凸轮轴机械加工工艺.ppt
凸轮轴生产制造工艺流程

凸轮轴生产制造工艺流程下载温馨提示:该文档是我店铺精心编制而成,希望大家下载以后,能够帮助大家解决实际的问题。
文档下载后可定制随意修改,请根据实际需要进行相应的调整和使用,谢谢!并且,本店铺为大家提供各种各样类型的实用资料,如教育随笔、日记赏析、句子摘抄、古诗大全、经典美文、话题作文、工作总结、词语解析、文案摘录、其他资料等等,如想了解不同资料格式和写法,敬请关注!Download tips: This document is carefully compiled by theeditor. I hope that after you download them,they can help yousolve practical problems. The document can be customized andmodified after downloading,please adjust and use it according toactual needs, thank you!In addition, our shop provides you with various types ofpractical materials,such as educational essays, diaryappreciation,sentence excerpts,ancient poems,classic articles,topic composition,work summary,word parsing,copy excerpts,other materials and so on,want to know different data formats andwriting methods,please pay attention!凸轮轴是发动机等机械设备中的重要零件,它的生产制造过程需要经过多个环节的精密加工。
凸轮轴
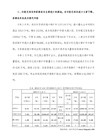
合金铸铁:将接近灰铸铁成份的铁水加入Mn、Cr、Mo、Cu等元素。从而与珠光体形成合金,减少铁素体的数量。合金铸铁的凸轮轴一般用于高转速凸轮轴。如CAC480凸轮轴,凸轮轴整体硬度HB263-311。
由于磨削速度很高,磨削热量来不及传入工件的深处,瞬时聚集在凸轮轴很薄的表层,形成切屑被带走。磨粒切削点的温度达1000?C以上,而内部只有几十度
选用CBN砂轮磨削,磨粒锋利,磨削力小,故磨削区发热量少
CBN显微硬度7300—9000HV,抗弯强度300MPa、抗压强度800--1000MPa、热稳定性1250?C--1350?C。
无进给磨削即光磨,可提高工件的几何精度和降低表面粗糙度参数值,表面粗糙度随光磨次数的增加而降低,细粒度砂轮比粗粒度好
砂轮的修整:修整通常包括整形和修锐,整形是使砂轮达到要求的几何形状和精度,砂轮的几何形状采用数控插补法进行,修锐是除去磨粒间的结合剂,使磨粒露出结合剂一定高度,形成切削刃,磨粒间空隙以容纳切屑。
金刚石滚轮磨削修整的特点:生产率高:以切入法进行修整,修整时间仅需2-10秒,可在进行凸轮轴更换工件时进行修整,不耽误生产节拍,同时由于金刚滚轮的寿命长,修整时间短,大大缩短了辅助时间,单件工件的消耗较低,金刚滚轮的精度较高,修整后的砂轮表面质量也较好。
矿物油冷却液的主要成份是轻质矿物油,加入适量的油溶性防锈添加剂。为了增加矿物油的润滑性能,常加入油性添加剂如脂肪酸等,以提高矿物油在低温低压时的渗透和润滑效果。矿物油的供给方法是喷射法,这样,可以提高供液压力,增大磨削液供给速度,以便将磨削热量迅速带走,并能冲破砂轮高速旋转的气流,使磨削液能有效的进入磨削区,改善磨削效果。由于砂轮的气孔小,磨削液必须经过精密过滤。由于磨削过程所产生的磨屑和砂粒等杂质在磨削液中不断增加,以至磨削液变脏变臭,不仅影响磨削工件的质量,还会危害环境卫生,快速点磨所用的过滤是柱状纸质过滤。
凸轮生产加工工艺流程

凸轮生产加工工艺流程英文回答:The process of cam production and machining involves several steps to ensure the creation of a high-quality and efficient camshaft. It begins with the selection ofsuitable raw materials, which are typically steel alloys or cast iron. These materials are chosen for their strength and durability, as they need to withstand the high stresses and temperatures experienced during engine operation.Once the raw materials are obtained, they are subjected to various shaping processes. The first step is usually rough machining, where the camshaft blank is cut to the approximate shape using milling or turning machines. This rough shape is then refined through a series of grinding operations to achieve the precise dimensions and surface finish required for proper camshaft functioning.After the shaping processes, the camshaft undergoesheat treatment to enhance its mechanical properties. Heat treatment involves heating the camshaft to a specific temperature and then rapidly cooling it to induce changesin its microstructure. This process improves the camshaft's hardness, strength, and wear resistance, ensuring its longevity and reliability in engine applications.Next, the camshaft is subjected to precision machining operations to create the cam lobes and other critical features. This typically involves the use of specialized grinding machines that can accurately shape the cam profile according to the design specifications. These machines use abrasive wheels to remove material from the camshaft surface, gradually forming the desired shape and dimensions.Once the cam lobes are machined, the camshaft undergoes a series of inspections and quality control measures to ensure its dimensional accuracy and surface integrity. This may involve the use of advanced metrology equipment, suchas coordinate measuring machines (CMMs), to verify the camshaft's profile, dimensions, and surface finish. Any deviations or defects are identified and corrected toensure the final product meets the required specifications.Finally, the finished camshaft is subjected to surface treatment processes, such as polishing or coating, tofurther enhance its performance and longevity. Polishing helps to reduce friction and wear, while coatings, such as nitriding or chrome plating, provide additional protection against corrosion and wear.中文回答:凸轮的生产加工工艺流程包括多个步骤,以确保生产出高质量和高效率的凸轮轴。
车铣技术凸轮轴加工工艺分析

车铣技术凸轮轴加工工艺分析凸轮轴是发动机的关键部件之一,负责控制发动机气门的开闭时间和行程,是发动机工作正常的保证之一。
车铣技术是一种广泛应用于机械制造中的加工工艺,它能够实现对复杂曲面的加工,因此非常适合用于凸轮轴的加工。
本文将对凸轮轴加工中常用的车铣技术进行分析,并探讨其工艺特点和优势。
一、车铣技术的工艺特点车铣技术是一种同时结合车削和铣削操作的加工技术,它能够实现对复杂曲面的加工,具有以下几个显著的工艺特点:1. 高加工精度:车铣技术能够通过多轴联动来控制刀具的移动,使得加工精度得到有效保证。
尤其对于凸轮轴这种复杂曲面的加工,车铣技术能够实现高精度的加工。
2. 高加工效率:车铣技术可以一次装夹完成复杂曲面的多面加工,能够大大提高加工效率。
而且,在现代数控机床的应用下,车铣技术能够实现自动化加工,进一步提高了加工效率。
3. 可加工性强:车铣技术适用于各种材料的加工,包括钢、铁、铝合金等。
对于凸轮轴这种材质较硬、形状复杂的零件,车铣技术能够更好地实现其加工要求。
凸轮轴作为发动机的关键部件之一,其加工要求较高。
下面将以一种常见的凸轮轴加工工艺为例,结合车铣技术进行分析。
凸轮轴加工的一般工艺流程如下:1. 材料选择与切削速度确定:根据凸轮轴的材料选择适当的切削工艺参数,包括切削速度、进给速度、切深等。
对于车铣工艺,一般选择较高的切削速度,以提高加工效率。
2. 凸轮轴的粗车:首先对凸轮轴进行粗车,即将材料的多余部分削除。
车铣技术通过刀具的高速旋转和移动,能够快速、高效地进行粗加工。
4. 其他加工工序:根据需要,还可以对凸轮轴进行其他的加工工序,如钻孔、铰孔等。
车铣技术同样适用于这些工序,能够实现高精度的加工。
车铣技术在凸轮轴加工中具有以下几个显著的优势:2. 高加工效率:车铣技术通过一次装夹完成多面加工,大大提高了加工效率。
4. 自动化加工:在现代数控机床的应用下,车铣技术能够实现自动化加工,提高了生产效率和一致性。
凸轮轴加工工艺
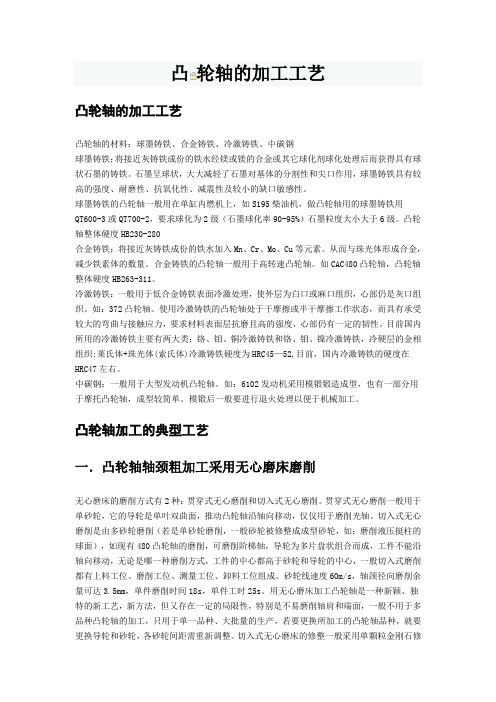
凸轮轴的加工工艺凸轮轴的加工工艺凸轮轴的材料:球墨铸铁、合金铸铁、冷激铸铁、中碳钢球墨铸铁:将接近灰铸铁成份的铁水经镁或镁的合金或其它球化剂球化处理后而获得具有球状石墨的铸铁。
石墨呈球状,大大减轻了石墨对基体的分割性和尖口作用,球墨铸铁具有较高的强度、耐磨性、抗氧化性、减震性及较小的缺口敏感性。
球墨铸铁的凸轮轴一般用在单缸内燃机上,如S195柴油机,做凸轮轴用的球墨铸铁用QT600-3或QT700-2,要求球化为2级(石墨球化率90-95%)石墨粒度大小大于6级。
凸轮轴整体硬度HB230-280合金铸铁:将接近灰铸铁成份的铁水加入Mn、Cr、Mo、Cu等元素。
从而与珠光体形成合金,减少铁素体的数量。
合金铸铁的凸轮轴一般用于高转速凸轮轴。
如CAC480凸轮轴,凸轮轴整体硬度HB263-311。
冷激铸铁:一般用于低合金铸铁表面冷激处理,使外层为白口或麻口组织,心部仍是灰口组织。
如:372凸轮轴。
使用冷激铸铁的凸轮轴处于干摩擦或半干摩擦工作状态,而具有承受较大的弯曲与接触应力,要求材料表面层抗磨且高的强度,心部仍有一定的韧性。
目前国内所用的冷激铸铁主要有两大类:铬、钼、铜冷激铸铁和铬、钼、镍冷激铸铁,冷硬层的金相组织:莱氏体+珠光体(索氏体)冷激铸铁硬度为HRC45—52,目前,国内冷激铸铁的硬度在HRC47左右。
中碳钢:一般用于大型发动机凸轮轴。
如:6102发动机采用模锻锻造成型,也有一部分用于摩托凸轮轴,成型较简单。
模锻后一般要进行退火处理以便于机械加工。
凸轮轴加工的典型工艺一.凸轮轴轴颈粗加工采用无心磨床磨削无心磨床的磨削方式有2种:贯穿式无心磨削和切入式无心磨削。
贯穿式无心磨削一般用于单砂轮,它的导轮是单叶双曲面,推动凸轮轴沿轴向移动,仅仅用于磨削光轴。
切入式无心磨削是由多砂轮磨削(若是单砂轮磨削,一般砂轮被修整成成型砂轮,如:磨削液压挺柱的球面),如现有480凸轮轴的磨削,可磨削阶梯轴,导轮为多片盘状组合而成,工件不能沿轴向移动,无论是哪一种磨削方式,工件的中心都高于砂轮和导轮的中心,一般切入式磨削都有上料工位、磨削工位、测量工位、卸料工位组成。
凸轮轴机械加工工艺ppt

凸轮轴机械加工工艺的未来发展趋势
总结词
数字化、智能化、自动化、绿色制造
详细描述
随着数字化、智能化、自动化、绿色制造等技术的不断 发展,凸轮轴机械加工工艺的未来发展趋势也将随之改 变。数字化技术可以实现凸轮轴机械加工的数字化建模 和仿真优化;智能化技术可以实现凸轮轴机械加工的智 能化控制和监测;自动化技术可以实现凸轮轴机械加工 的全自动化生产;绿色制造技术可以实现凸轮轴机械加结论与展望
总结凸轮轴机械加工工艺的重要性和发展现状
凸轮轴作为发动机的关键部件,其机械加工工艺对 于发动机的性能和可靠性有着至关重要的影响。
随着汽车工业的不断发展,凸轮轴机械加工工艺已 经得到了长足的进步,但仍面临着生产效率低下、
生产成本高昂等问题。
在当前能源紧缺、汽车向节能和环保方向发展的 趋势下,提高凸轮轴机械加工工艺的生产效率和
02
凸轮轴机械加工工艺详细流程
凸轮轴毛坯的选择与准备
1 2
材质选择
根据凸轮轴的工作条件和性能要求,选择合适 的材质,如合金钢、不锈钢等。
毛坯制备
对材料进行切割、锻造、车削等加工,制备出 符合要求的毛坯。
3
热处理
通过加热、冷却等处理,改善毛坯的力学性能 ,提高其抗疲劳性和使用寿命。
凸轮轴的粗加工工艺
某曲轴制造公司的凸轮轴机械加工工艺案例
曲轴制造公司背景
国内专业的曲轴制造企业,主要生产各种类型的汽车曲轴。
凸轮轴机械加工工艺流程
该企业采用了先进的凸轮轴机械加工工艺,主要包括粗车、精车、磨削、抛光等环节。
技术创新点
在磨削环节中,该企业采用了新型的砂轮材料和磨削液,能够实现高精度、高效率的加工。
某汽车制造公司的凸轮轴机械加工工艺案例
汽车凸轮轴零件工艺规程设计
汽车凸轮轴零件工艺规程设计摘要:汽车的凸轮轴在汽车发动机中占据了非常重要的位置,并且随着近几年来汽车发动机行业的蓬勃飞速发展,汽车发动机的制造已经实现了自动化生产,那么,凸轮轴的性能好坏成为了评价发动机性能好坏的一项重要指标。
因此,如何对凸轮轴进行生产,需要进行什么样的加工工艺具有非常大的现实意义,不仅在于可以降低成本、提高利润,还可以促进更好流水生产线的布置。
本文主要介绍了凸轮轴的加工过程,并对其加工工艺进行了详细的分析与研究。
关键词:凸轮轴;发动机;工艺分析1凸轮轴生产线工艺设计1.1生产线布置汽车的凸轮轴在整个汽车发动机的结构布局中占据了非常重要的位置,通常其在流水线的生产过程中选择进行U型布置的方式,U型的中间空间的部分用来放置安装备件的设备,各种仪器的操作面板一般也要面对着该走道,这些开口中间要连接着相应的滑道。
整个车间为整体地基。
这种形式使安装以及移动相关设备变得更加便利,这在对产品进行更换的时候,对提高移动设备的过程和时间是一种非常便利的安排,在对流水线的安排上也能有更大的自主选择权。
1.2工艺设计1.2.1定位基准的选择凸轮轴作为汽车发动机的重要组成部分在其设计过程中必须要保持轴线基准,因为凸轮轴各部分零件的加工很难完成于一次装夹里,故而,要想使加工凸轮轴的精度得到保障,最重要的就是要将多次装夹的定位差距降到最低。
常规方法是采用两顶尖孔来当作定位轴类零件的相关基准,这样不但能够防止在多次装夹的过程中工件因转换定位基准而在定位上产生误差,更能当作定位之后工序的基准,这就与“基准统一”原则相符了。
从凸轮轴的整个结构可以看出,其与一般的轴类零件是完全不一样的。
其具有一些不同的特色,比如整个凸轮是一个沿其轴线为非对称的回转表面,除此之外,凸轮在基圆尺寸、凸轮曲线升程和相位角等方面也有非常高的精度要求。
1.2.2加工阶段的划分与工序顺序的安排1、加工阶段的划分凸轮轴的加工过程一般可以分为三个阶段。
凸轮轴加工工艺
凸轮轴的加工工艺凸轮轴的加工工艺编辑本段凸轮轴的材料:球墨铸铁、合金铸铁、冷激铸铁、中碳钢球墨铸铁:将接近灰铸铁成份的铁水经镁或镁的合金或其它球化剂球化处理后而获得具有球状石墨的铸铁。
石墨呈球状,大大减轻了石墨对基体的分割性和尖口作用,球墨铸铁具有较高的强度、耐磨性、抗氧化性、减震性及较小的缺口敏感性。
球墨铸铁的凸轮轴一般用在单缸内燃机上,如S195柴油机,做凸轮轴用的球墨铸铁用QT600-3或QT700-2,要求球化为2级(石墨球化率90-95%)石墨粒度大小大于6级。
凸轮轴整体硬度HB230-280合金铸铁:将接近灰铸铁成份的铁水加入Mn、Cr、Mo、Cu等元素。
从而与珠光体形成合金,减少铁素体的数量。
合金铸铁的凸轮轴一般用于高转速凸轮轴。
如CAC480凸轮轴,凸轮轴整体硬度HB263-311。
冷激铸铁:一般用于低合金铸铁表面冷激处理,使外层为白口或麻口组织,心部仍是灰口组织。
如:372凸轮轴。
使用冷激铸铁的凸轮轴处于干摩擦或半干摩擦工作状态,而具有承受较大的弯曲与接触应力,要求材料表面层抗磨且高的强度,心部仍有一定的韧性。
目前国内所用的冷激铸铁主要有两大类:铬、钼、铜冷激铸铁和铬、钼、镍冷激铸铁,冷硬层的金相组织:莱氏体+珠光体(索氏体)冷激铸铁硬度为HRC45—52,目前,国内冷激铸铁的硬度在HRC47左右。
中碳钢:一般用于大型发动机凸轮轴。
如:6102发动机采用模锻锻造成型,也有一部分用于摩托凸轮轴,成型较简单。
模锻后一般要进行退火处理以便于机械加工。
凸轮轴加工的典型工艺编辑本段一.凸轮轴轴颈粗加工采用无心磨床磨削编辑本段无心磨床的磨削方式有2种:贯穿式无心磨削和切入式无心磨削。
贯穿式无心磨削一般用于单砂轮,它的导轮是单叶双曲面,推动凸轮轴沿轴向移动,仅仅用于磨削光轴。
切入式无心磨削是由多砂轮磨削(若是单砂轮磨削,一般砂轮被修整成成型砂轮,如:磨削液压挺柱的球面),如现有480凸轮轴的磨削,可磨削阶梯轴,导轮为多片盘状组合而成,工件不能沿轴向移动,无论是哪一种磨削方式,工件的中心都高于砂轮和导轮的中心,一般切入式磨削都有上料工位、磨削工位、测量工位、卸料工位组成。
凸轮轴机械加工工艺
根据加工要求选择合适的装夹方式,如轴向装夹、径向装夹、液气动装夹等,可以方便快捷地装夹工 件并提高加工效率。
切削液选择与使用
切削液类型
根据加工要求和工件材料选择合适的切削液类型,如乳 化液、合成液、极压切削油等,以提高加工性能和工件 质量。
切削液浓度
合理控制切削液浓度,过高的浓度会导致泡沫和污染, 而过低的浓度则会导致冷却和润滑不足,影响加工质量 和刀具寿命。
提高发动机效率
通过优化凸轮轴的机械加工工艺,可以减小气门间隙,提高 气门响应速度,从而优化发动机的燃烧效率,提高发动机的 动力性和经济性。
凸轮轴机械加工工艺的历史与发展
历史
凸轮轴机械加工工艺的发展经历了多个阶段,从早期的手工加工到现代的数控机 床加工,加工效率和精度不断提高。
发展
随着科技的不断发展,凸轮轴机械加工工艺也在不断进步。目前,高速切削、超 精密切削等先进技术正在逐步应用于凸轮轴的机械加工中,以提高加工效率和精 度。同时,数字化和智能化制造也正在逐步实现。
特点
凸轮轴具有复杂的几何形状和较高的精度要求,其加工过程相对较难。此外 ,凸轮轴的工作条件较为恶劣,需要具有较高的耐磨损性和抗疲劳性。
凸轮轴机械加工工艺的重要性
保证凸轮轴的精度和性能
凸轮轴的机械加工工艺对于保证凸轮轴的精度和性能具有至 关重要的作用。精度和性能不达标的凸轮轴会影响发动机的 性能和寿命。
刀具几何参数
合理设计刀具几何参数,如前角、后角、主偏 角、副偏角等,可以改善刀具切削性能和寿命 。
刃磨技术
采用先进的刃磨技术,如激光刃磨、电解刃磨 等,可以提高刀具刃磨质量和精度,延长刀具 使用寿命。
工件定位与装夹
工件定位
采用合理的定位方式,如三爪卡盘、四爪卡盘、液气动夹具等,可以确保工件的定位精度和稳定性。
机械设计凸轮机构设计
2)滚子从动件:从动件的端部装有滚子。 特点: 从动件与凸轮之间可形成滚动摩擦,所以磨损显著减 少,能承受较大载荷,应用较广。但端部重量较大, 又不易润滑,故仍不宜用于高速。
3)平底从动件:从动件端部为一平底。 特点: 若不计摩擦,凸轮对从动件的作用力始终垂直于 平底,传力性能良好,且凸轮与平底接触面间易 形成润滑油膜,摩擦磨损小、效率高,故可用于 高速,缺点是不能用于凸轮轮廓有内凹的情况。
一、凸轮机构的基本术语
以尖顶从动件为对象予以介绍
基圆—以凸轮理论轮廓最小向
径r0为半径所作的圆。
基圆半径—r0 推程—从动件从距离凸轮回 转中心最近位置到距离凸轮 回转中心最远位置的过程, 称为推程。 推程运动角δt —从动件推程 过程,对应凸轮转角称为推
r0 对心式尖顶从动 件盘形凸轮机构
ω
δt
送料机构
内燃机气门机构
应用实例:
盘形凸轮机构
等径凸轮机构
在印刷机中的应用
在机械加工中的应用
利用分度凸轮 机构实现转位
圆柱凸轮机构在机 械加工中的应用
三、凸轮机构的分类 1、按凸轮的形状分类
1)盘形凸轮:凸轮为一绕固定轴线转动且有变化向 径的盘形构件。
盘形凸轮机构简单, 应用广泛,但限于凸 轮径向尺寸不能变化 太大,故从动件的行 程较短。
对于高速凸轮机构,宜选择 amax值较小的运动规律。
若干种从动件运动规律特性比较
运动规律 等速
( hw / δ t )
1.00
vmax
a max
( hw 2 / δ t )
2
冲 击 刚性 柔性 柔性
应用场合 低速轻负荷
∞
等加速等减速 余弦加速度
正弦加速度 3-4-5多项式 改进型等速 改进型正弦加速度 改进型梯形加速度
- 1、下载文档前请自行甄别文档内容的完整性,平台不提供额外的编辑、内容补充、找答案等附加服务。
- 2、"仅部分预览"的文档,不可在线预览部分如存在完整性等问题,可反馈申请退款(可完整预览的文档不适用该条件!)。
- 3、如文档侵犯您的权益,请联系客服反馈,我们会尽快为您处理(人工客服工作时间:9:00-18:30)。
第四节 凸轮轴的检验
中间检验 1)由加工阶段和中间检验的性质 、目的、 作用所决定,每项检验内容的中检数量所 占百分比不同。 2) 对于单项检验,多使用专用定值量具 (如量规),以保证检验的效率和精度。 3)对于综合检验,(如齿轮的检验), 多使 用检验夹具,以保证迅速准确的反映多参 数的测量结果。
最终检验
1)单项检验仍采用专用定值量具,综合性检验仍 采用检验夹具。
二、凸轮轴的材料与毛坯
材料: 铸铁:冷硬铸铁、可淬硬的低合金铸铁、 球墨铸铁等。 钢: 中碳钢、渗碳钢。
毛坯制造方法: 精铸和精锻。 直接用棒料加工。
三、凸轮轴加工工艺性分析
机械加工工艺性差的两个主要原因
1.结构细长,易变形 受力变形、表面残余应力变形、热处理变形。 2.加工难度大 凸轮、偏心轮等复杂表面的尺寸、形状和相互位 置精度要求高。
三、主要表面的加工
(一)凸轮形面的加工
1. 凸轮形面的粗加工 凸轮传统的粗加工方法是采用靠模车床及液
压仿形凸轮铣床, 铣削的凸轮尺寸精度和形状精度 都优于车削, 可直接进行精磨。大量生产的凸轮轴 毛坯均采用精锻或精铸成形, 其毛坯精度高, 加工 余量小, 国外不少厂家采用以磨代车的新工艺, 极 大地简化了凸轮形面的加工。对于棒料毛坯, 由于 余量大, 国外先进的方法是采用CNC 凸轮铣床。
1.轴颈的尺寸精度及各轴颈之间的同轴度; 2.键槽的尺寸和位置精度; 3.止推面相对于支承轴颈轴线的垂直度; 4.凸轮基圆的尺寸精度和相对于支承轴颈 轴线的同轴度;
5.凸轮的周向位置精度(相位角); 6.凸轮的形状精度(曲线升程)等。
以CA 6102 发动机为例, 凸轮的升程偏差 为: A、 D 段为±0 . 015mm; B段为±0 . 05mm; C 段为±0 . 025mm。
多刀仿形单靠模车削
a) 车刀
b)工具的安装
2.凸轮形面的精加工
凸轮轴切点跟踪磨削加工
凸轮形面磨削的新技术
1)采用立方氮化硼砂轮 2)数控凸轮轴磨床 3)采用多片砂轮高强度砂轮进行高速磨削 4)采用主动测量 、自动补偿、自动修整等装置
(二)凸轮支撑轴颈的磨削
支撑轴颈的磨削可采用多砂轮磨床或无 心磨床, 如Junker 公司的Quick point 设备 可以高效率地磨削凸轮轴支撑轴颈。还有 的公司对凸轮轴的轴颈和桃形在精磨后进 行抛光, 与曲轴的超精加工类似。
凸轮轴机械加工工艺
第一节 概述
一、凸轮轴的用途、结构特点与技 术要求
用途: 通过凸轮轴的不断旋转,推动气门顶杆
上下运动,进而控制气门的开启与关闭。 通过改变凸轮轴的曲线,可精确调整气门 开启、关闭时间。
结构特点: 凸轮轴包括支承轴颈、进排气凸轮、偏
心轮、驱动发动机辅助装置的齿轮和正时 齿轮轴颈等几部分。
工序18:铣螺纹
螺纹铣床
工序19:去毛刺 工序20:清洗 工序21:中间检查 工序22:支承轴颈、齿轮表面淬火 工序23:凸轮、偏心轮淬火
工序24:修中心孔
立式钻床
工序25:校直
压床
工序26:磨凸轮、偏心轮
凸轮磨床
工序27:校直
压床
工序28:精磨正时齿轮轴颈外圆和止推面 端面外圆磨床
工序29:精磨四个支承轴颈外圆
外圆磨床
工序30:精磨凸轮和偏心轮
凸轮磨床
工序31:修整螺纹
压床
工序34:清洗 工序35:终检
清洗机
第三节 凸轮轴加工工艺分析
一、定位基准的选择
(一)粗基准的选择 支承轴颈的毛坯外圆柱面及一个侧面。
(二)精基准的选择 1.两顶尖孔 2.经加工的支承轴颈、正时齿轮轴颈
压床
工序10:磨正时齿轮轴颈和螺纹轴颈外圆等 外圆端面磨床
工序11:磨齿轮外圆
外圆磨床
工序12:磨四个支承轴颈外圆 外圆磨床
工序13:滚齿
滚齿机
工序14:去齿轮两端毛刺
去毛刺机
工序15:铣键槽
键槽铣床
工序17:车1、4、6、7、9、12凸轮及偏心轮 凸轮车床
工序17:车2、3、5、8、10、11凸轮 凸轮车床
凸轮轴刚性差、 易变形; 精度高, 加 工难度大。
凸轮轴的主体是一根与汽缸组长度相同 的圆柱形棒体。上面套有若干个凸轮,用 于驱动气门。
凸轮的侧面呈鸡蛋形。其设计的目的在 于保证汽缸充分的进气和排气,具体来说 就是在尽可能短的时间内完成气门的开、 闭动作。
6102发动机凸轮轴
凸轮轴的主要技术要求:
二、加工阶段的划分与工序顺序的 安排
(一)加工阶段的划分 粗加工阶段 半精加工阶段 精加工阶段 光整、精整加工阶段
二、加工阶段的划分与工序顺序的 安排
(二)工序顺序的安排 各支承轴颈、凸轮、偏心轮: 车——粗磨——精磨——抛光 从粗到精,主要表面与次要表面的加工工序交叉 进行。 淬火工序安排在各主要表面的半精加工之前 防止工件经淬火后变形过大造成精加工困难
快速点磨( quickpoint)
(三)砂带抛光
(四)自动校直 凸轮轴
钢料凸轮轴冷、热加工后一般都有弯曲 变形 ,需要校直才能后继加工 。传统工艺使 用压床人工校直 ,常因矫枉过正而反复多次 损害零件强度。而 自动校直由传感器测出轴 的弯曲度后 ,便向校直压头控制器发出指令 , 对轴施加最适当的校直压程 由输人的工艺参 数决定 ,零件只需一次校直 ,工时<2min 。
工序2:校直 压床
工序3: 车1、2支承轴颈外圆等 凸轮轴轴颈车床
工序4: 车3、4支承轴颈外圆等 凸轮轴轴颈车床
工序5:钻φ7孔 钻床
工序6:校直 压床
工序7:磨第2、3轴颈外圆 外圆磨床
工序8:车凸轮侧面和连接轴颈等 凸轮轴车床
工序8:车凸轮侧面和连接轴颈等 凸轮轴车床
工序9:校直
第二节 凸轮轴加工过程概述
发动机总类繁多,凸轮轴的结构形状各 异,但基本形状相差不大。
工序1:铣端面打中心孔 铣钻组合机
中心孔加工是以后加工工序的定位基准 ,在铣端面时,一般只限定5个自由度即可 ,用2个V型块限定4个自由度,轴向自由度 是由凸轮轴3#轴颈前端面或后端面(在产 品设计中,该面应提出具体要求)。目前 普遍采用的是自定心定位夹紧,密齿刀盘 铣削。轴向尺寸保证后端面到毛坯的粗定 位基准尺寸和整个凸轮轴长度