复合材料的成型工艺ppt课件
复合材料pdfPPT课件

良好的热导性
某些复合材料具有良好的热导性,适用于需要散热或传热的场合。
耐高温性能
通过选择合适的基体和增强材料,复合材料可以在高温环境下保持 较好的力学性能。
电学性能
绝缘性能
大多数复合材料具有良好的绝缘性能,适用于电气 和电子设备中。
后处理与加工
固化处理
对成型的复合材料进行加热或自然固化,使其达到所需的物理和化 学性能。
机械加工
对固化后的复合材料进行切割、钻孔、打磨等机械加工,以满足产 品形状和尺寸的要求。
表面处理
对复合材料表面进行喷漆、电镀、阳极氧化等处理,以提高其耐腐蚀 性、装饰性等性能。
04
复合材料的性能特点
力学性能
成型工艺
手糊成型
在模具上涂刷脱模剂,然后铺贴一层纤 维布或毡,再涂刷一层树脂,如此反复
直至达到所需厚度。
模压成型
将预浸料或纤维与树脂混合物放入模 具中,在加热和加压的条件下固化成
型。
喷射成型
将树脂和固化剂分别通过喷嘴喷到模 具上,同时用喷枪将纤维切断并喷到 树脂中,形成复合材料层。
注射成型
将树脂和固化剂混合后注入到装有纤 维的模具中,然后在一定温度和压力 下固化成型。
复合材料的组成与结构
基体材料
聚合物基体
如环氧树脂、聚酰亚胺等,具有良好的可加工性和韧 性。
金属基体
如铝、镁、钛等合金,具有高比强度和优异的导电导 热性能。
陶瓷基体
如氧化铝、氮化硅等,具有高温稳定性和耐磨损性。
增强材料
纤维增强材料
如碳纤维、玻璃纤维、芳纶纤维等,具有高比 强度和模量。
热固性复合材料成型工艺

(2)过氯乙烯脱模剂 配方:过氯乙烯粉5~10份 甲苯+丙酮(1:1)95~90份 按比例将物料与溶剂混和搅拌,放入密闭容器中(不
能用塑料容器)等完全溶解后即可使用。 (3)聚苯乙烯溶液脱模剂
配方:聚苯乙烯粉 5份 甲苯 95份
称量混合,搅拌均匀后,密封放置7天左右,若完全溶 解,搅拌均匀即可使用。
缺点:
劳动密集型的成型方法,生产效率低—喷射成型工艺 制品质量与操作者的技术水平有关 生产周期长 制品力学性能较其他方法低—袋压成型工艺
原材料
玻璃纤维及其织物
选择依据:容易被树脂浸润 有较好的形变性 满足制品的性能要求 价格便宜
种类:无捻粗纱 无捻粗纱布 短切原丝毡 加捻布 玻璃布袋
MPa
袋压成型工艺
装袋 固化
复合材料夹层结构的制造
概述
夹层结构有两层薄而高强度的面板材料,其间夹着一层 厚而轻质的芯材,是为了满足轻质高强要求发展起来的 一种结构形式。
面板材料:复合材料板、塑料板、铝板、胶合板等 夹芯材料:蜂窝芯材、泡沫塑料、强芯毯、软木等 优点:比强度高,表面光洁,结构稳定性好,承载能力
模具的结构形式
模具的结构
单模 阳模 对模 阴模
拼装模
❖ 模具材料选择:
(1)木材
要求均质、无节。常用红松、银杏、枣木等。木材模 具表面需要封孔处理。其特点是质轻、易加工;但不耐久 。适合于小批量生产小型制品。
(2)石膏
用半水石膏成型。制造简便,造价低;不耐用,怕冲 击,适合于小批量生产形状复杂的制品。
原材料:⑴模具用胶衣树脂:①固化放热和收缩小; ②优异的耐断裂、耐冲击性能;③优良的耐 热性、光泽度和硬度;④良好的涂刷性;⑤ 与制品胶衣色调相反 ⑵增强层树脂:①固化收缩率小;②韧性好; ③有易操作的黏度;④耐热性好
第五章 热固性复合材料成型工艺

2009-11-4
21
Dept. Polym. Sci. & Tech.
2009-11-4
22
Dept. Polym. Sci. & Tech.
四、工艺 1、原材料准备
(1) 胶液准备 胶液的主要工艺指标是:胶液粘度;凝胶时间。
胶液粘度:
表征流动特性,粘度控制在0.2~ 0.8Pa.s之间,一般用稀释剂调节
一般2~10mm
2009-11-4
9
Dept. Polym. Sci. & Tech.
玻璃纤维及其织物 二、原材料: 热固性树脂 辅助材料
1、玻璃纤维及其织物
无捻粗纱 无捻粗纱布 短切粗纱布 短切原丝毡 加捻布 玻璃布带
2009-11-4
10
Dept. Polym. Sci. & Tech.
A、玻璃纤维无捻粗纱:将拉丝得到的原纱,平行并股 卷成圆筒形。
Dept. Polym. Sci. & Tech.
2、热固性树脂
要求:
• 能够配制粘度适中的胶液; • 能在室温或较低温度下固化,固化时无低分子物产生; • 无毒或低毒; • 价格便宜,来源广泛。 目前国内大部分手糊制品均用不饱和聚酯树脂,约占 80%,其次是环氧树脂。
2009-11-4
14
Dept. Polym. Sci. & Tech.
1. 预浸料及其制造方法 预浸料是将树脂体系浸涂到纤维或纤维织物上,通过一定 的处理过程后贮存备用的半成品,预浸料是一个总称。 根据实际需要可将预浸料进行如下分类:
⑴ 按照增强材料的纺织形式:预浸带、预浸布、无纺布等; ⑵ 按照纤维的排布方式:单向预浸料、织物预浸料; ⑶按照纤维类型:玻璃纤维预浸料、碳纤维预浸料、有机纤维 预浸料等。
复合材料成型工艺

复合材料成型工艺是复合材料工业的发展基础和条件。
随着复合材料应用领域的拓宽,复合材料工业得到迅速发镇,其老的成型工艺日臻完善,新的成型方法不断涌现,目前聚合物基符合材料的成型方法已有20多种,并成功地用于工业生产,如:(1)手糊成型工艺--湿法铺层成型法;(2)喷射成型工艺;(3)树脂传递模塑成型技术(RTM技术);(4)袋压法(压力袋法)成型;(5)真空袋压成型;(6)热压罐成型技术;(7)液压釜法成型技术;(8)热膨胀模塑法成型技术;(9)夹层结构成型技术;(10)模压料生产工艺;(11)ZMC模压料注射技术;(12)模压成型工艺;(13)层合板生产技术;(14)卷制管成型技术;(15)纤维缠绕制品成型技术;(16)连续制板生产工艺;(17)浇铸成型技术;(18)拉挤成型工艺;(19)连续缠绕制管工艺;(20)编织复合材料制造技术;(21)热塑性片状模塑料制造技术及冷模冲压成型工艺;(22)注射成型工艺;(23)挤出成型工艺;(24)离心浇铸制管成型工艺;(25)其它成型技术。
视所选用的树脂基体材料的不同,上述方法分别适用于热固性和热塑性复合材料的生产,有些工艺两者都适用。
复合材料制品成型工艺特点:与其它材料加工工艺相比,复合材料成型工艺具有如下特点:(1)材料制造与制品成型同时完成一般情况下,复合材料的生产过程,也就是制品的成型过程。
材料的性能必须根据制品的使用要求进行设计,因此在造反材料、设计配比、确定纤维铺层和成型方法时,都必须满足制品的物化性能、结构形状和外观质量要求等。
(2)制品成型比较简便一般热固性复合材料的树脂基体,成型前是流动液体,增强材料是柔软纤维或织物,因此,用这些材料生产复合材料制品,所需工序及设备要比其它材料简单的多,对于某些制品仅需一套模具便能生产。
一、接触低压成型工艺接触低压成型工艺的特点是以手工铺放增强材料,浸清树脂,或用简单的工具辅助铺放增强材料和树脂。
接触低压成型工艺的另一特点,是成型过程中不需要施加成型压力(接触成型),或者只施加较低成型压力(接触成型后施加0.01~0.7MPa压力,最大压力不超过2.0MPa)。
树脂基复合材料ppt课件

3、SRIM
1)树脂(粘度10~100CP) 2)增强体
2CH2 CH R C O R' OH+ OCN R'' NCO
CH2 CH R C O R' O C N R" N C O R' O C R CH CH2
O
H HO
R (OH)n + 2 OCN R'' NCO
O R O C N R' N C
缠绕成型的特点:
1)由于可以按照承力要求确定纤维的方向、层次、数量,可实现 强度的设计
2)纤维伸直和按规律排列的整齐性和精确度高于任何其它成型方 法,制品能充分发挥纤维的强度,因此比强度和比刚度均高。
3)玻璃钢压力容器比钢质减重40~60%。 4)生产效率高可成型各种尺寸的制品; 5)设备投资大; 6)不能生产凹形制品;
4、模具
由于压力低,故RIM工艺所使用的模具的价格也比较 低,一般采用高质量工具钢、铝合金以及环氧树脂 (温度低于65℃)等
四、制品缺陷
1、由工艺过程造成的缺陷 1)原料污染; 2)温度控制; 3)混合计量控制; 4)模具是否清洁; 5)模具温度; 6)脱模时间;
第二节:树脂转移成型
树脂转移成型具有开发高性能、大体积低成本复合材料的能力
模压成型、注射成型相和反应注射成型的 温度和压力对比
成型工艺 温 度(℃) 模腔压力(bar)
RIM
60-120
5-15
IM CM RTM
120-350 130-175 20-120
20-140 70-2000
4-10
RIM的几种不同形式:
1、SRIM:结构反应注射成型(Structural RIM) 2、RRIM:增强反应注射成型 (Reinforced RIM) 3、MMRIM:(Mat Molding RIM)
复合材料的成型工艺ppt课件
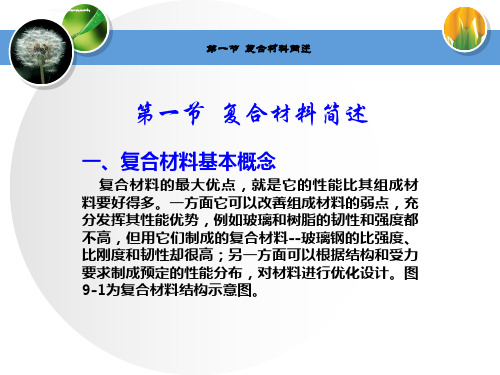
第二节 金属基复合材料(MMC)成形工艺
一、固态法
1.扩散黏结法(Diffusion Bonding) 如图9-2所示,扩散黏结是一种在较长时间、
较高温度和压力下,通过固态焊接工艺,使同类 或不同类金属在高温下互扩散而黏结在一起的工 艺方法。
2.形变法(Plastic Forming) 形变法就是利用金属具有塑性成型的工艺特点
2.复合材料的特点
(1)比强度和比刚度高 (2)抗疲劳性好 (3)高温性能好 (4)减振性能好 (5)断裂安全性高 (6)可设计性好
为 了 规 范 事 业单位 聘用关 系,建 立和完 善适应 社会主 义市场 经济体 制的事 业单位 工作人 员聘用 制度, 保障用 人单位 和职工 的合法 权益
第一节 复合材料简述
四 、 复 合 材 料 的 失 效 (Failure of Composite)
复合材料的失效一般是指其疲劳破坏过程。
1.制造加工损伤
此种损伤产生初始缺陷。,它包括:纤维铺设不 均,扭结、死扣等,树脂不均;纤维切断、错排; 固化不足;有孔隙、气泡;材质污染等。
2.使用引起的损伤
此种损伤导致缺陷发展。它包括:树脂裂纹或老 化;分层;纤维断裂;振动较大导致的纤维断裂; 温度变化较大;机加工产生内应力;碰撞等。
二、复合材料用原料
1.增强材料
(1)碳纤维(Carbon Fiber) (2)硼纤维(Boron Filament) (3)芳纶(Aramid Ring) (4)玻璃纤维(Glass Fiber) (5)碳化硅纤维(Silicon Carbide Fiber) (6)晶须(Whisker)
2.基体材料
3)基体能够很好地保护纤维表面,不产生表面 损伤、不产生裂纹。
第5章 成型工艺
第5章 复合材料成型工艺
本章主要内容:
5.1 概述
5.2 低压成型工艺 5. 3 层压成型工艺
七、 质量控制
2、制品内气泡太多 原因1: 树脂用量过多 解决办法: 1、控制胶含量 2、注意拌合方式 原因2: 树脂粘度过大 解决办法:1、适当增加稀释剂 2、提高环境温度
原因3: 增强材料选择不当 解决办法: 选用浸透性好的无捻玻璃布
七、 质量控制
3、流胶 原因1: 树脂粘度太小,可加入2~3%的活性氧化硅。
⑵ 材料性能和产品质量要求,如材料的物化性能、产品的强度 及表面粗糙度(光洁度)要求等; ⑷ 企业有可能提供的设备条件及资金;
⑶ 生产批量大小及供应时间(允许的生产周期),批量有区别;
⑸ 综合经济效益,保证企业效益。
举 例:
a. 生产批量大、数量多及外形复杂的小产品——模压 成型; e.g. 机械器件、电子器材等。 b.造型简单的大尺寸制品,批量小——手糊成型、喷 射成型; e.g. 浴盆、汽车部件、胎体外壳、大型储槽等。 c.压力管道及容器——缠绕工艺; d.板材及成型制品——连续成型工艺。
预浸料及其制造方法
预浸料(Prepregs):
纤维或织物预先浸渍树脂,经一定处理后贮存 备用的半成品。只需裁剪后,经一定成型工艺加工 成所需要的制品。
可分为单相预浸料和织物预浸料。
单向预浸料
a喷丝架 平铺 O 在制 品的各个部分。 2 树脂必须适量地均匀地分布在制品的 各个部位,并适当固化。 3 工艺过程中尽量减少气泡,降低孔隙 率,提高制品的致密性。 4 充分掌握所用树脂的工艺性能,制定 合理的工艺规范。
复合材料工艺
F-35
战 斗 机
复合材料进气道 预形件的编织是在一个大心轴上进行的,将其共分为35块, 以便在固化后分别从心轴上取下。心轴是由五层连续石墨 纤维编织而成,局部达八层厚。编织为一种自动化的经纬 编织法,零件表面纤维拉紧。
接触低压成型工艺
• 接触低压成型工艺的特点是以手工铺放增强材料,浸清树 脂,或用简单的工具辅助铺放增强材料和树脂。接触低压 成型工艺的另一特点,是成型过程中不需要施加成型压力 (接触成型),或者只施加较低成型压力(接触成型后施 加0.01~0.7MPa压力,最大压力不超过2.0MPa)。
原理1、纤维路径在整个缠绕过程中不打滑。 原理2、整个成型过程中,纤维不架桥。 原理3、纤维路径与芯模端部相切。
原理4、整条纤维尽可能均匀地完全覆盖芯模。
大型玻璃钢现场微控整体缠绕贮槽、贮罐,缠绕直径 4000mm-10000mm,缠绕长度为3000--12000mm。
(1)干法缠绕
• 干法缠绕是采用经过预浸胶处理的预浸纱或带,在缠绕机上经加热软 化至粘流态后缠绕到芯模上。
模具检验 及涂脱模 剂
图纸资料 胶液配制
玻璃布处理
预浸料制备
湿法铺陈 干法铺陈
装袋
固化炉 热压罐
模具
脱模 制件 加工和 修饰
试验片
检验区
检验
成
品
性能测试
真空袋成型
②真空袋法 此法是将手糊成型未固化的制品,加盖一层橡胶膜,制品处于橡 胶膜和模具之间,密封周边,抽真空(0.05~0.07MPa),使制品中的气泡 和挥发物排除。真空袋成型法由于真空压力较小,故此法仅用于聚酯和环氧 复合材料制品的湿法成型。
1层贴法
2 沉积法
3 缠绕法 4 编织法
复合材料的成型工艺
复合材料的成型工艺图1:热固性复合材料最基本的制备方法是手糊,通常包括将干层或半固化片层用手铺设到模具上,形成一个积层。
图中展示的是自由宇航公司的技术员(佛罗里达州墨尔本)正在通过手糊工艺加工一个碳/环氧预浸料,将用于制造通用航空飞机部件。
资料来源:自由宇航公司在复合材料的加工成型过程中会使用一系列模具,用来给未成形的树脂及其纤维增强材料提供一个成型的平台。
手糊(hand layup)成型是热固性复合材料最基本的制备方法,即通过人工将干层或半固化片层铺设到模具上,形成一个积层。
铺层方式分为两种:一种称为干法铺层,是先铺层后将树脂浸润(例如,通过树脂渗透方式)到干铺层上的方式,另一种方式是湿法铺层,即先浸润树脂后铺层的顺序。
现在普遍使用的固化方式可以分为以下几种:最基本的是室温固化。
不过,如果提高固化温度的话,固化进程也会相应加快。
比如通过烤箱固化,或使用真空袋(vacuum ba g)通过高压釜固化。
如果采用高压釜固化的话,真空袋内通常会包含透气膜,被放置在经手糊的半成型制品上,再连接到高压釜上,等最终固化完成后再将真空袋撤去。
在固化过程中,真空袋的作用是将产品密封在模具和真空袋之间,通过抽真空对产品均匀加压,将产品中汇总的气体排出,从而使产品更加密实、力学性能更好。
图2:热压釜独有的高温和高压条件使其成为完成热固性树脂零部件的固化的重要工具。
控制软件的改进则能够帮助经营者提高35-40%的生产量。
同时,一些新的树脂配方正在开发当中,将通过低压固化处理。
图中是Helicomb国际公司(俄克拉荷马州塔尔萨)的一名操作人员正在使用高压釜进行固化处理。
来源:Helicomb国际公司许多高性能热固性零件都需要在高热高压的条件下完成固化。
但是高压釜(Autocl aves)的设备成本和操作成本都较昂贵。
采购高压釜设备的制造商通常会一次性固化一定数量的部件。
对于高压釜的温度,压力,真空和惰性气体(inert atmosphere)等一系列参数,计算机系统能帮助实现远程甚至无人监控和检测,并最大限度地提高该技术的利用效率。
复合材料成型工艺---SMC模压成型
模压形状复杂、壁薄、 深度大的制品时,不宜 选用高模温,但经过预 热的塑料进行模压时, 由于内外层温度均匀, 流动性好,可选较高模 温。
模压时间主要与塑料的 固化速度有关,而固化 速度决定于塑料的种类 ,此外,模压时间与制 品的形状、厚度、模压 温度和压力以及是否预 热和预压有关
SMC模压工艺的优缺点
玻璃钢花盆
汽车装饰板
非球面透镜
模压材料工艺参数
流动性
在一定温度和压力下模压料充 满模腔的能力。不同的产品对模 塑料的流动性有不同的要求,形 状复杂和薄壁制品要求模塑料有 较大的流动性
固化速率
固化速率主要由热固性塑料的 交联反应性质决定,并受成型前 的预压、预热条件以及成型温度、 成型压力等多种因素的影响
优点
没有浇注系统,原料损失小
制品的收缩率小,且重复性较好
制品受纤维取向的影响较小,内应力 低,翘曲变形小,机械性能稳定
特别适用于成型不得翘曲的薄壁制品, 可生产壁厚小至0.6mm的制品
模压料流动距离短,模腔的磨损小且 模具的结构简单,制造成本低,维修 方便
模压成型适应性广,几乎每种塑料都 能适用,对于不适合采用注塑和挤出 成型的塑料,可采用模压成型
A段为装料室
由于具备装料室,该模具可适 用于压缩率较大的塑料。压制时, 当阳模伸入阴模,溢料只能从阳模 上开设的溢料槽中溢出。所以,物 料的外溢在这种模具中是受到一定 限制的。这种模具的特点是制造成 本高,压制时物料容易积留在支承 面上,从而导致型腔内的物料不能 得到足够的压力。
不溢出式压模
不溢式压缩模示意图 1.阳模 2.阴模 3.制品 4.推顶杆 5.定位下模板
模压成型工艺是将一定量预浸料放入到金属模具的对模模腔中,利用带热源的 压机产生一定的温度和压力,合模后在一定的温度和压力作用下使预浸料在模 腔内受热软化、受压流动、充满流动、充满模腔成型和固化,从而获得复合材 料制品的一种工艺方法
- 1、下载文档前请自行甄别文档内容的完整性,平台不提供额外的编辑、内容补充、找答案等附加服务。
- 2、"仅部分预览"的文档,不可在线预览部分如存在完整性等问题,可反馈申请退款(可完整预览的文档不适用该条件!)。
- 3、如文档侵犯您的权益,请联系客服反馈,我们会尽快为您处理(人工客服工作时间:9:00-18:30)。
第一节 复合材料简述
2.复合原则(Rule of Mixtures)
以纤维增强复合材料为例,说明复合材料的复 合原则。 (1)复合材料中基体起粘结作用,因而基体必须具 备如下特点:
1)对纤维具有好的润湿性,从而使基体与增强 材料间具有较强的结合力,使分离的纤维粘为一 个整体,保证纤维的合理分布。
2)基体应具有较好的塑性和韧性,能够延缓裂 纹的扩展。
四 、 复 合 材 料 的 失 效 (Failure of Composite)
复合材料的失效一般是指其疲劳破坏过程。
1.制造加工损伤
此种损伤产生初始缺陷。,它包括:纤维铺设不 均,扭结、死扣等,树脂不均;纤维切断、错排; 固化不足;有孔隙、气泡;材质污染等。
2.使用引起的损伤
此种损伤导致缺陷发展。它包括:树脂裂纹或老 化;分层;纤维断裂;振动较大导致的纤维断裂; 温度变化较大;机加工产生内应力;碰撞等。
第二节 金属基复合材料(MMC)成形工艺
第二节 金属基复合材料(MMC) 成形工艺
(1)固态法 固态法是指基体处于固态下制造金属 基复合材料的方法。
(2)液态法 液态法是指基体处于熔融状态下制造 金属基复合材料的方法。
(3)其他制造方法 主要包括原位自生成法、物理 气相沉积法、化学气相沉积法、化学镀和电镀法、复 合镀法等。
(1)碳纤维(Carbon Fiber) (2)硼纤维(Boron Filament) (3)芳纶(Aramid Ring) (4)玻璃纤维(Glass Fiber) (5)碳化硅纤维(Silicon Carbide Fiber) (6)晶须(Whisker)
2.基体材料
(1)热固性树脂(Thermosetting Resin) (2)热塑性树脂(Thermoplastic Resin)
第九章 复合材料的成型工艺
第九章 复合材料的成型工艺
复合材料(Composite Material)是指将两种以上 的不同材料,用物理或化学的方法复合而成的一种新 材料 。
第一节 复合材料简述
第一节 复合材料简述
一、复合材料基本概念
复合材料的最大优点,就是它的性能比其组成材 料要好得多。一方面它可以改善组成材料的弱点,充 分发挥其性能优势,例如玻璃和树脂的韧性和强度都 不高,但用它们制成的复合材料--玻璃钢的比强度、 比刚度和韧性却很高;另一方面可以根据结构和受力 要求制成预定的性能分布,对材料进行优化设计。图 9-1为复合材料结构示意图。
3. 夹 层 结 构 材 料 (Sandwich Structure Material)
夹层结构一般由两层簿的高强度板和中间夹着一层厚 而轻的芯结构构成。
第一节 复合材料简述
三、复合材料的增强机制和复合原则
1. 增 强 原 理 (The Principle of Reinforcement)
复合材料的复合不是由基体和增强两种材料简单的 组合而成,而是两种材料发生相互的物理、化学、力 学等作用的复杂组合过程。
如图9-4所示,真空压力浸渍法是在真空和高压惰 性气体的共同作用下,使熔融金属浸渗入预制件中制造 金属基复合材料的方法。
(3)液态金属搅拌铸造法(Stir-Casting Method of Liqu颗粒直接加入金属 熔体中,通过搅拌使颗粒均匀分散,然后浇铸成型制成 复合材料制品的方法 。
第一节 复合材料简述
1.复合材料的分类
(1)按材料的作用分类 结构复合材料和功能复合材料 。
(2)按基体材料分类 树脂基复合材料(resin matrix composites-
RMC) 、 金 属 基 复 合 材 料 (metallic matrix composites -MMC)、陶瓷基复合材料(ceramic matrix composites-CMC)、水泥基复合材料和 碳/碳复合材料等 。 (3)按增强材料的性质和形态分类
,通过热轧、热拉、热挤压等加工手段,使已复 合好的颗粒、晶须、短纤维增强金属基复合材料 进一步加工成板材。
3.粉末冶金法(Powder Metallurgy Method) 如图9-3所示,粉末冶金法是一种用于制备与
成形颗粒增强(非连续增强型)金属基复合材料的 传统固态工艺法。
第二节 金属基复合材料(MMC)成形工艺
第二节 金属基复合材料(MMC)成形工艺
2. 井喷沉积法(Spray Co-Deposition)
井喷沉积法是运用特殊的喷嘴,将液态金属 基体通过惰性气体气流的作用后雾化成细小的 液态金属流,将增强相颗粒加入到雾化的金属 流中,与金属液滴混合在一起并沉积在衬底上 ,凝固形成金属基复合材料的方法。
层叠复合材料、细粒复合材料、连续纤维复合 材料、短切纤维复合材料、碎片增强复合材料和骨 架复合材料等。
第一节 复合材料简述
2.复合材料的特点
(1)比强度和比刚度高 (2)抗疲劳性好 (3)高温性能好 (4)减振性能好 (5)断裂安全性高 (6)可设计性好
第一节 复合材料简述
二、复合材料用原料
1.增强材料
3)基体能够很好地保护纤维表面,不产生表面 损伤、不产生裂纹。
第一节 复合材料简述
(2)增强材料是承载的主要部分,因而纤维必须具 有很高的强度和刚度。
(3)增强材料与基体有好的结合强度。 (4)在复合材料中纤维必须具有适当的含量、直径
和分布。 (5) 纤维和基体应有相近的热膨胀系数。
第一节 复合材料简述
二、液态法
1. 液态金属浸润法 液态金属浸润法的实质是使基体 金属呈熔融状态时与增强材料浸润结合,然后凝固成型 。 (1)挤压铸造法(Squeeze Casting)
挤压铸造是通过压机将液态金属压入增强材料预制 件中制造复合材料的方法。
(2) 真 空 压 力 浸 渍 法 (Vacuum Pressure Infiltration)
第二节 金属基复合材料(MMC)成形工艺
一、固态法
1.扩散黏结法(Diffusion Bonding) 如图9-2所示,扩散黏结是一种在较长时间、
较高温度和压力下,通过固态焊接工艺,使同类 或不同类金属在高温下互扩散而黏结在一起的工 艺方法。
2.形变法(Plastic Forming) 形变法就是利用金属具有塑性成型的工艺特点