复合材料RTM模具的制备
碳纤维增强复合材料hp-rtm成型工艺及孔隙控制研究

碳纤维增强复合材料hp-rtm成型工艺及孔隙控制研究碳纤维增强复合材料(CFRP)是一种具有优异性能的材料,被广泛应用于航空航天、汽车制造、船舶制造和体育器材等领域。
其中,HP-RTM(High-Pressure Resin Transfer Molding,高压树脂转移成型)是一种常用的CFRP成型工艺。
本文将对HP-RTM工艺及孔隙控制进行研究。
HP-RTM工艺属于封闭式模具成型方法,其中包括母模、子模和螺旋开关等。
首先,在模具中布置纤维预浸料和加热元件,然后将两个模具合拢,经过压力施加和树脂注射,使树脂充分浸润纤维,并且通过加热元件进行硬化。
最后,将模具分开,取出成型件。
HP-RTM工艺具有以下优点:1.成型速度快。
树脂注射压力高,注射时间短,加热硬化时间也短,可以提高生产效率。
2.成型件的质量稳定。
由于高压注射,树脂能够充分浸润纤维,可以获得性能均匀一致的成型件。
3.可以生产复杂结构的零件。
HP-RTM工艺适用于生产具有复杂几何形状的零件,如整体翼板和车身结构。
HP-RTM工艺也存在一些问题,其中最重要的是控制成型过程中的孔隙问题。
孔隙是指CFRP制品中的小空洞或气泡,会降低成型件的强度和耐久性。
孔隙的形成主要有两个方面的原因,一是树脂注射过程中的气体积聚,二是纤维预浸料中的气体气泡。
为了解决孔隙问题,可以采取以下措施:1.控制树脂注射过程。
增加注射压力和注射速度可以减少气体积聚,同时在注射前进行真空处理也是有效的手段。
2.优化纤维预浸料的制备工艺。
提高纤维预浸料的浸润性和挤出性可以降低气泡的生成。
3.采用树酯成型树脂(Resin Transfer Molding,RTM)前驱体。
RTM前驱体在注射过程中可以释放出溶剂,减少气泡的形成。
4.模具结构的优化设计。
增加模具表面的喷嘴和逃孔,提高树脂的流动性,减少气体积聚的产生。
在实际应用中,HP-RTM成型工艺及孔隙控制研究还需要进一步探索和完善,特别是对孔隙形成机理的深入研究和优化控制方法的开发。
碳纤维增强复合材料hp-rtm成型工艺及孔隙控制研究

碳纤维增强复合材料(CFRP)是一种结构轻、强度高的先进材料,广泛应用于航空航天、汽车、体育器材等领域。
其中,HP-RTM (高压快速反应注射成型)是一种常用的CFRP复合材料成型工艺,它可以实现高质量、高效率的制造,并具有良好的孔隙控制能力。
HP-RTM成型工艺的基本步骤如下:1.模具准备:首先,准备一个具有所需形状和尺寸的模具,通常使用金属材料制作。
模具表面需要经过处理以提高表面平整度和表面润滑性,以便于后续注塑过程。
2.预制准备:根据需要,预先制备好所需的干预产物,即CFRP的纤维布和树脂浸润材料。
纤维布通常采用碳纤维预浸料,其中已经预先浸渍了树脂。
此外,还可以在纤维布上涂覆树脂胶粘剂以实现更好的树脂流动性和浸润性能。
3.注塑过程:将预制准备好的纤维布放置在模具的合适位置,然后将模具封闭。
接下来,通过高压注塑机将树脂推入模具内,使其浸润纤维布。
注塑过程中,高压和高温有利于树脂的流动和浸润性能提高。
4.固化过程:完成树脂注塑后,模具中的复合材料需要经过固化过程。
这一步主要是通过控制温度和时间来使树脂完全固化。
通常,温度较高且持续一定时间可以确保固化反应的充分进行。
在HP-RTM成型过程中,孔隙控制是一个关键的技术难题。
孔隙是指复合材料中的气体或液体空隙,对材料的强度和可靠性有不良影响。
为了控制孔隙的生成,研究人员采取了以下措施:1.注塑条件优化:通过调整注塑过程中的参数,如注塑温度、压力和时间,以提高树脂的浸润性能和流动性,减少气体捕获和孔隙形成。
2.模具设计和表面处理:合理设计模具结构,使得树脂在注塑过程中能够均匀分布并填充纤维布,减少树脂注塑过程中的空隙和气体捕获。
同时,模具表面的润滑处理可以减少树脂在模具表面的附着,并更好地填充纤维布。
3.树脂配方优化:通过调整树脂配方和添加剂,改善树脂的流动性和抗气泡性能,减少孔隙的生成。
常见的方法包括添加表面活性剂和消泡剂。
4.气体抽真空处理:在注塑过程中,通过在模具中抽真空来减少气体的含量,并帮助树脂充分浸润纤维布,减少孔隙的产生。
RTM树脂传递模塑料成型工艺经典实用
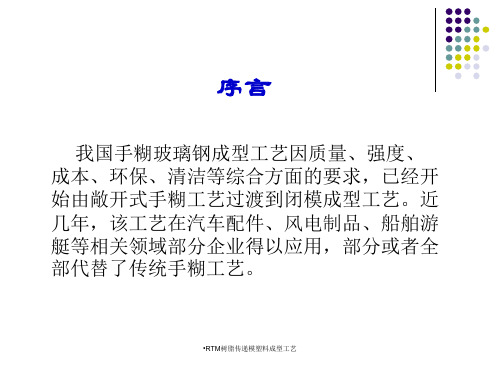
我国手糊玻璃钢成型工艺因质量、强度、 成本、环保、清洁等综合方面的要求,已经开 始由敞开式手糊工艺过渡到闭模成型工艺。近 几年,该工艺在汽车配件、风电制品、船舶游 艇等相关领域部分企业得以应用,部分或者全 部代替了传统手糊工艺。
•RTM树脂传递模塑料成型工艺
模具的工装夹具设计
在RTM模具中限位销是控制产品的厚度和上下模吻合
•RTM树脂传递模塑料成型工艺
•RTM树脂传递模塑料成型工艺
谢谢!
•RTM树脂传递模塑料成型工艺
铰链式搭扣合模
铰链 搭扣紧固
•RTM树脂传递模塑料成型工艺
铰链
油缸举升上模, 并限位
注胶口和排气口的位置
1、中心注入 2、四周注入 四周浇注可以比中心浇注充模时间减少60%以上,孔隙率可 以比之降低25%以上,同时也能提高一定的力学性能。 另外还有真空辅助和充模时间的控制。
•RTM树脂传递模塑料成型工艺
上下模完全靠螺栓锁 紧至上下定位销完全吻合
定位销完全吻合
•RTM树脂传递模塑料成型工艺
RTM-注射
注射压力小便于树脂流动注射压 力高便于气体的排出。 注射温度和树脂的黏度
注射温度低和树脂黏度低便于树 脂的流动。 注射压力低注射温度可以高点
•RTM树脂传递模塑料成型工艺
RTM-固化
固化过程:凝胶阶段、定型阶段(硬化阶段)、熟化阶段(完 全固化阶段) 固化控制:通过调控树脂胶液中的固化剂含量和固化温度来控 制固化度
•RTM树脂传递模塑料成型工艺
胶衣准备
铺层
合模
模具 准备
脱模
固化
树脂 注射
后处理
检验
制品
RTM成型工艺流程图
•RTM树脂传递模塑料成型工艺
rtm工艺技术
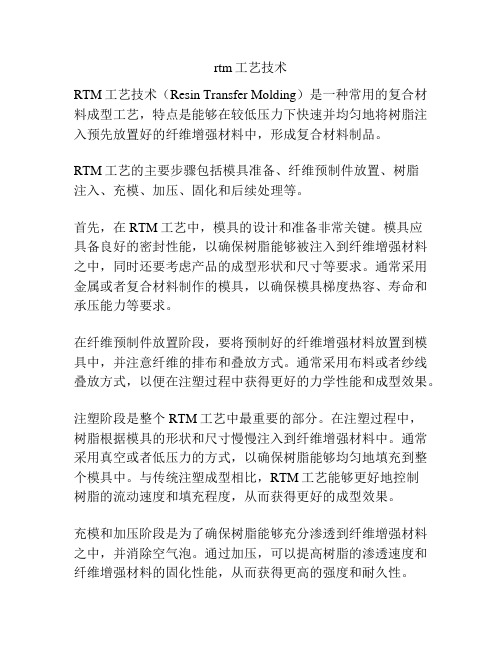
rtm工艺技术RTM工艺技术(Resin Transfer Molding)是一种常用的复合材料成型工艺,特点是能够在较低压力下快速并均匀地将树脂注入预先放置好的纤维增强材料中,形成复合材料制品。
RTM工艺的主要步骤包括模具准备、纤维预制件放置、树脂注入、充模、加压、固化和后续处理等。
首先,在RTM工艺中,模具的设计和准备非常关键。
模具应具备良好的密封性能,以确保树脂能够被注入到纤维增强材料之中,同时还要考虑产品的成型形状和尺寸等要求。
通常采用金属或者复合材料制作的模具,以确保模具梯度热容、寿命和承压能力等要求。
在纤维预制件放置阶段,要将预制好的纤维增强材料放置到模具中,并注意纤维的排布和叠放方式。
通常采用布料或者纱线叠放方式,以便在注塑过程中获得更好的力学性能和成型效果。
注塑阶段是整个RTM工艺中最重要的部分。
在注塑过程中,树脂根据模具的形状和尺寸慢慢注入到纤维增强材料中。
通常采用真空或者低压力的方式,以确保树脂能够均匀地填充到整个模具中。
与传统注塑成型相比,RTM工艺能够更好地控制树脂的流动速度和填充程度,从而获得更好的成型效果。
充模和加压阶段是为了确保树脂能够充分渗透到纤维增强材料之中,并消除空气泡。
通过加压,可以提高树脂的渗透速度和纤维增强材料的固化性能,从而获得更高的强度和耐久性。
固化阶段是将树脂完全固化,使纤维增强材料和树脂成为一个整体。
通常采用热固化或者光固化的方式,通过加热或者紫外线照射等方法,使树脂固化并与纤维增强材料牢固地结合在一起。
固化后的制品具有较高的强度、刚度和耐腐蚀性能,适用于各种工程应用。
最后,进行后续处理,如切割、修整、表面处理和涂装等,以获得符合要求的最终产品。
总之,RTM工艺技术是一种先进的复合材料成型工艺,具有成型效果好、成本低、产量高的优点。
通过合理选择纤维增强材料和树脂、优化模具设计、精确控制注塑和固化参数等,可以生产出符合要求的复合材料制品。
随着科学技术的不断发展,RTM工艺技术也将在航空航天、汽车工业、建筑业和体育用品等领域得到广泛应用。
RTM-模压工艺制备厚截面复合材料研究

目录摘要 (i)第一章绪论 (1)1.1 树脂传递模塑工艺(RTM)及其衍生工艺概述 (1)1.1.1树脂传递模塑工艺 (2)1.1.2 软模辅助RTM工艺 (3)1.1.3 真空辅助RTM工艺(VARTM) (4)1.1.4 高压RTM工艺(HP-RTM) (5)1.2 RTM-模压工艺及其研究进展 (6)1.2.1 RTM-模压工艺基本原理及特点 (7)1.2.2 RTM-模压工艺国内外研究现状 (7)1.2.3 RTM-模压工艺的关键工艺参数及其影响 (8)1.3 本文选题依据及研究内容 (10)第二章RTM-模压工艺制备厚截面复合材料试验方案设计及试样制备 (12)2.1 主要实验材料与仪器设备 (12)2.1.1树脂体系的选择 (12)2.1.2增强材料的选择 (13)2.1.3主要实验仪器设备 (15)2.2 正交试验方案设计 (15)2.3 RTM-模压工艺制备厚截面复合材料的工艺流程 (16)2.4 复合材料性能测试与表征方法 (18)第三章RTM-模压工艺用模具分析及设计 (22)3.1 RTM-模压模具设计方案 (22)3.2 RTM-模压工艺用模具的基本性能要求及设计方案 (23)3.2.1 RTM-模压工艺用模具的基本性能要求 (23)3.2.2 模具材料的选择 (23)3.2.3 模具结构的设计 (25)3.3 RTM-模压工艺模具受力分析及尺寸确定 (29)3.4模具加工与检测 (33)3.5本章小结 (36)第四章RTM-模压工艺制备厚截面复合材料性能分析 (38)4.1 正交试验分析及参数优化 (38)4.1.2结果分析与参数优化 (38)4.2RTM-模压工艺制备厚截面复合材料力学性能分析 (43)4.2.1制备异形厚截面复合材料 (43)4.2.2厚截面复合材料的弯曲性能 (44)4.2.3 厚截面复合材料的压缩性能 (46)4.2.4厚截面复合材料的层间剪切强度 (48)4.3RTM-模压工艺制备厚截面制品孔隙率计算与分析 (50)4.3.1复合材料的孔隙率计算 (50)4.3.2RTM-模压工艺制备复合材料的孔隙率分析 (51)4.3.3小结 (52)4.4RTM-模压工艺制备厚截面制品断面形貌分析 (52)4.4.1厚截面复合材料横截面的SEM分析 (52)4.4.2厚截面复合材料弯曲破坏断裂面的SEM分析 (53)4.4.3厚截面复合材料压缩破坏断裂面的SEM分析 (55)4.4.4厚截面复合材料层间剪切破坏断裂面的SEM分析 (56)4.5本章小结 (57)第五章结论与展望 (59)5.1全文总结 (59)5.2 研究展望 (60)致谢 (61)参考文献 (63)作者在学期间取得的学术成果 (68)表2.1 实验所采用的树脂体系 (12)表2.2 树脂体系室温(25℃)的基本性能参数 (13)表2.3 常用玻璃纤维的性能[62] (14)表2.4 实验中E玻纤主要性能参数 (15)表2.5 实验设备 (15)表2.6 试验因素及水平 (16)表2.7 正交表 (16)表3.1 常见模具材料的特点 (24)表3.2 常见模具材料的适用范围 (24)表3.3 45号钢常温下的基本性能 (25)表3.4 模具材料的基本性能 (33)表4.1 正交试验结果 (38)表4.2 试样的弯曲强度和弯曲模量 (45)表4.3 试样的压缩强度和压缩模量 (47)表4.4 试样的层间剪切强度 (49)表4.5 主要测试数据 (50)表4.6 试样的孔隙率 (51)图1.1 RTM工艺流程简图 (2)图1.2 软模辅助RTM工艺原理示意图 (4)图1.3 VARTM工艺原理示意图 (5)图1.4 VIMP工艺原理示意图 (5)图1.5 HP-RTM原理示意图 (6)图1.6 RTM-模压工艺原理示意图 (7)图2.1 环氧EP CYD-128/70#酸酐60℃时的粘度-时间特性曲线 (13)图2.2 环氧EP CYD-128/70#酸酐80℃时的粘度-时间特性曲线 (13)图2.3 斜纹布及其示意图 (14)图2.4 RTM-模压工艺工艺的基本流程 (16)图2.5 经过处理的RTM-模压平板模具 (17)图2.6 纤维增强体的铺放 (17)图2.7 定位螺杆 (17)图2.8 热电偶位置示意图 (18)图2.9 试验采用的固化制度 (18)图2.10 复合材料层间剪切力试样的形状及尺寸 (20)图2.11 排水法测量密度装置 (20)图3.1 常见RTM-模压模具设计方案 (23)图3.2 平板构件模具的流道设计 (26)图3.3 异形构件模具进胶口、出胶口及流道设计 (26)图3.4 压缩密封原理图 (27)图3.5 活塞系统结构图 (28)图3.6 两种密封方式示意图 (28)图3.7 限位方式示意图 (29)图3.8 阳模受力位置 (30)图3.9 网格划分及阳模位移云图 (31)图3.10 网格划分及阴模位移云图 (32)图3.11 异形模具剖面图 (33)图3.12 平板构件模具的主要尺寸 (34)图3.13 异形构件模具的主要尺寸 (35)图3.14 平板构件模具实物图 (36)图3.15 异形模具实物图 (36)图4.2 因素和参数对试样压缩性能的影响权重和影响情况 (39)图4.3 因素和参数对试样剪切性能的影响权重和影响情况 (40)图4.4 因素和参数对试样孔隙率的影响权重和影响情况 (40)图4.5 不同参数对复合材料性能的影响 (42)图4.6 不同参数组合下四种性能的比较 (43)图4.7 异形构件 (44)图4.8 厚截面复合材料板弯曲性能测试及破坏试样 (45)图4.9 不同平面RTM-模压试样的弯曲强度和弯曲模量变化曲线 (46)图4.10 厚截面复合材料板压缩性能测试及破坏试样 (47)图4.11 不同平面RTM-模压试样的弯曲强度和弯曲模量变化曲线 (48)图4.12 厚截面复合材料板弯曲性能测试及破坏试样 (49)图4.13 不同平面RTM-模压试样的层间剪切强度变化曲线 (50)图4.14 两种工艺试样孔隙率的比较 (51)图4.15 不同平面试样孔隙率变化曲线 (51)图4.16 试样的截面扫描电镜图 (53)图4.17 试样上下弯曲破坏断裂面扫描电镜图 (55)图4.18 试样压缩破坏断裂面扫描电镜图 (56)图4.19 试样剪切破坏断裂面扫描电镜图 (57)摘要采用传统RTM及其衍生工艺制备的复合材料制品的纤维体积分数较低(一般为40%),孔隙率难以有效降低,限制了复合材料性能的充分发挥和工艺的推广应用,尤其难以应用于制备高纤维体积分数的厚截面复合材料主承力结构件。
复合材料液体成型分类

复合材料液体成型分类
复合材料液体成型是一种制备复合材料的方法,液体成型可以
根据不同的工艺和原理进行分类。
主要的液体成型方法包括压模注
射成型(RTM)、真空辅助树脂浸渍成型(VARTM)、压模挤出成型(RTM)等。
首先,压模注射成型(RTM)是一种常见的液体成型方法,其工
艺流程是将预先切割好的纤维预形状放置在模具中,然后通过模具
封闭,注入树脂,树脂充满整个模具,最后经过固化,得到成型件。
其次,真空辅助树脂浸渍成型(VARTM)是一种利用真空辅助进
行树脂浸渍的液体成型方法,其工艺流程是在放置纤维预形状后,
利用真空将模具内的空气抽出,然后注入树脂,树脂在真空作用下
充满整个模具,最后经过固化,得到成型件。
此外,压模挤出成型(RTM)是一种将纤维和树脂预浸料放置在
模具中,然后通过挤出机将材料挤出,经过模具成型,最后经过固化,得到成型件。
除了上述三种常见的液体成型方法外,还有其他液体成型方法,
如真空压力成型(VIP)、真空注射成型(VIM)等,它们都是根据不同的工艺和原理进行分类的。
总的来说,液体成型方法是一种制备复合材料的重要工艺,不同的液体成型方法在工艺流程、成型效果和适用范围等方面有所不同,可以根据具体的需求选择合适的液体成型方法。
复合材料stm成型工艺流程
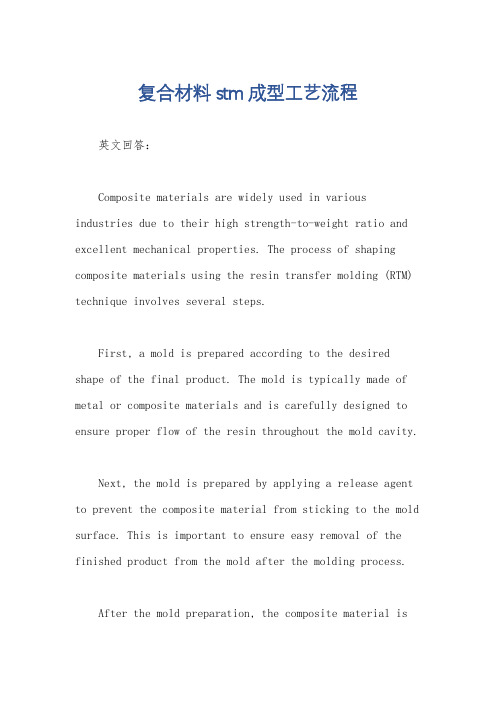
复合材料stm成型工艺流程英文回答:Composite materials are widely used in various industries due to their high strength-to-weight ratio and excellent mechanical properties. The process of shaping composite materials using the resin transfer molding (RTM) technique involves several steps.First, a mold is prepared according to the desired shape of the final product. The mold is typically made of metal or composite materials and is carefully designed to ensure proper flow of the resin throughout the mold cavity.Next, the mold is prepared by applying a release agent to prevent the composite material from sticking to the mold surface. This is important to ensure easy removal of the finished product from the mold after the molding process.After the mold preparation, the composite material isprepared. This usually involves the impregnation of reinforcing fibers with a resin matrix. The fibers can be made of carbon, glass, or aramid, depending on the specific requirements of the application. The resin matrix can be epoxy, polyester, or other compatible materials.Once the composite material is ready, it is placed into the mold cavity. The mold is then closed and clamped to ensure a tight seal. The next step is the injection of the resin into the mold cavity. This can be done under pressure to ensure proper impregnation of the fibers and to minimize voids in the final product.After the resin injection, the mold is kept under pressure and at an elevated temperature to facilitate the curing of the resin. This is known as the curing or consolidation stage. The curing process can take several hours or even days, depending on the specific resin system used.Once the resin has cured, the mold is opened, and the finished product is removed. The excess flash or trim isthen removed, and any necessary finishing operations, such as sanding or painting, are carried out.In summary, the process of shaping composite materials using the RTM technique involves mold preparation, composite material preparation, resin injection, curing, and finishing operations. This process allows for the production of complex and high-performance composite parts.中文回答:复合材料由于其高强度与轻重量比以及优异的力学性能,在各个行业中得到广泛应用。
rtm工艺流程
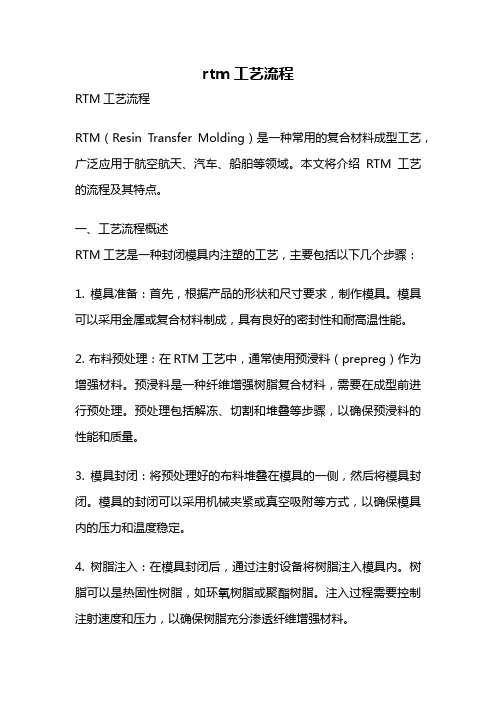
rtm工艺流程RTM工艺流程RTM(Resin Transfer Molding)是一种常用的复合材料成型工艺,广泛应用于航空航天、汽车、船舶等领域。
本文将介绍RTM工艺的流程及其特点。
一、工艺流程概述RTM工艺是一种封闭模具内注塑的工艺,主要包括以下几个步骤:1. 模具准备:首先,根据产品的形状和尺寸要求,制作模具。
模具可以采用金属或复合材料制成,具有良好的密封性和耐高温性能。
2. 布料预处理:在RTM工艺中,通常使用预浸料(prepreg)作为增强材料。
预浸料是一种纤维增强树脂复合材料,需要在成型前进行预处理。
预处理包括解冻、切割和堆叠等步骤,以确保预浸料的性能和质量。
3. 模具封闭:将预处理好的布料堆叠在模具的一侧,然后将模具封闭。
模具的封闭可以采用机械夹紧或真空吸附等方式,以确保模具内的压力和温度稳定。
4. 树脂注入:在模具封闭后,通过注射设备将树脂注入模具内。
树脂可以是热固性树脂,如环氧树脂或聚酯树脂。
注入过程需要控制注射速度和压力,以确保树脂充分渗透纤维增强材料。
5. 固化成型:树脂注入后,需要进行固化过程。
固化可以通过热固化或光固化等方式进行。
固化时间和温度需要根据树脂的性质和产品要求进行控制。
6. 模具开启:在树脂固化后,打开模具,取出成型件。
成型件具有优良的力学性能和表面质量。
二、RTM工艺的特点RTM工艺相比其他成型工艺具有以下特点:1. 成型件质量高:由于RTM工艺采用封闭模具,可以有效控制树脂的渗透和固化过程,从而获得高质量的成型件。
2. 复杂形状成型:RTM工艺适用于复杂形状的产品制造,可以满足各种工程要求。
3. 纤维含量高:RTM工艺可以实现高纤维含量的复合材料制造,提高产品的强度和刚度。
4. 自动化程度高:RTM工艺可以实现自动化生产,提高生产效率和一致性。
5. 环保节能:RTM工艺中的树脂可以回收再利用,减少了废料的产生,符合环保要求。
总结:RTM工艺是一种先进的复合材料成型工艺,具有高质量、适用于复杂形状、高纤维含量、自动化程度高和环保节能等特点。
- 1、下载文档前请自行甄别文档内容的完整性,平台不提供额外的编辑、内容补充、找答案等附加服务。
- 2、"仅部分预览"的文档,不可在线预览部分如存在完整性等问题,可反馈申请退款(可完整预览的文档不适用该条件!)。
- 3、如文档侵犯您的权益,请联系客服反馈,我们会尽快为您处理(人工客服工作时间:9:00-18:30)。
呈分散的微粒状, 使得交联的树脂体系变为双组分 体系 , 这些粒子吸收树脂固化过程中放出的热量而 发生热膨胀, 这种热膨胀过程与树脂收缩过程发生 抵消作用 , 当体系冷却时基体树脂与低收缩添加剂 两相收缩 , 树脂达到玻璃化转变温度后 , 其收缩率比 低收缩添加剂小得多, 低收缩添加剂收缩虽大, 但时 间上滞后于树脂的固化成型, 只能在其自身附近产 生空隙, 不能使整个树脂连续相收缩。 目前常见的低收缩添加剂主要有聚乙酸乙烯酯 ( PVAC )、 聚甲 基丙烯 酸甲 酯 ( PMMA ) 、 聚 苯乙 烯 ( PS)、 热塑性聚氨酯 ( PUR T ) 和聚酯 ( PES) 等。国 内外大量的研究表明 , 低收缩添加剂对降低 UP 的 固化收缩具有很好的效果。笔者选用帝斯曼公司生 产的牌号为 P18- 03 的 PVAC 作为低收缩添加剂。 表 1 列出低收缩添加剂不同用量对双酚 A 环氧乙 烯基酯树脂成型收缩率及弯曲强度的影响。
。但是它活性
较高、 固化反应速度较快, 固化时产生较大的体积收 缩并放出大量的热量, 成型收缩 率高达 5% ~ 8 %, [ 3, 4] 达不到 RTM 模具对基体树脂的要求 , 因此必须 对双酚 A 环氧乙烯基酯树脂进行相应的改性。 针对双酚 A 环氧乙烯基酯树脂成型收缩率大 的缺点 , 选用一种能降低其收缩率的被称为低收缩 添加剂的热塑性树脂来对其改性。其收缩控制机理 为 : 这种低收缩添加剂能溶解在苯乙烯溶液中 , 在树 脂固化过程中形成不溶解的固体粒子 , 析出第二相 ,
表 1 加入低收缩添加剂的双酚 A 环氧乙烯基酯树脂 的成型收缩率及弯曲强度 低收缩添加剂质量分数 /% 0 5 10 15 20 25 30 成型收缩率 /% 9. 5 6. 8 4. 2 2. 2 1. 6 1. 3 1. 1 弯曲强度 /M Pa 125 121 115 110 108 92 85
通常, 在树脂体系中加入低收缩添加剂时 , 其力 学性能会大幅度降低。但从表 2 可以看出 , 加入低 收缩添加剂后虽然体系的各项力学性 能均有所降 低 , 但降 幅不 大, 其 力 学 强度 仍 能 满足 复 合 材料 RTM 模具的要求。 2 . 3 低收缩树脂的制备 按照配比在一定量的双酚 A 环氧乙烯基酯树 脂中加入质量分数为 20 % 的 PVAC 和适量的环烷 酸钴等 , 用搅拌马达搅拌均匀; 称取一定量树脂混合 物 , 按配比加入异丙苯基过氧化氢调节树脂凝胶时 间约为 30 m in ; 并根据试验中得出各组分的配比称 量各组分, 配制成低收缩树脂。 2 . 4 复合材料 RTM 模具的制备 预先制备好复合材料 RTM 模具的胎模 , 要求胎 模表面光滑 , 在胎模表面涂覆一层厚度为 0 . 5~ 1 . 0 mm 的胶衣树脂膜 , 待树脂膜完全固化后, 称取一定
量的低收缩树脂, 按照测试的异丙苯基过氧化氢比 例配制树脂胶液, 用毛刷在树脂膜表面刷一层低收 缩树脂胶液, 然后铺一层 GF 经编织物, 用工具排出 气泡 , 自然固化 ; 依此直至涂层厚度能完全保证模具 的刚度、 强度要求为止, 使之固化脱模。并根据设计 要求安装上相应的连接件与连接结构 , 完成复合材 料 RTM 模具的制备。 3 复合材料 RTM 模具的优缺点 3 . 1 优点 ( 1)成本相对较低 复合材料 RTM 模具成本 低廉 , 有利于降低小批量制品的开发成本; ( 2) 开发周期短 对于批量小的产品 , 采用复 合材料模具有利于缩短产品开发周期; ( 3)精度较高 可以制造具有较小表面糙度的 复合材料制件 , 借助 于手工抛光, 可以达到 MR - 1 级标准。 3 . 2 缺点 ( 1) 表面强度较低、 容易受到损坏 合适的脱模剂 , 尽量提高模具的使用周期; ( 2)热效率较低 热时间较长。 4 结论 ( 1)以双酚 A 环氧乙烯基酯树脂为基体 , PVAC 为低收缩添加剂 , GF 经编织物为增强材料 , 并加入 相应的助剂, 制备了复合材料 RTM 模具。 ( 2)复合材料 RTM 模具具有成本较低、 开发周 期短、 精度较高等优点, 但表面强度和热效率较低。
表 2 G F 经编织物增强双酚 A 环氧乙烯基酯树脂加入 低收缩添加剂前后的性能对比 项目 拉伸强度 /M Pa 拉伸弹性模量 /G Pa 弯曲强度 /M Pa 弯曲弹性模量 /G Pa G F 经编织物增强双酚 A 环氧乙烯基酯树脂 含 20 % 低收缩添加剂 不含低收缩添加剂 415 21 . 5 483 23 . 6 458 25 .0 526 26 .0
从表 1 可以看出, 随着低收缩添加剂用量的增 加, 双酚 A 环氧乙烯基酯树脂的成型收缩率呈下降 趋势。当低收缩添加剂的质量分数为 20 % 时, 双酚 A 环氧乙烯基酯树脂的成型收缩率降至为 1 . 6 %, 降幅接近 83. 2 % , 由此可见, 低收缩添加 剂具有十 分显著的低收缩特性, 而此时树脂材料的弯曲强度 为 108 MP a , 保持率仍达 86 . 4 % , 这说明低收缩添加
参考文献
1 黄发荣 , 焦扬声 , 郑安呐 . 塑 料工业手 册 ! ! ! 不饱和聚酯 树脂 . 北 京 : 化学工业出版社 , 2000 . 2 周菊兴 , 董永祺 . 不饱和聚酯树脂 . 北京 : 化学工业出版社 , 2000 . 3 区英鸿 , 邢春 明 , 李永 先 , 等 . 塑 料手册 . 北京 : 兵器工 业出 版社 , 1991 . 4 沈开猷 . 不饱和聚酯树脂 . 北京 : 化学工业出版社 , 2001 .
收稿日期: 2006 03 01
王海文 , 等 : 复合材料 RTM 模具的制备
41
剂对基体树脂的强度影响不大 , 强度保持率较高, 能 够满足制备复合材料 RTM 模具的要求。 2 . 2 增强材料的选择 制备树脂基复合材料模具, 需要采用增强材料 对树脂进行增强 , 提高复合材料的强度, 以满足复合 材料模具的刚度、 强度要求 ; 由于模具的形状较为复 杂 , 需要采用随型性好的 经编织物作为 增强材料。 经筛选采用圣戈班复合材料工程有限公司生产的玻 璃纤维 ( GF ) 经编织物 ( 45 ) 作为增强材料 , 并对 用其增强的双酚 A 环氧乙烯基酯树脂加入低收缩 添加剂前后的性能进行对比, 结果见表 2 。
要求选择
复合材料 RTM 模 具需要加
M ANUFACTURE OF RTM M OULD OF CO M PO SITE
W ang H a i w en
( Inst itu te of Petroleum Engin eering, C hina U n iversity of Petro leum, D ongy ing 257062, C h ina)
40
工程塑料 应用
2006 年 , 第 34 卷 , 第 5 期
复合材料 RTM 模具的制备
王海文
[ 中国石油大学 ( 华东 )石油工程学院 , 东营 257062]
范建礼
( 胜利石油管理局井下作业二公司 , 东营 257000)
摘要
根据树脂传递 模塑 ( RTM ) 模具对基体树脂的基本要求 , 选用双酚 A 环氧乙烯基酯树 脂为基体 , 聚 乙酸乙
F an Jian li
( D ownholeW orkover Service 2th C ompany , Shengli Petroleum A dm in istrat ive Bureau, D ongying 25in transfer m o ld ing ( RTM ) mould w as m anufactured w ith b ispheno l A epox ide v inylester resin as m atr ix , po ly ( v inyl aceta te) as low shrinkage additive and g lass fiber tr icot as re inforc ing m ater ia , l acco rd ing to the basic requ irem ent of ma tr ix res in o f RT M m ould . T he mould had m erits such as low cost , short deve lopm ent cyc le and h igh prec ision, wh ile it had de fects of low sur face streng th and ther m a l effic iency . K EYW ORDS resin transfer m o lding , bispheno l A epox ide v iny lester resin, low shrinkage add itive , composite , m ould
烯酯为低收缩添 加剂 , 玻璃纤维经编织物为增强材料 , 并加入相应 的助剂 , 制备了复 合材料 RTM 模具 。 该模 具具有 成本较低 、 开发周期短 、 精 度较高等优点 , 但表面强度和热效率较低 。 关键词 树 脂传递模塑 双酚 A 环氧乙烯基酯树脂 低收缩添 加剂 复合材料 模具
树脂传递模塑 ( RTM ) 工艺是成型纤维增强塑 料 ( FRP ) 的重要工艺之一。该工艺对成型模具的要 求较高 , 既要求模具具有优异的强度和刚度、 良好的 尺寸稳定性和较高的耐热性 , 又要求模具具有优良 的耐化学药品性、 耐磨损性和平整度。 RTM 模具可 以由金属制造, 也可以采用树脂基复合材料制造, 因 复合材料模具成本相对较低、 开发周期短而得到广 泛应用。 1 复合材料 RTM 模具对基体树脂的要求 根 据 RTM 模具 的 使 用要 求 , 制备 复 合 材料 RTM 模具用基体树脂应具备的特性为: ( 1) 低收缩 特性, 甚至达到零收缩 ; ( 2) 良好的工艺性; ( 3) 固化 后能提供足够的力学强度和刚度; ( 4) 良好的耐热 性 ; ( 5) 优良的耐腐蚀性。 2 复合材料 RTM 模具的制备 2 . 1 基体树脂的选择及改性 经过性能比较, 选用金陵帝斯曼树脂有限公司 生产的牌号为 A tlac382 的双酚 A 环氧乙烯基酯树 脂作为基体树脂。这是因为该环氧乙烯基酯树脂是 由环氧树脂 ( EP ) 与甲基丙烯酸在催化剂存在下通 过开环加成聚合反应而制得的 , 它既保留了 EP 的 基本链段, 具有较高的力学性能 , 同时又具有不饱和 聚酯树脂 ( UP )的良好工艺性能 , 能在适宜条件下固 化而表现出某些特殊的优良性能