相量增加,大块状组织全部分离成相互独立的多边形颗粒。
随着加热时间的继续延长和试样温度的升高,从而引发α→L相变,使α相中的Al含量略微减少,β相中的Al含量略有增加,α→L相变使多边形晶粒的凸棱熔化而发生球化,直至体系达到固-液相平衡态。
3 结论(1)随着保温时间的延长,晶粒由等轴晶→枝晶熔断→分裂成块状→球化。
(2)在等温热处理过程中晶界处共晶首先熔化,随着热处理温度的上升,在两固相颗粒间的液态薄膜逐渐包裹了固相颗粒,形成固相颗粒分散在液态基体中的半固态浆料。
(3)半固态部分重熔过程中经历以下相变:β→α,α+β→L,α→L。
参考文献[1] Kaneko Tadataka, Suzuki Masami Automotive applications of magnesium alloys [J]. Materials Science Forum, 2003, 419-422(1):67 - 72.[2] Nicholas N H, Trichka M R, Young K P. Application of Semi-solid Metal Forming to the Production of Small Components [A]. Proceeding of the 5th International Conference on Semi-solid Processing of Alloys and Compri-SiteS [C]. Colorado USA, 1999, 6(23-25): 79-85. [3] 路贵民,董杰,崔建忠等. 液相线半连续铸造7075Al合金二次加热与触变成形[J] 金属学报,2001,37(11) :1185-1188.[4] 王瑞权,张大华等。