Injection Molding_B
Tooling各种浇口介绍_(chinese)

Tooling Development
Processing Problems (工艺问题)
• Weld Lines(加水纹) • Burn Marks(焦烧)
• Dimensional Control(尺寸控制)
• Streaking(条痕) • Sticking(粘模) • Brittleness(脆化)
MOLD MAKER (模具制造者)
Tooling
TOOLING DEVELOPMENT
(加工过程)
Tooling Development
Processing Problems (工艺问题)
• Black Specks(黑点) • Gloss(反光) • Jetting(射流纹) • Delamination(分层) • FinNyprorprinting(印刷起鳍) • Plate-Out(结垢)
Nypro Guangzhou
Injection Mold Tooling
(注射模具加工)
Tooling Considerations
GOOD PART (良品)
Tooling Considerations
RESIN
SUPPLIER (树脂供应商)
END USER (最终用户) MOLDER (铸工)
INCOE
(无流道成型系统)
KONA
D-M-E
PLASTHING
Hot One
RAMA
Cool One
HUSKY
MOLDMASTER
FASTHEAT
SPEAR
EUROPE & ASIA
HOMEMADE
SPRUELESS
Tooling Runnerless Molding
[说明]Injection-CompressionMolding
![[说明]Injection-CompressionMolding](https://img.taocdn.com/s3/m/71c6f3fd162ded630b1c59eef8c75fbfc77d9449.png)
Injection-Compression Molding一、前言射出壓縮成型(Injection-Compression Molding)為一新的製程技術,近年來在學界與業界引起了相當多的研究與討論,而此一製程技術目前已廣泛應用在需高精度尺寸及考慮光學性質的光學產品如DVD、CD-ROM或光學鏡片等的製造。
本文傴簡介射出壓縮成型的製程特性與射出壓縮成型模板控制,最後並以光學鏡片在本公司研發之全電式射出成型機上之應用為案例說明射出壓縮製程相較於傳統射出成型對於光學鏡片成品品質之影響。
二、射出壓縮製程特性射出壓縮成型其操作結合了射出成型以及壓縮成型兩種成型技術,此種製程主要是在一般傳統射出成型製程中之外加入模具壓縮的製程,亦即在充填之初模具不完全閉鎖,當部份塑料注入模穴後,再利用鎖模機構閉鎖模具,由模心模壁向模穴內熔膠施加壓力以壓縮成型來完成模穴充填。
此種成型方式不但可以降低充填模穴所需之射出壓力,且由於均勻加壓使得整個成型製程可以在低壓的環境下完成而得到模穴內熔膠均勻的壓力分佈(圖一)。
比起傳統的射出成型,射出壓縮成型具有以下優點:(1)降低射出壓力。
(2)降低殘餘應力。
(3)減少分子定向。
(4)均勻保壓減少不均勻收縮。
(5)克服凹陷及翹曲。
(6)減少成品雙折射率差。
(7)緩和比容積變化。
(8)增進尺寸精度(圖一)三、射出成型模板的控制射出壓縮成型方法中活動模板的位置控制直接影響射出階段的模穴厚度、流動阻力,以及成品的殘留應力;而在壓縮段活動模板的壓力速度直接對應熔膠的保壓及流動,也因此影響成品的收縮與翹曲狀況。
活動模板的控制模式可分為二種模:其中一種為壓力控制模式,亦即模板在射出階段前以低壓力鎖模,此時模具已密合只是鎖模力極低,在射出階段時再利用射出壓力迫使模具打開,以使模穴空間加大同時降低流動阻力,當完成射出動作後再使模具移動進行壓縮動作(圖二)。
第二則為位置控制模式,模板在射出前以預先定位某一位子,並預留較大的模穴空間,此時射出動作擠入熔膠並且可以低壓方式進入模穴,待射出完成後再進行壓縮工作(圖三)。
注塑(成型)模具安装及调试

注塑(成型)模具安装及调试Injection Mold Installing and Setup注塑模具安装及调试1. Purpose (⽬的)To provide the general standard guideline for injection mold installing and setup.Ensure consistent approach is used for each injection mold installing and setup processes.提供⼀套标准注塑模具安装及调试⽅法。
确保每次注塑模具安装及调试⽅法⼀致。
2. Scope (应⽤)This instruction applies to injection molding machine inside Grakon injection molding division.本指引适⽤于所有Grakon注塑部注塑机。
3. Responsibilities (责任)Injection Molding In-charge need to ensure all of the Injection Molding Foremen and operators are been trained and qualified forinjection mold installing and setup.Production Engineering Manager delivers proper training to Project Engineers, Process Improvement Engineers and Technicians to ensurethat all the molding activities, tooling qualification and moldingparameter determination follow this guideline.注塑部总负责⼈需确保所有注塑部领班和操作员有适当及充⾜模具安装及调试训练. 及后各⼈取得模具安装及调试资格。
injection_molding_introduce
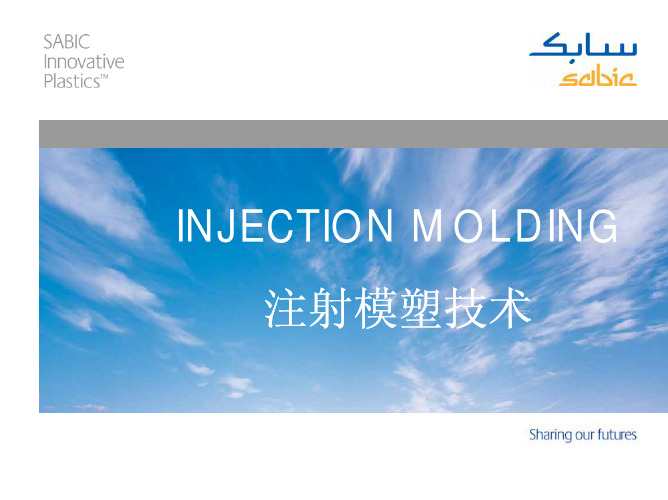
Cylinder Bore料筒 主体
Provides Mechanical and Thermal Connection From Hot Cylinder to Colder Mold 提供从热的料筒到相对冷的模具的机械和热连接
Injection Molding Equipment
Radius 半径
Injection Molding Process
Injection Molding Steps:
•Drying the Pellets •Loading Into Molding Machine •Heating and Shearing Material Into a Melt •Injecting the Melt Into the Mold Cavity •Part Cooling, Solidification •Ejecting the Finished Part From the Mold
Injection Molding Equipment
MACHINE SHOT SIZE 机器注射容量
Part Weight = 30 - 80 % of Machine Shot Size 制件重量 = 30 - 80 % 机器注射容量 Optimal Part Weight = 40 ~ 60 % of Machine Shot Size 制件重量 = 40- 60 % 机器注射容量
Injection Molding Variables
Melt Temperature 熔融温度
35
M e l t F l o w
30 25 20 15
101 @ 600 deg. F
LEXAN?101 550 deg F.
模具注塑术语中英对照

20 Crack/Splits/Chips Cushion 21 22 23 Cycle Cycle Time
lěng què shuǐ cooling dào waterways duàn liè break crack incomplete cán liàng amount xún huán chéng xíng zhōu qī qǐ ké huán xíng jiāo kǒu chǐ cun chāo chā zhí jiāo kǒu wū diǎn (biàn sè) guò lǜ qì cycle complete model cycle rise skin
11 Cavity 12 Charge Clamp 13 14 15 Clamping Plate Clamping Pressure
16 Clarifiers Closed-loop Control 17 18 19 Cold Flow/Orange Peel/Lumps Cooling Channels
5 6 7 8 9 10
Back Pressure Backing Plate
背压 母模背板
Blistering Boss Broken Mold Marks Bubbles
起泡 柱子 模痕 气泡 母模 计量 锁模 锁模板 锁模力 改善PP料的透明度添加剂 回路控制 皱纹 冷却水道 断裂 残量 循环 成型周期
241725486.xlsx
English
Chinese Translated by Tooling, Hi-P Shanghai 烧焦 抗老化剂 抗静电剂 纵横比
பைடு நூலகம்
Pinyan
English INJECTION MOLDING GLOSSARY Back to English scorch A patch or streak of brown or black material on the component caused by air or gases that have not been properly vented from the mold and have caused the material to overheat and burn.
Injectionmolding
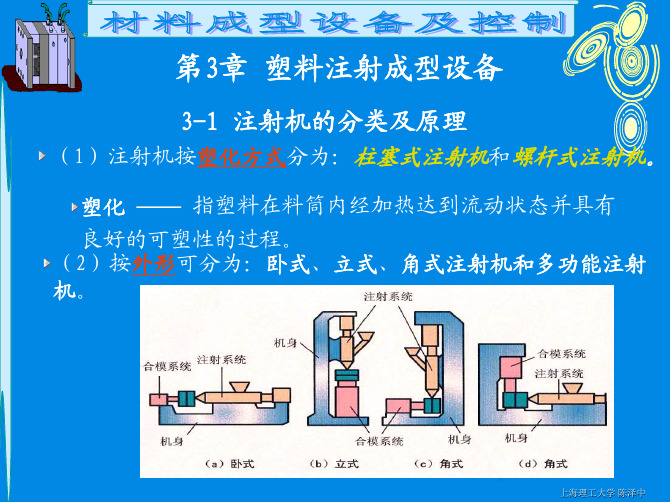
上海理工大学 陈泽中
上海理工大学 陈泽中
3.3 注射机有关工艺参数的校核
注射机类型
柱塞式 螺杆式
(1)对于单分型面模具的开模行程的校核
上海理工大学 陈泽中
S H1 H 2 (5 ~ 10) Smax Sk H m
上海理工大学 陈泽中
(2)对于双分型面模具的开模行程的校核
S H1 H 2 a (5 ~ 10) Smax Sk H m
上海理工大学 陈泽中
螺杆式较柱塞式多一旋转动作,产生分力(Ft),可使 材料在螺旋槽间产生混炼作用,增加了塑化能力。
上海理工大学 陈泽中
3.2 注射机技术参数 见表2-3,2-4
1、注射量 也称公称注射量,指空注射条件下注射
螺杆或注塞做一次最大注射行程时,注射装
置所能达到的最大注射量。
柱塞式注射机的最大注射量是以一次注射聚苯乙烯的最大克数为标准。 螺杆式注射机是以体积表示最大注射量,与塑料的品种无关。 选择时,实际注射量应为注射机公称注射量的 25%~70% 为宜。
F.安装螺孔尺寸
模具重量较轻用压板固定 模具重量较重的用螺钉固定
上海理工大学 陈泽中
G、开模行程的校核
注射机最大开模行程(S)与模具厚度(Hm )无关
对液压式合模装置,注塑机模座最大间距Sk 是个固定 值,注塑机最大模座行程Smax在△H范围内可调; 对液压机械式合模装置,注塑机最大模座行程Smax 是 个固定值,模座最大间距Sk在△H范围内可调。
injection molding

Injection MoldingIntroductionInjection molding is a widely used manufacturing process in the field of plastic production. It involves injecting molten material into a mold cavity, allowing it to cool and solidify, before ejecting the molded part. This process is known for its efficiency, accuracy, and versatility, making it suitable for producing a wide range of plastic products. In this document, we will explore the injection molding process, its advantages, limitations, and relevant considerations.The Injection Molding ProcessStep 1: ClampingThe first step in the injection molding process is clamping. The mold cavity is closed and clamped shut, ensuring that it remains tight and secure during the subsequent steps of the process. The clamping force is controlled depending on the size and complexity of the part being molded.Step 2: InjectionOnce the mold is clamped shut, the molten material, typically a thermoplastic polymer, is injected into the mold cavity through a nozzle. The material is heated and liquefied in a barrel before being pushed under high pressure into the mold. The molten material fills the cavity and takes the shape of the mold.Step 3: CoolingAfter the cavity is filled, the molten material is left to cool and solidify. Cooling time is determined by several factors, including material properties, part design, and thickness. It is crucial to control the cooling process to ensure uniform solidification and prevent defects such as warping or shrinkage.Step 4: EjectionOnce the molded part has cooled and solidified, the mold is opened, and the part is ejected. Ejection mechanisms such as pins or ejector plates are used to remove the part from the mold without causing damage.Step 5: Post-processingDepending on the requirements of the final product, additional post-processing steps may be required. This can include trimming excess material, adding surface finishes, or assembling multiple injected parts.Advantages of Injection MoldingInjection molding has numerous advantages over other manufacturing processes, including:EfficiencyInjection molding allows for high-volume production with minimal wastage. The process can produce a large number ofidentical parts within a short period, making it highly efficient for mass production.Cost-effectivenessOnce the initial mold is created, the cost per unit decreases significantly. This makes injection molding cost-effective for large-scale production runs, as the cost is spread over a large number of parts.Design flexibilityInjection molding offers design flexibility, allowing for the creation of intricate and complex parts. It enables the incorporation of features such as undercuts, threads, and varying wall thicknesses.Material optionsInjection molding supports a wide range of material options, including various thermoplastics and thermosetting plastics. This enables the production of parts with different physical properties, colors, and finishes.Limitations and ConsiderationsHigh initial costThe initial cost of tooling and mold creation can be high. However, this cost is typically offset by the cost savings achieved during large-scale productions runs.Design constraintsCertain design constraints apply to injection molding, such as draft angles and uniform wall thickness. These constraints are necessary to ensure proper mold filling, uniform cooling, and easy ejection of the part.Part size limitationsInjection molding is most suitable for producing small to medium-sized parts. Large parts may require special considerations and equipment.Parting line and gate designThe parting line, where the two halves of the mold meet, and the gate design are important considerations in injection molding. Proper placement of the parting line and gate helps prevent defects like sink marks or visible gate scars.Environmental impactInjection molding relies on the use of plastic materials, which can have a significant environmental impact. Proper disposal and recycling of plastic waste are crucial to mitigate these impacts.ConclusionInjection molding is a highly efficient and versatile manufacturing process for producing plastic parts. From the clamping of the mold to the ejection of the final part, each stepin the process is crucial to ensure high-quality parts. Understanding the advantages, limitations, and considerations of injection molding allows manufacturers to make informed decisions and optimize the production process.。
INJECTION BLOW MOLDING BOTTLE TROUBLESHOOTING 中英文版

INJECTION BLOW MOLDING BOTTLE TROUBLESHOOTING瓶子注吹问题的解决方法The contents of this troubleshooting guide are meant only to give the leaders andmachine operators something to refer to, when trying to correct a problem with abottle on the injection blow molding. The below list is not all the possibility which may be become the cause of the problem, and indeed, the solution may be acombination of several things.这个问题解决方法的内容只是为了在解决瓶子注吹问题时,给领班和机器操作员一些参考。
以下的列表不是所有可能导致问题的原因,事实上,解决方法可能是几件事情的结合。
There are several important things to remember when trying a troubleshooting: 当式着解决一个问题时,有几件很重要的事需要记住:1.THINK! Think about the problem and the possibility reason for it before youtry anything.思考!在你做出任何尝试之前思考出现的问题以及可能的原因。
2.Try only one change at a time. Don’t lose your p erspective.一次只试着改变一个变量!不要失去你的观点3.Be patient! Give a change an opportunity to work before you go into somethingelse. For example, a change in the barrel heat setting may take 15 to 20 minutes before its true effect will be noticed.有耐心!在你得到一些结果之前给变量一个运作的机会。
- 1、下载文档前请自行甄别文档内容的完整性,平台不提供额外的编辑、内容补充、找答案等附加服务。
- 2、"仅部分预览"的文档,不可在线预览部分如存在完整性等问题,可反馈申请退款(可完整预览的文档不适用该条件!)。
- 3、如文档侵犯您的权益,请联系客服反馈,我们会尽快为您处理(人工客服工作时间:9:00-18:30)。
Revision B
SVP Procedure for Critical Process Control
-Injection Molding-
I.PURPOSE
This procedure identifies the injection molding parameters that must be measured, analyzed, controlled, and appropriately acted upon, under the auspices of the Safety Verification Process (SVP). Any control methods used must be proven effective via empirical study, and the data made available in the SVP database.
II.PROCEDURE
For each design and program, the HK/China based team will set up a control plan identifying which parameters will be controlled, and how they will be controlled. At a minimum, the following parameters must always be monitored and controlled in any injection molding process used in SVP: Cycle time, barrel temperature, injection pressure and regrind levels.
A processing window* for each of these setting parameters will be set utilizing data from the machine manufacturer, material manufacturer, designed experiment or other empirical source.
For each of these parameters, and any other machine parameters estab lished by the control plan, the actual readings from each molding machine and regrind levels will be checked, at a minimum, every 4 hours by factory staff.
Regrind level data will be sent to the agency and lab, every day.
For the rest of the parameters listed above, records of the readings taken shall be maintained by the factory staff at the factory, and will be available to agency and laboratory staff, upon request. These records need not be sent the agency or lab, unless a machine operates outside its processing window* or unless specifically requested by the agency or lab. In addition, if molded parts are trimmed or treated in any way after molding, work instructions will be written to describe the proper method of trimming or treatment. Proper performance of work instructions will be checked at each molding machine every 4 hours by factory staff.
If a machine operates for any period of time outside the processing window*, the following will occur:
The factory QC staff will quarantine the affected parts
The factory QC staff will notify the agency of the problem via email
2.6.3The factory, agency and lab staff team will create a CAP identifying what
went wrong, what should be done with the produced parts (re-work, scrap,
sort, other..) and what will be done in future to prevent the event from re-
occurring. Consideration should be given to heightened QC checks, in
Revision B order to detect the problem, should it re-occur. Agency and lab QC staff
will check to see that these procedures are followed during their in process
audits at factories.
2.7 The Control Plan will establish some critical dimensions and tolerances on the
product. Such critical dimensions will be those that, if they excessively will result in an unsafe condition on the final product.
2.8Factory staff will measure and record these critical dimensions on, at a minimum,
5 randomly selected samples from each molding machine, every four hours. Such
records will be available to McDonald’s, the labs and the agency 24 hours of
when the data is collected.
2.9If parts are found that do not comply with set tolerance limits, the following will
occur:
2.9.1 The factory QC staff will quarantine the affected parts
2.9.2 The factory QC staff will notify the agency of the problem via email
2.9.3 The factory, agency and lab staff team will create a CAP identifying what
went wrong, what should be done with the produced parts (re-work, scrap,
sort, other..) and what will be done in future to prevent the event from re-
occurring. Consideration should be given to heightened QC checks, in order
to detect the problem, should it re-occur. Agency and lab QC staff will
check to see that these procedures are followed during their in process audits
at factories.
2.9.4 The CAP will be made available to McDonald’s, the a gency and both labs
for reference.。