化学品典型反应过程的安全技术范本
典型反应过程的安全技术范文

典型反应过程的安全技术范文随着工业化的发展,反应过程在许多行业中得到了广泛应用。
然而,一些反应过程涉及到高温、高压、易燃易爆等危险因素,给生产运营带来一定的风险。
因此,为了保障工作人员的安全和减少事故发生的可能性,必须采取适当的安全技术措施。
首先,工艺设计的安全性是保障反应过程安全的重要环节。
在设计阶段,应该充分考虑物料的特性和反应条件,确保设备能够承受预期的工作负荷。
同时,应合理布局设备和管道,保证其互不干扰,避免交叉污染的发生。
另外,应该选择合适的材料和设备,以抗腐蚀、耐高温、耐压的性能。
总之,通过科学的工艺设计,可以降低反应过程中的风险。
其次,设备的维护保养是保障反应过程安全持续运行的关键。
定期检查设备的磨损程度、泄漏情况和腐蚀程度,及时修复和更换有问题的部件。
在设备启动前,应进行全面的检查,确保设备正常运行。
并且,要建立健全的设备维护记录,记录设备的运行状态和维修情况,为设备的长期稳定运行提供参考。
此外,操作人员的安全培训和监督也非常重要。
操作人员应接受相应的培训,了解反应过程的工艺参数和操作规程,熟悉应急处理措施和安全规范。
工作中,严格按照操作规程进行操作,遵守安全操作程序,确保操作的安全性。
此外,还应建立操作人员的安全考核和监督制度,不合格的操作人员要及时进行纠正和培训。
最后,实验室和生产现场的安全管理也必不可少。
实验室要定期检查仪器设备的安全性能,确保其正常工作。
要建立规范的实验室操作流程,保证实验操作的规范性和安全性。
同时,实验室应配备应急处理设备和材料,并制定应急处理预案,以应对各种突发情况。
生产现场要进行安全隐患排查,如排查设备的腐蚀、泄漏等情况,及时采取纠正措施。
并且,定期组织演练,以检验应急处理预案的有效性。
综上所述,对于典型反应过程的安全技术,必须采取一系列综合措施。
从工艺设计、设备维护、操作人员培训和实验室、现场管理等方面提高反应过程的安全性。
只有实施全面的安全技术措施,才能有效降低工作场所事故的发生率,保障工作人员的生命安全和财产安全。
典型反应过程的安全技术
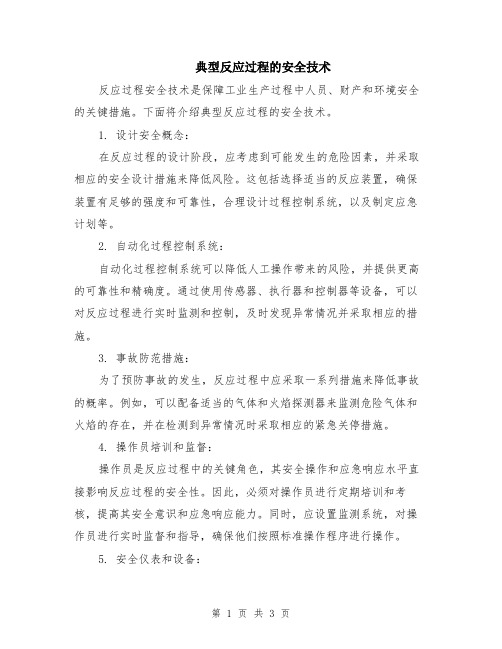
典型反应过程的安全技术反应过程安全技术是保障工业生产过程中人员、财产和环境安全的关键措施。
下面将介绍典型反应过程的安全技术。
1. 设计安全概念:在反应过程的设计阶段,应考虑到可能发生的危险因素,并采取相应的安全设计措施来降低风险。
这包括选择适当的反应装置,确保装置有足够的强度和可靠性,合理设计过程控制系统,以及制定应急计划等。
2. 自动化过程控制系统:自动化过程控制系统可以降低人工操作带来的风险,并提供更高的可靠性和精确度。
通过使用传感器、执行器和控制器等设备,可以对反应过程进行实时监测和控制,及时发现异常情况并采取相应的措施。
3. 事故防范措施:为了预防事故的发生,反应过程中应采取一系列措施来降低事故的概率。
例如,可以配备适当的气体和火焰探测器来监测危险气体和火焰的存在,并在检测到异常情况时采取相应的紧急关停措施。
4. 操作员培训和监督:操作员是反应过程中的关键角色,其安全操作和应急响应水平直接影响反应过程的安全性。
因此,必须对操作员进行定期培训和考核,提高其安全意识和应急响应能力。
同时,应设置监测系统,对操作员进行实时监督和指导,确保他们按照标准操作程序进行操作。
5. 安全仪表和设备:通过安装安全仪表和设备,可以实现对反应过程中的各种参数进行实时监测和控制。
例如,温度、压力、液位等参数的监测仪表可以提供及时的反馈信息,帮助操作员及时发现异常情况并采取相应措施。
6. 安全阀和爆破片:安全阀和爆破片是常用的压力安全装置,用于在反应过程中发生异常压力上升时自动释放压力,以避免容器或管道发生破裂事故。
这些装置必须周期性进行检测和校验,确保其工作正常、灵敏可靠。
7. 材料选择和储存:在反应过程中使用的材料选择具有重要的安全意义。
应选择化学性质稳定、不易发生爆炸、燃烧或有毒气体释放的材料。
同时,应采取正确的储存和处理方式,避免材料的泄漏、混合和污染。
8. 固体粉尘防爆措施:在反应过程中,一些固体物料可能会形成可燃或易爆的粉尘。
化学分析安全操作规程范本(二篇)
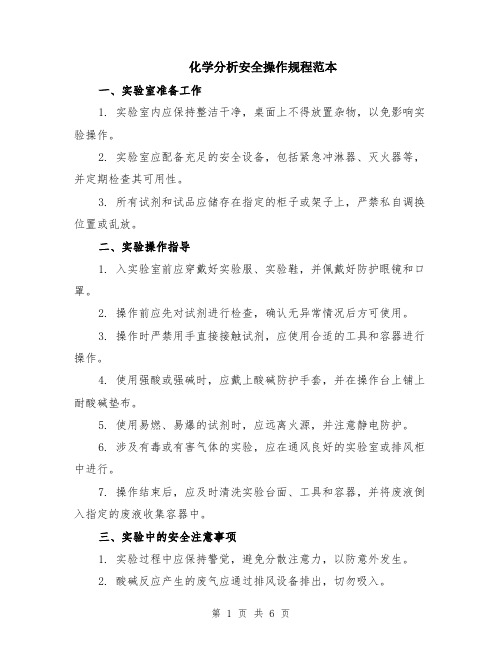
化学分析安全操作规程范本一、实验室准备工作1. 实验室内应保持整洁干净,桌面上不得放置杂物,以免影响实验操作。
2. 实验室应配备充足的安全设备,包括紧急冲淋器、灭火器等,并定期检查其可用性。
3. 所有试剂和试品应储存在指定的柜子或架子上,严禁私自调换位置或乱放。
二、实验操作指导1. 入实验室前应穿戴好实验服、实验鞋,并佩戴好防护眼镜和口罩。
2. 操作前应先对试剂进行检查,确认无异常情况后方可使用。
3. 操作时严禁用手直接接触试剂,应使用合适的工具和容器进行操作。
4. 使用强酸或强碱时,应戴上酸碱防护手套,并在操作台上铺上耐酸碱垫布。
5. 使用易燃、易爆的试剂时,应远离火源,并注意静电防护。
6. 涉及有毒或有害气体的实验,应在通风良好的实验室或排风柜中进行。
7. 操作结束后,应及时清洗实验台面、工具和容器,并将废液倒入指定的废液收集容器中。
三、实验中的安全注意事项1. 实验过程中应保持警觉,避免分散注意力,以防意外发生。
2. 酸碱反应产生的废气应通过排风设备排出,切勿吸入。
3. 操作过程中如发现异常情况,如试剂颜色变化、异味等,应立即停止操作并向导师或实验室管理人员报告。
4. 实验操作完毕后,应关闭气源、断开电源,确保实验室环境的安全。
5. 长时间操作实验时,应注意休息和补充水分,避免过度疲劳。
四、应急措施1. 实验室应配备急救箱和急救设施,并有专人负责急救工作。
2. 发生意外事故时,应立即采取适当的应急处理措施,并通知有关人员。
3. 发生火灾时,应立即按照消防预案进行疏散和灭火。
五、实验室管理1. 实验室管理人员应定期检查和维护实验设备的安全性能。
2. 每位实验人员完成实验后,应及时整理好实验台面,并清理周围环境。
3. 实验室应建立健全的安全责任制度,明确实验人员的安全责任和义务。
4. 实验室应组织定期的安全培训,提高实验人员的安全意识和应急处理能力。
六、实验室安全检查1. 实验室应定期进行安全检查,发现问题及时整改。
化工常见化学反应及其安全技术范文
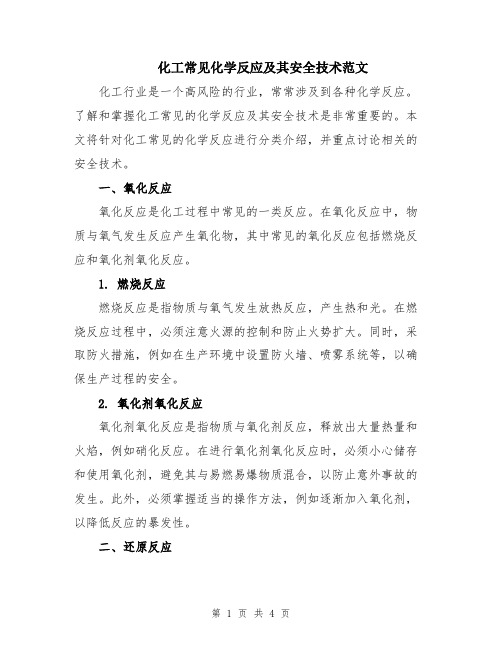
化工常见化学反应及其安全技术范文化工行业是一个高风险的行业,常常涉及到各种化学反应。
了解和掌握化工常见的化学反应及其安全技术是非常重要的。
本文将针对化工常见的化学反应进行分类介绍,并重点讨论相关的安全技术。
一、氧化反应氧化反应是化工过程中常见的一类反应。
在氧化反应中,物质与氧气发生反应产生氧化物,其中常见的氧化反应包括燃烧反应和氧化剂氧化反应。
1. 燃烧反应燃烧反应是指物质与氧气发生放热反应,产生热和光。
在燃烧反应过程中,必须注意火源的控制和防止火势扩大。
同时,采取防火措施,例如在生产环境中设置防火墙、喷雾系统等,以确保生产过程的安全。
2. 氧化剂氧化反应氧化剂氧化反应是指物质与氧化剂反应,释放出大量热量和火焰,例如硝化反应。
在进行氧化剂氧化反应时,必须小心储存和使用氧化剂,避免其与易燃易爆物质混合,以防止意外事故的发生。
此外,必须掌握适当的操作方法,例如逐渐加入氧化剂,以降低反应的暴发性。
二、还原反应还原反应是指原有物质失去氧化性,与还原剂发生反应,产生新的物质。
在还原反应中,常见的反应包括氢氧化反应、金属与酸反应等。
1. 氢氧化反应氢氧化反应是指溶液中的金属阳离子与氧化物阴离子发生反应,生成金属水合物。
在进行氢氧化反应时,必须注意防止过量添加还原剂,以防止产生高热和剧烈反应。
2. 金属与酸反应金属与酸反应是化学实验中常见的一类反应。
金属与酸反应时,常常会产生大量气体,例如金属与盐酸反应时会生成氯气。
在金属与酸反应中,必须注意使用盐酸、硝酸等强酸时的操作方法,避免直接接触以及溅洒到皮肤和眼睛上。
三、酸碱反应酸碱反应是指酸和碱发生中和反应,形成盐和水。
在酸碱反应过程中,常常需要注意酸碱的浓度、配比以及温度等因素。
1. 酸碱浓度在酸碱反应中,酸碱浓度的选择应根据实际需求进行合理的配置。
若浓度选择不当,可能会引发剧烈反应或爆炸事故,因此必须严格控制酸碱的浓度。
2. 酸碱配比在进行酸碱反应时,必须按照化学方程式的要求进行合理的酸碱配比,以确保反应的顺利进行。
化学品典型反应过程的安全技术
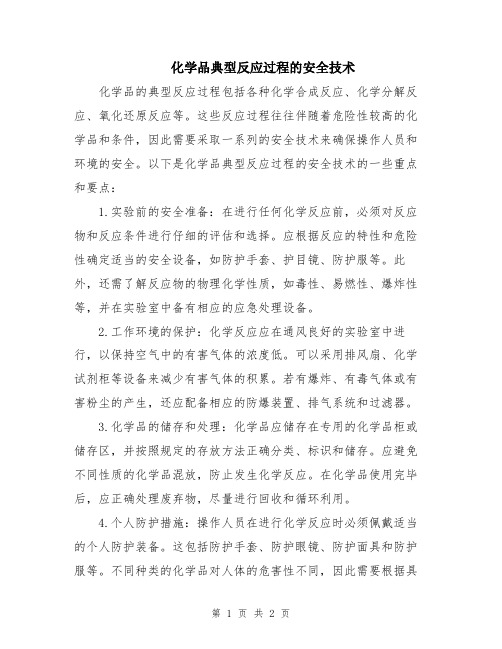
化学品典型反应过程的安全技术化学品的典型反应过程包括各种化学合成反应、化学分解反应、氧化还原反应等。
这些反应过程往往伴随着危险性较高的化学品和条件,因此需要采取一系列的安全技术来确保操作人员和环境的安全。
以下是化学品典型反应过程的安全技术的一些重点和要点:1.实验前的安全准备:在进行任何化学反应前,必须对反应物和反应条件进行仔细的评估和选择。
应根据反应的特性和危险性确定适当的安全设备,如防护手套、护目镜、防护服等。
此外,还需了解反应物的物理化学性质,如毒性、易燃性、爆炸性等,并在实验室中备有相应的应急处理设备。
2.工作环境的保护:化学反应应在通风良好的实验室中进行,以保持空气中的有害气体的浓度低。
可以采用排风扇、化学试剂柜等设备来减少有害气体的积累。
若有爆炸、有毒气体或有害粉尘的产生,还应配备相应的防爆装置、排气系统和过滤器。
3.化学品的储存和处理:化学品应储存在专用的化学品柜或储存区,并按照规定的存放方法正确分类、标识和储存。
应避免不同性质的化学品混放,防止发生化学反应。
在化学品使用完毕后,应正确处理废弃物,尽量进行回收和循环利用。
4.个人防护措施:操作人员在进行化学反应时必须佩戴适当的个人防护装备。
这包括防护手套、防护眼镜、防护面具和防护服等。
不同种类的化学品对人体的危害性不同,因此需要根据具体情况选择合适的个人防护装备,并确保其贴合完整,以防止有害物质接触皮肤、眼睛和呼吸道。
5.注意火源与静电防护:在进行化学反应时,需注意与火源的距离,如使用易燃化学品时,应远离明火和高温物体。
此外,还需注意静电的产生和积累,采取相应的措施来消除静电,如放置适当的接地设备,使用有防静电功能的工具和容器等。
6.应急处理和事故预防:在化学反应过程中,如果发生事故或泄漏,操作人员应立即采取应急措施,如迅速撤离现场、切断电源、控制泄漏等,同时及时向有关部门报告。
此外,可以通过合理的试验设计和技术控制,来预防事故的发生。
化学反应过程的危险性及基本安全技术
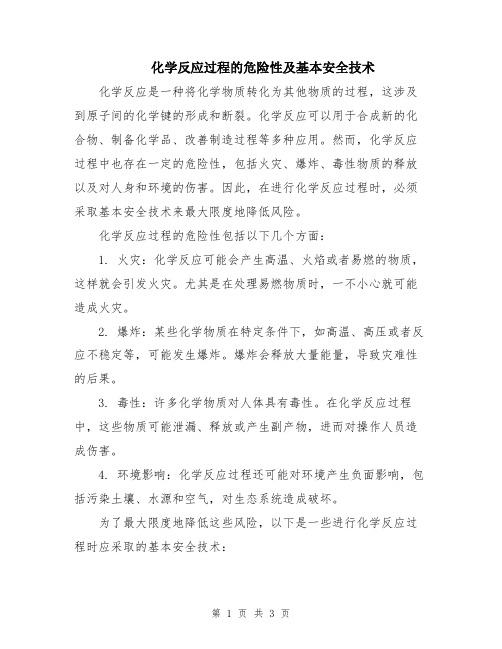
化学反应过程的危险性及基本安全技术化学反应是一种将化学物质转化为其他物质的过程,这涉及到原子间的化学键的形成和断裂。
化学反应可以用于合成新的化合物、制备化学品、改善制造过程等多种应用。
然而,化学反应过程中也存在一定的危险性,包括火灾、爆炸、毒性物质的释放以及对人身和环境的伤害。
因此,在进行化学反应过程时,必须采取基本安全技术来最大限度地降低风险。
化学反应过程的危险性包括以下几个方面:1. 火灾:化学反应可能会产生高温、火焰或者易燃的物质,这样就会引发火灾。
尤其是在处理易燃物质时,一不小心就可能造成火灾。
2. 爆炸:某些化学物质在特定条件下,如高温、高压或者反应不稳定等,可能发生爆炸。
爆炸会释放大量能量,导致灾难性的后果。
3. 毒性:许多化学物质对人体具有毒性。
在化学反应过程中,这些物质可能泄漏、释放或产生副产物,进而对操作人员造成伤害。
4. 环境影响:化学反应过程还可能对环境产生负面影响,包括污染土壤、水源和空气,对生态系统造成破坏。
为了最大限度地降低这些风险,以下是一些进行化学反应过程时应采取的基本安全技术:1. 安全装备:操作人员应正确佩戴个人防护装备,如实验室衣着、手套、眼镜、面罩和鞋套等。
这些装备能够保护操作人员免受化学品的直接接触。
2. 通风系统:化学反应过程中产生的有害气体或蒸气必须通过合适的通风系统排出。
这样可以降低空气中有毒物质的浓度,保护操作人员的健康和安全。
3. 实验室规章制度:制定并执行严格的实验室规章制度,包括禁止吃喝、吸烟、奔跑等行为,遵守操作流程和安全操作指南。
这些规章制度有助于降低意外事故的发生。
4. 废物处理:化学反应过程中产生的废物必须进行正确的处理,以防止对环境造成污染和危害。
废物应被妥善包装和标记,并按照当地法规进行处置。
5. 防火设施:在进行化学反应实验时,应配备适当的防火设施,如灭火器、消防栓和灭火毯等。
这些设备能够在火灾发生时迅速控制和扑灭火源。
6. 工艺安全:选择正确的工艺条件,如温度、压力和物质浓度等,以最小化发生爆炸或危险情况的可能性。
第五章 典型的化学反应过程
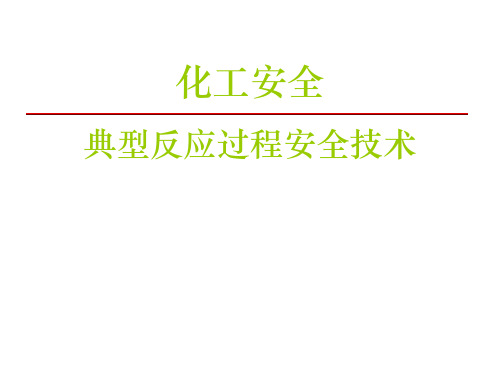
1.3 防火防爆措施
•2.工艺过程的火灾爆炸预防措施 (5)严格按照操作规程作业。
(6)使用氧化剂氧化无机物时,如使用氯酸钾氧化 生成铁蓝颜料,应控制产品烘干温度不超过其着火点, 在烘干之前应用清水洗涤产品,将氧化剂彻底除净,以 防止未完全反应的氯酸钾引起已烘干的物料起火。有些 有机化合物的氧化,特别是在高温下的氧化,在设备及 管道内可能产生焦状物,应及时清除,以防自燃。
1.4 硝酸的生产方法:物料危险性
一、氨
引燃温度:65.1℃,爆炸极限:15.7%--27.4%。
MAC: 30mg/m3. LD50:350mg/kg(大鼠经口); LC50:1 390mg/m3 (4小时,大鼠吸入)
氨经呼吸道进入人体,低浓度氨对黏膜有刺激腐蚀 作用,浓度过高时尚可使中枢神经系统兴奋性增强,引 起痉挛。氨对人体的毒性见下表。急性氨中毒的发生多 由于意外事故,主要表现为呼吸道黏膜刺激和灼伤。轻 度中毒表现有:咳嗽、胸闷、鼻炎、咽炎、气管炎或支 气管炎等表现。
使用硝酸、高锰酸钾等氧化剂时,要严格控 制加料速度,防止多加、错加,固体氧化剂应粉 碎后使用,最好呈溶液状态使用。
1.3 防火防爆措施
•2.工艺过程的火灾爆炸预防措施 (2)及时移走反应热,保证反应在特定的温度范围
内进行。反应中要保证冷却设施正常工作,不间断搅拌, 严格控制反应温度,决不许超过被氧化物质的自燃点。
1.2 工艺危险性分析
•2. 工艺条件危险性分析
• ①氧化反应需要加热,但反应过程又是放热反应。 特别是催化气相反应,一般都是在250~600℃的高 温下进行。
为保证反应正常进行,必须及时移走反应热,否 则将会使反应温度迅速升高,压力增大,反应加速, 造成反应恶性循环,有燃烧爆炸的危险。
典型化工单元操作过程安全技术(一)
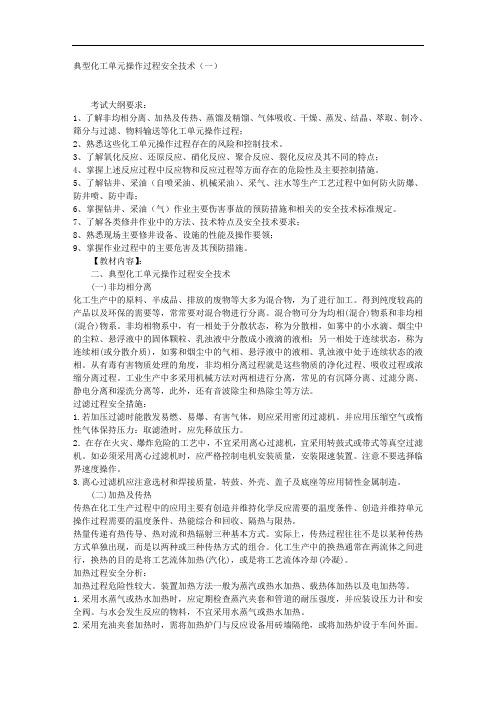
典型化工单元操作过程安全技术(一)考试大纲要求:1、了解非均相分离、加热及传热、蒸馏及精馏、气体吸收、干燥、蒸发、结晶、萃取、制冷、筛分与过滤、物料输送等化工单元操作过程;2、熟悉这些化工单元操作过程存在的风险和控制技术。
3、了解氧化反应、还原反应、硝化反应、聚合反应、裂化反应及其不同的特点;4、掌握上述反应过程中反应物和反应过程等方面存在的危险性及主要控制措施。
5、了解钻井、采油(自喷采油、机械采油)、采气、注水等生产工艺过程中如何防火防爆、防井喷、防中毒;6、掌握钻井、采油(气)作业主要伤害事故的预防措施和相关的安全技术标准规定。
7、了解各类修井作业中的方法、技术特点及安全技术要求;8、熟悉现场主要修井设备、设施的性能及操作要领;9、掌握作业过程中的主要危害及其预防措施。
【教材内容】:二、典型化工单元操作过程安全技术(一)非均相分离化工生产中的原料、半成品、排放的废物等大多为混合物,为了进行加工。
得到纯度较高的产品以及环保的需要等,常常要对混合物进行分离。
混合物可分为均相(混合)物系和非均相(混合)物系。
非均相物系中,有一相处于分散状态,称为分散相,如雾中的小水滴、烟尘中的尘粒、悬浮液中的固体颗粒、乳浊液中分散成小液滴的液相;另一相处于连续状态,称为连续相(或分散介质),如雾和烟尘中的气相、悬浮液中的液相、乳浊液中处于连续状态的液相。
从有毒有害物质处理的角度,非均相分离过程就是这些物质的净化过程、吸收过程或浓缩分离过程。
工业生产中多采用机械方法对两相进行分离,常见的有沉降分离、过滤分离、静电分离和湿洗分离等,此外,还有音波除尘和热除尘等方法。
过滤过程安全措施:1.若加压过滤时能散发易燃、易爆、有害气体,则应采用密闭过滤机。
并应用压缩空气或惰性气体保持压力:取滤渣时,应先释放压力。
2.在存在火灾、爆炸危险的工艺中,不宜采用离心过滤机,宜采用转鼓式或带式等真空过滤机。
如必须采用离心过滤机时,应严格控制电机安装质量,安装限速装置。
- 1、下载文档前请自行甄别文档内容的完整性,平台不提供额外的编辑、内容补充、找答案等附加服务。
- 2、"仅部分预览"的文档,不可在线预览部分如存在完整性等问题,可反馈申请退款(可完整预览的文档不适用该条件!)。
- 3、如文档侵犯您的权益,请联系客服反馈,我们会尽快为您处理(人工客服工作时间:9:00-18:30)。
解决方案编号:LX-FS-A54657化学品典型反应过程的安全技术范本In the daily work environment, plan the important work to be done in the future, and require the personnel to jointly abide by the corresponding procedures and code of conduct, so that the overall behavior oractivity reaches the specified standard编写:_________________________审批:_________________________时间:________年_____月_____日A4打印/ 新修订/ 完整/ 内容可编辑化学品典型反应过程的安全技术范本使用说明:本解决方案资料适用于日常工作环境中对未来要做的重要工作进行具有统筹性,导向性的规划,并要求相关人员共同遵守对应的办事规程与行动准则,使整体行为或活动达到或超越规定的标准。
资料内容可按真实状况进行条款调整,套用时请仔细阅读。
典型反应过程的安全技术(一)、氧化反应1)、氧化反应的主要危险性(1)、氧化反应需要加热,同时绝大多数反应又是放热反应,因此,反应热如不及时移去。
将会造成反应失控,甚至发生爆炸。
(2)、氧化反应中被氧化的物质大部分是易燃、易爆物质,如乙烯氧化制取环氧乙烷、甲醇氧化制取甲醛、甲苯氧化制取苯甲酸中,乙烯是可燃气体,甲苯和甲醇是易燃液体。
(3)、氧化反应中的有些氧化剂本身是强氧化剂,如高锰酸钾、氯酸钾、过氧化氢、过氧化苯甲酰等,具有很大的危险性,如受高温、撞击、摩擦或与有机物、酸类接触,易引起燃烧或爆炸。
(4)、许多氧化反应是易燃、易爆物质与空气或氧气反应,反应投料比接近爆炸极限,如果物料配比或反应温度控制不当,极易发生燃烧爆炸。
(5)、氧化反应的产品也具有火灾、爆炸危险性。
如环氧乙烷、36.7%的甲醛水溶液等。
(6)、某些氧化反应能生成过氧化物副产物,它们的稳定性差,遇高温或受撞击、摩擦易分解,造成燃烧或爆炸。
如乙醛氧化制取醋酸过程中生成过醋酸。
2、氧化过程的安全措施1)、在氧化反应中,一定要严格控制氧化剂的投料比,当以空气或氧气为氧化剂时,反应投料比应严格控制在爆炸范围以外。
(2)、氧化剂的加料速度不宜过快,防止多加、错加。
反应过程应有良好的搅拌和冷却装置,严格控制反应温度、流量,防止超温、超压。
(3)、防止因设备、物料含有杂质为氧化剂提供催化剂,例如有些氧化剂遇金属杂质会引起分解。
空气进入反应器前一定要净化,除掉灰尘、水分、油污以及可使催化剂活性降低或中毒的杂质,减少着火和爆炸的危险。
(4)、反应器和管道上应安装阻火器,以阻止火焰蔓延,防止回火。
接触器应有泄压装置,并尽可能采用自动控制、报警连锁装置。
(5)、在设备系统中宜设置氮气、水蒸气灭火装置,以便及时扑灭火灾。
(二)还原反应1)、还原反应的主要危险性(1)、许多还原反应都是在氢气存在条件下,并在高温、高压下进行,如果因操作失误或设备缺陷发生氢气泄漏,极易发生爆炸。
(2)、还原反应中使用的催化剂,如雷内镍、钯碳等,在空气中吸湿后有自燃危险,在没有点火源存在的条件下,也能使氢气和空气的混合物引燃。
(3)、还原反应中使用的固体还原剂,如保险粉,氢化铝锂、硼氢化钾等,都是遇湿易燃危险品。
(4)、还原反应的中间体,特别是硝基化合物还原反应的中间体,也有一定的火灾危险,例如,邻硝基苯甲醚还原为邻氨基苯甲醚过程中,产生150℃下可自燃的氧化偶氮苯甲醚。
苯胺在生产过程中如果反应条件控制不好,可生成爆炸危险性很大的环已胺。
(5)、高温、高压下的氢对金属有渗碳作用,易造成氢腐蚀。
2)、还原反应过程的安全措施(1)、操作过程中一定要严格控制温度、压力、流量等各种反应参数和反应条件。
(2)、注意催化剂的正确使用和处置。
雷内镍、钯碳等催化剂平时不能暴露在空气中,要浸在酒精中。
反应前必须用氮气置换反应器内的全部空气,经测定确认氧含量符合要求后,方可通入氢气。
反应结束后,应先用氮气把氢气置换掉,才可出料,以免空气与反应器内的氢气混合,在催化剂自燃的情况下发生爆炸。
(3)、注意还原剂的正确使用和处置。
例如,氢化铝锂应浸没在煤油中储存。
使用时应先用氮气置换干净,在氮气保护下投料和反应。
(4)、对设备和管道的选材要符合要求,并定期检测,以防止因氢腐蚀造成事故。
(5)、车间内的电气设备必须符合防爆要求,厂房通风要好,且应采用轻质屋顶,设置天窗或风帽,使氢气易于逸出,尾气排放管要高出屋脊2 m以上并设阻火器。
(三)、硝化反应过程的主要危险及控制有机化合物分子中引入硝基取代氢原子而生成硝基化合物的反应,称为硝化。
用硝酸根取代有机化合物中的羟基的化学反应,则是另一种类型的硝化反应,产物称为硝酸酯。
硝化反应是生产染料、药物及某些炸药的重要反应。
硝化过程常用的硝化剂是浓硝酸或浓硝酸和浓硫酸配制的混合酸。
此外,硝酸盐和氧化氮也可做硝化剂。
一般的硝化反应是先把硝酸和硫酸配制成混酸,然后在严格控制温度的条件下将混酸滴入反应器,进行硝化反应。
1.硝化反应的主要危险性(1)、硝化反应是放热反应,温度越高,硝化反应的速度越快,放出的热量越多,越极易造成温度失控而爆炸。
(2)、被硝化的物质大多为易燃物质,有的兼具毒性,如苯、甲苯、脱脂棉等,使用或储存不当时,易造成火灾。
(3)、混酸具有强烈的氧化性和腐蚀性,与有机物特别是不饱和有机物接触即能引起燃烧。
硝化反应的腐蚀性很强,会导致设备的强烈腐蚀。
混酸在制备时,若温度过高或落入少量水,会促使硝酸的大量分解,引起突沸冲料或爆炸。
(4)、硝化产品大都具有火灾、爆炸危险性,尤其是多硝基化合物和硝酸酯,受热、摩擦、撞击或接触点火源,极易爆炸或着火。
2.硝化反应过程的安全措施(1)、制备混酸时,应严格控制温度和酸的配比,并保证充分的搅拌和冷却条件,严防因温度猛升而造成的冲料或爆炸。
不能把未经稀释的浓硫酸与硝酸混合。
稀释浓硫酸时,不可将水注入酸中。
(2)、必须严格防止混酸与纸、棉、布、稻草等有机物接触,避免因强烈氧化而发生燃烧爆炸。
(3)、应仔细配制反应混合物并除去其中易氧化的组分,不得有油类、酐类、甘油、醇类等有机物杂质,含水也不能过高;否则,此类杂质与酸作用易引发爆炸事故。
(4)、硝化过程应严格控制加料速度,控制硝化反应温度。
硝化反应器应有良好的搅拌和冷却装置,不得中途停水断电及搅拌系统发生故障。
硝化器应安装严格的温度自动调节、报警及自动连锁装置,当超温或搅拌故障时,能自动报警并停止加料。
硝化器应设有泄爆管和紧急排放系统,一旦温度失控,紧急排放到安全地点。
(5)、处理硝化产物时,应格外小心,避免摩擦、撞击、高温、日晒,不能接触明火、酸、碱等。
管道堵塞时,应用蒸气加温疏通,不得用金属棒敲打或明火加热。
(6)、要注意设备和管道的防腐,确保严密不漏。
(四)聚合反应由低分子单体合成聚合物的反应称为聚合反应。
聚合反应的类型很多,按聚合物单体元素组成和结构的不同,分为加成聚合和缩合聚合两大类。
聚合过程在工业上的应用十分广泛,如聚氯乙烯、聚乙烯、聚丙烯等塑料,聚丁二烯、顺丁、丁腈等橡胶以及尼龙纤维等,都是通过小分子单体聚合的方法得到的。
1.聚合反应的主要危险性(1)、聚合反应中的使用单体、溶剂、引发剂、催化剂等大多是易燃、易爆物质,使用或储存不当时,易造成火灾、爆炸。
如聚乙烯的单体乙烯是可燃气体,顺丁橡胶生产中的溶剂苯是易燃液体,引发剂金属钠是遇湿易燃危险品。
(2)、许多聚合反应在高压条件下进行,单体在压缩过程中或在高压系统中易泄漏,发生火灾、爆炸。
例如,乙烯在130~300 MPa的压力下聚合合成聚乙烯。
(3)、聚合反应中加入的引发剂都是化学活性很强的过氧化物,一旦配料比控制不当,容易引起爆聚,反应器压力骤增易引起爆炸。
(4)、聚合物分子量高,黏度大,聚合反应热不易导出,一旦遇到停水、停电、搅拌故障时,容易挂壁和堵塞,造成局部过热或反应釜飞温,发生爆炸。
2.聚合反应过程的安全措施(1)、应设置可燃气体检测报警器,一旦发现设备、管道有可燃气体泄漏,将自动停车。
(2)、反应釜的搅拌和温度应有检测和连锁装置,发现异常能自动停止进料。
(3)、高压分离系统应设置爆破片、导爆管,并有良好的静电接地系统,一旦出现异常,及时泄压。
(4)、对催化剂、引发剂等要加强储存、运输、调配、注入等工序的严格管理。
(5)、注意防止爆聚现象的发生。
(6)、注意防止粘壁和堵塞现象的发生。
(五)裂化反应裂化有时又称为裂解,是指有机化合物在高温下分子发生分解的反应过程。
而石油产品的裂化主要是以重油为原料,在加热、加压或催化荆作用下,分子量较高的烃类发生分解反应生成分子量较小的烃类,在经分馏而得到裂化气、汽油、煤油和残油等产品。
裂化可分为热裂化、催化裂化、加氢裂化3种类型。
1.热裂化热裂化在加热和加压下进行,根据所用压力的不同分为高压热裂化和低压热裂化。
产品有裂化气体、汽油、煤油、残油和石油焦。
热裂化装置的主要设备有管式加热炉、分馏塔、反应塔等。
1)、热裂化的主要危险性热裂化在高温、高压下进行,装置内的油品温度一般超过其自燃点,漏出会立即着火。
热裂化过程产生大量的裂化气,如泄漏会形成爆炸性气体混合物,遇加热炉等明火,会发生爆炸。
2)、热裂化反应过程的安全措施(1)、要严格遵守操作规程,严格控制温度和压力。
(2)、由于热裂化的管式炉经常在高温下运转,要采用高镍铬合金钢制造。
(3)、裂解炉炉体应设有防爆门,备有蒸气吹扫管线和其他灭火管线,以防炉体爆炸和用于应急灭火。
设置紧急放空管和放空罐,以防止因阀门不严或设备漏气造成事故。
(4)、设备系统应有完善的消除静电和避雷措施。
高压容器、分离塔等设备均应安装安全阀和事故放空装置。
低压系统和高压系统之问应有止逆阀。
配备固定的氮气装置、蒸气灭火装置。
(5)、应备有双路电源和水源,保证高温裂解气直接喷水急冷时的用水用电,防止烧坏设备。
发现停水或气压大于水压时,要紧急放空。
(6)、应注意检查、维修、除焦,避免炉管结焦,使加热炉效率下降,出现局部过热,甚至烧穿。
2.催化裂化催化裂化在高温和催化剂的作用下进行,用于由重油生产轻油的工艺。
催化裂解装置主要由反应再生系统、分馏系统、吸收稳定系统组成。
1)、催化裂化的主要危险性催化裂化在160~520℃的高温和0.1~0.2 MPa的压力下进行,火灾、爆炸的危险性也较大。
操作不当时,再生器内的空气和火焰可进入反应器引起恶性爆炸事故。
U形管上的小设备和阀门较多,易漏油着火。
裂化过程中,会产生易燃的裂化气。