机械工程专业英语论文(精编文档).doc
有关工程机械的英语作文

有关工程机械的英语作文Title: The Evolution and Importance of Engineering Machinery。
Engineering machinery plays a pivotal role in modern construction and infrastructure development. From towering skyscrapers to expansive highways, these machines form the backbone of the construction industry, enabling projects to be completed efficiently and effectively. In this essay, we will delve into the evolution and significance of engineering machinery.The history of engineering machinery dates back centuries, with rudimentary tools like pulleys and levers being used for lifting and moving heavy objects. However, it was during the Industrial Revolution that significant advancements were made in mechanical engineering, leading to the development of steam-powered machines. These early innovations laid the foundation for the sophisticated engineering machinery we see today.One of the most iconic pieces of engineering machinery is the crane. Cranes come in various types, including tower cranes, mobile cranes, and crawler cranes, each suited for different construction tasks. Tower cranes, for instance, are commonly used in the construction of tall buildings, providing the necessary height and lifting capacity. On the other hand, mobile cranes are versatile and can be easily transported to different job sites, making them ideal for various construction projects.Excavators are another indispensable piece of engineering machinery. These heavy-duty machines are used for digging trenches, foundations, and earthmoving tasks. With their hydraulic systems and powerful digging arms, excavators can handle a wide range of materials, from soil and rocks to concrete and debris. The versatility of excavators makes them essential for any construction project, from building skyscrapers to digging tunnels.In recent years, there has been a surge in the development of automated and robotic engineering machinery.These advanced machines utilize cutting-edge technology, such as artificial intelligence and machine learning, to enhance efficiency and productivity on construction sites. Robotic bricklayers, for example, can lay bricks with precision and speed, reducing labor costs and construction time. Similarly, automated bulldozers and graders can perform earthmoving tasks with greater accuracy, minimizing errors and rework.The significance of engineering machinery in construction cannot be overstated. These machines not only improve productivity and efficiency but also enhance safety on job sites. By mechanizing repetitive and labor-intensive tasks, engineering machinery reduces the risk of accidents and injuries, creating a safer working environment for construction workers.Furthermore, engineering machinery plays a crucial role in sustainable construction practices. With growing concerns about environmental impact, there is a greater emphasis on using eco-friendly materials and construction methods. Modern engineering machinery is designed tominimize energy consumption and emissions, contributing to a more sustainable construction industry.In conclusion, engineering machinery is the backbone of the construction industry, enabling the realization of complex projects with efficiency and precision. From cranes and excavators to automated robots, these machines continue to evolve, driving innovation and progress in construction practices. As we look to the future, the role of engineering machinery will only become more prominent, shaping the landscape of modern infrastructure and development.。
机械工程科技论文 英文版

MICRO PLANETARY REDUCTION GEAR USINGSURFACE-MICROMACHININGAbstractA micro planetary gear mechanism featuring a high gear reduction ratio with compactness in size ispresented in this paper. SUMMiT V is employed for the fabrication method so that the redundancy of assembling parts is eliminated. The design rules of which has also been checked. To make full use of the benefits of the surface- micro - machining, the planetary reduction gear is designed toward using the on-chip micro- engine. The expected gearreduction ratio is calculated and compared with the conventional chain gear mechanism. The microplanetary gear mechanism presented in this paper is expected to have 162:1 reduction ratio utilizing less space consumption. This is an order of magnitude higher than the previously reported design in a single reduction gear train.Keywords:MEMS, planetary gear, reduction gear surface-micromachining, SUMMiT V processNomenclaturea sun gearb planet gearsc internal gear (fixed)d internal gear (rotary)n the number of units of gear trainD diameter of the pitch circleN number of teethP number of planetsa ngular velocityIntroductionThe gear mechanisms in microelectro mechanical systems(MEMS) are commonly expected to generate high torque in the confined micro-size systems. However, it is generally difficult for the micro-scale systems to have such a high torque without having multiple reduction systems.The design of the reduction gear drive based on a planetary paradox gear mechanism can increase the torque within a compact area, since the microplanetary gear system has an advantage of high reduction ratio per unit volume [1]. However its mechanism is so complicated that relatively few attempts have been made to miniaturize the gear systems [2-3]. Suzumori et al.[2] used the mechanical paradox planetary gear mechanism to drive a robot for 1-in pipes forward or backward. They employed a single motor to drive the gear mechanisms with high reduction ratio. Precise gear fabrication was enabled by micro wire electrical discharge machining (micro-EDM). These parts, however, should be assembled before the drive motor is attached to the gearbox. Takeuchi et. al. [3] also used micro-EDM to fabricate the microplanetary gears. They suggested special cermets or High Carbon Steel for possible materials. While the design can achieve a reduction ratio of 200, the gears should also be assembled and motor driven.To enable the driving of the planetary gear by onchip means, Sandia Ultra- planar Multi-level MEMS Technology (SUMMiT-V) process [4] for planetary gear fabrication is adopted in this study. The SUMMiT-V process is the only foundry process available which utilizes four layers of releasable polysilicon, for a total of five layers (including a ground plane) [5]. Due to this fact, it is frequently used in complicated gear mechanisms being driven by on-chip electrostatic actuators [5].However, in many cases, the microengines may not produce enough torque to drive the desired mechanical load, since their electrostatic comb drives typically only generate a few tens of micronewtons of force. Fortunately, these engines can easily be driven at tens of thousands of revolutions per minutes. This makes it very feasible to trade speed for torque [7].Rodgers et al. [7] proposed two dual level gears with an overall gear reduction ratio of 12:1. Thus six of these modular transmission assemblies can have a 2,985,984:1 reduction ratio at the cost of the huge space.With the desire for size compactness and at the same time, high reduction ratios, the planetary gear system is presented in this paper. It will be the first planetary gear mechanism using surface micromachining,to the authors knowledge. The principles of operations of the planetary gear mechanism, fabrication, and the expected performance of the planetary gear systems are described in this paper.Principles of operationAn alternative way of using gears to transmit torque is to make one or more gears, i.e., planetary gears, rotate outside of one gear, i.e. sun gear. Most planetary reduction gears, at conventional size, are used as well-known compact mechanical power transmission systems [1]. The schematic of the planetary gear system employed is shown in FigureSince SUMMiT V designs are laid out using AutoCAD 2000, the Figure 1 is generated automatically from the lay out masks (Appendix [1]). One unit of the planetary gear system is composed of six gears: one sun gear, a, three planetary gears, b, one fixed ring gear, c, one rotating ring gear, d, and one output gear. The number of teeth for each gear is different from one another except among the planetary gears. An input gear is the sun gear, a, driven by the arm connected to the micro-engine. The rotating ring gear, d, is served as an output gear. For example, if the arm drives the sun gear in the clockwise direction, the planetary gears, b, will rotate counter-clockwise at their own axis and at the same time, those will rotate about the sun gear in clockwise direction resulting in planetary motion. Due to the relative motion between the planetary gears, b, and the fixed ring gear, c, the rotating ring gear, d, will rotate counterclockwise direction. This is so called a 3K mechanical paradox planetary gear [1]. Fabrication procedure and test structuresThe features of the SUMMiT V process offer four levels of structural polysilicon layers and an electrical poly level, and also employ traditional integrated circuit processing techniques [4]. TheSUMMiT V technology is especially suitable for the gear mechanism. The planetary gear mechanism can be driven by the on-chip engine and thus is another reason of using the SUMMiT V process.Since the Sandia process is such a well-known procedure [5-7], only brief explanation is presented. Figure 2 represents the cross-sectional view of Figure 1, and also was generated from the AutoCAD layout masks (Appendix [1]). The discontinuity in the cross-section is for the etch holes. The poly1 (gray) is used for the hubs and also patterned to make the fixed ring gear, i.e., c, the sun gear, i.e., a, the rotating ring gear, i.e., c, and the output gear is patterned in the poly2. Since the planetary gear needs to contact both the fixed ring and rotating ring gear, poly2 is added to poly3, where the gear teeth are actually formed. The poly4 layer is used for the arm that drives the sun gear. After the release etch, the planetary gears will fall down so that those will engage both the ring gears.The figures for the test structures are presented in Appendix [2]. Since the aim of this paper is to suggest a gear reduction mechanism, the planetary gear system is decomposed to several gear units to verify its performance. The first test structure is about the arm, which rotates the sun gear, connected to the on-chip engine. The angular velocity of the arm depends on the engine output speed. The second test structure describes the point at which the sun gear and planetary gears are engaged to the fixed ring gear. Because of the fact that the ring gear is fixed, the planetary gear is just transmitting the torque from the sun gear to the fixed ring gear without planet motion, e.g., rotating its own axis not around the sun gear. When the rotating ring gear is mounted on top of the fixed ring gear, i.e., the third test structure, the planetary gears begin to rotate around the sun gear so that the planet motion are enabled. Therefore, once one output gear is attached to the rotating ring gear, i.e., the final test structure, the whole reduction unit is completed. Dismantling theplanetary gear into three test structures allows the pinpointing of possible errors in the gear system.Solutions procedure and expected performanceThe reduction ratio is defined as the ratio between the angular velocity of the driver gear and that of the driven gear. High reduction ratios indicate trading speed for torque. For example, a 10:1 gear reduction unit could increase torque an order of magnitude. Since the gears in the planetary system should be meshed to one another , the design of gear module should follow a restriction. For example, the number of teeth for the sun gear plus either that of the fixed ring gear or that of the rotating ring gear should be the multiple of the number of planets, P (equation 1). Equation 2, which represent the reduction ratio, should observe the equation 1 first. The N is the number of the teeth for corresponding gear.Gears, a, b, c, d in the planetary gear system have a tooth module of 4 m, which is a comparable size of the current gear reduction units[5], and the tooth numbers are 12, 29, 69, and 72 respectively. Therefore the overall reduction ratio is 162:1 from equation (2). Rodgers et al.[7] reported a 12:1 reduction unit using surface micromachining, which is less than order of magnitude for the gear reduction ratio of the planetary gear system. Although the reduction from Rodgers et al. [7] needs to be occupied in approximately 0.093 mm2, the planetary gear system only utilizes an area of approximately 0.076 mm2. Thus, this planetary reduction design can achieve an order of magnitude higher reduction ratio with less space. Since thereduction module is composed of several reduction units, the advantage of using a planetary gear system is self evident in Figure 3.Figure 3 shows the comparison of reduction ratios between the proposed planetary gear mechanism i.e. 162n, and the Sandia gear system [7], i.e. 12n, as a function of the number of units, i.e., n. The ordinate is drawn in log scale so that the orders of magnitude differences between two modules are evident. For example, in a module with five numbers of units, the reduction ratio difference between two is approximately six orders of magnitudes. Furthermore, the planetary gear system can save 8500 m2 in such a five unit reduction system.Conclusion and discussionsThe planetary gear reduction system using surface-micromachining, driven by an on-chip engine, first appears in this paper within the authors’ knowledge. The single reduction unit can achieve an order of magnitude higher reduction ratio than that of the previous design. However, due to the surface friction, and the backlash, which is inevitable for the gear manufacturing process, the overall reduction ratio may be less than 162:1 in the real situation. Even though some loss might be expected in the real application, the overall reduction ratio should be order of magnitude higher and the space consumption is less than the previous design [7].The authors learned a lot about the surfacemicromachining process during the project grant,and realized that a lot of the design needed to be revisited and corrected. This became prevalent when drawing the cross-sectional views of the design. Since the authors utilized the SUMMit V Advanced design Tools Software package and verified the design rules, the planetary gear layout is ready for fabrication. The authors hope that this planetary reduction unit will continue to be updated by successive researchers.AcknowledgementThe authors would acknowledge that discussions with Prof. Kris Pister, Prof. Arun Majumdar, Ms. Karen Cheung, and Mr. Elliot Hui contributed to this work tremendously.References1. Hori, K., and Sato, A., “Micro-planetary reduction gear” Proc. IEEE 2nd Int. Symp. Micro Machine and Human Sciences, pp. 53- 60 (1991).2. Suzumori, K., Miyagawa, T., Kimura, M., and Hasegawa, Y., “Micro Inspection Robot for 1-in Pipes”, IEEE/ASME Trans. On Mechatronics, Vol. 4., No. 3, pp. 286-292 (1999).3. Takeuchi, H., Nakamura, K., Shimizu, N., and Shibaike, N., “Optimization of Mechanical Interface for a Practical Micro-Reducer”, Proc. IEEE 13th Int. Symp. Micro Electro Mechanical Systems, pp. 170-175 (2000).4. Sandia National Laboratories, “Design Rules Design Rules”, Microelectronics Development Laboratory, Version 0.8, (2000)5. Krygowask, T. W., Sniegowask, J. J., Rodgers, M. S., Montague, S., and Allen, J. J., “Infrastructure, Technology and Applications of Micro-Electro-Mechanical Systems (MEMS)”, Sensor Expo 1999 (1999).6. Sniegowski, J. J., Miller, S. L., LaVigne, G. F., Rodgers, M. S., and McWhorter, P. J., “Monolithic G eared-Mechanisms Driven by aPolysilicon Surface-Micromachined On-Chip Electrostatic Microengine”, Solid-State Sensor and Actuator Workshop, pp. 178-182, (1996).7. Rogers, M. S., Sniegowski, S. S., Miller, S., and LaVigne, G. F., “Designing and OperatingE lectrostatically Driven Microengines”, Proceedings of the 44th International Instrumentation Symposium, Reno, NV, May 3-7, pp. 56-65 (1998).Figure 1. The schematic of the planetarygear mechanism generated from SUMMiT Vdesign layout softwareFigure 2. A schematic cross-section of the planetary gear system generated by SUMMiT-V technologyFigure 3. The comparison of reduction ratios as a function of the number of units采用表面微加工技术制造微型行星齿轮减速器摘要这篇文章论述了一种结构紧凑、传动比高的微型行星齿轮减速机构。
机械专业论文中英文

机械专业论文中英文Gearbox Noise —— Correlation with Transmission Error and Influence of Bearing Preload变速箱噪声——相关的传输错误和轴承预压的影响摘要ABSTRACTThe five appended papers all deal with gearbox noise and vibration. The first paper presents a review of previously published literature on gearbox noise and vibration.The second paper describes a test rig that was specially designed and built for noise testing of gears. Finite element analysis was used to predict the dynamic properties of the test rig, and experimental modal analysis of the gearbox housing was used to verify the theoretical predictions of natural frequencies.In the third paper, the influence of gear finishing method and gear deviations on gearbox noise is investigated in what is primarily an experimental study. Eleven test gear pairs were manufactured using three different finishing methods. Transmission error, which is considered to be an important excitation mechanism for gear noise, was measured as well as predicted. The test rig was used to measure gearbox noise and vibration for the different test gear pairs. The measured noise and vibration levels were compared with the predicted and measured transmission error. Most of the experimental results can be interpreted in terms of measured and predicted transmission error. However, it does not seem possible to identify one single parameter,such as measuredpeak-to-peak transmission error, that can be directly related to measured noise and vibration. The measurements also show that disassembly and reassembly of the gearbox with the same gear pair can change the levels of measured noise andvibration considerably.This finding indicates that other factors besides the gears affect gear noise.In the fourth paper, the influence of bearing endplay or preload on gearbox noise and vibration is investigated. Vibration measurements were carried out at torque levels of 140 Nm and 400Nm, with 0.15 mm and 0 mm bearing endplay, and with 0.15 mm bearing preload. The results show that the bearing endplay and preload influence the gearbox vibrations. With preloaded bearings, the vibrations increase at speeds over 2000 rpm and decrease at speeds below 2000 rpm, compared with bearings with endplay. Finite element simulations show the same tendencies as the measurements.The fifth paper describes how gearbox noise is reduced by optimizing the gear geometry for decreased transmission error. Robustness with respect to gear deviations and varying torque is considered in order to find a gear geometry giving low noise in an appropriate torque range despite deviations from the nominal geometry due to manufacturing tolerances. Static and dynamic transmission error, noise, and housing vibrations were measured. The correlation between dynamic transmission error, housing vibrations and noise was investigated in speed sweeps from 500 to 2500 rpm at constant torque. No correlation was found between dynamic transmission error and noise. Static loaded transmission error seems to be correlated with the ability of the gear pair to excite vibration in the gearbox dynamic system.论文描述了该试验台是专门设计和建造噪音齿轮测试。
机械的工作英文作文

机械的工作英文作文英文:As a mechanical engineer, my work involves designing, developing, and testing mechanical devices and systems. This can range from simple machines like gears and pulleys to complex systems like engines and robots. I work closely with other engineers and technicians to ensure that the products we create meet the needs of our clients and are safe and reliable.One of the most challenging aspects of my job is troubleshooting. When a machine or system isn't working properly, it's up to me to figure out what's causing the problem and come up with a solution. This often involves a lot of trial and error, as well as creative thinking and problem-solving skills.Another important part of my job is staying up-to-date with the latest technology and industry trends. This meansattending conferences and workshops, reading industry publications, and networking with other professionals in my field. By staying informed, I can ensure that the products I design and develop are cutting-edge and meet the needs of our clients.Overall, my job as a mechanical engineer is challenging but rewarding. I enjoy the problem-solving aspect of my work and the satisfaction of seeing a project through from conception to completion.中文:作为一名机械工程师,我的工作涉及设计、开发和测试机械设备和系统。
机械类英语作文

Thirdly, the career prospects for mechanical engineers are vast and diverse. Graduates have the opportunity to work in industries such as automotive, aerospace, energy, and manufacturing. They are involved in the design and development of products, machinery, and systems, as well as the optimization of existing technologies. The demand for mechanical engineers is expected to grow in the coming years, particularly in emerging fields such as renewable energy and biomedical engineering.
机械专业交际英语作文

机械专业交际英语作文English:Effective communication is essential in the field of mechanical engineering in order to ensure successful collaboration, accurate problem-solving, and clear conveyance of ideas. Communication plays a crucial role in working with team members, clients, and other stakeholders in various engineering projects. Engineers not only need to possess technical knowledge and skills but also the ability to effectively communicate with others in a clear and concise manner. This includes the ability to explain complex technical concepts, present ideas in meetings, write reports, and collaborate with colleagues. Good communication skills also help in building strong relationships with clients, understanding their needs, and providing efficient solutions to their problems. In addition, effective communication can help prevent misunderstandings, conflicts, and errors in engineering projects, ultimately resulting in successful outcomes. Therefore, developing strong communication skills is vital for mechanical engineers to excel in their field and contribute effectively to the industry.中文翻译:在机械工程领域,有效的沟通至关重要,以确保成功的合作,准确的问题解决,以及清晰的思想传达。
机械工程专业的作文英语
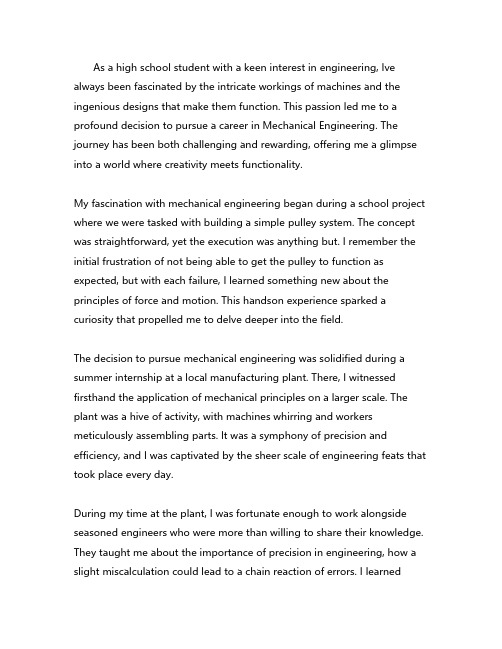
As a high school student with a keen interest in engineering, Ive always been fascinated by the intricate workings of machines and the ingenious designs that make them function. This passion led me to a profound decision to pursue a career in Mechanical Engineering. The journey has been both challenging and rewarding, offering me a glimpse into a world where creativity meets functionality.My fascination with mechanical engineering began during a school project where we were tasked with building a simple pulley system. The concept was straightforward, yet the execution was anything but. I remember the initial frustration of not being able to get the pulley to function as expected, but with each failure, I learned something new about the principles of force and motion. This handson experience sparked a curiosity that propelled me to delve deeper into the field.The decision to pursue mechanical engineering was solidified during a summer internship at a local manufacturing plant. There, I witnessed firsthand the application of mechanical principles on a larger scale. The plant was a hive of activity, with machines whirring and workers meticulously assembling parts. It was a symphony of precision and efficiency, and I was captivated by the sheer scale of engineering feats that took place every day.During my time at the plant, I was fortunate enough to work alongside seasoned engineers who were more than willing to share their knowledge. They taught me about the importance of precision in engineering, how a slight miscalculation could lead to a chain reaction of errors. I learnedabout the various components of a machine, from the smallest gear to the largest engine block, and how each played a crucial role in the overall function of the system.One of the most enlightening experiences was when I was given the opportunity to participate in the design of a new machine part. It was a humbling experience to see my ideas come to life, and the sense of accomplishment was indescribable. It was during this project that I realized the true potential of mechanical engineering the ability to create solutions that can improve lives and drive progress.As I progressed through my high school years, I began to explore the various subfields within mechanical engineering. I was particularly drawn to robotics and automation, intrigued by the potential to create machines that could perform tasks with a level of precision and efficiency beyond human capabilities. I spent countless hours researching, building, and programming robots, each project teaching me more about the complexities of mechanical systems and the importance of problemsolving skills.The journey towards a career in mechanical engineering has not been without its challenges. The coursework has been demanding, requiring a strong foundation in mathematics, physics, and computer science. Yet, the challenges have only served to strengthen my resolve. Ive learned to embrace the complexities of the field, to find joy in solving complex problems, and to appreciate the beauty of welldesigned machinery.Looking ahead, I am excited about the prospect of attending university and furthering my education in mechanical engineering. I am eager to explore new technologies, to learn from experts in the field, and to contribute to the advancement of mechanical engineering. Whether its designing more efficient engines, developing advanced robotics, or creating sustainable energy solutions, I am confident that a career in mechanical engineering will offer endless opportunities for growth and innovation.In conclusion, my journey towards mechanical engineering has been a testament to my passion for problemsolving and my love for the intricate world of machines. It has taught me the importance of perseverance, precision, and creativity, and has opened my eyes to the endless possibilities that await in this everevolving field. As I prepare to embark on the next chapter of my life, I am filled with anticipation and a deep sense of purpose, ready to contribute to the world of mechanical engineering and make a difference in the world.。
机械工程专业英语作文举例理由总结

机械工程专业英语作文举例理由总结全文共3篇示例,供读者参考篇1Mechanical engineering is a field of engineering that deals with the design, construction, and operation of machines and mechanical systems. It is a highly diverse and challenging field that requires a strong foundation in mathematics, physics, and materials science.One reason why I am interested in pursuing a career in mechanical engineering is because of the variety of job opportunities available in this field. Mechanical engineers are in high demand in a wide range of industries, including automotive, aerospace, energy, and manufacturing. This means that as a mechanical engineer, I would have the opportunity to work on a variety of projects and gain experience in different areas of engineering.Another reason why I am drawn to mechanical engineering is the opportunity to work on cutting-edge technology and innovation. Mechanical engineers are responsible for designing and developing new products and systems that can have asignificant impact on society. For example, mechanical engineers are involved in the development of renewable energy technologies, such as wind turbines and solar panels, which have the potential to reduce our dependence on fossil fuels and combat climate change.Furthermore, I am excited about the prospect of working in a field that is constantly evolving and pushing the boundaries of what is possible. As a mechanical engineer, I would have the opportunity to collaborate with experts in other fields, such as robotics, nanotechnology, and artificial intelligence, to develop new and innovative solutions to complex engineering challenges.In conclusion, I believe that pursuing a career in mechanical engineering would provide me with the opportunity to work on a wide range of exciting projects, contribute to important technological advancements, and make a positive impact on society. I am confident that my passion for mathematics and science, coupled with my strong problem-solving skills, will enable me to excel in this challenging and rewarding field.篇2Mechanical Engineering Professional English CompositionWith the rapid development of technology and industry, the demand for mechanical engineering professionals is increasing. As a result, it is essential for mechanical engineering students to master professional English writing skills in order to excel in their career. In this essay, I will provide examples, reasons, and conclusions to support this idea.Firstly, mastering professional English writing skills can help mechanical engineering students effectively communicate with colleagues, clients, and superiors. For instance, when preparing technical reports, project proposals, or presentation materials, clear and concise writing is crucial to convey complex engineering concepts and solutions. In addition, effective communication skills in English can facilitate collaboration with international partners and enhance the overall efficiency of engineering projects.Secondly, proficient English writing skills can broaden the career opportunities for mechanical engineering professionals. In today’s globalized economy, many engineering companies operate on an international scale, and multilingual engineers are highly sought after. By demonstrating strong English writing abilities, mechanical engineering students can stand out in jobapplications and interviews, and increase their chances of securing lucrative job offers both domestically and abroad.Furthermore, mastering professional English writing skills can enhance the professional reputation and credibility of mechanical engineering professionals. In academic settings, publishing research papers in reputable journals and presenting at international conferences are crucial for career advancement. By honing their English writing skills, mechanical engineering students can produce high-quality research papers and presentations that attract attention from fellow researchers and industry leaders, thereby establishing themselves as experts in their field.In conclusion, mastering professional English writing skills is essential for mechanical engineering students to succeed in their careers. By effectively communicating with colleagues, expanding career opportunities, and enhancing professional reputation, mechanical engineers can distinguish themselves as top performers in the industry. Therefore, I strongly recommend that mechanical engineering students prioritize the development of their English writing skills, as it will undoubtedly benefit their future professional growth and success.篇3Mechanical engineering is a fascinating field that involves the design, analysis, manufacturing, and maintenance of mechanical systems. As a mechanical engineering student, it is essential to have a good understanding of engineering principles and concepts in order to succeed in this challenging and dynamic field. In this essay, I will discuss the importance of learning and using English in the study of mechanical engineering, provide examples of how English is used in the field, and summarize the reasons why English proficiency is crucial for success in mechanical engineering.First and foremost, English is the universal language of communication in the field of mechanical engineering. Whether you are working on a project with colleagues from different countries or collaborating with clients from around the world, the ability to communicate effectively in English is key to ensuring successful outcomes. This is especially important in the era of globalization, where international collaboration and communication are becoming increasingly common in the engineering industry.For example, when working on a multinational project to design a new automobile engine, engineers from different countries need to be able to communicate effectively with oneanother in English in order to share ideas, coordinate tasks, and solve problems. Without a common language of communication, misunderstandings and mistakes can easily occur, leading to delays and cost overruns.Furthermore, technical documentation and research papers in the field of mechanical engineering are often written in English. To stay current with the latest advancements in the field and contribute to the body of knowledge, it is essential for mechanical engineering students to be able to read and understand technical literature in English. This includes research papers, textbooks, journals, and conference proceedings, which are all valuable sources of information for furthering one's understanding of mechanical engineering principles and applications.In addition, many multinational engineering companies require their employees to have a good command of English in order to work on international projects, attend conferences and seminars, and interact with clients and partners from different countries. By being proficient in English, mechanical engineers can expand their career opportunities and increase their competitiveness in the job market.In summary, English proficiency is crucial for success in the field of mechanical engineering due to its importance as a universal language of communication, its role in accessing technical literature, and its relevance in international collaboration and career advancement. By developing strong English language skills, mechanical engineering students can enhance their ability to communicate effectively, stay up-to-date with the latest advancements in the field, and take advantage of the many opportunities available in this dynamic and rewarding profession.。
- 1、下载文档前请自行甄别文档内容的完整性,平台不提供额外的编辑、内容补充、找答案等附加服务。
- 2、"仅部分预览"的文档,不可在线预览部分如存在完整性等问题,可反馈申请退款(可完整预览的文档不适用该条件!)。
- 3、如文档侵犯您的权益,请联系客服反馈,我们会尽快为您处理(人工客服工作时间:9:00-18:30)。
【最新整理,下载后即可编辑】《专业英语论文考核》专业年级机械电子141姓名韦继虎学号**********指导教师董文彬完成时间2017年6月10日Application and Development of Lightweight Material for AutomobileAbstractCar lightweight is an important means to achieve energy-saving emission reduction and methods, in improving the fuel economy and environmental protection has an important role. At present, the lightweight new material is the main way of the current body weight reduction, through the multi-material structure optimization, both to improve vehicle performance, but also significantly reduce the quality. This chapter discusses the performance and application of several lightweight materials, describes the development of lightweight materials in the automotive industry and the application of the trendKey words: automotive ;lightweight ;lightweight materialsPrefaceThe study of lightweight car is a mainstream of modern car design and manufacturing. Car lightweight, is to ensure the strength and safety of the car under the premise of the car as much as possible to reduce the quality of the preparation, thereby enhancing the vehicle's power, reduce fuel consumption and reduce exhaust pollution. Data show that if the car to reduce the quality of 10%, fuel efficiency can be increased by 6% to 8%, fuel consumption can be reduced by 6% to 10%. Fuel consumption decline, emissions also decreased, while resource utilization increased, extended life of the car, the use of performance has improved significantly. Car body quality accounts for about 50% of the quality of the vehicle, it is clear that the lightweight body for the vehicle lightweight play a pivotal role [1]. At present, the car body weight reduction has two main research directions: First, the use of lightweight materials; Second, optimize the structure. Structural optimization potential space has been very small, the gradual use of lightweight new materials is the current body of one of the main means of lightweight.1 New high strength steelIn recent years, with the progress of metallurgical technology, on the basis of high-strength steel, with ultra-low carbon as the basic characteristics, and gradually formed with deep drawing, high strength, baking hardening performance of new high-strength steel. At present, the use of high-strength automotive body is mainly sheet metal and pipe. Mainly: (1) BH steel (bake hardening steel). BH steel plate yield strength in the baking paint increased, without loss of formability under the premise of improving the anti-depression, can reduce the steel plate, mainly for high strength and difficult to form parts, such as roof, Doors, luggage and other components, the main use of tensile strength of 340 ~ 390MPa BH steel plate. (2) RIP steel (phase change induced plastic steel). Mainly used for the collision must absorb more energy when the high-strength structural parts, such as body frame. (3) MS steel (martensitic phase steel). Used to hit the high impact parts, that is, in a very short collision deformation stroke to absorb a lot of energy, such as side crash protection. (4) boron steel. Used to require high strength and high degree of molding of parts, can minimize the quality. Such as A, B column reinforcement, etc. [2].Practice has proved that when the thickness of the steel were reduced 0.05,0.10,0.15 mm, the body weight loss were 6%, 12%, 18%. In terms of development trends, the use of new high-strength steel plate in the body is constantly thinning, while the body strength has increased, while increasing the safety of the car, reducing noise and vibration, improve fuel efficiency and reduce the overall quality of the car. The cost did not increase, while the acceleration, driving performance has improved. Whether from the cost point of view, or from the performance point of view, the new high-strength steel plate is to meet the lightweight body to improve the safety of the collision of the best materials. The proportion of new high-strength steel plates used in various automobile factories is increasing. Japan's Mitsubishi Pajero (SPORT) for the company's latest SUV car designed a new body structure, body 70% of the components made of high-strength steel plate, the vehicle's torsional stiffness even higher than the Grand Cherokee 45% Body carrying capacity of up to 2t or more. Ford's Windstar body frame 60% is high strength steel. Toyota's new Vitz body structure in high-strength steel accounted for 48%, than the company's Starlet car to reduce the quality of 17kg.However, the high strength of the steel sheet is liable to cause a decrease in plasticity, a poor formability, and an increase in yieldstrength, which causes surface distortion and springback, and increases the shape's instability. Thus, high strength steel sheets are a difficult to form material. Thermoforming technology is a new type of high-strength stamping parts for the advanced manufacturing technology, can be used to form a strength of up to 1500MPa stamping parts, including the thermoforming process is stamping The frontier technology of the field can be widely used in the production of front and rear bumper, A-pillar, B-pillar, C-pillar, roof structure, door interior plate, door anti-collision beam and other components.2 light alloy material2.1 aluminum and aluminum alloyAluminum is the ideal choice for lightweight car, the resource is wide, lightweight, recycling, saving resources, absorbing impact energy, corrosion resistance, is the best overall performance of the basic material. The aluminum alloy used in the body is mainly deformed aluminum alloy, mainly AI-Cu-Mg system (2000 series), AI-Mg system (5000 series), AI-Mg-Si series (6000 series), AI-Mg- Zn-Cu system. Which 2000 series and 6000 series is heat treatment can strengthen the alloy, while the 5000 series is heat treatment can not strengthen thealloy. The former through the coating drying process after the strength is improved, mainly for the body outside the board and other emphasis on strength, stiffness of the site, such as car cover, hood, lift rear door, front fender, etc .; the latter excellent shape, Mainly used in the body plate and other complex parts of the shape, such as car floor structure and so on. At present, low density, high strength, high elastic modulus and superplasticity of the AI-Li alloy and aluminum anti-vibration plate, etc. has been gradually applied to the body.Aluminum alloy has good formability. Aluminum alloy body structure mainly used aluminum extrusion profiles as the main body of the space frame structure, generally with medium and strong aluminum can meet the requirements. Extrusion profiles are mainly hollow materials, in addition to light weight, high rigidity, high temperature strength, heat resistance, corrosion resistance is also very good, and can be welded, surface treatment and bending processing. The current aluminum body is made of thick-walled forged aluminum beams, and is more advantageous than stamping thin steel in terms of structural strength and stiffness, and the overall stability of the mechanism is better. Lightweight and high-strength aluminum body more solid than the traditional steel body, and do not worry about corrosion caused by the reduction of strength [3].From the aluminum panel application development trend, high strength, good forming processability, excellent surface quality aluminum plate will replace the steel plate as the main material of the car cover. The late 90s of the 20th century, there have been from the hood, fender and other parts of the body aluminum plate gradually developed into the body all the use of aluminum panels of the car, compared to steel plate by 40% to 50% of the results. Europe and the United States more developed aluminum industry, so Europe and the United States in the aluminum car to go ahead Europe and the United States and Japan in the automotive industry competition and its domestic energy and environmental legislation to promote the acceleration of the car lightweight (aluminum) pace. Germany Audi A8 sedan body are made of aluminum, the framework of three-dimensional frame structure, the cover for the aluminum stamping, was rated as one of the world's important scientific and technological achievements in 1994 one of the 100. This aluminum body compared with the steel body, the quality of 30% to 50%, fuel consumption reduced by 5% to 8%. Japan Honda's car body with aluminum alloy up to 162kg, steel body weight loss of about 40%. And China's aluminum production, prices, the comprehensive impact of the technical level of the automotive industry, making aluminum and itsalloys still can not be used in a large number of cars. Increase the variety, improve quality and reduce costs, has become China's aluminum processing industry and the automotive industry to the world's advanced level of development research。