影响泵送混凝土泵送的因素及控制措施
泵送混凝土在施工中易出现的问题及防治

泵送混凝土在施工中易出现的问题及防治泵送混凝土是现代建筑施工中的一项重要工艺,它可以降低施工成本,提高施工效率,但同时也存在一些问题,如果不及时防治,就会对施工质量和安全产生影响。
下面就是泵送混凝土在施工中易出现的问题及防治方法。
一、混凝土泵堵塞混凝土泵堵塞一般都是由于混凝土中的固体颗粒过大或沉积在泵管弯头处引起的。
堵塞现象非常严重,如果处理不当,就会使混凝土泵发生管道炸裂、沉积等情况,严重危及施工安全。
因此,防治混凝土泵堵塞是十分重要的。
防治方法:1、设计合理的配合比和粘度,避免混凝土密实和易结块,以减少管道的摩擦力。
2、使用高质量的混凝土,避免使用过期或劣质的混凝土。
3、在泵送混凝土前,要检查泵道内是否有杂物,如有杂物必须清除干净,以避免引起管道堵塞。
二、泵送混凝土的坍落度过低坍落度过低是指混凝土在泵送过程中坍落度下降,造成泵送阻力加大,从而导致泵发送生卡顿、停顿等不良反应。
通常情况下,泵送混凝土时的坍落度应当控制在8-15cm,否则将会影响施工效率。
防治方法:1、严格按照混凝土的设计配合比进行施工,在施工过程中控制水灰比,避免混凝土坍落度过低。
2、混凝土在泵送前需要经过充分的搅拌,以克服混凝土颗粒之间的内部摩擦力。
3、在泵送混凝土时可以添加流动性剂、减水剂等辅助剂来提高混凝土的坍落度,降低其粘度,从而达到更好的泵送效果。
三、管道磨损泵送混凝土时,管道内的混凝土将高速流动,如果管道质量不好或运输时管道与拖车摩擦,就会引起管道的磨损和变形,从而影响施工效果。
防治方法:1、采用耐磨性好的材料进行管道制造,如铸铁、钢等材料,尽量减少使用塑料、橡胶等易损耗材料。
2、管道的支架及接头必须牢固、可靠,防止管道发生位移、震动等情况。
3、运输过程中要对管道进行严格的包装和保护,避免管道与运输工具摩擦,产生磨损和变形。
四、安全隐患泵送混凝土有很多危险因素,例如:管道炸裂、人员伤亡、电击等。
这些危险因素可能会对施工人员和现场环境产生严重影响。
泵送混凝土堵管的原因及处理方法

泵送混凝土堵管的原因及处理方法
泵送混凝土时出现堵管情况是施工中常见的问题之一,主要原因有以下几个方面:
1. 混凝土配合比不合理:混凝土配合比中水灰比过小,粉煤灰含量过高,砂粒过细等都会增加混凝土的黏性,容易堵塞管道。
2. 混凝土含水量过大:混凝土的含水量过大会导致混凝土流动性差,易产生堵塞现象。
3. 混凝土粒径不合适:过大或过小的混凝土颗粒会增加阻力,阻碍混凝土的流动,从而造成堵塞。
4. 管道磨损:长时间使用的泵送管道内壁会产生磨损,导致管道粗糙度增加,容易产生堵塞。
针对堵管问题,可采取以下处理方法:
1. 调整混凝土配合比:合理设计混凝土配合比,增加水灰比和粉煤灰含量,使用适当的砂粒粒径,提高混凝土的流动性,减少堵塞风险。
2. 控制混凝土含水量:在施工中严格控制混凝土的含水量,确保其
流动性能良好,减少堵塞的可能性。
3. 清洗管道:定期对泵送管道进行清洗,去除管道内的混凝土渣滓和堵塞物,保持管道的畅通。
4. 更换管道:如果管道磨损严重,影响混凝土的流动性,应及时更换管道,确保施工的顺利进行。
5. 控制泵送速度:适当控制泵送速度,避免过快或过慢,以减少堵塞的风险。
总之,对于泵送混凝土堵管问题,需要从混凝土配合比、含水量、管道磨损等多个方面进行综合考虑,并采取相应的处理措施,确保施工过程的顺利进行。
浇筑方案中的泵送混凝土施工控制要点

浇筑方案中的泵送混凝土施工控制要点泵送混凝土施工是现代建筑施工中常见的一种施工方式,其具有施工工期短、施工效率高、工作环境优良等优点。
然而,泵送混凝土施工也存在一些潜在的问题和风险,如泵送压力控制不当、混凝土成分配比不合理等。
为了保证泵送混凝土施工质量,提高施工效率,下面从施工控制要点、控制措施等方面进行讨论。
1. 施工控制要点1.1 混凝土配制混凝土配制是泵送混凝土施工的基础,合理的混凝土配制可以保证混凝土的流动性和均匀性,从而避免施工过程中出现堵塞、冒浆等问题。
在混凝土配制过程中,需要根据施工要求和现场实际情况,选择合适的水灰比、胶凝材料和骨料,确保混凝土的强度和耐久性。
1.2 泵送压力控制泵送压力是泵送混凝土施工中最关键的参数之一,过高或过低的泵送压力都会导致泵送混凝土施工出现问题。
如果泵送压力过高,可能会引起管道破裂、气泡过多等情况;如果泵送压力过低,可能会导致流动性差、堵塞等问题。
因此,在泵送混凝土施工中,需要根据混凝土的流动性和泵送距离等因素,合理控制泵送压力,确保泵送过程稳定顺畅。
1.3 浇筑速度控制浇筑速度是指泵送混凝土的流量和速度,过快或过慢的浇筑速度都会影响混凝土的均匀性和质量。
如果浇筑速度过快,可能会导致混凝土流动性差、坍落度减小等问题;如果浇筑速度过慢,可能会引起冒浆、堵塞等情况。
因此,在泵送混凝土施工过程中,需要根据混凝土的流动性和泵送距离,合理控制浇筑速度,保证施工质量。
2. 施工控制措施2.1 混凝土的试验与检验在泵送混凝土施工之前,需要对混凝土进行试验和检验,确保其达到施工要求。
试验内容包括强度试验、抗渗试验等,通过试验结果判断混凝土的质量和性能是否符合要求。
检验内容包括骨料、胶凝材料和混凝土的外观、含水量等,通过检验结果判断材料的质量和配比是否合理。
2.2 泵送设备的维护和保养泵送设备是泵送混凝土施工的核心设备,其运行状态直接影响施工质量。
因此,需要定期对泵送设备进行维护和保养,包括清洗管道、检查管道连接部位是否松动、检查橡胶环是否老化等。
混凝土超高泵送施工措施
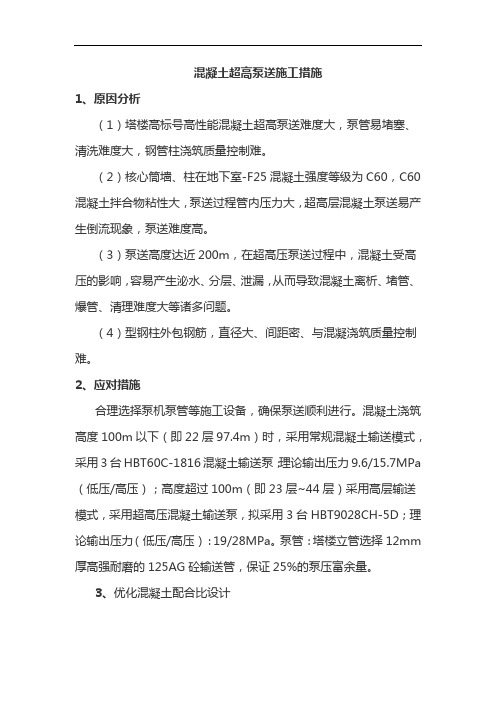
混凝土超高泵送施工措施1、原因分析(1)塔楼高标号高性能混凝土超高泵送难度大,泵管易堵塞、清洗难度大,钢管柱浇筑质量控制难。
(2)核心筒墙、柱在地下室-F25混凝土强度等级为C60,C60混凝土拌合物粘性大,泵送过程管内压力大,超高层混凝土泵送易产生倒流现象,泵送难度高。
(3)泵送高度达近200m,在超高压泵送过程中,混凝土受高压的影响,容易产生泌水、分层、泄漏,从而导致混凝土离析、堵管、爆管、清理难度大等诸多问题。
(4)型钢柱外包钢筋,直径大、间距密、与混凝浇筑质量控制难。
2、应对措施合理选择泵机泵管等施工设备,确保泵送顺利进行。
混凝土浇筑高度100m以下(即22层97.4m)时,采用常规混凝土输送模式,采用3台HBT60C-1816混凝土输送泵;理论输出压力9.6/15.7MPa (低压/高压);高度超过100m(即23层~44层)采用高层输送模式,采用超高压混凝土输送泵,拟采用3台HBT9028CH-5D;理论输出压力(低压/高压):19/28MPa。
泵管:塔楼立管选择12mm 厚高强耐磨的125AG砼输送管,保证25%的泵压富余量。
3、优化混凝土配合比设计1)配备高可泵性、高强度、高耐久性、低收缩、低成本、低水化热、自密实、自养护、自流平的高性能混凝土。
2)建立混凝土流变与可泵性关系,检测混凝土在管道输送过程中的粘滞阻力,为混凝土优化配合比提供依据。
3)水灰比宜控制在0.26-0.32之间,总用水量控制在150-170kg/m³。
4)当采用泵送工艺时,泵送混凝土的砂率宜为38%-45%。
5)控制混凝土的可泵性,一般10s时的相对压力泌水率不宜超过40%。
4、钢管柱选用高流态自密实混凝土,由混凝土自重、泵送压力、自身良好性能达到密实状态。
待混凝土终凝后对钢管混凝土进行超声波检测,确保钢管混凝土的浇筑质量。
混凝土泵送堵管的原因分析及预防措施

混凝土泵送堵管的原因分析及预防措施一、原因分析1.混凝土过于干燥:混凝土过于干燥会造成泵送困难,增加摩擦阻力,容易导致堵塞。
2.混凝土中含有大颗粒物料:混凝土中含有大颗粒物料,会增大泵送阻力,容易引发堵管。
3.管道内积聚物:在连续施工的过程中,管道内会积聚一些混凝土渣块和杂物,堵塞管道,使得混凝土无法正常泵送。
4.泵送压力过大:泵送压力过大会导致管道内混凝土堵塞,阻力增大,影响泵送效果。
5.泵送管道弯曲过多:管道过度弯曲会增加摩擦阻力,容易造成堵管。
6.泵送速度过快:泵送速度过快会导致混凝土流动不畅,堵塞管道。
二、预防措施1.控制混凝土的配合比:合理的配合比可以有效控制混凝土的流动性,避免混凝土过于干燥,减少泵送堵塞的风险。
2.筛选合适的骨料:在施工前筛选合适的骨料,避免大颗粒物料进入混凝土中,减少堵管的可能性。
3.定期清理管道:定期清理管道内的混凝土渣块和杂物,保持管道的畅通,减少泵送堵塞的风险。
4.控制泵送压力:合理控制泵送压力,避免泵送压力过大引发管道堵塞。
5.控制管道弯曲度:合理规划管道布置,控制管道弯曲度,减少摩擦阻力,降低堵管的可能性。
6.控制泵送速度:控制泵送速度,避免速度过快造成混凝土流动不畅,堵塞管道。
7.定期检测管道:定期对泵送管道进行检测,及时发现并修复管道问题,确保泵送畅通。
8.增加润滑剂:在混凝土中加入适量的润滑剂,降低摩擦阻力,增加流动性,减少堵塞的风险。
9.配备清洗设备:为了应对堵管情况,配备相应的清管设备,及时进行清理,保证泵送的正常进行。
总之,混凝土泵送堵管问题的发生与多种因素有关,需要综合考虑。
以上提出的预防措施,旨在减少堵管的风险,提高混凝土泵送的效率与质量。
在实践中,还可以根据具体情况结合经验进行相应的调整和改进。
混凝土泵送时的防堵方法

混凝土泵送时的防堵方法混凝土泵送是现代建筑中常用的一种施工方式,它可以提高施工效率,降低劳动强度,但是在泵送过程中可能会出现堵塞的情况,严重影响施工进度。
因此,防止混凝土泵送时的堵塞是十分重要的。
1. 选择合适的泵送设备首先要选择合适的泵送设备,如选择泵送管道直径和弯头角度适当的泵车,这样可以减小混凝土流动阻力,减少堵塞的可能性。
同时,要根据混凝土的性质和泵送距离选择合适的泵送设备。
2. 控制混凝土的流速在混凝土泵送过程中,要控制混凝土的流速,避免过快或过慢的泵送速度。
过快的泵送速度容易使混凝土在管道中产生堵塞,过慢的泵送速度则容易使混凝土凝固,同样会引起堵塞。
3. 控制混凝土的含水量混凝土含水量过高也容易引起堵塞,因此,在施工前要对混凝土的含水量进行控制。
一般来说,混凝土的含水量控制在50%左右是比较合适的,同时要注意控制混凝土的饱和度,避免过度饱和导致堵塞。
4. 清洗泵送管道在施工过程中,要定期清洗泵送管道,避免管道内混凝土凝固。
一般来说,每泵送500-800立方米混凝土后就应进行一次清洗,同时要保持泵送管道内的湿润状态,避免管道内干燥。
5. 使用防堵剂在泵送过程中,可以添加防堵剂来减少堵塞的可能性。
防堵剂的添加量一般为混凝土总重量的1-2%,并在搅拌混凝土时充分混合。
防堵剂可以改变混凝土的流动性能,减少混凝土在管道中的摩擦力和黏附力,从而减少堵塞的可能性。
6. 增加泵送压力在出现堵塞时,可以适当增加泵送压力,以推动混凝土通过管道。
但是,增加压力过大容易引起管道破裂,因此要根据实际情况掌握增加压力的度。
7. 停机清理在出现堵塞时,应及时停机清理。
清理时要先关闭泵送管道上的阀门,放空管道内的混凝土,然后用清洁水进行冲洗。
清理完毕后再重新启动泵车,进行泵送。
总之,防止混凝土泵送时的堵塞是一个综合性的问题,需要从多个方面进行控制。
只有细心认真的操作,才能保证施工顺利进行。
混凝土泵送堵泵原因分析及解决方法

混凝土泵送堵泵原因分析及解决方法导言使用过混凝土输送泵的人都知道,在使用过程中都不可避免的会出现堵管现象。
那么到底是什么原因造成了堵管问题呢?我们应如何合理解决呢?堵管原因1.操作不当操作人员精力不集中;泵送速度选择不当;余料量控制不适当;混凝土的坍落度过小时采取措施不当;停机时间过长。
2.管道未清洗干净3.管道连接不当4.混凝土或砂浆的离析5.局部漏浆造成的堵管输送管道接头密封不严;眼镜板和切割环之间的间隙过大;混凝土活塞磨损严重;因混凝土输送缸严重磨损而引起的漏浆。
6.非合格的泵送混凝土导致的堵管混凝土坍落度过大或过小;含砂率过小、粗骨料级配不合理;水泥用量过少或过多;外加剂的选用不合理。
解决措施1.合理布管和操作(1)根据工程需要,领用足够的管道、管箍、橡胶密封圈等用品。
(2)服从前场工长指挥,按泵机安全操作规程操作,根据现场实际情况合理布管。
(3)泵机连接直管不得小于10m,尽量减少弯头,软管后不得连接6m以上的直管。
(4)严禁软管做弯管使用,生产中软管不得小于90°使用。
(5)操作过程必须配戴好安全帽,穿好工作服。
2.防止混凝土泵送过程中管路跳动(1)泵送连接平管,每10m应浇筑600mm×400mm×400mm混凝土稳定墩,固定混凝土泵管至立管位置。
(2)立管必须用钢管架牢固,并每班检查,合格后使用。
(3)在泵送过程中,应沿管路检查管道有无磨损、管卡有无松动、橡胶密封圈有无破损和漏浆、漏气现象。
3.防止堵管的措施(1)生产结束后,清理所有管道,拆除立管以下所有管道,清除管内沉积的残留物。
(2)卡箍、密封胶圈按规范装置,不得漏浆、漏气。
(3)向下布管时不得按90°垂直敷设管道,应按30°~45°倾斜布管。
(4)当敷设较长的管路时,应尽可能减少弯管、软管的数量和弯管的度数,当不得不采用90°弯管时,应尽可能使用半径为1m的90°弯管。
泵送混凝土的关键性能特征及影响因素

泵送混凝土的关键性能特征及影响因素混凝土是建筑施工中常见的材料之一,而泵送混凝土则是在特定施工条件下将混凝土通过泵送设备进行输送的一种施工工艺。
泵送混凝土与传统的浇筑方式相比,具有许多优势,如施工速度快、工作效率高、施工质量好等。
然而,泵送混凝土的性能特征与影响因素是需要施工人员重视的关键问题。
首先,泵送混凝土的关键性能特征主要包括以下几个方面。
1. 流动性:泵送混凝土在输送过程中需要具备一定的流动性,以确保顺利通过管道输送到施工现场。
流动性主要取决于混凝土的水灰比、粉料含量、粒径分布以及外加剂的使用等因素。
2. 泵送性能:泵送混凝土需要具备良好的泵送性能,即在泵送设备的作用下能够顺利输送到指定位置。
泵送性能主要取决于混凝土的流动性、粘度、凝结时间和颗粒分布等特性。
3. 抗坍性:泵送混凝土在泵送过程中需要具备一定的抗坍性,以避免塌陷变形或者分层现象的发生。
抗坍性主要取决于混凝土的初凝时间、塑性黏度和骨料形状等因素。
4. 干缩性:泵送混凝土在施工后需要具备一定的干缩性,以确保减少由于干燥引起的收缩开裂风险。
干缩性主要取决于混凝土的水胶比、外加剂的使用以及养护条件等因素。
其次,泵送混凝土的性能特征受到多个因素的影响。
1. 骨料的特性:骨料是混凝土的主要组成部分之一,其颗粒形状、粒径分布、含水率等特性都会对混凝土的流动性、抗坍性等性能产生影响。
2. 水胶比:水胶比是指混凝土中水的质量与水泥和其他胶凝材料质量之比。
水胶比的选择直接影响混凝土的流动性、强度以及耐久性。
3. 外加剂的使用:外加剂是改善混凝土性能的常用手段,可以调节混凝土的流动性、抗坍性、黏度和凝结时间等性能。
4. 施工条件:施工条件包括温度、湿度、泵送设备及管道的状态等因素,这些都会对泵送混凝土的性能产生一定的影响。
为了确保泵送混凝土的施工质量,施工人员可以采取以下措施。
1. 准确掌握混凝土的配合比、骨料特性和外加剂使用量等参数,以保证所使用的混凝土符合设计要求。
- 1、下载文档前请自行甄别文档内容的完整性,平台不提供额外的编辑、内容补充、找答案等附加服务。
- 2、"仅部分预览"的文档,不可在线预览部分如存在完整性等问题,可反馈申请退款(可完整预览的文档不适用该条件!)。
- 3、如文档侵犯您的权益,请联系客服反馈,我们会尽快为您处理(人工客服工作时间:9:00-18:30)。
影响泵送混凝土质量的因素及控制措施
随着建筑业的蓬勃发展,社会对施工环境的要求越来越高,泵送混凝土在工程施工中越来越多地被采用。
泵送混凝土具有输送混凝土能力大、速度快、工期短、费用低及能连续作业的特点,尤其对于高层建筑和大体积混凝土的施工,更能显示出其优越性。
因此加强泵送混凝土质量是当前重中之重。
一、影响因素
从长期的实践和试验中得知,影响泵送混凝土的质量主要有水泥熟料中的C3A含量、外加剂和温度。
因此,做好这三方面的控制,便可减小对混凝土不利的影响。
二、防治措施
1、水泥熟料中的C3A含量
现在建筑施工企业或商品混凝土搅拌站使用散装水泥。
水泥是混凝土的主要原料,在混凝土中发挥着重要作用。
当水泥与水接触时,水泥中C3A迅速水化,生成水化铝酸四钙和水化铝酸二钙,并放出大量的热,然后逐渐转化为水化铝酸三钙。
在这个水化反应的过程中,放出的热量使混凝土内部温度迅速升高,水化反应加速进行。
这将造成混凝土的和易性差而且坍落度损失大,对混凝土的泵送造成很大的影响。
同时对强度的增长也是非常不利的,因为水化反应过快,很大部分水泥颗粒都被包裹在水泥水化产物里面,很难进行水化反应,这其中包括C3S、C2S等强度增长的主要成分,此外还将造成混凝土的孔
隙率增大。
对此,现在很多厂家尽量减少C3A的含量,控制在5%的范围内,同时在水泥熟料中加入适量的石膏。
以改变水泥水化过程和缓解水化发热时间。
因为水泥浆调和后,石膏溶入液体,同时由于硅酸三钙水化,液体中氢氧化钙浓度迅速和硫酸钙浓度升高。
大约经过1-2min 后,硫酸钙和氢氧化钙浓度都升高高某种适当的数值,此时铝酸三钙水化将不生成水化铝酸四钙,而是高硫铝酸钙(钙矾石):3CaO.Al2O3 + 3CaSO4 水 3CaO.Al2O3 .3CaSO4.3CaSO4 .32H2O
钙矾石以极为细小的晶粒生成,积聚在水泥颗粒表面上,有如一种致密的覆盖膜,使C3A不再能够强烈水化,直至硅酸三钙的水化过了潜伏期,在此强烈进行,这一覆盖膜被冲破,不能继续存在,这样,便可按照我们的意愿进行。
2、外加剂
2.1、减水剂
减水剂对现在混凝土而言,已经是必不可少的组成部分,在混凝土中充当的位臵也越来越突出。
减水剂在混凝土中主要起润湿、润滑、分散、发泡和消泡的作用。
减水剂在混凝土中主要是改变水泥水化反应速度。