晶圆代工厂决战新制程
浅谈晶圆代工厂制程节点和应用

浅谈晶圆代工厂制程节点和应用显示驱动芯片(DDIC)是显示面板制造中的一个关键部件。
通常,无晶圆厂IC设计公司(如联咏科技、奇景光电和LX Semicon)设计DDIC,在半导体晶圆代工厂中采用不同的制程节点(以微米[µm]或纳米[nm]为单位)制造IC芯片。
晶圆代工厂作为原始设备制造商(OEM)与IC公司合作,或为分包商制造关系。
之后,IC封装和测试公司完成DDIC的后道工序。
然后,DDIC被交付给显示面板厂商,将IC粘合在面板上,实现显示信号驱动功能。
DDIC通常以带载封装(TCP)形式包装和运输。
图1显示了LCD面板和DDIC之间的关系。
图1:LCD面板和DDICSource: ChipMos显示面板的分辨率通常以像素和子像素的形式出现。
例如,FHD面板意味着分辨率为1920×1080,而4K或超高清(UHD)面板意味着分辨率为3840×2160。
3840表示X轴,而2160表示Y轴。
3840×2160分辨率表示面板有3840×2160(8,294,400)个像素。
每个像素有三个子像素(红、绿、蓝)。
因此,面板总共有3840xRGBx2160(2490万)个子像素。
像素和子像素构成了分辨率。
DDIC的功能是驱动这些子像素的显示信号。
因此,分辨率和每颗DDIC的信道数(pin)决定了每片面板中DDIC的数量,而不一定由面板尺寸决定。
当涉及到DDIC规格时,面板的分辨率是最关键的因素。
在制造DDIC时,晶圆代工厂的制程节点是最关键的因素。
DDIC通过不同的粘合技术被粘合在面板边缘,如COG (chip-on-glass)和COF (chip-on-film)。
柔性OLED面板也采用COP (chip-on-plastic)方式,如图2所示。
图2:DDIC的COG、COF和COP粘合Source: Omdia由于分辨率是以X轴和Y轴形式出现的,所以有几种驱动IC:源极驱动芯片(Source driver IC):它驱动X轴上的信号,也被称为source端或column端。
中美科技实力对比:决战新一代信息技术
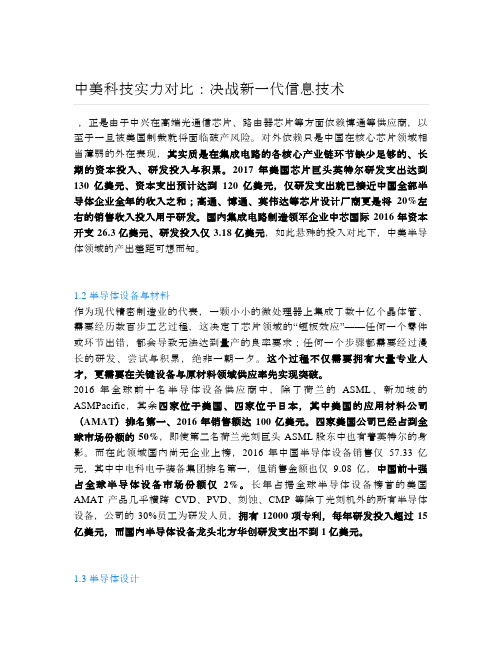
中美科技实力对比:决战新一代信息技术,正是由于中兴在高端光通信芯片、路由器芯片等方面依赖博通等供应商,以至于一旦被美国制裁就将面临破产风险。
对外依赖只是中国在核心芯片领域相当薄弱的外在表现,其实质是在集成电路的各核心产业链环节缺少足够的、长期的资本投入、研发投入与积累。
2017年美国芯片巨头英特尔研发支出达到130亿美元、资本支出预计达到120亿美元,仅研发支出就已接近中国全部半导体企业全年的收入之和;高通、博通、英伟达等芯片设计厂商更是将20%左右的销售收入投入用于研发。
国内集成电路制造领军企业中芯国际2016年资本开支26.3亿美元、研发投入仅3.18亿美元,如此悬殊的投入对比下,中美半导体领域的产出差距可想而知。
1.2半导体设备与材料作为现代精密制造业的代表,一颗小小的微处理器上集成了数十亿个晶体管、需要经历数百步工艺过程,这决定了芯片领域的“短板效应”——任何一个零件或环节出错,都会导致无法达到量产的良率要求;任何一个步骤都需要经过漫长的研发、尝试与积累,绝非一朝一夕。
这个过程不仅需要拥有大量专业人才,更需要在关键设备与原材料领域供应率先实现突破。
2016年全球前十名半导体设备供应商中,除了荷兰的ASML、新加坡的ASMPacific,其余四家位于美国、四家位于日本,其中美国的应用材料公司(AMAT)排名第一、2016年销售额达100亿美元。
四家美国公司已经占到全球市场份额的50%,即使第二名荷兰光刻巨头ASML股东中也有着英特尔的身影。
而在此领域国内尚无企业上榜,2016年中国半导体设备销售仅57.33亿元,其中中电科电子装备集团排名第一,但销售金额也仅9.08亿,中国前十强占全球半导体设备市场份额仅2%。
长年占据全球半导体设备榜首的美国AMAT产品几乎横跨CVD、PVD、刻蚀、CMP等除了光刻机外的所有半导体设备,公司的30%员工为研发人员,拥有12000项专利,每年研发投入超过15亿美元,而国内半导体设备龙头北方华创研发支出不到1亿美元。
半导体生产模式

半导体生产模式
半导体生产模式主要包括以下几种:
1. 晶圆代工模式:这是半导体行业中最常见的生产模式之一。
在这种模式下,半导体制造商(通常被称为晶圆代工厂)接受其他公司的设计订单,根据客户提供的设计规格和要求,使用自己的生产线和设备来生产芯片。
晶圆代工厂专注于芯片的制造工艺,而客户则负责芯片的设计和销售。
2. IDM 模式:IDM 代表 "Integrated Device Manufacturer",即集成器件制造商。
在这种模式下,公司同时进行芯片的设计、制造和销售。
IDM 公司拥有自己的晶圆制造厂和封装测试设施,能够实现从芯片设计到成品的整个生产流程。
3. 无晶圆厂模式:也被称为 Fabless 模式,它是指一些半导体公司专注于芯片的设计,但不拥有自己的晶圆制造厂。
这些公司将设计好的芯片交给晶圆代工厂进行生产,然后再进行封装和测试。
无晶圆厂模式的公司通常专注于特定领域的芯片设计,通过与多家晶圆代工厂合作来实现生产。
4. 系统集成模式:在这种模式下,公司将半导体芯片与其他组件(如电路板、传感器等)集成在一起,形成一个完整的系统或产品。
这种模式通常涉及到系统设计、硬件和软件开发等多个方面。
5. 合作生产模式:有时候,半导体公司之间会进行合作生产。
这种模式可以是共同开发新技术、共享生产设施或合作进行特定项目的生产。
这些生产模式在半导体行业中各有优劣,不同的公司根据自身的资源、能力和战略选择适合的生产模式。
随着技术的发展和市场需求的变化,生产模式也在不断演变和创新。
晶圆代工厂工艺制作分类

晶圆代工厂工艺制作分类
晶圆代工厂工艺制作分类主要包括晶圆处理工序、晶圆针测工序和构装工序。
1. 晶圆处理工序:主要工作是在晶圆上制作电路及电子元件(如晶体管、电容、逻辑开关等),其处理程序通常与产品种类和所使用的技术有关,但一般基本步骤是先将晶圆适当清洗,再在其表面进行氧化及化学气相沉积,然后进行涂膜、曝光、显影、蚀刻、离子植入、金属溅镀等反复步骤,最终在晶圆上完成数层电路及元件加工与制作。
2. 晶圆针测工序:经过上道工序后,晶圆上就形成了一个个的小格,即晶粒。
一般情况下,为便于测试,提高效率,同一片晶圆上制作同一品种、规格的产品;但也可根据需要制作几种不同品种、规格的产品。
3. 构装工序:将单个的晶粒固定在塑胶或陶瓷制的芯片基座上,并把晶粒上蚀刻出的一些引接线端与基座底部伸出的插脚连接,以作为与外界电路板连接之用,最后盖上塑胶盖板,用胶水封死。
其目的是用以保护晶粒避免受到机械刮伤或高温破坏。
此外,根据厂商类型,晶圆加工又可分为IDM和Foundry模式。
IDM 属于重资产模式,为IC设计—IC制造—IC封测一体化垂直整合,主要企业为三星等。
而Foundry模式厂商相较IDM仅具备IC制造和封测能力,剥
离了设计业务。
晶圆专业代工厂商降低了IC产业的进入门槛,激发了上游
IC设计厂商的爆发,以及产品设计和应用的创新,继而加速了IC产品的开
发应用周期,拓展了下游IC产品应用。
以上信息仅供参考,如需了解更多信息,建议查阅相关书籍或咨询专业人士。
晶圆代工厂开发流程 -回复
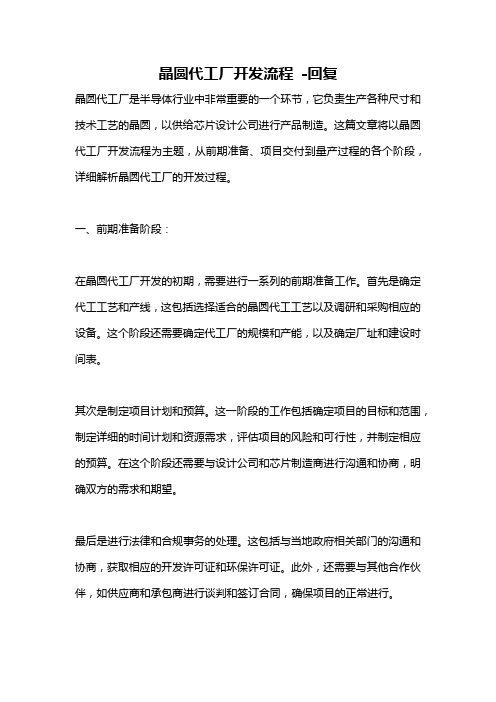
晶圆代工厂开发流程-回复晶圆代工厂是半导体行业中非常重要的一个环节,它负责生产各种尺寸和技术工艺的晶圆,以供给芯片设计公司进行产品制造。
这篇文章将以晶圆代工厂开发流程为主题,从前期准备、项目交付到量产过程的各个阶段,详细解析晶圆代工厂的开发过程。
一、前期准备阶段:在晶圆代工厂开发的初期,需要进行一系列的前期准备工作。
首先是确定代工工艺和产线,这包括选择适合的晶圆代工工艺以及调研和采购相应的设备。
这个阶段还需要确定代工厂的规模和产能,以及确定厂址和建设时间表。
其次是制定项目计划和预算。
这一阶段的工作包括确定项目的目标和范围,制定详细的时间计划和资源需求,评估项目的风险和可行性,并制定相应的预算。
在这个阶段还需要与设计公司和芯片制造商进行沟通和协商,明确双方的需求和期望。
最后是进行法律和合规事务的处理。
这包括与当地政府相关部门的沟通和协商,获取相应的开发许可证和环保许可证。
此外,还需要与其他合作伙伴,如供应商和承包商进行谈判和签订合同,确保项目的正常进行。
二、项目交付阶段:在前期准备阶段完成后,进入项目交付阶段。
这个阶段的工作包括以下几个步骤:1. 装修和设备安装:根据前期准备阶段的规划和设计,进行厂房的装修和设备的安装。
这包括调试设备,确保其正常运行,以及进行相应的培训和测试。
2. 材料和供应链管理:建立一个有效的材料和供应链管理系统,确保原材料的及时供应和库存的控制。
这涉及到与供货商的协商和合作,以及制定相应的采购计划和品质管理措施。
3. 测试和验证:在设备安装完成后,需要进行各种测试和验证工作,以确保工艺和产线的稳定性和可靠性。
这包括设备的性能验证,工艺的品质控制,以及制定相关的测试方案和指标。
4. 培训和人员招聘:进行相关的培训计划,并招聘和培养相应的人员。
这涉及到与培训机构和教育机构的合作,以及制定培训计划和考核机制。
5. 质量体系建立:制定和建立一套完善的质量管理体系,包括质量控制和质量保证的相关流程和制度。
mems晶圆生产工艺流程
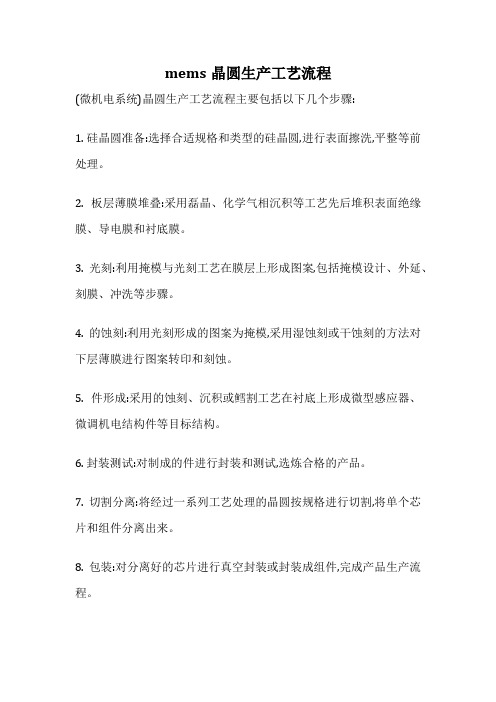
mems晶圆生产工艺流程
(微机电系统)晶圆生产工艺流程主要包括以下几个步骤:
1. 硅晶圆准备:选择合适规格和类型的硅晶圆,进行表面擦洗,平整等前处理。
2. 板层薄膜堆叠:采用磊晶、化学气相沉积等工艺先后堆积表面绝缘膜、导电膜和衬底膜。
3. 光刻:利用掩模与光刻工艺在膜层上形成图案,包括掩模设计、外延、刻膜、冲洗等步骤。
4. 的蚀刻:利用光刻形成的图案为掩模,采用湿蚀刻或干蚀刻的方法对下层薄膜进行图案转印和刻蚀。
5. 件形成:采用的蚀刻、沉积或鳕割工艺在衬底上形成微型感应器、微调机电结构件等目标结构。
6. 封装测试:对制成的件进行封装和测试,选炼合格的产品。
7. 切割分离:将经过一系列工艺处理的晶圆按规格进行切割,将单个芯片和组件分离出来。
8. 包装:对分离好的芯片进行真空封装或封装成组件,完成产品生产流程。
晶圆代工发展历程

晶圆代工发展历程一、技术发展晶圆代工的技术发展历程可以说是其成功的关键。
自晶圆代工诞生以来,技术进步一直是推动产业发展的核心动力。
晶圆代工的技术发展可以分为以下几个阶段:1.早期阶段:在这个阶段,晶圆代工的技术主要集中在制造小规模、低复杂度的集成电路。
工艺技术以薄膜制备、光刻和刻蚀为主,设备较为简单。
2.成熟阶段:随着技术的进步,晶圆代工开始能够制造大规模、高集成度的集成电路。
这期间,技术发展主要体现在工艺控制、良品率提升以及新型材料的开发等方面。
3.先进阶段:在这个阶段,晶圆代工的技术重点转向了纳米级工艺的研发,如14nm,7nm等。
此外,还涉及到高级封装技术、异质整合技术等多元化领域,以满足不断增长的性能需求。
二、产业转移随着技术的进步和市场的变化,晶圆代工的产业布局也经历了多次转移。
最初的晶圆代工主要集中在美国和欧洲,但随着技术的进步和市场的变化,产业开始向日本和韩国转移。
近年来,随着中国市场的崛起,晶圆代工产业又出现向中国大陆转移的趋势。
这种产业转移不仅推动了技术进步,也带动了地区经济的发展。
三、专业化分工晶圆代工的发展历程中,专业化分工的趋势日益明显。
在过去,集成电路的制造往往由整机制造商自己完成,但随着技术的复杂性和生产规模的扩大,整机制造商开始将制造环节外包给专业的晶圆代工厂。
这种专业化分工有助于提高生产效率和降低成本,同时也促进了晶圆代工产业的快速发展。
四、产能扩张随着技术的发展和市场需求的增长,晶圆代工厂的产能也在不断扩张。
早期的晶圆代工厂规模较小,但随着技术的进步和市场的扩大,晶圆代工厂的产能不断攀升。
此外,为了满足市场对高性能集成电路的需求,晶圆代工厂还不断投入资金进行设备升级和产能扩张。
这种产能扩张不仅提高了生产效率,也使得晶圆代工厂能够更好地应对市场变化和满足客户需求。
五、竞争格局晶圆代工产业的竞争格局在不断变化中。
早期的市场竞争主要集中在几个大型的晶圆代工厂,但随着技术的进步和市场的发展,越来越多的新进入者开始进入这个领域。
晶圆代工发展历程

晶圆代工发展历程晶圆代工是指半导体企业将设计好的芯片制作工艺交由专业晶圆代工厂来生产。
晶圆代工能够节约企业的研发和生产成本,提高生产效率,同时也可以让企业更加专注于芯片设计和市场销售,因此在半导体产业中发挥着重要作用。
晶圆代工的发展历程是一个充满挑战和竞争的过程,以下将对其发展历程进行详细描述。
一、2000年前的晶圆代工起步阶段20世纪90年代后期至21世纪初,随着信息技术行业的迅速发展,全球半导体市场迎来了快速增长期。
半导体制造技术的进步加速了芯片制程的密度提升和成本降低,这使得晶圆代工这一商业模式在半导体产业中崭露头角。
当时,台积电、格罗方德等代工厂逐渐崭露头角,开始为世界各地的芯片设计公司提供制程服务。
二、2000年至2010年,晶圆代工迅速崛起随着全球半导体市场的持续扩张和技术的日新月异,晶圆代工行业迎来了快速发展的黄金十年。
全球范围内新兴的半导体企业增多,而这些企业往往缺乏自己的生产设备和制程技术,因此更加依赖于晶圆代工厂。
作为技术提供商的代工厂也在这一时期不断创新,推动了制程工艺的进步和生产效率的提高,满足了市场对各种芯片产品的需求。
三、2010年至今,晶圆代工迈入高端制程时代随着移动互联网、人工智能、物联网等新兴技术的迅猛发展,对芯片性能和功耗的要求也日益提高。
在这样的大背景下,晶圆代工更加注重技术创新和高端制程的提升。
全球范围内的晶圆代工巨头纷纷加大投资,引入先进的制程设备和技术,致力于为客户提供更加先进、高性能的芯片制程。
为了满足芯片市场多元化和个性化的需求,晶圆代工厂也加强与客户的合作,提供差异化的定制服务,满足客户不同领域、不同应用的需求。
在这一历程中,晶圆代工行业从最初的起步阶段,到快速崛起,再到进入高端制程时代,不断迎来新的发展机遇和挑战。
随着技术的不断革新和市场需求的提升,晶圆代工必将继续发挥着重要作用,推动着半导体产业的进步和发展。
- 1、下载文档前请自行甄别文档内容的完整性,平台不提供额外的编辑、内容补充、找答案等附加服务。
- 2、"仅部分预览"的文档,不可在线预览部分如存在完整性等问题,可反馈申请退款(可完整预览的文档不适用该条件!)。
- 3、如文档侵犯您的权益,请联系客服反馈,我们会尽快为您处理(人工客服工作时间:9:00-18:30)。
晶圆代工厂决战新制程
晶圆代工厂决战新制程
日本强震虽震出半导体供应链疑虑,但包括台积电、联电、全球晶圆(Globalfoundries)及三星等晶圆代工厂均不畏局势逆转,重申不下修今年资本支出,要在先进的28纳米制程做激烈决战。
市调机构Gartner统计,今年全球晶圆代工厂总资本支出,将达到187亿美元,其中台积电资本支出就高达78亿美元,占总资本支出近42%,仍是晶圆代工厂中投资手笔最大。
全球晶圆为追赶台积电,今年资本支出也高达四、五十亿美元,投资手笔也相当大;联电今年资本支出也上调到18亿美元;连南韩三星也加速抢夺全球晶圆代工大饼的行列。
Gartner表示,今年各家资本支出大多投注在先进制程40纳米和28纳米制程,尤其台积电已宣布28纳米先进制程要提早在今年第三季投片,预定第四季产出,更让其它竞争者加速脚步。
Gartner科技与服务供货商研究总监王端分析,由于28纳米导入先进的高介电常数/金属闸极(HKMG)材料的先进制程技术,更能解决微处理器、绘图芯片、基频、射频、影像感测等高阶芯片的漏电问题,且达到体积更小、容量更大的要求,预料将吸引更多的芯片大厂投片兴趣。
王端强调,目前包括全球晶圆、三星等晶圆代工厂似乎已不让台积电在28纳米制程代工服务专美于前,坚持要在今年底完成28纳米制程量产;联电也宣布28纳米制程预定明年量产。
王端分析,28纳米制程将是全球晶圆代工版块的关键分野;由于依摩尔定律,28纳米后的下世代20或14纳米,将遭遇很大的困难,全球晶圆和三星可能在28纳米制程赶上台积电,未来晶圆代工的竞争将愈趋激烈。